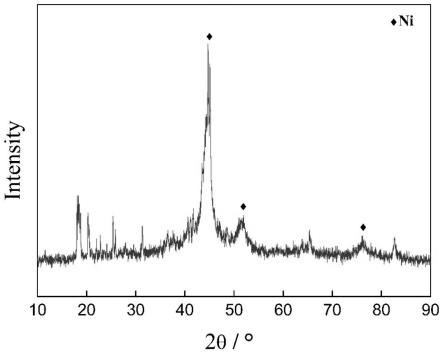
1.本发明属对孟烷制备领域,尤其涉及一种用于制造有机过氧化物引发剂、过氧化氢对孟烷的前体原料及香料中间体和溶剂的对孟烷的工业化制备方法。
背景技术:
2.工业双戊烯是松节油深加工生产樟脑或松油醇过程中的副产物,主要是以苧烯(柠檬烯)、松油烯、异松油烯、莰烯、蒈烯、对伞花烃等为主要成分的液体混合物。其中双戊烯、对伞花烃、异松油烯含量较大且利用价值较高,结构中含有丰富的共轭双键、碳碳双键、环状结构、桥环结构等高反应活性单元,具备发生异构等反应的化学基础。我国年产合成樟脑约占全世界合成樟脑总产量的70%~80%,不同来源的双戊烯总量巨大。目前,国内工业双戊烯的市售价格低廉,多以原料形式出口或作为油污清洗剂、低档油漆的溶剂、废旧橡胶再生以及配制廉价香料的基础原料使用,经济效益有限,使其潜在的价值未能得到充分利用。
3.对孟烷是合成香精香料,医药、化工多种精细化工产品的重要中间体,是石油溶剂的绿色替代品、潜在的合成燃料添加剂、开发抗结核药物的潜在候选药物、可用于萜烯碲化物的合成和过氧化氢对孟烷的合成。
4.目前,对孟烷大多以双戊烯为原料,经加氢催化制得。但传统的双戊烯加氢制备对孟烷的方法,气液体积比大、能耗和物耗高、设备投资和运行成本高,生产量小、效率低,不适合工业化生产。
技术实现要素:
5.本发明旨在克服现有技术的不足之处而提供一种对孟烷的工业化制备方法,其具有设备简单,投资和运行成本低,催化剂效率高,可以解决现有技术生产量小、效率低,不适合工业化生产问题等特点。
6.一种对孟烷的工业化制备方法,依次包括以下步骤:
7.a、将双戊烯与氢气混合,通过加热器预热;
8.b、将预热后的气液混合物送入管式固定床反应器中,在催化剂作用下进行加氢反应;
9.c、通过对反应器进行分段温度控制,使双戊烯中的不同组分连续分梯度进行加氢反应,生成以对孟烷为主的加氢产物。
10.作为一种优选方案,本发明所述双戊烯包括苧烯、松油烯、异松油烯、蒎烯及对伞花烃等中的一种或两种以上的组合。
11.进一步地,本发明所述步骤a中,双戊烯的纯度≥97%。
12.进一步地,本发明所述步骤a中,双戊烯与氢气的体积比为1:1000~1500。
13.进一步地,本发明所述步骤a中,加热器的预热温度为140~150℃。
14.进一步地,本发明所述步骤b中,对选用的镍系催化剂以xrd进行表征,结果表明
xrd图谱与jcpds粉末衍射文件中的参考图谱相似(01-070-1849),催化剂活性组分镍以非晶形式存在于载体的多孔结构中。
15.进一步地,本发明所述步骤b中,对选用的镍系催化剂以sem进行表征,结果表明催化剂呈现不规则的片状结构形态。
16.进一步地,本发明所述步骤b中,对选用的镍系催化剂以bet进行表征,结果表明催化剂的比表面积为52.5m2/g,孔容为0.07cm3/g,孔径为2.7nm,其吸附脱附等温线与经典的iv型吸附脱附等温线类似,具有介孔结构。
17.进一步地,本发明所述步骤c中,加氢反应压力为9~12mpa。
18.进一步地,本发明所述步骤c中,通过对反应器进行分三段温度控制,控制温度依次为:180~200℃、210~230℃、240~260℃。
19.与现有技术相比,本发明具有如下特点:
20.(1)本发明通过对反应温度、反应压力、氢油比等多项因素进行多次单因素对比试验及正交试验考察对孟烷的最优生产工艺。单因素试验中,通过在固定床中装入足量的催化剂,控制进料量20ml/h,反应压力10mpa,氢油比1200: 1的工艺条件下,考察反应温度(160~280℃)对加氢反应的影响。结果表明,随着反应温度的升高,原料的转化率和产品的收率不断升高,当反应温度到 260℃后,原料的转化率和产品的收率基本不变。通过在固定床中装入足量的催化剂,控制进料量20ml/h,反应温度240℃,氢油比1200:1的工艺条件下,考察反应压力(6~14mpa)对加氢反应的影响。结果表明,随着反应压力的升高,原料的转化率和产品的收率不断升高,当反应压力到12mpa后,原料的转化率和产品的收率基本不变。通过在固定床中装入足量的催化剂,控制进料量 20ml/h,反应温度240℃,反应压力10mpa的工艺条件下,考察氢油比(800~1800: 1)对加氢反应的影响。结果表明,随着氢油比的升高,原料的转化率和产品的收率不断升高,当氢油比到1500:1后,原料的转化率和产品的收率基本不变。根据单因素试验结果设计正交试验进一步探究反应条件对反应效果的影响。通过分析不同反应条件下产品的组成,总结发现原料双戊烯中不同组分的反应条件不同。在反应温度180~200℃,反应压力9~12mpa的条件下,原料中的苧烯、松油烯、异松油烯可生成较稳定的对孟烷,反应式如下:
[0021][0022]
随着反应温度的升高,当温度达到210~230℃,反应压力9~12mpa时,原料中的对伞花烃发生反应生成对孟烷,反应式如下:
[0023]
[0024]
当反应温度到达240~260℃,反应压力9~12mpa时,原料中含有的少量桉叶素发生反应生成对孟烷,反应式如下:
[0025][0026]
因此如果固定一个反应条件使所有组分同时发生反应会造成大量的不必要能耗。本发明通过对反应器进行分段温度控制,使原料双戊烯中的不同组分连续分梯度的进行加氢反应生成以对孟烷为主的加氢产物,大大降低了不必要的能耗。
[0027]
(2)传统的制备方法中,连续化制备工艺在同一反应条件下进行制备,未对反应条件分段控制,能耗高、运行成本高。间歇化制备工艺,设备投资成本高、产量小、效率低。本发明制备方法弥补了传统制备方法的不足之处,具有设备简单,投资和运行成本低,催化剂效率高的特点。原料双戊烯转化率可达 99.9%,产品中对孟烷含量大于95%。有效解决了现有技术生产量小、效率低,不适合工业化生产的问题。
附图说明
[0028]
图1为本发明催化剂xrd谱图;
[0029]
图2为本发明催化剂sem照片;
[0030]
图3为本发明催化剂孔径分布图;
[0031]
图4为本发明催化剂吸附脱附等温线;
[0032]
图5为本发明对孟烷制备装置示意图。
具体实施方案
[0033]
以下对本发明的实施例作详细说明:本实施例在以本发明技术方案为前提下进行实施,给出了详细的实施方式和过程,但本发明的保护范围不限于以下的实施例,下列实施例中未注明具体条件的实验方法,通常按照常规条件。
[0034]
实施例1
[0035]
对孟烷的工业化制备方法包含以下步骤:将足量镍系催化剂装入反应器中,缓慢开启氮气入口阀引入氮气使系统压力稳定上升至实验压力,稳压10分钟并用肥皂水检查气密性,无压降无气泡后缓慢开启排气阀将系统压力降至标准大气压,上述过程重复2次后关闭氮气入口阀,缓慢开启氢气入口阀引入氢气使系统压力稳定上升至实验压力。启动进料泵控制原料双戊烯进料量20ml/h,氢气流量20l/h,即双戊烯与氢气的体积比为1:1000,混合后进入加热器预热,预热温度控制在140~150℃,预热后的气液混合物进入反应器进行加氢反应,通过氢气减压阀控制反应压力9~10mpa,对反应器分三段进行温度控制,第一阶段反应温度:180~185℃,第二阶段反应温度:210~215℃,第三阶段反应温度: 240~245℃。反应后所得产物经过冷却器降温后进入气液分离器,分离后得到的液相产品即是以对孟烷为主要成分的目标产物。
[0036]
实施例2
[0037]
将足量镍系催化剂装入反应器中,缓慢开启氮气入口阀引入氮气使系统压力稳定上升至实验压力,稳压10分钟并用肥皂水检查气密性,无压降无气泡后缓慢开启排气阀将系统压力降至标准大气压,上述过程重复2次后关闭氮气入口阀,缓慢开启氢气入口阀引入氢气使系统压力稳定上升至实验压力。启动进料泵控制原料双戊烯进料量30ml/h,氢气流量36l/h,双戊烯与氢气的体积比为1:1200,混合后进入加热器预热,预热温度控制在140~150℃,预热后的气液混合物进入反应器进行加氢反应,通过氢气减压阀控制反应压力10~11mpa,对反应器分三段进行温度控制,第一阶段反应温度:185~190℃,第二阶段反应温度:215~220℃,第三阶段反应温度:245~250℃。反应后所得产物经过冷却器降温后进入气液分离器,分离后得到的液相产品即是以对孟烷为主要成分的目标产物。
[0038]
实施例3
[0039]
将足量镍系催化剂装入反应器中,缓慢开启氮气入口阀引入氮气使系统压力稳定上升至实验压力,稳压10分钟并用肥皂水检查气密性,无压降无气泡后缓慢开启排气阀将系统压力降至标准大气压,上述过程重复2次后关闭氮气入口阀,缓慢开启氢气入口阀引入氢气使系统压力稳定上升至实验压力。启动进料泵控制原料双戊烯进料量40ml/h,氢气流量50l/h,双戊烯与氢气的体积比为1:1250,混合后进入加热器预热,预热温度控制在140~150℃,预热后的气液混合物进入反应器进行加氢反应,通过氢气减压阀控制反应压力11~12mpa,对反应器分三段进行温度控制,第一阶段反应温度:190~195℃,第二阶段反应温度:220~225℃,第三阶段反应温度:250~255℃。反应后所得产物经过冷却器降温后进入气液分离器,分离后得到的液相产品即是以对孟烷为主要成分的目标产物。
[0040]
以上内容仅仅是对本发明结构所作的举例和说明,所属本领域的技术人员不经创造性劳动即对所描述的具体实施例做的修改或补充或采用类似的方式替代仍属本专利的保护范围。
再多了解一些
本文用于企业家、创业者技术爱好者查询,结果仅供参考。