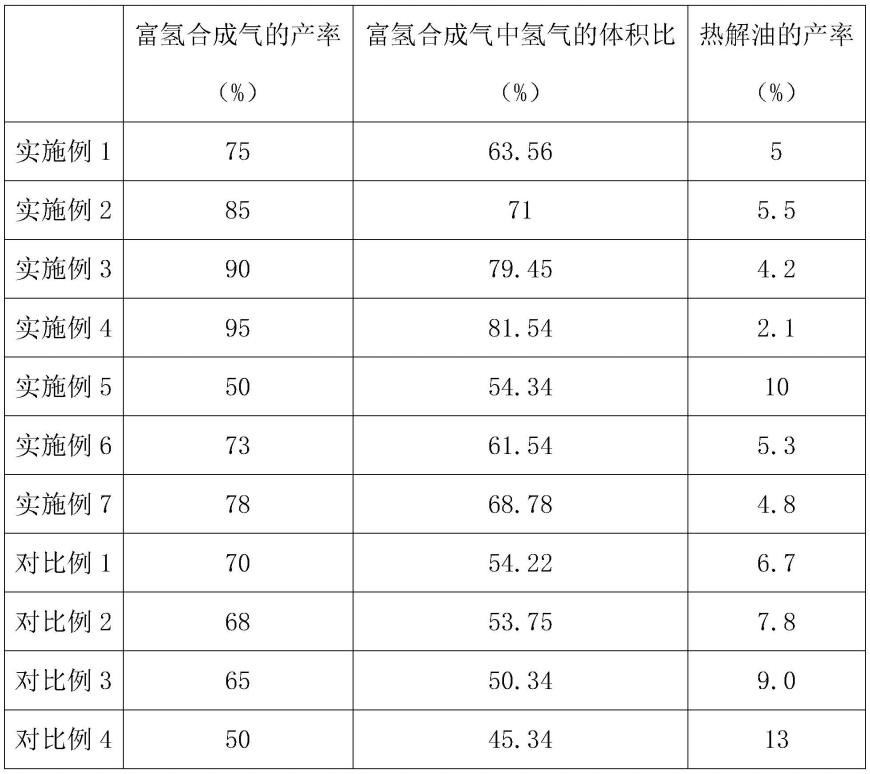
一种ca-ni灰基催化剂、富氢合成气的制备方法
技术领域
1.本发明属于固体废物资源化技术领域,具体涉及一种ca-ni灰基催化剂、富氢合成气的制备方法。
背景技术:
2.污泥是由水和污水处理过程所产生的固体沉淀物质,污泥中含有大量有机物、致病菌、重金属和无机物等,如何使污泥得到有效安全的处理处置,同时实现污泥中有机物的有效资源化和能源化转化成为污泥处置工艺的主要发展方向。其中气化技术作为实现污泥稳定化和资源化有效的处理工艺之一,因其具有能量回收,污泥减量无害化,处理周期短等特点具有较大的发展潜力。但是,常规气化过程中不可避免的产生焦油等副产物,不仅降低了气化转化效率,同时由于焦油具有黏度大,含水率高特点,严重影响了气化设备的稳定运行。另一方面,常规的污泥气化系统中,污泥热干化单元的能量消耗占整体系统的80%左右。因此,如何通过高效低耗的方式实现污泥深度脱水取代污泥干化单元,同时提高污泥的气化效率降低焦油产量成为该技术推广应用的主要技术瓶颈。
3.水热技术作为重要的污泥脱水调理技术,其处理过程中水分不发生相态的转化,使其能耗显著低于热干化工艺。现有技术中公开了一种基于水热前处理的污泥高效能源化处理方法,包括以下步骤,步骤一,在污泥中加入铁基调理剂进行水热处理,步骤二,得到的气体进行热解处理,步骤三,热解处理后的气体进行厌氧消化处理,得到沼气。
4.但是现有技术中公开的污泥处理方法,热解处理后的固相并没有进行有效处理。
技术实现要素:
5.因此,本发明要解决的技术问题在于克服现有技术中热解处理后固相并没有进行有效处理的缺陷,从而提供一种ca-ni灰基催化剂、富氢合成气的制备方法。
6.为此,本发明提供了以下技术方案,
7.本发明提供了一种ca-ni灰基催化材料的制备方法,包括以下步骤,
8.将污泥在60-160℃的条件下水热处理5-60min,然后加入调理剂混合后进行脱水,再加入镍盐混合、研磨粉碎后热解处理,热解得到的固相为ca-ni灰基催化材料。
9.可选的,所述调理剂为单宁酸和钙基调理剂。
10.可选的,所述钙基调理剂包括氧化钙、氢氧化钙、碳酸钙中的一种或多种;
11.和/或,所述单宁酸和钙基调理剂的质量比为(1-2):(1-2)。
12.可选的,所述污泥包括初沉污泥、剩余污泥、浓缩污泥、脱水污泥、消化污泥中的一种或多种;
13.和/或,所述污泥的含固量为1%-25%。
14.可选的,当水热处理的温度为60-120℃时,所述水热处理的压力为0.02-0.2mpa;
15.和/或,所述调理剂的添加量,以污泥干重为基准,为0.1-0.4g/g。
16.可选的,当水热处理的温度为120-160℃时,所述水热处理的压力为0.2-0.65mpa;
捕获剂促进水煤气反应的正向进行。
40.2.本发明采用单宁酸作为水热处理过程的调理剂。单宁酸由于其独特的结构特征,与污泥中的亲水性蛋白发生结合,使其固定在固相产物中,不仅大大改善了水热后污泥的脱水性能,同时显著降低了滤液中含氮污染物的浓度,降低了脱水后滤液的处理难度和成本。对于水热后产生的脱水污泥,单宁酸的添加显著提高了固相产物中含氮有机物的稳定性,减少气化过程含氮污染物的产量。
41.3.本发明采用水热处理工艺,污泥经过水热处理后,污泥絮体结构被破坏,结合水向自由水转化,污泥中的有机物发生溶出,水解等反应实现了分质重整。作为污泥气化的预处理工艺,从根本上改变了污泥中有机物气化过程中的反应途径,实现了富氢气体的制备。与此同时,本发明采用的水热条件较温和,避免了由于美拉德等缩聚反应产生的难降解有机物,降低了污泥脱水后滤液的处理难度和成本。
42.4.本发明根据不同水热条件有机物的聚合度以及空间结构的不同,采用不同的投加方式,实现污泥中亲水性蛋白类物质的有效固定和稳定化调理。
43.5.本发明还提供了一种富氢合成气的制备方法,包括以下步骤,将污泥在60-160℃的条件下水热处理5-60min,然后加入调理剂混合后进行脱水,再加入镍盐混合、研磨粉碎后热解处理,热解得到的焦油及气相产物加入上述制备方法制备出的ca-ni灰基催化剂进行水蒸气气化处理,气化后得到富氢合成气。本发明采用ca-ni灰基催化剂进行水蒸气气化处理,该种催化剂中含有大量分散度较高,催化活性较强的ni以及cao,对焦油进行催化重整,促进了焦油中c-o和c-n键的断裂,提高焦油的气化转化效率,实现了气化制备富氢气体的定向转化。
44.6.本发明污泥气化反应条件选择700-1000℃,避免了气化温度过高,污泥中的活性金属在颗粒内部扩散和烧结,降低气化后催化剂的催化活性。实现了富氢清洁气体燃料和催化剂的同时制备。
具体实施方式
45.提供下述实施例是为了更好地进一步理解本发明,并不局限于所述最佳实施方式,不对本发明的内容和保护范围构成限制,任何人在本发明的启示下或是将本发明与其他现有技术的特征进行组合而得出的任何与本发明相同或相近似的产品,均落在本发明的保护范围之内。
46.实施例中未注明具体实验步骤或条件者,按照本领域内的文献所描述的常规实验步骤的操作或条件即可进行。所用试剂或仪器未注明生产厂商者,均为可以通过市购获得的常规试剂产品。
47.实施例1
48.本实施例提供了一种ca-ni灰基催化剂的制备方法,
49.将80kg含固率为10%的脱水污泥放入有效容积为100l的水热反应釜内胆中,设定温度为160℃,压力为0.65mpa,达到设定温度后维持30min,水蒸气回收并用于预热储泥罐污泥,污泥冷却后,向其中添加单宁酸调理剂0.05g/g(ts),充分搅拌1min,静置20min。再向污泥中添加cao调理剂0.05g/g(ts),单宁酸与cao调理剂质量比为1:1,搅拌混合并进行框压滤脱水,脱水后污泥含固率降至20%。产生的湿泥饼与3%的硝酸镍进行研磨破碎成粒径
为0.15-1.05mm的颗粒,随后进入热解系统进行转化,热解温度为600℃,热解时间为30min。热解产生的固相即为ca-ni灰基催化剂。
50.本实施例还提供了一种富氢合成气的制备方法,
51.上述热解产生的焦油及其他产物进入气化系统中进行气化,其气化温度为800℃,ca-ni灰基催化剂的添加量为50%(ts),水碳比为2.2:1,气化时间为15min。即得到了富氢合成气和热解油。
52.实施例2
53.本实施例提供了一种ca-ni灰基催化剂的制备方法,
54.将400kg含固率为5%的浓缩污泥放入水热反应釜内胆中,,同时添加单宁酸调理剂0.3g/g(ts),搅拌均匀,设定温度为120℃,压力为0.2mpa,达到设定温度后维持30min,水蒸气回收并用于预热储泥罐污泥,污泥冷却后,向其中caco3调理剂0.15g/g(ts),单宁酸与cao调理剂质量比为2:1,搅拌混合并进行框压滤脱水,脱水后污泥含固率降至40%。产生的湿泥饼与4%(ts)的硝酸镍进行研磨破碎成粒径为0.21-1.54mm的颗粒,随后进入热解系统进行转化,热解温度为500℃,热解时间为60min。热解产生的固相即为ca-ni灰基催化剂。
55.本实施例还提供了一种富氢合成气的制备方法,
56.上述热解产生的焦油及其他产物进入气化系统中进行气化,其热解温度为700℃,ca-ni灰基催化剂的添加量为70%(ts),水碳比为1.7:1,气化时间为30min。即得到了富氢合成气和热解油。
57.实施例3
58.本实施例提供了一种ca-ni灰基催化剂的制备方法,
59.将320kg含固率为8%的市政污泥放入水热反应釜内胆中,设定温度为140℃,压力为0.36mpa,达到设定温度后维持45min,水蒸气回收并用于预热储泥罐污泥,污泥冷却后,其中添加单宁酸调理剂0.2g/g(ts),充分搅拌2min,静置15min。再向污泥中添加ca(oh)2调理剂0.15g/g(ts),单宁酸与cao调理剂质量比为4:3,搅拌混合并进行框压滤脱水,脱水后污泥含固率降至35%。产生的湿泥饼与5.5%(ts)的硝酸镍进行研磨破碎成粒径为0.12-1.21mm的颗粒,随后进入热解系统进行转化,热解温度为600℃,热解时间为90min。热解产生的固相即为ca-ni灰基催化剂。
60.本实施例还提供了一种富氢合成气的制备方法,
61.上述热解产生的焦油及其他产物进入气化系统中进行气化,其热解温度为900℃,ca-ni灰基催化剂的添加量为90%(ts),水碳比为1.9:1,气化时间为45min。即得到了富氢合成气和热解油。
62.实施例4(跟实施例1相比,采用数据的端点值)
63.本实施例提供了一种ca-ni灰基催化剂的制备方法,
64.将300kg含固率为1%的浓缩污泥放入有效容积为100l的水热反应釜内胆中,设定温度为160℃,压力为0.65mpa,达到设定温度后维持5min,水蒸气回收并用于预热储泥罐污泥,污泥冷却后,向其中添加单宁酸调理剂0.05g/g(ts),充分搅拌2min,静置15min。再向污泥中添加cao调理剂0.1g/g(ts),单宁酸与cao调理剂质量比为1:2,搅拌混合并进行框压滤脱水,脱水后污泥含固率降至20%。产生的湿泥饼与3%的硝酸镍进行研磨破碎成粒径为0.15-1.05mm的颗粒,随后进入热解系统进行转化,热解温度为600℃,热解时间为90min。热
解产生的固相即为ca-ni灰基催化剂。
65.本实施例还提供了一种富氢合成气的制备方法,
66.上述热解产生的焦油及其他产物进入气化系统中进行气化,其气化温度为1000℃,ca-ni灰基催化剂的添加量为100%(ts),水碳比为2:1,气化时间为60min。即得到了富氢合成气和热解油。
67.实施例5(跟实施例1相比,采用数据的另一端点值)
68.本实施例提供了一种ca-ni灰基催化剂的制备方法,
69.将70kg含固率为25%的脱水污泥放入有效容积为100l的水热反应釜内胆中,设定温度为60℃,压力为0.02mpa,达到设定温度后维持15min,水蒸气回收并用于预热储泥罐污泥,污泥冷却后,向其中添加单宁酸调理剂0.4g/g(ts),充分搅拌2min,静置15min。再向污泥中添加cao调理剂0.4g/g(ts),单宁酸与cao调理剂质量比为1:1,搅拌混合并进行框压滤脱水,脱水后污泥含固率降至50%。产生的湿泥饼与7%的硝酸镍进行研磨破碎成粒径为0.15-1.05mm的颗粒,随后进入热解系统进行转化,热解温度为400℃,热解时间为90min。热解产生的固相即为ca-ni灰基催化剂。
70.本实施例还提供了一种富氢合成气的制备方法,
71.上述热解产生的焦油及其他产物进入气化系统中进行气化,其气化温度为700℃,ca-ni灰基催化剂的添加量为100%(ts),水碳比为3:1,气化时间为15min。即得到了富氢合成气和热解油。
72.实施例6(跟实施例1相比,采用不同的物质)
73.本实施例提供了一种ca-ni灰基催化剂的制备方法,
74.将80kg含固率为10%的消化污泥放入有效容积为100l的水热反应釜内胆中,设定温度为160℃,压力为0.65mpa,达到设定温度后维持30min,水蒸气回收并用于预热储泥罐污泥,污泥冷却后,向其中添加单宁酸调理剂0.05g/g(ts),充分搅拌1min,静置20min。再向污泥中添加碳酸钙调理剂0.05g/g(ts),单宁酸与碳酸钙调理剂质量比为1:1,搅拌混合并进行框压滤脱水,脱水后污泥含固率降至20%。产生的湿泥饼与3%的氯化镍进行研磨破碎成粒径为0.15-1.05mm的颗粒,随后进入热解系统进行转化,热解温度为600℃,热解时间为30min。热解产生的固相即为ca-ni灰基催化剂。
75.本实施例还提供了一种富氢合成气的制备方法,
76.上述热解产生的焦油及其他产物进入气化系统中进行气化,其气化温度为800℃,ca-ni灰基催化剂的添加量为50%(ts),水碳比为2.2:1,气化时间为15min。即得到了富氢合成气和热解油。
77.实施例7(跟实施例1相比,采用不同的物质)
78.本实施例提供了一种ca-ni灰基催化剂的制备方法,
79.将80kg含固率为10%的剩余污泥放入有效容积为100l的水热反应釜内胆中,设定温度为160℃,压力为0.65mpa,达到设定温度后维持30min,水蒸气回收并用于预热储泥罐污泥,污泥冷却后,向其中添加单宁酸调理剂0.05g/g(ts),充分搅拌1min,静置20min。再向污泥中添加氢氧化钙调理剂0.05g/g(ts),单宁酸与氢氧化钙调理剂质量比为1:1,搅拌混合并进行框压滤脱水,脱水后污泥含固率降至20%。产生的湿泥饼与3%的氯化镍进行研磨破碎成粒径为0.15-1.05mm的颗粒,随后进入热解系统进行转化,热解温度为600℃,热解时
间为30min。热解产生的固相即为ca-ni灰基催化剂。
80.本实施例还提供了一种富氢合成气的制备方法,
81.上述热解产生的焦油及其他产物进入气化系统中进行气化,其气化温度为800℃,ca-ni灰基催化剂的添加量为50%(ts),水碳比为2.2:1,气化时间为15min。即得到了富氢合成气和热解油。
82.对比例1(跟实施例1相比,加入别的调理剂)
83.本实施例提供了一种ca-ni灰基催化剂的制备方法,
84.将80kg含固率为10%的脱水污泥放入有效容积为100l的水热反应釜内胆中,设定温度为160℃,压力为0.65mpa,达到设定温度后维持30min,水蒸气回收并用于预热储泥罐污泥,污泥冷却后,向其中添加pam调理剂0.05g/g(ts),充分搅拌1min,静置20min。再向污泥中添加碳酸钙调理剂0.05g/g(ts),单宁酸与碳酸钙调理剂质量比为1:1,搅拌混合并进行框压滤脱水,脱水后污泥含固率降至30%。产生的湿泥饼与3%的硝酸镍进行研磨破碎成粒径为0.15-1.05mm的颗粒,随后进入热解系统进行转化,热解温度为600℃,热解时间为30min。热解产生的固相即为ca-ni灰基催化剂。
85.本实施例还提供了一种富氢合成气的制备方法,
86.上述热解产生的焦油及其他产物进入气化系统中进行气化,其气化温度为800℃,ca-ni灰基催化剂的添加量为50%(ts),水碳比为2.2:1,气化时间为15min。即得到了富氢合成气和热解油。
87.对比例2(跟实施例1相比,不加入单宁酸)
88.本实施例提供了一种ca-ni灰基催化剂的制备方法,
89.将80kg含固率为10%的脱水污泥放入有效容积为100l的水热反应釜内胆中,设定温度为160℃,压力为0.65mpa,达到设定温度后维持30min,水蒸气回收并用于预热储泥罐污泥,污泥冷却后,向污泥中添加cao调理剂0.05g/g(ts),单宁酸与cao调理剂质量比为1:1,搅拌混合并进行框压滤脱水,脱水后污泥含固率降至60%。产生的湿泥饼与3%的硝酸镍进行研磨破碎成粒径为0.15-1.05mm的颗粒,随后进入热解系统进行转化,热解温度为600℃,热解时间为30min。热解产生的固相即为ca-ni灰基催化剂。
90.本实施例还提供了一种富氢合成气的制备方法,
91.上述热解产生的焦油及其他产物进入气化系统中进行气化,其气化温度为800℃,ca-ni灰基催化剂的添加量为50%(ts),水碳比为2.2:1,气化时间为15min。即得到了富氢合成气和热解油。
92.对比例3(跟实施例1相比,水热温度不在范围内)
93.本实施例提供了一种ca-ni灰基催化剂的制备方法,
94.将80kg含固率为10%的脱水污泥放入有效容积为100l的水热反应釜内胆中,设定温度为40℃,压力为0.01mpa,达到设定温度后维持30min,水蒸气回收并用于预热储泥罐污泥,污泥冷却后,向其中添加单宁酸调理剂0.05g/g(ts),充分搅拌1min,静置20min。再向污泥中添加cao调理剂0.05g/g(ts),单宁酸与cao调理剂质量比为1:1,搅拌混合并进行框压滤脱水,脱水后污泥含固率降至60%。产生的湿泥饼与3%的硝酸镍进行研磨破碎成粒径为0.15-1.05mm的颗粒,随后进入热解系统进行转化,热解温度为600℃,热解时间为30min。热解产生的固相即为ca-ni灰基催化剂。
95.本实施例还提供了一种富氢合成气的制备方法,
96.上述热解产生的焦油及其他产物进入气化系统中进行气化,其气化温度为800℃,ca-ni灰基催化剂的添加量为50%(ts),水碳比为2.2:1,气化时间为15min。即得到了富氢合成气和热解油。
97.对比例4(跟实施例1相比,制备富氢合成气时,不加入ca-ni灰基催化剂)
98.本实施例提供了一种ca-ni灰基催化剂的制备方法,
99.将80kg含固率为10%的脱水污泥放入有效容积为100l的水热反应釜内胆中,设定温度为160℃,压力为0.65mpa,达到设定温度后维持30min,水蒸气回收并用于预热储泥罐污泥,污泥冷却后,向其中添加单宁酸调理剂0.05g/g(ts),充分搅拌1min,静置20min。再向污泥中添加cao调理剂0.05g/g(ts),单宁酸与cao调理剂质量比为1:1,搅拌混合并进行框压滤脱水,脱水后污泥含固率降至20%。产生的湿泥饼与3%的硝酸镍进行研磨破碎成粒径为0.15-1.05mm的颗粒,随后进入热解系统进行转化,热解温度为600℃,热解时间为30min。热解产生的固相即为ca-ni灰基催化剂。
100.本实施例还提供了一种富氢合成气的制备方法,
101.上述热解产生的焦油及其他产物进入气化系统中进行气化,其气化温度为800℃,气化时间为15min。即得到了富氢合成气和热解油。
102.测试例
103.对实施例1-7和对比例1-4中制备出的富氢合成气和热解油进行测试。
104.富氢合成气的产率测试方法为:采用气相色谱法进行测试;
105.富氢合成气中氢气的体积比测试方法为:采用气相色谱法进行测试;
106.热解油的产率测试方法为:采用二氯化碳收集并通过溶剂蒸发称重法进行测试。
107.测试结果如下:
[0108][0109]
通过上述表格可以看出,水热处理与单宁酸的耦合有效的提高了污泥的脱水性能,实现了污泥的深度脱水。同时单宁酸的具有较强的螯合作用,通过提高镍盐固相产物中的分散度,从而有提高ca-ni灰基催化剂的催化性能,促进焦油催化重整阶段的转化效率。不同的钙基调理均可以做作为co2的捕获剂促进水煤气反应的正向进行,进而实现污泥热解的定向制氢转化过程。通过实施例充分证明了本专利中所采用的调理剂以及过程参数的必要性,合理性和先进性。
[0110]
显然,上述实施例仅仅是为清楚地说明所作的举例,而并非对实施方式的限定。对于所属领域的普通技术人员来说,在上述说明的基础上还可以做出其它不同形式的变化或变动。这里无需也无法对所有的实施方式予以穷举。而由此所引伸出的显而易见的变化或变动仍处于本发明创造的保护范围之中。
再多了解一些
本文用于企业家、创业者技术爱好者查询,结果仅供参考。