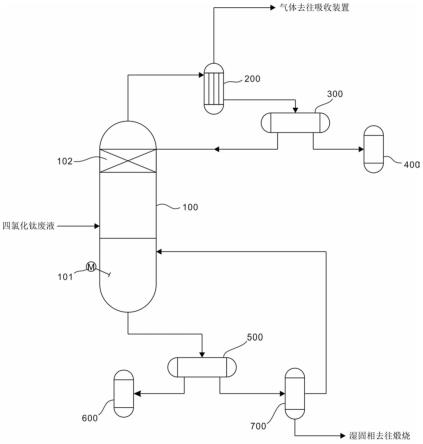
1.本发明属于废液处理技术领域,具体涉及到一种四氯化钛废液处理工艺。
背景技术:
2.在聚烯烃工业生产中,齐格勒-纳塔(ziegler-natta)催化剂是获得应用的主要催化剂类型。该催化剂通常采用含有卤素或者卤氧化的钛作为触媒,以获得高效的聚合反应速率和高质量的聚合反应效果。在齐格勒-纳塔(ziegler-natta)催化剂的生产制备过程中,会产生大量四氯化钛废液,其中除含有未反应的四氯化钛外,还可能会含有烃类有机溶剂、烷氧基钛或卤代烷氧基钛等有机组分。
3.根据不同可挥发性组份沸点的差异,通常可以采用精馏/蒸馏的方法,将四氯化钛废液中相应的组分逐次从母液分离出来。为提高四氯化钛及其中挥发性有机物的收率,也有使用薄膜蒸发器来进行处理的报道。但是,由于物料组成的特性,在实际物料的精馏过程中,随着四氯化钛的减少和挥发性有机组分浓度的降低,釜温将会逐渐升高,低沸点的四氯化钛与高沸点的烷氧基钛会混杂在一起,难以分离,在釜中形成高沸物釜残液。蒸发浓缩后残余料液的粘度会变大,过度蒸馏将导致严重结垢和堵塞,使得釜中残液难以排出。特别地,该釜残液经冷却降温后,甚至会凝固为固态,存在设备内部结块和凝固的风险。在实际生产中,通常不能将废液中的四氯化钛及挥发性有机物彻底回收,因此会产生较多的四氯化钛废液。
4.四氯化钛遇空气会剧烈发烟,与空气中的水反应生成二氧化钛固体和盐酸液滴的混合物。为消除隐患,通常采取的方式是将高沸物釜残液与水混合,然后再往该强酸性水解废液中加入碱性物质(如氢氧化钠、氢氧化钙、氧化钙等)进行中和。但这种处理方法会产生大量高盐高cod废液和废渣,其中的钛、有机物及氯化氢也无法充分回收或资源化利用,存在成本高、三废多等问题。
5.在我们此前的研究中,报道了一种四氯化钛废液的处理方法(cn201510354029.4),可以将四氯化钛废液处理回收得到氯化氢、二氧化钛和有机油相,从而实现对该四氯化钛废液的资源化处理。该方法中采用了两步法对四氯化钛进行处理,即(1)将含四氯化钛废液和水接触以进行水解;(2)将上述水解后的废液进行蒸馏,待油相蒸出20体积%以上后,从剩余的物料中收集含钛化合物。但实际应用中,发现该方法存在如下主要问题:1)四氯化钛的水解是一个剧烈的放热反应,为保证水解过程的平稳进行,在该处理方法的第一步水解操作需要充分冷却换热以及时移走反应的放热量,在第二步蒸馏时又需要大量供热换热以保证油水物料的蒸发,在这一过程中四氯化钛的水解热不能被充分利用,导致过程能量利用率差、能耗高;2)四氯化钛的水解是一个复杂的反应过程,在该处理方法的第一步水解操作时液相中会以钛的氯氧化物等形式积累大量氯,在第二步蒸馏沸腾条件下会出现大量且快速的剧烈氯化氢析气,这将带来设备超压危险,过大设备设计裕量(应对瞬时释气)又会带来设备成本和操作成本(例如大回流比保持填料充分润湿导致的能耗)问题;3)在该处理方法的第一步水解操作条件下,四氯化钛在气相中会剧烈发烟,从而
污染析出的氯化氢气体;此外,液相水解反应中析出的氯化氢会导致发泡逃液,该逃液中含有高浓度的固形物,其夹带进氯化氢气体中,不仅将污染氯化氢气体,还将进一步导致换热器表面结垢沉积(降低换热效率)、管路阀门堵塞(系统超压危险)等问题。4)此外,因为操作条件要求的不同,两步操作还将导致繁琐的物料周转问题。在该处理方法的第一步水解操作过程中,液相中会出现固体析出物,浆料的周转工艺设计不仅将导致操作时间的延长,还容易发生管路堵塞问题。
技术实现要素:
6.本部分的目的在于概述本发明的实施例的一些方面以及简要介绍一些较佳实施例。在本部分以及本技术的说明书摘要和发明名称中可能会做些简化或省略以避免使本部分、说明书摘要和发明名称的目的模糊,而这种简化或省略不能用于限制本发明的范围。
7.鉴于上述和/或现有技术中存在的问题,提出了本发明。
8.本发明的其中一个目的是提供一种四氯化钛废液处理工艺,具有工艺流程简单的优势,一步反应精馏不仅解决了物料周转的繁琐操作,也缩短了操作时间和能耗。
9.为解决上述技术问题,本发明提供了如下技术方案:一种四氯化钛废液处理工艺,包括,
10.将水或以水为主要成分的水化剂加入到反应精馏塔的塔釜中,升高反应精馏塔塔釜中的水化剂温度至沸腾,同时打开塔顶冷凝;
11.在搅拌下,将四氯化钛废液缓慢加到装有水化剂的反应精馏塔塔釜中,进行反应精馏操作;塔体内上升的气相,经塔顶冷凝器冷凝,然后经第一分相罐分相处理,水相回流回塔顶,回流润湿反应精馏塔塔身内的分离介质,油相收集至轻油罐;不凝气氯化氢去吸收装置制备盐酸;
12.反应精馏结束后,釜液经第二分相罐分相处理,难挥发性重油收集至重油罐;水相浆料去固液分离处理,分离得到的湿固相物经煅烧制备二氧化钛,分离得到的滤液作为水化剂回用至下一批反应精馏处理过程。
13.作为本发明四氯化钛废液处理工艺的一种优选方案,其中:所述四氯化钛废液与所述水化剂的质量比为1:3~10;水化剂为纯水、水溶液或者固液分离收集的滤液中的一种或多种;反应釜温度为水化剂的沸腾温度,温度为100~120℃。
14.作为本发明四氯化钛废液处理工艺的一种优选方案,其中:所述将四氯化钛废液缓慢加到装有水化剂的反应精馏塔塔釜中,控制四氯化钛废液的添加速率,调控氯化氢的析出速率及釜液中偏钛酸晶体的生长速率;
15.所述反应精馏塔塔釜内四氯化钛废液的添加速率由釜压控制,釜压不超过反应精馏设备系统耐压上限的1/4。
16.作为本发明四氯化钛废液处理工艺的一种优选方案,其中:所述反应精馏塔塔身内的分离介质为填料或塔板。
17.作为本发明四氯化钛废液处理工艺的一种优选方案,其中:所述反应精馏塔塔顶冷凝器冷凝后回流的流体,回流量不低于分离介质润湿所需回流量的下限值。
18.作为本发明四氯化钛废液处理工艺的一种优选方案,其中:所述反应精馏塔塔塔顶冷凝器冷凝后的流体,可经气液分离器进一步脱除不凝气氯化氢中夹带的因冷凝产生的
雾滴。
19.作为本发明四氯化钛废液处理工艺的一种优选方案,其中:所述氯化氢气体可经净化装置处理以脱除其中的污染物,氯化氢气体经水吸收制备盐酸,也可经石灰乳吸收制备氯化钙。
20.作为本发明四氯化钛废液处理工艺的一种优选方案,其中:所述固液分离,可使用洗涤剂对滤饼进行洗涤,洗涤剂为水或稀酸。
21.作为本发明四氯化钛废液处理工艺的一种优选方案,其中:所述固液分离,分离前料浆温度《75℃。
22.作为本发明四氯化钛废液处理工艺的一种优选方案,其中:所述分离得到的湿固相物经煅烧制备二氧化钛,其中煅烧温度》120℃,收集并回收干燥、煅烧过程中释放的挥发性组分。
23.与现有技术相比,本发明具有如下有益效果:
24.本发明工艺方法具有工艺流程简单的优势,一步反应精馏不仅解决了物料周转的繁琐操作,也缩短了操作时间和能耗。本发明工艺方法具有能量利用率高的特点,水解放热用于精馏,避免了水解放热时降温的能耗,也避免了后面精馏时又要升温的能耗。
附图说明
25.为了更清楚地说明本发明实施例的技术方案,下面将对实施例描述中所需要使用的附图作简单地介绍,显而易见地,下面描述中的附图仅仅是本发明的一些实施例,对于本领域普通技术人员来讲,在不付出创造性劳动性的前提下,还可以根据这些附图获得其它的附图。其中:
26.图1为本发明处理工艺系统图。
具体实施方式
27.为使本发明的上述目的、特征和优点能够更加明显易懂,下面结合说明书实施例对本发明的具体实施方式做详细的说明。
28.在下面的描述中阐述了很多具体细节以便于充分理解本发明,但是本发明还可以采用其他不同于在此描述的其它方式来实施,本领域技术人员可以在不违背本发明内涵的情况下做类似推广,因此本发明不受下面公开的具体实施例的限制。
29.其次,此处所称的“一个实施例”或“实施例”是指可包含于本发明至少一个实现方式中的特定特征、结构或特性。在本说明书中不同地方出现的“在一个实施例中”并非均指同一个实施例,也不是单独的或选择性的与其他实施例互相排斥的实施例。
30.本发明提供的四氯化钛废液处理工艺的系统图如图1所示,反应精馏塔的塔釜100底部加入水化剂,其内部设置搅拌器101,塔釜100上部为填料102;
31.塔釜100顶部设置有冷凝器200,塔釜100顶部出口与冷凝器200入口相连,冷凝器200具有液体出口和气体出口,冷凝器200的气体出口连接吸收装置,冷凝器200的液体出口则连接第一分相罐300,第一分相罐300具有水相出口和油相出口,第一分相罐300的水相出口与塔釜100上部的填料102连通,回流润湿反应精馏塔塔釜100内的填料102,第一分相罐300的油相出口则连接轻油罐400,用于轻油相的回收。
32.塔釜100底部连接有第二分相罐500,第二分相罐500具有液相出口和固相出口,第二分相罐500的液相出口连接重油罐600,第二分相罐500的固相出口则连接固液分离器700,固液分离器700的滤液出口与塔釜100底部连接,用于将滤液回收作为水化剂使用,固液分离器700的滤饼出口则连接煅烧装置,湿固相物经煅烧制备二氧化钛。
33.利用该工艺系统,进行如下实施例。
34.实施例1
35.在反应精馏塔(塔釜容积5l,塔釜带变频搅拌,塔径35mm,内装两层各10cm的玻璃弹簧填料,直管冷凝器)塔釜中加入水化剂(纯水)4500ml,然后升温至沸腾,在塔顶冷凝器冷凝回流,回流量约300ml/h。100rpm搅拌条件下,将1000ml的四氯化钛废液(四氯化钛60%v/v,己烷20%v/v,甲苯等杂质20%v/v)以10ml/min的速度流加到塔釜中,保持釜液沸腾及塔顶回流状态,塔顶冷凝器凝液进入分相器分相,水相回流至塔顶,油相(甲苯、己烷等)约400ml收集至轻油瓶;反应中释放出来的白雾状氯化氢气体与上升蒸汽在塔内经回流液逐级洗涤以脱除悬混的污染物(含钛化合物),洁净气相经冷凝器冷凝分离出凝液(水相和油相液体)后,最终基本不产生不凝气氯化氢(氯化氢在釜液中被吸收生成浓度约15%的盐酸溶液)。
36.在该四氯化钛废液添加过程中,釜液表面通常会有淡黄色四氯化钛废液池形成。因此在保持釜压值《2kpa情况下,需同时观察釜液面,如有淡黄色四氯化钛废液池形成,应立刻停止加料并加强搅拌,待淡黄色液池消失后才可继续加料,以避免形成大的接液池倾覆,导致瞬间釜压暴增及塔身液泛等问题。
37.在四氯化钛添加过程中,因为四氯化钛与水的反应是剧烈的放热反应(总放热量约1480kj),因此可注意依据塔顶的回流液速及塔压降情况降低塔釜的加热速率(或壁面温差),减少塔釜的热量供应(减少量与反应放热量相当,约1480kj),以实现有效节能,同时也避免蒸发量过大导致液泛。
38.反应精馏结束后,保持釜液搅拌,5h降温至50℃,同时实现对釜液料浆中析出的偏钛酸颗粒的陈化结晶作用,然后放料进入布氏漏斗进行固液分离得到约850g湿滤饼。湿滤饼用纯水抽滤洗涤干净,然后煅烧粉碎后制备得到微米二氧化钛,滤液合并后套用至下一批反应精馏过程。
39.实施例2
40.在反应精馏塔(塔釜容积5l,塔釜带变频搅拌,塔径35mm,内装20cm的玻璃拉西环填料,球形冷凝器)塔釜中加入套用滤液3500ml,然后升温至沸腾,塔顶冷凝回流,回流量约250ml/h。150rpm搅拌条件下,将800ml的四氯化钛废液(四氯化钛70%v/v,己烷10%v/v,甲苯20%v/v)以8ml/min的速度流加到塔釜中,保持釜液沸腾及塔顶回流状态,塔顶冷凝器凝液进入分相器分相,水相回流至塔顶,油相(甲苯、己烷等)约240ml收集至轻油瓶;反应中释放出来的白雾状氯化氢气体与上升蒸汽在塔内经回流液逐级洗涤以脱除悬混的污染物(含钛化合物),洁净气相经冷凝器冷凝分离出凝液(水相和油相液体)后,最终不凝气氯化氢去吸收系统制备得到浓度》30%wt的透明液体盐酸(浊度《10ntu)。
41.在该四氯化钛废液添加过程中,釜液表面偶尔会有淡黄色四氯化钛废液池形成。因此在保持釜压值《2kpa情况下,需同时观察釜液面,如有超过釜液面表面积1%(约5cm2)的淡黄色四氯化钛废液池形成,应立刻停止加料并加强搅拌,待淡黄色液池消失后才可继
续加料,以避免接液池倾覆导致的瞬间釜压暴增及塔身液泛等问题。
42.在四氯化钛添加过程中,因为四氯化钛与水的反应是剧烈的放热反应(总放热量约1380kj),因此可注意依据塔顶的回流液速及塔压降情况降低塔釜的加热速率(或壁面温差),减少塔釜的热量供应(减少量与反应放热量相当,约1380kj),以实现有效节能,同时也避免蒸发量过大导致液泛。
43.反应精馏结束后,保持釜液搅拌,5h降温至45℃,同时实现对釜液料浆中析出的偏钛酸颗粒的陈化结晶作用,然后放料进入布氏漏斗进行固液分离得约820g湿滤饼。湿滤饼用纯水抽滤洗涤干净,然后煅烧制备二氧化钛,滤液合并后套用至下一批反应精馏过程。
44.实施例3
45.在反应精馏塔(塔釜容积1l,塔釜带变频搅拌,塔径20mm,内装20cm的蜂窝陶瓷填料,球形冷凝器)塔釜中加入套用滤液500ml,然后升温至沸腾,塔顶冷凝回流,回流量约50ml/h。150rpm搅拌条件下,将100ml的四氯化钛废液(四氯化钛65%v/v,己烷5%v/v,甲苯20%v/v,高沸有机物10%v/v)以1ml/min的速度流加到塔釜中,保持釜液沸腾及塔顶回流状态,塔顶冷凝器凝液进入分相器分相,水相回流至塔顶,油相(甲苯、己烷等)收集至轻油瓶;反应中释放出来的白雾状氯化氢气体与上升蒸汽在塔内经回流液逐级洗涤以脱除悬混的污染物(含钛化合物),洁净气相经冷凝器冷凝分离出凝液(水相和油相液体)后,最终不凝气氯化氢去吸收系统制备得到浓度》25%wt的透明液体盐酸(浊度《10ntu)。
46.在该四氯化钛废液添加过程中,釜液表面可能会有淡黄色四氯化钛废液池形成。在保持釜压值《1kpa情况下,需同时观察釜液面,如有淡黄色四氯化钛废液池形成,应立刻停止加料并加强搅拌,待淡黄色液池消失后才可继续加料,以避免接液池倾覆导致的瞬间釜压暴增及塔身液泛等问题。
47.在四氯化钛添加过程中,因为四氯化钛与水的反应是剧烈的放热反应(总放热量约160kj),因此可注意依据塔顶的回流液速及塔压降情况降低塔釜的加热速率(或壁面温差),减少塔釜的热量供应(减少量与反应放热量相当,约160kj),以实现有效节能,同时也避免蒸发量过大导致液泛。
48.反应精馏结束后,保持釜液搅拌,5h降温至65℃,同时实现对釜液料浆中析出的偏钛酸颗粒的陈化结晶作用;然后停搅拌静置60min,油相分层结束后,将上层油相抽出,水相浆料放料进入布氏漏斗进行固液分离得约95g湿滤饼。湿滤饼用纯水抽滤洗涤干净,然后煅烧粉碎后制备二氧化钛,滤液合并后套用至下一批反应精馏过程。
49.实施例4
50.实施例4与实施例1基本相同,差别之处在于水化剂种类不同,分别采用纯水、15%盐酸、以及固液分离收集的滤液(约20%盐酸)作为水化剂。
51.试验结果显示,采用纯水作为水化剂,回流液为稀盐酸(浓度《20%),反应生成的氯化氢在塔内被吸收,终了釜液为含氯化氢(浓度约19%)的钛氧化物悬混液,塔顶基本无不凝气氯化氢释放。
52.采用15%盐酸作为水化剂,回流液为盐酸(初始浓度《15%,终了浓度约36%),终了釜液为含氯化氢20~30%的钛氧化物悬混液,总释放的氯化氢不凝气为反应产生氯化氢量与釜液吸收氯化氢的差值。
53.采用固液分离收集的滤液(约20%盐酸)作为水化剂,初始回流液为盐酸(初始浓
度约20%,终了浓度约36%),终了釜液为含氯化氢20%-36%的钛氧化物悬混液,总释放的氯化氢不凝气约等于反应产生氯化氢。
54.实施例5
55.实施例5与实施例1基本相同,差别之处在于四氯化钛与水化剂的质量比不同,试验结果显示:
56.废液与水化剂(纯水)的质量比为1:1时,回流液为盐酸(初始为水,最高浓度约36%),反应生成的氯化氢部分在塔内被吸收,终了釜液为含氯化氢(浓度约20%)的粘稠浆状钛氧化物悬混液,塔顶释放的氯化氢不凝气总量约为原料废液质量的42%。
57.废液与水化剂(纯水)的质量比为1:3时,回流液为稀盐酸(初始为水,最高浓度约21%),终了釜液为含氯化氢(浓度约20%)的钛氧化物悬混液,塔顶基本无不凝气氯化氢释放。
58.废液与水化剂(纯水)的质量比为1:10时,回流液为稀盐酸(初始为水,最高浓度《6%),终了釜液为含氯化氢(浓度约6%)的钛氧化物悬混液,塔顶基本无不凝气氯化氢释放。
59.实施例6
60.实施例6与实施例1基本相同,差别之处在于反应釜温度不同,分别在温度100℃、110℃、120℃下进行试验,试验结果显示:
61.反应釜温度为100℃时,系统压力为近常压,釜液处于油/水/固非均相沸腾状态,反应放热量约为废液中所含甲苯及己烷完全汽化所需热量的14倍。
62.反应釜温度为110℃时,系统压力约为165kpa,釜液处于油/水/固非均相沸腾状态,反应放热量约为废液中所含甲苯及己烷完全汽化所需热量的14倍;系统压力为近常压,釜液中非均相己烷和甲苯等已蒸出,釜液处于水/固非均相沸腾状态。
63.反应釜温度为120℃时,系统压力约为225kpa,釜液处于油/水/固非均相沸腾状态,反应放热量约为废液中所含甲苯及己烷完全汽化所需热量的14倍;系统压力约为205kpa,釜液中非均相己烷和甲苯等已蒸出,釜液处于水/固非均相沸腾状态。
64.在水溶液中,四氯化钛的水解是一个复杂的反应过程。四氯化钛遇少量水会生成固形钛氯氧化物,在低温条件下,四氯化钛遇水会迅速水化为溶液态。而在高温和充足水供应条件下,四氯化钛遇水后会发生深度的水解反应,进而迅速析出固体钛氧化物(二氧化钛/偏钛酸)和氯化氢。持续的能量供应(例如保持溶液沸腾)有利于溶液中钛氯氧化物的充分水解和钛氧化物及氯化氢的析出,特别是在沸腾条件下,高于氯化氢-水共沸物组成(氯化氢-水的常压共沸点组成为20.24%,共沸点温度约108℃)的氯化氢将从溶液中挥发出来。
65.在反应精馏工艺装备中,可以提供良好的反应温度、搅拌及水供应等操作条件,通过控制四氯化钛废液的添加速率可控制水解反应和物料精馏的速度,并调节氯化氢和固体钛氧化物的析出速度,有机油相的挥发速度。特别地,由于废液中四氯化钛和挥发性有机物共存,四氯化钛与水反应放出的热量可形成局部高温,而该高温极大地促进了挥发性有机物的热量吸收和利用,从而有效提高了热量的利用率。在四氯化钛含量》70%wt的四氯化钛废液中,四氯化钛水解放热量和挥发性有机物汽化潜热吸热量,甚至能够基本持平,这意味着在该物料的水解精馏过程中,总体的能量消耗将得到极大降低。
66.利用反应精馏塔的精馏和冷凝器的冷凝作用,可持续将四氯化钛废液制备得到富含氯化氢的蒸气,通过冷凝器将该蒸气中的水蒸汽冷凝为液体,从而可解析得到氯化氢气体。在四氯化钛废液的加入过程中,沸腾状态的釜液液面上气相中的水蒸气分压较高(或说该气相湿度较大),该气体与四氯化钛接触将会发生快速的水解反应和放热,气体变为白烟状,从而使得析出的氯化氢气体受到污染。在反应精馏塔中,填料的捕集和回流液的洗涤作用可清除该白烟状气体(含钛氧化物微粒和酸雾)中的污染物,从而得到洁净的氯化氢气体。
67.反应精馏结束后得到的晶浆,经过滤可得到白色钛氧化物滤饼,该滤饼可使用纯水、水溶液等洗涤剂进行洗涤处理。过滤得到的滤液可据其组成情况,套用至后批次的水解过程或洗涤过程。滤饼经干燥和煅烧,可得到固体二氧化钛。针对煅烧后物料中出现的微粒团聚及结块现象,可进行研磨处理以得到符合要求的二氧化钛粉体。
68.本发明工艺方法具有工艺流程简单的优势,一步反应精馏不仅解决了物料周转的繁琐操作,也缩短了操作时间和能耗。
69.本发明工艺方法具有能量利用率高的特点,水解放热用于精馏,避免了水解放热时降温的能耗,也避免了后面精馏时又要升温的能耗。
70.本发明工艺方法具有氯化氢析气过程本质安全的显著优势,在反应精馏耦合一步操作过程中,四氯化钛废液进料后立即反应析出气体,避免了先水化/水解再析气过程存在的气体释放量大且难以控制的问题,避免了可能出现的设备超压、设备设计裕量过大(应对瞬时释气)带来的安全和设备成本、操作可可行性问题(例如设备尺寸过大,则持液量就会升高,否则不能充分润湿)。
71.本发明工艺方法有效避免了液相发泡导致的逃液(特别是低温时液体表面张力过大,水解析气过程迅速大量发泡逃液)、产品污染(析气发泡会导致液体夹带,沿管路夹带到氯化氢气体中,污染气体,进而污染后继产品)、设备堵塞(逃液中夹带的钛的氯氧化物及钛的氧化物固体,在管路及换热设备等表面沉积,形成垢层或堵塞)等问题。
72.本发明工艺方法实现了四氯化钛废液水解产物的全资源化,并且可将固液分离后的液体重新循环利用,工艺过程可控,通过调节四氯化钛添加速率来控制二氧化钛的析出速率和氯化氢的释放速率,具有操作简单,绿色环保,易于工业化生产的特点。
73.应说明的是,以上实施例仅用以说明本发明的技术方案而非限制,尽管参照较佳实施例对本发明进行了详细说明,本领域的普通技术人员应当理解,可以对本发明的技术方案进行修改或者等同替换,而不脱离本发明技术方案的精神和范围,其均应涵盖在本发明的权利要求范围当中。
再多了解一些
本文用于企业家、创业者技术爱好者查询,结果仅供参考。