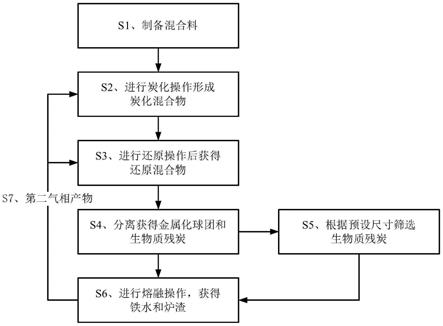
1.本发明涉及金属火法冶炼还原技术领域,尤其涉及一种直接应用生物质固废的金属化球团及铁水生产方法。
背景技术:
2.世界各国高度重视钢铁工业的温室气体减排的技术创新,这些技术紧紧依靠低碳冶金技术的创新、低碳冶金工艺流程再造、二氧化碳补集封存(ccs)、绿色能源、绿色还原剂制备技术作为基础,从源头上控制碳排放,实现低碳冶金绿色制造的转型。
3.目前国内外生产金属化球团的直接还原技术,根据还原剂种类,有气基和煤基两大类,气基主要有midrex(米德雷克斯法)、hyl(希尔法)等;煤基主要有回转窑法、转底炉法和煤基竖炉等。
4.气基还原技术需要优质的还原气,该技术存在还原气的制备和重整工艺和装置非常复杂、还原过程难以控制、对原料要求高、投资大、运行费用高等缺点,另外还原气来源于天然气、煤制煤气和焦炉煤气,这些气源均为化石能源。
5.现有的煤基直接还原技术虽然已经提出使用生物质炭、生物质气参与还原的方式,但仍然存在能耗高、产量小、不能直接采用生物质固废等缺点,对于生物质固废的利用程度有限。
6.而对于铁水生产工艺,主要有高炉炼铁工艺和非高炉熔融还原炼铁工艺,其中非高炉熔融还原炼铁工艺主要有corex工艺、finex工艺和hismelt工艺,上述四种炼铁工艺的产品均为铁水,均存在各自明显的工艺缺点:
7.高炉炼铁工艺的主要工艺缺点:工艺流程太长(包括烧结、球团、焦化)、污染物排放量很大、依赖焦煤资源、占地大、备件多、人员多;
8.corex和finex熔融还原工艺的主要缺点:投资太大、生产成本没有竞争力、铁水中硅含量高;
9.hismelt熔融还原工艺的主要缺点:渣中feo太高、炉缸寿命较短、铁的收得率低、喷吹设备寿命短、规模较小、投资较高;
10.这四种炼铁工艺除了各自的缺点外,均存在一项相同的严重缺陷:这就是都采用了大量的煤炭这种化石能源,每年均向大气中排入了大量的二氧化碳。这给我国及世界钢铁工业炼铁领域的的大幅度减碳带来了巨大的挑战。
11.如何降低目前现有炼铁工艺生产过程中产生的大量二氧化碳,世界各国都在积极探索和试验,采取的措施主要有:尽量加大绿氢的应用、尽量加大富氧的比例、喷吹富氢燃料、二氧化碳的脱除后炉顶煤气的循环使用、尽量加大绿电的使用及完善炉料质量等措施,这些措施有的效果将很有限,有的措施经济性差难以推广,有的技术上还不成熟,这些问题有的很难解决,有的还需要很长一段时间才能解决。
技术实现要素:
12.为解决现有技术的不足,本发明提出一种直接应用生物质固废的金属化球团及铁水生产方法,充分利用生物质固废这种可再生能源来还原含铁原料,与现有的各种高炉和非高炉直接还原和熔融还原炼铁工艺比较,不仅具有大幅度降低二氧化碳排放和标准煤能源消耗的突出优点,而且该方法还具有技术先进、装备可靠、规模大、成本低、环保好和质量优等技术特点。
13.为实现以上目的,本发明所采用的技术方案包括:
14.一种直接应用生物质固废的金属化球团及铁水生产方法,其特征在于,包括:
15.s1、制备混合料,所述混合料由生物质固废颗粒和含铁块组成;
16.s2、将混合料装入双基竖炉,所述混合料在双基竖炉的炭化段进行炭化操作形成炭化混合物,所述炭化混合物由生物质固废颗粒炭化形成的生物质炭和经过预热的含铁块组成;
17.s3、所述炭化混合物在双基竖炉的还原段进行还原操作后获得还原混合物,所述还原操作包括以生物质炭作为固体还原剂配合气体还原剂对含铁块进行还原,所述还原混合物由生物质炭经还原操作后所余生物质残炭和含铁块经还原操作所得金属化球团组成,所述气体还原剂包括炭化操作和/或还原操作产生的第一气相产物经净化操作所得还原气;
18.s4、还原混合物在双基竖炉的冷却段降温后排出并分离获得金属化球团和生物质残炭。
19.进一步地,所述方法还包括:
20.s5、根据预设尺寸筛选生物质残炭,将生物质残碳分类为大颗粒生物质残碳和小颗粒生物质残碳;
21.s6、将金属化球团、大颗粒生物质残碳、生物质固废颗粒和溶剂混合装入熔融炉进行熔融操作,获得金属化球团经熔融操作终还原所得铁水和炉渣;
22.s7、所述熔融操作产生的第二气相产物作为燃料气、冷却气和/或气体还原剂参与炭化操作、还原操作和熔融操作中的任意一种或多种。
23.进一步地,所述含铁块由含铁品位30%至72%的铁精粉、天然块矿、钢铁厂含铁固废、钒钛磁铁矿精矿粉、海砂矿精矿粉和钛铁矿精矿粉中的任意一种或多种含铁原料制备得到。
24.进一步地,所述含铁块由含铁品位30%至72%的铁精粉、天然块矿、钢铁厂含铁固废中的任意一种或多种含铁原料制备得到。
25.进一步地,所述生物质固废颗粒由玉米杆、棉花杆、大豆杆、玉米芯、麦草、稻草、杂草、花生壳、谷壳、树叶、树枝、树根、树皮、锯末、蘑菇袋、皮头、枯藤和海藻中的任意一种或多种生物质固体废弃物制备得到。
26.进一步地,所述生物质固废颗粒包括直径5至30mm、长度10至50mm的圆柱体颗粒;所述生物质固废颗粒的密度为1至2t/m3;所述生物质固废颗粒的热值为12000至22000kj/kg。
27.进一步地,所述混合料中含铁块与生物质固废颗粒的质量之比为1:0.3至1:3。
28.进一步地,所述炭化段炉温为200至1000℃,所述还原段炉温为1000至 1150℃,所
述气体还原剂的预热温度为1050至1250℃,所述金属化球团和大颗粒生物质残碳的温度为600至650℃,所述熔融炉的热风温度为1000至 1150℃,所述第二气相产物的温度为950至1150℃,所述铁水和炉渣的排出温度为1450至1550℃。
29.进一步地,所述步骤s7包括子步骤:
30.s71、使用余热锅炉对第二气相产物进行热量回收,并使用布袋除尘器对第二气相产物进行除尘净化。
31.进一步地,所述步骤s7还包括以下子步骤中的任意一种或多种组合:
32.s72、使用除尘净化后的第二气相产物作为熔融炉的热风加热燃料;
33.s73、使用除尘净化后的第二气相产物作为气体还原剂的预热燃料;
34.s74、使用除尘净化后的第二气相产物作为冷却段的冷却气;
35.s75、使用除尘净化后的第二气相产物作为气体还原剂。
36.进一步地,所述净化操作包括降温、脱水、二氧化碳脱除中的任意一种或多种组合。
37.进一步地,所述步骤s4包括:
38.使用热筛、冷筛、磁选中的任意一种或多种组合分离金属化球团和生物质残炭。
39.进一步地,所述金属化球团的金属化率不小于50%。
40.进一步地,所述方法还包括:
41.s8、对炉渣进行水淬操作得到水渣。
42.本发明的有益效果为:
43.采用本发明所述直接应用生物质固废的金属化球团及铁水生产方法能够实现多种有益效果,包括:1)大幅度降低二氧化碳的排放:由于生物质能源作为重要的可再生能源,是国际公认的零碳可再生能源,本发明直接采用生物质固废在双基竖炉和熔融炉中直接得到生物质炭和生物质气,两者分别作为固体还原剂和气体还原剂,并且生物质气还能通过燃烧提供还原所需要的热量,因此本发明与采用化石能源的其它炼铁工艺比较,不仅大幅度降低了二氧化碳的排放,降低幅度≥70%,而且很有希望实现零碳排放、甚至负碳排放。2)大幅度降低标准煤能源消耗:炼铁过程主要的能源消耗在于还原剂的消耗、燃料的消耗、电耗、水耗、氮气、压缩空气、蒸汽消耗等,前两者的消耗占总消耗的80-85%。由于生物质能源作为重要的可再生能源,是国际公认的零碳可再生能源,国家明确规定不纳入能源消耗总量中。本发明直接采用生物质固废在双基竖炉和熔融炉中直接得到生物质炭和生物质气,两者分别作为固体还原剂和气体还原剂,并且生物质气还能通过燃烧提供还原所需要的热量,因此本发明与采用化石能源的炼铁工艺比较,不仅大幅度降低了折合成标准煤的能源消耗,降低幅度≥70%,而且很有希望实现标准煤零消耗、甚至是标准煤负消耗。3)在双基竖炉和熔融炉中完成了两大功能:本发明在双基竖炉和熔融炉中完成了生物质固废的炭化和含铁原料的还原,生物质固废的炭化和含铁原料的还原在同一套装置中完成,这在现有的炼铁装置上实现了重大突破和重大创新,这将带来很多的十分有益的价值。4)在双基竖炉和熔融炉中同时实现了气固还原和固固还原:本发明在双基竖炉和熔融炉中完成了生物质颗粒的炭化和一系列的化学反应,因此不仅得到了作为固体还原剂的生物质炭,同时还得到了大量作为气体还原剂的生物质气,这就使得在双基竖炉和熔融炉中同时实现了双基还原:气固还原和固固还原,因此实现了双基还原的双基竖炉和熔融炉对含铁物料
的还原效率和物料运行等方面都是十分有利的。5)生物质固废的来源十分广泛、且为很好的还原剂:生物质固废为玉米杆、棉花杆、大豆杆、玉米芯、麦草、稻草、杂草、花生壳、谷壳、树叶、树枝、树根、树皮、锯末、蘑菇袋、皮头、枯藤和海藻等各种生物质固体废弃物,来源十分广泛,且每年的产生量很大,另外用其生产的生物质炭和生物质气有害元素含量很低、反应性好,是很好的固体还原剂和气体还原剂。6) 克服了目前生物质炭化装备规模小产量低的缺点:目前的生物质固废的炭化装置产量低、规模小,很难提供规模化的生物质炭和生物质气。双基竖炉能够规模化的高产量的处理生物质颗粒的炭化,从而能够为含铁原料的还原提供大量的生物炭固体还原剂、生物质气气体还原剂和生物质气燃料。7)生产能力远大于现有的煤基直接还原工艺:本发明双基竖炉采用了气体还原剂和固体还原剂,传热效率和还原效率均大大提高,另外物料是依靠自身的重力来运行的,因此生产能力远大于现有的煤基直接还原工艺,生产能力有望达到或超过现有的气基竖炉,从而从而有利于实现铁水生产的规模化。8)生产成本将低于现有的炼铁工艺:本发明采用广泛且低廉的生物质固废为原料,利用双基竖炉得到了还原需要的炭和气,生物质炭化和含铁原料的还原又能实现规模化,因此本发明的生产成本将低于现有的各种炼铁工艺。9)含铁原料的适应性将优于现有的炼铁工艺:含铁原料的含铁品位为30%-72%,具体为铁精粉、钢铁厂含铁固废等各种含铁原料,含铁原料的适应性强。10)为将来氢冶金的发展创造了更好的条件:本发明采用双基竖炉和熔融炉,既有气体还原剂,又有固体还原剂,待氢气制备的经济性得到市场认可后,双基竖炉和熔融炉将可以使用足够多的氢气作为还原剂,这将为世界氢冶金的发展创造了更好的条件。11)为电炉短流程的发展提供更加低碳和优质的原料:本发明双基竖炉生产的金属化球团,其金属化率可以≥90%,并且是规模化和低成本的低碳绿色制造,这将极大地助力我国短流程电炉炼钢的发展和壮大。12)为复杂矿难选矿的规模化生产创造了条件:本发明双基竖炉生产的金属化球团,其金属化率针对不同的原料能够实现≥90%的高金属化率,含铁原料适应的品位范围大、原料品种多,因此本发明生产的产品具有广阔的应用市场,不仅能为电炉炼钢或转炉炼钢提供优质的原料,而且还将能为回收钒、钛、锌等有价元素生产出优质的原料。
附图说明
44.图1为本发明直接应用生物质固废的金属化球团及铁水生产方法流程示意图。
45.图2为本发明第一实施例具体流程示意图。
46.图3为本发明第三实施例具体流程示意图。
具体实施方式
47.为了更清楚的理解本发明的内容,将结合附图和实施例详细说明。
48.如图1所示为本发明直接应用生物质固废的金属化球团及铁水生产方法的典型方法流程示意图,包括:
49.s1、制备混合料,所述混合料由生物质固废颗粒和含铁块组成。
50.其中,生物质固废经过粉碎、干燥和制粒等工序后得到生物质颗粒,含铁原料和粘结剂经过混匀、压块和烘干后得到含铁块,含铁块与生物质颗粒以质量之比1:0.3至1:3混合后形成混合料。
51.所述含铁块由含铁品位30%至72%的铁精粉、天然块矿、钢铁厂含铁固废、钒钛磁铁矿精矿粉、海砂矿精矿粉和钛铁矿精矿粉中的任意一种或多种含铁原料制备得到,优选的,采用含铁块由含铁品位30%至72%的铁精粉、天然块矿、钢铁厂含铁固废中的任意一种或多种含铁原料制备得到。同时,当含铁原料只为块矿时就不需要添加粘结剂进行混匀和压块这两个工序。
52.所述生物质固废颗粒由玉米杆、棉花杆、大豆杆、玉米芯、麦草、稻草、杂草、花生壳、谷壳、树叶、树枝、树根、树皮、锯末、蘑菇袋、皮头、枯藤和海藻中的任意一种或多种生物质固体废弃物制备得到,优选的,所述生物质固废颗粒包括直径5至30mm、长度10至50mm的圆柱体颗粒,密度为1至2t/m3,热值为12000至22000kj/kg。
53.s2、将混合料装入双基竖炉,所述混合料在双基竖炉的炭化段进行炭化操作形成炭化混合物,所述炭化混合物由生物质固废颗粒炭化形成的生物质炭和经过预热的含铁块组成。
54.具体的,混合料通过炉顶装料装置装入双基竖炉中,混合料在双基竖炉中向下运行,先经过炭化段,炭化段的温度在200℃-1000℃;混合料中的生物质颗粒在炭化段完成炭化,炭化后的生物质炭作为含铁块的固体还原剂;混合料中的含铁块在炭化段和还原段完成预热和还原。
55.s3、所述炭化混合物在双基竖炉的还原段进行还原操作后获得还原混合物,所述还原操作包括以生物质炭作为固体还原剂配合气体还原剂对含铁块进行还原,所述还原混合物由生物质炭经还原操作后所余生物质残炭和含铁块经还原操作所得金属化球团组成,所述气体还原剂可以优选的采用包括炭化操作、还原操作产生的第一气相产物经净化操作所得还原气,还可以进一步优选的使用由外部输入的富氢还原气进行搭配以得到效果适合的气体还原剂。
56.具体的,还原段的温度在1000℃-1150℃,生物质颗粒的炭化过程中和在含铁块的还原过程中形成的炉顶气从双基竖炉的顶部排出,炉顶气经过净化等工序得到还原气,还原气被加热至1050℃-1250℃后送入双基竖炉中,加热后的还原气不仅提供含铁块还原需要的热量,而且还原气还作为含铁块的气体还原剂。
57.s4、还原混合物在双基竖炉的冷却段降温后排出并分离获得金属化球团和生物质残炭。
58.优选的,步骤s4所得金属化球团可以作为一种半成品产品,例如使用如铁精粉、天然块矿、钢铁厂含铁固废、钒钛磁铁矿精矿粉、海砂矿精矿粉和钛铁矿精矿粉中的任意一种或多种含铁原料,生成金属化率≥90%的金属化球团,可以用于电炉炼钢或转炉炼钢等的生产原料。
59.另一方面,采用铁精粉、天然块矿、钢铁厂含铁固废等不含或含有少量钒、钛元素的含铁原料制得的金属化率≥50%的金属化球团可以适用于熔融炉生产铁水。
60.s5、根据预设尺寸筛选生物质残炭,将生物质残碳分类为大颗粒生物质残碳和小颗粒生物质残碳。
61.s6、将金属化球团、大颗粒生物质残碳、生物质固废颗粒和溶剂混合装入熔融炉进行熔融操作,获得金属化球团经熔融操作终还原所得铁水和炉渣。
62.具体的,将温度为600℃-650℃的金属化球团和大颗粒的生物质残炭通过炉顶装
置装入熔融炉中,同时从顶部向熔融炉中加入生物质颗粒和熔剂,从下部向熔融炉中喷入1000℃-1150℃的热风,最终从熔融炉排出1450℃-1550℃铁水和炉渣。铁水运至炼钢车间或铸造车间作为电炉或转炉或其它装置的优质原料,炉渣经过水淬后得到的水渣可以使用磨粉装置处理得到微粉,能够作为水泥厂的优质原料。
63.s7、所述熔融操作产生的第二气相产物作为燃料气、冷却气和/或气体还原剂参与炭化操作、还原操作和熔融操作中的任意一种或多种。优选的,从熔融炉顶部排出950℃-1150℃的炉顶煤气,经过余热锅炉回收热量和布袋除尘器净化后,炉顶煤气的一部分作为热风炉的燃料,一部分作为双基竖炉还原气的加热燃料,还有一部分作为双基竖炉的还原气和/或冷却段的冷却气。
64.如图2所示为本发明第一实施例具体流程示意图,工艺流程主要由生物质颗粒的制备工艺、含铁块的制备工艺、金属化球团的生产工艺、炉顶气的处理工艺及金属化球团的出料工艺组成,其中生物质颗粒的制备工艺主要包括生物质固废的粉碎装置、干燥装置和制粒装置等;含铁块的制备工艺主要包括含铁原料的粘结剂的混匀装置、压块装置和烘干装置;金属化球团的生产工艺主要包括装料装置、内衬材料、还原气进口装置、冷却气装置和炉顶气出口装置;炉顶气的处理工艺主要包括降温装置、净化装置、风机装置、脱水装置、成分调整装置和还原气加热装置;金属化球团的出料工艺主要包括排料装置、热筛装置、冷筛装置、磁选装置等。
65.应用如第一实施例所示方法时的具体操作步骤可以包括:
66.1)假设年处理铁精粉135万吨,铁精粉的品位≥67%;
67.2)生物质固废采用树枝、秸秆、稻草等,通过粉粹机粉粹,然后干燥,水分≤5%,最后通过制粒机制粒,每年得到生物质颗粒30万吨,生物颗粒的直径为10mm,长度为15mm;
68.3)铁精粉和粘结剂混匀后,采用对辊式压球机压球,压球通过网带式干燥机干燥,干燥后的球水分≤2%,尺寸为20mmx25mmx30mm;
69.4)干燥球和生物质颗粒混合后通过炉顶装置装入双基还原炉,双基还原炉内部直径为6m,总高度为25m;
70.5)生物质颗粒在竖炉内的上部完成炭化生成生物质碳,同时炭化过程中得到大量的生物质气,这些生物质气主要为生物质颗粒中含有的大量的挥发分组成,然后生物质炭作为还原剂参与干燥球的还原,生物质气的大部分作为炉顶气的一部分全部从竖炉顶部排出;
71.6)排出的炉顶气为300℃-350℃,首先经过多级洗涤塔等装置降温、除焦油、净化和脱水后,得到常温和净化后的炉顶气,炉顶气最后经过脱出二氧化碳装置的得到主要成分为co和h2的还原气,利用外部燃料将还原气加热至1100℃后送入双基竖炉的中下部,加热后入炉还原气的流量为20万nm3/h-22万nm3/h;
72.7)生物质颗粒和干燥球在经过双基竖炉的炭化段和还原段后完成了生物质颗粒的炭化和干燥球的还原,再经过冷却气的冷却后排出炉外,排出炉外的温度 650℃,最后经过热筛装置筛分分别得到金属化率≥92%、全铁≥89%的直接还原铁100万吨和生物质残炭约5万吨,最后600℃直接还原铁直接加入电炉作为电炉炼钢的优质原料,生物质残炭通过冷却筒冷却后作为炭肥的优质原料。
73.应用如第一实施例所示方法能实现的有益效果包括:1)采用生物质固废和铁精粉
用于生产直接还原铁(高品位高金属化率的金属化球团),由于生物质固废炭化得到的生物质炭和生物质气作为铁精粉还原的固体还原剂和气体还原剂,使得生产最终产品的碳排放量大幅度降低,标准煤消耗量也将大幅度降低,降低幅度均≥70%;2)生物质固废的炭化和含铁原料的还原在同一套装置中完成,这在现有的所有直接还原装置上实现了重大突破和重大创新,这将带来很多的十分有益的价值;3)在双基竖炉中同时实现了双基还原:气固还原和固固还原,因此实现了双基还原的双基竖炉对含铁物料的还原效率和物料运行等方面都是十分有利的;4)生物质炭和生物质气有害元素含量很低、反应性好,是很好的固体还原剂和气体还原剂;5)双基竖炉能够规模化的高产量的处理生物质颗粒的炭化,从而能够为含铁原料的还原提供大量的生物炭固体还原剂、生物质气气体还原剂和生物质气燃料;6)双基竖炉采用了气体还原剂和固体还原剂,传热效率和还原效率均大大提高,另外物料是依靠自身的重力来运行的,因此生产规模远大于现有的煤基直接还原工艺;7)由于采用廉价的生物质固废作为原料,产品的生产成本将低于现有的气基和煤基直接还原工艺;8)含铁原料的适应性强,含铁原料的含铁品位范围大,为30%-72%,不仅能还原铁精粉,还能还原钢铁厂含铁固废、钒钛磁铁矿精矿粉、海砂矿精矿粉或钛铁矿精矿粉等各种含铁原料;9)双基竖炉将可以使用足够多的全氢或富氢作为还原剂,这将为氢冶金的发展创造了更好的条件;10)本发明将极大地助力我国短流程电炉炼钢的发展和壮大,还将能为最终回收钒、钛、锌等有价元素生产出优质的原料。
74.第二实施例所采用的方法流程类似于图2所示第一实施例,包括:
75.1)假设年处理含锌含铁钢铁厂固废50万吨,综合含铁品位为50%、含zn 为3.5%;
76.2)生物质固废采用树枝、秸秆、稻草等,通过粉粹机粉粹,然后干燥,水分≤5%,最后通过制粒机制粒,每年得到生物质颗粒25万吨,生物颗粒的直径为10mm,长度为15mm;
77.3)钢铁厂固废和粘结剂混匀后,采用对辊式压球机压球,压球通过网带式干燥机干燥,干燥后的球水分≤2%,尺寸为20mmx25mmx30mm;
78.4)干燥球和生物质颗粒混合后通过炉顶装置装入双基还原炉,双基还原炉内部直径为4.5m,总高度为20m;
79.5)生物质颗粒在竖炉内的上部完成炭化生成生物质碳,同时炭化过程中得到大量的生物质气,这些生物质气主要为生物质颗粒中含有的大量的挥发分组成,然后生物质炭作为还原剂参与干燥球的还原,生物质气的大部分作为炉顶气的一部分全部从竖炉顶部排出;
80.6)排出的炉顶气为950℃-1000℃,首先经过余热锅炉余热回收降温后,在通过布袋除尘器净化,每年得到粗锌粉3.15万吨;
81.7)炉顶气最后经过脱出二氧化碳装置的得到主要成分为co和h2的还原气,利用生物质气作为燃料将还原气加热至1100℃后送入双基竖炉的中下部,加热后入炉还原气的流量为10万nm3/h-12万nm3/h;
82.8)生物质颗粒和干燥球在经过双基竖炉的炭化段和还原段后完成了生物质颗粒的炭化和干燥球的还原,再经过冷却气的冷却后排出炉外,排出炉外的温度≤150℃,最后经过冷筛装置筛分分别得到金属化率≥90%、全铁≥68%的金属化球团38万吨和生物质残炭约3万吨,金属化球团可以作为转炉炼钢的冷却剂,生物质残炭作为炭肥的优质原料。
83.如图3所示为本发明第三实施例具体流程示意图,工艺流程主要由生物质颗粒的
制备工艺、含铁块的制备工艺、金属化球团的生产工艺、炉顶气的处理工艺、金属化球团的出料工艺、熔融炉的装料工艺、熔融炉炉顶煤气的处理工艺、熔融炉热风的喷入工艺、熔融炉出铁出渣工艺等组成,其中生物质颗粒的制备工艺主要包括生物质固废的粉碎装置、干燥装置和制粒装置等;含铁块的制备工艺主要包括含铁原料的粘结剂的混匀装置、压块装置和烘干装置;金属化球团的生产工艺主要包括装料装置、内衬材料、还原气进口装置、冷却气装置和炉顶气出口装置;炉顶气的处理工艺主要包括降温装置、净化装置、风机装置、脱水装置、成分调整装置和还原气加热装置;金属化球团的出料工艺主要包括排料装置、热筛装置、冷筛装置、磁选装置;熔融炉的装料工艺主要包括高温链板输送机装置、炉顶装置、大倾角输送机装置等;熔融炉炉顶煤气的处理工艺主要包括汽化烟道、旋风除尘器、余热锅炉、布袋除尘器等;熔融炉热风的喷入工艺主要包括鼓风机、热风炉、助燃风机等;熔融炉出铁出渣工艺主要包括泥炮、开口机、渣铁沟、铁水罐等。
84.应用如第三实施例所示方法时的具体操作步骤可以包括:
85.1)假设年处理铁精粉146万吨,铁精粉的品位≥65%;
86.2)生物质固废采用树枝、秸秆、稻草等,通过粉粹机粉粹,然后干燥,水分≤5%,最后通过制粒机制粒,每年得到生物质颗粒50万吨,生物颗粒的直径为20mm,长度为30mm;
87.3)铁精粉和粘结剂混匀后,采用对辊式压球机压球,压球通过网带式干燥机干燥,干燥后的球水分≤2%,尺寸为20mmx25mmx30mm;
88.4)干燥球和生物质颗粒混合后通过炉顶装置装入双基还原炉,双基还原炉内部直径为6.5m,总高度为28m;
89.5)生物质颗粒在竖炉内的上部完成炭化生成生物质碳,同时炭化过程中得到大量的生物质气,这些生物质气主要为生物质颗粒中含有的大量的挥发分组成,然后生物质炭作为还原剂参与干燥球的还原,生物质气的大部分作为炉顶气的一部分全部从竖炉顶部排出;
90.6)排出的炉顶气为300℃-350℃,首先经过多级洗涤塔等装置降温、除焦油、净化和脱水后,得到常温和净化后的炉顶气,炉顶气最后经过脱出二氧化碳装置的得到主要成分为co和h2的还原气,利用外部燃料将还原气加热至1100℃后送入双基竖炉的中下部,加热后入炉还原气的流量为30万nm3/h-35万nm3/h;
91.7)生物质颗粒和干燥球在经过双基竖炉的炭化段和还原段后完成了生物质颗粒的炭化和干燥球的还原,再经过冷却气的冷却后排出炉外,排出炉外的温度 650℃,最后经过热筛装置筛分分别得到金属化率≥70%、全铁≥80%的金属化球团108万吨和生物质残炭约20万吨,最后600℃金属化球团和大颗粒残炭直接加入熔融炉;
92.8)从熔融炉顶部向熔融炉中加入生物质颗粒和熔剂,从下部向熔融炉中喷入1000℃-1150℃的热风;
93.9)从熔融炉顶部排出950℃-1150℃的炉顶煤气,经过余热锅炉回收热量和布袋除尘器净化后,炉顶煤气的一部分作为热风炉的燃料,一部分作为双基竖炉还原气的加热燃料,还有一部分作为双基竖炉的还原气和/或冷却段的冷却气;
94.10)最终从熔融炉排出1450℃-1550℃铁水和炉渣,铁水年产量为100万吨,运至炼钢车间或铸造车间作为电炉或转炉或其它装置的优质原料,炉渣经过水淬后得到的水渣(每年32万吨)作为水泥厂的优质原料。
95.应用如第三实施例所示方法能实现的有益效果包括:1)采用生物质固废和铁精粉用于生产铁水,由于生物质固废炭化得到的生物质炭和生物质气作为铁精粉还原的固体还原剂和气体还原剂,使得生产最终产品的碳排放量大幅度降低,标准煤消耗量也将大幅度降低;2)生物质固废的炭化和含铁原料的还原在同一套装置中完成,这在现有的所有直接还原装置上实现了重大突破和重大创新,这将带来很多的十分有益的价值;3)在双基竖炉和熔融炉中同时实现了双基还原:气固还原和固固还原,因此实现了双基还原的双基竖炉和熔融炉对含铁物料的还原效率和物料运行等方面都是十分有利的;4)生物质炭和生物质气有害元素含量很低、反应性好,是很好的固体还原剂和气体还原剂;5)双基竖炉和熔融炉能够规模化的高产量的处理生物质颗粒的炭化,从而能够为含铁原料的还原提供大量的生物炭固体还原剂、生物质气气体还原剂和生物质气燃料;6) 双基竖炉和熔融炉采用了气体还原剂和固体还原剂,传热效率和还原效率均大大提高,另外物料是依靠自身的重力来运行的,因此生产规模大;7)由于采用廉价的生物质固废作为原料,产品的生产成本将低于现有的炼铁工艺;8)含铁原料的适应性强,含铁原料的含铁品位范围大,为30%-72%,不仅能还原铁精粉,还能还原钢铁厂含铁固废等含铁原料;9)双基竖炉和熔融炉将可以使用足够多的全氢或富氢作为还原剂,这将为氢冶金的发展创造了更好的条件。
96.第四实施例所采用的方法流程类似于图3所示第三实施例,包括:
97.1)假设年处理含锌含铁固废50万吨,综合含铁品位为50%、含zn为3.5%;
98.2)生物质固废采用树枝、秸秆、稻草等,通过粉粹机粉粹,然后干燥,水分≤5%,最后通过制粒机制粒,每年得到生物质颗粒25万吨,生物颗粒的直径为20mm,长度为30mm;
99.3)钢铁厂固废和粘结剂混匀后,采用对辊式压球机压球,压球通过网带式干燥机干燥,干燥后的球水分≤2%,尺寸为20mmx25mmx30mm;
100.4)干燥球和生物质颗粒混合后通过炉顶装置装入双基还原炉,双基还原炉内部直径为4.5m,总高度为20m;
101.5)生物质颗粒在竖炉内的上部完成炭化生成生物质碳,同时炭化过程中得到大量的生物质气,这些生物质气主要为生物质颗粒中含有的大量的挥发分组成,然后生物质炭作为还原剂参与干燥球的还原,生物质气的大部分作为炉顶气的一部分全部从竖炉顶部排出;
102.6)排出的炉顶气为950℃-1000℃,首先经过余热锅炉余热回收降温后,在通过布袋除尘器净化,每年得到粗锌粉3.15万吨;
103.7)炉顶气最后经过脱出二氧化碳装置的得到主要成分为co和h2的还原气,利用生物质气作为燃料将还原气加热至1100℃后送入双基竖炉的中下部,加热后入炉还原气的流量为10万nm3/h-12万nm3/h;
104.8)生物质颗粒和干燥球在经过双基竖炉的炭化段和还原段后完成了生物质颗粒的炭化和干燥球的还原,再经过冷却气的冷却后排出炉外,排出炉外的温度≤150℃,最后经过冷筛装置筛分分别得到金属化率≥90%、全铁≥68%的金属化球团38万吨和生物质残炭约3万吨,最后600℃金属化球团和大颗粒残炭直接加入熔融炉;
105.9)从熔融炉顶部向熔融炉中加入生物质颗粒和熔剂,从下部向熔融炉中喷入1000℃-1150℃的热风;
106.10)从熔融炉顶部排出950℃-1150℃的炉顶煤气,经过余热锅炉回收热量和布袋
除尘器净化后,炉顶煤气的一部分作为热风炉的燃料,一部分作为双基竖炉还原气的加热燃料,还有一部分作为双基竖炉的还原气和/或冷却段的冷却气;
107.11)最终从熔融炉排出1450℃-1550℃铁水和炉渣,铁水年产量为26万吨,运至炼钢车间或铸造车间作为电炉或转炉或其它装置的优质原料,炉渣经过水淬后得到的水渣(每年10万吨)作为水泥厂的优质原料。
108.以上所述仅为本发明较佳的具体实施方式,但本发明的保护范围并不局限于此,任何熟悉本技术领域的技术人员在本发明揭露的技术范围内,可轻易想到的变化或替换等都应涵盖在本发明的保护范围之内。因此,本发明的保护范围应该以权利要求书的保护范围为准。
再多了解一些
本文用于企业家、创业者技术爱好者查询,结果仅供参考。