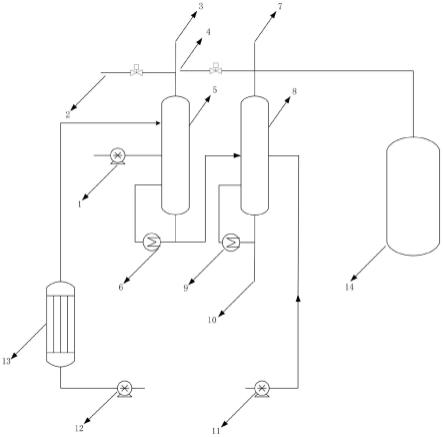
1.本发明属于三氟甲磺酰氟的纯化技术领域,具体涉及一种连续精馏纯化三氟甲磺酰氟的装置和方法。
背景技术:
2.三氟甲磺酰氟是精细化工领域重要的中间体,可以作为有机合成、农药医药、离子液体及锂离子电解质等重要原料。三氟甲磺酰氟常压下沸点为-21.7℃,常温下是有微弱气味,易液化的气体,与氢气不反应,不溶于冷水、氟化氢等,在热水及碱性条件下易水解。
3.三氟甲磺酰氟有光解法、化学直接氟化法、电解法以及以氟化钾氟化三氟甲磺酰氯的方法,但是目前工业上应用最广的还是电解法,以甲基磺酰氟(ch3so2f)或甲基磺酰氯(ch3so2cl)电解生产三氟甲磺酰氟的方法,是以甲基磺酰氟或甲基磺酰氯(ch3so2cl)为原料和过量的液体氟化氢在电解槽中进行电化学氟化反应,产物有三氟甲磺酰氟(cf3so2f)、氢气(h2)、四氟化碳(cf4)、二氟亚砜(sof2)、二氧化碳(co2)及二氟化氧(of2),由于氟化氢过量,且其饱和蒸汽压较高,使得产出的气体混合物中夹杂有一定量的氟化氢(hf)气体。此气体混合物中,除氢气之外,其余杂质气体含量不高,但是影响三氟甲磺酰氟的使用,因此必须对其进行提纯。
4.有关三氟甲磺酰氟的纯化方法较少,在非专利文献《三氟甲烷磺酸酐的合成研究》报道了将三氟甲基磺酰氟从电解槽出口与氢气一起被引出,经过冷凝器使被挟带出的氟化氢冷却回流重新返回到电解槽,其余气体经缓冲器进入水吸收器与碱洗吸收器除去全部氯化氢和氟化氢,再经过气液分离器而进入贮气柜,气体被氢气压缩机抽出先进入冷冻脱水器后通过分子筛干燥器,以除去水洗及碱洗过程带入的水份,被干燥的气体经过深冷液化流入三氟甲烷磺酰氟贮槽,未被冷凝液化的氢气放空。
5.中国专利cn200810243626.x报道了三氟甲磺酰氟分离精制的方法包括以下内容:将甲基磺酰氟电化学氟化气相产物进行降温冷凝,使其中的氟化氢冷凝为液相,之后经过气液分离后,将气相物料通过碳酸盐水溶液水洗吸收除去氟化氢,再经过气液分离,然后将气相物料加入脱水剂,进行脱水干燥,再经过气固分离后,将气相物料进行深冷,最后对其进行气液分离精制得到产品三氟甲磺酰氟气体。
6.中国船舶集团有限公司第七一八研究所提供了在精馏塔内提纯电解生成的三氟甲磺酰氟气体,最后得到的产品纯度较高有99.5%。
7.上述资料中,以电解甲基磺酰氟(或甲基磺酰氯)产物为原料三氟甲磺酰氟纯化方法均包含如下步骤:冷凝除去部分氟化氢,碳酸盐水洗除去大部分氟化氢,使用脱水剂除去除氟化氢过程中带来的水分,再经过深冷除去氢气得到较为纯净的三氟甲磺酰氟,这类纯化方法有如下问题:(1)纯化步骤多,需要的设备也较多,需要走多步的气液分离设备,除水设备;(2)工艺的安全性问题,由于采用的工艺路线较长,并且氢气在最后一步才去除,容易发生氢气的泄漏爆炸事故,因此对所有纯化设备的密封性要求较高;(3)三氟甲磺酰氟在碱性溶液中能够水解,使用碳酸盐溶液吸收除去氟化氢,会同时吸收一部分三氟甲磺酰氟,造
成产品的损失,同时三氟甲磺酰氟和碳酸盐反应会产生二氧化碳,带来新的杂质,影响产品的纯度;(4)采取先引入水分,再经过脱水剂除水的方法,活化脱水剂需要消耗惰性气体及电能,使纯化的能耗增加;(5)产品最后只是经过简单的气液分离除去氢气得到,轻组分杂质如四氟化碳(cf4)、二氟亚砜(sof2)、二氧化碳(co2)及二氟化氧(of2)没有经过有效措施除去,产品三氟甲磺酰氟的最终纯度在文献中均没有提及。中国船舶集团提出的纯化方法对于生产量较少的情况比较适用,对于生产量大的情况,需要设备较多,效率较低。
8.以电解甲基磺酰氟(或甲基磺酰氯)产物为原料三氟甲磺酰氟纯化方法均包含如下步骤:在一个精馏塔内去除轻组分和重组分杂质,分多个阶段,这类纯化方法有如下问题:(1)纯化操作步骤多,设备涉及到多个状态切换,能量利用率低;(2)氟化氢和三氟甲磺酰氟分离效果较差,产品的纯度不高;(3)生产效率较低,同样的产能需要的设备较多;(4)排轻过程排出的产品含量较高,收率较低。因此,需要开发一种连续精馏纯化三氟甲磺酰氟的装置和方法。
技术实现要素:
9.本发明所要解决的技术问题在于针对上述现有技术的不足,提供一种连续精馏纯化三氟甲磺酰氟的装置和方法,本发明方法采用较少的纯化设备,简化了纯化流程,避免了产品随着排轻排出,造成损失,提高了三氟甲磺酰氟的纯度,降低了设备运行压力,有效地提高了生产过程的安全性。
10.为解决上述技术问题,本发明采用的技术方案是:连续精馏纯化三氟甲磺酰氟的装置和方法,包括第一流体输送装置,所述第一流体输送装置的出料口连接有脱轻塔,所述脱轻塔的顶部设置有脱轻塔排放口,所述脱轻塔的上部连接有氟化氢冷却器,所述脱轻塔的底部出料口连接有脱重塔,所述脱重塔的出料口连接有精品罐;所述脱轻塔的底部连接有脱轻塔再沸器,所述脱重塔的底部连接有脱重塔再沸器,所述脱重塔的顶部设置有轻组分排放口,所述脱重塔的底部还设置有底部产物排放口。
11.优选地,所述脱轻塔排放口上设置有脱轻塔取样口;所述脱重塔中部连接有第二流体输送装置;所述氟化氢冷却器底部连接有第三流体输送装置。
12.优选地,所述脱轻塔的高度为3m~15m、直径为0.05m~1m;所述脱重塔的高度为3m~15m、直径为0.05m~1m。
13.优选地,所述脱轻塔和所述脱重塔内的填料均为θ环、鲍尔环或拉西环,所述填料的直径为5mm~100mm。
14.本发明还提供一种采用上述装置连续精馏纯化三氟甲磺酰氟的方法,其特征在于,包括以下步骤:
15.s1、将甲基磺酰氟的电解产物和经冷却的氟化氢通入脱轻塔中精馏,所述脱轻塔塔顶产出轻组分杂质,所述脱轻塔塔底产出底部产物;所述脱轻塔塔顶温度为-60~-15℃,塔釜的温度为-10℃~10℃、塔釜压力为0.6mpa~1.3mpa,回流比为50~500;所述经冷却的氟化氢和甲基磺酰氟的电解产物的质量比为(0.12~0.30):1;
16.s2、将s1中得到的底部产物的一部分加热回流到脱轻塔中,剩余部分通入脱重塔中,且向所述脱重塔中通入甲基磺酰氟,所述脱重塔塔顶产出精品三氟甲磺酰氟,所述脱重塔塔底产出重组分杂质;所述重组分杂质的一部分加热回流到脱重塔中,剩余部分排出;所
述脱重塔的塔顶温度为-50~0℃,塔釜温度为-5℃~25℃、塔釜压力为0.3mpa~1.0mpa,回流比为10~30。
17.优选地,s1中所述甲基磺酰氟的电解产物的组成包括三氟甲磺酰氟的含量≥15vol%,氟化氢的含量≤2vol%,氢气的含量≤80vol%,四氟化碳的含量≤1vol%,二氟亚砜的含量≤1vol%,二氧化碳的含量≤0.4vol%,二氟化氧的含量≤0.5vol%。
18.优选地,s1中所述甲基磺酰氟的电解产物的温度为-10℃~20℃,所述甲基磺酰氟的电解产物通入脱轻塔的质量流量为30kg/h~300kg/h;所述氟化氢的冷却温度为-70℃~-30℃。
19.优选地,s1中所述脱轻塔的理论塔板数为10~50;s2中所述脱重塔的理论塔板数为20~80;控制通入所述脱重塔中的甲基磺酰氟与剩余部分的底部产物的质量流量为(0.05~0.1):1。
20.优选地,s2中所述精品三氟甲磺酰氟的纯度≥99.9vol%,其中水分的含量≤0.01vol%,氟化氢的含量≤0.05vol%,四氟化碳的含量≤0.005vol%,二氟亚砜的含量≤0.005vol%,二氧化碳的含量≤0.005vol%,二氟化氧的含量≤0.005vol%。
21.本发明与现有技术相比具有以下优点:
22.1、本发明方法中甲基磺酰氟的电解产物通过脱轻塔精馏与一定量的氟化氢冷却回流混合,氟化氢有氟氢键和三氟甲磺酰氟更容易结合到一起,有利于三氟甲磺酰氟的回流收集,控制了三氟甲磺酰氟的排出,提高了排轻的效率,节省了冷量;脱重塔中加入甲基磺酰氟,甲基磺酰氟加入打破了三氟甲磺酰氟和氟化氢之间的平衡,有利于精馏时,氟化氢和三氟甲磺酰氟的分离,且甲基磺酰氟从脱重塔底部排出,可返回电解系统作为原料使用。
23.2、本发明方法通过控制脱轻塔精馏、脱重塔精馏的条件,脱轻塔上部经冷却后氟化氢的量,脱重塔加入甲基磺酰氟的比例,脱轻塔底部产出的底部产物输送至脱重塔的速率、由脱重塔顶部收集纯化后三氟甲磺酰氟的时间,完成对三氟甲磺酰氟的纯化。本发明方法得到的精品三氟甲磺酰氟具有较高的纯度,可达到99.9%,且本发明方法操作简单,有利于工业化稳定生产,具有较高的生产效率,极大的降低了生产成本。
24.3、本发明工艺连续运行,避免了不同阶段的冷热切换浪费的时间,在提高了运行效率,同样产能的条件下,使用更少的设备。
25.下面结合附图和实施例对本发明作进一步详细说明。
附图说明
26.图1是本发明装置的结构示意图。
27.附图标记说明:
28.1—第一流体输送装置;2—脱轻塔取样口;3—脱轻塔排放口;4—脱重塔取样口;5—脱轻塔;6—脱轻塔再沸器;7—轻组分排放口;8—脱重塔;9—脱重塔再沸器;10—底部产物排放口;11—第二流体输送装置;12—第三流体输送装置;13—氟化氢冷却器;14—精品罐。
具体实施方式
29.以下结合实施例对本发明进一步说明。本发明包括但不限于以下实施例,凡是在
本发明精神的原则之下进行的任何等同替换或局部改进,都将视为在本发明的保护范围之内。
30.以下实施例中用到的原料氟化氢为承德莹科精细化工股份有限公司生产,甲基磺酰氟为中船重工(邯郸)派瑞特种气体有限公司自产。实施例中所用到的检测方法及仪器见表1。
31.表1实施例中检测方法
32.检测项目检测方法hf氟离子电极法h2o五氧化二磷电解法气体组分气相色谱法
33.注:表1气体组分指三氟甲磺酰氟(cf3so2f)、氢气(h2)、四氟化碳(cf4)、二氟亚砜(sof2)、二氧化碳(co2)及二氟化氧(of2)。
34.所述指标要求如下:三氟甲磺酰氟的体积含量≥99.9%,水分的体积含量≤0.01%,氟化氢的体积含量≤0.05%,四氟化碳的体积含量≤0.01%,二氟亚砜的体积含量≤0.01%,二氧化碳的体积含量≤0.01%,二氟化氧的体积含量≤0.01%。
35.实施例1
36.如图1所示,本实施例的连续精馏纯化三氟甲磺酰氟的装置,包括第一流体输送装置1,所述第一流体输送装置1的出料口连接有脱轻塔5,所述脱轻塔5的顶部设置有脱轻塔排放口3,所述脱轻塔5的上部连接有氟化氢冷却器13,所述脱轻塔5的底部出料口连接有脱重塔8,所述脱重塔8的顶部出料口连接有精品罐14;所述脱轻塔5的底部连接有脱轻塔再沸器6,所述脱重塔8的底部连接有脱重塔再沸器9,所述脱重塔8的顶部还设置有轻组分排放口7,所述脱重塔8的底部还设置有底部产物排放口10。
37.本实施例中,所述脱轻塔排放口3上设置有脱轻塔取样口2;所述脱重塔8中部连接有第二流体输送装置11;所述氟化氢冷却器13底部连接有第三流体输送装置12。
38.本实施例中采用的装置,脱轻塔5高为3m,直径为0.05m,理论塔板数为10,脱轻塔5内置直径为5mm的不锈钢θ环填料;脱重塔8高为5m,直径为0.05m,理论塔板数为20,脱重塔8内置直径为5mm的不锈钢θ环填料;脱轻塔5、脱重塔8塔体、精品罐、氟化氢冷却器以及再沸器和管路均采用蒙乃尔材质。
39.本实施例装置对甲基磺酰氟的电解产物进行纯化时,先将甲基磺酰氟的电解产物在脱轻塔5中精馏,冷却后的氟化氢在脱轻塔5内回流下落;甲基磺酰氟的电解产物中的轻组分杂质由脱轻塔5的顶部出口收集,去除大部分轻组分杂质;再将脱轻塔5底部产出的底部产物输送至脱重塔8进行精馏,底部产物由脱重塔8中部进入,底部产物中的重质杂质氟化氢和甲基磺酰氟留在脱重塔8的底部,精品三氟甲磺酰氟由脱重塔8顶部的出口收集得到。本实施例装置将甲基磺酰氟的电解产物依次经过脱轻塔5精馏和脱重塔8精馏,利用杂质和产品的特性,去除了甲基磺酰氟的电解产物中的轻质杂质和重质杂质,提高了三氟甲磺酰氟的纯度;且提高了生产效率。
40.实施例2
41.本实施例采用实施例1中的装置连续精馏纯化三氟甲磺酰氟的方法,包括以下步骤:
42.s1、首先将实施例1中的装置整体抽真空至-0.1mpa,然后将甲基磺酰氟的电解产物经第一流体输送装置1以30kg/h的流量通入脱轻塔5中,将氟化氢经第三流体输送装置12输送至氟化氢冷却器13内,在温度为-70℃,流量为3.6kg/h的条件下通入脱轻塔5中上部,然后在所述脱轻塔5内进行精馏,所述脱轻塔5塔顶产出轻组分杂质,在脱轻塔取样口2进行取样检测分析,检测轻组分杂质中,三氟甲磺酰氟(cf3so2f)的含量为0,所述脱轻塔5塔底产出底部产物;所述脱轻塔5塔顶温度为-60,塔釜的温度为-10℃、压力为0.65mpa,回流比为50;
43.所述轻组分杂质包括氢气(h2)、四氟化碳(cf4)、二氟亚砜(sof2)、二氧化碳(co2)及二氟化氧(of2);所述底部产物包括氟化氢和三氟甲磺酰氟;所述经冷却的氟化氢和甲基磺酰氟的电解产物的质量比为0.12:1;所述甲基磺酰氟的电解产物的温度为-10℃;
44.s2、将s1中得到的底部产物的一部分以5kg/h的流量通入脱轻塔再沸器6中,加热蒸发回到脱轻塔5以提供精馏过程中的热量,剩余部分以28.6kg/h的流量通过压差脱重塔8中,且经第二输送装置11向所述脱重塔8中通入甲基磺酰氟,所述脱重塔8塔顶产出精品三氟甲磺酰氟,所述脱重塔8塔底产出的重组分杂质的一部分以30kg/h流量进入脱重塔再沸器9,加热蒸发回到脱重塔8中经蒸发精馏后收集,剩余部分以5.6kg/h的流量通过压差从底部产物排放口10排入电解槽继续使用;所述脱重塔8的塔顶温度为-50,塔釜温度为-5℃、塔釜压力为0.35mpa,回流比为10;所述重组分杂质包括氟化氢、甲基磺酰氟和三氟甲磺酰氟;控制通入所述脱重塔8中的甲基磺酰氟与剩余部分的底部产物的质量流量为0.05:1;
45.在脱重塔取样口4进行取样检测分析,检测精品三氟甲磺酰氟的纯度,如精品三氟甲磺酰氟的纯度<99.9(vol)%,则通过轻组分排放口7将气体排入电解气系统,重新经过精馏系统提纯;当三氟甲磺酰氟的纯度≥99.9(vol)%时,将制得的精品三氟甲磺酰氟收集到精品罐14内,其他杂质含量见表2。
46.本实施例中采用的装置与实施例1中的装置不同的是,脱轻塔5高为15m,直径为1m,理论塔板数为50,脱轻塔5内置直径为100m的不锈钢θ环填料;脱重塔8高为15m,直径为1m,理论塔板数为80,脱重塔8内置直径为100mm的不锈钢θ环填料;脱轻塔5、脱重塔8塔体、精品罐、氟化氢冷却器以及再沸器和管路均采用蒙乃尔材质。
47.实施例3
48.本实施例采用实施例1中的装置连续精馏纯化三氟甲磺酰氟的方法,包括以下步骤:
49.s1、首先将实施例1中的装置整体抽真空至-0.1mpa,然后将甲基磺酰氟的电解产物经第一流体输送装置1以300kg/h的流量通入脱轻塔5中,将氟化氢经第三流体输送装置12输送至氟化氢冷却器13内,在温度为-40℃,流量为90kg/h的条件下通入脱轻塔5中上部,然后在所述脱轻塔5内进行精馏,所述脱轻塔5塔顶产出轻组分杂质,在脱轻塔取样口2进行取样检测分析,检测轻组分杂质中,三氟甲磺酰氟(cf3so2f)的含量为0,所述脱轻塔5塔底产出底部产物;所述脱轻塔5塔顶温度为-20℃,塔釜的温度为5℃、压力为1.30mpa,回流比为500;
50.所述轻组分杂质包括氢气(h2)、四氟化碳(cf4)、二氟亚砜(sof2)、二氧化碳(co2)及二氟化氧(of2);所述底部产物包括氟化氢和三氟甲磺酰氟;所述经冷却的氟化氢和甲基磺酰氟的电解产物的质量比为0.30:1;所述甲基磺酰氟的电解产物的温度为20℃;
51.s2、将s1中得到的底部产物的一部分以50kg/h的流量通入脱轻塔再沸器6中,加热蒸发回到脱轻塔5以提供精馏过程中的热量,剩余部分以340kg/h的流量通过压差脱重塔8中,且经第二输送装置11向所述脱重塔8中通入甲基磺酰氟,所述脱重塔8塔顶产出精品三氟甲磺酰氟,所述脱重塔8塔底产出的重组分杂质中的一部分以300kg/h流量进入脱重塔再沸器9,加热蒸发回到脱重塔8中经蒸发精馏后收集,剩余部分以125.2kg/h的流量通过压差从底部产物排放口10排入电解槽继续使用;所述脱重塔8的塔顶温度为-5,塔釜温度为20℃、塔釜压力为1.0mpa,回流比为30;所述重组分杂质包括氟化氢、甲基磺酰氟和三氟甲磺酰氟;控制通入所述脱重塔8中的甲基磺酰氟与剩余部分的底部产物的质量流量为0.1:1;
52.在脱重塔取样口4进行取样检测分析,检测精品三氟甲磺酰氟的纯度,如精品三氟甲磺酰氟的纯度<99.9(vol)%,则通过轻组分排放口7将气体排入电解气系统,重新经过精馏系统提纯;当三氟甲磺酰氟的纯度≥99.9(vol)%时,将制得的精品三氟甲磺酰氟收集到精品罐14内,其他杂质含量见表2。
53.本实施例中采用的装置与实施例1中的装置不同的是,脱轻塔5高为15m,直径为1m,理论塔板数为50,脱轻塔5内置直径为100m的鲍尔环填料;脱重塔8高为15m,直径为1m,理论塔板数为80,脱重塔8内置直径为100mm的鲍尔环填料;脱轻塔5、脱重塔8塔体、精品罐、氟化氢冷却器以及再沸器和管路均采用蒙乃尔材质。
54.实施例4
55.本实施例采用实施例1中的装置连续精馏纯化三氟甲磺酰氟的方法,包括以下步骤:
56.s1、首先将实施例1中的装置整体抽真空至-0.1mpa,然后将甲基磺酰氟的电解产物经第一流体输送装置1以200kg/h的流量通入脱轻塔5中,将氟化氢经第三流体输送装置12输送至氟化氢冷却器13内,在温度为-50℃,流量为40kg/h的条件下通入脱轻塔5中上部,然后在所述脱轻塔5内进行精馏,所述脱轻塔5塔顶产出轻组分杂质,在脱轻塔取样口2进行取样检测分析,检测轻组分杂质中,三氟甲磺酰氟(cf3so2f)的含量为0,所述脱轻塔5塔底产出底部产物;所述脱轻塔5塔顶温度为-30,塔釜的温度为0℃、压力为0.8mpa,回流比为300;
57.所述轻组分杂质包括氢气(h2)、四氟化碳(cf4)、二氟亚砜(sof2)、二氧化碳(co2)及二氟化氧(of2);所述底部产物包括氟化氢和三氟甲磺酰氟;所述经冷却的氟化氢和甲基磺酰氟的电解产物的质量比为0.2:1;所述甲基磺酰氟的电解产物的温度为10℃;
58.s2、将s1中得到的底部产物的一部分以80kg/h的流量通入脱轻塔再沸器6中,加热蒸发回到脱轻塔5以提供精馏过程中的热量,剩余部分以163.4kg/h的流量通过压差脱重塔8中,且经第二输送装置11向所述脱重塔8中通入甲基磺酰氟,所述脱重塔8塔顶产出精品三氟甲磺酰氟,所述脱重塔8塔底产出的重组分杂质中的一部分以200kg/h流量进入脱重塔再沸器9,加热蒸发回到脱重塔8中经蒸发精馏后收集,剩余部分以59.4kg/h的流量通过压差从底部产物排放口10排入电解槽继续使用;所述脱重塔8的塔顶温度为-30,塔釜温度为5℃、塔釜压力为0.55mpa,回流比为20;所述重组分杂质包括氟化氢、甲基磺酰氟和三氟甲磺酰氟;控制通入所述脱重塔8中的甲基磺酰氟与剩余部分的底部产物的质量流量为0.07:1;
59.在脱重塔取样口4进行取样检测分析,检测精品三氟甲磺酰氟的纯度,如精品三氟甲磺酰氟的纯度<99.9(vol)%,则通过轻组分排放口7将气体排入电解气系统,重新经过精馏系统提纯;当三氟甲磺酰氟的纯度≥99.9(vol)%时,将制得的精品三氟甲磺酰氟收集
到精品罐14内,其他杂质含量见表2。
60.本实施例中采用的装置与实施例1中的装置不同的是,脱轻塔5高为10m,直径为0.3m,理论塔板数为25,脱轻塔5内置直径为30m的不锈钢θ环填料;脱重塔8高为10m,直径为0.3m,理论塔板数为50,脱重塔8内置直径为30mm的不锈钢θ环填料;脱轻塔5、脱重塔8塔体、精品罐、氟化氢冷却器以及再沸器和管路均采用蒙乃尔材质。
61.表2实施例2-4中得到的精品三氟甲磺酰氟中各物质组分的含量表
[0062][0063]
实施例5
[0064]
本实施例采用实施例1中的装置连续精馏纯化三氟甲磺酰氟的方法,包括以下步骤:
[0065]
s1、首先将实施例1中的装置整体抽真空至-0.1mpa,然后将甲基磺酰氟的电解产物经第一流体输送装置1以30kg/h的流量通入脱轻塔5中,将氟化氢经第三流体输送装置12输送至氟化氢冷却器13内,在温度为-65℃,流量为3.6kg/h的条件下通入脱轻塔5中上部,然后在所述脱轻塔5内进行精馏,所述脱轻塔5塔顶产出轻组分杂质,在脱轻塔取样口2进行取样检测分析,检测轻组分杂质中,三氟甲磺酰氟(cf3so2f)的含量为0,所述脱轻塔5塔底产出底部产物;所述脱轻塔5塔顶温度为-55℃,塔釜的温度为-5℃、压力为0.6mpa,回流比为50;
[0066]
所述轻组分杂质包括氢气(h2)、四氟化碳(cf4)、二氟亚砜(sof2)、二氧化碳(co2)及二氟化氧(of2);所述底部产物包括氟化氢和三氟甲磺酰氟;所述经冷却的氟化氢和甲基磺酰氟的电解产物的质量比为0.12:1;所述甲基磺酰氟的电解产物的温度为5℃;所述甲基磺酰氟的电解产物的组成包括三氟甲磺酰氟的含量≥15vol%,氟化氢的含量≤2vol%,氢气的含量≤80vol%,四氟化碳的含量≤1vol%,二氟亚砜的含量≤1vol%,二氧化碳的含量≤0.4vol%,二氟化氧的含量≤0.5vol%;
[0067]
s2、将s1中得到的底部产物的一部分以5kg/h的流量通入脱轻塔再沸器6中,加热蒸发回到脱轻塔5以提供精馏过程中的热量,剩余部分以28.6kg/h的流量通过压差脱重塔8中,且经第二输送装置11向所述脱重塔8中通入甲基磺酰氟,所述脱重塔8塔顶产出精品三氟甲磺酰氟,所述脱重塔8塔底产出的重组分杂质的一部分以30kg/h流量进入脱重塔再沸器9,加热蒸发回到脱重塔8中经蒸发精馏后收集,剩余部分以5.6kg/h的流量通过压差从底部产物排放口10排入电解槽继续使用;所述脱重塔8的塔顶温度为-45℃,塔釜温度为0℃、塔釜压力为0.3mpa,回流比为10;所述重组分杂质包括氟化氢、甲基磺酰氟和三氟甲磺酰氟;控制通入所述脱重塔8中的甲基磺酰氟与剩余部分的底部产物的质量流量为0.05:1;
[0068]
在脱重塔取样口4进行取样检测分析,检测精品三氟甲磺酰氟的纯度,如精品三氟
甲磺酰氟的纯度<99.9(vol)%,则通过轻组分排放口7将气体排入电解气系统,重新经过精馏系统提纯;当三氟甲磺酰氟的纯度≥99.9(vol)%时,将制得的精品三氟甲磺酰氟收集到精品罐14内,其他杂质含量见表2。
[0069]
本实施例中采用的装置与实施例1中的装置不同的是,脱轻塔5高为3m,直径为0.05m,理论塔板数为10,脱轻塔5内置直径为5mm的拉西环;脱重塔8高为5m,直径为0.05m,理论塔板数为20,脱重塔8内置直径为5mm的不锈钢θ环填料;脱轻塔5、脱重塔8塔体、精品罐、氟化氢冷却器以及再沸器和管路均采用蒙乃尔材质。
[0070]
实施例6
[0071]
本实施例采用实施例1中的装置连续精馏纯化三氟甲磺酰氟的方法,包括以下步骤:
[0072]
s1、首先将实施例1中的装置整体抽真空至-0.1mpa,然后将甲基磺酰氟的电解产物经第一流体输送装置1以300kg/h的流量通入脱轻塔5中,将氟化氢经第三流体输送装置12输送至氟化氢冷却器13内,在温度为-30℃,流量为90kg/h的条件下通入脱轻塔5中上部,然后在所述脱轻塔5内进行精馏,所述脱轻塔5塔顶产出轻组分杂质,在脱轻塔取样口2进行取样检测分析,检测轻组分杂质中,三氟甲磺酰氟(cf3so2f)的含量为0,所述脱轻塔5塔底产出底部产物;所述脱轻塔5塔顶温度为-15℃,塔釜的温度为10℃、压力为1.25mpa,回流比为500;
[0073]
所述轻组分杂质包括氢气(h2)、四氟化碳(cf4)、二氟亚砜(sof2)、二氧化碳(co2)及二氟化氧(of2);所述底部产物包括氟化氢和三氟甲磺酰氟;所述经冷却的氟化氢和甲基磺酰氟的电解产物的质量比为0.30:1;所述甲基磺酰氟的电解产物的温度为-5℃;所述甲基磺酰氟的电解产物的组成包括三氟甲磺酰氟的含量≥15vol%,氟化氢的含量≤2vol%,氢气的含量≤80vol%,四氟化碳的含量≤1vol%,二氟亚砜的含量≤1vol%,二氧化碳的含量≤0.4vol%,二氟化氧的含量≤0.5vol%;
[0074]
s2、将s1中得到的底部产物的一部分以50kg/h的流量通入脱轻塔再沸器6中,加热蒸发回到脱轻塔5以提供精馏过程中的热量,剩余部分以340kg/h的流量通过压差脱重塔8中,且经第二输送装置11向所述脱重塔8中通入甲基磺酰氟,所述脱重塔8塔顶产出精品三氟甲磺酰氟,所述脱重塔8塔底产出的重组分杂质中的一部分以300kg/h流量进入脱重塔再沸器9,加热蒸发回到脱重塔8中经蒸发精馏后收集,剩余部分以125.2kg/h的流量通过压差从底部产物排放口10排入电解槽继续使用;所述脱重塔8的塔顶温度为0℃,塔釜温度为25℃、塔釜压力为0.95mpa,回流比为30;所述重组分杂质包括氟化氢、甲基磺酰氟和三氟甲磺酰氟;控制通入所述脱重塔8中的甲基磺酰氟与剩余部分的底部产物的质量流量为0.1:1;
[0075]
在脱重塔取样口4进行取样检测分析,检测精品三氟甲磺酰氟的纯度,如精品三氟甲磺酰氟的纯度<99.9(vol)%,则通过轻组分排放口7将气体排入电解气系统,重新经过精馏系统提纯;当三氟甲磺酰氟的纯度≥99.9(vol)%时,将制得的精品三氟甲磺酰氟收集到精品罐14内,其他杂质含量见表2。
[0076]
本实施例中采用的装置与实施例1中的装置不同的是,脱轻塔5高为15m,直径为1m,理论塔板数为50,脱轻塔5内置直径为100m的鲍尔环填料;脱重塔8高为15m,直径为1m,理论塔板数为80,脱重塔8内置直径为100mm的鲍尔环填料;脱轻塔5、脱重塔8塔体、精品罐、氟化氢冷却器以及再沸器和管路均采用蒙乃尔材质。
[0077]
实施例7
[0078]
本实施例采用实施例1中的装置连续精馏纯化三氟甲磺酰氟的方法,包括以下步骤:
[0079]
s1、首先将实施例1中的装置整体抽真空至-0.1mpa,然后将甲基磺酰氟的电解产物经第一流体输送装置1以200kg/h的流量通入脱轻塔5中,将氟化氢经第三流体输送装置12输送至氟化氢冷却器13内,在温度为-40℃,流量为40kg/h的条件下通入脱轻塔5中上部,然后在所述脱轻塔5内进行精馏,所述脱轻塔5塔顶产出轻组分杂质,在脱轻塔取样口2进行取样检测分析,检测轻组分杂质中,三氟甲磺酰氟(cf3so2f)的含量为0,所述脱轻塔5塔底产出底部产物;所述脱轻塔5塔顶温度为-25℃,塔釜的温度为5℃、压力为0.75mpa,回流比为300;
[0080]
所述轻组分杂质包括氢气(h2)、四氟化碳(cf4)、二氟亚砜(sof2)、二氧化碳(co2)及二氟化氧(of2);所述底部产物包括氟化氢和三氟甲磺酰氟;所述经冷却的氟化氢和甲基磺酰氟的电解产物的质量比为0.2:1;所述甲基磺酰氟的电解产物的温度为15℃;所述甲基磺酰氟的电解产物的组成包括三氟甲磺酰氟的含量≥15vol%,氟化氢的含量≤2vol%,氢气的含量≤80vol%,四氟化碳的含量≤1vol%,二氟亚砜的含量≤1vol%,二氧化碳的含量≤0.4vol%,二氟化氧的含量≤0.5vol%;
[0081]
s2、将s1中得到的底部产物的一部分以80kg/h的流量通入脱轻塔再沸器6中,加热蒸发回到脱轻塔5以提供精馏过程中的热量,剩余部分以163.4kg/h的流量通过压差脱重塔8中,且经第二输送装置11向所述脱重塔8中通入甲基磺酰氟,所述脱重塔8塔顶产出精品三氟甲磺酰氟,所述脱重塔8塔底产出的重组分杂质中的一部分以200kg/h流量进入脱重塔再沸器9,加热蒸发回到脱重塔8中经蒸发精馏后收集,剩余部分以59.4kg/h的流量通过压差从底部产物排放口10排入电解槽继续使用;所述脱重塔8的塔顶温度为-25℃,塔釜温度为10℃、塔釜压力为0.45mpa,回流比为20;所述重组分杂质包括氟化氢、甲基磺酰氟和三氟甲磺酰氟;控制通入所述脱重塔8中的甲基磺酰氟与剩余部分的底部产物的质量流量为0.07:1;
[0082]
在脱重塔取样口4进行取样检测分析,检测精品三氟甲磺酰氟的纯度,如精品三氟甲磺酰氟的纯度<99.9(vol)%,则通过轻组分排放口7将气体排入电解气系统,重新经过精馏系统提纯;当三氟甲磺酰氟的纯度≥99.9(vol)%时,将制得的精品三氟甲磺酰氟收集到精品罐14内,其他杂质含量见表2。
[0083]
本实施例中采用的装置与实施例1中的装置不同的是,脱轻塔5高为10m,直径为0.3m,理论塔板数为25,脱轻塔5内置直径为30m的不锈钢θ环填料;脱重塔8高为10m,直径为0.3m,理论塔板数为50,脱重塔8内置直径为30mm的不锈钢θ环填料;脱轻塔5、脱重塔8塔体、精品罐、氟化氢冷却器以及再沸器和管路均采用蒙乃尔材质。
[0084]
以上所述,仅是本发明的较佳实施例,并非对本发明作任何限制。凡是根据发明技术实质对以上实施例所作的任何简单修改、变更以及等效变化,均仍属于本发明技术方案的保护范围内。
再多了解一些
本文用于企业家、创业者技术爱好者查询,结果仅供参考。