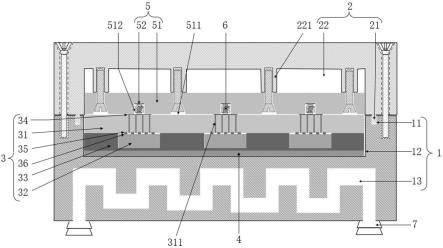
基于tsv工艺晶上系统与pcb板互连结构及制造方法
技术领域
1.本发明涉及微纳加工技术、液冷流道技术、硅通孔(tsv)技术、印制电路板制作技术、机械加工技术、大功率散热等技术领域,尤其涉及一种基于tsv工艺晶上系统与pcb板互连结构及制造方法。
背景技术:
2.在半导体制造领域,有一个著名的摩尔定律,然而,近些年来,微纳加工线宽已达到3nm甚至更小尺寸,摩尔定律已逐渐失效,工艺进步对计算性能的提升明显放缓,而万物互联的数据量却在指数级爆炸式增长,数据规模和计算能力的“剪刀差”鸿沟越来越大,集成电路正在迎来“后摩尔时代”的技术与产业重大变革期。
3.针对摩尔定律已存在不可延续的难题,学术界和产业界主要采用芯片级集成(soc)技术,系统级封装(sip)技术和晶圆级系统(sow)技术对摩尔定律进行扩展。soc技术本质上仍是芯片设计技术,把不同功能相同工艺的芯片集成在一起,受制于芯片加工技术和半导体材料的性能,soc难以形成功能强大的独立系统;高密度基板是sip集成的物理载体,其功能包括元器件之间的电气互连,传输射频、模拟、数字等信号,并且可内埋集成部分无源元件以及功分器、滤波器等,为元器件提供散热通道。sip封装技术本质上是采用多颗芯片利用flip chip工艺或者wire bonding工艺进行2d封装,封装后的器件仍需要贴装在pcb上与其它器件(如电源管理、接口驱动、i/o接口器件)协同工作。并且sip由于其本身集成规模的限制,以及部分功能集成手段的制约,仍很难综合解决散热、电源、外部互连和平台集成等系统必备需求,也无法构成独立的系统。
4.与soc和 sip不同的是:sow所使用的基板为整张半导体晶圆,如2至12英寸硅晶圆,晶圆不划片,晶圆使用rdl工艺进行布线,晶圆采用半导体工艺根据系统功能制备有源器件,如开关、运算放大器、adc、逻辑单元电路等,也可根据系统应用需求不制备器件,仅使用rdl布线,并使用整张晶圆替代传统基板,所有功能电路和有源单元均在晶圆上集成。sow贯穿到集成电路设计、加工和封装的全流程,融合预制件组装和晶圆集成等先进理念,借助晶圆级互连的高带宽、低延迟、低功耗等显著优势,可以实现单一晶圆上集成成千上万的传感、射频、计算、存储、通信等“预制件”颗粒。通过打破现有集成电路的设计方法、实现材料、集成方式等边界条件,有效破解当前芯片性能极限并打破关键信息基础设施依赖“堆砌式”工程技术路线面临的“天花板效应”,刷新传统装备或系统的技术物理形态,使系统综合技术指标获得连乘性增益,满足智能时代5g、大数据、云平台、ai、边缘计算、智慧网络等新一代基础设施的可持续发展需求。
5.然而,受晶圆的机械强度及rdl布线规则约束,大尺寸sow实现难度遇到前所未有的挑战,主要原因在于尽管核心算力、存储、控制、接口ip等功能模块可以在晶圆上集成,但外围电路如电源管理模块、i/o接插件、换能传感器、显示模块、机械传动模块仍需要集成在传统pcb板上,这是因为pcb板材的机械强度和布线层数远胜于晶圆。因此,为实现sow稳定、可靠、高效地工作,融合晶圆电路和pcb电路各自的优势,将sow和pcb集成在一起成为了良
好的解决方案。但pcb电路板由于布线导致内层残铜率不一致,正反面过孔不对称,各层层压材料、厚度不一致,层压子板热膨胀系数(cte)不相同。
6.为此,我们提出一种基于tsv工艺晶上系统与pcb板互连结构及制造方法以解决上述技术问题。
技术实现要素:
7.本发明的目的在于提供一种基于tsv工艺晶上系统与pcb板互连结构及制造方法,通过刚性结构件凹槽固定并展平翘曲的pcb板,通过粘稠胶和结构件凹槽固定晶上系统,芯粒和晶圆压焊点通过tsv孔连接,利用弹性连接器连接pcb焊盘和晶圆压焊点,解决了大尺寸晶圆与翘曲pcb之间的信息交互问题,利用结构件液冷通道解决了晶上系统散热问题。
8.本发明采用的技术方案如下:一种基于tsv工艺晶上系统与pcb板互连结构,包括底部结构件和顶部结构件,所述底部结构件与所述顶部结构件通过连接件可拆卸链接,所述底部结构件的上表面设置有底部凹槽,所述底部凹槽内设置有晶上系统,所述晶上系统的下表面与所述底部凹槽之间贴合连接,所述顶部结构件的下表面设置有顶部凹槽,所述顶部凹槽内通过连接件连接有pcb预制件,所述pcb预制件的另一端通过弹性连接器连接所述晶上系统。
9.进一步地,所述晶上系统包括晶圆、芯粒、有机填充物、晶圆压焊点、晶圆键合点和芯粒键合点,所述晶圆设置于所述底部凹槽内,所述晶圆上设置有若干组贯通的tsv孔,所述tsv孔对应的所述晶圆的下表面设置有所述晶圆键合点,所述晶圆键合点的下表面连接所述芯粒键合点,所述芯粒键合点的另一端连接所述芯粒,相邻所述芯粒之间填充所述有机填充物,所述tsv孔对应的所述晶圆的上表面设置所述晶圆压焊点。
10.进一步地,所述晶圆键合点的下表面通过热压键合工艺或者无污染焊接工艺键合连接所述芯粒键合点。
11.进一步地,每组所述tsv孔为四个,且所述tsv孔与所述晶圆键合点交错设置。
12.进一步地,所述pcb预制件包括pcb板和焊盘,所述顶部凹槽的上表面设置有若干凸台,所述pcb板上设置有与所述凸台对应的贯通孔,所述pcb板通过连接件贯穿所述贯通孔并延伸至所述凸台与所述顶部凹槽连接,所述pcb板的下表面均布设置有若干盲孔,所述盲孔与所述晶圆压焊点对应,所述盲孔的顶壁设置所述焊盘,所述焊盘的下表面连接所述弹性连接器,所述弹性连接器的另一端连接所述晶圆压焊点。
13.进一步地,所述底部结构件的内部设置有液冷通道。
14.进一步地,所述液冷通道两端设置有接头。
15.进一步地,所述底部结构件和顶部结构件的材质为金属或者陶瓷,所述底部结构件的上表面设置有若干定位孔,所述顶部结构件的下表面设置有与所述定位孔契合连接的定位销。
16.进一步地,所述弹性连接器为微弹簧、毛纽扣或弹性绝缘子。
17.本发明还提供一种基于tsv工艺晶上系统与pcb板互连结构的制造方法,包括以下步骤:步骤s1:在pcb板上加工若干贯通孔,在pcb板的下表面加工若干盲孔,盲孔内焊接焊盘,形成pcb预制件;
步骤s2:通过微纳工艺在晶圆上制备若干贯通的tsv孔,tsv孔对应的晶圆的上表面设置晶圆压焊点,tsv孔对应的晶圆的下表面设置晶圆键合点,将若干芯粒倒扣在晶圆上,使芯粒键合点与晶圆键合点对齐,并使用热压键合工艺或者无污染焊接工艺键合连接在一起,再使用有机填充物填充缝隙,然后使用cmp工艺磨平、减薄,形成晶上系统;步骤s3:加工顶部结构件,顶部结构件下表面制备顶部凹槽,顶部凹槽内制备凸台,顶部结构件的下表面设置定位销;步骤s4:加工底部结构件,底部结构件上表面制备底部凹槽,底部结构件还制备与顶部结构件契合定位孔,底部结构件内部制备封闭液冷通道;步骤s5:将pcb预制件安置在顶部结构件的顶部凹槽内,使用连接件穿过pcb板的贯通孔并延伸至凸台与顶部凹槽固定连接,形成顶部预制件;步骤s6:将晶上系统安置在底部结构件的底部凹槽内,并使芯粒朝下,晶上系统与底部凹槽之间贴合固定,形成底部预制件;步骤s7:将弹性连接器插入pcb板的盲孔并与焊盘连接,并将顶部结构件的定位销与底部结构件上的定位孔契合连接,使弹性连接器的另一端与晶上系统上的晶圆压焊点连接,并通过若干连接件贯穿顶部结构件并延伸至底部结构件,形成互联结构体;步骤s8:将接头安装在底部结构件的液冷通道的端口处,并使用胶密封以确保不漏水,完成装配。
18.本发明的有益效果是:利用顶部结构件顶部凹槽和凸台,不仅能支撑和固定pcb板,还能修正并改善pcb板因子板cte差异和高温层压、内层走线、盲孔、铜厚等不一致、不对称导致的翘曲问题,使pcb板的翘曲率降低至少90%。tsv技术作为最为先进的微纳加工工艺,由于连接密度高,信号时延小而广受应用,但现有tsv技术只在小面积芯片(<30mm
×
30mm)多层堆叠封装上应用较为成熟,如128层、164层、196层存储芯片,对于大尺寸晶圆(>8英寸)高密度tsv孔技术目前尚无成熟的应用方案。本发明创造性地通过高密度大尺寸晶圆tsv工艺,将晶上系统的调试口、馈电口、信号i/o口统一分配至晶圆同侧,以便与pcb板等外围电路进行信息交换,这解决了晶圆上高密度、高速率信号连接与传输问题,也显著降低了晶圆上布线(rdl)的难度和复杂度。由于在大尺寸晶圆上制备高密度tsv孔需要将晶圆减薄,并且tsv孔金属化填充也会引起晶圆发生翘曲,这也是传统高密度tsv工艺仅用于小尺寸芯片3d封装的主要原因。本发明利用粘稠胶的柔性和展性,结合弹性连接器的可伸缩性,通过pcb预制件对晶圆均匀施加一定的压力,在改善晶圆翘曲的同时实现了晶圆与pcb板之间良好的电气连接,从而解决晶上系统与pcb板电路信息互通难题。
附图说明
19.图1为本发明的整体结构示意图;图2为本发明实施例的子板一顶视图和侧视图;图3为本发明实施例的子板二底视图和侧视图;图4为本发明实施例的pcb板底视图和侧视图;图5为本发明实施例的晶上系统侧视图;图6为本发明实施例的晶上系统俯视图;图7为本发明实施例的晶上系统底视图;
图8为本发明实施例顶部结构件斜二测图;图9为本发明实施例的底部结构件下半部分的顶视图和侧视图;图10为本发明实施例的底部结构件上半部分的顶视图和侧视图;图11为本发明实施例底部结构件的顶视图和侧视图。
20.附图标记说明1-底部结构件,11-定位孔,12-底部凹槽,13-液冷通道,2-顶部结构件,21-定位销,22-顶部凹槽,221-凸台,3-晶上系统,31-晶圆,311-tsv孔,32-芯粒,33-有机填充物,34-晶圆压焊点,35-晶圆键合点,36-芯粒键合点,4-粘稠胶,5-pcb预制件,51-pcb板,511-贯通孔,512-盲孔,52-焊盘,6-弹性连接器,7-接头。
具体实施方式
21.以下对至少一个示例性实施例的描述实际上仅仅是说明性的,决不作为对本发明及其应用或使用的任何限制。基于本发明中的实施例,本领域普通技术人员在没有作出创造性劳动前提下所获得的所有其他实施例,都属于本发明保护的范围。
22.见图1,一种基于tsv工艺晶上系统与pcb板互连结构,包括底部结构件1和顶部结构件2,所述底部结构件1与所述顶部结构件2通过连接件可拆卸链接,所述底部结构件1的上表面设置有底部凹槽12,所述底部凹槽12内设置有晶上系统3,所述晶上系统3的下表面与所述底部凹槽12之间贴合连接,所述顶部结构件2的下表面设置有顶部凹槽22,所述顶部凹槽22内通过连接件连接有pcb预制件5,所述pcb预制件5的另一端通过弹性连接器6连接所述晶上系统3。
23.所述晶上系统3包括晶圆31、芯粒32、有机填充物33、晶圆压焊点34、晶圆键合点35和芯粒键合点36,所述晶圆31设置于所述底部凹槽12内,所述晶圆31上设置有若干组贯通的tsv孔311,所述tsv孔311对应的所述晶圆31的下表面设置有所述晶圆键合点35,所述晶圆键合点35的下表面连接所述芯粒键合点36,所述芯粒键合点36的另一端连接所述芯粒32,相邻所述芯粒32之间填充所述有机填充物33,所述tsv孔311对应的所述晶圆31的上表面设置所述晶圆压焊点34。
24.所述晶圆键合点35的下表面通过热压键合工艺或者无污染焊接工艺键合连接所述芯粒键合点36。
25.每组所述tsv孔311为四个,且所述tsv孔311与所述晶圆键合点35交错设置。
26.所述pcb预制件5包括pcb板51和焊盘52,所述顶部凹槽22的上表面设置有若干凸台221,所述pcb板51上设置有与所述凸台221对应的贯通孔511,所述pcb板51通过连接件贯穿所述贯通孔511并延伸至所述凸台221与所述顶部凹槽22连接,所述pcb板51的下表面均布设置有若干盲孔512,所述盲孔512与所述晶圆压焊点34对应,所述盲孔512的顶壁设置所述焊盘52,所述焊盘52的下表面连接所述弹性连接器6,所述弹性连接器6的另一端连接所述晶圆压焊点34。
27.所述底部结构件1的内部设置有液冷通道13。
28.所述液冷通道13两端设置有接头7。
29.所述底部结构件1和顶部结构件2的材质为金属或者陶瓷,所述底部结构件1的上表面设置有若干定位孔11,所述顶部结构件2的下表面设置有与所述定位孔11契合连接的
定位销21。
30.所述弹性连接器6为微弹簧、毛纽扣或弹性绝缘子。
31.一种基于tsv工艺晶上系统与pcb板互连结构的制造方法,包括以下步骤:步骤s1:在pcb板51上加工若干贯通孔511,在pcb板51的下表面加工若干盲孔512,盲孔512内焊接焊盘52,形成pcb预制件5;步骤s2:通过微纳工艺在晶圆31上制备若干贯通的tsv孔311,tsv孔311对应的晶圆31的上表面设置晶圆压焊点34,tsv孔311对应的晶圆31的下表面设置晶圆键合点35,将若干芯粒32倒扣在晶圆31上,使芯粒键合点36与晶圆键合点35对齐,并使用热压键合工艺或者无污染焊接工艺键合连接在一起,再使用有机填充物33填充缝隙,然后使用cmp工艺磨平、减薄,形成晶上系统3;步骤s3:加工顶部结构件2,顶部结构件2下表面制备顶部凹槽22,顶部凹槽22内制备凸台221,顶部结构件2的下表面设置定位销21;步骤s4:加工底部结构件1,底部结构件1上表面制备底部凹槽12,底部结构件1还制备与顶部结构件2契合定位孔11,底部结构件1内部制备封闭液冷通道13;步骤s5:将pcb预制件5安置在顶部结构件2的顶部凹槽22内,使用连接件穿过pcb板51的贯通孔511并延伸至凸台221与顶部凹槽22固定连接,形成顶部预制件;步骤s6:将晶上系统3安置在底部结构件1的底部凹槽12内,并使芯粒32朝下,晶上系统3与底部凹槽12之间用粘稠胶4固定,形成底部预制件;步骤s7:将弹性连接器6插入pcb板51的盲孔512并与焊盘52连接,并将顶部结构件2的定位销21与底部结构件1上的定位孔11契合连接,使弹性连接器6的另一端与晶上系统3上的晶圆压焊点34连接,并通过若干连接件贯穿顶部结构件2并延伸至底部结构件1,形成互联结构体;步骤s8:将接头7安装在底部结构件1的液冷通道13的端口处,并使用胶密封以确保不漏水,完成装配。
32.实施例:步骤s1:参见图2,使用松下m4板材层压尺寸340mm
×
340mm
×
1.5mm多层pcb板51,共6层,pcb板51的下表面加工若干盲孔512,盲孔512内连接直径0.3mm的焊盘52,焊盘52与pcb模块单元(如电源管理模块、i/o模块、debug模块)具有电气连接特性,然后在焊盘52同侧加工若干适配m2.5螺钉的沉头通孔,记为子板一;参见图3,准备单层高强度无铜pcb子板,pcb子板尺寸为340mm
×
340mm
×
1.5mm,pcb子板加工位置、数量、尺寸与子板一中m2.5沉头通孔及φ0.3mm契合的通孔,记为子板二;参见图4,将子板一和子板二层压结合在一起,并使用丝网印刷工艺制备厚度10um阻焊层,完成pcb预制件5的加工。
33.步骤s2:参见图5-图7,采用微纳加工技术在12英寸硅晶圆31一侧加工若干晶圆压焊点34,晶圆压焊点34直径0.3mm,另一侧加工若干晶圆键合点35,晶圆键合点35尺寸、位置和数量与待键合的芯粒键合点36对齐,加工若干tsv孔311,tsv孔311直径10um,tsv孔311与晶圆压焊点34、晶圆键合点35形成电气连接,并将晶圆31减薄至120um左右。将若干芯粒32通过热压键合工艺键合在晶圆31上,键合时确保晶圆键合点35与芯粒键合点36对准,键合完毕后使用机填充物33在芯粒32侧填充平整,再使用机械化学抛光(cmp)工艺磨平、减薄至220-240um厚度,制成晶上系统3。
34.步骤s3:参见图8,使用紫铜加工尺寸为400mm
×
400mm
×
20mm的顶部结构件2,在顶部结构件2下表面制备顶部凹槽22,顶部凹槽22尺寸为340mm
×
340mm
×
10mm,顶部凹槽22内加工凸台221,凸台221高度7mm,直径5mm,凸台221中心加工m2.5
×
10螺纹孔,凸台221中心位置、数量与步骤s1中pcb预制件5的m2.5通孔位置及数量对应。顶部结构件2底部还加工有两个φ1.5
×
1.5mm定位销21;整个顶部结构件2还加工有若干φ3.5通孔,通孔位置、数量与步骤7加工的m3.5
×
10mm螺纹孔契合,制成顶部结构件2。
35.步骤s4:参见图9,使用紫铜加工底部结构件1下半部分,尺寸为400mm
×
400mm
×
15mm,在底部结构件1的上表面四周加工若干m3
×
9mm螺纹孔,在底部结构件1的上表面中间区域加工蛇形走线的凹槽,凹槽宽度3mm,相邻凹槽壁厚5mm,槽深1.5mm,凹槽走线首末各加工一个φ2.5mm通孔;参见图10,使用紫铜加工底部结构件1上半部分,尺寸为400mm
×
400mm
×
15mm,四周加工若干与上半部分位置、数量、尺寸契合的φ3通孔,在底部结构件1的上表面加工φ304.8mm底部凹槽12,深0.4mm,底部结构件1的下表面加工宽度、走向、壁厚与底部结构件1上表面契合的凹槽,槽深1.5mm,底部结构件1的上表面斜对的角落还加工有两个φ1.5
×
2mm的定位孔11和若干m3.5
×
10mm螺纹孔;参见图11,把底部结构件1的上表面和下表面贴合在一起,底部结构件1下半部分和底部结构件1上半部分的凹槽贴合在一起形成封闭液冷通道13,并用若干m3
×
20mm螺丝钉穿过底部结构件1下半部分的φ3通孔直入底部结构件1上半部分的螺纹孔,形成底部结构件1。
36.步骤s5:将pcb预制件5使用若干m2.5
×
8mm的沉头螺钉安装固定在顶部结构件2顶部凹槽22内的凸台221上,并使φ0.3盲孔512朝顶部凹槽22外,露出焊盘52,并将若干数量与盲孔512一致的直径0.254mm、长度1.78mm的毛纽扣穿过φ0.3的盲孔512并与焊盘52接触制成顶部预制件。
37.步骤s6:在底部结构件1底部凹槽12内均匀涂覆约250um厚的导热硅脂,将晶上系统3经过cmp处理的一侧朝下放入底部凹槽12内,制成底部预制件。
38.步骤s7:将底部预制件和顶部预制件通过定位销21定位对准,贴合在一起,并使用若干m3.5
×
36mm螺丝钉固定,形成组合件。
39.步骤s8:在组合件底部φ2.5mm孔内安装尺寸契合的接头7,并确保接头7与组合件之间密封良好,至此装配完成。
40.更详细的实施前后效果对比参见表1,表1从pcb板51的翘曲率,晶上系统3翘曲率,pcb板51与晶上系统3贴合形成的高度差变化情况,使用液冷散热前后晶上系统3工作温度和等方面加以对比分析:由于pcb板51通过与顶部结构件2顶部凹槽22内的凸台221固定后,pcb板51翘曲率由0.35%降为0.05%,翘曲高度差仅有0.17mm。而晶上系统3由于使用有机填充物33和cmp工艺,平整度良好,翘曲率仅有0.03%,高度差为0.092mm。从表1还可以看到,使用液冷散热技术后,晶上系统3工作温度下降了30℃。
41.表1本实施例前后对比
对比例:参见表2,金属层与层压板cte差异大等原因导致pcb容易翘曲;参见表3,目前国内外一线pcb制造厂根据层压板材、走线、过孔、铜厚等因素加工的pcb总体翘曲率在0.25%-1%,大尺寸复杂结构的混压板翘曲率>0.5%。
42.表2常见板材参数
表3常见材料热膨胀系数根据表2和表3提供的数据,可以选择cte与金属cte相近的板材可适度改善pcb板的翘曲,但无论是平整度还是翘曲度,pcb板都与晶圆有较大的差距,晶圆可以通过抛光、磨平来保证平整度,而pcb板无法使用相似的工艺进行改善。因此,pcb板与晶圆之间的互连无法参照芯粒与晶圆互连采用的热压键合或者焊料焊接工艺来解决,这已成为sow技术整机集成的关键技术难题。
43.综上所述,本发明实施例提供了一种基于tsv工艺的晶上系统与pcb板的互连结构及其制造方法,不仅可解决大尺寸晶上系统与翘曲pcb板连通问题,还可以解决晶上系统散热问题,从而为晶上系统的供电、调试、信号输入输出提供技术支撑,为更高速率、更大容量的晶上系统的设计与制造提供技术保障。
44.以上所述仅为本发明的优选实施例而已,并不用于限制本发明,对于本领域的技术人员来说,本发明可以有各种更改和变化。凡在本发明的精神和原则之内,所作的任何修改、等同替换、改进等,均应包含在本发明的保护范围之内。
再多了解一些
本文用于企业家、创业者技术爱好者查询,结果仅供参考。