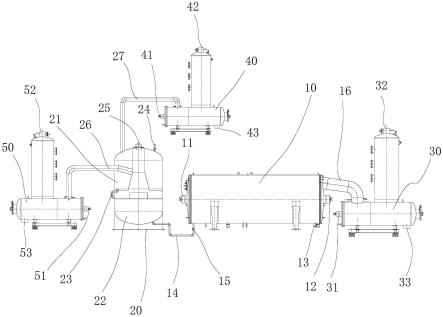
1.本发明涉及密封技术领域,特别是一种聚酯合成真空系统及其密封件的在线更换方法。
背景技术:
2.在聚酯生产高速发展的今天,面对日益激烈的竞争,为降低生产成本和增加竞争力,许多生产厂家在少改动或不改动现有生产装置的前提下,通过优化生产工艺参数来提高聚酯产品的质量和产量。
3.在聚酯合成真空系统中采用刮板冷凝器,可以消除低聚物堵塞的弊端,提高生产效率;由于刮板冷凝器是在高温、中真空(中减压)、低转速条件下工作,所以刮板轴的密封性能要求很高,现有技术中,广泛采用的是吉玛公司引进的动力组合式密封,它是将迷宫式密封与填料密封或唇形密封(j型密封环)组合使用,这种结构依赖j型密封环作为其主要密封元件;其结构复杂,造价昂贵。
4.本技术人的在先申请,授权公告号为cn214500049u的专利文献,公布了一种聚酯反应器用机封组件,通过设置双端面机械密封,实现对聚酯反应器轴套的密封。针对刮板冷凝器的特点,如何双端面机械密封设置在刮板轴上,实现对刮板轴的密封,是本领域技术人员急需解决的技术问题。
5.由于聚酯合成真空系统的真空度要求很高,其密封件的重要性不言而喻,由于密封件的使用寿命有所限制,密封件的更换是不可避免的,聚酯合成反应的温度需要维持在250℃-270℃左右,需要靠热媒维持温度的稳定性,停机更换密封件造成的结果是停车时间长(基本30天左右),中断热媒供应,造成巨大的能耗损失,且损失了产能,给企业带来巨大负担。
技术实现要素:
6.本发明要解决的技术问题是提供一种结构简单、易于操作的聚酯合成真空系统及其密封件的在线更换方法。
7.为解决上述技术问题,本发明提供的聚酯合成真空系统,包括预缩聚反应器、终聚反应器,所述终聚反应器的进料口与预缩聚反应器的出料口相通,所述终聚反应器的两端分别设置进料端机械密封和出料端机械密封,所述终聚反应器与终聚刮板冷凝器相通,终聚刮板冷凝器的一端设置第一机械密封,终聚刮板冷凝器的顶端设置终聚反应器气相抽出口;所述预缩聚反应器设置预缩聚机械密封,预缩聚反应器与刮板冷凝器相通,刮板冷凝器设置气相抽出口,使用时由pta和eg酯化后获得的产物经预缩聚进料口进入预缩聚反应器,完成预缩聚后的产物进入终聚反应器,由终聚反应器气相抽出口将终聚反应器内的气体经终聚刮板冷凝器抽出,由气相抽出口经刮板冷凝器将预缩聚反应器内的气体经刮板冷凝器抽出。
8.进一步,所述预缩聚反应器包括相互隔离的预缩聚反应器上室和预缩聚反应器下
室,所述预缩聚反应器上室和预缩聚反应器下室之间经预缩聚连通管连通,所述预缩聚反应器的顶部设置与预缩聚反应器上室相通的预缩聚进料口,预缩聚反应器上室经上室引出管与上室刮板冷凝器相通,上室刮板冷凝器的一端设置第二机械密封,上室刮板冷凝器的顶端设置上室气相抽出口;预缩聚反应器下室经终聚进料管与终聚反应器相通,预缩聚反应器下室经下室引出管与下室刮板冷凝器相通,下室刮板冷凝器的一端设置第三机械密封,下室刮板冷凝器的顶端设置下室气相抽出口,所述预缩聚反应器的顶部中心设置预缩聚机械密封,使用时由pta和eg酯化后获得的产物经进入预缩聚反应器上室,再经预缩聚连通管进入预缩聚反应器下室,完成预缩聚后的产物进入终聚反应器,由终聚反应器气相抽出口将终聚反应器内的气体经终聚刮板冷凝器抽出,由上室气相抽出口将预缩聚反应器上室内的气体经上室刮板冷凝器抽出,由下室气相抽出口将预缩聚反应器下室内的气体经下室刮板冷凝器抽出。
9.进一步,所述预缩聚反应器包括第一预缩聚反应器和第二预缩聚反应器,所述第一预缩聚反应器的一端设置第四机械密封,所述第一预缩聚反应器与第一刮板冷凝器相通,所述第一刮板冷凝器设置第一气相抽出口,所述第一预缩聚反应器的出料口与第二预缩聚反应器的第二进料口相通,第一刮板冷凝器的一端设置第五机械密封,所述第二预缩聚反应器的一端设置第六机械密封,所述第二预缩聚反应器与第二刮板冷凝器相通,所述第二刮板冷凝器设置第二气相抽出口,所述第二预缩聚反应器的出料口与终聚反应器的进料口相通,第二刮板冷凝器的一端设置第七机械密封,使用时由pta和eg酯化后获得的产物进入第一预缩聚反应器,再进入第二预缩聚反应器完成预缩聚后的产物经终聚进料管进入终聚反应器,由终聚反应器气相抽出口将终聚反应器内的气体经终聚刮板冷凝器抽出,由第一气相抽出口将第一预缩聚反应器内的气体经第一刮板冷凝器抽出,由第二气相抽出口将第二预缩聚反应器内的气体经第二刮板冷凝器抽出。
10.上述聚酯合成真空系统密封件的在线更换方法,包括如下步骤:首先关闭预缩聚进料口,停止向预缩聚反应器内加料,但预缩聚反应器和终聚反应器的热媒持续保持,使得预缩聚反应器内的预缩聚反应和终聚反应器内的终聚反应持续进行,并将成品持续排出,以使预缩聚反应器和终聚反应器内的物料持续减少,直至基本排空,然后向预缩聚反应器和终聚反应器内充入惰性气体,直至与大气平衡,使得预缩聚反应器和终聚反应器内保持微正压,然后逐一更换各机械密封中的一个或多个。
11.进一步,所述惰性气体为氮气。
12.发明的技术效果:(1)本发明的聚酯合成真空系统,相对于现有技术,在终聚反应器、预缩聚反应器、各刮板冷凝器都设置机械密封,大幅提高了密封效果;在对各机械密封进行更换时,采用的是不停止供应热媒,利用惰性气体对终聚反应器、预缩聚反应器进行填充的方法,使得终聚反应器、预缩聚反应器保持微正压状态对机械密封进行更换,无需对终聚反应器、预缩聚反应器进行降温冷却,减少了热能消耗,更换速度大幅提升,即使全套更换机械密封也仅需24小时左右,更换完各机械密封后,继续向预缩聚反应器引入物料即可继续升温,在此过程中终聚反应器、预缩聚反应器保持反应温度,无需进行生姜味,由于充入的是惰性气体,对预缩聚反应和终聚反应都没有影响,惰性气体排出即可。
附图说明
13.下面结合说明书附图对本发明作进一步详细说明:图1是本发明聚酯合成真空系统的结构示意图;图2是本发明聚酯合成真空系统为五釜聚酯系统的结构示意图;图中:终聚反应器10,进料端机械密封11,出料端机械密封12,出料口13,终聚进料管14,终聚进料阀15,终聚引出管16,预缩聚反应器20,预缩聚反应器上室21,预缩聚反应器下室22,预缩聚连通管23,预缩聚进料口24,预缩聚机械密封25,下室引出管26,上室引出管27,终聚刮板冷凝器30,第一机械密封31,终聚反应器气相抽出口32,第一残渣出口33,上室刮板冷凝器40,第二机械密封41,上室气相抽出口42,第二残渣出口43,下室刮板冷凝器50,第三机械密封51,下室气相抽出口52,第三残渣出口53,第二预缩聚反应器60,第六机械密封61,第二缩聚反应器出渣口62,第二进料口63,第二预缩聚引出管64,第二刮板冷凝器70,第七机械密封71,第二气相抽出口72,第二刮板冷凝器出渣口73。
具体实施方式
14.实施例1如图1所示,本实施例的聚酯合成真空系统为四釜聚酯系统,包括第一酯化反应器(图中未示出)、第二酯化反应器(图中未示出)、预缩聚反应器20、终聚反应器10,预缩聚反应器20为多层式反应器,预缩聚反应器20具体包括相互隔离的预缩聚反应器上室21和预缩聚反应器下室22,预缩聚反应器上室21和预缩聚反应器下室22之间经预缩聚连通管23连通,预缩聚连通管23上设置用于控制通断的控制阀;预缩聚反应器20的顶部设置与预缩聚反应器上室21相通的预缩聚进料口24,预缩聚进料口24与第二酯化反应器相通且预缩聚进料口24上设置进料阀;预缩聚反应器上室21经上室引出管27与上室刮板冷凝器40相通,上室刮板冷凝器40的一端设置第二机械密封41,上室刮板冷凝器40的顶端设置上室气相抽出口42,用于抽真空,上室刮板冷凝器40的底部设置残渣出口43用于出料;预缩聚反应器下室22经终聚进料管14与终聚反应器10相通,终聚进料管14上设置终聚进料阀15,预缩聚反应器下室22经下室引出管26与下室刮板冷凝器50相通,下室刮板冷凝器50的一端设置第三机械密封51,下室刮板冷凝器51的顶端设置下室气相抽出口52,用于抽真空,下室刮板冷凝器51的底端设置第三残渣出口53用于出料;预缩聚反应器20的顶部中心设置预缩聚机械密封25,终聚反应器10的两端分别设置进料端机械密封11和出料端机械密封12,终聚反应器10的底部设置出料口13;终聚反应器10经终聚引出管16与终聚刮板冷凝器30相通,终聚刮板冷凝器30的一端设置第一机械密封31,终聚刮板冷凝器30的顶端设置终聚反应器气相抽出口32,用于抽真空,终聚刮板冷凝器的底部设置第一残渣出口33用于出料;
使用时由pta和eg在第一酯化反应器、第二酯化反应器内酯化后获得的产物经预缩聚进料口24进入预缩聚反应器20的预缩聚反应器上室21,再经预缩聚连通管23进入预缩聚反应器下室22,完成预缩聚后的产物经终聚进料管14进入终聚反应器10,由终聚反应器气相抽出口32将终聚反应器10内的气体经终聚刮板冷凝器30抽出,由上室气相抽出口42将预缩聚反应器上室21内的气体经上室刮板冷凝器40抽出,由下室气相抽出口52将预缩聚反应器下室22内的气体经下室刮板冷凝器50抽出。
15.实施例2如实施例1中的聚酯合成真空系统,其密封件的在线更换方法,包括如下步骤:首先关闭预缩聚进料口24上的进料阀,停止向预缩聚反应器20内加料,但预缩聚反应器20和终聚反应器10的热媒持续保持供应,使得预缩聚反应器20内的预缩聚反应和终聚反应器10内的终聚反应持续进行,并将成品持续排出,以使预缩聚反应器20和终聚反应器10内的物料持续减少,直至基本排空,然后向预缩聚反应器20和终聚反应器10内充入惰性气体氮气,直至终聚反应器10内气压与大气基本平衡,使得预缩聚反应器20和终聚反应器10内保持微正压,然后逐一更换第一机械密封31、第二机械密封41、第三机械密封51、预缩聚机械密封25、进料端机械密封11、出料端机械密封12中的一个或多个。
16.需要单独对终聚反应器10的进料端机械密封11和出料端机械密封12进行更换时,则仅需要关闭终聚进料管14上的终聚进料阀15,停止向预终聚反应器10内加料,但预缩聚反应器20和终聚反应器10的热媒持续保持供应,使得终聚反应器10内的终聚反应持续进行,并将成品持续排出,以使终聚反应器10内的物料持续减少,直至基本排空,然后向终聚反应器10内充入惰性气体氮气,直至终聚反应器10内气压与大气基本平衡,使得终聚反应器10内保持微正压,然后逐一更换进料端机械密封11、和/或出料端机械密封12。
17.实施例3如图2所示,本实施例的聚酯合成真空系统为五釜聚酯系统,包括依次串联的第一酯化反应器(图中未示出)、第二酯化反应器(图中未示出)、第一预缩聚反应器(图中未示出)、第二预缩聚反应器60、终聚反应器10,终聚反应器10的两端分别设置进料端机械密封11和出料端机械密封12,终聚反应器10的底部设置出料口13;终聚反应器10经终聚引出管16与终聚刮板冷凝器30相通,终聚刮板冷凝器30的一端设置第一机械密封31,终聚刮板冷凝器30的顶端设置终聚反应器气相抽出口32,用于抽真空,终聚刮板冷凝器的底部设置第一残渣出口33用于出料;第一预缩聚反应器的一端设置第四机械密封,第一预缩聚反应器的底端设置第一缩聚反应器出渣口,第一预缩聚反应器经第一预缩聚引出管与第一刮板冷凝器相通;第一刮板冷凝器的顶部设置第一气相抽出口,第一刮板冷凝器的一端设置第五机械密封,第一刮板冷凝器的底端设置第一刮板冷凝器出渣口,第一预缩聚反应器的出料口与第二预缩聚反应器60的第二进料口63相通;第二预缩聚反应器60的一端设置第六机械密封61,第二预缩聚反应器60的底端设置第二缩聚反应器出渣口64,第二预缩聚反应器60经第二预缩聚引出管64与第二刮板冷凝器70相通,第二刮板冷凝器70的顶部设置第二气相抽出口72,第二刮板冷凝器70的一端设置
第七机械密封71,第二刮板冷凝器70的底端设置第二刮板冷凝器出渣口73,第二预缩聚反应器60的出料口经终聚进料管14与终聚反应器10的进料口相通,终聚进料管14上设置终聚进料阀15,使用时由pta和eg经第一酯化反应器、第二酯化反应器酯化后获得的产物经进入第一预缩聚反应器,再进入第二预缩聚反应器60,完成预缩聚后的产物经终聚进料管14进入终聚反应器10,由终聚反应器气相抽出口32将终聚反应器10内的气体经终聚刮板冷凝器30抽出,由第一气相抽出口将第一预缩聚反应器内的气体经第一刮板冷凝器抽出,由第二气相抽出口72将第二预缩聚反应器60内的气体经第二刮板冷凝器70抽出。
18.实施例4如实施例3中的聚酯合成真空系统,其密封件的在线更换方法,包括如下步骤:首先关闭第一预缩聚反应器的进料阀,停止向第一预缩聚反应器、第二预缩聚反应器60内加料,但第一预缩聚反应器、第二预缩聚反应器60和终聚反应器10的热媒持续保持供应,使得第一预缩聚反应器、第二预缩聚反应器60内的预缩聚反应和终聚反应器10内的终聚反应持续进行,并将成品持续排出,以使第一预缩聚反应器、第二预缩聚反应器60和终聚反应器10内的物料持续减少,直至基本排空,然后向第一预缩聚反应器、第二预缩聚反应器60和终聚反应器10内充入惰性气体氮气,直至终聚反应器10内气压与大气基本平衡,使得第一预缩聚反应器、第二预缩聚反应器60和终聚反应器10内保持微正压,然后逐一更换第四机械密封、第五机械密封、第六机械密封61、第七机械密封71、第一机械密封31、进料端机械密封11、出料端机械密封12中的一个或多个。
19.需要单独对终聚反应器10的进料端机械密封11和出料端机械密封12进行更换时,则仅需要关闭终聚进料管14上的终聚进料阀15,停止向预终聚反应器10内加料,但第一预缩聚反应器、第二预缩聚反应器60和终聚反应器10的热媒持续保持供应,使得终聚反应器10内的终聚反应持续进行,并将成品持续排出,以使终聚反应器10内的物料持续减少,直至基本排空,然后向终聚反应器10内充入惰性气体氮气,直至终聚反应器10内气压与大气基本平衡,使得终聚反应器10内保持微正压,然后逐一更换进料端机械密封11、和/或出料端机械密封12。
20.显然,上述实施例仅仅是为清楚地说明本发明所作的举例,而并非是对本发明的实施方式的限定。对于所属领域的普通技术人员来说,在上述说明的基础上还可以做出其它不同形式的变化或变动。这里无需也无法对所有的实施方式予以穷举。而这些属于本发明的精神所引申出的显而易见的变化或变动仍处于本发明的保护范围之中。
再多了解一些
本文用于企业家、创业者技术爱好者查询,结果仅供参考。