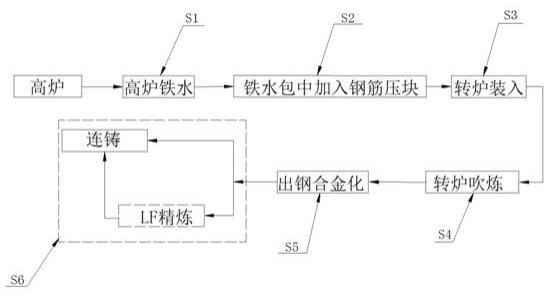
1.本发明属于钢铁冶金领域,转炉炼钢过程,尤其涉及一种不采用废钢预热不添加发热剂仅通过工艺改进来实现提高废钢比的冶炼方法。
背景技术:
2.废钢相对矿石而言是一种清洁资源,可无限循环使用,与采用矿石、焦煤生产钢铁相比,使用废钢炼钢,可大幅度节能减排,因此钢水冶炼中提高废钢比可大幅降低环境污染和降低综合能耗。我国环保政策日益收紧,严格限制烧结矿、高炉的产量,在缺少铁水情况下,提高废钢比可增加钢产量,降低成本,同时,随着我国钢铁蓄积量和废钢资源的增加,废钢价格优势凸显,提高废钢比,可降低钢水成本。
3.提高废钢比的瓶颈技术在于转炉系统热量的补偿。目前提高废钢比的技术中,有采用废钢预热的方式提高废钢的物理热以提高废钢比,如现有技术一种提高转炉废钢比的冶炼方法,其公开号为cn111254250a,此技术需采用氧气和焦炉煤气对转炉内的废钢进行预热3~5min,实施此项技术需要增设焦炉煤气输送管道、预热氧枪及其控制系统等设备,预热氧枪结构复杂使用难度大、风险系数高,同时预热3~5min降低了转炉工作效率,增加了生产组织难度,预热使用焦炉煤气增加能源消耗增加了生产成本;除此方法之外还有采用向转炉中加入焦炭或碳化硅等发热剂来提高铁水化学热实现提高废钢比的技术,这种技术存在能源消耗增大,碳排放增加,铁损高,炼钢成本升高等问题。
技术实现要素:
4.针对现有技术存在的问题,本发明提供了一种不采用废钢预热不添加发热剂仅通过工艺改进来实现提高废钢比的冶炼方法。
5.本发明是这样实现的,一种提高废钢比的冶炼方法,其特征在于,包括如下步骤:s1、高炉铁水:铁水作为转炉炼钢的主要原材料,为转炉冶炼提供物理热和化学热,出铁温度应大于或等于1500℃,铁水成分中c:大于或等于4.0%,si:0.40~0.60%,mn:0.30~0.60%,p:小于或等于0.130%,s:小于或等于0.035%;s2、铁水包中加入钢筋压块:在兑入铁水前向铁水包中加入钢筋压块;钢筋压块尺寸要求长小于或等于1800mm,宽、厚小于或等于800mm,钢筋的直径要求6~30mm;钢筋压块加入量控制在10~15t,加完钢筋压块静置10~12min再兑入铁水,铁水兑入量80~85t;铁水包兑入铁水后静置时间大于或等于10min,保证加入的钢筋压块全部熔化,并保证铁水温度在大于或等于1250℃;s3、转炉装入:将上一炉溅渣后温度大于或等于1300℃的高热渣保留1.0~2.0t,使用废钢斗向转炉内加入废钢22~30t,单块废钢不大于1t,废钢中的渣钢加入量不大于废钢量的5%,根据铁水及废钢情况配加生铁0~3t,以提高钢水化学热,向转炉内兑入铁水,进行吹炼;s4、转炉吹炼:将转炉吹炼用氧枪的氧压控制在0.78~0.86mpa;促进熔池活跃,保
证吹炼过程废钢完全熔化,枪位采用低位、高位、低位模式,前期氧枪位控制低位为1650mm~1900mm,快速提温;中期氧枪位控制高位为1900mm~2200mm,后期控制氧枪位控制低位为1400mm~1550mm;在吹炼过程中通过高位料仓加入直径小于或等于60mm,厚度4~10mm的冲压余料废钢,冲压余料废钢要求表面光滑没有挂刺;冲压余料废钢加入量0.8~2.4t,供氧吹炼600s后严禁再加入废钢;冶炼终点目标c大于或等于0.06%,温度大于或等于1580℃;s5、出钢合金化:出钢时间控制在150~350s,钢包离线时间小于或等于60min;出钢过程中随合金再次加入钢筋头和/或冲压余料废钢废钢,总和加入量0.3~1t,出钢过程严禁下渣,要求渣层厚度小于或等于30mm;炉后进行软吹氩,要求使液面轻微涌动,不裸露钢液,吹氩时间大于或等于5min;s6、吹氩完毕后钢包吊至lf炉进行精炼处理或吊至连铸机进行浇注。
6.优选的,步骤s1出铁温度大于或等于1550℃,出铁过程中向鱼雷罐加入钢筋头和/或冲压余料废钢4~7t。
7.优选的,步骤s6中钢包吊至lf炉进行精炼处理过程中,钢包内加入冲压余料废钢0.5~2t,再用给电加热方式提高钢水温度。
8.本发明的有益效果为:由于本发明采用上述技术方案,既没有增加废钢预热设施,避免了增加设备投资和能源消耗,也没有向转炉中添加焦炭、碳化硅等发热剂而增加碳排放和成本,仅通过工艺改进,充分利用铁水的物理热、化学热,利用铁水包余热、倒罐铁流动力,精准的吹炼控制,合理的废钢要求及加入位置等手段实现了提高废钢比的目的。本发明中提高废钢比的冶炼工艺可行,克服了现有技术中需废钢预热和加入发热剂等问题,操作安全方便。采用本工艺,废钢占比可达到30%以上,在不采用废钢预热不添加发热剂仅通过工艺改实现了高废钢比钢水冶炼,同时还实现了钢水冶炼过程的节能减排,提高了钢水产量,取得了较好社会效益和经济效益。
附图说明
9.图1是本发明提供方法实施的流程图。
具体实施方式
10.为了使本发明的目的、技术方案及优点更加清楚明白,以下结合实施例,对本发明进行进一步详细说明。应当理解,此处所描述的具体实施例仅仅用以解释本发明,并不用于限定本发明。
11.请参阅图1,一种提高废钢比的冶炼方法,包括如下步骤:s1、高炉铁水:铁水作为转炉炼钢的主要原材料,为转炉冶炼提供物理热和化学热,出铁温度应大于或等于1500℃,铁水成分:c:大于或等于4.0%,si:0.40~0.60%,mn:0.30~0.60%,p:小于或等于0.130%,s:小于或等于0.035%;铁水成分的控制尤其是si含量要求0.40~0.60%,目的是在保证高炉顺行的前提下提高铁水的化学热;s2、铁水包中加入钢筋压块:在兑入铁水前向铁水包中加入钢筋压块;钢筋压块尺寸长小于或等于1800mm,宽、厚小于或等于800mm,钢筋的直径要求6~30mm;加入钢筋压块是因为钢筋压块有一定的骨架支撑作用且不致密,与铁水接触面积大,便于熔化。如果采用小块废钢,容易造成废钢粘住包底不宜熔化;采用大块废钢,废钢熔化不完全;采用轻薄废钢,
废钢装入量少且温降大;钢筋压块尺寸要求是为实现钢筋压块便于装入铁包和快速熔化目的。钢筋压块加入量控制在10~15t,加完钢筋压块静置10~12min再兑入铁水,目的是将废钢上的水分蒸发,以防止带入钢中影响钢材质量,并将废钢进行初步预热;兑入铁水量80~85t,兑铁水过程应先小流倒入,熔池稳定后再正常流加入,兑铁过程应在保证安全的情况下加大铁水流速,保证铁水对废钢的冲击利于其熔化;铁水包兑入铁水后静置时间不小于10min,保证加入的钢筋压块全部熔化,并保证铁水温度在大于或等于1250℃;通过充分利用铁水的物理热和铁水动能,在不增加废钢预热设施的情况下增加废钢加入量;s3、转炉装入:将上一炉溅渣后温度大于或等于1300℃的高热渣保留1.0~2.0t,保留高热渣的目的一是减少造渣料的消耗从而降低造渣料带来的热量损失,二是高热渣可以预热加入到转炉的废钢,加快废钢熔化速度便于冶炼;使用废钢斗向转炉内加入废钢22~30t,废钢搭配合理,单块废钢不大于1t,废钢中的渣钢加入量不大于废钢量的5%,可根据加入转炉的铁水和废钢情况配加生铁0~3t,目的是可用于调节钢水的化学热;继续向转炉内兑入铁水,进行吹炼;s4、转炉吹炼:转炉吹炼用氧枪的氧压控制在0.78~0.86mpa,促进熔池活跃,保证吹炼过程废钢完全熔化,枪位采用低位、高位、低位模式,前期氧枪位控制低位为1650mm~1900mm快速提温,中期氧枪位控制高位1900mm~2200mm,后期氧枪位控制低位1400mm~1550mm;在吹炼过程中通过高位料仓加入直径小于或等于60mm,厚度4~10mm的冲压余料废钢,冲压余料废钢要求表面光滑没有挂刺,冲压余料废钢尺寸要求是为了便于运送高位料仓和在下料过程中防止卡料;冲压余料废钢加入量0.8~2.4t;供氧吹炼600s后严禁加入,此时已为吹炼后期,防止加入的废钢未完全熔化;冶炼终点目标c大于或等于0.06%,温度大于或等于1580℃;s5、出钢合金化:出钢时间控制在150~350s,出钢时间过长导致钢水温降过大,出钢时间过短容易造成出钢下渣。钢包离线时间小于或等于60min;出钢过程中随合金再次加入钢筋头和/或冲压余料废钢,总和加入量0.3~1t;出钢过程严禁下渣,要求渣层厚度小于或等于30mm;炉后进行软吹氩,要求使液面轻微涌动,不裸露钢液,吹氩时间大于或等于5min;s6、吹氩完毕后钢包吊至lf炉进行精炼处理或吊至连铸机进行浇注。
12.当步骤s1中出铁温度大于或等于1550℃时,出铁过程中向鱼雷罐中加入钢筋头和/或冲压余料废钢4~7t;高炉铁水经出铁沟流入鱼雷罐的过程中,随铁水流向鱼雷罐中加入钢筋头和/或冲压余料废钢;高炉铁水经由鱼雷罐运送至炼钢区域,在倒罐站将铁水倒入至铁水包内,一罐鱼雷罐铁水可倒2.5~3包铁水;在钢包吊至lf炉进行精炼处理过程中,可向钢包内加入冲压余料废钢0.5~2t,再用给电加热方式提高温度,增加钢产量。当市场钢材效益好,提高钢产量可显著增加效益时,可采用在精炼过程中加入冲压余料废钢,再通过给电加热的方式提高钢水温度,来提高钢产量增加效益。由于废钢中磷、硫等有害元素较高,因此在精炼时废钢加入量不宜过高。
13.由此实现了不采用废钢预热不添加发热剂,仅通过工艺改进来实现了提高废钢比的目的。为说明实施效果,特举以下实施例。
14.实施例1:一种提高废钢比的冶炼方法,包括如下步骤:s1、高炉铁水:出铁温度:1520℃,铁水成分:c:4.21%、si:0.41%、mn:0.42%、p:
0.127%、s:0.031%;s2、铁水包中加入钢筋压块:铁水包加入钢筋压块12.2t,加完钢筋压块静置时间11.5min;兑入铁水量83.6t,铁水温度1378℃;铁水包兑入铁水后静置时间12min,温度1274℃;s3、转炉装入:上炉留渣量1.1t,加入普通废钢,类型为重型废钢和中型废钢,加入量为27.4t,加入生铁2t;s4、转炉吹炼:转炉吹炼过程控制情况,参见表1;表1为实施例1转炉吹炼过程控制情况终点成分:c:0.07%,终点温度为1621℃;s5、出钢合金化:钢包离线时间44min正常包,出钢时间247s,出钢过程中加入钢筋头0.85t,软吹8min;s6、吹氩完毕后钢包吊至连铸进行浇注。
15.本实施例共加入废钢41.65t,铁水83.6t,生铁2.0t,废钢比32.73%,实现高废钢比冶炼。
16.实施例2:一种提高废钢比的冶炼方法,包括如下步骤:s1、高炉铁水:出铁温度:1530℃,铁水成分:c:4.78%、si:0.58%、mn:0.38%、p:0.121%、s:0.025%; s2、铁水包中加入钢筋压块:铁水包加入钢筋压块14.5t,加完钢筋压块静置时间11min;兑入铁水量80.5t,铁水温度1385℃;铁水包兑入铁水后静置时间11.5min,温度1258℃;s3、转炉装入:上炉留渣量1.8t,加入普通废钢,类型为重型废钢和中型废钢,加入量为29.7t,未加入生铁;s4、转炉吹炼:转炉吹炼过程控制情况,参见表2;表2为实施例2转炉吹炼过程控制情况终点成分:c:0.06%,终点温度为1600℃;s5、出钢合金化:钢包离线时间48min正常包,出钢时间305s,出钢过程中加入钢筋头和冲压余料废钢共计0.55t;软吹时间6.5min;s6、吹氩完毕后钢包吊至lf进行精炼处理。
17.本实施例共加入废钢46.75t,铁水80.5t,生铁0t,废钢比36.74%,实现高废钢比冶炼。
18.实施例3:一种提高废钢比的冶炼方法,包括如下步骤:s1、高炉铁水:出铁温度:1530℃,铁水成分:c:4.71%、si:0.51%、mn:0.44%、p:0.117%、s:0.026%。
[0019] s2、铁水包中加入钢筋压块:铁水包加入钢筋压块14.7t,加完钢筋压块静置时间10.5min;兑入铁水量82.0t,铁水温度1398℃;铁水包兑入铁水后静置时间12.5min,温度1260℃;s3、转炉装入:上炉留渣量1.5t,加入普通废钢,类型为重型废钢和中型废钢,加入量为27.8t,加入生铁2.2t;s4、转炉吹炼:转炉吹炼过程控制情况,参见表 3;表3为实施例3转炉吹炼过程控制情况终点成分:c:0.08%,终点温度为1614℃;s5、出钢合金化:钢包离线时间54min正常包,出钢时间195s,加入冲压余料废钢0.65t,软吹8.5分钟;s6、吹氩完毕后钢包吊至连铸进行浇注。
[0020]
本实施例共加入废钢44.45t,铁水82.0t,生铁2.2t,废钢比34.55%,实现高废钢比冶炼。
[0021]
实施例4:一种提高废钢比的冶炼方法,包括如下步骤:s1、高炉铁水:出铁温度:1560℃,铁水成分:c:4.85%、si:0.52%、mn:0.36%、p:0.123%、s:0.027%;鱼雷罐中加入钢筋头废钢6.2t,折合每炉加入废钢2.3t。
[0022] s2、铁水包中加入钢筋压块:铁水包加入钢筋压块13.7t,加完钢筋压块静置时间10.5min;兑入铁水量80.3t;铁水温度1365℃;铁水包兑入铁水后静置时间11.5min,温度1255℃;s3、转炉装入:上炉留渣量1.7t,加入普通废钢,类型为重型废钢和中型废钢,加入量为26.9t,未加入生铁;s4、转炉吹炼:转炉吹炼过程控制情况,参见表4;表4为实施例4转炉吹炼过程控制情况
终点成分:c:0.06%,终点温度为1588℃;s5、出钢合金化:钢包离线时间43min正常包,出钢时间284s,加入钢筋头废钢0.65t;软吹5.5分钟后吊至lf精炼处理;s6、吹氩完毕后钢包吊至lf进行精炼处理,在处理过程中加入冲压余料废钢0.8t,精炼给电时间增加4.5min,处理完毕后吊至连铸进行浇注。
[0023]
本实施例共加入废钢46.75t,铁水80.3t,生铁0t,废钢比37.47%,实现高废钢比冶炼。
[0024]
通过上述实施例证明,本发明中提高废钢比的冶炼工艺可行,且克服了现有技术中废钢预热和加入发热剂等问题,操作安全方便。采用本工艺,废钢占比可达30%以上,不采用废钢预热不添加发热剂,仅通过工艺改进实现了提高废钢比的目的,同时还实现了钢水冶炼过程的节能减排,提高了钢水产量,取得了较好社会效益和经济效益。
[0025]
以上所述仅为本发明的较佳实施例而已,并不用以限制本发明,凡在本发明的精神和原则之内所作的任何修改、等同替换和改进等,均应包含在本发明的保护范围之内。
再多了解一些
本文用于企业家、创业者技术爱好者查询,结果仅供参考。