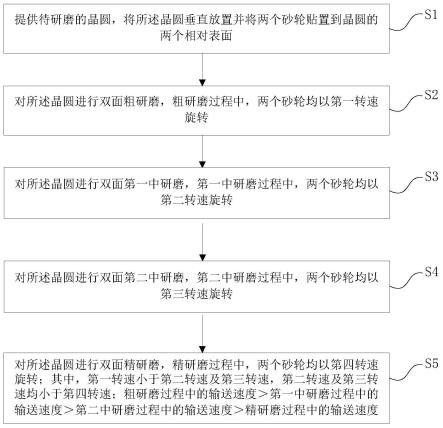
1.本发明涉及半导体工艺技术领域,特别是涉及一种双面研磨方法。
背景技术:
2.随着半导体制造技术的非常发展,器件的特征尺寸日益缩小而器件集成度日益提高,晶圆表面平坦度对生产良率的影响越来越大。现有技术中,晶棒切割后得到的晶圆都需要经过研磨和抛光等工艺以实现表面平坦化。这其中,研磨工艺主要是为了去除刚切割出的晶圆表面残留有树脂、颗粒等杂质的缺陷层和损伤层并实现晶圆的表面平坦化。具体地,现有的研磨工艺通常包括单面研磨和双面研磨(double side lapping)。其中,双面研磨的具体方法为:将晶圆水平放置,同时使用al2o3和压板同时覆盖晶圆的两侧对晶圆进行研磨,该研磨方法可以有效地消除晶圆表面呈波纹状的表面纳米形貌。但是,由于该方法要使用研磨浆料,容易对环境造成危害;而且现有技术中使用多步固定转速的旋转方式进行研磨,即从最初阶段的粗研磨到最终精研磨,各阶段的转速完全相同,导致研磨效果较差,砂轮消耗量过大。
技术实现要素:
3.鉴于以上所述现有技术的缺点,本发明的目的在于提供一种双面研磨方法,用于解决现有的双面研磨方法中,从最初阶段的粗研磨到最终精研磨,各阶段采用完全相同的转速,导致研磨效果较差,砂轮消耗量过大等问题。
4.为实现上述目的及其他相关目的,本发明提供一种双面研磨方法,所述双面研磨方法包括以下步骤:
5.s1:提供待研磨的晶圆,将所述晶圆垂直放置并将两个砂轮贴置到晶圆的两个相对表面;
6.s2:对所述晶圆进行双面粗研磨,粗研磨过程中,两个砂轮均以第一转速旋转;
7.s3:对所述晶圆进行双面第一中研磨,第一中研磨过程中,两个砂轮均以第二转速旋转;
8.s4:对所述晶圆进行双面第二中研磨,第二中研磨过程中,两个砂轮均以第三转速旋转;
9.s5:对所述晶圆进行双面精研磨,精研磨过程中,两个砂轮均以第四转速旋转;
10.其中,第一转速小于第二转速及第三转速,第二转速及第三转速均小于第四转速;粗研磨过程中的输送速度>第一中研磨过程中的输送速度>第二中研磨过程中的输送速度>精研磨过程中的输送速度。
11.可选地,所述第一转速为2500r/min,所述第二转速及第三转速均为3500r/min,所述第四转速为4000r/min。
12.可选地,粗研磨过程中的输送速度为240μm/min,第一中研磨过程中的输送速度为80μm/min,第二中研磨过程中的输送速度为60μm/min,精研磨过程中的输送速度为40μm/
min。
13.可选地,待研磨的晶圆垂直放置于一载体上,通过流体静压力平衡并与载体一起以低于1000r/min的转速旋转。
14.可选地,粗研磨过程中的研磨量和精研磨过程中的研磨量均小于第一中研磨过程中的研磨量以及第二中研磨过程的研磨量。
15.更可选地,待研磨晶圆的初始最大厚度为930μm,粗研磨过程中的研磨量为20μm,第一中研磨过程中的研磨量为50μm,第二中研磨过程中的研磨量为55μm,精研磨过程中的研磨量为10μm。
16.可选地,各研磨过程中还包括向晶圆表面供应冷却液的步骤。
17.更可选地,冷却液流量为1.6l/min。
18.可选地,两个砂轮的旋转方向相反。
19.如上所述,本发明的双面研磨方法,具有以下有益效果:本发明创造性地在不同的研磨阶段设定不同的砂轮转速以达到更理想的研磨效果,包括在起步粗研磨阶段使用较低的转速可有效减少砂轮与晶圆摩擦接触产生的高热量,而第一中研磨阶段和第二中研磨阶段采用相对较高的恒定转速,以在获得较快的研磨速率的同时控制研磨效果,而最终的精研磨转速则选择高速旋转以对晶圆表面进行细致的打磨,达到最佳的表面镜面效果,且在此过程中相应匹配不同的输送速度。由于输送速度与转速应成反比,当大输送速度时选用低转速高扭矩,故而起步阶段选择低速介入,然后逐步加大转速并降低输送速度,从而可加工出理想的产品。由于砂轮消耗主要来自研磨时产生的热量无法散发,所以降低起步阶段转速可有效减少砂轮发热现象,可有效延长砂轮使用寿命,从而极大降低研磨成本,可将砂轮消耗量由现有的2800片/套延长至3800片/套,晶圆的平均厚度波动可由现有的1.9um降低至1.0um,极大提升晶圆的表面平坦度。
附图说明
20.图1显示为本发明提供的双面研磨方法的流程示意图。
具体实施方式
21.以下通过特定的具体实例说明本发明的实施方式,本领域技术人员可由本说明书所揭露的内容轻易地了解本发明的其他优点与功效。本发明还可以通过另外不同的具体实施方式加以实施或应用,本说明书中的各项细节也可以基于不同观点与应用,在没有背离本发明的精神下进行各种修饰或改变。
22.请参阅图1。需要说明的是,本实施例中所提供的图示仅以示意方式说明本发明的基本构想,虽图示中仅显示与本发明中有关的组件而非按照实际实施时的组件数目、形状及尺寸绘制,其实际实施时各组件的形态、数量及比例可为一种随意的改变,且其组件布局型态也可能更为复杂。
23.如图1所示,本发明提供一种双面研磨方法,所述双面研磨方法包括以下步骤:
24.s1:提供待研磨的晶圆,将所述晶圆垂直放置并将两个砂轮贴置到晶圆的两个相对表面,即于晶圆的左右侧两个表面分别各设置一个砂轮,可称之为左砂轮和右砂轮,砂轮通常为金刚石砂轮,左右两个砂轮可通过相同或不同的马达驱动;
25.s2:对所述晶圆进行双面粗研磨,粗研磨过程中,两个砂轮均以第一转速旋转,经粗研磨以去除晶圆表面的损伤层及缺陷层;由于初始阶段,晶圆表面的粗糙度很大,故而初始阶段中,较低的砂轮转速可以降低摩擦的剧烈程度,并由此有效减少砂轮与晶圆摩擦接触产生的高热量,降低砂轮损耗;
26.s3:对所述晶圆进行双面第一中研磨,第一中研磨过程中,两个砂轮均以第二转速旋转,第二转速大于第一转速;
27.s4:对所述晶圆进行双面第二中研磨,第二中研磨过程中,两个砂轮均以第三转速旋转,第三转速同样大于第一转速;在中研磨过程中采用较高转速以提高研磨速率,同时在两个中研磨过程中配合不同的输送速度以进一步改善研磨效果;
28.s5:对所述晶圆进行双面精研磨,精研磨过程中,两个砂轮均以第四转速旋转,第四转速大于第二转速及第三转速;即精研磨过程中采用较高的转速以修正晶圆的镜面形貌;
29.并且,粗研磨过程中的输送速度>第一中研磨过程中的输送速度>第二中研磨过程中的输送速度>精研磨过程中的输送速度。
30.本发明创造性地在不同的研磨阶段设定不同的砂轮转速以达到更理想的研磨效果,包括在起步粗研磨阶段使用较低的转速可有效减少砂轮与晶圆摩擦接触产生的高热量,而第一中研磨阶段和第二中研磨阶段采用相对较高的恒定转速,以在获得较快的研磨速率的同时控制研磨效果,而最终的精研磨转速则选择高速旋转以对晶圆表面进行细致的打磨,达到最佳的表面镜面效果,且在此过程中相应匹配不同的输送速度。由于输送速度与转速应成反比,当大输送速度时选用低转速高扭矩,故而起步阶段选择低速介入,然后逐步加大转速并降低输送速度,从而可加工出理想的产品。由于砂轮消耗主要来自研磨时产生的热量无法散发,所以降低起步阶段转速可有效减少砂轮发热现象,可有效延长砂轮使用寿命,从而极大降低研磨成本,可将砂轮消耗量由现有的2800片/套延长至3800片/套,晶圆的平均厚度波动可由现有的1.9um降低至1.0um,极大提升晶圆的表面平坦度。
31.各阶段的研磨转速极大影响研磨效果及效率,需要精心设计。发明人在长期工作中经大量实验验证,当所述第一转速为2500r/min,所述第二转速及第三转速均为3500r/min,所述第四转速为4000r/min时的效果尤佳,砂轮的使用寿命可以显著延长且研磨出的晶圆的表面平坦性大大提高。
32.作为示例,各研磨过程中,两个砂轮的旋转方向相反,即一个为顺时针方向转动而另一个为逆时针方向转动,这有助于进一步平衡晶圆表面的受力情况,降低碎片风险。
33.在一较佳示例中,粗研磨过程中的输送速度为240μm/min,第一中研磨过程中的输送速度为80μm/min,第二中研磨过程中的输送速度为60μm/min,精研磨过程中的输送速度为40μm/min。各研磨过程中的输送速度与砂轮转速相匹配,可以有效改善研磨效果。
34.作为示例,待研磨的晶圆垂直放置于一载体上,通过流体静压力平衡并与载体一起以低于1000r/min的转速旋转。让晶圆保持旋转可以避免晶圆表面受力不均匀,降低碎片风险,同时提高研磨均匀性。
35.作为示例,粗研磨过程中的研磨量和精研磨过程中的研磨量均小于第一中研磨过程中的研磨量以及第二中研磨过程的研磨量,这样的设置在便于控制晶圆形貌的同时有助于提高研磨效率。比如,由于粗研磨阶段的转速偏低,研磨速率比较慢,故而粗研磨阶段设
置的研磨量较少,而中研磨阶段的研磨速率比较快,故而大部分研磨去除量都通过中研磨阶段去除,之后再经精研磨对晶圆表面形貌做最后的微调。在一示例中,待研磨晶圆的初始最大厚度为930μm(待研磨晶圆表面不平坦,各处的厚度不同,本示例中的厚度均指最大厚度),粗研磨过程中的研磨量为20μm,第一中研磨过程中的研磨量为50μm,第二中研磨过程中的研磨量为55μm,精研磨过程中的研磨量为10μm,经这多个研磨步骤后,最终的厚度为795μm。当然,各阶段的研磨量根据需要还可以有其他设置,但两个中研磨阶段的研磨量通常大于目标研磨量的50%以上,通常为60~75%,以在确保良好的研磨效果的同时提高研磨效率。
36.作为示例,各研磨过程中还包括向晶圆表面供应冷却液的步骤,以避免晶圆因表面过热发生翘起甚至碎片。在一示例中,冷却液流量为1.6l/min,所述冷却液可以为包含冷却水的砂浆。
37.需要说明的是,根据需要,还可以对完成精研磨的晶圆依次进行刻蚀及抛光的步骤,以进一步平坦化所述晶圆,从而得到表面更为平整的所述晶圆。比如可以使用干法刻蚀或湿法刻蚀中的任一种对完成精研磨的晶圆进行刻蚀以消除所述晶圆上的应力;之后可以采用包括但不仅限于化学机械抛光工艺对刻蚀后的所述晶圆进行双面抛光及正面抛光。由于刻蚀及抛光工艺均为本领域人员所熟知,此处不再累述。
38.综上所述,本发明提供一种双面研磨方法,s1:提供待研磨的晶圆,将所述晶圆垂直放置并将两个砂轮贴置到晶圆的两个相对表面;s2:对所述晶圆进行双面粗研磨,粗研磨过程中,两个砂轮均以第一转速旋转;s3:对所述晶圆进行双面第一中研磨,第一中研磨过程中,两个砂轮均以第二转速旋转;s4:对所述晶圆进行双面第二中研磨,第二中研磨过程中,两个砂轮均以第三转速旋转;s5:对所述晶圆进行双面精研磨,精研磨过程中,两个砂轮均以第四转速旋转;其中,第一转速小于第二转速及第三转速,第二转速及第三转速均小于第四转速;粗研磨过程中的输送速度>第一中研磨过程中的输送速度>第二中研磨过程中的输送速度>精研磨过程中的输送速度。本发明创造性地在不同的研磨阶段设定不同的砂轮转速以达到更理想的研磨效果,包括在起步粗研磨阶段使用较低的转速可有效减少砂轮与晶圆摩擦接触产生的高热量,而第一中研磨阶段和第二中研磨阶段采用相对较高的恒定转速,以在获得较快的研磨速率的同时控制研磨效果,而最终的精研磨转速则选择高速旋转以对晶圆表面进行细致的打磨,达到最佳的表面镜面效果,且在此过程中相应匹配不同的输送速度。由于输送速度与转速应成反比,当大输送速度时选用低转速高扭矩,故而起步阶段选择低速介入,然后逐步加大转速并降低输送速度,从而可加工出理想的产品。由于砂轮消耗主要来自研磨时产生的热量无法散发,所以降低起步阶段转速可有效减少砂轮发热现象,可有效延长砂轮使用寿命,从而极大降低研磨成本,可将砂轮消耗量由现有的2800片/套延长至3800片/套,晶圆的平均厚度波动可由现有的1.9um降低至1.0um,极大提升晶圆的表面平坦度。
39.上述实施例仅例示性说明本发明的原理及其功效,而非用于限制本发明。任何熟悉此技术的人士皆可在不违背本发明的精神及范畴下,对上述实施例进行修饰或改变。因此,举凡所属技术领域中具有通常知识者在未脱离本发明所揭示的精神与技术思想下所完成的一切等效修饰或改变,仍应由本发明的权利要求所涵盖。
再多了解一些
本文用于企业家、创业者技术爱好者查询,结果仅供参考。