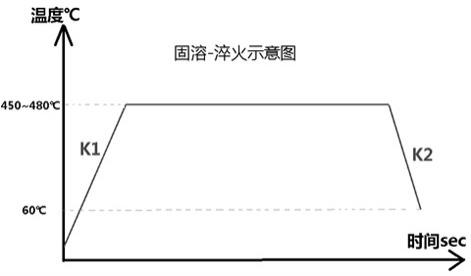
1.本发明属于铝合金带材制备领域,具体涉及一种高强韧薄型7系铝合金带材的制备方法。
背景技术:
2.采用气垫式连续退火炉进行连续热处理,带材通过速度差获得张应力及上下循环风机吹动,保证带材处于稳定漂浮状态,并通过水冷或风冷进行降温,生产效率高,温度控制精度高,组织性能稳定,深受材料制作商的青睐。
3.7系铝合金属于超高强度铝合金,具有高的比强度、比模量、良好的导电导热性、优良的切削性能等特点,被广泛应用于航空航天、汽车、机械制造、船舶、化学工业及民用工业,在电脑、手机、显示屏的背光板和结构件上也得以推广应用。
4.超高强7系铝合金因强度高,塑韧性差,其薄材加工难度很大。一般采用热轧卷切成中厚板材,经辊底炉进行固溶淬火处理,再预拉伸机矫直,最终人工时效产出成品,几乎无冷轧薄料及气垫式连续退火炉固溶淬火的生产方式报道。究其原因主要是在气垫式连续退火炉进行固溶淬火的过程中,一方面需快速升至高温和急速降温实现良好的组织性能,前后卷材热处理工艺可能相差较大,衔接缝合后容易起皱,工艺操作不当容易造成快速运行中带材容易跑偏甚至断带,另一方面快速淬火造成薄带材版型迅速恶化及应力残留,进而严重限制其应用。因此,目前关于厚度0.15~0.50mm的高强韧薄型7系铝合金带材的制备技术仍属于行业内的共性难题。
5.申请号为202011392715.8的中国专利公开了一种650mpa级超高强铝合金薄带制备方法,其通过在al-zn-mg-cu合金基础上添加适量稀土元素er,结合冷轧和退火工艺获得厚度0.50mm的超高强铝合金薄带,而无厚度0.15~0.50mm的生产说明。
6.申请号为202010013070.6的中国专利公开了一种超高强铝合金及其制备方法,其在al-zn-cu-mg系的基础上添加zr、ti和y元素,热挤压加工之后进行固溶时效处理,强度高于900mpa,断后伸长率最大为5.6%,但未涉及气垫式连续退火炉冷轧薄带的加工方法。
7.申请号为201911372829.3及201811484941.1的中国专利分别公开了一种7系铝合金型材及其制造方法和一种航空航天用超高强度7系铝合金型材的生产方法,其均未涉及压延薄带材及气垫式连续退火炉的制作方法。
技术实现要素:
8.本发明针对高强韧7系铝薄材生产制备难的问题,结合冷轧、固溶、淬火、人工时效等工艺,提出一种高强韧薄型7系铝合金带材的制备方法,以顺应电脑、手机、显示屏用材高强度减薄的发展趋势。
9.为实现上述目的,本发明采用如下技术方案:一种高强韧薄型7系铝合金带材的制备方法,其是将7系铝合金带材经冷轧后,于气垫式连续退火炉中进行机械缝合、穿带、预清洗、固溶、淬火及预拉伸处理后,再进行箱式
人工时效退火,以制得所述高强韧薄型7系铝合金带材。其具体操作如下:1) 将7系铝合金带材冷轧至厚度为0.1~0.5mm,然后将其送入气垫式连续退火炉进行前后卷材的机械缝合及穿带;2)将步骤1)整理好的铝合金带材进行碱洗、漂洗等预清洗,以去除轧制过程产生的油污和铝粉;3)将步骤2)清洗后的铝合金带材进行固溶、淬火;4)将步骤3)淬火后的卷材进行0.2~3%的预拉伸处理;5)将预拉伸后的卷材进行箱式人工时效退火。
10.其中,步骤3)中所述固溶是由0~60℃加热至450℃~490℃,保温0~1000s,其温度(单位为℃)随时间(单位为sec)变化的曲线斜率k1为1≤k1≤5;所述淬火的温度随时间变化的曲线斜率k2为3≤k2≤10。进行固溶及淬火时,气垫式连续退火炉的参数设定为:带材加热和冷却的风机流量=(100 m3/sec~200 m3/sec)
×
厚度;带材上下加热和冷却的风机流量差≤
±
5%;炉内张应力=(20%~50%)
×
7系铝合金带材在450℃~490℃范围内的高温屈服强度。所用带材的在线板型应<50i,进行前后缝合的带材厚差应<
±
20%,宽差应<
±
20%,横截面积差应<
±
20%。
11.本发明的有益效果在于:本发明针对高强韧薄型7系铝合金带材存在的生产制备难题,通过限定缝合前后卷材的尺寸偏差及板型控制,结合产品组织性能要求,制定合理的固溶、淬火工艺,并通过炉内张应力、风机流量的协同调控,实现利用气垫式连续退火炉的稳定化生产,开发出一种高强韧7系铝薄带材的制备方法,所制得的铝合金薄带材的成品厚度为0.15~0.50mm,抗拉强度≥510mpa,屈服强度≥430mpa,断后延伸率≥15%,可广泛用于电脑、手机、显示屏的背光板和结构件。
附图说明
12.图1为本发明进行固溶、淬火时温度随时间变化的曲线斜率示意图。
13.图2为实施例1与对比例1所用带料的板型对比图。
14.图3为实施例2(a)与对比例2(b)中气垫式连续退火炉出口板型的对比图。
具体实施方式
15.本发明提供了一种高强韧薄型7系铝合金带材的制备方法,其是将7系铝合金带材利用气垫式连续退火炉进行生产;其具体步骤如下:1)将7系铝合金带材冷轧至厚度为0.1~0.5mm,然后将其送入气垫式连续退火炉进行前后卷材的机械缝合及穿带;2)将步骤1)整理好的铝合金带材进行碱洗、漂洗等预清洗,以去除轧制过程产生的油污和铝粉;3)将步骤2)清洗后的铝合金带材进行固溶、淬火;4)将淬火后的卷材进行0.2~3%的预拉伸处理;5)将预拉伸后的卷材进行箱式人工时效退火,得到所述高强韧薄型7系铝合金带材。
16.为避免因板型不良或突变造成带材运行过程中的急剧恶化,及因前后气垫炉工艺变化造成严重的褶皱甚至断带风险。需管控来料带材的在线板型<50i,前后缝合的带材厚差<
±
20%,宽差<
±
20%,横截面积差<
±
20%。
17.带材快速升温至固溶温度,有利于再结晶晶粒细化,但在急热的条件容易造成带板型的恶化,因此在固溶过程中带材应由0~60℃加热至450℃~490℃,保温0~1000s,温度随时间变化的曲线斜率k1以1≤k1≤5为宜;同理,快速淬火冷却有利于控制析出相的聚集长大,但急冷的条件容易起皱、跑偏甚至断带,因此淬火过程中温度随时间变化的曲线斜率k2以3≤k2≤10为宜(如图1)。
18.进行固溶及淬火时,气垫式连续退火炉利用张力和上下循环风的漂浮作用实现稳定化生产,过大的风机流量及上下流量差容易造成薄料上下、左右浮动运行不稳,轻则刮到炉壁,重则带材直接裂开断带,因此应控制加热和冷却时的风机流量=(100m3/sec~200m3/sec)
×
厚度;带材上下加热和冷却的风机流量差≤
±
5%;同理,作为气垫炉稳定化生产的核心,炉内张应力过小则带材拉扯不紧,运行不稳定,炉内张应力过大则带材高温性能偏低造成拉断风险,因此炉内张应力=(20%~50%)
×
7系铝合金带材的高温(450℃~490℃)屈服强度为宜。
19.为了使本发明所述的内容更加便于理解,下面结合具体实施方式对本发明所述的技术方案做进一步的说明,但是本发明不仅限于此。
20.实施例1(1)将含主要元素cu 0.67%、mg 1.74%、zn 5.46%,其余为铝及其他微量元素的7系铝合金带材冷轧至成品厚度为0.15mm;(2)将冷轧后的带材送入气垫式连续退火炉进行前后卷材的机械缝合及穿带;所用带材的在线板型为20i,前后缝合的带材规格(厚度
×
宽度)分别为0.18mm
×
1200mm、0.15mm
×
1250mm,厚差16.67%,宽差-4.17%,横截面积差13.19%;(3)将穿带后的铝合金带材进行在线碱洗、漂洗等预清洗,以去除轧制过程产生的油污和铝粉;(4)将清洗后的带材进行在线固溶和淬火处理;铝带材上、下加热和冷却的风机流量分别为54m3/sec、55m3/sec;带材上下加热和冷却的风机流量差≤1.85%;炉内张应力为4.4n/mm2(带材在450℃高温屈服强度为22mpa);将清洗后的铝合金带材由30℃加热至450℃(耗时210sec),保温600sec,再快速冷却至60℃(耗时50sec),即升温的斜率k1=2,降温的斜率k2=7.8;(5)将淬火后的卷材进行气垫炉在线0.2%预拉伸处理;(6)将预拉伸后的卷材进行110℃/24h的箱式人工时效退火。
21.制得的铝合金薄带材成品厚度为0.15mm,抗拉强度为582mpa,屈服强度为514mpa,断后延伸率16.2%,该薄板可广泛用于电脑、手机、显示屏的背光板和结构件。
22.实施例2(1)将含主要元素cu 1.32%、mg 2.12%、zn 5.86%,其余为铝及其他微量元素的7系铝合金带材冷轧至成品厚度0.30mm;(2)将冷轧后的带材送入气垫式连续退火炉进行前后卷材的机械缝合及穿带;所用带材的在线板型为30i,前后缝合的带材规格(厚度
×
宽度)分别为0.28mm
×
1500mm、
0.30mm
×
1450mm,厚差7.14%,宽差-3.33%,横截面积差3.57%;(3)将穿带后的铝合金带材进行在线碱洗、漂洗等预清洗,以去除轧制过程产生的油污和铝粉;(4)将清洗后的带材进行在线固溶和淬火处理;铝带材上、下加热和冷却的风机流量分别为15m3/sec、15.5m3/sec;带材上下加热和冷却的风机流量差≤3.23%;炉内张应力为6n/mm2(带材在470℃高温屈服强度为15mpa);将清洗后的铝合金带材由20℃加热至470℃(耗时150sec),保温300sec,再快速冷却至60℃(耗时82sec),即升温的斜率k1=3,降温的斜率k2=5;(5)将淬火后的卷材进行气垫炉在线1%预拉伸处理;(6)将预拉伸后的卷材进行115℃/30h的箱式人工时效退火。
23.制得的铝合金薄带材成品厚度为0.30mm,抗拉强度为567mpa,屈服强度为489mpa,断后延伸率16.7%,该薄板可广泛用于电脑、手机、显示屏的背光板和结构件。
24.实施例3(1)将含主要元素cu 1.32%、mg 2.12%、zn 5.86%,其余为铝及其他微量元素的7系铝合金带材冷轧至成品厚度0.45mm;(2)将冷轧后的带材送入气垫式连续退火炉进行前后卷材的机械缝合及穿带;所用卷材的在线板型12i,前后缝合的带材规格(厚度
×
宽度)分别为0.50mm
×
1600mm、0.45mm
×
1660mm,厚差10%,宽差3.75%,横截面积差6.625%;(3)将穿带后的铝合金带材进行在线进行碱洗、漂洗等预清洗,以去除轧制过程产生的油污和铝粉;(4)将清洗后的带材进行在线固溶和淬火处理;铝带材上、下加热和冷却的风机流量分别为90m3/sec、93m3/sec;带材上下加热和冷却的风机流量差≤3.33%;炉内张应力为4.25n/mm2(带材在480℃高温屈服强度为17mpa);将清洗后的铝合金带材由40℃加热至480℃(耗时147sec),保温500sec,再快速冷却至60℃(耗时42sec),即升温的斜率k1=3,降温的斜率k2=10;(5)将淬火后的卷材进行气垫炉在线2%预拉伸处理;(6)将预拉伸后的卷材进行120℃/24h的箱式人工时效退火。
25.制得的铝合金薄带材成品厚度为0.45mm,抗拉强度为600mpa,屈服强度为537mpa,断后延伸率15.3%,该薄板可广泛用于电脑、手机、显示屏的背光板和结构件。
26.对比例1(1)将含主要元素cu 0.67%、mg 1.74%、zn 5.46%,其余为铝及其他微量元素的7系铝合金带材冷轧至成品厚度为0.15mm;(1)将冷轧后的带材送入气垫式连续退火炉进行前后卷材的机械缝合及穿带;所用带材的在线板型为55i,前后缝合的带材规格(厚度
×
宽度)分别为0.18mm
×
1200mm、0.15mm
×
1250mm,厚差16.67%,宽差-4.17%,横截面积差13.19%;(2)将穿带后的铝合金带材进行在线碱洗、漂洗等预清洗,以去除轧制过程产生的油污和铝粉;(3)将清洗后的带材进行在线固溶和淬火处理,因来料板型不佳,在快速加热和冷却过程中造成板型突变,褶皱断带,无法继续生产及获得成品。
27.对比例2(1)将含主要元素cu 1.32%、mg 2.12%、zn 5.86%,其余为铝及其他微量元素的7系铝合金带材冷轧至成品厚度0.30mm;(2)将冷轧后的带材送入气垫式连续退火炉进行前后卷材的机械缝合及穿带;所用带材的在线板型为30i,前后缝合的带材规格(厚度
×
宽度)分别为0.28mm
×
1500mm、0.30mm
×
1450mm,厚差7.14%,宽差-3.33%,横截面积差3.57%;(3)将穿带后的铝合金带材进行在线碱洗、漂洗等预清洗,以去除轧制过程产生的油污和铝粉;(4)将清洗后的带材进行在线固溶和淬火处理;铝带材上、下加热和冷却的风机流量分别为15m3/sec、15.5m3/sec;带材上下加热和冷却的风机流量差≤3.23%;炉内张应力为6n/mm2(带材在470℃高温屈服强度为15mpa);将清洗后的铝合金带材由20℃加热至470℃(耗时85sec),保温300sec,再快速冷却至60℃(耗时35sec),即升温的斜率k1=5.29,降温的斜率k2=11.71;在快速加热和冷却过程中造成板型突变,褶皱断带,无法继续生产及获得成品。
28.对比例3(1)将含主要元素cu 1.32%、mg 2.12%、zn 5.86%,其余为铝及其他微量元素的7系铝合金带材冷轧至成品厚度0.30mm;(2)将冷轧后的带材送入气垫式连续退火炉进行前后卷材的机械缝合及穿带;所用卷材的在线板型12i,前后缝合的带材规格(厚度
×
宽度)分别为0.50mm
×
1600mm、0.45mm
×
1660mm,厚差10%,宽差3.75%,横截面积差6.625%;(3)将穿带后的铝合金带材进行在线碱洗、漂洗等预清洗,以去除轧制过程产生的油污和铝粉;(4)将清洗后的带材进行在线固溶和淬火处理;铝带材上、下加热和冷却的风机流量分别为90m3/sec、95m3/sec;带材上下加热和冷却的风机流量差5.56%;炉内张应力为4.25n/mm2(带材在480℃高温屈服强度为17mpa);将清洗后的铝合金带材由40℃加热至480℃(耗时147sec),保温500sec,再快速冷却至60℃(耗时42sec),即升温的斜率k1=3,降温的斜率k2=10;因上下风机流量相差较大,薄材在快速加热和冷却过程中上下浮动大,挂至炉壁造成褶皱断带,无法继续生产及获得成品。
29.以上所述仅为本发明的较佳实施例,凡依本发明申请专利范围所做的均等变化与修饰,皆应属本发明的涵盖范围。
再多了解一些
本文用于企业家、创业者技术爱好者查询,结果仅供参考。