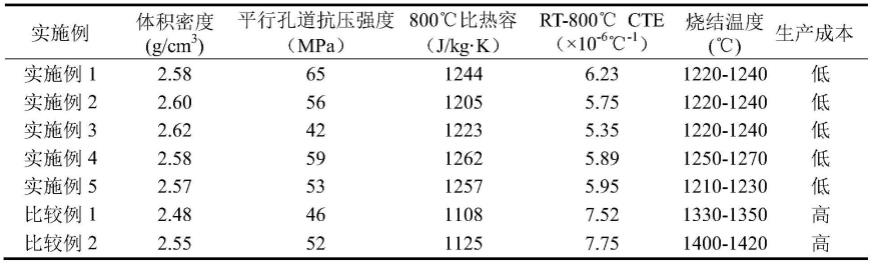
1.本发明属于环保节能新材料技术领域,具体涉及一种低成本高性能蜂窝陶瓷及其制备方法。
背景技术:
2.蓄热燃烧法(rto)是处理挥发性有机物vocs的主流技术之一,高性能蜂窝陶瓷正是rto装置中的核心部件,具有比表面积大、抗热震性好、蓄热能力高、压降小、热阻小、导热性能好、适应性强等优点,在我国喷涂、食用油业、石化行业、化学化工、制药业、电子行业、纺织业、采矿业、垃圾焚烧、印刷等行业的vocs处理中发挥了重要的作用,其工作温度一般在800℃左右。
3.目前,国内外rto装置中高性能蜂窝陶瓷体材质主要为莫来石质、堇青石质、碳化硅质、氧化铝质等一种或多种材质复合而成,使用的原材料主要是莫来石、氧化铝、碳化硅、滑石、高岭土、铝矾土、红柱石等,价格昂贵,且烧成温度高,导致vocs处理用蜂窝陶瓷生产成本过高,中国专利cn106977174b也提到了这一点。另外,蜂窝陶瓷挤出成型要求泥料具有较好的塑性,添加了大量的粘结剂、塑化剂,使用的粘结剂多为甲基纤维素、羟丙基甲基纤维素、羧甲基纤维素、聚乙烯醇等,价格昂贵,进一步提高了蜂窝陶瓷生产成本。
4.我国是工业大国,每年会产生大量工业固废,如铝矾土尾矿、堇青石废瓷粉等,其处理方式一般是堆存、填埋等,不仅会造成资源浪费,还会造成土地占用、环境污染和安全堆存等系列问题。
技术实现要素:
5.为解决现有问题,本发明的目的之一是,提供一种低成本高性能蜂窝陶瓷的制备方法,本发明的另一目的在于提供一种低成本高性能蜂窝陶瓷。本发明的技术方案既可以降低高性能蜂窝陶瓷的原材料成本和烧结成本,又可以消耗铝矾土尾矿、堇青石废瓷粉等工业固废,实现高性能化、高值化利用。
6.本发明所提供的技术方案如下:
7.一种低成本高性能蜂窝陶瓷的制备方法,包括以下步骤:
8.1)配料:分别称取45-65wt%的铝矾土尾矿、20-40wt%的堇青石废瓷粉、5-20wt%的助熔剂,然后采用干法混合,例如1h,制得无机混合粉料,以所述无机混合粉料的总重量计,称取0.5-2wt%的膨润土,1-2wt%的有机粘结剂,然后干法混合,例如1h,制得总混合粉料;
9.2)捏合:将步骤1)所得的所述总混合粉料置于捏合机器中,加入总混合粉料16-20wt%的水进行捏合,例如10分钟,再加入总混合粉料1-2wt%的润滑剂和1-2wt%的塑化剂进行捏合,得到泥料;
10.3)粗炼泥:使用真空炼泥机将步骤2)得到的所述泥料炼制成泥段,真空度为-0.08mpa~-0.1mpa;
11.4)陈腐:将步骤3)得到的所述泥段用塑料膜密封包裹,置于温度为20-30℃,湿度≥40%rh的环境中≥24h;
12.5)精炼泥:使用真空炼泥机将步骤4)得到的泥段炼制2-3遍,真空度为-0.08mpa~-0.1mpa;
13.6)挤出成型:将步骤5)得到的具有塑性的泥段通过真空挤出机和模具挤出成蜂窝状结构,然后进行连续微波干燥;
14.7)烧结:将步骤6)得到的干燥后的坯体切割成固定高度后在1210-1270℃的高温中进行烧结,得到所述的低成本高性能蜂窝陶瓷。
15.上述技术方案中:
16.堇青石是一种低膨胀的陶瓷材料,使用堇青石废瓷粉为原材料制备的高性能蜂窝陶瓷具有较低的热膨胀系数cte(rt-800℃)为5.35-6.23
×
10-6
℃-1
,使高性能蜂窝陶瓷在频繁蓄热、放热使用过程中不容易开裂,延长使用寿命;
17.使用膨润土可提高制作过程中坯体的塑性和结合性,改善了蜂窝陶瓷成型性能,减少了价格昂贵的有机粘结剂、塑化剂使用量约1-2wt%,进一步降低了高性能蜂窝陶瓷的生产成本;
18.铝矾土尾矿中铁含量较高,与锂瓷石或透辉石协同作用,降低高温液相形成温度,促进烧结,使高性能蜂窝陶瓷的烧结温度降低约100-200℃,节约烧成成本;
19.总体上,使用铝矾土尾矿、堇青石废瓷粉等工业固废制备高性能蜂窝陶瓷,固废含量比达到80%-95%,从原料成本上极大地降低了高性能蜂窝陶瓷的原材料成本。
20.具体的,步骤1)中,所述铝矾土尾矿为山西铝矾土熟料手选尾矿加工成的粉料,堆积密度≥1.3g/cm3,主要化学组成含有al2o
3 55-65wt%,sio
2 28-38wt%,fe2o
3 5-10wt%,tio2≤2wt%,其它杂质含量不超过5wt%。
21.具体的,所述铝矾土尾矿1000℃烧失为0。
22.具体的步骤1)中,所述的堇青石废瓷粉为生产堇青石蜂窝陶瓷加工过程中的磨削粉和/或不合格品加工成的粉料,堆积密度≥1g/cm3,主要化学组成含有al2o
3 32.7-37.7wt%,sio
2 47.5-52.5wt%,mgo 11.5-15.5wt%,fe2o3≤1wt%,tio2≤1wt%,cao≤1wt%。
23.具体的,步骤1)中,堇青石废瓷粉1000℃烧失为0。
24.具体的,步骤1)中,所述无机混合粉料中各无机粉料粒度分别为230目筛以下。
25.具体的,步骤1)中,所述有机粘结剂为甲基纤维素、羟丙基甲基纤维素、羧甲基纤维素、乙基纤维素或聚乙烯醇中的任意一种或几种按任意比例的混合物。
26.具体的,步骤2)中,所述润滑剂为玉米油、豆油、桐油、轻矿物油、α-烯烃、聚烯烃油、多元醇酯、烃油或妥尔油中的任意一种或多种以上的组合。
27.具体的,,步骤2)中,所述塑化剂为甘油。
28.本发明还提供了根据上述制备方法所制得的低成本高性能蜂窝陶瓷。
29.本发明制备的低成本高性能蜂窝陶瓷性能指标为体积密度2.57-2.62g/cm3,平行孔道抗压强度为42-65mpa,cte(rt-800℃)为5.35-6.23
×
10-6
℃-1
,800℃比热容>1200j/kg
·
k,具有体积密度大,强度高,cte低,比热容大等优点,可以满足喷涂、食用油业、石化行业、化学化工、制药业、电子行业、纺织业、采矿业、垃圾焚烧、印刷等行业各种处理vocs的
rto设备用的蜂窝陶瓷蓄热体使用要求。
30.本发明实现了铝矾土尾矿、堇青石废瓷粉等工业固废的高性能化、高值化利用,缓解了工业固废带来的环境污染、土地占用、安全堆存等系列问题,推进资源全面节约和循环利用,具有重大的经济效益和社会效益。
具体实施方式
31.以下对本发明的原理和特征进行描述,所举实施例只用于解释本发明,并非用于限定本发明的范围。
32.实施例1:
33.1)配料:分别称取65wt%的铝矾土尾矿、20wt%的堇青石废瓷粉、15wt%的透辉石,然后采用干法混合1h制得无机混合粉料,以无机混合粉料计,称取0.5wt%的膨润土,2wt%的甲基纤维素,然后干法混合1h制得总混合粉料;
34.2)捏合:将步骤1)所得总混合粉料置于捏合机器中,加入总混合粉料16%的水进行捏合10分钟,加入总混合粉料2wt%的豆油和2wt%的甘油进行捏合20分钟;
35.3)粗炼泥:使用真空炼泥机将步骤2)中捏合的泥料炼制成泥段,真空度为-0.08mpa~-0.1mpa;
36.4)陈腐:将步骤3)的泥段用塑料膜密封包裹,置于温度为20-30℃,湿度≥40%rh的环境陈腐24h;
37.5)精炼泥:使用真空炼泥机将步骤4)的泥段炼制3遍,真空度为-0.08mpa~-0.1mpa;
38.6)挤出成型:将步骤5)具有塑性的泥段通过真空挤出机和模具挤出成蜂窝状结构,然后进行连续微波干燥;
39.7)烧结:将步骤6)中干燥后的坯体切割成固定高度后在1220℃-1240℃的高温中进行烧结。
40.实施例2:
41.1)配料:分别称取50wt%的铝矾土尾矿、35wt%的堇青石废瓷粉、15wt%的透辉石,然后采用干法混合1h制得无机混合粉料,以无机混合粉料计,称取1wt%的膨润土,1.5wt%的羟丙基甲基纤维素,然后干法混合1h制得总混合粉料;
42.2)捏合:将步骤1)所得总混合粉料置于捏合机器中,加入总混合粉料18%的水进行捏合10分钟,加入总混合粉料1.5wt%的桐油和1.5wt%的甘油进行捏合20分钟;
43.3)粗炼泥:使用真空炼泥机将步骤2)中捏合的泥料炼制成泥段,真空度为-0.08mpa~-0.1mpa;
44.4)陈腐:将步骤3)的泥段用塑料膜密封包裹,置于温度为20-30℃,湿度≥40%rh的环境中陈腐24h;
45.5)精炼泥:使用真空炼泥机将步骤4)的泥段炼制2-3遍,真空度为-0.08mpa~-0.1mpa;
46.6)挤出成型:将步骤5)具有塑性的泥段通过真空挤出机和模具挤出成蜂窝状结构,然后进行连续微波干燥;
47.7)烧结:将步骤6)中干燥后的坯体切割成固定高度后在1220℃-1240℃的高温中
进行烧结。
48.实施例3:
49.1)配料:分别称取45wt%的铝矾土尾矿、40wt%的堇青石废瓷粉、15wt%的透辉石,然后采用干法混合1h制得无机混合粉料,以无机混合粉料计,称取2wt%的膨润土,1wt%的羧甲基纤维素,然后干法混合1h制得总混合粉料;
50.2)捏合:将步骤1)所得总混合粉料置于捏合机器中,加入总混合粉料20%的水进行捏合10分钟,加入总混合粉料1wt%的桐油和1wt%的甘油进行捏合20分钟;
51.3)粗炼泥:使用真空炼泥机将步骤2)中捏合的泥料炼制成泥段,真空度为-0.08mpa~-0.1mpa;
52.4)陈腐:将步骤3)的泥段用塑料膜密封包裹,置于温度为20-30℃,湿度≥40%rh的环境中陈腐24h;
53.5)精炼泥:使用真空炼泥机将步骤4)的泥段炼制2-3遍,真空度为-0.08mpa~-0.1mpa;
54.6)挤出成型:将步骤5)具有塑性的泥段通过真空挤出机和模具挤出成蜂窝状结构,然后进行连续微波干燥;
55.7)烧结:将步骤6)中干燥后的坯体切割成固定高度后在1220℃-1240℃的高温中进行烧结。
56.实施例4:
57.1)配料:分别称取60wt%的铝矾土尾矿、35wt%的堇青石废瓷粉、5wt%的锂瓷石,然后采用干法混合1h制得无机混合粉料,以无机混合粉料计,称取2wt%的膨润土,1wt%的乙基纤维素,然后干法混合1h制得总混合粉料;
58.2)捏合:将步骤1)所得总混合粉料置于捏合机器中,加入总混合粉料20%的水进行捏合10分钟,加入总混合粉料1wt%的聚烯烃油和1wt%的甘油进行捏合20分钟;
59.3)粗炼泥:使用真空炼泥机将步骤2)中捏合的泥料炼制成泥段,真空度为-0.08mpa~-0.1mpa;
60.4)陈腐:将步骤3)的泥段用塑料膜密封包裹,置于温度为20-30℃,湿度≥40%rh的环境中陈腐24h;
61.5)精炼泥:使用真空炼泥机将步骤4)的泥段炼制2-3遍,真空度为-0.08mpa~-0.1mpa;
62.6)挤出成型:将步骤5)具有塑性的泥段通过真空挤出机和模具挤出成蜂窝状结构,然后进行连续微波干燥;
63.7)烧结:将步骤6)中干燥后的坯体切割成固定高度后在1250-1270℃的高温中进行烧结。
64.实施例5:
65.1)配料:分别称取55wt%的铝矾土尾矿、25wt%的堇青石废瓷粉、20wt%的锂瓷石,然后采用干法混合1h制得无机混合粉料,以无机混合粉料计,称取2wt%的膨润土,1wt%的聚乙烯醇,然后干法混合1h制得总混合粉料;
66.2)捏合:将步骤1)所得总混合粉料置于捏合机器中,加入总混合粉料20%的水进行捏合10分钟,加入总混合粉料1wt%的多元醇酯和1wt%的甘油进行捏合20分钟;
67.3)粗炼泥:使用真空炼泥机将步骤2)中捏合的泥料炼制成泥段,真空度为-0.08mpa~-0.1mpa;
68.4)陈腐:将步骤3)的泥段用塑料膜密封包裹,置于温度为20-30℃,湿度≥40%rh的环境中陈腐24h;
69.5)精炼泥:使用真空炼泥机将步骤4)的泥段炼制2-3遍,真空度为-0.08mpa~-0.1mpa;
70.6)挤出成型:将步骤5)具有塑性的泥段通过真空挤出机和模具挤出成蜂窝状结构,然后进行连续微波干燥;
71.7)烧结:将步骤6)中干燥后的坯体切割成固定高度后在1210-1230℃的高温中进行烧结。
72.比较例1:
73.1)配料:分别称取80wt%的特级铝矾土、20wt%的锂瓷石,然后采用干法混合1h制得无机混合粉料,以无机混合粉料计,4wt%的甲基纤维素,然后干法混合1h制得总混合粉料;
74.2)捏合:将步骤1)所得总混合粉料置于捏合机器中,加入总混合粉料23%的水进行捏合10分钟,加入总混合粉料4wt%的豆油和5wt%的甘油进行捏合20分钟;
75.3)粗炼泥:使用真空炼泥机将步骤2)中捏合的泥料炼制成泥段,真空度为-0.08mpa~-0.1mpa;
76.4)陈腐:将步骤3)的泥段用塑料膜密封包裹,置于温度为20-30℃,湿度≥40%rh的环境中陈腐24h;
77.5)精炼泥:使用真空炼泥机将步骤4)的泥段炼制2-3遍,真空度为-0.08mpa~-0.1mpa;
78.6)挤出成型:将步骤5)具有塑性的泥段通过真空挤出机和模具挤出成蜂窝状结构,然后进行连续微波干燥;
79.7)烧结:将步骤6)中干燥后的坯体切割成固定高度后在1330℃-1350℃的高温中进行烧结。
80.比较例2:
81.1)参照发明cn111377723b,配料:分别称取45wt%的煅烧高岭土、48wt%的工业氧化铝,5wt%的水洗高岭土,3wt%的滑石,球磨2小时,过100目振动筛,得到陶瓷粉末;
82.2)配液:分别称取3wt%聚乙二醇、3wt%聚乙烯醇、2wt%木质素磺酸钙、92wt%水加入到50℃的温水中,充分溶解定量后得具有润滑减水作用的水溶液,备用。
83.3)将步骤1)的陶瓷粉末、复合羟丙基甲基纤维素、水溶液按照100:3:7的重量比在强力混料机中混合,水溶液通过喷雾装置喷洒于物料上,强力混合1小时,混合均匀,制备成半湿性混合料;
84.4)捏合:将步骤3)所得半湿性混合料置于捏合机器中,加入总混合粉料10%的水进行捏合10分钟
85.5)炼泥及陈腐:真空练制步骤2)中捏合的泥料成泥段,陈腐24h;
86.6)挤出成型:将步骤5)具有塑性的泥段挤出成蜂窝状结构,然后进行连续微波干燥;
87.7)烧结:将步骤6)中干燥后的坯体切割成固定高度后在1400-1420℃的高温中进行烧结。
88.专利中列举的各实施例1-5、比较例1-2的测试结果如表1所示。其中,体积密度的检测方法:参考gb/t 2997-2015所公开的检测标准,平行孔道抗压强度的检测方法:参考jc/t 686-1998所公开的检测标准,800℃比热容的检测方法:参考jc/t 2135-2012所公开的检测标准,cte的检测方法:参考gb/t 7320-2008顶杆法所公开的检测标准,其中,各实施例和各比较例中制出用来测试用的样品的规格为150*150*150mm,单边35孔,当然实际生产的产品的规格不仅仅局限于此。
89.表1专利中列举的各实施例1-5、比较例1-2的测试结果
[0090][0091]
本专利列举了部分实施例说明本发明,并不构成对本发明的限制,可以进行许多修改。
[0092]
从实施例1-5和比较例1-2可以看出,蜂窝陶瓷蓄热体的体积密度、平行于孔道抗压强度等关键性能指标较接近,无明显差距,且cte和800℃比热容实施例优于对比例,可以满足喷涂、食用油业、石化行业、化学化工、制药业、电子行业、纺织业、采矿业、垃圾焚烧、印刷等行业各种处理vocs的rto设备用的蜂窝陶瓷蓄热体使用要求。
[0093]
实施例1-5使用铝矾土尾矿、堇青石废瓷粉等工业固废制备高性能蜂窝陶瓷,固废含量比达到80%-95%,从原料成本上极大地降低了高性能蜂窝陶瓷的原材料成本,同时也实现了铝矾土尾矿、堇青石废瓷粉等工业固废的高性能化、高值化利用,缓解了工业固废带来的环境污染、土地占用、安全堆存等系列问题,推进资源全面节约和循环利用,具有重大的经济效益和社会效益,加快生态文明建设;
[0094]
实施例1-5由于铝矾土尾矿中铁含量较高和透辉石或锂瓷石协同作用,降低高温液相形成温度,促进烧结,使高性能蜂窝陶瓷的烧结温度降低约100-200℃,节约烧成成本;
[0095]
实施例1-5使用了低价膨润土,可提高制作过程中坯体的塑性和结合性,改善了蜂窝陶瓷成型性能,减少了价格昂贵的有机粘结剂、塑化剂使用量,进一步降低了高性能蜂窝陶瓷的生产成本。实施例1-3可以看出,膨润土用量增加,有机粘结剂、塑化剂、润滑剂等成型助剂使用量减少,在保证泥料挤出性能的情况下,膨润土用量越多,有机粘结剂、塑化剂、润滑剂等成型助剂使用量越少越好,可以降低成本,减少烧成收缩。
[0096]
实施例1-5,使用低膨胀堇青石废瓷粉为原材料制备的高性能蜂窝陶瓷具有较低的热膨胀系数cte(rt-800℃)为5.35-6.23
×
10-6
℃-1
,使高性能蜂窝陶瓷在频繁蓄热、放热使用过程中不容易开裂,延长使用寿命。
[0097]
以上所述仅为本发明的较佳实施例,并不用以限制本发明,凡在本发明的精神和原则之内,所作的任何修改、等同替换、改进等,均应包含在本发明的保护范围之内。
再多了解一些
本文用于企业家、创业者技术爱好者查询,结果仅供参考。