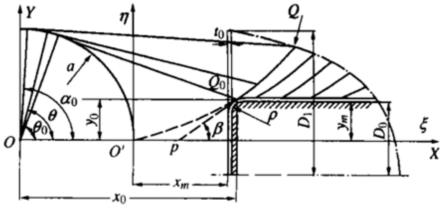
1.本发明涉及一种大型薄壁高温合金构件的旋压成形工艺,属于金属塑性成形技术领域。
背景技术:
2.高温合金由于其良好的屈服强度、抗拉强度、持久强度,以及优异的抗腐蚀、抗辐照、热加工及焊接性能等特点,被广泛用于航空、航天、化工、能源等领域。随着航空、航天发动机性能的不断提高,人们对发动机关键用材在承温能力、持久蠕变性能和抗疲劳性能等方面提出了更高要求,以满足先进航空发动机高性能、高可靠性、长寿命的需求。因此,如何通过合适的加工工艺制备高性能的高温合金结构材料是当前的一个研究重点。
3.旋压成形工艺作为塑性成形的一个重要分支,具有良好的柔性以及较低的成本,是制备高性能薄壁回转体构件的重要手段,申请号为201811619399.6的中国发明专利公开了一种难变形镍基高温合金复合曲母线构件室温旋压成形方法,该方法首先将毛坯加热至1141℃~1250℃,保温60min,进行固溶处理后水冷至室温。然后采用蝶形旋轮旋压获得预制锥形件,进给比为0.2mm/r,再通过复合旋轮圆弧往程轨迹进行多道次普通旋压获得复合曲母线构件。该方法虽然可以实现高温合金的室温成形,并通过剪切旋压结合多道次普通旋压获得复杂曲母线构件,但在成形过程中由于高温合金室温变形能力差容易产生开裂以及褶皱等缺陷,旋压件成形质量较差。
4.申请号为201611174457.x中国发明专利公开了一种镍基合金带底筒形件的旋压加工方法,该方法首先对芯模预热处理,温度为400℃~600℃,然后将板料毛坯加热到700℃~980℃进行热旋成形,芯模转速为100~400r/min,进给速度为50~150mm/min,旋轮圆角半径为15~30mm。该方案探索出一种针对gh4169镍基合金筒形件的热旋成形方法,但该方法仅适用于筒形件的成形,不适用于锥形件以及曲母线等复杂薄壁构件的成形。
5.目前,为了提高加工效率,高温合金旋压一般采用热旋成形,其中最常见的一种加热方式是火焰喷枪加热,具有简单,高效以及温度范围大等优点。文献“l.l.sun,h.c.kou,r.hu,j.wang,h.w.li,j.s.li,fem numerical simulation of first-pass heat spinning for ni-cr-w-mo superalloy workpiece with curvilinear shape,journal of plasticity engineering,17(2010)(孙立军,寇海川,胡若荣,王建军,李厚伟,李建新,ni-cr-w-mo高温合金曲线件一次热旋压有限元数值模拟,塑性工程杂志,17(2010)):33-38”建立了ni-cr-w-mo合金异型件热旋成形有限元模型,工艺参数为:芯模圆角半径10mm,进给比2mm/r,芯模预热温度400℃,旋压温度1050℃。结果表明,由于在加热过程中易出现温度波动,且加热精度不高,在热旋成形过程中旋压件容易产生较大的由于温度不均导致的热应力,容易进而使得旋压件容易产生开裂风险导致旋压失败。
6.为了解决大型薄壁高温合金构件旋压过程成形困难,易出现开裂、起皱等缺陷,旋压后需要大的机械加工量满足构建形状和尺寸要求的问题,着手对大型薄壁高温合金构件的旋压工艺进行优化。
技术实现要素:
7.本发明的目的是提供一种大型薄壁高温合金构件的近净旋压成形工艺,该工艺不仅解决了现有技术中旋压成形困难,易出现开裂、起皱等缺陷的问题,还解决了现有技术中成形余量大,需要二次加工的问题。
8.为达到上述目的,本发明采用的技术方案是:一种大型薄壁高温合金构件的近净旋压成形工艺,所述工艺包括:
9.将坯料装配值尾顶和芯模之间并进行预热处理,预热温度为300~400℃;
10.基于渐开线轨迹,进行6~8次旋压成形,旋压过程中,芯模转速为150r/min~180r/min,旋轮同步进给,进给速度为150mm/min~180mm/min;
11.其中,使用渐开线方程得到渐开线轨迹,渐开线方程为:
12.x=a[cosθ θsinθ-1]cosα-a[sinθ-θcosθ]sinα;
[0013]
y=a[cosθ θsinθ-1]sinα-a[sinθ-θcosθ]cosα;
[0014]
其中,a为基圆半径,θ为渐开线仰角,渐开线的旋转角α初始设为0
°
,后续每道次的α设为5
°
;
[0015]
使用火焰枪跟随旋轮进给,并对旋压部位加热,使旋压温度为800~900℃。
[0016]
进一步地,装配所述坯料前,轧制获得高温合金板料毛坯,并将毛坯于900~950℃退火处理,保温0.5~1小时候,空冷获得旋压坯料。
[0017]
进一步地,所述板料毛坯的厚度为4~6mm。
[0018]
进一步地,所述旋轮数量为2。
[0019]
进一步地,两个所述旋轮中心对称排列,对称中心为芯模轴线。
[0020]
进一步地,所述旋轮的圆角半径为6mm。
[0021]
进一步地,所述旋轮被动旋转。
[0022]
由于上述技术方案的运用,本发明与现有技术相比具有下列优点:
[0023]
1、本发明一种大型薄壁高温合金构件的近净旋压成形工艺,通过多道次高温旋压,有效降低旋压件贴膜区的应变值,均匀应变分布,同时,有效降低单道次的贴膜量,降低变形阻力,有效降低贴膜部位内外应变差,减少开裂风险,且通过控制旋转角从0
°
到5
°
,并选择合适的旋压运动轨迹,将渐开线轨迹向坯料一侧倾斜,减小仰角,提高旋压效果,在保证质量的同时实现了无余量/少余量成形。
[0024]
2、本发明一种大型薄壁高温合金构件的近净旋压成形工艺,通过使用4-6mm的薄板进行旋压成形,直接成形出厚度小于2mm的大尺寸薄壁构件,大幅度提高了材料利用率,实现了近净成形。
[0025]
3、本发明一种大型薄壁高温合金构件的近净旋压成形工艺,通过双旋轮对称分布进行旋压时,由于受力对称,因此力矩作用较弱,夹持端的应力集中得到了显著缓解,有效地提高了旋压变形的稳定性,促进了坯料的拉伸变形和减薄,提高旋压效率。
附图说明
[0026]
附图1为本发明的渐开线轨迹示意图;
[0027]
图中:xoy为以渐开线基圆中心为原点的坐标系、θ0为渐开线初始仰角、θ为某个时刻的渐开线仰角、α0为第一道次旋压终点处的渐开线仰角、a为基圆半径、y0为渐开线基圆中
心与初始旋压点沿y轴的距离、x0为渐开线基圆中心与初始旋压点沿x轴的距离、xm为渐开线起始位置与坯料外表面沿x轴的距离、εo’η为以渐开线起始位置为原点的坐标系、d0为芯模半径、d1为坯料半径、q0为坯料旋压起始位置、q为坯料旋压终点、t0为坯料厚度、ρ为芯模圆角半径、β为坯料初始旋压点的渐开线切线与x轴的夹角、ym为渐开线起始位置与坯料内表面沿y轴的距离。
具体实施方式
[0028]
实施例1:一种大型薄壁高温合金构件的近净旋压成形工艺,所述工艺包括以下步骤:
[0029]
s1:根据构件设计要求的形状尺寸,计算得到构件体积,由于体积不变,通过轧制获得φ420
×
4mm的高温合金圆柱形板料毛坯;
[0030]
这里,使用的高温合金为in625合金。
[0031]
s2:将轧制获得的毛坯于950℃退火处理,并保温0.5小时,空冷后获得旋压坯料。
[0032]
s3:将坯料夹装于尾顶和芯模之间,并对坯料进行预热处理,预热温度为300℃;
[0033]
其中,旋压用旋轮为圆旋轮,圆角半径为6mm,且旋轮的数目为2个,以芯模的轴线为对称轴,中心对称分布于芯模轴线的两侧,通过双旋轮对称分布进行旋压,缓解夹持端的应力集中现象,有效地提高了旋压变形的稳定性,促进了坯料的拉伸变形和减薄,提高旋压效率。
[0034]
s4:基于渐开线的旋压轨迹规划,进行8道次旋压成形,旋压过程中,芯模转速为160r/min,旋轮同步进给,进给速度为160mm/min,且旋轮在于坯料的摩擦作用下被动旋转。
[0035]
这里,旋压过程中,使用火焰枪对坯料进行局部加热,且火焰枪跟随旋轮进给,保证温度的稳定性,同时,手动或自动调节热流密度(热流密度的调节可通过调节喷口与坯料的距离、火焰功率、火焰枪数量等参数和条件实现),使加热区域的温度恒定为900℃。
[0036]
其中,参照附图1,渐开线规划轨迹规划方法如下:将xoy坐标系下的渐开线绕旋转中心o点旋转α度使之与芯模圆角外侧相切,获得的渐开线方程为:
[0037]
x=a[cosθ θsinθ-1]cosα-a[sinθ-θcosθ]sinα;
[0038]
y=a[cosθ θsinθ-1]sinα-a[sinθ-θcosθ]cosα;
[0039]
其中旋转角α决定了后续道次轨迹,当α为零时,渐开线轨迹为原始轨迹;当α大于零时,渐开线轨迹逐渐向旋压件一侧倾斜,仰角逐渐减小,坯料逐渐贴合芯模,初始α设为0度,后续每道次的α设为5度;
[0040]
这里,基圆半径a为600mm,初始仰角θ0为60
°
,y0取27.36mm,旋压得到与芯模相贴合的锥形旋压件,成形质量好,余量少,无需二次加工。
[0041]
实施例2:一种大型薄壁高温合金构件的近净旋压成形工艺,所述工艺包括以下步骤:
[0042]
s1:根据构件设计要求的形状尺寸,计算得到构件体积,由于体积不变,通过轧制获得φ850
×
5mm的高温合金圆柱形板料毛坯;
[0043]
这里,使用的高温合金为in625合金。
[0044]
s2:将轧制获得的毛坯于950℃退火处理,并保温0.5小时,空冷后获得旋压坯料。
[0045]
s3:将坯料夹装于尾顶和芯模之间,并对坯料进行预热处理,预热温度为300℃;
[0046]
其中,旋压用旋轮为圆旋轮,圆角半径为6mm,且旋轮的数目为2个,以芯模的轴线为对称轴,中心对称分布于芯模轴线的两侧,通过双旋轮对称分布进行旋压,缓解夹持端的应力集中现象,有效地提高了旋压变形的稳定性,促进了坯料的拉伸变形和减薄,提高旋压效率。
[0047]
s4:基于渐开线的旋压轨迹规划,进行8道次旋压成形,旋压过程中,芯模转速为160r/min,旋轮同步进给,进给速度为160mm/min,且旋轮在于坯料的摩擦作用下被动旋转。
[0048]
这里,旋压过程中,使用火焰枪对坯料进行局部加热,且火焰枪跟随旋轮进给,保证温度的稳定性,同时,手动或自动调节热流密度(热流密度的调节可通过调节喷口与坯料的距离、火焰功率、火焰枪数量等参数和条件实现),使加热区域的温度恒定为900℃。
[0049]
其中,参照附图1,渐开线规划轨迹规划方法如下:将xoy坐标系下的渐开线绕旋转中心o点旋转α度使之与芯模圆角外侧相切,获得的渐开线方程为:
[0050]
x=a[cosθ θsinθ-1]cosθ-a[sinθ-θcosθ]sinα;
[0051]
y=a[cosθ θsinθ-1]sinα-a[sinθ-θcosθ]cosα;
[0052]
其中旋转角α决定了后续道次轨迹,当α为零时,渐开线轨迹为原始轨迹;当α大于零时,渐开线轨迹逐渐向旋压件一侧倾斜,仰角逐渐减小,坯料逐渐贴合芯模,初始α设为0度,后续每道次的α设为5度;
[0053]
这里,基圆半径a为1500mm,初始仰角θ0为60
°
,y0取27.36mm,旋压得到与芯模相贴合的锥形旋压件,成形质量好,余量少,无需二次加工。
[0054]
实施例3:一种大型薄壁高温合金构件的近净旋压成形工艺,所述工艺包括以下步骤:
[0055]
s1:根据构件设计要求的形状尺寸,计算得到构件体积,由于体积不变,通过轧制获得φ1100
×
6mm的高温合金圆柱形板料毛坯;
[0056]
这里,使用的高温合金为in625合金。
[0057]
s2:将轧制获得的毛坯于950℃退火处理,并保温0.5小时,空冷后获得旋压坯料。
[0058]
s3:将坯料夹装于尾顶和芯模之间,并对坯料进行预热处理,预热温度为300℃;
[0059]
其中,旋压用旋轮为圆旋轮,圆角半径为6mm,且旋轮的数目为2个,以芯模的轴线为对称轴,中心对称分布于芯模轴线的两侧,通过双旋轮对称分布进行旋压,缓解夹持端的应力集中现象,有效地提高了旋压变形的稳定性,促进了坯料的拉伸变形和减薄,提高旋压效率。
[0060]
s4:基于渐开线的旋压轨迹规划,进行8道次旋压成形,旋压过程中,芯模转速为160r/min,旋轮同步进给,进给速度为160mm/min,且旋轮在于坯料的摩擦作用下被动旋转。
[0061]
这里,旋压过程中,使用火焰枪对坯料进行局部加热,且火焰枪跟随旋轮进给,保证温度的稳定性,同时,手动或自动调节热流密度(热流密度的调节可通过调节喷口与坯料的距离、火焰功率、火焰枪数量等参数和条件实现),使加热区域的温度恒定为900℃。
[0062]
其中,参照附图1,渐开线规划轨迹规划方法如下:将xoy坐标系下的渐开线绕旋转中心o点旋转α度使之与芯模圆角外侧相切,获得的渐开线方程为:
[0063]
x=a[cosθ θsinθ-1]cosα-a[sinθ-θcosθ]sinα;
[0064]
y=a[cosθ θsinθ-1]sinα-a[sinθ-θcosθ]cosα;
[0065]
其中旋转角α决定了后续道次轨迹,当α为零时,渐开线轨迹为原始轨迹;当α大于
零时,渐开线轨迹逐渐向旋压件一侧倾斜,仰角逐渐减小,坯料逐渐贴合芯模,初始α设为0度,后续每道次的α设为5度;
[0066]
这里,基圆半径a为3000mm,初始仰角θ0为60
°
,y0取27.36mm,旋压得到与芯模相贴合的曲母线形旋压件,成形质量好,余量少,无需二次加工。
再多了解一些
本文用于企业家、创业者技术爱好者查询,结果仅供参考。