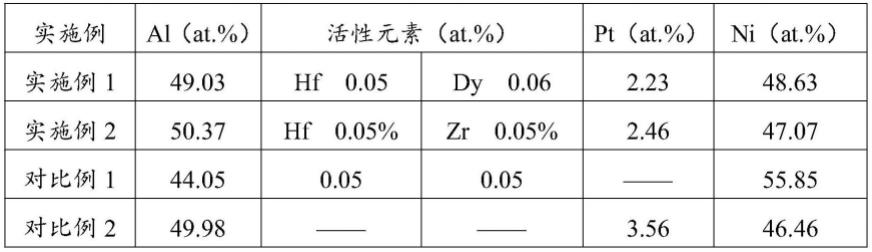
β-(ni,pt)al耐高温材料及应用、
β-(ni,pt)al粘结层的制备方法
技术领域
1.本发明属于热障涂层技术领域,具体涉及一种单相β-(ni,pt)al耐高温材料及应用、单相β-(ni,pt)al粘结层的制备方法。
背景技术:
2.热障涂层主要用于航空发动机的热端部件,一般由两部分组成:对合金部件起隔热作用的陶瓷层和抗高温氧化腐蚀的粘结层。粘结层位于金属基体和陶瓷层之间,改善了涂层、基体之间的热膨胀差异,缓解了体系的热应力,阻碍了氧气氧化基体。
3.β-nial是一种长程有序的金属间化合物,存在于ni50al50合金。由于金属键和共价键共存的特性,ni50al50的熔点tm为1638℃,具有制备超高温热障涂层粘结层的先决条件。此外ni50al50有较低的密度(5.9g/cm3)、较高的杨氏模量(240gpa),因此长期以来作为高温结构器件的备选材料而得到广泛关注。β-nial具有优良抗高温氧化性能,其抗高温氧化性能主要基于能够形成具有低生长速率的单一完整的α-al2o3氧化膜。然而β-nial体系的粘结层中的al在高温的环境下长期服役会向基体转移,从而减少粘结层中al的含量进而降低β-nial体系粘结层的抗氧化性。
技术实现要素:
4.有鉴于此,本发明提供了一种单相β-(ni,pt)al耐高温材料及应用、单相β-(ni,pt)al粘结层的制备方法,本发明提供的单相β-(ni,pt)al耐高温材料在高温环境下长期服役仍会保持较高抗氧化性。
5.为了解决上述技术问题,本发明提供了一种单相β-(ni,pt)al耐高温材料,包括以下原子百分含量的组分:
[0006][0007]
所述活性元素包括稀土元素、hf、zr和ti中的两种。
[0008]
优选的,所述稀土元素包括镧、铈、镝、钬、铒、铥和镥中的一种或多种。
[0009]
本发明提供了上述技术方案所述单相β-(ni,pt)al耐高温材料作为热障涂层中粘结层的应用;
[0010]
所述粘结层为单相β-(ni,pt)al粘结层。
[0011]
本发明还提供了上述技术方案所述单相β-(ni,pt)al粘结层的制备方法,包括以下步骤:
[0012]
提供含有两种活性元素的β-γ'双相镍铝合金;
[0013]
在基体表面制备pt层;
[0014]
将所述含有两种活性元素的β-γ'双相镍铝合金在所述pt层表面制备双相β-γ'粘结层;
[0015]
对所述双相β-γ'粘结层进行渗铝处理,在所述基体表面得到单相β-(ni,pt)al粘结层。
[0016]
优选的,所述制备pt层的方式包括电镀;
[0017]
所述电镀的电流密度为0.5~2a/dm2,所述电镀用镀铂液的温度为90~100℃,所述电镀的时间为15~60min。
[0018]
优选的,所述镀铂液包括亚硝酸二氨铂、硝酸铵、亚硝酸钠和氨水;
[0019]
所述镀铂液中亚硝酸二氨铂的质量浓度为15~20g/l,硝酸铵的质量浓度为98~102g/l,亚硝酸钠的质量浓度为8~12g/l,氨水的质量浓度为48~52g/l。
[0020]
优选的,制备pt层后还包括:对制备得到的pt层进行退火热处理。
[0021]
优选的,所述渗铝处理的方式为化学气相沉积,所述渗铝处理的温度为950~1050℃;时间为3~10h。
[0022]
优选的,含有两种活性元素的β-γ'双相镍铝合金的制备方法包括以下步骤:
[0023]
将两种活性元素、镍源和铝源熔炼后浇铸,得到铸锭;
[0024]
将所述铸锭进行退火处理,得到含有两种活性元素的β-γ'双相镍铝合金。
[0025]
优选的,所述退火处理的温度为1200~1400℃,时间为22~26h。
[0026]
本发明提供了一种单相β-(ni,pt)al耐高温材料,包括以下原子百分含量的组分:30~60at.%al,0.04~0.2at.%活性元素,2~9at.%pt和余量的ni,所述活性元素包括稀土元素、hf、zr和ti中的两种。在本发明中,所述铂能够减小耐高温材料中铝的活度,从而抑制耐高温材料在高温环境下服役过程中铝向基体扩散,从而减少耐高温材料中铝的流失避免β相向γ'相退化,使得耐高温材料在高温环境下长期服役仍保持优良的抗氧化性。
附图说明
[0027]
图1为实施例1制备得到的单相β-(ni,pt)al粘结层的样品实物图;
[0028]
图2为实施例1制备得到的双相β-γ'粘结层样品和单相β-(ni,pt)al粘结层样品的结构示意图,其中a为双相β-γ'粘结层样品的结构示意图,b为单相β-(ni,pt)al粘结层样品的结构示意图;
[0029]
图3为实施例1和对比例1样品在不同氧化处理时间下质量变化点线图;
[0030]
图4为实施例1和对比例2样品在不同氧化处理时间下质量变化点线图。
具体实施方式
[0031]
本发明提供了一种单相β-(ni,pt)al耐高温材料,包括以下原子百分含量的组分:
[0032]
[0033]
所述活性元素包括稀土元素、hf、zr和ti中的两种。
[0034]
在本发明中,以原子百分含量计,所述单相β-(ni,pt)al耐高温材料包括30~60at.%al,优选为32~51at.%,更优选为35~40at.%。
[0035]
在本发明中,以原子百分含量计,所述单相β-(ni,pt)al耐高温材料包括0.04~0.2at.%活性元素,优选为0.05~0.15at.%。在本发明中,所述活性元素优选包括稀土元素、hf、zr、和ti中的两种,更优选为稀土元素、hf和zr、的两种;更进一步优选为dy和hf。在本发明中,所述稀土元素优选包括镧、铈、镨、钕、钷、钐、铕、钆、铽、镝、钬、铒、铥、镱、钇、钪和镥中的一种或多种,更优选为镧、铈、镝、钬、铒、铥和镥中的一种或多种,更进一步优选为铈、镝或铒,最优选为镝。本发明对两种活性元素的质量配比无特殊限定,采用任意配比即可。在本发明中,两种活性元素的质量比优选为0.02~0.1:0.02~0.1,更优选为1:1。
[0036]
在本发明中,所述活性元素可通过阻止高温氧化过程中氧元素的内扩散和铝元素的外扩散从而减少界面空洞等因素同时改善氧化膜的粘附性和降低氧化膜的生长速率,进一步提高耐高温材料的抗氧化性。同时活性元素的添加使得耐高温材料在高温氧化过程中在耐高温材料表面形成的α-al2o3氧化膜有着更好的黏附性,在循环氧化过程中不易脱落,使得该耐高温材料有着更长的高温氧化寿命。
[0037]
在本发明中,所述两种活性元素会起到协同作用能够更好的提高耐高温材料的抗高温性。在本发明中,活性元素的原子半径比铝元素的原子半径大能够有效阻碍铝元素的外扩散从而降低氧化速率。两种不同的活性元素结合可以形成较单一活性元素半径更大的离子团,对铝原子外扩散的抑制更加明显,从而降低氧化速率。
[0038]
在本发明中,以原子百分含量计,所述单相β-(ni,pt)al耐高温材料包括2~9at.%pt,优选为3~8at.%,更优选为4~7at.%。在本发明中,所述铂能够减小耐高温材料中铝的活度,从而抑制耐高温材料在高温环境下服役过程中铝向基体扩散,从而减少耐高温材料中铝的流失避免β相向γ'相退化,使得该耐高温材料在高温环境下长期服役仍保持优良的抗氧化性。
[0039]
在本发明中,以原子百分含量计,所述单相β-(ni,pt)al耐高温材料还包括余量ni。
[0040]
本发明还提供了上述技术方案所述耐高温材料作为热障涂层中粘结层的应用;所述粘结层为单相β-(ni,pt)al粘结层。
[0041]
在本发明中,所述单相β-(ni,pt)al粘结层的厚度优选为20~90μm,更优选为40~60μm。
[0042]
本发明还提供了上述技术方案所述单相β-(ni,pt)al粘结层的制备方法,包括以下步骤:
[0043]
提供含有两种活性元素的β-γ'双相镍铝合金;
[0044]
在基体表面制备pt层;
[0045]
将所述含有两种活性元素的β-γ'双相镍铝合金在所述pt层表面制备双相β-γ'粘结层;
[0046]
对所述双相β-γ'粘结层进行渗铝处理,在所述基体表面得到单相β-(ni,pt)al粘结层。
[0047]
本发明提供含有两种活性元素的β-γ'双相镍铝合金。在本发明中,所述活性元素
优选包括稀土元素、hf、zr、和ti中的两种,更优选为稀土元素、hf和zr中的两种;更进一步优选为镝和hf。在本发明中,所述稀土元素优选包括镧、铈、镝、钬、铒、铥和镥中的一种或多种,更优选为铈、镝或铒,更进一步优选为镝。在本发明中,所述活性元素优选以金属单质的形式提供。
[0048]
在本发明中,所述含有两种活性元素的β-γ'双相镍铝合金的制备方法优选包括以下步骤:
[0049]
将两种活性元素、镍源和铝源熔炼后浇铸,得到铸锭;
[0050]
将所述铸锭进行退火处理,得到含有两种活性元素的β-γ'双相镍铝合金。
[0051]
本发明将两种活性元素、镍源和铝源熔炼后浇铸,得到铸锭。
[0052]
在本发明中,所述镍源优选为镍块,所述铝源优选为铝块。在本发明中,所述活性元素占铸锭的原子百分含量优选为0.02~0.1at.%,更优选为0.03~0.09at.%。在本发明中,所述铝源占铸锭的原子百分含量优选为20~40at.%,更优选为25~29at.%。
[0053]
在本发明中,所述熔炼前还优选包括:将两种活性元素、镍源和铝源依次进行清洗和干燥。在本发明中,所述清洗优选为超声清洗,所述超声清洗用溶剂优选为丙酮;所述超声清洗的时间优选为25~35min,更优选为30min;本发明对所述超声的功率无特殊限定,只要能清洗干净即可。本发明对所述干燥的温度和时间无特殊限定,只要能够除去活性元素、镍源和铝源表面的溶剂即可。
[0054]
在本发明中,所述熔炼优选为真空熔炼,所述真空熔炼的真空度优选为1
×
10-5
~1
×
10-4
pa,更优选为0.51
×
10-4
~0.81
×
10-4
pa。本发明对真空熔炼的温度和时间无特殊限定,只要能够能够实现熔炼即可。本发明在熔炼过程中优选进行翻炼,所述翻炼的次数优选为4~8次,更优选为5~6次。本发明经过翻炼能够使铸锭中成分均匀分布。本发明对所述真空熔炼的装置无特殊限定,采用本领域常规的装置即可,本发明的实施例中采用电弧熔炼炉进行真空熔炼。
[0055]
得到铸锭后,本发明将所述铸锭进行退火处理,得到含有两种活性元素的β-γ'双相镍铝合金。在本发明中,所述退火处理的温度优选为1200~1400℃,更优选为1250~1300℃;时间优选为22~26h,更优选为24~25h。在本发明中,所述退火处理后还优选包括:将退火处理的产物降温至室温,所述室温的温度优选为20~35℃,更优选为25~30℃。
[0056]
本发明在基体表面制备pt层。在本发明中,所述基体优选包括镍基高温合金,所述镍基高温合金优选包括n5镍基单晶高温合金、ic21镍基单晶高温合金、dd6镍基单晶高温合金或ic31镍基单晶高温合金,更优选为ic21镍基单晶高温合金。本发明对所述基体的形状和尺寸无特殊限定,根据需要进行设定即可。
[0057]
本发明在制备铂层前优选还包括:将所述基体依次进行喷砂、活化处理、洗涤和镀镍,得到预处理基体。本发明对所述喷砂无特殊限定,采用本领域常规的方式即可。在本发明中,所述活化处理优选为将喷砂后样品在盐酸溶液中浸泡。在本发明中,所述盐酸溶液的质量浓度优选为5~18%,更优选为10~15%。在本发明中,所述浸泡的时间优选为1~3min,更优选为1.5~2.5min。在本发明中,所述洗涤用溶剂优选为水,所述水优选为去离子水;所述洗涤的次数优选为3~4次。在本发明中,所述镀镍优选为冲击镀镍。在本发明中,所述镀镍用镀镍溶液优选包括ni(nh2so3)2、nicl2和h3bo3。在本发明中所述镀镍溶液中所述ni(nh2so3)2的质量浓度优选为100~150g/l,更优选为110~140g/l;所述nicl2的质量浓度优
选为5~100g/l,更优选为60~90g/l;所述h3bo3的质量浓度优选为40~60g/l,更优选为45~55g/l。在本发明中,所述冲击镀镍的电流密度优选为0.5~4a/dm2,更优选为1~3a/dm2;所述镀镍溶液的温度优选为45~75℃,更优选为50~70℃;所述冲击镀镍的时间优选为0.5~2min,更优选为0.8~1.3min。
[0058]
在本发明中,所述镀镍后优选还包括:将镀镍后样品进行洗涤;所述洗涤用溶剂优选为水,所述水优选为去离子水;所述洗涤的次数优选为3~4次。
[0059]
本发明镀铂前在基体表面镀镍,然后在镍层表面镀铂,提高了pt层与基底的结合力。
[0060]
在本发明中,所述制备pt层的方式优选包括电镀;所述电镀的电流密度优选为0.5~2a/dm2,更优选为0.8~1.3a/dm2;所述电镀用镀铂液的温度优选为65~100℃,更优选为70~90℃;所述电镀的时间优选为15~60min,更优选为20~50min。在本发明中,所述镀铂液优选包括亚硝酸二氨铂、硝酸铵、亚硝酸钠和氨水。在本发明中,所述镀铂液中亚硝酸二氨铂的质量浓度优选为15~20g/l,更优选为16~18g/l;硝酸铵的质量浓度优选为98~102g/l,更优选为99~100g/l;亚硝酸钠的质量浓度优选为8~12g/l,更优选为10~11g/l;氨水的质量浓度优选为48~52g/l,更优选为49~51g/l。
[0061]
在本发明中,所述铂层的厚度优选为2~10μm,更优选为3~9μm。
[0062]
本发明制备pt层后优选还包括:对制备得到的pt层进行退火热处理。在本发明中,所述退火热处理优选包括依次进行低温退火热处理和高温退火热处理。在本发明中,所述低温退火热处理的温度优选为260~300℃,更优选为265~290℃;所述低温退火热处理的时间优选为4~8h,更优选为4.5~7.5h。在本发明中,所述高温退火热处理的温度优选为1000~1080℃,更优选为1030~1070℃;所述高温退火热处理的时间优选为1~3h,更优选为1.5~2.5h。本发明优选在低温退火热处理温度的基础上继续升温至高温退火处理的温度。在本发明中,所述升温的升温速率优选为2~8℃/min,更优选为4~6℃/min。在本发明中,所述退火热处理的装置优选为真空热处理炉。
[0063]
在本发明中,所述退火热处理使铂与基体进行扩散以提高铂层与基体合金的结合力。
[0064]
得到pt层后,本发明将所述含有两种活性元素的β-γ'双相镍铝合金在所述pt层表面制备双相β-γ'粘结层。在本发明中,制备双相β-γ'粘结层的方式优选包括多弧离子镀或物理气相沉积,更优选为多弧离子镀。在本发明中,所述多弧离子镀的弧电流优选为160~200a,更优选为180~190a;偏压优选为10~30v,更优选为20~25v;真空度优选为1
×
10-3
~9
×
10-3
pa,更优选为5
×
10-3
pa;所述多弧离子镀过程中基体的温度优选为300~500℃,更优选为400~450℃。
[0065]
本发明采用多弧离子镀制备双相β-γ'粘结层前还优选包括:将基体表面进行喷砂预处理后进行机械加工,使所述基体的形状适应物理气相沉积设备。在本发明中,所述喷砂预处理用砂的粒度优选为120目;所述喷砂处理的压力优选为0.1~0.5mpa,更优选为0.2~0.4mpa。在本发明中,所述机械加工后还优选包括:将机械加工后的基体依次进行打磨处理和倒角处理。在本发明中,所述打磨处理后基体表面的粗糙度优选为ra《0.8,本发明对所述打磨的方式无特殊限定,只要能够达到所述粗糙度即可。本发明对倒角处理无特殊限定,采用本领域常规的方式即可。本发明进行倒角处理的目的是避免出现边缘效应。
[0066]
在本发明中,所述倒角处理后还优选包括:将倒角后基体进行清洗。在本发明中,所述清洗优选为依次在无水乙醇和丙酮中进行超声清洗,所述在无水乙醇中超声清洗和在丙酮中超声清洗的时间独立的优选为13~20min,更优选为15~18min。在本发明中,所述清洗后还优选包括:将清洗后的基体烘干。在本发明中,所述烘干的温度优选为70~200℃,更优选为80~150℃;时间优选为1~2h,更优选为1.5~1.8h。
[0067]
在本发明中,所述物理气相沉积的条件优选为:沉积室真空度优选为1
×
10-5
~1
×
10-3
pa,更优选为0.5
×
10-4
~1
×
10-4
pa;基板旋转速率优选为8~10r/min,更优选为9r/min;基板温度优选为700~800℃,更优选为750~780℃;电子束电流优选为1.2~1.5a,更优选为1.3~1.4a;电子束电压优选为17~19kv,更优选为17.5~18kv。在本发明中,所述基板为气相沉积的样品。
[0068]
本发明采用物理气相沉积制备双相β-γ'粘结层前还优选包括:将基体进行机械加工,使所述基体的形状适应物理气相沉积设备。
[0069]
得到双相β-γ'粘结层后本发明对所述双相β-γ'粘结层进行渗铝处理,在所述基体表面得到单相β-(ni,pt)al粘结层。在本发明中,所述渗铝处理的方式优选为化学气相沉积,所述渗铝处理的温度优选为950~1050℃,更优选为990~1000℃;时间优选为3~10h,更优选为6~8h。在本发明中,所述化学气相沉积的原料优选包括铝源、填充剂和活化剂,所述铝源优选包括铝粉或铝合金;所述铝合金包括nial合金、coal合金或cral合金,更优选为nial合金。
[0070]
在本发明中,靠近基体一侧的粘结层富含铂,两种活性元素以单质或金属间化合物的形式在弥散分布在粘结层中。
[0071]
本发明提供的制备方法利用含有二元活性元素的双相靶材,在镀铂的基体上沉积双相粘结层,再通过渗铝方式得到该种二元活性元素掺杂的单相β-(ni,pt)al粘结层;较常规的直接利用(较难炼制和加工的)二元活性元素的单相靶材在基体表面沉积含二元活性元素单相粘结层的制备方法大大提高了制备这种粘结层的成功率。
[0072]
为了进一步说明本发明,下面结合实施例对本发明提供的技术方案进行详细地描述,但不能将它们理解为对本发明保护范围的限定。
[0073]
实施例中称量工具为电子天平(cpa225d型,sartorius,精度10-5
g)。
[0074]
实施例1
[0075]
准备基体:
[0076]
利用线切割的方法将ic21合金切割成规格为直径为16.23mm厚度为3.67mm的圆柱形试样(试样表面积为562mm2),在试样直径两端分别开一个直径为1mm的孔,以便于在制备涂层时将试样悬挂在支架上;
[0077]
准备靶材:
[0078]
分别将镍块、铝块、铪块和镝块在丙酮中超声清洗30min后干燥;将干燥后的镍块、铝块、铪块和镝块置于电弧熔炼炉中进行真空熔炼(真空度为10-4
pa),熔炼过程中翻炼4次,其中铝块的原子百分含量为30at.%,铪块的原子百分含量为0.05at.%,镝块的原子百分含量为0.05at.%,镍块的原子百分含量为69.9at.%;真空熔炼后进行浇铸,得到铸锭;
[0079]
将所述铸锭1300℃退火处理24h,降温至30℃,得到β-γ'双相nialhfdy合金;将β-γ'双相nialhfdy合金机械加工成粗糙度ra<0.5的圆盘状的靶材,以适应多弧离子镀设
备;
[0080]
镀铂:
[0081]
将准备好的基体样品表面喷砂后置于质量浓度为12%的盐酸溶液中活化处理1min后,用去离子水冲洗4次;然后将活化处理后的样品表面进行冲击镀镍,用去离子水冲洗4次,得到镀镍基体;镀镍溶液成分为:ni(nh2so3)2的质量浓度为120g/l,nicl2的质量浓度为80g/l,h3bo3的质量浓度为50g/l;冲击镀镍的工艺:电流密度2a/dm2,镀液温度为60℃,电镀时间为1min;
[0082]
将所述镀镍基体放入镀铂溶液中电镀pt层,镀铂溶液的成分是:亚硝酸二氨铂的质量浓度为17g/l,硝酸铵的质量浓度为100g/l,亚硝酸钠的质量浓度为10g/l,氨水的质量浓度为50g/l;电镀pt工艺参数为:电流密度为1a/dm2,镀铂溶液温度为80℃,电镀时间30min,镀层厚度为5μm。
[0083]
电镀铂层成后280℃低温热退火处理6h,在280基础上升温至1060℃高温热退火处理2h,得到镀铂基体。
[0084]
制备双相β-γ'粘结层:
[0085]
将镀铂基体进行喷砂预处理(喷砂用砂的目数为120目,压力为0.2mpa)后依次用320#、600#、800#水磨砂纸进行打磨,使基体试样表面粗糙度ra《0.8,将边缘全部倒成圆角;将打磨好的基体试样依次用无水乙醇和丙酮超声清洗15min;将清洗后的基体试样80℃烘干2h;得到预处理镀铂基体;
[0086]
将所述β-γ'双相nialhfdy合金在温度为400℃的预处理镀铂基体表面进行多弧离子镀(电流为180a,偏压为25v,真空度为5
×
10-3
pa),得到平均厚度为50μm的双相β-γ'粘结层;
[0087]
渗铝处理:
[0088]
采用化学气相沉积对所述双相β-γ'粘结层进行渗铝处理(1000℃,8h),在ic21合金表面得到单相β-(ni,pt)al粘结层。
[0089]
实施例2
[0090]
按照实施例1的方法制备单相β-(ni,pt)al粘结层,不同之处在于,将基体替换为ic31合金,将准备靶材步骤中的镝块替换为锆块。
[0091]
对比例1
[0092]
按照实施例1的方法制备粘结层,不同之处在于,省略镀铂的步骤,直接在基体表面制备双相β-γ'粘结层。
[0093]
对比例2
[0094]
按照实施例1的方法制备粘结层,不同之处在于,靶材中不含有活性元素,仅以镍铝合金为靶材。
[0095]
将实施例1~2和对比例1~2制备得到的粘结层中组分的含量列于表1中。
[0096]
表1实施例1~2和对比例1~2制备得到的粘结层中组分含量
[0097][0098]
图1为实施例1制备得到的单相β-(ni,pt)al粘结层的样品实物图。
[0099]
实施例1制备得到的双相β-γ'粘结层和单相β-(ni,pt)al粘结层的结构示意图如图2所示,其中a为双相β-γ'粘结层的结构示意图,b为单相β-(ni,pt)al粘结层的结构示意图。双相β-γ'粘结层中铂层和β-γ'层双相镍铝成层结构;得到的单相β-(ni,pt)al粘结层中铂与镍、铝融合称为一层同时两种活性元素以单质和金属间化合物的形式分布在镍铂铝层中。
[0100]
按照hb5258-2000钢及高温合金的抗氧化性测定试验方法将实施例1和对比例1~2制备得到的粘结层的样品在1200℃进行200h的氧化处理。不同氧化处理时间后样品增加的质量列于表1中。
[0101]
表1不同氧化处理时间后样品增加的质量
[0102]
[0103][0104]
将实施例1和对比例1样品增加质量的数据绘制点线图,如图3所示。结合表1和图3可知,实施例1制备得到的得的单相β-(ni,pt)al粘结层的增重要低于对比例1制备得到的粘结层的增重,即本发明提供的单相β-(ni,pt)al粘结层的抗氧化性能优于无pt的的粘结层。
[0105]
将实施例1和对比例2样品增加质量的数据绘制点线图,如图4所示。结合表1和图4可知,实施例1制备得到的得的单相β-(ni,pt)al粘结层未发生剥落减重现象,而对比例2制备得到的粘结层氧化一定时间后出现了剥落减重现象,即本发明提供的单相β-(ni,pt)al粘结层的抗氧化性和α-al2o3氧化膜的黏附性能优于对比例2制备得到的粘结层。
[0106]
尽管上述实施例对本发明做出了详尽的描述,但它仅仅是本发明一部分实施例,而不是全部实施例,人们还可以根据本实施例在不经创造性前提下获得其他实施例,这些实施例都属于本发明保护范围。
再多了解一些
本文用于企业家、创业者技术爱好者查询,结果仅供参考。