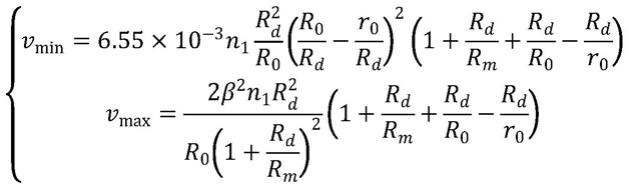
1.本发明属于轧制技术领域,具体涉及一种大型外轮廓激变环件径-轴向多辊协同近净轧制成形方法。
背景技术:
2.大型外轮廓激变环件是一种典型的异形环件,广泛应用于航空航天、核能、轮船、石油化工和汽车等工业领域。通常该类环件的外表面带有多个台阶结构,内表面为直壁结构,且台阶结构的径向深度较大。环件轧制是一种先进的制造技术,其主要通过对环坯进行连续塑性变形来制造高质量无缝环件,但传统轧制方式难以调控成形过程金属沿径向流动成形轮廓截面以及沿周向流动扩大直径的能力,且往往以周向流动扩大直径为主,因此,容易导致环件直径达到目标尺寸而截面轮廓不能完全成形。
3.目前,大型外轮廓激变环件主要采用简化锻件轧制成形,即先通过环件轧制成形深度较浅的外轮廓结构,然后进行大量削深加工,不仅生产效率低、材料浪费大,而且破坏金属流线分布,削弱了产品力学性能。因此,亟需开发一种大型外轮廓激变环件近净成形方法,实现该类环件低消耗、高效率成形,改善金属流线分布完整性,并提高产品综合力学性能。
技术实现要素:
4.本发明的目的在于提供一种大型外轮廓激变环件径-轴向多辊协同近净轧制成形方法,本发明能够调控环件轧制过程金属沿径向和周向的流动能力,从而协调环件截面轮廓成形和直径扩大速度,实现大型外轮廓激变环件近净轧制成形,能够大大节约原材料,降低生产成本,同时提高环件力学性能。
5.本发明所采用的技术方案是:
6.一种大型外轮廓激变环件径-轴向多辊协同近净轧制成形方法,包括步骤:
7.步骤一、外轮廓成形阶段:对镦粗冲孔后的矩形截面环坯进行多辊协同约束轧制,获得的预成形环坯用于后续扩孔轧制,参与协同约束轧制的孔型包括驱动辊与芯辊构成的径向孔型、上下锥辊构成的轴向孔型以及位于径向孔型出口侧的导辊,过程中,驱动辊做慢速旋转运动带动矩形截面环坯转动,芯辊做低速进给运动保证环坯稳定轧制,导辊位置固定限制矩形截面环坯外径增长,相对于驱动辊旋转,锥辊做低速旋转运动,使环坯向锥辊出口侧的导辊方向偏移,当环坯截面轮廓填充完成后,得到与锻件形状相似的预成形环坯;
8.步骤二、扩孔阶段:改变轧辊运动方式,对截面轮廓填充完整的预成形环坯进行多辊协同扩孔轧制,过程中,驱动辊做旋转运动带动预成形环坯转动,导辊随预成形环坯外径增大做随动运动,提高锥辊转速,使锥辊转速与驱动辊线速度匹配,位于预成形环坯中的芯辊做快速进给运动,对预成形环坯进行扩孔轧制,当预成形环坯外径达到目标尺寸后得到锻件。
9.在步骤一中,在多辊运动协同调控下,矩形截面环坯受到径向孔型、轴向孔型和导
辊三点约束作用,能有效限制环坯外径扩大,促使金属沿轴向流动成形突变轮廓,外轮廓成形阶段环坯直径较小、壁厚较厚,环件刚度好,能避免约束轧制导致环件发生塑性失稳现象,环坯外径基本不变,外轮廓逐渐成形,当环件外表面全部与驱动辊工作面贴合后,得到与锻件形状相似的预成形环坯;在步骤二中,当预成形环坯外径尺寸接近目标尺寸时,芯辊慢速进给,对预成形环坯进给整形轧制,整个扩孔轧制过程中,预成形环坯壁厚减薄,内、外径扩大,高度基本不变,当预成形环坯外径达到目标尺寸后得到锻件。
10.优选地,外轮廓成形阶段得到的预成形环坯尺寸为:
[0011][0012]
其中,r、l、r分别为预成形环坯的凹槽半径、凸台长度和内半径,b、b1、b2分别为预成形环坯的总高度、凸台高度和凹槽高度;k为轧制比;rf、lf、rf分别为锻件的凹槽半径、凸台长度和内半径,bf、b
f1
、b
f2
分别为锻件的总高度、凸台高度和凹槽高度,vf为锻件体积,
[0013]vf
=2π(rf l
f-rf)2b
f1
π(r
f-rf)2b
f2
[0014]
其中,rf为锻件内半径;
[0015]
矩形截面环坯尺寸为:
[0016][0017]
其中,r0、b0和r0为矩形截面环坯的外半径、高度和内半径,v为预成形环坯体积,v=vf。
[0018]
优选地,在大型外轮廓激变环件径-轴向多辊协同近净轧制成形过程中,导辊初始位置在径向孔型出口侧,且与驱动辊之间的夹角为90
°
。
[0019]
优选地,锥辊各阶段转速为:
[0020]
在外轮廓成形阶段中,锥辊低速旋转,其转速为:n2=knn,kn为锥辊转速调节系数,一般取0.1~0.5,
[0021][0022]
其中,n1为驱动辊转速,rd为驱动辊半径,r1为环坯上端外半径,l为锥辊顶点到速度匹配点的距离,α为锥辊锥角的一半;
[0023]
在扩孔阶段,锥辊转速为匹配转速,转速为n3=n。
[0024]
优选地,锥辊在轧制过程中的运动控制为:
[0025]
在外轮廓成形阶段,为保证矩形截面环坯轧制稳定性,锥辊位置固定;
[0026]
在扩孔阶段,锥辊随预成形环坯外径增大而做径向跟随运动,以保证环坯上下表
面始终与锥辊接触。
[0027]
优选地,芯辊进给量根据环坯在外轮廓成形和扩孔阶段中凹槽位置处的壁厚减薄量确定,为:
[0028]
外轮廓成形阶段进给量:
△
h1=b
0-b;
[0029]
扩孔阶段芯辊进给量:
△
h2=b-bf,
[0030]
其中,b0=r
0-r0矩形截面环坯凹槽处壁厚,b=r-r为预成形环坯凹槽处壁厚,bf=r
f-rf为锻件凹槽处壁厚。
[0031]
优选地,芯辊进给速度v取值范围确定为:
[0032][0033]vmin
≤v≤v
max
[0034]
其中,rm为芯辊半径,β为摩擦角,v
min
为芯辊最小进给速度,v
max
为芯辊最大进给速度。
[0035]
优选地,芯辊各阶段进给速度控制为:
[0036]
在外轮廓成形阶段,芯辊的进给速度按两个阶段规划,即咬入阶段和轮廓成形阶段;
[0037]
咬入阶段进给量:δh1′
=(0.1~0.15)δh1[0038]
咬入阶段进给速度:
[0039]
轮廓成形阶段进给量:δh1″
=δh
1-δh1′
[0040]
轮廓成形阶段进给速度:
[0041]
在扩孔阶段,芯辊的进给速度按两个阶段规划,即直径扩大阶段和整形阶段;
[0042]
直径扩大阶段进给量:δh2′
=(0.8~0.95)δh2[0043]
直径扩大阶段进给速度:
[0044]
整形阶段进给量:δh2″
=δh
2-δh2′
[0045]
整形阶段进给速度:
[0046]
优选地,驱动辊与导辊两端设有凸缘,以限制环坯在大型外轮廓激变环件径-轴向多辊协同近净轧制成形过程中的轴向窜动,驱动辊与导辊工作表面几何尺寸与目标锻件表面几何尺寸一致。
[0047]
本发明的有益效果是:
[0048]
本发明能够调控环件轧制过程金属沿径向和周向的流动能力,从而协调环件截面轮廓成形和直径扩大速度,实现大型外轮廓激变环件近净轧制成形,能够大大节约原材料,降低生产成本,同时提高环件力学性能:1)在外轮廓成形阶段,通过多辊运动协同,形成三点约束轧制,可以限制环坯外径增长,促进金属沿轴向流动填充截面轮廓,能够提高激变轮
廓径向尺寸成形能力;2)在成形外表面轮廓后,仅需改变导辊和锥辊的运动方式,可以直接进行扩孔轧制,极大的提高生产效率,并能满足不同径向尺寸异形环件的柔性成形,应用范围广;3)该方法可以在传统径-轴向轧制设备上进行,仅需对不同阶段的各轧辊运动进行协调匹配,能够调控环件轧制过程金属沿径向和周向的流动能力,从而协调环件截面轮廓成形和直径扩大速度,实现大型外轮廓激变环件近净轧制成形。
附图说明
[0049]
图1是本发明实施例中的目标锻件剖视结构示意图;
[0050]
图2是本发明实施例中的预成形环坯剖视结构示意图;
[0051]
图3是本发明实施例中的矩形截面环坯剖视结构示意图;
[0052]
图4a为本发明一种大型外轮廓激变环件径-轴向多辊协同近净轧制成形方法在外轮廓成形阶段开始时刻的俯视结构示意图;
[0053]
图4b为本发明一种大型外轮廓激变环件径-轴向多辊协同近净轧制成形方法在外轮廓成形阶段开始时刻的剖视结构示意图;
[0054]
图5a为本发明一种大型外轮廓激变环件径-轴向多辊协同近净轧制成形方法在外轮廓成形阶段结束时刻的俯视结构示意图;
[0055]
图5b为本发明一种大型外轮廓激变环件径-轴向多辊协同近净轧制成形方法在外轮廓成形阶段结束时刻的剖视结构示意图;
[0056]
图6a为本发明一种大型外轮廓激变环件径-轴向多辊协同近净轧制成形方法在扩孔阶段结束时刻的俯视结构示意图;
[0057]
图6b为本发明一种大型外轮廓激变环件径-轴向多辊协同近净轧制成形方法在扩孔阶段结束时刻的剖视结构示意图;
[0058]
图7为本发明实施例中的芯辊进给曲线图。
[0059]
图中,1-驱动辊,2-矩形截面环坯,3-芯辊,4-锥辊,5-导辊。
具体实施方式
[0060]
下面结合附图和实施例对本发明作进一步的说明。
[0061]
参照图1至图6b,本发明提出一种大型外轮廓激变环件径-轴向多辊协同近净轧制成形方法,包括以下步骤:
[0062]
步骤一、外轮廓成形阶段
[0063]
如图4和图5所示,将镦粗冲孔后的矩形截面环坯2放置在轧制孔型中,对矩形截面环坯2进行多辊协同约束轧制,其中参与协同约束轧制孔型包括:驱动辊1和芯辊3构成的径向孔型,上、下锥辊4构成的轴向孔型,以及位于径向孔型出口侧的导辊5。外轮廓成形过程中,驱动辊1做低速旋转运动带动矩形截面环坯2转动,保证矩形截面环坯2轧制稳定性,导辊5位置固定限制矩形截面环坯2外径增长,位于矩形截面环坯2中的芯辊3做慢速进给运动使矩形截面环坯2壁厚减薄,锥辊4做低速旋转运动,使矩形截面环坯2向锥辊出口侧的导辊5的方向偏移。各轧辊协同约束限制矩形截面环坯2凹槽外径增长,促进矩形截面环坯2上下端凸台成形,当矩形截面环坯2截面轮廓填充完成后,得到与锻件形状相似的预成形环坯,如图5b所示;
[0064]
步骤二、扩孔阶段
[0065]
如图6所示,调整导辊5与锥辊4运动方式,对外轮廓成形阶段获得的预成形环坯进行多辊协同扩孔轧制。扩孔轧制过程中,驱动辊1做旋转运动带动预成形环坯转动,导辊5随预成形环坯外径扩大做随动运动,提高锥辊4转速,使其转速与驱动辊1转速相匹配。扩孔轧制前期,位于预成形环坯中的芯辊3做快速进给运动,进行直径扩大轧制。当预成形环坯外径尺寸接近目标尺寸时,芯辊3慢速进给,对预成形环坯进行整形轧制。整个扩孔轧制过程中,预成形环坯壁厚减薄,内、外径扩大,高度基本不变,当预成形环坯外径达到目标尺寸后得到锻件。
[0066]
如图2所示,外轮廓成形阶段得到的预成形环坯尺寸如下:
[0067][0068]
其中,r、l、r分别为预成形环坯的凹槽半径、凸台长度、内半径,b、b1、b2分别为预成形环坯的总高度、凸台高度和凹槽高度;k为轧制比;rf、lf、rf分别为预成形环坯的凹槽半径、凸台长度、内半径,bf、b
f1
、b
f2
分别为预成形环坯的总高度、凸台高度和凹槽高度,vf为锻件体积,
[0069]vf
=2π(rf l
f-rf)2b
f1
π(r
f-rf)2b
f2
[0070]
其中,rf为锻件内半径,预成形环坯如图2所示。
[0071]
如图3所示,矩形截面环坯2尺寸为:
[0072][0073]
其中,r0、b0和r0为矩形截面环坯2的外半径、高度和内半径,v为预成形环坯体积,v=vf,矩形截面环坯2如图3所示。
[0074]
在步骤一中,导辊5初始位置在径向孔型出口侧,且与驱动辊1之间的夹角为90
°
,如图4a所示。
[0075]
在大型外轮廓激变环件径-轴向多辊协同近净轧制成形过程中,锥辊4各阶段转速按如下控制:
[0076]
在外轮廓成形阶段,锥辊4低速旋转,转速为:n2=knn,其中kn为转速调节系数,一般取0.1~0.5,
[0077][0078]
其中,n1为驱动辊1转速,rd为驱动辊1半径,r1为环坯上端外半径,l为锥辊4顶点到速度匹配点的距离,α为锥辊4锥角的一半。
[0079]
在扩孔阶段,锥辊4转速为匹配转速,即转速为n3=n。
[0080]
在大型外轮廓激变环件径-轴向多辊协同近净轧制成形过程中,锥辊4在轧制过程中运动按如下控制:
[0081]
在外轮廓成形阶段,为保证矩形截面环坯2轧制稳定性,锥辊4位置固定;
[0082]
在扩孔阶段,锥辊4随预成形环坯外径增大而做径向跟随运动,以保证预成形环坯上下表面始终与锥辊4接触。
[0083]
在大型外轮廓激变环件径-轴向多辊协同近净轧制成形过程中,芯辊3进给量根据环坯在外轮廓成形阶段和扩孔阶段中凹槽位置处的壁厚减薄量确定,具体如下:
[0084]
外轮廓成形阶段进给量:
△
h1=b-b0;
[0085]
扩孔阶段芯辊进给量:
△
h2=b
f-b,
[0086]
其中,b=r-r为预成形环坯凹槽处壁厚,b0=r
0-r0矩形截面环坯2凹槽处壁厚,bf=r
f-rf为锻件凹槽处壁厚。
[0087]
在大型外轮廓激变环件径-轴向多辊协同近净轧制成形过程中,芯辊3进给速度v取值范围按如下公式确定:
[0088][0089]vmin
≤v≤v
max
[0090]
其中,rm为芯辊3半径,β为摩擦角,v
min
为芯辊3最小进给速度,v
max
为芯辊3最大进给速度。
[0091]
参照图7,在大型外轮廓激变环件径-轴向多辊协同近净轧制成形过程中,芯辊3各阶段进给速度按如下控制:
[0092]
在步骤一外轮廓成形阶段,芯辊3的进给速度按两个阶段规划,即咬入阶段和轮廓成形阶段,
[0093]
咬入阶段进给量:δh1′
=(0.1~0.15)δh1[0094]
咬入阶段进给速度:
[0095]
轮廓成形阶段进给量:δh1″
=δh
1-δh1′
[0096]
轮廓成形阶段进给速度:
[0097]
在步骤二扩孔阶段,芯辊3的进给速度按两个阶段规划,即直径扩大阶段和整形阶段,
[0098]
直径扩大阶段进给量:δh2′
=(0.8~0.95)δh2[0099]
直径扩大阶段进给速度:
[0100]
整形阶段进给量:δh2″
=δh
2-δh2′
[0101]
整形阶段进给速度:
[0102]
如图4a所示,驱动辊1与导辊5两端设有凸缘,以限制环坯在大型外轮廓激变环件径-轴向多辊协同近净轧制成形中的轴向窜动,驱动辊1与导辊5工作表面几何尺寸与目标锻件表面几何尺寸一致。
[0103]
实施例
[0104]
以下以某深槽环件具体为例,来说明本大型外轮廓激变环件径-轴向多辊协同近净轧制成形方法。
[0105]
目标锻件尺寸为:rf=117mm,rf=109mm,lf=23mm,bf=52mm,b
f1
=16mm,b
f2
=20mm,,大型外轮廓激变环件径-轴向多辊协同近净轧制成形方法步骤如下:
[0106]
(1)外轮廓成形阶段
[0107]
将镦粗冲孔后的矩形截面环坯放置在轧制孔型中,进行多辊协同约束轧制,其中参与协同约束轧制孔型包括:驱动辊1和芯辊3构成的径向孔型,上、下锥辊4构成的轴向孔型,以及位于径向孔型出口侧的导辊5。外轮廓成形过程中,驱动辊1做低速旋转运动带动矩形截面环坯2转动,保证矩形截面环坯2轧制稳定性,导辊5位置固定限制矩形截面环坯2外径增长,位于矩形截面环坯2中的芯辊3做慢速进给运动使矩形截面环坯2壁厚减薄,锥辊4做低速旋转运动,使矩形截面环坯2向锥辊出口侧的导辊5的方向偏移。各轧辊协同约束限制矩形截面环坯2凹槽外径增长,促进矩形截面环坯2上下端凸台成形,当矩形截面环坯2截面轮廓填充完成后,得到与锻件形状相似的预成形环坯,如图5b所示;其中,预成形环坯尺寸:r=78mm,r=56.2mm,l=23mm,b=52mm,b1=16mm,b2=20mm,矩形截面环坯尺寸为:r0=78mm,r0=25mm,b0=52mm,轧制比k=1.5。
[0108]
(2)扩孔阶段
[0109]
如图6所示,调整导辊5与锥辊4运动方式,对多辊协同约束轧制获得的预成形环坯进行多辊协同扩孔轧制。扩孔轧制过程中,驱动辊1做旋转运动带动预成形环坯转动,导辊5随预成形环坯外径扩大做随动运动,提高锥辊4转速,使其转速与驱动辊1转速相匹配。扩孔轧制前期,位于预成形环坯中的芯辊3做快速进给运动,进行直径扩大轧制。当预成形环坯外径尺寸接近目标尺寸时,芯辊3慢速进给,对预成形环坯进行整形轧制。整个扩孔轧制过程中,预成形环坯壁厚减薄,内、外径扩大,高度基本不变,当预成形环坯外径达到目标尺寸后得到锻件。
[0110]
上述方案中,导辊5初始位置在径向孔型出口侧,且与驱动辊1之间的夹角为90
°
,如图4a所示。
[0111]
上述方案中,锥辊在外轮廓成形阶段低速旋转,转速为:
[0112]
锥辊4在扩孔阶段转速与环坯匹配,其转速为:
[0113][0114]
其中,n1=3r/s为驱动辊1转速,rd=180mm为驱动辊1半径,r1为环坯上端外半径,l为锥辊4顶点到速度匹配点的距离,α=17.5
°
为锥辊4锥角的一半。
[0115]
上述方案中,在外轮廓成形阶段,为保证环坯轧制稳定性,锥辊4位置固定;在扩孔阶段,锥辊4随预成形环坯外径增大而做径向跟随运动,以保证预成形环坯上下表面始终与锥辊4接触。
[0116]
上述方案中,芯辊3各阶段进给量如下:
[0117]
外轮廓成形阶段进给量:
△
h1=31.2mm;
[0118]
扩孔阶段芯辊进给量:
△
h2=13.8mm。
[0119]
上述方案中,芯辊3进给速度按如下控制:
[0120]
在步骤一外轮廓成形阶段,芯辊3的进给速度按两个阶段规划,即咬入阶段和轮廓成形阶段,
[0121]
咬入阶段进给量
△
h1'=3.2mm,芯辊3进给速度v1'=0.4mm/s。
[0122]
轮廓成形阶段进给量
△h1”=28mm,芯辊3进给速度v
1”=1.6mm/s。
[0123]
在步骤二扩孔阶段,芯辊3的进给速度按两个阶段规划,即直径扩大阶段和整形阶段,
[0124]
直径扩大阶段进给量
△
h2'=12mm,芯辊3进给速度v2'=2mm/s。
[0125]
整形阶段进给量
△h2”=1.8mm,芯辊3进给速度v
2”=0.4mm/s。
[0126]
上述方案中,驱动辊1与导辊5两端设有凸缘,以限制环坯在大型外轮廓激变环件径-轴向多辊协同近净轧制成形过程中轴向窜动,驱动辊1与导辊5工作表面几何尺寸与目标锻件表面几何尺寸一致。
[0127]
应当理解的是,对本领域普通技术人员来说,可以根据上述说明加以改进或变换,而所有这些改进和变换都应属于本发明所附权利要求的保护范围。
再多了解一些
本文用于企业家、创业者技术爱好者查询,结果仅供参考。