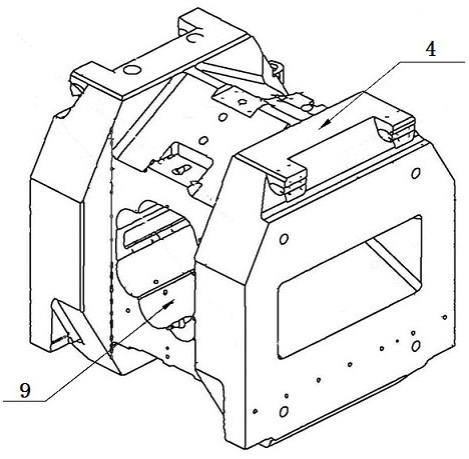
1.本发明属于铸造技术应用领域,涉及一种大型梅花孔机架铸造方法。
背景技术:
2.二十辊轧机是用于生产不锈钢、合金钢及硅钢等难变形金属和薄带材的可逆式轧机,具有工作辊直径小、辊系刚度大、轧制道次压下量较大、带材表面质量高,以及轧制力小、运行成本低、辊系变形小等特点。梅花机架是不锈钢二十辊轧机的核心零件,中心8个梅花孔分别安装支承辊,对梅花孔四周要求较高。与梅花通孔垂直的侧面开有通过带材的四棱锥形窗口。分散传到各支撑辊装置上的轧制压力,在八个梅花状通孔位置被整体机架所吸收。梅花孔位置和侧面开有通过带材的四棱锥形窗口探伤要求较严,需用双晶探头进行探伤,其质量的好坏直接影响轧机的正常运行。
3.根据梅花孔机架铸件的结构,一般采用多个分散冒口的工艺方案,即在厚大部位分别设置冒口的方案,这种方式在厚大结构的铸件中使用的最多。但梅花孔机架整体尺寸大,厚大的部位与薄壁处壁厚差可达800-1000mm,采取此种多个分散冒口的方案,由于局部厚大,为了满足补缩要求,冒口尺寸较大,但由于铸件整体尺寸的限制,冒口数量受到限制,不能兼顾铸件的每一个厚大部分,冒口不能完全发挥其补缩效果,凝固模拟效果显示铸件易出现内部质量缺陷,同时铸件壁厚差较大,此种冒口设置方案易出现凝固应力导致的裂纹缺陷。
4.而梅花孔位置和侧面的四棱锥形窗口(带材通过的窗口)探伤要求较严,需用双晶探头进行探伤,此种工艺方案难以满足双晶无损探伤的要求,一旦出现探伤缺陷,铸件报废的风险较大,因此针对此种特殊结构的梅花孔机架的铸造工艺方法就尤为重要。
技术实现要素:
5.有鉴于此,为解决上述现有技术的不足,本发明的目的在于提供一种大型梅花孔机架铸造方法,有效的控制了铸件的顺序凝固过程,保证满足无损探伤的要求,采用此种冒口集中补缩的铸造方法后,铸件具有良好的顺序凝固的温度梯度条件,同时避免了由于大的壁厚差造成的凝固应力大从而导致凝固过程的热裂纹的产生。
6.为实现上述目的,本发明所采用的技术方案是:一种大型梅花孔机架铸造方法,包括以下步骤:s1:进行散厚大截面且壁厚差值较大的铸钢件结构铸造时,采用单个大冒口集中补缩的工艺方案;s11:以梅花孔的中心为中心,将梅花孔局部铸实作为补贴和补缩通道,在铸件中心位置设置一个大冒口,在满足各个厚大截面部位的基础上均匀各个部位的壁厚尺寸,实现铸件由铸件到冒口的顺序凝固;s2:对热节的计算和冒口补贴的设计,确定最大热节并设置单个冒口;s21:自铸件本体最厚大部位开始,采取滚热节圆法设置补块,自下而上画圆,d1、
d2、d3
…
dn的圆心分别在d、d1、d2
…
dn-1的圆周上,且与铸件的内壁相切;s22:划线与热节圆d1、d2、d3
…
dn相切,得出铸件冒口补贴尺寸线,所述冒口补贴尺寸线以梅花孔的中心线为中心旋转实体后为铸件的冒口补贴;s23:画圆与冒口补贴及铸件本体相切,做出铸件的最大热节圆d
大,
在冒口补贴的上方设置单独冒口;s3:冒口补贴以下的梅花孔形状在内腔砂芯中做出;s4:在底面和侧面设置挂砂冷铁;s5:钢水冶炼时加入细化晶粒元素,得到更为细小的铸件晶粒组织。
7.进一步的,所述热节为热节圆d1、d2、d3
…
dn的直径,其中热节圆d1、d2、d3
…
dn的直径满足:d1=(1.05~1.1)d,d2=(1.05~1.1)d1,d3=(1.05~1.1)d2
…
dn=(1.05~1.1)dn-1。
8.进一步的,所述步骤s2中所述冒口的直径为最大热节圆d
大
直径的1.6~2.0倍,冒口浇高为冒口直径的1.2~1.5倍。
9.进一步的,所述步骤s4中底面挂砂冷铁厚度按热节的0.75~1.2倍设置;侧面设置阶梯型冷铁,侧面设置阶梯型冷铁,阶梯型冷铁下层的厚度按热节的0.6~1.0倍设置,阶梯型冷铁上层按热节的0.5~0.8倍设置。
10.进一步的,所述步骤s5中所述细化晶粒元素为0.025%nb,促进形成更多的形核。
11.进一步的,所述一种大型梅花孔机架铸造方法,在铸造时采用砂箱造型的方法制作型腔,型腔造型完成后,将熔炼好的钢液浇注到型腔内并按工艺保温时间进行保温,保温完成后进行铸件的清砂、浇冒口切割、毛坯正回火处理。
12.本发明的有益效果是:在本发明中,以梅花孔的中心为中心,将梅花孔局部铸实作为补贴和补缩通道,在铸件中心位置设置一个大冒口,在满足各个厚大截面部位的基础上均匀各个部位的壁厚尺寸,配合各个部位冷铁的激冷作用,实现铸件由铸件到冒口的顺序凝固,保证铸件的内部质量;冒口补贴以下的梅花孔形状在内腔砂芯中做出,减小梅花孔处加工余量,保证表层致密区域保留与铸件,满足探伤要求和使用要求;加入细化晶粒元素,可以得到更为细小的铸件晶粒组织;梅花孔形状随形铸出,减小梅花孔各个部分的加工余量,确保表层细密晶粒组织不被加工去除,满足梅花孔处严格探伤要求。
13.采用此种冒口集中补缩的铸造方法后,铸件具有良好的顺序凝固的温度梯度条件,同时避免了由于大的壁厚差造成的凝固应力大从而导致凝固过程的热裂纹的产生;用本发明中所述铸造工艺方案,可以满足厚大型铸钢件超声波探伤的要求,且表面质量良好,无裂纹、疏松,气孔、夹渣等铸造缺陷。
附图说明
14.为了更清楚地说明本发明实施例或现有技术中的技术方案,下面将对实施例或现有技术描述中所需要使用的附图作简单地介绍,显而易见地,下面描述中的附图仅仅是本发明的一些实施例,对于本领域普通技术人员来讲,在不付出创造性劳动的前提下,还可以根据这些附图获得其他的附图。
15.图1为本发明的梅花孔机架形状示意图;
图2是本发明的梅花孔机架探伤要求;图3是本发明的热节计算过程示意图;图4是本发明的最大热节计算过程示意图;图5是本发明梅花孔形状随形铸出示意图;图6是本发明局部铸实工艺方案示意图;图7是本发明实施例中铸件的示意图;图中标记:1、冒口补贴尺寸线,2、冒口补贴,3、热节,4、铸件本体,5、冒口直径,6、热节圆,7、冒口,8、冷铁,9、梅花孔。
具体实施方式
16.下面给出具体实施例,对本发明的技术方案作进一步清楚、完整、详细地说明,显然,所描述的实施例仅仅是本发明一部分实施例,而不是全部的实施例。基于本发明中的实施例,本领域普通技术人员在没有做出创造性劳动的前提下所得到的所有其它实施方式,都属于本发明所保护的范围。
17.实施例1:一种大型梅花孔机架铸造方法,满足铸件整体探伤及关键部位双晶探头的探伤要求,包括以下步骤:s1:进行散厚大截面且壁厚差值较大的铸钢件结构铸造时,采用单个大冒口7集中补缩的工艺方案;s11:以梅花孔9的中心为中心,将梅花孔9局部铸实作为补贴和补缩通道,如图6所示,在铸件中心位置设置一个大冒口7,在满足各个厚大截面部位的基础上均匀各个部位的壁厚尺寸,实现铸件由铸件到冒口7的顺序凝固,有效的满足铸件各个部位的补缩要求,有利于满足铸件的探伤及使用要求;s2:对热节3的计算和冒口补贴2的设计,确定最大热节并设置冒口7;s3:冒口补贴2以下的梅花孔9形状在内腔砂芯中做出,减小梅花孔9各个部分的加工余量,确保表层细密晶粒组织不被加工去除,满足梅花孔9处严格探伤要求,如图5所示;s4:在底面和侧面设置挂砂冷铁8,增加了冒口7的补缩距离,同时可以加速铸件的凝固速度,细化晶粒组织,提高铸件的力学性能;s5:钢水冶炼时加入细化晶粒元素,促进形成更多的形核,达到细化晶粒的目的。
18.进一步的,所述步骤s2中按剖视图中最厚大部位开始采取滚热节圆法设置补块并确定冒口7尺寸,自下而上画圆,圆d1、d2、d3
…
dn的圆心分别在d、d1、d2
…
dn-1的圆周上,且与铸件的内壁相切;划线与d1、d2、d3
…
dn相切,得出铸件冒口补贴尺寸线1,用圆角过渡后所述尺寸线以梅花孔9的中心线为中心旋转实体后即为铸件的冒口补贴2。
19.进一步的,所述热节为热节圆d1、d2、d3
…
dn的直径,其中热节圆d1、d2、d3
…
dn的直径满足:d1=(1.05~1.1)d,d2=(1.05~1.1)d1,d3=(1.05~1.1)d2
…
dn=(1.05~1.1)dn-1。
20.进一步的,所述步骤s2中冒口补贴2设计确定后,画圆与冒口补贴2及铸件本体4相切,做出铸件的最大热节圆d
大
,并在冒口补贴2的上方设置单独冒口7,冒口直径r为最大热
节圆d
大
直径的1.6~2.0倍,冒口浇高为冒口直径的1.2~1.5倍,满足厚大铸钢件的补缩要求。
21.进一步的,为了达到探伤二级,所述步骤s4中底面挂砂冷铁8厚度按热节3的0.75-1.2倍设置;侧面设置阶梯型冷铁8,下层冷铁8的厚度按热节3的0.6~1.0倍设置,上层冷铁8按热节3的0.5~0.8倍设置,以避免出现内部组织疏松,提高铸件内部质量。
22.进一步的,所述步骤s5中所述细化晶粒元素为0.025%质量的nb,促进形成更多的形核。
23.进一步的,所述一种大型梅花孔机架铸造方法,在铸造时采用砂箱造型的方法制作型腔,型腔造型完成后,将熔炼好的钢液浇注到型腔内并按工艺保温时间进行保温,保温完成后进行铸件的清砂、浇冒口切割、毛坯正回火处理。
24.本实例中所采用的梅花孔机架铸件轮廓尺寸为2440m
×
2575m
×
2380m,最大壁厚尺寸为1020mm,最小壁厚尺寸为240mm,如图1所示。
25.具体实施过程如下:1、工艺设计:以梅花孔9的中心为中心设置一个冒口7,将梅花孔9局部铸实作为补贴和补缩通道。
26.2、热节3计算和冒口补贴2的设计。
27.铸件本体4最厚大处热节圆6直径d=647mm,d1=710mm,d2=780mm。划线与d1、d2圆相切,做出冒口补贴尺寸线1,并在中心以r200圆过渡,如图3所示。
28.3、冒口7的设计与冒口补贴2及铸件本体4相切的最大热节圆6的直径d
大
=915mm,冒口直径1800mm,冒口浇高为2200mm,如图4所示。
29.4、冷铁的设置在底面和侧面设置挂砂冷铁8,冷铁8处铸件壁厚635mm,底面采取500mm厚冷铁,侧面下层采取450mm厚冷铁,侧面上层采用350mm厚冷铁,如图7所示。
30.5、生产验证在铸造时采用砂箱造型的方法制作型腔。采取中间分模、1/2抽芯实样的造型操作方式;型腔造型完成后,将熔炼好的钢液浇注到型腔内并按工艺保温时间进行保温,保温完成后进行铸件的清砂、浇冒口切割、毛坯正回火处理。
31.粗加工后进行ut检查,皆满足图纸的探伤要求,梅花,9和吊耳附近100mm范围内的关键区域探伤满足图纸jb/t5000.14-2007的2级要求,梅花孔9四周双晶探头ut探伤满足要求,如图2所示。
32.通过后期实际ut探伤检查,采用本发明中所述铸造工艺方案,可以满足厚大型铸钢件超声波探伤的要求,且表面质量良好,无裂纹、疏松,气孔、夹渣等铸造缺陷。
33.以上所述、仅为本发明的具体实施方式,但本发明的保护范围并不局限于此,任何本领域的技术人员在本发明借楼的技术范围内,对本发明所做的变形或替换,都应该涵盖在本发明的保护范围内;因此本发明的保护范围应以所述的权利要求的保护范围为准。
再多了解一些
本文用于企业家、创业者技术爱好者查询,结果仅供参考。