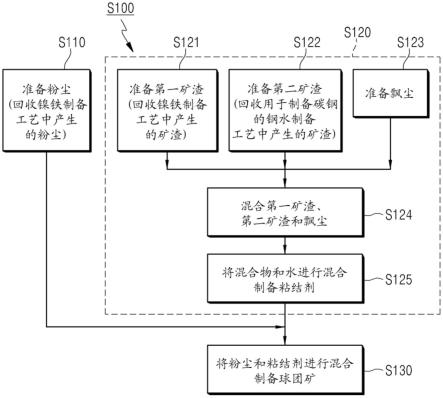
1.本发明涉及一种球团矿和粘结剂的制备方法、利用它制备的球团矿。更详细地,本发明涉及一种可以降低用于制备球团矿的成本的球团矿和粘结剂的制备方法、利用它制备的球团矿。
背景技术:
2.用于制备不锈钢的钢水一般是经由精炼处理过程制成,该过程中通过熔化固态镍铁、铬铁和废铁来制备含镍和铬的铁液,并从所制备的铁液中去除碳。
3.制备镍铁的过程包含:对含镍矿石(以下称为镍矿)进行干燥的过程、对干燥后的镍矿进行焙烧和预还原的过程、将完成焙烧和预还原的镍矿装入电炉进行熔化和还原的过程、去除熔化物中硫(s)的脱硫过程、将完成脱硫的熔化物制备成固体形式的过程。
4.另一方面,对镍矿进行干燥的过程、焙烧和预还原的过程、熔化和还原的过程中分别产生气体,而所产生的气体排放到各装置的外部。
5.排放到外部的气体(以下称为废气)中含有固态的颗粒状粉尘。另外,该粉尘中含有高含量的氧化镍(nio)。
6.因此,将粉尘作为用于制备镍铁的源材料再利用。此时,将回收的粉尘再利用时,粉尘制备成预定粒径以上的球团矿,并且通过对镍矿进行焙烧和预还原的过程中一起加入所制备的球团矿的方法予以再利用。
7.另一方面,当球团矿的强度较弱时,球团矿在输送或焙烧和预还原过程中磨损或破碎,从而可能会重新粉化。因此,在焙烧和预还原过程中,可能会产生大量的粉尘。
8.因此,将粉尘成型为球团矿时,通过将用于提高强度的粘结剂一起加入进行制备。然而,由于使用高价无机粘结剂作为粘结剂,存在用于制备球团矿的成本高的问题。
9.在先技术文献
10.专利文献1:韩国授权专利kr0942109
技术实现要素:
11.技术问题
12.本发明涉及一种可以降低用于制备球团矿的成本的球团矿和粘结剂的制备方法、利用它制备的球团矿。
13.本发明涉及一种可以将镍铁制备工艺中产生的矿渣回收再利用的球团矿和粘结剂的制备方法、利用它制备的球团矿。
14.技术方案
15.根据本发明实施例的球团矿的制备方法包含:将镍铁制备工艺中产生的粉尘回收备用的过程;利用作为镍铁制备工艺中产生的矿渣的第一矿渣和镍铁制备工艺之外的工艺中产生的副产物制备粘结剂的过程;以及将所述粉尘和所述粘结剂进行混合、造粒制备球团矿的过程。
16.所述副产物包含作为用于制备碳钢的钢水制备中产生的矿渣的第二矿渣和飘尘(fly ash)。
17.所述粉尘回收过程用于回收如下过程中的至少一个过程中产生的粉尘:在所述镍铁制备工艺中,对镍矿进行干燥的干燥过程;将所述镍矿加热以进行焙烧、预还原的焙烧和预还原过程;将所述镍矿加热以生成熔化物以及使所述镍矿还原的熔化和还原过程。
18.所述第一矿渣包含氧化镍(nio)3.0重量%至5.0重量%。
19.所述第一矿渣是将去除所述熔化物中硫(s)的脱硫工艺中产生的矿渣回收而备用的矿渣。
20.所述第二矿渣是将使钢水中碳(c)达到1重量%以下的精炼过程中产生的矿渣回收而备用的矿渣。
21.所述方法包含如下过程:控制所述第一矿渣、第二矿渣和飘尘(fly ash)的混合量,使得所述粘结剂总量中包含氧化硅(sio2)30重量%至50重量%、氧化钙(cao)15重量%至25重量%、氧化铝(al2o3)10重量%至20重量%、氧化铁(feo)10重量%至20重量%。
22.在制备所述粘结剂时,可以进一步混合na基助熔剂。
23.所述na基助熔剂可以包含na2co3。
24.所述方法包含如下过程中的至少一个过程:在混合所述第一矿渣、第二矿渣和飘尘之前,将所述第一矿渣、第二矿渣和飘尘分别进行破碎的过程;以及将混合有所述第一矿渣、第二矿渣和飘尘的第一混合物进行破碎的过程。
25.所述制备球团矿的过程包含将所述粉尘、粘结剂和水进行混合的过程,相对于混合有所述粉尘、粘结剂和水的第二混合物总重量%,混合成含有所述粉尘65重量%至85重量%、粘结剂5重量%至15重量%、水10重量%至20重量%。
26.本发明实施例作为用于制备球团矿的粘结剂的制备方法包含:准备作为镍铁制备工艺中产生的矿渣的第一矿渣的过程;准备作为用于制备碳钢的钢水制备中产生的矿渣的第二矿渣的过程;准备工业副产物飘尘的过程;以及将所述第一矿渣、第二矿渣和飘尘进行混合以制备粘结剂的过程。
27.所述第一矿渣是包含氧化镍(nio)3.0重量%至5.0重量%的矿渣,所述第二矿渣是将使钢水中碳(c)达到1重量%以下的精炼过程中产生的矿渣回收而备用的矿渣。
28.所述第一矿渣是将去除所述熔化物中硫(s)的脱硫工艺中产生的矿渣回收而备用的矿渣,并且所述第一矿渣是将所述脱硫工艺中产生的矿渣中粒径为1mm以下的矿渣回收而备用的矿渣。
29.所述方法包含如下过程:控制所述第一矿渣、第二矿渣和飘尘(fly ash)的混合量,使得所述粘结剂总量中包含氧化硅(sio2)30重量%至50重量%、氧化钙(cao)15重量%至25重量%、氧化铝(al2o3)10重量%至20重量%、氧化铁(feo)10重量%至20重量%,在控制所述第一矿渣、第二矿渣和飘尘(fly ash)的混合量的过程中,相对于混合有所述第一矿渣、第二矿渣、飘尘的第一混合物总重量%,混合成含有所述第一矿渣10重量%至30重量%、第二矿渣10重量%至30重量%、飘尘40重量%至60重量%。
30.所述制备粘结剂的过程还包含混合na基助熔剂的过程,相对于混合有所述第一矿渣、第二矿渣、飘尘和na基助熔剂的第一混合物总重量%,混合成含有所述第一矿渣10重量%至30重量%、第二矿渣10重量%至30重量%、飘尘40重量%至60重量%、na基助熔剂3
重量%至15重量%。
31.所述na基助熔剂可以包含na2co3。
32.根据本发明实施例的球团矿包含镍铁制备工艺中产生的粉尘和含有作为镍铁制备工艺中产生的矿渣的第一矿渣的粘结剂。
33.所述粘结剂包含:作为用于制备碳钢的钢水制备中产生的矿渣的第二矿渣;以及工业副产物飘尘。
34.所述第一矿渣包含氧化镍(nio)3.0重量%至5.0重量%。
35.在所述粘结剂总量中,所述粘结剂包含氧化硅(sio2)30重量%至50重量%、氧化钙(cao)15重量%至25重量%、氧化铝(al2o3)10重量%至20重量%、氧化铁(feo)10重量%至20重量%。
36.球团矿的粒径可为15mm至20。
37.球团矿的残存率可为94%至99.5%,落下残存率可为92%至95%。
38.球团矿的压缩强度可为1.8千克力至2.1千克力。
39.发明效果
40.在本发明实施例中,通过将镍铁制备工艺的脱硫过程中产生的矿渣、用于制备碳钢的钢水制备工艺中产生的矿渣、工业副产物飘尘(flay ash)再利用来制备粘结剂。因此,与现有技术相比,可以低成本制备粘结剂。另外,利用根据实施例的粘结剂制备用于制备镍铁的原料球团矿时,可以制备出与利用现有粘结剂制备的球团矿强度类似或者强度提高的球团矿。
41.因此,根据本发明实施例,既可降低用于制备球团矿的成本,又可确保球团矿的强度。
42.另外,由于通过将镍铁制备工艺的脱硫过程中产生的小颗粒脱硫矿渣再利用来制备粘结剂,可以节省现有现有技术中未能再利用的小颗粒脱硫矿渣的库存管理成本。
43.此外,小颗粒脱硫矿渣中含有镍(ni),将其作为粘结剂的原料再利用制备球团矿,因此所述粘结剂起到用于制备镍铁或用于提供镍(ni)的源材料的作用。
44.因此,可以减少用于制备镍铁的主原料和用于提供镍(ni)的源材料的高价镍矿的使用量,从而可以降低制备镍铁所需的成本。
附图说明
45.图1是依次示出根据本发明第一实施例的球团矿的制备方法的流程图。
46.图2是依次示出常规镍铁制备方法的视图。
47.图3是示出基于矿渣粒径的氧化镍(nio)含量的曲线图,其中矿渣是镍铁制备工艺中脱硫工艺所产生的矿渣。
48.图4是依次示出根据本发明第二实施例的球团矿的制备方法的流程图。
49.图5是整理出通过根据第一和第二比较例、第一和第二实施例的方法来制备的球团矿的残存率(%)、落下残存率(%)、压缩强度(千克力)和形状的表格。
具体实施方式
50.在下文中,将参照附图进一步详细描述本发明实施例。然而,本发明能够以各种不
同方式实施,并不限于下面公开的实施例。下面提供本实施例的目的在于完整地公开本发明,以使得普通技术人员完全理解发明的范围。为了描述本发明实施例,附图可被放大,附图中相同的附图标记表示相同的构件。
51.本发明涉及一种可以降低用于制备球团矿的成本以及可以将镍铁制备工艺中产生的矿渣再利用的球团矿和粘结剂的制备方法。更具体地,本发明涉及一种球团矿和粘结剂的制备方法,在制备镍铁制备中用作原料的球团矿时,可以确保强度,并且降低制备成本。
52.图1是依次示出根据本发明第一实施例的球团矿的制备方法的流程图。图2是依次示出常规镍铁制备方法的视图。图3是示出基于矿渣粒径的氧化镍(nio)含量的曲线图,其中矿渣是镍铁制备工艺中脱硫工艺所产生的矿渣。
53.参见图1,根据本发明第一实施例的球团矿的制备方法s100包含:准备镍铁制备工艺中产生的粉尘的过程s110、制备粘结剂的过程s120以及将粉尘和粘结剂进行混合、造粒制备球团矿的过程s130。
54.粘结剂是通过根据第一实施例的方法来制备的粘结剂。
55.根据第一实施例的制备粘结剂的过程包含准备镍铁制备工艺中产生的矿渣(第一矿渣)的过程、准备镍铁制备工艺之外的工艺中产生的副产物的过程、将第一矿渣和粘结剂进行混合的过程、利用混合有第一矿渣和副产物的混合物制备粘结剂的过程。
56.与第一矿渣混合在一起的副产物可以包含用于制备碳钢的钢水制备工艺中产生的矿渣(第二矿渣)和工业副产物飘尘(flay ash)。
57.在下文中,参照图1描述根据第一实施例的粘结剂的制备方法时,以与第一矿渣混合在一起的副产物是用于制备碳钢的钢水制备工艺中产生的第二矿渣和飘尘(flay ash)为例进行描述。
58.参见图1,根据第一实施例的制备粘结剂的过程s120包含准备作为镍铁制备工艺中产生的矿渣的第一矿渣的过程s121、准备作为用于制备碳钢的钢水制备工艺中产生的矿渣的第二矿渣的过程s122、准备工业副产物飘尘(flay ash)的过程s123、将第一和第二矿渣、飘尘进行混合的过程s124、利用混合有第一和第二矿渣、飘尘的混合物制备粘结剂的过程s125。
59.在本发明中,制备球团矿时,如上所述,将镍铁制备工艺中产生的粉尘予以再利用。
60.在下文中,具体描述根据第一实施例的球团矿的制备方法之前,先描述镍铁制备方法。
61.参见图2,镍铁制备方法包含对镍矿进行干燥的过程s10、对干燥后的镍矿进行焙烧和还原的过程s20、对焙烧和还原的镍矿进行熔化和还原制备镍铁熔化物(以下称为熔化物)的过程s30以及去除熔化物中硫(s)的脱硫过程s40。
62.作为用于制备镍铁或者用于提供镍(ni)和铁(fe)的源材料,镍矿是包含氧化镍(nio)、氧化钙(cao)、氧化硅(sio2)、氧化铝(al2o3)、氧化铁(feo)的矿石,可以是包含所述氧化镍(nio)1.5重量%至2重量%的矿石。另外,除了上述的成分之外,镍矿还可以包含氧化锰(mno)、五氧化二磷(p2o5)、氧化镁(mgo)、氧化钛(tio2)、碳(c)、硫(s)。对于这种镍矿,例如可以是腐泥土(saprolite)。更具体地,镍矿可以具有如下表1的一个实例所示的组分。
63.【表1】
[0064][0065]
在对镍矿进行干燥的过程s10中,去除镍矿中含有的水分。此时,对镍矿进行干燥的干燥装置可以是例如装入待处理物以及具有可旋转的滚筒的旋转干燥机(rotary dryer)。
[0066]
对于利用旋转干燥机进行干燥的方法,将镍矿装入滚筒内部,在使滚筒旋转的同时加热内部,例如加热到200℃的温度。由此,从装入滚筒内部的镍矿去除水分。
[0067]
在加热旋转干燥机的滚筒时,例如可以采用将热风送入滚筒内的方法。当然,加热滚筒内部的方法不限于上述的例子,可以采用各种方法。此外,对镍矿进行干燥的干燥装置不限于上述的旋转干燥机,可以采用能够从镍矿去除水分的各种装置。
[0068]
在焙烧和还原的过程s20中,对镍矿进行热处理使其焙烧,从而增加强度,并且使所述镍矿中含有的氧化镍(nio)和氧化铁(feo)等金属氧化物还原成镍(ni)和铁(fe)。
[0069]
对于将镍矿进行焙烧和还原的装置(以下称为焙烧装置),例如可以是具有可旋转的滚筒和用于在滚筒内部产生火焰的燃烧器的回转炉(rotary kiln)。
[0070]
对于利用回转炉使镍矿焙烧和还原的方法,将镍矿、含碳(c)还原剂如煤炭装入滚筒内部,并使滚筒旋转的同时加热内部。此时,向燃烧器供应燃料气体,通过燃烧器在滚筒内部产生火焰,以将所述滚筒内部加热到600℃至800℃的温度。
[0071]
如此,滚筒内部加热到600℃至800℃的温度时,镍矿被焙烧,其强度增加,镍矿中含有的氧化镍(nio)和氧化铁(feo)等金属氧化物被还原。
[0072]
上文中描述了加热回转炉的滚筒内部时通过燃烧器产生火焰的方法,但是不限于此,可以采用能够将滚筒内部加热到600℃至800℃的温度的各种加热方法。此外,对镍矿进行焙烧和还原的焙烧装置不限于上述的回转炉,可以采用能够使镍矿焙烧和还原的各种装置。
[0073]
另一方面,在该过程s20中,当镍矿被加热时,作为后续操作的镍矿的熔化和还原过程s30中容易加热到目标温度。此外,在焙烧和还原过程s20中,如上所述将镍矿加热到600℃至800℃的温度,以使金属氧化物还原,而该温度低于作为后续操作的熔化和还原过程s30中的温度(1200℃以上)。因此,在焙烧和还原过程s20中,被还原的金属氧化物的量少于熔化和还原过程s30的。
[0074]
因此,可以将焙烧和还原过程s20中发生的还原描述为比起熔化和还原过程s30中的还原预先或预备实施的还原。因此,将熔化和还原过程s30前实施的焙烧和还原过程s20通常命名为焙烧和预还原过程s20。更具体地,回转炉中实施的焙烧和还原过程s20可被命名为焙烧和预还原过程s20。
[0075]
在熔化和还原过程s 40中,将镍矿进行熔化,使得镍矿中含有的氧化镍(nio)和氧化铁(feo)等金属氧化物还原。此时,将镍矿进行熔化和还原时,可以使用电炉。电炉可以配置成包含具有内部空间的主体和用于向主体内部产生作为热源的电弧(arc)的电极棒。
[0076]
对于电炉中使镍矿熔化和还原的方法,首先向电炉的主体内部加入镍矿和含碳(c)的还原剂。对于还原剂,例如可以是煤炭。当镍矿和还原剂装入主体内时,通过电极棒向
主体内部产生电弧(arc)。此时,镍矿和还原剂被电弧热熔化,并且镍矿还原,从而制备出熔化物即镍铁熔化物。
[0077]
另一方面,电炉中制备的熔化物中含有4000ppm左右的硫(s),硫(s)是降低产品如不锈钢的品质的因素。因此,当电炉中制备熔化物时,将会实施从所述熔化物去除硫(s)的脱硫s40,此时需要将(s)控制成600ppm以下。
[0078]
对于从熔化物去除硫(s)的脱硫,例如可以利用kr(kanvara reactor)装置来实施。kr装置可以是包含浸入装在钢包(ladle)内的熔化物中可旋转的叶轮的装置。
[0079]
kr装置中的脱硫操作可以如下进行。当电炉中制备的熔化物装入钢包(ladle)内时,将叶轮浸入钢包内的熔化物中。然后,旋转浸入熔化物的叶轮,同时向所述熔化物中加入脱硫剂如氧化钙(cao)。
[0080]
当熔化物中加入脱硫剂时,通过熔化物中硫(s)与脱硫剂之间的反应生成cas,所生成的cas进入悬浮在熔化物表面上的矿渣中。因此,从熔化物去除硫(s),并制备硫(s)的含量为600ppm以下的镍铁熔化物。
[0081]
另一方面,在如上所述的镍铁的制备工艺中,干燥过程s10、焙烧和预还原过程s20、熔化和还原过程s 30中分别产生气体,该气体排放到装置的外部。也就是说,在用于对镍矿进行干燥的干燥装置、用于对镍矿进行焙烧和预还原的焙烧装置、用于熔化和还原的电炉中分别产生气体,而所产生的气体排放到各装置的外部。
[0082]
排放到外部的气体(以下称为废气)中含有固态颗粒状的粉尘。另外,该粉尘中含有含量类似于镍矿的氧化镍(nio)。
[0083]
因此,将镍铁制备中产生的粉尘作为用于制备镍铁或者用于提供镍(ni)的源材料再利用。也就是说,从干燥装置、焙烧装置和电炉排出的废气回收粉尘,将回收的粉尘与镍矿一起作为源材料再利用。
[0084]
为此,通过在干燥装置、焙烧装置和电炉上分别设置用于收集废气中的粉尘的废气处理装置来回收粉尘。
[0085]
对于废气处理装置,例如可以是具有气体经过的管道、用于产生吸引力以将气体吸入管道内部的驱动单元、设置在管道内部用于使气体流过并截留粉尘的过滤器、用于储存被截留的粉尘的收集单元的装置。
[0086]
另外,将回收的粉尘再利用时,对镍矿进行焙烧和预还原的过程s20中加入粉尘予以再利用。更具体地,向焙烧装置如回转炉内部加入镍矿和回收的粉尘进行焙烧和预还原。
[0087]
另一方面,从废气回收的粉尘的粒径为0.1mm以下,由于粒径较小,如果直接再利用,则随着制备镍铁的工艺次数增加,可能会出现粉尘生成量持续增加的问题。更具体地,从焙烧装置产生的粉尘量可能会持续增加。
[0088]
因此,将镍铁制备中产生的粉尘制备成预定粒径以上的球团矿,将所制备的球团矿加入到焙烧装置作为源材料再利用。
[0089]
然而,即使将粉尘制备成球团矿后再利用,如果球团矿的强度较弱,则由于磨损和破碎,也可能重新产生大量的粉尘。也就是说,如果球团矿的强度较弱,则为了再利用而输送的过程中,由于球团矿受到冲击或磨损而破碎,可能会产生粉尘。此外,镍矿、煤炭装入作为焙烧装置的回转炉的滚筒内,随着滚筒的旋转被焙烧和还原。此时,如果球团矿的强度较弱,则由于滚筒的旋转以及与镍矿和煤炭的摩擦,球团矿会磨损和破碎,因此可能会产生粉
尘。
[0090]
如上所述,若球团矿的强度较弱,则球团矿会在再利用过程中重新粉化,因此需要增加球团矿的强度。为此,将粉尘造粒制备成球团矿时,通过一起加入粘结剂进行制备。然而,在现有技术中,由于使用高价无机粘结剂作为粘结剂,存在球团矿的制备成本上升的问题。
[0091]
因此,在本发明实施例中,准备了确保球团矿的强度且价格低于现有粘结剂的粘结剂,并利用它制备球团矿。
[0092]
根据第一实施例的粘结剂是利用镍铁制备工艺的脱硫(s40)过程中产生的镍铁脱硫矿渣(第一矿渣)、用于制备碳钢的钢水制备工艺中产生的矿渣(第二矿渣)和飘尘(fly ash)进行制备。
[0093]
另外,利用第一矿渣、第二矿渣和飘尘来制备含有氧化硅(sio2)、氧化钙(cao)、氧化铝(al2o3)和氧化铁(feo)的粘结剂。此时,相对于粘结剂总量,制备成含有氧化硅(sio2)30重量%至50重量%、氧化钙(cao)15重量%至25重量%、氧化铝(al2o3)10重量%至20重量%、氧化铁(feo)10重量%至20重量%。此外,除了氧化硅(sio2)、氧化钙(cao)、氧化铝(al2o3)和氧化铁(feo)之外,粘结剂中还可以包含不可避免的其他成分或杂质。
[0094]
另一方面,在粘结剂中,如果氧化硅(sio2)、氧化钙(cao)、氧化铝(al2o3)、氧化铁(feo)中至少一种超出上面给出的各含量范围,则无法确保类似于利用现有粘结剂制备的球团矿的强度。
[0095]
也就是说,在粘结剂中,如果氧化硅(sio2)含量小于30重量%或大于50重量%、或者氧化钙(cao)小于15重量%或大于25重量%、或者氧化铝(al2o3)含量小于10重量%或大于20重量%、或者氧化铁(feo)含量小于10重量%或大于20重量%,则利用该粘结剂制备的球团矿的强度可能无法类似于利用现有粘结剂制备的球团矿的强度。
[0096]
对于如上所述制备氧化硅(sio2)为30重量%至50重量%、氧化钙(cao)为15重量%至25重量%、氧化铝(al2o3)为10重量%至20重量%、氧化铁(feo)为10重量%至20重量%的粘结剂,可以通过控制第一矿渣、第二矿渣和飘尘各自的混合量来实现。
[0097]
在下文中,将参照图1描述根据本发明第一实施例的粘结剂的制备方法。
[0098]
参见图1,制备粘结剂的过程s120包含准备作为镍铁制备工艺的脱硫过程s40中产生的矿渣的第一矿渣的过程s121、准备作为用于制备碳钢的钢水制备工艺中产生的矿渣的第二矿渣的过程s122、准备飘尘(fly ash)的过程s123、将第一和第二矿渣、飘尘进行混合的过程s124,利用混合有第一和第二矿渣、飘尘的混合物制备粘结剂的过程s125。
[0099]
此外,还可以包含:在混合第一和第二矿渣、飘尘之前,将所述第一和第二矿渣、飘尘分别进行破碎的过程,或者将第一和第二矿渣、飘尘混合之后,将该混合物进行破碎的过程。
[0100]
第一矿渣是将镍铁制备工艺的脱硫过程s40中产生的矿渣回收而备用的矿渣。
[0101]
如上所述,脱硫过程s40是从电炉中制备的熔化物去除硫(s)的过程,为了脱硫,向熔化物中加入氧化钙(cao)等脱硫剂。当熔化物中加入脱硫剂时,通过熔化物中硫(s)与脱硫剂之间的反应生成cas,所生成的cas进入悬浮在熔化物表面上的矿渣中。然后,当脱硫结束时,将悬浮在熔化物表面上的矿渣向外排出。
[0102]
脱硫过程s40中产生的矿渣中包含氧化镍(nio)、氧化钙(cao)、氧化硅(sio2)、氧
化铝(al2o3)、氧化铁(feo)。此外,还可以包含氧化锰(mno)、五氧化二磷(p2o5)、氧化镁(mgo)、氧化钛(tio2)、碳(c)、硫(s)。
[0103]
如上所述,脱硫过程s40中产生的矿渣中含有氧化镍(nio),由于氧化镍(nio)的含量高,作为用于制备镍铁的镍源材料再利用,并且通过加入电炉的方法来再利用。
[0104]
此时,在脱硫过程s40中产生的矿渣中,仅将粒径为0.5mm以上的矿渣加入电炉再利用,而小于0.5mm的脱硫矿渣进行库存管理,不会回收再利用。这是因为,当小于0.5mm的小颗粒脱硫矿渣加入电炉时,由于加入的大量矿渣过轻,将被直接吸入废气处理装置的管道中。
[0105]
另一方面,根据矿渣的粒径,所含有的氧化镍(nio)的含量不同。也就是说,如图3所示,在粒径为10mm以上的矿渣中,氧化镍含量为10重量%以上,在粒径为5mm以上且小于10mm的矿渣中,氧化镍含量为6.6重量%,在粒径为3mm以上且小于5mm的矿渣中,氧化镍含量为2.9重量%,在粒径为1mm以上且小于3mm的矿渣中,氧化镍含量为3.3重量%,在粒径为0.5mm以上且小于1mm的矿渣中,氧化镍含量为1.9重量%,在粒径小于0.5mm的矿渣中,氧化镍(nio)含量为3.0重量%至5重量%,更具体为4.0重量%左右。
[0106]
在粒径小于0.5mm的矿渣中,氧化镍的含量少于粒径为10mm以上的矿渣、粒径为5mm以上且小于10mm的矿渣,但是由于其含量高达3.0重量%至5重量%,充分具有再利用价值。
[0107]
然而,目前脱硫过程s40中产生的矿渣中小于0.5mm的脱硫矿渣没有被再利用。
[0108]
因此,在实施例中,将脱硫过程s40中产生的矿渣中粒径小于0.5mm的矿渣作为用于制备粘结剂的原料再利用。因此,第一矿渣可以被描述为镍铁制备工艺的脱硫过程s40中产生的矿渣中粒径为0.5mm以下的矿渣。
[0109]
另外,在实施例中,如上所述,脱硫过程s40中产生的矿渣中粒径小于0.5mm的矿渣即第一矿渣中包含氧化镍(nio)之外的氧化钙(cao)、氧化硅(sio2)、氧化铁(feo)。氧化钙(cao)可以含有25重量%至30重量%,氧化硅(sio2)可以含有15重量%至20重量%,氧化铁(feo)可以含有15重量%至20重量%。此外,第一矿渣中可以包含氧化铝(al2o3)、氧化锰(mno)、五氧化二磷(p2o5)、氧化镁(mgo)、氧化钛(tio2)、碳(c)、硫(s),第一矿渣的具体实例如表2所示。
[0110]
第一矿渣作为用于制备粘结剂的原料,相对于其他成分,大量含有氧化钙(cao)、氧化硅(sio2)、氧化铁(feo),因此,第一矿渣可以被描述为用于将粘结剂的氧化钙(cao)、氧化硅(sio2)、氧化铁(feo)分别控制成目标含量的原料。
[0111]
此外,如上所述,第一矿渣中含有氧化镍(nio)3.0重量%至5重量%,因此所述第一矿渣还起到用于制备镍铁或用于提供镍(ni)的源材料的作用。
[0112]
【表2】
[0113][0114]
第二矿渣是碳钢用钢水的制备工艺中产生的矿渣。
[0115]
碳钢用钢水的制备工艺一般包含去除铁水中硫(s)的预精炼过程、去除预精炼结束的铁水中碳(c)的转炉精炼过程、从转炉精炼结束的铁水即钢水进一步去除碳(c)并去除氧(脱氧)的二次精炼过程。
[0116]
对于预精炼,例如可以利用kr(kanvara reactor)装置来实施,此时可以利用氧化钙(cao)等脱硫剂。
[0117]
转炉精炼过程是将铁水装入转炉内通过喷枪向铁水吹入氧气以将所述铁水中c(碳)控制为4重量%以下的过程。
[0118]
二次精炼可以在真空脱气装置rh(rheinstahl huttenwerke&heraeus)装置中实施。真空脱气装置设置在钢包的上侧,并且包含具有内部空间的真空槽、设置成贯穿真空槽上部的喷枪和在真空槽的下部沿所述真空槽的宽度方向隔开安装的一对浸渍管。一对浸渍管中一个浸渍管上贯穿插设有喷嘴,向其内部注入惰性气体如ar气体。在一对浸渍管中,将贯穿插设有喷嘴或者供应惰性气体的浸渍管称为上升管,而另一个称为下降管。
[0119]
这种真空槽脱气装置将真空槽减压到几托以下,使得钢包内的钢水上升到真空槽内后,使钢水从上升管往下降管循环。如此,使钢包内的钢水循环或回流经过上升管和下降管时,通过喷枪吹入氧气将钢水中的碳(c)控制成1重量%以下。
[0120]
在真空槽脱气装置中结束二次精炼后,将钢包内悬浮在钢水上的矿渣排出。
[0121]
碳钢用钢水的制备工艺中二次精炼所产生的矿渣中包含氧化钙(cao)、氧化硅(sio2)、氧化铝(al2o3)、氧化铁(feo)。氧化钙(cao)可以含有35重量%至40重量%,氧化硅(sio2)可以含有10重量%至15重量%,氧化铝(al2o3)可以含有20重量%至25重量%,氧化铁(feo)可以含有20重量%至25重量%。此外,还可以包含氧化锰(mno)、五氧化二磷(p2o5)、氧化镁(mgo)、氧化钛(tio2)、碳(c)、硫(s)。碳钢用钢水的制备工艺中二次精炼所产生的矿渣的具体实例如表2所示。
[0122]
在第一实施例中,碳钢用钢水的制备工艺中二次精炼所产生的矿渣作为用于制备粘结剂的原料再利用。因此,第二矿渣可以被描述为碳钢用钢水的制备工艺中二次精炼所产生的矿渣。
[0123]
这种第二矿渣作为用于制备粘结剂的原料,相对于其他成分,大量含有氧化钙(cao)、氧化硅(sio2)、氧化铝(al2o3)和氧化铁(feo)。因此,第二矿渣可以被描述为用于将粘结剂的氧化钙(cao)、氧化硅(sio2)、氧化铝(al2o3)和氧化铁(feo)分别控制成目标含量的原料。
[0124]
飘尘(fly ash)作为含有氧化硅(sio2)60重量%至80重量%、氧化铝(al2o3)10重量%至20重量%的原料,可以是在火力发电厂等燃烧煤炭时产生的工业副产物。
[0125]
除了氧化硅(sio2)、氧化铝(al2o3)之外,飘尘中包含氧化钙(cao)、氧化铁(feo)。此外,飘尘中还可以包含氧化锰(mno)、五氧化二磷(p2o5)、氧化镁(mgo)、氧化钛(tio2)、碳(c)、硫(s)。另外,飘尘的具体实例如表2所示。
[0126]
这种飘尘作为用于制备粘结剂的原料,相对于其他成分,大量含有氧化硅(sio2)和氧化铝(al2o3)。因此,飘尘可以被描述为用于将粘结剂的氧化硅(sio2)和氧化铝(al2o3)分别控制成目标含量的原料。
[0127]
准备如上述所述的第一和第二矿渣与飘尘(s121、122、123)后,将它们进行混合之前,优选将第一和第二矿渣与飘尘分别进行破碎,使其粒径达到100μm以下。当然,本发明不限于此,也可以将第一和第二矿渣与飘尘进行混合后,通过将该混合物进行破碎,使其粒径达到100μm以下。
[0128]
这是为了在混合粘结剂和粉尘后造粒制备球团矿时提高造粒性。
[0129]
准备如上所述的第一和第二矿渣与飘尘(s121、122、123)后,将它们进行混合(s124)。此时,相对于混合有第一矿渣、第二矿渣、飘尘的混合物(以下称为第一混合物)总重量%,混合成第一矿渣为10重量%至30重量%,第二矿渣为10重量%至30重量%,飘尘为40重量%至60重量%。
[0130]
另一方面,在第一混合物中,当第一矿渣、第二矿渣和飘尘中至少一种超出上面给出的各含量范围时,可能难以制备氧化硅(sio2)为30重量%至50重量%、氧化钙(cao)为15重量%至25重量%、氧化铝(al2o3)为10重量%至20重量%、氧化铁(feo)为10重量%至20重量%的粘结剂。
[0131]
也就是说,在第一混合物中,当第一矿渣的含量小于10重量%或大于30重量%,或者第二矿渣的含量小于10重量%或大于30重量%,或者飘尘的含量小于40重量%或大于60重量%时,可能难以制备氧化硅(sio2)为30重量%至50重量%、氧化钙(cao)为15重量%至25重量%、氧化铝(al2o3)为10重量%至20重量%、氧化铁(feo)为10重量%至20重量%的粘结剂。另外,当使用这种粘结剂时,可能无法确保类似于利用现有粘结剂制备的球团矿的强度。
[0132]
因此,在实施例中混合成第一矿渣为10重量%至30重量%,第二矿渣为10重量%至30重量%,飘尘为40重量%至60重量%。
[0133]
在混合第一和第二矿渣与飘尘后(s124),将该混合物(即,第一混合物)与水进行混合制备粘结剂(s125)。
[0134]
如上所述,利用第一和第二矿渣与飘尘制备粘结剂后,将所准备的粉尘、所制备的粘结剂和水进行混合制备球团矿(s130)。
[0135]
对于将粉尘造粒制成球团矿的造粒机,例如可以是具有用于装入或容纳待造粒的原料的圆盘、用于使圆盘旋转的驱动单元的造粒机(pelletizer)。
[0136]
对于利用造粒机(pelletizer)制备球团矿的方法,先将粉尘、粘结剂和水加入到圆盘内部,并启动驱动单元使所述圆盘旋转。此时,通过圆盘的旋转动作将粉尘、粘结剂和水进行混合造粒,从而制备预定大小的造粒物即球团矿。
[0137]
将粉尘、粘结剂和水进行混合制备球团矿时,混合成在混合有粉尘、粘结剂和水的
混合物(以下称为第二混合物)总量中粉尘为65重量%至85重量%,粘结剂为5重量%至15重量%,水为10重量%至20重量%。
[0138]
另一方面,例如,当混合有粉尘、粘结剂和水的第二混合物中至少一种超出上面给出的各含量范围时,可能难以制备氧化硅(sio2)为30重量%至50重量%、氧化钙(cao)为15重量%至25重量%、氧化铝(al2o3)为10重量%至20重量%、氧化铁(feo)为10重量%至20重量%的粘结剂。另外,当使用这种粘结剂时,可能无法确保类似于利用现有粘结剂制备的球团矿的强度。
[0139]
另外,球团矿的粒径大小优选控制成15mm至20mm,这可以通过控制造粒时间、圆盘的旋转速度和装入圆盘内部的原料(第二混合物)的装入量中至少一个进行控制。
[0140]
图4是依次示出根据本发明第二实施例的球团矿的制备方法的流程图。
[0141]
在上述的第一实施例中,制备粘结剂时,通过混合第一矿渣、第二矿渣、飘尘进行制备。
[0142]
但是,本发明不限于此,在制备粘结剂时,如图4所示,可以进一步混合na基助熔剂。也就是说,根据第二实施例的制备粘结剂的过程包含准备作为镍铁制备工艺的脱硫过程中产生的矿渣的第一矿渣的过程s121、准备作为用于制备碳钢的钢水制备工艺中产生的矿渣的第二矿渣的过程s 122、准备飘尘(flay ash)的过程s123、准备na基助熔剂的过程s126、将第一矿渣、第二矿渣、飘尘和na基助熔剂进行混合过程s124、利用混合有第一矿渣、第二矿渣、飘尘和na基助熔剂的混合物制备粘结剂的过程s125。
[0143]
na基助熔剂是为了提高球团矿的强度而加入的,na基助熔剂例如可以是包含na2co3的材料。
[0144]
此外,相对于混合有第一矿渣、第二矿渣、飘尘、na基助熔剂的混合物(第一混合物)总量,优选混合成所述na基助熔剂的含量为3重量%至15重量%。也就是说,混合成在第一混合物总量中第一矿渣为10重量%至30重量%,第二矿渣为10重量%至30重量%,飘尘为40重量%至60重量%,na基助熔剂为3重量%至15重量%。
[0145]
另一方面,例如,当第一混合物中na基助熔剂的含量小于3重量%时,与使用没有混合所述na基助熔剂的根据第一实施例的粘结剂相比,球团矿的强度提高效果可能微乎其微。相反地,当na基助熔剂的含量大于15重量%时,相对于加入量,球团矿的强度增加率小。因此,从相对于加入量的效果显现层面来看,na基助熔剂的含量优选为15重量%以下。
[0146]
图5是整理出通过根据第一和第二比较例、第一和第二实施例的方法来制备的球团矿的残存率(%)、落下残存率(%)、压缩强度(千克力)和形状的表格。
[0147]
根据第一和第二比较例、第一和第二实施例的球团矿是将镍铁制备工艺中产生的粉尘回收后造粒而制备的球团矿。另外,第一比较例是没有使用粘结剂的球团矿,第二比较例是使用现有无机粘结剂制备的球团矿。
[0148]
此外,根据第一实施例的球团矿是利用根据第一实施例的粘结剂(即,将第一矿渣、第二矿渣和飘尘进行混合而制备的粘结剂)来制备的球团矿。此时,混合成在混合有第一矿渣、第二矿渣和飘尘的第一混合物总量中第一矿渣为10重量%至30重量%,第二矿渣为10重量%至30重量%,飘尘为40重量%至60重量%。
[0149]
另外,根据第二实施例的球团矿是利用根据第二实施例的粘结剂(即,将第一矿渣、第二矿渣、飘尘和na基助熔剂进行混合而制备的粘结剂)来制备的球团矿。此时,混合成
在混合有第一矿渣、第二矿渣、飘尘和na基助熔剂的混合物总量中第一矿渣为10重量%至30重量%,第二矿渣为10重量%至30重量%,飘尘为40重量%至60重量%,na基助熔剂为3重量%至15重量%。
[0150]
在图5中,残存率是指将球团矿装入焙烧装置即回转炉的滚筒内,并以5rpm的速度旋转滚筒,同时以600℃的温度加热所述滚筒内部20分钟,使球团矿焙烧和还原时,焙烧和还原结束后,粒径为10mm以上的球团矿的重量比。也就是说,残存率是焙烧和还原结束后粒径为10mm以上的球团矿与装入回转炉滚筒的球团矿的总重量的重量比。
[0151]
此外,落下残存率是指球团矿从2.5m的高度连续5次落下时10mm以上的球团矿的重量比例。也就是说,落下残存率是在落下的球团矿总量中粒径为10mm以上的球团矿的重量比例。
[0152]
压缩强度(千克力,kgf)是指对每单位重量的抵抗力,压缩强度是测量对放置在辊压装置上的球团矿的上部施加一定速度的压力直至球团矿破坏的最大载荷的值。
[0153]
参见图5,根据第二比较例、第一和第二实施例的球团矿的残存率、落下残存率、压缩强度远高于第一比较例。此外,当比较所制备的球团矿中粒径为5mm以下的小颗粒球团矿的量时,第二比较例、第一和第二实施例远少于第一比较例。
[0154]
此外,当比较第二比较例与第一和第二实施例时,根据第一和第二实施例的球团矿的残存率高于利用高价无机粘结剂制备的第二比较例。
[0155]
另外,与第二比较例相比,根据第一实施例的球团矿的落下残存率和压缩强度在预定范围内较小,但是落下残存率和压缩强度类似于第二比较例,这是制备镍铁时不会出现问题的程度。此外,与使用高价无机粘结剂的第二比较例相比,根据第二实施例的球团矿的落下残存率和压缩强度高于预定范围。
[0156]
由此可见,利用通过根据本发明实施例的方法来制备的粘结剂制备的球团矿具有与利用现有粘结剂制备的球团矿类似或进一步改善的强度。
[0157]
另外,与根据第一实施例的粘结剂相比,根据第二实施例的粘结剂可以制备出残存率、落下残存率和压缩强度高的球团矿。
[0158]
如上所述,在本发明实施例中,将镍铁制备工艺的脱硫过程中产生的矿渣、用于制备碳钢的钢水制备工艺中产生的矿渣、工业副产物飘尘(flay ash)予以再利用,由此制备粘结剂。因此,可以制备成本低于现有技术的粘结剂。
[0159]
另外,利用根据实施例的粘结剂制备用于制备镍铁的原料球团矿时,可以制备出与利用现有粘结剂制备的球团矿强度类似或者强度提高的球团矿。
[0160]
因此,根据本发明实施例,既可降低用于制备球团矿的成本,又可确保强度。
[0161]
另外,由于通过将镍铁制备工艺的脱硫过程中产生的小颗粒脱硫矿渣再利用来制备粘结剂,可以节省现有现有技术中未能再利用的小颗粒脱硫矿渣的库存管理成本。
[0162]
此外,小颗粒脱硫矿渣中含有镍(ni),将其作为粘结剂的原料再利用制备球团矿,因此所述小颗粒脱硫矿渣起到用于制备镍铁或用于提供镍(ni)的源材料的作用。
[0163]
因此,可以减少用于制备镍铁的主原料和用于提供镍(ni)的源材料的高价镍矿的使用量,从而可以降低制备镍铁所需的成本。
[0164]
工业实用性
[0165]
根据本发明实施例的球团矿的制备方法,可以制备成本低于现有技术的粘结剂。
另外,利用根据实施例的粘结剂制备用于制备镍铁的原料球团矿时,可以制备出与利用现有粘结剂制备的球团矿强度类似或者强度提高的球团矿。
再多了解一些
本文用于企业家、创业者技术爱好者查询,结果仅供参考。