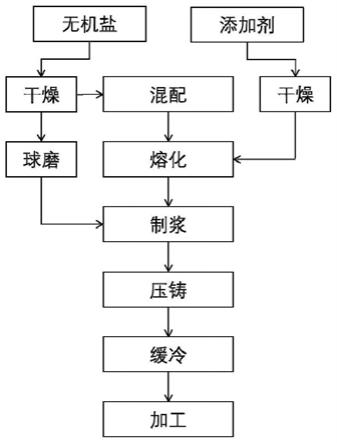
1.本发明属于铸造技术领域,具体涉及一种利用高压铸造工艺制备水溶型芯的工艺及水溶盐芯的使用方法。
背景技术:
2.复杂内腔及弯曲孔道铸件在现代工业中具有非常广泛的应用。由于树脂砂芯在制备复杂内腔铸件时,有机树脂在高温金属液的作用下会发生裂解产生大量气体,从而导致铸件内壁产生气孔以及有毒有害气体污染环境等问题,且在节能降耗的背景下,铸件低温浇铸又使得型芯溃散性能不佳,复杂内腔及弯曲孔道铸件脱芯十分困难。因此,具有优异水溶溃散性能以及环境友好特性的水溶型芯在此类铸件的成型中具有广泛的应用前景。
3.水溶型芯种类繁多,然而大多数型芯强度较低,一般仅适用于重力铸造,而用于压力铸造特别是高压铸造的水溶型芯的报道相对较少。从近年公布的专利文献来看,用于压力铸造的水溶盐芯成型工艺主要有压制烧结、熔融浇铸和压力铸造等几种典型的工艺形式。如:专利cn200710113017.8公布了一种以氯化钠粉、金红石型氧化钛粉、氧化铝粉等为原料用于制备油冷活塞用盐芯的工艺;专利cn201710117447.0也公布了一种用于铝合金活塞铸造用的耐高压盐芯。上述这类制备水溶盐芯的方法均为压制烧结工艺,而该工艺存在需要专用高压设备且仅适用于成型简单的结构型芯,且其成型工艺流程长。
4.专利cn202010703060.5、cn202010703905.0公布了一种以nacl和na2so4等为原料制备水溶盐芯的工艺和方法,所得水溶盐芯的抗弯强度可达20mpa以上。樊自田等在《铝镁合金铸件用复合硫酸盐水溶性砂芯性能的研究》中亦介绍了以硫酸镁等为原料制备压铸用型芯的工艺方法。这些型芯的成型均采用熔融浇铸工艺,该工艺将熔融无机盐浇铸于型芯模具中,待其冷却后即可得到所需型芯。然而,由于盐芯存在吸潮问题,压制的型芯必须快速投入使用或置于干燥箱内保存,这导致该工艺存在使用效率较低,不能满足现代工业流程化生产要求的缺点。专利cn201810877770.2和cn202011125362.5分别公布了一种以nacl为主要原料,通过熔融压铸成型制备型芯的方法,然而,由于压铸适合于成型薄壁铸件,且熔盐的凝固收缩较大,因此在制备较大尺寸盐芯时存在盐芯缩孔较大、致密度不够等问题,严重影响型芯的强度和服役性能。
技术实现要素:
5.1.要解决的问题
6.本发明的目的在于解决现有水溶盐芯制备工艺存在的以上问题,提供了一种半固态压铸制备水溶盐芯的方法,该方法既可以实现水溶盐芯的高效成型,又能获得适用于压力铸造用高强韧易水溶溃散的水溶盐芯。
7.2.技术方案
8.为了解决上述问题,本发明所采用的技术方案如下:
9.本发明的一种半固态压铸制备水溶盐芯的方法,向熔融无机盐中添加对应微米级
无机盐粉末,制备得到半固态熔盐浆料;然后采用压铸工艺使半固态浆料充填盐芯压铸模具,即成型得到水溶盐芯。
10.熔盐凝固过程中的液态收缩很大,其凝固时有较大的缩孔产生倾向,从而影响所得水溶盐芯的性能。而本发明采用半固态压铸技术,由于所浇铸的熔盐进入固液两相温度区间,且在一定压力下凝固,大大减小了液态收缩占整个凝固过程中的收缩比例,降低了缩松缩孔产生的可能性,提升了压铸盐芯的致密度,从而大大提升了制备所得水溶盐芯的性能。
11.更进一步的,在与微米级无机盐粉末混合之前,熔融无机盐中额外添加5%~15%的添加剂,该添加剂包含石英砂、莫来石砂、镁砂等耐火骨料和高岭土、硅藻土、氧化硅粉、氧化铝粉等耐火粉体,通过添加剂的复合添加,一方面有利于进一步减少凝固收缩,避免缩孔缩松现象,另一方面还可以作为形核的核心,有利于细化晶粒。
12.更进一步的,所述耐火骨料和耐火粉体的混合比例为0.2~5,耐火骨料的粒度为100~200目,耐火粉体的粒度为400~800目。
13.更进一步的,所述无机盐由碱金属氯化盐和碱金属碳酸盐组成,微米级无机盐粉末的粒度为10~50微米,其添加量为熔融无机盐质量的5%~10%。
14.更进一步的,具体包括以下步骤:
15.(1)熔炼:将混备好的无机盐置于熔化炉中,控制炉内温度达到复合盐液相线温度以上30℃~100℃,然后加入添加剂,保温10min~50min并搅拌均匀,随后去除溶液表面浮渣;
16.(2)制浆:向熔盐中加入微米级无机盐粉末,并将浆料通过水冷模具转移至制备半固态浆料的控温制浆容器中,采用超声搅拌器对其进行搅拌,控制熔盐浆料温度至液固两相温度区间,以制备半固态熔盐浆料;
17.本发明采用添加微米级无机盐粉末并辅以超声搅拌方式来制备半固态浆料,其目的在于外加温度较低的无机盐粉末,有利于熔盐快速进入液固两相温度区间,同时所加入的无机盐粉末也能成为熔盐结晶形核的核心,在超声搅拌作用下,有利于形成等轴细小晶粒,获得性能优异的半固态浆料。
18.(3)压铸:将半固态熔盐浆料浇入压铸机浇口杯中,利用压铸机冲头使半固态浆料充填盐芯压铸模具,成型水溶盐芯,待型芯温度冷却至复合盐芯发生固态相变温度以上50℃~100℃之间,打开压铸模具,顶出压铸盐芯;在压铸过程中要求其模具需待型芯温度冷却至复合盐芯固态相变温度以上再开模的目的在于避免压铸模具退让性差,使得复合盐芯在固态收缩及相变过程中产生裂纹而影响其性能。
19.(4)冷却和加工:对压铸盐芯进行冷却处理,然后去除其浇铸系统及冒口,即得到所需水溶盐芯。
20.更进一步的,步骤(4)中将从压铸机上顶出的压铸盐芯快速转移至固态相变温度以上20℃~80℃的炉内进行缓冷,冷却速度为1℃1min~10℃1min。通过缓冷处理可以降低盐芯固态相变速率,防止盐芯因快速相变而产生微裂纹,降低盐芯的强度。
21.更进一步的,待压铸盐芯缓冷至固态相变温度以下50℃~100℃后从炉中取出。
22.更进一步的,所述无机盐和添加剂在使用之前先置于120℃~200℃下进行烘干处理。
23.本发明制备所得水溶盐芯的使用方法,将水溶盐芯置于200℃~300℃的控温箱中备用或型芯温度在200℃~300℃时直接安装在压铸铸件模具上使用,从而可以有效避免盐芯在使用过程中直接受到熔融金属激热作用而产生裂纹或脆断,且其直接使用既大大降低了保温存放时的能量消耗,又能提升盐芯的成型使用效率。
附图说明
24.图1为本发明的半固态压铸制备水溶盐芯的方法的工艺流程图。
具体实施方式
25.下面结合具体实施例对本发明进一步进行描述。
26.实施例1
27.结合图1,本实施例的一种半固态压铸制备水溶盐芯的方法,包括以下步骤:
28.(1)原料预处理:将氯化钠、碳酸钠、200目石英砂,400目高岭土放入烘箱内烘干,烘箱温度控制在120℃。将用于制备盐芯的氯化钠、碳酸钠按照质量比1:2的质量比进行混合,待熔化备用。将干燥的部分氯化钠和碳酸钠按1:2的质量比混合进行球磨,获得10~50微米无机盐粉末,待制备半固态浆料备用。将干燥的200目石英砂、400目高岭土按1:1的质量比混配,待熔化时配备。
29.(2)熔炼:将混备好的无机盐置于熔化炉中,控制炉内温度达到800℃-850℃,加入预处理过程中混配好的石英砂和高岭土(添加总量为熔融无机盐质量的10%),保温10min并搅拌均匀,然后去除溶液表面浮渣。
30.(3)制浆:向熔盐中加入原料预处理阶段制备好的球磨微米级无机盐粉末(添加量为熔融无机盐质量的8%),并将浆料通过水冷模具转移至制备半固态浆料的控温制浆容器中,采用超声搅拌器对其进行搅拌,控制熔盐浆料温度660620℃,以制备半固态熔盐浆料。
31.(4)压铸:将半固态熔盐浆料浇入压铸机浇口杯中,利用压铸机冲头使半固态浆料充填盐芯压铸模具,成型水溶盐芯,待型芯温度冷至530610℃之间,打开压铸模具,顶出压铸盐芯。
32.(5)缓冷:将从压铸机上顶出的压铸盐芯快速转移至初始温度为500℃610℃的炉内进行缓冷,以1℃1min的冷速待其冷却至350℃以下后,将盐芯从炉内取出。
33.(6)加工:从炉内取出的盐芯,去除其浇铸系统及冒口,得到所需水溶盐芯。
34.(7)使用:将水溶盐芯置于250℃610℃的控温箱中备用或型芯温度在250℃610℃时直接安装在压铸铸件模具上使用。
35.实施例2
36.本实施例的一种半固态压铸制备水溶盐芯的方法,包括以下步骤:
37.(1)原料预处理:将氯化钾、碳酸钾、100目莫来石砂,600目硅藻土放入烘箱内烘干,烘箱温度控制在200℃。将用于制备盐芯的氯化钾、碳酸钾按照质量比2:1的质量比进行混合,待熔化备用。将干燥的部分氯化钾和碳酸钾按2:1的质量比混合进行球磨,获得10~50微米无机盐粉末,待制备半固态浆料备用。将干燥的莫来石砂、硅藻土按0.2:1的质量比混配,待熔化时配备。
38.(2)熔炼:将混备好的无机盐置于熔化炉中,控制炉内温度达到900℃-950℃,加入
预处理过程中混配好的莫来石砂和硅藻土,保温50min并搅拌均匀,然后去除溶液表面浮渣,添加剂的添加量为熔融无机盐质量的15%。
39.(3)制浆:向熔盐中加入原料预处理阶段制备好的球磨微米级无机盐粉末(添加量为熔融无机盐质量的10%),并将浆料通过水冷模具转移至制备半固态浆料的控温制浆容器中,采用超声搅拌器对其进行搅拌,控制熔盐浆料温度680620℃,以制备半固态熔盐浆料。
40.(4)压铸:将半固态熔盐浆料浇入压铸机浇口杯中,利用压铸机冲头使半固态浆料充填盐芯压铸模具,成型水溶盐芯,待型芯温度冷至500℃610℃时,打开压铸模具,顶出压铸盐芯。
41.(5)缓冷:将从压铸机上顶出的压铸盐芯快速转移至初始温度为430℃610℃的炉内进行缓冷,以10℃1min的冷速待其冷却至350℃以下后,将盐芯从炉内取出。
42.(6)加工:从炉内取出的盐芯,去除其浇铸系统及冒口,得到所需水溶盐芯。
43.(7)使用:将水溶盐芯置于290℃610℃的控温箱中备用或型芯温度在290℃610℃时直接安装在压铸铸件模具上使用。
44.实施例3
45.本实施例的一种半固态压铸制备水溶盐芯的方法,包括以下步骤:
46.(1)原料预处理:将氯化钾、碳酸钾、200目镁砂,800目氧化铝粉等放入烘箱内烘干,烘箱温度控制在170℃。将用于制备盐芯的氯化钾、碳酸钾按照质量比1:1的质量比进行混合,待熔化备用。将干燥的部分氯化钾和碳酸钾按1:1的质量比混合进行球磨,获得10~50微米无机盐粉末,待制备半固态浆料备用。将干燥的镁砂、氧化铝粉按5:1的质量比混配,待熔化时配备。
47.(2)熔炼:将混备好的无机盐置于熔化炉中,控制炉内温度达到920℃-970℃,加入预处理过程中混配好的石英砂和高岭土(添加剂的添加量占熔融无机盐质量的13%),保温25min并搅拌均匀,然后去除溶液表面浮渣。
48.(3)制浆:向熔盐中加入原料预处理阶段制备好的球磨微米级无机盐粉末(添加量为熔融无机盐质量的5%),并将浆料通过水冷模具转移至制备半固态浆料的控温制浆容器中,采用超声搅拌器对其进行搅拌,控制熔盐浆料温度690620℃,以制备半固态熔盐浆料。
49.(4)压铸:将半固态熔盐浆料浇入压铸机浇口杯中,利用压铸机冲头使半固态浆料充填盐芯压铸模具,成型水溶盐芯,待型芯温度冷至510℃610℃时,打开压铸模具,顶出压铸盐芯。
50.(5)缓冷:将从压铸机上顶出的压铸盐芯快速转移至初始温度为420℃610℃的炉内进行缓冷,以6℃1min的冷速待其冷却至350℃以下后,将盐芯从炉内取出。
51.(6)加工:从炉内取出的盐芯,去除其浇铸系统及冒口,得到所需水溶盐芯。
52.(7)使用:将水溶盐芯置于210℃610℃的控温箱中备用或型芯温度在210℃610℃时直接安装在压铸铸件模具上使用。
再多了解一些
本文用于企业家、创业者技术爱好者查询,结果仅供参考。