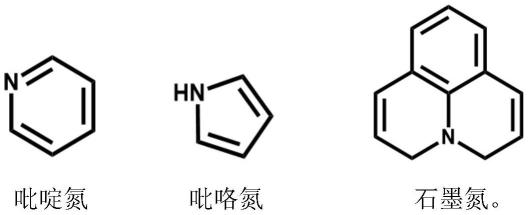
1.本发明属于缓蚀剂技术领域,具体涉及一种赖氨酸基碳量子点缓蚀剂及其制备方法与应用。
背景技术:
2.金属材料如钢铁、铜等被广泛应用于关乎国计民生的各个行业,比如机械制造业、海洋工业、国防工业、建筑行业、交通运输业等,具有非常重要的地位。但是金属材料在使用过程中极易遭受环境中腐蚀介质(如酸、碱、盐等)的侵蚀而发生腐蚀现象。而金属的腐蚀与以其为基础所制备的机械装置、仪器设备、生产建筑、工作平台、金属管道等安全性紧密相关。
3.为了减少腐蚀造成的损失,添加缓蚀剂是应用最为广泛的手段之一,该方法具有用量小、操作简单、成本低廉、效果显著、通用性强等优点,使其在各种防腐蚀方法中占据了重要的地位。最早的选择是无机缓蚀剂,例如铬酸盐,磷酸盐和钼酸盐。尽管这些缓蚀剂能有效抑制金属或合金的腐蚀,但在这些传统缓蚀剂中仍检测到一些有害成分,可能危害人体健康或导致严重的生态污染。特别是近年来,人们对环境保护的认识逐渐提高,对缓蚀剂的开发和应用要求也越来越高。高效、环保、价格低廉的绿色抑制剂的研究与发展已逐渐成为未来发展的方向。因此开发一种新的用于金属的缓蚀剂是亟待解决的问题。
技术实现要素:
4.本发明的主要目的在于提供一种赖氨酸基碳量子点缓蚀剂及其制备方法与应用,以克服现有技术的不足。
5.为实现前述发明目的,本发明采用的技术方案包括:
6.本发明实施例提供了一种赖氨酸基碳量子点缓蚀剂,所述赖氨酸基碳量子点缓蚀剂是通过赖氨酸和/或赖氨酸衍生物高温裂解获得的,所述赖氨酸基碳量子点缓蚀剂包括由c、h、o、n构成的芳杂环结构,其中n以类吡啶氮、类吡咯氮或类石墨氮的形式存在,所述赖氨酸基碳量子点缓蚀剂的尺寸大小为5~20nm。
7.本发明实施例还提供了前述的赖氨酸基碳量子点缓蚀剂的制备方法,其包括:使赖氨酸和/或赖氨酸衍生物于150~250℃高温裂解1~3h,制得赖氨酸基碳量子点缓蚀剂。
8.本发明实施例还提供了前述的赖氨酸基碳量子点缓蚀剂于金属基材表面防腐领域的用途。
9.本发明实施例还提供了一种金属基材的表面防护方法,其包括:将前述的赖氨酸基碳量子点缓蚀剂施加于所述金属基材表面,从而实现对金属基材的防护。
10.与现有技术相比,本发明的有益效果在于:
11.(1)本发明提供的高温裂解制备赖氨酸基碳量子点缓蚀剂的方法,具有操作方便、成本低廉,环保的优点;
12.(2)本发明提供的赖氨酸基碳量子点缓蚀剂具有优异的水溶性及耐腐蚀性能,赖
氨酸基碳量子点缓蚀剂具有更多的活性位点,提高了与金属表面的化学键合,从而降低金属的腐蚀速率;同时良好的水溶性能有效提高缓蚀剂在水环境下的分散性;
13.(3)本发明通过将赖氨酸和/或赖氨酸衍生物的高温裂解,制备的缓蚀剂水溶性好、防腐性能优良,可应用在钢铁、化工、石油、电力、造纸、炼油、船舶、储存、交通等行业中,尤其有望在化工设备、钢铁、石油、海上平台等大型设备上取得应用,将本发明的缓蚀剂用于金属基体表面,还可以提高基体的使用寿命。
附图说明
14.为了更清楚地说明本发明实施例或现有技术中的技术方案,下面将对实施例或现有技术描述中所需要使用的附图作简单地介绍,显而易见地,下面描述中的附图仅仅是本发明中记载的一些实施例,对于本领域普通技术人员来讲,在不付出创造性劳动的前提下,还可以根据这些附图获得其他的附图。
15.图1是本发明中一典型实施方案中赖氨酸基碳量子点缓蚀剂的制备流程示意图;
16.图2a-图2b是本发明对比例1中碳钢在1m hcl环境下的电化学阻抗谱图;
17.图3是本发明对比例1中碳钢在1m hcl环境下的极化曲线图;
18.图4a-图4b是本发明对比例2中碳钢在3.5%nacl环境下的电化学阻抗谱图;
19.图5是本发明对比例2中碳钢在3.5%nacl环境下的极化曲线图;
20.图6a-图6b是本发明对比例3中碳钢在含有不同缓蚀剂环境下的电化学阻抗谱图;
21.图7是本发明实施例1中赖氨酸基碳量子点的红外光谱图;
22.图8a-图8b是本发明实施例1中电极的电化学阻抗谱图;
23.图9a-图9b是本发明实施例2中电极的极化曲线和腐蚀电流密度图;
24.图10是本发明实施例2中电极的腐蚀速率图;
25.图11a-图11b是本发明实施例3中电极的电化学阻抗谱图;
26.图12a-图12b是本发明实施例4中电极的极化曲线和腐蚀电流密度图;
27.图13是本发明实施例4中电极的腐蚀速率图;
28.图14a-图14b是本发明实施例5中电极的电化学阻抗谱图;
29.图15a-图15b是本发明实施例6中电极的电化学阻抗谱图;
30.图16a-图16b是本发明实施例7电极中的电化学阻抗谱图;
31.图17a-图17b是本发明实施例8电极中的电化学阻抗谱图。
具体实施方式
32.鉴于现有技术的缺陷,本案发明人经长期研究和大量实践,得以提出本发明的技术方案,下面将对本发明的技术方案进行清楚、完整地描述,显然,所描述的实施例是本发明一部分实施例,而不是全部的实施例。基于本发明中的实施例,本领域普通技术人员在没有做出创造性劳动前提下所获得的所有其他实施例,都属于本发明保护的范围。
33.具体的,作为本发明技术方案的一个方面,其所涉及的一种赖氨酸基碳量子点缓蚀剂,所述赖氨酸基碳量子点缓蚀剂是通过赖氨酸和/或赖氨酸衍生物高温裂解获得的,所述赖氨酸基碳量子点缓蚀剂包括由c、h、o、n构成的芳杂环结构,所述赖氨酸基碳量子点缓蚀剂中n元素以类吡啶氮、类吡咯氮或类石墨氮的形式存在,所述赖氨酸基碳量子点缓蚀剂
的尺寸大小为5~20nm。
34.其中,吡啶氮、吡咯氮、石墨氮的结构式分别如下式所示:
[0035][0036]
在一些优选实施方案中,所述赖氨酸基碳量子点缓蚀剂在水中的溶解度为5~500mg/1ml水,即所述赖氨酸基碳量子点缓蚀剂具有优异的水溶性。
[0037]
在一些优选实施方案中,所述赖氨酸衍生物包括d-赖氨酸盐酸盐、l-赖氨酸盐酸盐、l-赖氨酸水合物中的任意一种或两种以上的组合,且不限于此。
[0038]
在一些优选实施方案中,金属在所述赖氨酸基碳量子点缓蚀剂的hcl和nacl溶液中浸泡24h后阻抗仍能达到102~103数量级,腐蚀电流密度则低至10-5
~10-6
a/cm2,表现出优异的抗腐蚀性。
[0039]
进一步地,金属在所述赖氨酸基碳量子点缓蚀剂的hcl和nacl溶液中浸泡24h后,与置于未添加缓蚀剂的溶液中相比,低频阻抗模量提高了1~2个数量级。
[0040]
进一步地,金属在所述赖氨酸基碳量子点缓蚀剂的hcl和nacl溶液中浸泡24h后,与置于未添加缓蚀剂的溶液中相比,腐蚀电流密度下降了1~2个数量级。
[0041]
本发明实施例的另一个方面还提供了前述的赖氨酸基碳量子点缓蚀剂的制备方法,其包括:使赖氨酸和/或赖氨酸衍生物于150~250℃高温裂解1~3h,制得赖氨酸基碳量子点缓蚀剂。
[0042]
在一些较为具体的实施方案中,所述赖氨酸基碳量子点缓蚀剂的制备流程示意图如图1所示。
[0043]
在一些优选实施方案中,所述制备方法还包括:将赖氨酸置于烧杯中后,先通过锡箔纸封口,而后在其表面扎一些小孔排气,最后至于恒温干燥箱中进行高温裂解处理。
[0044]
在一些优选实施方案中,所述制备方法还包括:对所述赖氨酸基碳量子点缓蚀剂进行溶解、离心、过滤、透析、干燥处理。
[0045]
进一步地,所述制备方法包括:将所述赖氨酸基碳量子点缓蚀剂与水混合进行搅拌、超声处理,其中所述搅拌处理的时间为10~20min,超声处理的时间为10~25min。
[0046]
进一步地,所述离心处理的转速为8000~15000r/min。
[0047]
进一步地,所述过滤的步骤重复3~5次。
[0048]
进一步地,所述透析处理采用的透析袋分子量为1kd~3kd。
[0049]
进一步地,所述干燥处理的温度为60~90℃,时间为24~48h。
[0050]
本发明实施例的另一个方面还提供了前述的赖氨酸基碳量子点缓蚀剂于金属基材表面防腐领域的用途。
[0051]
进一步地,所述金属基材包括碳钢、铜、铁、合金中的任意一种,且不限于此。
[0052]
进一步地,所述金属基材可用于石油行业、海洋工业、国防工业、机械行业、造纸行业、交通运输平台等,但不限于此。
[0053]
本发明中的赖氨酸基碳量子点缓蚀剂可用于钢铁、化工、石油、电力、造纸、炼油、船舶、储存、交通等领域。
[0054]
本发明实施例的另一个方面还提供了一种金属基材的表面防护方法,其包括:将金属基材的表面浸泡于前述的赖氨酸基碳量子点缓蚀剂溶液中,从而实现对金属基材的防护。
[0055]
藉由上述技术方案,本发明提供的赖氨酸基碳量子点缓蚀剂在赖氨酸的基础上增加了更多的活性位点,提高了与金属表面化学键合的几率,从而降低金属的腐蚀速率;同时,赖氨酸基碳量子点良好的水溶性能有效提高缓蚀剂在水环境下的分散性。
[0056]
综上所述,本发明通过高温裂解法制备的缓蚀剂水溶性好、防腐性能优良,可应用在钢铁、化工、石油、电力、造纸、炼油、船舶、储存、交通等行业中,尤其有望在化工设备、钢铁、石油、海上平台等大型设备上取得应用,将本发明的缓蚀剂用于金属基体表面,还可以提高基体的使用寿命。
[0057]
下面结合若干优选实施例及附图对本发明的技术方案做进一步详细说明,本实施例在以发明技术方案为前提下进行实施,给出了详细的实施方式和具体的操作过程,但本发明的保护范围不限于下述的实施例。
[0058]
下面所用的实施例中所采用的实验材料,如无特殊说明,均可由常规的生化试剂公司购买得到。
[0059]
对比例1
[0060]
首先对q235碳钢基底先进行除油处理,然后通过焊锡将铜导线焊接至碳钢表面,再密封于ab胶(3:1)中,仅露出1cm
×
1cm的测试面,接着分别用400#、800#、1500#的砂纸对工作面进行打磨20min,最后用乙醇冲洗,吹干。处理完后将碳钢基底作为工作电极,饱和甘汞电极作为参比电极,铂片作为对电极进行电化学测试,其在1m hcl溶液中的电化学阻抗谱及极化曲线可参见图2a-图2b和图3。
[0061]
对比例2
[0062]
首先对q235碳钢基底先进行除油处理,然后通过焊锡将铜导线焊接至碳钢表面,再密封于ab胶(3:1)中,仅仅露出1cm
×
1cm的测试面,接着分别用400#、800#、1500#的砂纸对工作面进行打磨20min,最后用乙醇冲洗,吹干。处理完后将碳钢基底作为工作电极,饱和甘汞电极作为参比电极,铂片作为对电极进行电化学测试,其在3.5%nacl溶液中的电化学阻抗谱及极化曲线可参见图4a-图4b和图5。
[0063]
对比例3
[0064]
将柠檬酸、苏氨酸、亮氨酸、天冬氨酸各2g置于烧杯中,随后转移至干燥箱中,加热温度设置为210℃,加热时间2h。待反应结束后,向烧杯中加入30ml去离子水,搅拌10min后再超声处理10min,将所得到的水溶液进行过滤和离心处理,离心过程中转速为10000r/min,之后进行透析处理,透析袋分子量为2kd。最后将透析液放入真空干燥箱中干燥处理,温度为60℃,得到碳量子点缓蚀剂。随后将一定量的碳量子点加入至1m hcl溶液中,配置浓度为200mg/l的缓蚀剂溶液。将对比例中制备的电极置于上述溶液中进行电化学测量,最终得到的电化学阻抗谱如图6a-图6b所示。在抗菌性能方面,选用大肠杆菌和金黄色葡萄球菌为研究对象。经测试,柠檬酸、苏氨酸、亮氨酸、天冬氨酸碳量子点对大肠杆菌和金黄色葡萄球菌的抑菌率约为8~15%和12~20%。
[0065]
实施例1
[0066]
将2g赖氨酸置于烧杯中,随后转移至干燥箱中,加热温度设置为210℃,加热时间2h。待反应结束后,向烧杯中加入30ml去离子水,搅拌10min后再超声处理10min,将所得到的水溶液进行过滤和离心处理,离心过程中转速为10000r/min,之后进行透析处理,透析袋分子量为2kd。最后将透析液放入真空干燥箱中干燥处理,温度为60℃,得到赖氨酸基碳量子点缓蚀剂,其红外表征如图7所示。随后将一定量的赖氨酸基碳量子点加入至1m hcl溶液中,配置浓度为25,50,100,200mg/l的缓蚀剂溶液。将对比例1中制备的电极置于上述溶液中进行电化学测量,最终得到的电化学阻抗谱如图8a-图8b所示。通过抗菌实验发现,赖氨酸基碳量子点对大肠杆菌和金黄色葡萄球菌的抑菌率约为81%和90%。
[0067]
实施例2
[0068]
将2g赖氨酸置于烧杯中,随后转移至干燥箱中,加热温度设置为200℃,加热时间2h。待反应结束后,向烧杯中加入30ml去离子水,搅拌10min后再超声处理10min,将所得到的水溶液进行过滤和离心处理,离心过程中转速为10000r/min,之后进行透析处理,透析袋分子量为2kd。最后将透析液放入真空干燥箱中干燥处理,温度为60℃,得到赖氨酸基碳量子点缓蚀剂。随后将一定量的赖氨酸基碳量子点加入至1m hcl溶液中,配置浓度为25,50,100,200mg/l的缓蚀剂溶液。将对比例1中制备的电极置于上述溶液中进行电化学测量,最终得到的极化曲线及腐蚀电流密度如图9a-图9b所示。同时,在浸泡后利用失重法对基体的腐蚀速率进行计算分析,结果如图10所示。通过抗菌实验发现,赖氨酸基碳量子点对大肠杆菌和金黄色葡萄球菌的抑菌率约为78%和86%。
[0069]
实施例3
[0070]
将2g赖氨酸置于烧杯中,随后转移至干燥箱中,加热温度设置为210℃,加热时间2h。待反应结束后,向烧杯中加入30ml去离子水,搅拌10min后再超声处理10min,将所得到的水溶液进行过滤和离心处理,离心过程中转速为10000r/min,之后进行透析处理,透析袋分子量为2kd。最后将透析液放入真空干燥箱中干燥处理,温度为60℃,得到赖氨酸基碳量子点缓蚀剂。随后将一定量的赖氨酸基碳量子点加入至3.5%nacl溶液中,制备浓度为25,50,100,200mg/l的缓蚀剂溶液。将对比例1中制备的电极置于上述溶液中进行电化学测量,最终得到的电化学阻抗谱如图11a-图11b所示。通过抗菌实验发现,赖氨酸基碳量子点对大肠杆菌和金黄色葡萄球菌的抑菌率约为80%和89%。
[0071]
实施例4
[0072]
将2g赖氨酸置于烧杯中,随后转移至干燥箱中,加热温度设置为200℃,加热时间2h。待反应结束后,向烧杯中加入30ml去离子水,搅拌10min后再超声处理10min,将所得到的水溶液进行过滤和离心处理,离心过程中转速为10000r/min,之后进行透析处理,透析袋分子量为2kd。最后将透析液放入真空干燥箱中干燥处理,温度为60℃,得到赖氨酸基碳量子点缓蚀剂。随后将一定量的赖氨酸基碳量子点加入至3.5%nacl溶液中,配置浓度为25,50,100,200mg/l的缓蚀剂溶液。将对比例1中制备的电极置于上述溶液中进行电化学测量,最终得到的极化曲线及腐蚀电流密度如图12a-图12b所示。同时,在浸泡后利用失重法对基体的腐蚀速率进行计算分析,结果如图13所示。通过抗菌实验发现,赖氨酸基碳量子点对大肠杆菌和金黄色葡萄球菌的抑菌率约为81%和90%。
[0073]
实施例5
[0074]
将2g赖氨酸置于烧杯中,随后转移至干燥箱中,加热温度设置为210℃,加热时间2.5h。待反应结束后,向烧杯中加入30ml去离子水,搅拌10min后再超声处理10min,将所得到的水溶液进行过滤和离心处理,离心过程中转速为10000r/min,之后进行透析处理,透析袋分子量为2kd。最后将透析液放入真空干燥箱中干燥处理,温度为60℃,得到赖氨酸基碳量子点缓蚀剂。随后将一定量的赖氨酸基碳量子点加入至1m hcl溶液中,配置浓度为25,50,100mg/l的缓蚀剂溶液。将对比例1中制备的电极置于上述溶液中进行电化学测量,最终得到的电化学阻抗谱如图14a-图14b所示。通过抗菌实验发现,赖氨酸基碳量子点对大肠杆菌和金黄色葡萄球菌的抑菌率约为75%和87%。
[0075]
实施例6
[0076]
将2g赖氨酸置于烧杯中,随后转移至干燥箱中,加热温度设置为180℃,加热时间2h。待反应结束后,向烧杯中加入30ml去离子水,搅拌10min后再超声处理10min,将所得到的水溶液进行过滤和离心处理,离心过程中转速为10000r/min,之后进行透析处理,透析袋分子量为2kd。最后将透析液放入真空干燥箱中干燥处理,温度为60℃,得到赖氨酸基碳量子点缓蚀剂。随后将一定量的赖氨酸基碳量子点加入至3.5%nacl溶液中,配置浓度为25,50,100mg/l的缓蚀剂溶液。将对比例1中制备的电极置于上述溶液中进行电化学测量,最终得到的电化学阻抗谱如图15a-图15b所示。通过抗菌实验发现,赖氨酸基碳量子点对大肠杆菌和金黄色葡萄球菌的抑菌率约为77%和86%。
[0077]
实施例7
[0078]
将2g赖氨酸置于烧杯中,随后转移至干燥箱中,加热温度设置为150℃,加热时间3h。待反应结束后,向烧杯中加入30ml去离子水,搅拌20min后再超声处理15min,将所得到的水溶液进行过滤和离心处理,离心过程中转速为8000r/min,之后进行透析处理,透析袋分子量为1kd。最后将透析液放入真空干燥箱中干燥处理,温度为80℃,得到赖氨酸基碳量子点缓蚀剂。随后将一定量的赖氨酸基碳量子点加入至1m hcl溶液中,配置浓度为25,50,100mg/l的缓蚀剂溶液。将对比例1中制备的电极置于上述溶液中进行电化学测量,最终得到的电化学阻抗谱如图16a-图16b所示。通过抗菌实验发现,赖氨酸基碳量子点对大肠杆菌和金黄色葡萄球菌的抑菌率约为79%和85%。
[0079]
实施例8
[0080]
将2g赖氨酸置于烧杯中,随后转移至干燥箱中,加热温度设置为250℃,加热时间1h。待反应结束后,向烧杯中加入30ml去离子水,搅拌15min后再超声处理20min,将所得到的水溶液进行过滤和离心处理,离心过程中转速为10000r/min,之后进行透析处理,透析袋分子量为3kd。最后将透析液放入真空干燥箱中干燥处理,温度为90℃,得到赖氨酸基碳量子点缓蚀剂。随后将一定量的赖氨酸基碳量子点加入至1m hcl溶液中,配置浓度为25,50,100mg/l的缓蚀剂溶液。将对比例1中制备的电极置于上述溶液中进行电化学测量,最终得到的电化学阻抗谱如图17a-图17b所示。通过抗菌实验发现,赖氨酸基碳量子点对大肠杆菌和金黄色葡萄球菌的抑菌率约为80%和84%。
[0081]
对比对比例1、实施例1、2、5中所制备的赖氨酸基碳量子点缓蚀剂在hcl环境下对碳钢的电化学行为进行表征,将碳钢浸泡于具有不同缓蚀剂浓度的1m hcl溶液中,浸泡24h后,采用上海辰华chi660e电化学工作站监测交流阻抗谱及极化曲线。如图2a-图2b所示,碳钢在1m hcl溶液中浸泡24h后的阻抗为70ωcm2。如图8a-图8b所示,在添加25、50、100、
200mg/l碳量子点缓蚀剂后,碳钢的阻抗依次为160、580、750、1200ωcm2,较之于未添加缓蚀剂前,碳钢的低频阻抗模量依次提高了2.3、8.3、10.7、17.1倍。如图14a-图14b所示,随着加热时间的延长,在添加25、50、100mg/l碳量子点缓蚀剂后,碳钢的阻抗依次为380、760、1000ωcm2,较之于实例1也到一定程度的提升。如图3所示,碳钢在1m hcl溶液中浸泡24h后的腐蚀电流密度为3.1
×
10-4
a cm2。如图9a-图9b所示,较之于未添加缓蚀剂,在添加25、50、100、200mg/l碳量子点缓蚀剂后,碳钢的腐蚀电流密度依次降低了6.6、8.7、14.5、21.1倍,且相应的腐蚀抑制效率为86.8%、89.7%、93.5%、95.5%,表明缓蚀剂在1m hcl环境下对碳钢有优异的防护效果。如图10所示,碳钢在1m hcl溶液中浸泡24h后的腐蚀速率最高。随着缓蚀剂浓度的增加,碳钢的腐蚀速率急剧下降,这主要是因为碳钢表面形成了有效的吸附膜,该膜的本质是赖氨酸基碳量子点与钢表面之间的化学吸附和物理吸附。其中,化学吸附主要归因于类吡啶n和类吡咯n原子。由于孤对电子的存在,它们可以轻易地填充至铁原子外未被占据的3d轨道,然后在杂原子和钢基体之间形成化学配位键,降低碳钢表面的金属活性位点。同时,赖氨酸基碳量子点中剩余的类石墨n原子会聚集到钢表面,进而诱发团聚效应,减少碳钢在腐蚀环境下的暴露面积(物理吸附)。这两种行为的协同作用使得赖氨酸基碳量子点在腐蚀介质中表现出优异的防护性能。
[0082]
对比对比例2、实施例3、4、6中所制备的赖氨酸基碳量子点缓蚀剂在nacl环境下对碳钢的电化学行为进行表征,将碳钢浸泡于不同缓蚀剂浓度下3.5%nacl溶液中浸泡24h,浸泡过程中,采用上海辰华chi660e电化学工作站监测交流阻抗谱及极化曲线。如图4a-图4b所示,碳钢在3.5%nacl溶液中浸泡24h后的阻抗为185ωcm2。如图11a-图11b所示,在添加25、50、100、200mg/l碳量子点缓蚀剂后,碳钢的阻抗依次为630、1250、1600、1900ωcm2,较之于未添加缓蚀剂前,碳钢的低频阻抗模量依次提高了3.4、6.8、8.6、10.3倍。如图15a-图15b所示,随着加热温度的降低,在添加25、50、100mg/l碳量子点缓蚀剂后,碳钢的阻抗依次为450、1200、1550ωcm2,较之于实例3也到轻微的下降。如图5所示,碳钢在3.5%nacl溶液中浸泡24h后的腐蚀电流密度为1.7
×
10-4
a cm2。如图12a-图12b所示,较之于未添加缓蚀剂,在添加25、50、100、200mg/l碳量子点缓蚀剂后,碳钢的腐蚀电流密度依次降低了8.7、16.3、22.9、24.8倍,且相应的腐蚀抑制效率为89.7%、94.2%、95.8%、96.2%,表明缓蚀剂在3.5%nacl环境下对碳钢有优异的防护效果。如图13所示,碳钢在3.5%nacl溶液中浸泡24h后的腐蚀速率最高。随着缓蚀剂浓度的增加,碳钢的腐蚀速率急剧下降。
[0083]
对比对比例1、实施例7、8中所制备的赖氨酸基碳量子点缓蚀剂在hcl环境下对碳钢的电化学行为进行表征,将碳钢浸泡于具有不同缓蚀剂浓度的1m hcl溶液中,浸泡24h后,采用上海辰华chi660e电化学工作站监测交流阻抗谱。如图2a-图2b所示,碳钢在1m hcl溶液中浸泡24h后的阻抗为70ωcm2。如图16a-图16b所示,在添加25、50、100mg/l碳量子点缓蚀剂后,碳钢的阻抗依次为380、740、1050ωcm2,较之于空白环境,碳钢的低频阻抗模量依次提高了5.4、10.6、15倍。如图17a-图17b所示,在添加25、50、100mg/l碳量子点缓蚀剂后,碳钢的阻抗依次为370、720、1000ωcm2,较之于空白环境,碳钢的低频阻抗模量依次提高了5.3、10.3、14.3倍。
[0084]
对比对比例3和实施例1中所制备的碳量子点缓蚀剂在hcl环境下对碳钢的电化学行为进行表征,将碳钢浸泡于200mg/l浓度下1m hcl溶液中浸泡24h,浸泡过程中,采用上海辰华chi660e电化学工作站监测交流阻抗谱。如图6a-图6b所示,在添加200mg/l柠檬酸、苏
氨酸、亮氨酸、天冬氨酸碳量子点缓蚀剂后,碳钢的阻抗依次为130、210、270、330ωcm2。而添加200mg/l赖氨酸基碳量子点缓蚀剂后,如图8a-图8b所示,碳钢的阻抗约为1200ωcm2,较之于柠檬酸、苏氨酸、亮氨酸、天冬氨酸碳量子点分别提高了9.2、5.7、4.4、3.6倍,这表明赖氨酸基碳量子点相比于其他氨基酸基碳量子点具有更好的防护效果。通过对比抗菌性能发现,赖氨酸基碳量子点对大肠杆菌和金黄色葡萄球菌的抑菌率是其他氨基酸基碳量子点的4~6倍。
[0085]
此外,本案发明人还参照前述实施例,以本说明书述及的其它原料、工艺操作、工艺条件进行了试验,并均获得了较为理想的结果。
[0086]
应当理解,本发明的技术方案不限于上述具体实施案例的限制,凡是在不脱离本发明宗旨和权利要求所保护的范围情况下,根据本发明的技术方案做出的技术变形,均落于本发明的保护范围之内。
再多了解一些
本文用于企业家、创业者技术爱好者查询,结果仅供参考。