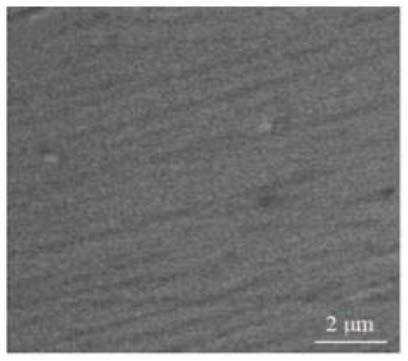
1.本发明涉及涂层制备技术领域,且特别涉及一种非晶态难熔金属合金抗烧蚀涂层及其制备方法和应用。
背景技术:
2.火炮是现代战场两军对战使用的一种极其重要的火器军事装备。火炮是指口径在20mm以上,通过发射药反应产生能量抛射弹丸的身管武器,身管是火炮最贵重的构件。各国一直在致力于改进火炮性能,以期获得更远的射程、更短的发射间隔、更精确的打击和更大的毁伤威力。因此,越来越多的新型高能火药被作为火炮的发射药使用。新型高能发射药燃烧虽然为弹丸提供更大的初速,但是使火炮关键部件遭受更大的燃烧压力负载与燃烧气体烧蚀——火炮身管内膛表面首当其冲。因此,随着弹药向高初速、远射程方向发展,身管需要适应高载、高温等更加极端恶劣的工况条件,身管的烧蚀与磨损问题成为制约高性能火炮发展的亟待解决的重大关键共性技术问题。身管内膛表面的抗烧蚀耐磨损性能是身管延寿的关键因素,国内外专家学者广泛认为在身管内壁开发新型抗烧蚀涂层技术至关重要。迄今为止,因为电镀cr镀层具有硬度高、很好的耐磨性、抗烧蚀性和耐腐蚀性,同时cr熔点高(1907℃),是最常见的身管内壁抗烧蚀涂层。然而,电镀cr镀层自带的微裂纹是高温发射药气体进入身管基体的天然通道,严重破坏镀层与基体界面的结合,最后造成镀层脱落。同时,镀液中cr
6
是强致癌物质,危害自然环境,废液处理成本高。因此,身管内膛表面延寿迫切需要找到一种替代电镀cr涂层的绿色技术。
3.新型火炮身管内膛涂层技术不断涌现,如:电火花沉积cr、w合金,熔盐电镀难熔金属w、ta,磁控溅射ta等。ta由于熔点高(2996℃)、耐磨性好、抗腐蚀性高、表面易钝化,在身管内膛涂层材料中常常作为首选材料。磁控溅射是一种备受关注的ta涂层制备技术。然而,ta溅射涂层一般由α-ta和β-ta相组成,α-ta韧性好而β-ta脆性大。因此α-ta所占比例越高,涂层性能越好。但是,仅有单相的α-ta涂层在沉积过程中需要较高的加热温度,恶化炮钢力学性能。同时,ta的硬度偏低,甚至低于炮钢基体的硬度,这样会导致ta涂层的耐磨性不足。若开发钽合金涂层有望成为一种新型高性能身管内膛延寿涂层制备新方法。鉴于此,特提出本发明。
技术实现要素:
4.本发明的目的在于提供一种非晶态难熔金属合金抗烧蚀涂层及其制备方法和应用,其通过非晶态难熔金属涂层有效地避免了纯ta晶态涂层的组织脆性、硬度低和耐磨性不足等有关问题,兼具ta、cr涂层的性能优势,同时也具备非晶涂层的性能特点。
5.本发明的技术方案是:
6.一种非晶态难熔金属合金抗烧蚀涂层,采用真空磁控溅射技术在基体表面形成非晶态难熔金属合金抗烧蚀涂层,非晶态难熔金属合金抗烧蚀涂层的元素包括ta、cr,其原子百分比分别为cr 25%~75%和ta 25%~75%。
7.所述的非晶态难熔金属合金抗烧蚀涂层,非晶态难熔金属合金抗烧蚀涂层的厚度为1~6μm。
8.所述的非晶态难熔金属合金抗烧蚀涂层的制备方法,具体包括如下步骤:
9.(1)将高纯cr和高纯ta分别制备成纯cr单质金属靶材和纯ta单质金属靶材;
10.(2)采用真空磁控溅射技术实施双靶材共溅射方式,在炮钢基体表面形成非晶态难熔金属合金抗烧蚀涂层。
11.所述的非晶态难熔金属合金抗烧蚀涂层的制备方法,纯cr单质金属靶材和纯ta单质金属靶材分别是通过高温熔炼和粉末冶金的方式进行制备。
12.所述的非晶态难熔金属合金抗烧蚀涂层的制备方法,步骤(2)中,炮钢基体经过预处理:首先以炮钢pcrni3mova为基体,对基体表面依次采用#240、#600、#1000、#1500、#2000砂纸进行打磨以及抛光处理,然后分别用丙酮、酒精和去离子水超声清洗,吹干。
13.所述的非晶态难熔金属合金抗烧蚀涂层的制备方法,步骤(2)中,采用真空磁控溅射时,在衬底真空度小于或等于3
×
10-3
pa、基体温度350℃的条件下进行,基体直流偏压为-100v~0v,工作气压为0.3~0.5pa,氩气流量20sccm。
14.所述的非晶态难熔金属合金抗烧蚀涂层的制备方法,步骤(2)中,纯cr单质金属靶材采用直流电源,功率为20~50w;纯ta单质金属靶材采用射频电源,功率为80~180w。
15.所述的非晶态难熔金属合金抗烧蚀涂层的应用,非晶态难熔金属合金抗烧蚀涂层在制备火药发射军事装备的热端部件中的应用。
16.所述的非晶态难熔金属合金抗烧蚀涂层的应用,采用真空磁控溅射技术在基体表面形成非晶态难熔金属合金抗烧蚀涂层,在非晶态难熔金属合金抗烧蚀涂层表面涂覆高温防护涂层。
17.所述的非晶态难熔金属合金抗烧蚀涂层的应用,高温防护涂层为nicr涂层或nicral涂层,高温防护涂层的厚度为50~200μm。
18.本发明的设计思想是:
19.本发明非晶态难熔金属合金抗烧蚀涂层应用在炮钢pcrni3mova(军用高强度中碳合金钢)基体表面,采用磁控溅射的方式进行制备,其中薄膜包含的元素为cr和ta。在高真空热处理的过程中,利用难熔金属合金涂层的缓慢扩散和晶化转变作用,形成难熔金属的纳米合金涂层能够有效缓解基体的高温烧蚀,同时减少涂层因高温烧蚀和磨损而脱落。
20.在钽铬金属合金(如:ta
62.5
cr
37.5
、ta
41.7
cr
58.3
、ta
75
cr
25
、ta
35
cr
65
、ta
40
cr
60
、ta
50
cr
50
、ta
60
cr
40
、ta
70
cr
30
等)中,cr和ta的协同作用机理如下:根据磁控溅射理论,当涂层的晶化转变温度高于磁控溅射的试样加热温度,易制得非晶态涂层。依据差示扫描量热法(dsc),tacr合金的晶化转变温度是374℃,高于试样加热温度350℃,因此tacr涂层易形成非晶态合金组织。该非晶态组织经过真空扩散退火可形成纳米晶或纳米与非晶复合材料涂层,该纳米或纳米复合涂层兼具难熔金属涂层及纳米/复合涂层的优点,具有高硬度、高韧性、高熔点、良好耐磨性和抗烧蚀性等诸多性能。
21.本发明的优点及有益效果如下:
22.1、本发明提供一种非晶态难熔金属合金抗烧蚀涂层及其制备工艺,其通过利用多种元素形成非晶态难熔金属合金抗烧蚀涂层,其中包括cr和ta,该非晶态难熔金属合金抗烧蚀涂层与基体之间具有良好的结合力以及匹配性,能够有效抵御高温火药气体的烧蚀,
同时减少基体表面涂层的脱落,提高涂层抗高温氧化及热腐蚀能力,同时提高涂层的摩擦学性能,延长涂层体系的服役寿命,非晶态难熔金属合金抗烧蚀涂层抗烧蚀效果相比于炮钢基体或传统金属涂层材料有明显提升。
23.2、本发明非晶态难熔金属合金抗烧蚀涂层可以应用在火药发射军事装备领域,为提升部件服役寿命和火炮身管延寿提供理论和技术支持。
附图说明
24.为了更清楚地说明本发明实施例的技术方案,下面将对实施例中所需要使用的附图作简单地介绍,可以看到,以下附图仅是实验实施例的一部分,以下简单示图对于本领域普通技术人员来讲,在不付出创造性劳动的前提下,还可以根据这些附图获得其他相关的附图。
25.图1为本实施例中ta-cr非晶态合金涂层的电子显微镜(sem)表面图和截面形貌图以及x射线衍射图;其中,图1(a)为电子显微镜表面图,图1(b)为电子显微镜截面图,图1(c)为x射线衍射图,横坐标2θ(
°
)代表衍射角,纵坐标intensity(counts)代表相对强度。
26.图2为ta-cr非晶态合金涂层的纳米力学性能曲线。
27.图3为实施例中ta-cr非晶态合金涂层于900℃大气条件下氧化4h后的表面和截面形貌图;其中,图3(a)为表面形貌图,图3(b)为截面形貌图。
28.图4为实施例中炮钢pcrni3mova基体、ta-cr非晶态合金涂层样品于900℃大气与时间4h条件下的表面xrd谱;其中,图4(a)为炮钢pcrni3mova基体的表面xrd谱,图4(b)为ta-cr非晶态合金涂层的表面xrd谱,横坐标2θ(
°
)代表衍射角,纵坐标intensity(counts)代表相对强度。
29.图5为实施例中炮钢pcrni3mova基体、ta-cr非晶态合金涂层样品于900℃大气与时间4h条件下的氧化动力学曲线。
具体实施方式
30.在具体实施过程中,本发明非晶态难熔金属合金抗烧蚀涂层及其制备方法,在炮钢pcrni3mova基体表面形成非晶态难熔金属合金抗烧蚀涂层,抗烧蚀元素为cr和ta,阻抗烧蚀元素按照原子百分比进行计算,抗烧蚀元素保证在cr 25%~75%和ta25%~75%(优选为cr 30%~70%和ta 30%~70%)。为了保证阻非晶态难熔金属合金抗烧蚀涂层是非晶相,可以通过控制靶材的制备,将高纯cr(纯度为99.99wt%)和高纯ta(纯度为99.99wt%)元素独立制成单一金属靶材,采用真空磁控溅射技术实施双靶材共溅射方式,可以控制涂层的元素含量,在基体表面形成非晶态难熔金属合金抗烧蚀涂层,cr靶功采用直流电源,ta靶采用射频电源;具体的,为了保证清晰表明涂层的抗烧蚀性能,基体选用了炮钢pcrni3mova,选用的材料不做限定。非晶态难熔金属合金抗烧蚀涂层的厚度为2~3μm左右,该厚度既不会明显增加部件的重量(不影响应用性),又能够不降低基体合金的尺寸精度。涂层的厚度可以根据需要进行调控工艺参数来改变,本实施例仅是根据需求所做。
31.采用真空磁控溅射技术形成非晶态难熔金属合金抗烧蚀涂层,具体参数如下:背景真空度小于或等于3
×
10-3
pa、基体温度350℃、基体直流偏压为-150~0v、靶基距6cm、工作气压为0.3~0.5pa。需要说明的是,通过进一步优化磁控溅射的工艺参数,使形成的涂层
结构致密、成分均匀、抗烧蚀性能更好。通过在上述参数范围内进行非晶态难熔金属合金抗烧蚀涂层制备能够有效的保证涂层的综合性能以及抗烧蚀效果。在本发明的其他实施例中,工艺参数还可以根据需求进行调整。
32.为使本发明实施例的目的、技术方案和优点更加清楚,下面将对本发明实施例中的技术方案进行清楚、完整地描述。很明显看出,所描述的只是实施例中的一部分,而不是实施例中的全部。下面,对本发明实施例提供的非晶态难熔金属合金抗烧蚀涂层制备方法和应用进行具体说明。
33.实施例1
34.本实施例提供一种非晶态难熔金属合金抗烧蚀涂层的制备方法,其通过以下方法制备得到:
35.(1)靶材制备:将cr金属粉末分别按一定重量进行称量,采用真空熔炼的方法制备成的单一金属材料作为磁控溅射的靶材,即cr靶材;将ta金属粉末按一定重量进行称量,采用粉末冶金的方法制备成的单一金属材料作为磁控溅射的靶材,即ta靶材。
36.(2)基体预处理:以炮钢pcrni3mova为基体,对基体表面依次采用#240、#600、#1000、#1500、#2000砂纸进行打磨以及抛光处理,然后分别用丙酮、酒精和去离子水超声清洗,吹干。
37.(3)非晶态难熔金属合金抗烧蚀涂层沉积:采用磁控溅射在清洗后的基体表面沉积非晶态难熔金属合金抗烧蚀涂层,其工艺参数为:背景真空度2
×
10-3
pa,基体温度350℃,cr靶采用直流电源、功率为30w,ta靶采用射频电源、功率为120w,基体直流偏压为-80v、靶基距6cm,工作气压为0.3pa,氩气流量为20sccm。溅射时间2h控制涂层厚度为1.5μm左右,得到含有非晶态难熔金属合金抗烧蚀涂层ta
62.5
cr
37.5
(下角标为该元素的原子百分比)材料。
38.实施例2
39.本实施例提供一种非晶态难熔金属合金抗烧蚀涂层的制备方法,其与实施例1的区别仅在于:在步骤(3)中,涂层沉积的工艺参数为:背景真空度3
×
10-3
pa,基体温度350℃,cr靶采用直流电源、功率为40w,ta靶采用射频电源、功率为100w,基体直流偏压为-80v、靶基距6cm,工作气压为0.3pa,氩气流量为20sccm,通过控制改变溅射时间为4h达到厚度大约3μm,得到含有非晶态难熔金属合金抗烧蚀涂层ta
41.7
cr
58.3
(下角标为该元素的原子百分比)材料。
40.实施例3
41.本实施例提供一种非晶态难熔金属合金抗烧蚀涂层的制备方法,其与实施例1的区别仅在于:
42.在步骤(3)中,涂层沉积的工艺参数为:背景真空度1
×
10-3
pa,基体温度350℃,cr靶采用直流电源、功率为20w,ta靶采用射频电源、功率为90w,基体直流偏压为-80v、靶基距6cm,工作气压为0.3pa,氩气流量为20sccm,通过控制改变溅射时间为6h达到厚度大约4.5μm,得到含有非晶态难熔金属合金抗烧蚀涂层ta
75
cr
25
(下角标为该元素的原子百分比)材料。
43.实施例4
44.本实施例提供一种非晶态难熔金属合金抗烧蚀涂层的制备方法,其与实施例1的区别仅在于:
45.在步骤(3)中,涂层沉积的工艺参数为:背景真空度2.5
×
10-3
pa,基体温度350℃,cr靶采用直流电源、功率为50w,ta靶采用射频电源、功率为85w,基体直流偏压为-80v、靶基距6cm,工作气压为0.3pa,氩气流量为20sccm。溅射时间2h控制涂层厚度为1.5μm左右,得到含有非晶态难熔金属合金抗烧蚀涂层ta
35
cr
65
(下角标为该元素的原子百分比)材料。
46.实施例5
47.本实施例提供一种非晶态难熔金属合金抗烧蚀涂层的制备方法,其与实施例1的区别仅在于:
48.在步骤(3),涂层沉积的工艺参数为:背景真空度1.5
×
10-3
pa,基体温度350℃,cr靶采用直流电源、功率为50w,ta靶采用射频电源、功率为100w,基体直流偏压为-80v、靶基距6cm,工作气压为0.3pa,氩气流量为20sccm。溅射时间2h控制涂层厚度为1.5μm左右,得到含有非晶态难熔金属合金抗烧蚀涂层ta
40
cr
60
(下角标为该元素的原子百分比)材料。
49.实施例6
50.本实施例提供一种非晶态难熔金属合金抗烧蚀涂层的制备方法,其与实施例1的区别仅在于:
51.在步骤(3)中,涂层沉积的工艺参数为:背景真空度0.5
×
10-3
pa,基体温度350℃,cr靶采用直流电源、功率为40w,ta靶采用射频电源、功率为120w,基体直流偏压为-80v、靶基距6cm,工作气压为0.3pa,氩气流量为20sccm。溅射时间2h控制涂层厚度为1.5μm左右,得到含有非晶态难熔金属合金抗烧蚀涂层ta
50
cr
50
(下角标为该元素的原子百分比)材料。
52.实施例7
53.本实施例提供一种非晶态难熔金属合金抗烧蚀涂层的制备方法,其与实施例1的区别仅在于:
54.在步骤(3)中,涂层沉积的工艺参数为:背景真空度1.2
×
10-3
pa,基体温度350℃,cr靶采用直流电源、功率为25w,ta靶采用射频电源、功率为150w,基体直流偏压为-80v、靶基距6cm,工作气压为0.3pa,氩气流量为20sccm。溅射时间2h控制涂层厚度为1.5μm左右,得到含有非晶态难熔金属合金抗烧蚀涂层ta
60
cr
40
(下角标为该元素的原子百分比)材料。
55.实施例8
56.本实施例提供一种非晶态难熔金属合金抗烧蚀涂层的制备方法,其与实施例1的区别仅在于:
57.在步骤(3)中,涂层沉积的工艺参数为:背景真空度1.8
×
10-3
pa,基体温度350℃,cr靶采用直流电源、功率为20w,ta靶采用射频电源、功率为180w,基体直流偏压为-80v、靶基距6cm,工作气压为0.3pa,氩气流量为20sccm。溅射时间2h控制涂层厚度为1.5μm左右,得到含有非晶态难熔金属合金抗烧蚀涂层ta
70
cr
30
(下角标为该元素的原子百分比)材料。
58.试验例1
59.对实施例1中非晶态难熔金属合金抗烧蚀涂层进行结构表征,包括扫描电镜和xrd检测;非晶态难熔金属合金抗烧蚀涂层表面结果见图1(a)和阻扩散涂层截面结果见图1(b),其中:图1(a)为非晶态难熔金属合金抗烧蚀涂层sem表面图,图1(b)为扩散障sem截面图;对实施例1中得到的非晶态难熔金属合金抗烧蚀涂层进行xrd检测其相结构,见图1(c)。
60.如图1(a)和图1(b)所示,非晶态难熔金属合金抗烧蚀涂层表面和截面sem图可以看出,涂层表面很均匀,通过截面可以看出涂层结构致密且成分均匀。如图1(c)所示,采用
xrd检测其相结构,涂层为非晶相。
61.试验例2
62.对实施例2和实施3中非晶态难熔金属合金抗烧蚀涂层进行纳米力学性能测试,结果见图2;三种ta-cr合金涂层随着ta含量降低,ta-cr涂层的硬度、弹性模量与韧性均升高。
63.试验例3
64.实施例1和对比例1中制备得到非晶态难熔金属合金抗烧蚀涂层的抗高温氧化行为,将实施例1中得到的非晶态难熔金属合金抗烧蚀涂层和炮钢基体的样品于900℃的条件下进行氧化试验,4h后该样品的表面、截面sem图以及xrd谱见图3和图4,图3为4h、900℃高温氧化结果,其中:图3(a)为实施例1中非晶态难熔金属合金抗烧蚀涂层的表面形貌,图3(b)为对比例1中非晶态难熔金属合金抗烧蚀涂层的截面形貌。图4为4h、900℃高温氧化后非晶态难熔金属合金抗烧蚀涂层的xrd谱。
65.图3结果显示,在900℃扩散4h后,图3(a)中非晶态难熔金属合金抗烧蚀涂层样品表面氧化均匀,未发生明显的涂层脱落。图3(b)非晶态难熔金属合金抗烧蚀涂层样品断面形貌表明涂层表面的氧化物膜致密,氧化物膜作为样品的面层与底层结合良好。
66.图4结果显示,在900℃扩散4h后,图4(a)中炮钢pcrni3mova基体的氧化4h后的氧化产物以fe的氧化物为主。图4(b)中非晶态难熔金属合金抗烧蚀涂层样品的氧化4h后的氧化产物以ta的氧化物为主。
67.图5结果显示,在900℃扩散4h后,图5明显观察到非晶态难熔金属合金抗烧蚀涂层比炮钢pcrni3mova基体的氧化动力学行为更平缓,非晶态难熔金属合金抗烧蚀涂层抑制了覆有涂层炮钢基体的氧化行为。
68.实施例结果表明,本发明以非晶态难熔金属合金抗烧蚀涂层及其制备技术为契机,将为火炮身管延寿提供新思路,促进延寿技术发展,产生显著的社会效益和经济效益。
69.对于任何熟悉本领域的技术人员而言,在不脱离本发明技术方案范围情况下,都可利用上述揭示的技术内容对本发明技术方案作出许多可能的变动和修饰,或修改为等同变化的等效实施例。因此,凡是未脱离本发明技术方案的内容,依据本发明的技术实质对以上实施例所做的任何简单修改、等同变化及修饰,均应仍属于本发明技术方案保护的范围内。
再多了解一些
本文用于企业家、创业者技术爱好者查询,结果仅供参考。