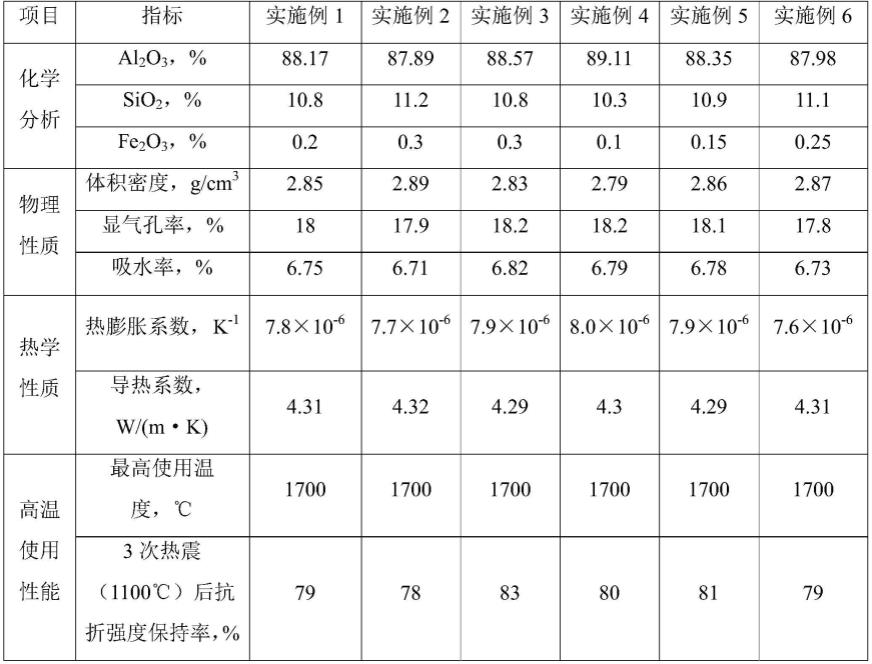
1.本发明属于高温耐火材料技术领域,具体涉及一种金属精密铸造用抗热震刚玉莫来石坩埚及其制备方法。
背景技术:
2.我国是当今世界上最大的铸件生产国家,据资料介绍,最近几年,由于铸件进出口贸易增长较快,我国铸造产品的产值在国民经济中约占9%左右。我国铸造厂多达2万多家,从业人员达到120多万。当前我国精密铸造产业已经有相当的规模,一大批铸件行业科技进步成果进入应用领域,个别产品的制造水平甚至接近国际先进水平。一些中高精密铸造产品还服务于汽车、航空航天、船舶、能源等重点领域。
3.坩埚作为精密铸造中金属熔炼主要的辅助工具。具有优异的耐腐蚀、抗侵蚀和抗热震性等性能的坩埚,可减少铸件夹杂物并最大程度地提高质量及产量。尤其是在航空发动机和涡轮制造的应用中,要求的熔化容器需要优异的性能。等静压坩埚的开发被视为熔模铸造行业的重大突破。坩埚在一定压力下形成,可生产出具有极高品质、密度均匀且孔径大小一致的坩埚。在制造复杂且昂贵的铸件时,使用等静压坩埚可以确保熔体的纯净度,有利于提高铸件的质量及产量。
4.目前,国内通过等静压技术生产刚玉莫来石坩埚的企业极少,大多是生产碳化硅、石墨坩埚,但是坩埚中的碳元素容易进入金属熔体中,抗侵蚀性能差;氧化镁坩埚在高温下容易与碳、钛、铝等活性元素发生还原反应,从而污染熔体,导致铸件纯净度的降低;氧化钙坩埚容易与水发生水化反应,不易压制成型;刚玉坩埚,虽然具有良好的化学稳定性、耐酸碱性、抗渣性等优点,但其抗热震性能差,骤冷骤热容易发生开裂。
5.坩埚属于一种高温耐火材料制品,一般按照“紧密堆积”的原则,颗粒分为粗、中、细三种粒径,粗颗粒和中颗粒组成骨架,细粉填充到骨架的空隙中,形成最紧密堆积。但是,细粉是形成耐火材料基质的基础,也是抗热震性最薄弱的点。
技术实现要素:
6.本发明要解决的技术问题是:克服现有技术的不足,提供一种具有抗热震性能好、抗渣性好、耐高温耐磨损、化学稳定性好的金属精密铸造用抗热震刚玉莫来石坩埚;同时本发明还提供其制备方法。
7.本发明是采用以下技术方案实现的:
8.所述的金属精密铸造用抗热震刚玉莫来石坩埚,原料包括以下质量百分比的组分:板状刚玉15~25%、电熔刚玉15~25%、电熔莫来石25~35%、片状氧化铝20~30%、活性氧化铝5~15%和二氧化硅1~5%;以上述原料的总质量计,外加粘结剂2~6%和增塑剂2~6%。采用的原料均为高纯原料,防止杂质在金属熔炼时进入熔体中影响铸件的纯净度和质量。
9.对原料颗粒级配进行配比设计,用以提高刚玉莫来石坩埚的抗热震性能,有利于
延长坩埚的使用寿命,其颗粒级配百分比为:
10.1mm<粒径≤3mm
ꢀꢀꢀꢀꢀꢀꢀꢀꢀꢀꢀꢀ
10~25%
11.0.1mm≤粒径≤1mm
ꢀꢀꢀꢀꢀꢀꢀꢀꢀꢀ
35~50%
12.粒径<0.1mm
ꢀꢀꢀꢀꢀꢀꢀꢀꢀꢀꢀꢀꢀꢀꢀ
30~45%。
13.引进粒径<0.1mm的片状氧化铝,粒径小于0.1mm的细粉是耐火材料性能最薄弱的组织,片状结构能大幅提高抗热震性能,从而延长坩埚的使用寿命。
14.粒径<0.1mm的活性氧化铝和二氧化硅微粉在高温下发生固相反应原位生成呈柱状或者棒状的二次莫来石,与片状氧化铝形成连续交错的网络结构,可以起到纤维增强的增韧作用,有利于提高坩埚基质的抗热震性能。
15.所述的粘结剂优选为聚乙烯醇、丙烯酸聚合物、淀粉、糊精或甲基纤维素中的一种或多种。
16.所述的增塑剂优选为聚乙二醇、聚丙三醇或酯类化合物中的的一种或多种。
17.本发明所述的金属精密铸造用抗热震刚玉莫来石坩埚的制备方法,
18.包括以下步骤:
19.(1)按质量百分比称量所需原料,对原料颗粒级配后,将1mm<粒径≤3mm和0.1mm≤粒径≤1mm的原料预混,时间为1~3h;混合均匀后,加入粘结剂和增塑剂,混合均匀,时间为1~2h;然后加入粒径<0.1mm的原料,混合3~5h;
20.(2)混合均匀后,将物料陈腐15~25h,以确保水分更均匀;
21.(3)物料陈腐后,将物料装入等静压模具中,振实,在等静压设备中压制成型,成型压力为70~120mpa;
22.(4)成型后的坩埚生坯自然干燥24~48h;
23.(5)干燥后的坩埚进行高温烧结,烧结温度为1600~1700℃,保温时间3~6h,随炉冷却。
24.所述的原料混合采用混碾机。混碾机内衬和搅拌装置均采用陶瓷材质,防止金属材质被磨损,磨屑混入原料中导致污染。
25.所述的等静压模具钢芯采用硬质合金材质,胶套采用聚氨酯材质。原料中板状刚玉、电熔刚玉、电熔莫来石具有尖锐结构,容易损伤钢芯,减少寿命,导致脱模困难;聚氨酯胶套回弹好,不粘料,压制后迅速脱模,效率高。
26.所述的振实设备为三维振动平台。耐火材料具有颗粒级配,采用三维振动平台,防止振动时造成颗粒分层。
27.所述的等静压成型工艺采用冷等静压设备。等静压成型的坩埚致密度高、密度均匀,减少润滑剂使用量,降低对坩埚的污染。
28.所述的烧结工艺采用电炉高温烧成。电炉烧结,温度易控制,升温速度快,降低成本,保护环境。
29.刚玉莫来石不仅利用了莫来石的熔点高、热膨胀系数低、抗蠕变及抗热震等优点,而且还利用了刚玉的耐磨、抗化学侵蚀、抗氧化等优点,因而其具有较高的高温性能、高温机械强度、抗热震性、荷重软化温度、较高的使用温度,其化学稳定性好,不与其他产品发生反应。在刚玉莫来石复相结构中,莫来石一般为柱状、棒状晶体,刚玉一般为粒状,刚玉状晶体填充于莫来石柱状晶网络结构的空隙中,形成连续的交错网络骨架结构,刚玉相晶体可
以起到增强、增韧作用;或者莫来石柱状晶体填充于刚玉相晶体的空隙中,柱状莫来石晶体的存在,可以起到类似于纤维和颗粒的增强、增韧作用,这两种填充状态对提高刚玉莫来石复相陶瓷高温力学性能均非常有利。本发明采用等静压技术压制成型,解决金属精密铸造中坩埚抗热震性能差、抗渣性差、化学稳定性差等缺点,从而提高坩埚的使用寿命、熔体的纯净度和铸件的质量,适用于普通钢、不锈钢、镍基/钴基高温合金等金属材质的精密铸造,降低生产成本,提高铸件的质量及产量。
30.与现有技术相比,本发明的有益效果如下:
31.1、本发明提供的金属精密铸造用抗热震刚玉莫来石坩埚采用等静压工艺成形,具有极高品质、密度均匀且孔径大小一致。
32.2、本发明通过引进粒径<0.1mm的片状氧化铝细粉进一步提高坩埚的最薄弱组织的抗热震性能,具有优异的抗渣性、化学稳定性、耐高温耐磨损等优点,从而延长坩埚的使用寿命、提高熔体的纯净度和铸件的质量。
33.3、本发明通过引进粒径<0.1mm的活性氧化铝和二氧化硅微粉在高温下发生固相反应原位生成呈柱状或者棒状的二次莫来石,与片状氧化铝形成连续交错的网络结构,可以起到纤维增强的增韧作用,有利于提高坩埚基质的抗热震性能。
34.4、本发明制备工艺中采用内衬和搅拌装置均采用陶瓷材质的混碾机、冷等静压设备、硬质合金钢芯、电炉等设备,确保刚玉莫来石坩埚具有高纯的成分,降低金属熔炼时污染概率。
35.5、本发明制备工艺中采用聚氨酯胶套和三维振动平台,可提高生产效率和成品率。
附图说明
36.图1为本发明实施例1中高温烧成坩埚基质的扫描电镜图。
具体实施方式
37.下面结合实施例对本发明做进一步的说明。
38.实施例1
39.取按质量百分比称量所需原料,板状刚玉17%、电熔刚玉18%、电熔莫来石27%,片状氧化铝24%、活性氧化铝11%、二氧化硅3%,外加粘结剂3.5%和增塑剂4%。其颗粒级配百分比:1mm<粒径≤3mm 17%,0.1mm≤粒径≤1mm 45%,粒径<0.1mm 38%。将1mm<粒径≤3mm和0.1mm≤粒径≤1mm的原料预混,时间为1.5h,混合均匀后,加入粘结剂和增塑剂,混合均匀,时间为1.5h;然后加入粒径<0.1mm的原料,混合4h;混合均匀后,物料陈腐18h,以确保水分更均匀;物料陈腐后,将物料装入模具中,在等静压设备中压制成型,成型压力为90mpa;成型后的坩埚生坯自然干燥24h;干燥后的坩埚进行高温烧结,烧结温度为1650℃,保温时间5h,随炉冷却。
40.实施例2
41.取按质量百分比称量所需原料,板状刚玉15%、电熔刚玉19%、电熔莫来石28%,片状氧化铝20%、活性氧化铝15%、二氧化硅3%,外加粘结剂3.5%和增塑剂4%。其颗粒级配百分比:1mm<粒径≤3mm 15%,0.1mm≤粒径≤1mm 47%,粒径<0.1mm 38%。将1mm<粒
径≤3mm和0.1mm≤粒径≤1mm的原料预混,时间为2h,混合均匀后,加入粘结剂和增塑剂,混合均匀,时间为2h;然后加入粒径<0.1mm的原料,混合3h;混合均匀后,物料陈腐24h,以确保水分更均匀;物料陈腐后,将物料装入模具中,在等静压设备中压制成型,成型压力为90mpa;成型后的坩埚生坯自然干燥24h;干燥后的坩埚进行高温烧结,烧结温度为1600℃,保温时间6h,随炉冷却。
42.实施例3
43.取按质量百分比称量所需原料,板状刚玉17%、电熔刚玉16%、电熔莫来石27%,片状氧化铝26%、活性氧化铝11%、二氧化硅3%,外加粘结剂3.5%和增塑剂4%。其颗粒级配百分比:1mm<粒径≤3mm 17%,0.1mm≤粒径≤1mm 43%,粒径<0.1mm 40%。将1mm<粒径≤3mm和0.1mm≤粒径≤1mm的原料预混,时间为3h,混合均匀后,加入粘结剂和增塑剂,混合均匀,时间为1h;然后加入粒径<0.1mm的原料,混合5h;混合均匀后,物料陈腐18h,以确保水分更均匀;物料陈腐后,将物料装入模具中,在等静压设备中压制成型,成型压力为80mpa;成型后的坩埚生坯自然干燥24h;干燥后的坩埚进行高温烧结,烧结温度为1650℃,保温时间4h,随炉冷却。
44.实施例4
45.取按质量百分比称量所需原料,板状刚玉20%、电熔刚玉15%、电熔莫来石27%,片状氧化铝24%、活性氧化铝11%、二氧化硅3%,外加粘结剂4.5%和增塑剂2%。其颗粒级配百分比:1mm<粒径≤3mm 20%,0.1mm≤粒径≤1mm 42%,粒径<0.1mm 38%。将1mm<粒径≤3mm和0.1mm≤粒径≤1mm的原料预混,时间为2h,混合均匀后,加入粘结剂和增塑剂,混合均匀,时间为1.5h;然后加入粒径<0.1mm的原料,混合4h;混合均匀后,物料陈腐18h,以确保水分更均匀;物料陈腐后,将物料装入模具中,在等静压设备中压制成型,成型压力为80mpa;成型后的坩埚生坯自然干燥48h;干燥后的坩埚进行高温烧结,烧结温度为1650℃,保温时间4h,随炉冷却。
46.实施例5
47.取按质量百分比称量所需原料,板状刚玉23%、电熔刚玉10%、电熔莫来石27%,片状氧化铝24%、活性氧化铝13%、二氧化硅3%,外加粘结剂3.5%和增塑剂4%。其颗粒级配百分比:1mm<粒径≤3mm 23%,0.1mm≤粒径≤1mm 37%,粒径<0.1mm 40%。将1mm<粒径≤3mm和0.1mm≤粒径≤1mm的原料预混,时间为3h,混合均匀后,加入粘结剂和增塑剂,混合均匀,时间为2h;然后加入粒径<0.1mm的原料,混合4h;混合均匀后,物料陈腐24h,以确保水分更均匀;物料陈腐后,将物料装入模具中,在等静压设备中压制成型,成型压力为120mpa;成型后的坩埚生坯自然干燥24h;干燥后的坩埚进行高温烧结,烧结温度为1700℃,保温时间3h,随炉冷却。
48.实施例6
49.取按质量百分比称量所需原料,板状刚玉20%、电熔刚玉20%、电熔莫来石27%,片状氧化铝20%、活性氧化铝10%、二氧化硅3%,外加粘结剂3.5%和增塑剂4%。其颗粒级配百分比:1mm<粒径≤3mm 20%,0.1mm≤粒径≤1mm 47%,粒径<0.1mm 33%。将1mm<粒径≤3mm和0.1mm≤粒径≤1mm的原料预混,时间为2h,混合均匀后,加入粘结剂和增塑剂,混合均匀,时间为2h;然后加入粒径<0.1mm的原料,混合3h;混合均匀后,物料陈腐18h,以确保水分更均匀;物料陈腐后,将物料装入模具中,在等静压设备中压制成型,成型压力为
90mpa;成型后的坩埚生坯自然干燥24h;干燥后的坩埚进行高温烧结,烧结温度为1600℃,保温时间6h,随炉冷却。
50.性能测试
51.如图1所示,本发明刚玉莫来石坩埚基质中,片状氧化铝和原位生成二次莫来石形成的相互紧密交错的网络结构,起到类似于纤维和颗粒的增强、增韧作用,有利于提高基质的抗热震性能,从而延长坩埚的使用寿命,降低使用成本。
52.对实施例1-6制备的坩埚按照常规标准进行性能测试,测试结果见表1。
53.表1实施例1-6高温烧成坩埚的性能测试结果
[0054][0055]
从表1可知,本发明刚玉莫来石坩埚具有很高的使用温度,较高的体积密度以及较低的显气孔率和吸水率,较低的热膨胀系数和较高的导热系数,以及较高的热震后抗折强度保持率,因此,本发明刚玉莫来石坩埚具有优异的抗热震性能,有利于延长坩埚的使用寿命。
[0056]
表2实施例1和同质坩埚的性能对比
[0057][0058]
从表2可知,通过对比抗热震性和使用寿命,本发明刚玉莫来石坩埚的抗热震性(1300℃,水冷)达到20次以上和使用寿命达到150炉以上,相对于同质坩埚,具有明显优势,表明本发明中片状结构氧化铝的添加和原位合成的莫来石与片状氧化铝形成的连续交错
网络结构,提高坩埚的抗热震性能。
[0059]
当然,上述内容仅为本发明的较佳实施例,不能被认为用于限定对本发明的实施例范围。本发明也并不仅限于上述举例,本技术领域的普通技术人员在本发明的实质范围内所做出的均等变化与改进等,均应归属于本发明的专利涵盖范围内。
再多了解一些
本文用于企业家、创业者技术爱好者查询,结果仅供参考。