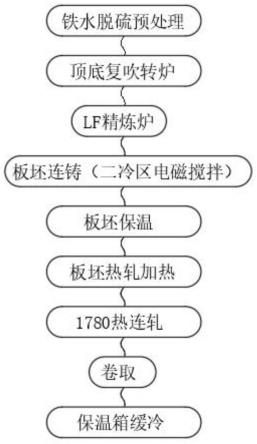
1.本发明属于弹簧钢生产技术领域,具体是一种高碳弹簧钢热轧卷板制备方法。
背景技术:
2.弹簧钢广泛应用于汽车、机械等领域,其中62si2mn是我国使用最为广泛的弹簧钢品种之一,占弹簧钢总量的约70%,市场容量较大。
3.根据现有申请的专利:一种低成本60sizmn弹簧钢及其生产工艺(专利申请号为201410473996.8)”报道,其组分及重量百分比:c:0.58%-%0.62%,si:1.70%%-1.80%,mn:0.80%-0.90%,cr:≤0.35%,ni:≤0.35%,cu:≤0.20%,还包括如下重量百分比s:≤0.030%,p:≤0.030%,剩余的为fe和一些其它微量残余元素;上述低成本60si2mn弹簧钢的生产工艺步骤是:转炉冶炼—炉外精炼—连铸—加热轧制—冷却定尺;该生产为方坯连铸;
4.根据“一种用于制造单片或少片变截面板簧的超高强度弹簧钢及其制备方法(专利申请号为201810198677.9)”报道,其化学成分按重量百分比为c:0.48-0.54%;si:0.8-1.2%;mn:0.7-1.0%;cr:0.8-1.1%;v:0.08-0.15%;nb:0.02-0.05%;此外还有其它元素,其成分设计中含有nb、v等合金元素,不利于降低弹簧钢的成本。
5.根据“一种高碳弹簧用热轧卷板及其生产方法(专利申请号201910212256.1)”报道,其所述的方法采用rh真空精炼、直装方式生产工序复杂、对生产节奏要求高;热轧卷取及后处理工艺能否解决扁卷问题未见说明;在热轧卷取后采用保温罩并不适用。
技术实现要素:
6.(一)解决的技术问题
7.针对现有技术的不足,本发明提供了一种高碳弹簧钢热轧卷板制备方法,在获得合格窄成分、良好的钢水洁净度的同时,解决连铸板坯生产高碳弹簧钢容易产生的铸坯边角裂纹、偏析等问题,保证较低的脱碳层,解决产品卷取后扁卷,冷却裂纹、组织不均等质量问题,满足用户对该弹簧钢的要求。
8.(二)技术方案
9.为实现以上目的,本发明通过以下技术方案予以实现:
10.一种高碳弹簧钢热轧卷板制备方法,包括:
11.s1、铁水脱硫预处理,
12.利用cao、钝化mg粉进行混合喷吹脱硫;
13.s2、顶底复吹转炉,
14.采用大渣量造渣或滑板挡渣的方式控制p含量;
15.s3、lf精炼炉,
16.采用萤石和适量改质剂造渣,不加入铝铁或铝线,并在精炼结束后加入纯钙线;
17.s4、板坯连铸,
18.连铸时采用的方式包括大包长水口、高碳覆盖剂、中间包水口氩封、浸入式水口以及高碳钢保护渣;
19.s5、板坯保温,
20.在进行保温处理时,采用板坯保温坑,铸坯下线后进入保温坑保温;
21.s6、板坯热轧加热,
22.将板坯热装,其中,热装时间≤24h;
23.s7、热连轧,
24.热连轧进行的加热温度为:1100-1240℃,粗轧除鳞压力≥16mpa,粗轧终轧温度控制在1040-1100℃,精轧终轧温度控制在880-930℃,热轧卷取温度控制在720
±
10℃;
25.s8、卷取,
26.使用卷取机,将热连轧后的钢材卷取成卷筒状;
27.s9、保温箱缓冷,
28.热卷下线后及时进入保温箱进行缓冷处理。
29.进一步的,在所述s1中,
30.预处理的终点:s≤0.008%。
31.进一步的,在所述s2中,
32.转炉出钢时,c:≥0.15%、p≤0.020%,出钢温度≥1600℃。
33.进一步的,在所述s3中,
34.进入纯钙线后,控制ca目标为0.0010-0.010%,其中,
35.软搅拌时间≥8min。
36.进一步的,在所述s4中,
37.板坯的断面为800-1600mm
×
230mm;
38.采用恒拉速,其拉速为0.80-1.0m/min;
39.二冷配水量0.84l/kg,并采用二冷电磁搅拌,其中的电流和频率分别为450a和6hz。
40.进一步的,在所述s5中,
41.铸坯在保温坑内的时长为60-180min。
42.进一步的,在所述s9中,
43.在进行热卷下线后及时进入保温箱进行缓冷,该缓冷时间≥48h。
44.进一步的,经过所述s9后,
45.得到的产品为高碳弹簧钢,其成分控制范围为,
46.c:0.56-0.64%、si:1.50-2.0%、mn:0.70-1.0%、p:≤0.25%、s≤0.010%、ni:≤0.35%、cu:≤0.25%、cr:≤0.35%、al:≤0.020%;其中,
47.实际产品典型金相组织和脱碳层厚度≤30μm,脱碳层深度为0.40-1.9%。
48.(三)有益效果
49.一是,本发明解决了常规板坯连铸、1780热连轧生产高碳弹簧钢卷板的工艺控制问题;
50.二是,本发明缩短了工艺流程,降低了生产成本;
51.三是,本发明采用良好的连铸工艺控制,二冷区电磁搅拌减少了铸坯偏析,保证了
铸坯内部质量;并通过缓冷坑的形式,保证了板坯热装的铸坯品质,降低了生产组织的难度,从而有利于该钢种的生产组织;
52.四是,本发明通过对热轧温度等工艺的控制,解决产品卷取后扁卷的问题。
53.五是,本发明通过下线保温箱冷却的措施,解决了产品冷却裂纹、组织不均的质量问题,比起保温罩的使用要更加方便。
附图说明
54.图1是本发明的整体制备方法流程图;
55.图2是本发明的4.0mm金相组织及脱碳层厚度在显微镜下的示意图。
具体实施方式
56.下面将结合本发明实施例中的附图,对本发明实施例中的技术方案进行清楚、完整地描述,显然,所描述的实施例仅仅是本发明的一部分实施例,而不是全部的实施例。基于本发明中的实施例,本领域普通技术人员在没有作出创造性劳动前提下所获得的所有其他实施例,都属于本发明保护的范围。此外,下文为了描述方便,所引用的“上”、“下”、“左”、“右”等于附图本身的上、下、左、右等方向一致,下文中的“第一”、“第二”等为描述上加以区分,并没有其他特殊含义。
57.针对现有技术中存在的问题,本发明提供一种高碳弹簧钢热轧卷板制备方法,包括:
58.s1、铁水脱硫预处理,
59.利用cao、钝化mg粉进行混合喷吹脱硫,通过铁水脱硫预处理保证铁水的低硫成分,保证最终成品的硫含量控制;预处理的终点:s≤0.008%;另外,也可采用现如今常用的kr搅拌法及喷枪插入铁水中的喷吹法。
60.s2、顶底复吹转炉,
61.采用大渣量造渣或滑板挡渣的方式控制p含量,转炉出钢时,c:≥0.15%、p≤0.020%,出钢温度≥1600℃;
62.s3、lf精炼炉,
63.采用萤石和适量改质剂造渣,不加入铝铁或铝线,并在精炼结束后加入纯钙线;进入纯钙线后,控制ca目标为0.0010%,其中,
64.软搅拌时间≥8min。
65.s4、板坯连铸,
66.连铸时采用的方式包括大包长水口、高碳覆盖剂、中间包水口氩封、浸入式水口以及高碳钢保护渣;板坯的断面为800mm
×
230mm;
67.采用恒拉速,其拉速为0.80/min;
68.二冷配水量0.84l/kg,并采用二冷电磁搅拌,其中的电流和频率分别为450a和6hz;可减少板坯内部偏析,保证内部质量。
69.s5、板坯保温,
70.在进行保温处理时,采用板坯保温坑,铸坯下线后进入保温坑保温;铸坯在保温坑内的时长为60min
71.s6、板坯热轧加热,
72.将板坯热装,其中,热装时间≤24h;
73.s7、热连轧,
74.热连轧进行的加热温度为:1100-1240℃,粗轧除鳞压力≥16mpa,粗轧终轧温度控制在1040-1100℃,精轧终轧温度控制在880-930℃,热轧卷取温度控制在720
±
10℃;保证脱碳层厚度满足产品要求,解决扁卷问题。
75.s8、卷取,
76.使用卷取机,将热连轧后的钢材卷取成卷筒状;
77.s9、保温箱缓冷,
78.热卷下线后及时进入保温箱进行缓冷处理;在进行热卷下线后及时进入保温箱进行缓冷,该缓冷时间≥48h;用于解决产品冷却裂纹、组织不均等质量问题。
79.经过所述s9后,
80.得到的产品为高碳弹簧钢,其成分控制范围为,
81.c:0.56-0.64%、si:1.50-2.0%、mn:0.70-1.0%、p:≤0.25%、s≤0.010%、ni:≤0.35%、cu:≤0.25%、cr:≤0.35%、al:≤0.020%;其中,
82.具体参照图2可以看出,实际产品典型金相组织和脱碳层厚度≤30μm,脱碳层深度为0.40-1.9%。
83.参照图1所示,上述整个步骤可概括为:铁水脱硫预处理
→
顶底复吹转炉
→
lf精炼炉
→
板坯连铸(二冷区电磁搅拌)
→
板坯保温
→
板坯热轧加热
→
1780热连轧
→
卷取
→
保温箱缓冷,其中给出的具体温度数值等其他数值可在后续的实施例中进行调控,以实现多组实施例,在此不多作赘述。
84.该工艺的优点为:主要针对常规板坯连铸、热连轧生产高碳弹簧钢卷板,在保证钢水的窄成分控制、良好的钢水洁净度的情况下,缩短工艺流程、降低生产成本;通过连铸二冷配水、二冷区电磁搅拌、板坯保温坑等措施解决高碳钢生产中容易产生的铸坯边角裂纹、偏析等板坯质量问题;通过适宜的热轧工艺控制解决产品热轧卷取后出现的扁卷问题;通过钢卷下线保温箱冷却的措施解决产品下线后的冷却裂纹、组织不均等质量问题。
85.以上内容是结合具体的优选实施方式对本发明所作的进一步详细说明,不能认定本发明的具体实施只局限于这些说明。对于本发明所属技术领域的普通技术人员来说,在不脱离本发明构思的前提下,还可以做出若干简单推演或替换,都应当视为属于本发明的保护范围。
再多了解一些
本文用于企业家、创业者技术爱好者查询,结果仅供参考。