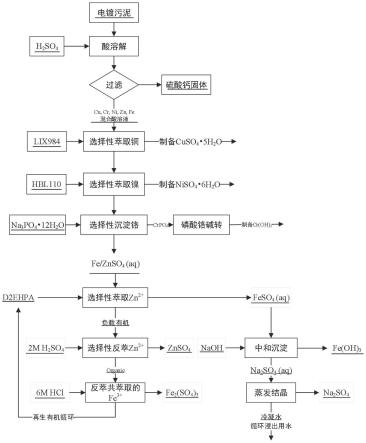
1.本发明涉及金属分离技术领域,具体是一种锌铬铁选择性分离的方法以及一种电镀污泥中多金属回收的方法。
背景技术:
2.电镀是一种常用的金属和塑料表面处理技术,可以提高耐磨性、防腐蚀和装饰美观。然而,电镀行业在预处理和洗涤过程中产生大量的重金属废水。一般情况下,大部分废水通过中和法沉淀,形成电镀污泥。电镀污泥中含有60-80%的水分和相当数量的重金属,如cu(1~2%)、ni(0.5~1%)、zn(1~2%)、cr(2~3%)等。这些重金属通过地下水系统和食物链对人类健康带来致命的潜在威胁,因此电镀污泥被列为危险固废,仅中国每年就生产约1000万吨电镀污泥。在过去,大部分电镀污泥都是在垃圾填埋场进行固化处理,这带来了长期的环境问题和垃圾填埋场空间问题,另外,随着矿石资源的消耗,镍、钴、铜、铬等矿石的枯竭是社会可持续发展面临的另一个重要问题。近年来,随着环保法规的日益严格和可持续生产的发展,电镀污泥的资源利用和无害化处理越来越受到人们的关注。
3.从电镀污泥中回收单一或多种有价金属可以通过火法冶金和湿法冶金过程来实现。火法冶金回收金属作为合金材料,一般是混合金属钢锭,并制备残渣作为建筑材料,资源利用效率低,附加值低。与常规冶金路线相比,湿法冶金在单一工艺中实现了单个金属的提取和分离,对含多种重金属的电镀污泥的回收利用表现出良好的适应性。
4.目前工业上对电镀污泥中重金属回收主要为铜、镍、锌、铬,其中铜采用lix984或m5640(萃取剂)可以做到高选择性回收,而其他金属大都采用沉淀法,因为镍、锌、铬及铁的化合沉淀ph接近,沉淀产物中相互夹带严重,沉淀不完全,且铬以夹带大量锌镍的铬铁渣形式,作为二次危废堆存或委外处理,产品纯度不高。整体资源化利用率(或单一金属回收率)低,产品附加值不高、产生大量二次危废。
5.江西理工大学徐志峰提出了磷酸盐沉淀铬并用氢氧化钠转型为氢氧化铬的工艺,但该工艺存在磷酸盐与氢氧化钠无法循环并产生含铬的钠盐废水;同时其他金属采用(除了铜外)沉淀法生产粗制产品,存在与传统工艺相同的问题。
技术实现要素:
6.本发明的目的是提供一种铬铁选择性分离的方法以及一种电镀污泥中多金属回收的方法,旨在解决现有电镀污泥中有价金属难以得到有效回收且易产生废水的缺陷。
7.为实现上述目的,本发明提出的一种锌铬铁选择性分离的方法包括以下步骤:
8.(1)在含锌铬铁的溶液中,加入还原剂进行预处理并调整溶液ph值;
9.(2)向步骤(1)中溶液加入可溶性磷酸盐搅拌,进行选择性沉铬反应;
10.(3)过滤分离,得到磷酸铬滤渣和含铁锌滤液,滤渣用稀酸洗涤,以将夹带的铁和氢氧化铬洗掉;
11.(4)在高温下用浓碱浸出洗后的滤渣,得到氢氧化铬固体和浸出液;
12.(5)将浸出液冷却,得到可溶性磷酸盐沉淀,过滤后,磷酸盐晶体可返回步骤(2)用于选择性沉铬,滤液浓缩后返回步骤(4)用于磷酸铬沉淀转型过程。
13.优选地,所述含铬铁的溶液中,铬离子含量为0.1-30g/l,铁离子含量为0.1-20g/l,锌离子含量为0.1~10g/l。
14.优选地,所述的加入还原剂进行预处理过程,是加入硫代硫酸钠或亚硫酸钠或fe粉中的至少一种进行还原预处理,使得溶液中的铬、铁离子分别保持在cr
3
、fe
2
状态。
15.优选地,所述步骤(1)中,溶液ph值范围为0.5-2.5。
16.优选地,所述步骤(2)中添加的可溶性磷酸盐的量以磷酸根计,磷酸根与铬离子摩尔比为0.8-1.5;沉铬反应温度为60-90℃,反应时间为30-120min。
17.优选地,所述步骤(2)为向步骤(1)处理后的溶液加入磷酸铬固体,再加入可溶性磷酸盐搅拌,进行选择性沉铬反应。
18.优选地,所述步骤(3)中稀酸的ph范围为0.5-2;所述的稀酸洗涤的反应温度控制为60-90℃,反应时间为30-120min,液固比为1:1-5:1。
19.优选地,所述步骤(4)中的浓碱为naoh溶液,且naoh的浓度为100g/l-250g/l;所述的浓碱浸出洗后的滤渣过程中,温度控制为60-90℃,时间为30-120min,液固比为2:1-10:1。
20.为实现上述目的,本发明提出的一种电镀污泥中铜、镍、铬、锌、铁多金属资源化回收的方法包括以下步骤:
21.a.采用稀硫酸浸出电镀污泥,获得硫酸钙固体和含镍、锌、铜、铬、铁的浸出液;
22.b.采用特效萃取剂对步骤a中浸出液中的铜进行萃取、洗涤、反萃取,得到硫酸铜溶液和含镍、锌、铬、铁的萃余液,其中,所述特效萃取剂包括lix984或m5640;
23.c.用特效萃取剂hbl110对步骤b中萃余液中的镍进行皂化、萃取、洗涤、反萃取,得到硫酸镍溶液和含锌、铬、铁的萃余液;
24.d.采用如权利要求1-8任一项所述的方法处理含锌、铬、铁的萃余液;
25.e.将步骤d处理得到的含铁滤液,采用酸性磷类萃取剂萃取锌,通过皂化、萃取、洗涤、分步反萃得到硫酸锌富集溶液和硫酸亚铁萃余液;
26.f.将步骤e得到的硫酸亚铁萃余液采用氢氧化钠中和沉淀,得到氢氧化铁沉淀和硫酸钠母液。
27.优选地,所述步骤e中分步反萃时采用的是:大于0.5mol/l的稀硫酸反萃锌、6mol/l盐酸反萃少量共萃的铁。
28.本发明中铬铁分离的技术构思如下:
29.首先利用cr
3
、fe
2
的磷酸盐溶解度差异,实现铬和铁的选择性沉淀分离。随着ph的升高,金属水解的顺序为fe(iii)》cu(ii)≈cr(iii)》zn(ii)≈fe(ii)》ni(ii),说明铁(iii)较其他金属离子优先水解,可以从cr(iii)中分离出来。但实际中,在铁(iii)水解过程中,约30%的cr(iii)与fe(iii)共沉淀,导致fe(iii)与cr(iii)分离不理想。研究发现,在ph值1.0-5.0范围内,金属磷酸盐的析出顺序为cr(iii)》fe(iii)》fe(ii)》ni(ii)》cu(ii)》zn(ii),进一步增大ph会导致金属磷酸盐转化为相应的羟基。fe(iii)、cu(ii)、zn(ii)、ni(ii)、cr(iii)和fe(ii)的转换ph值分别为5.0、8.0、9.5、10.0、10.2和10.5。这说明采用磷酸盐沉淀法可以从浸出液中分离出镍、锌、铜和铁、铬。磷酸铬沉淀可被氢氧化钠分
解形成氢氧化铬,磷酸盐沉淀物可再生利用。
30.与现有技术相比,本发明的有益技术效果为:
31.1、采用自主合成的镍特效萃取剂hbl-110(具体请参照cn103421952a)及自主研发的直接萃镍新工艺,实现了酸性条件下镍的选择性萃取富集及与铁、铬、锌的深度分离,为整个工艺实现提供了保证;
32.2、采用磷酸盐沉淀铬-氢氧化钠转型-磷酸钠低温析出-碱循环实现了磷酸钠和氢氧化钠的闭路循环,消除了铬重金属废水,并大幅降低了试剂消耗,且全流程无重金属废水产生;
33.3、采用电位还原,选择性萃取锌-分步反萃分离锌铁,实现锌的高选择性回收;
34.4、整个流程实现了电镀污泥有价金属铜、镍、铬、锌的产品化高值利用,相较于电镀污泥传统处理工艺,废渣量大幅度降低,废水近零排放,是一典型的低成本清洁高效节能减排生产工艺。
附图说明
35.图1为本发明提出的锌铬铁选择性分离的方法一实施例的流程图;
36.图2为本发明提出的电镀污泥中铜、镍、铬、锌、铁多金属资源化回收的方法一实施例的流程图。
具体实施方式
37.下面将对本发明实施例中的技术方案进行清楚、完整地描述,显然,所描述的实施例仅是本发明一部分实施例,而不是全部实施例,基于本发明中的实施例,本领域普通技术人员在没有做出创造性劳动前提下所获得的所有其他实施例,都属于本发明保护的范围。
38.实施例1
39.请参照图1,料液为实验室配制的铁、铬、锌硫酸盐溶液:料液中含cr4.9g/l,fe 2.0g/l,zn 1.6g/l。还原剂选择亚硫酸钠,按铁、铬完全还原所需反应理论量的1.5倍加入亚硫酸钠,用硫酸调节ph至2.0,按磷酸根与铬离子摩尔比1.1加入磷酸钠,在90℃下保温搅拌60min,过滤得到磷酸铬粗沉淀,滤液中铬、铁、锌浓度分别为0.07g/l、1.67g/l、1.57g/l,沉铬率为98.59%,沉铁率为19.21%,沉锌率为1.21%。滤渣即为除铬渣,滤液为除铬后液。
40.取新鲜除铬渣5g,用ph=1的硫酸洗水洗涤,液固比为2:1,向滤液中加入1g亚硫酸钠,在90℃条件下保温搅拌60min,过滤,滤液返回磷酸盐沉铬步骤,滤液中含铬、铁、锌分别为0.47g/l、0.48g/l、0.1g/l。滤渣为磷酸铬洗涤渣。
41.取洗涤渣5g,用200g/l的naoh溶液按液固比5:1在90℃下保温搅拌60min,过滤,滤液中含铁、铬、锌、磷分别为0.02g/l、0.03g/l、0.1g/l、1.5g/l,碱度为3.65mol/l,滤渣即为氢氧化铬转型渣,将滤液冷却至常温,析出大量磷酸钠晶体,可返回作为除铬沉淀剂,滤液在补充消耗的碱之后可返回将磷酸铬洗涤渣转型为氢氧化铬渣。
42.实施例2
43.溶液配制:
44.在酸性条件下配制cr
3
/fe
2
/zn
2
混合溶液([cr
3
]
初始
=5.00g/l,[fe
2
]
初始
=3.15g/l,[zn
2
]
初始
=2.78g/l);
[0045]
配制一定体积的十二水磷酸钠溶液;配制一定体积的氢氧化钠溶液(4.5mol/l)。
[0046]
铬铁锌溶液预处理:
[0047]
加入少量亚硫酸钠还原预处理铬铁锌溶液,以保证溶液中的铁全部以fe
2
形式存在。
[0048]
沉淀实验(常压):
[0049]
量筒量取铬铁混合溶液0.5l,滴加一两滴混合溶液于5%的硫氰酸钾溶液中,检测有无fe
3
存在(若有红色,则加入少量亚硫酸钠还原),若无,滴加硫酸调整溶液ph=2.0(ph计测定);取实验前液样,烧杯杯口采用保鲜膜密封;不开磁力搅拌,水浴升温至80℃(用水银温度计校准);开启磁力搅拌,设置转速500rpm,按po
43-/cr
3
摩尔比1.1的量缓慢滴入磷酸钠溶液;加样中滴加少量硫酸控制溶液ph小于3.0,加样完毕后,反应30min;停止搅拌,继续保温30min;真空过滤,滤饼加少量酸水(ph=2.0)漂洗,测量混合滤液体积,混合均匀后测定滤液ph及取样;将沉淀物用适量酸水(ph=1.0)在常温下进行磁力搅拌(500rpm)洗涤1h;过滤,滤饼加少量酸水(ph=2.0)漂洗,测量混合滤液体积,混合均匀后测定滤液ph及取样;将滤饼放入烘箱烘干,称重,取样分解后送icp检测。
[0050]
沉淀对照实验(加入磷酸铬晶种):
[0051]
其它部分同沉淀实验的步骤,改变以下条件:按po
43-/cr
3
摩尔比1.1的量计算,先加入5%(按理论生成磷酸铬量)磷酸铬固体,再滴入当量的磷酸钠溶液。表1显示了加晶种与否对磷酸盐沉淀铬铁实验的影响。
[0052]
分解实验:
[0053]
制备一定量的酸洗后磷酸铬固体(干基),按l/s=5:1的比例加入一定量的氢氧化钠溶液(4.5mol/l);水浴升温至80℃(用酒精温度计校准);开启磁力搅拌(500rpm),反应60min;真空过滤,加入适量纯水漂洗,计算混合滤液体积,混合均匀后取样;将转型后的沉淀物加入适量纯水在t=80℃条件下搅拌洗涤30min;过滤,计算滤液体积,加入适量纯水漂洗,计算混合滤液体积,混合均匀后取样;滤饼烘干称重,取样分解送icp检测。表2显示了金属沉淀率及碱转元素浸出率。
[0054]
磷酸盐沉淀实验中,加入磷酸铬晶种可降低铁的沉淀率,同时增加铬的沉淀率,也即沉淀后液中铬含量降低。
[0055]
表1
[0056][0057]
磷酸盐沉淀实验中,通过控制反应过程ph,可使铬的沉淀率达到98.0%以上,同时控制铁的沉淀率在5.0%以内。磷酸盐转型实验中,通过控制液碱和沉淀物的液固比,可使磷的浸出率达到90.0%以上,而铬几乎不被浸出。
[0058]
表2
[0059][0060]
实施例3
[0061]
请参照图2,将电镀污泥用硫酸溶解,得到硫酸钙固体和浸出液,其中浸出液为cu、cr、ni、zn、fe混合酸溶液([cu
2
]
初始
=1.03g/l,[ni
2
]
初始
=2.04g/l,[cr
3
]
初始
=5.00g/l,[fe
2
]
初始
=3.15g/l,[zn
2
]
初始
=2.78g/l))。
[0062]
在浸出液中,采用萃取剂lix984选择性萃取铜,将萃取铜后的有机相采用硫酸反萃得到硫酸铜。
[0063]
在萃取铜后的萃余相中,采用萃取剂hbl110选择性萃取镍,将萃取镍后的有机相采用硫酸反萃得到硫酸镍。
[0064]
向萃取镍后的萃余相中加入磷酸钠搅拌,过滤分离后得到磷酸铬滤渣和含铁滤液,滤渣用稀酸洗涤,以将夹带的铁和氢氧化铬洗掉。在高温下用浓碱浸出洗后的滤渣,得到氢氧化铬固体和浸出液。将浸出液冷却,得到可溶性磷酸盐沉淀,过滤后,磷酸盐沉淀循环用于选择性沉铬,滤液浓缩后循环用于磷酸铬沉淀转型过程。
[0065]
将含铁滤液采用萃取剂d2ehpa萃取剂选择性萃取锌,通过皂化、萃取、洗涤、分步反萃得到硫酸锌富集溶液和硫酸亚铁萃余液,其中,分步反萃时采用的是:0.6mol/l硫酸反萃锌、6mol/l盐酸反萃少量共萃的铁。
[0066]
将硫酸亚铁萃余液采用氢氧化钠中和沉淀,得到氢氧化铁沉淀和硫酸钠母液,硫酸钠母液蒸发后得到硫酸钠晶体和冷凝水,冷凝水用于配置硫酸来溶解电镀污泥。
[0067]
表3
[0068][0069]
注:各工序萃取/沉淀率以该工序产品中金属含量除以原料液中该金属的总含量
[0070]
以上所述仅是本发明的优选实施方式,本发明的保护范围并不仅局限于上述实施例。对于本技术领域的技术人员来说,在不脱离本发明技术构思前提下所得到的改进和变换也应视为本发明的保护范围。
再多了解一些
本文用于企业家、创业者技术爱好者查询,结果仅供参考。