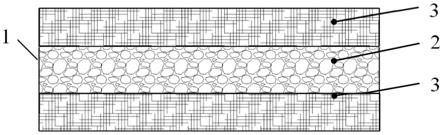
1.本发明属于有机复合材料技术领域,涉及高渗透性插层增韧材料及其制备方法。
背景技术:
2.复合材料液体成型(liquid composite molding,简称lcm)工艺是制备热固性树脂基复合材料的主流工艺之一,是生产高性能、低成本复合材料制品的有效途径,其基本原理是利用较低粘度的液态热固性树脂流动实现对干态纤维或织物的浸渍,具体的是将纤维增强材料叠层铺设在模具中,然后通过一定的压力将液态树脂注入模腔,浸润纤维增强材料并同时排除空气,填充固化后脱模成型复合材料制品。lcm的典型工艺技术包括rtm、vartm、vip、scrimp等。
3.目前几种常用的增韧方法是在热固性树脂中加入橡胶弹性体或在交联网络中加入柔性链段,使用较多的有聚碳酸酯(polycarbonate,pc)、聚醚酮(polyether ketone,pek)、聚醚醚酮(polyetherether ketone,peek)、聚砜(poly sulfone,psf)以及聚醚砜(polyether sulfone,pes)等热塑性工程塑料。该方法虽然显著提高了热固性树脂的增韧改性效果,但同时会增大树脂粘度,降低树脂渗透浸润纤维能力,因此如何解决树脂高渗透性和复合材料高韧性的矛盾是突破复合材料液体成型工艺发展瓶颈的关键。
4.为解决上述矛盾,中国发明专利“一种液态成型复合材料用预制织物及其制备方法(公开号cn101220561a)”,提出了一种具有定型-增韧双功能的预制织物的制备方法,通过在基底纤维织物的表面黏附增韧层和定型层的方法,具体是将增韧层应用溶液涂覆(胶液)、热熔涂覆(粉末)、成膜复合(薄膜)、热压转移(热熔胶)等方法形成连续增韧层或离散增韧层。中国专利“一种rtm预成型体织物粉末预定型及其制备方法”(公开号:cn101760965a),提出一种将增韧剂及定型剂共混的定型增韧复合材料的方法。中国发明专利“一种兼具定型-增韧双功能的纤维织物的制备方法”(公开号:cn102644199a),提出一种单面带有增韧剂,另一面带有定型剂的增强纤维织物。中国发明专利“一种兼具复合材料定型-增韧双功能的非织造布(公开号):cn104401070a”提出了一种中间层为复合材料增韧纤维层,上层与下层由定型剂制备纤维层的解决方案。
5.以上发明专利均是以热压或热熔方式将胶液状态、粉末状态和成膜状态的增韧材料涂覆在基底纤维织物上,胶液状态和粉末状态的涂覆方式很难保证增韧材料的均匀性和透气性,而成膜状态的涂覆方式虽能解决增韧材料均匀性的问题,但其加热加压的复合转移过程较为复杂,工业化生产难度大,同时会造成增韧层(非织造布)的空隙率降低,甚至会出现空隙融合封闭现象,对基底纤维织物透气性也会造成一定影响,进而导致树脂在增韧层和增强纤维织物层内流动的速度不平衡,在增韧层内部残留严重的气泡和针孔,降低了复合材料制品质量。
技术实现要素:
6.本发明的一个目的是提供一种高渗透性插层增韧材料,解决了现有树脂复合材料
不能同时具备高渗透性和高韧性的的问题。
7.本发明的另一个目的是提供一种高渗透性插层增韧材料的制备方法。
8.本发明所采用的第一技术方案是,一种高渗透性插层增韧材料,由增韧层和渗透层组成,增韧层位于芯部,渗透层位于增韧层的两侧,呈夹芯结构,增韧层的重量百分比为65%~80%,两侧渗透层的重量百分比相同,增韧层和两侧渗透层的重量百分比之和为100%,增韧层为丝连网状结构,材质为热塑性树脂,渗透层为短切纤维毡。
9.其中,热塑性树脂为聚氨酯、聚酰胺、聚醚砜、聚砜或聚醚酰亚胺。
10.增韧层的面密度为40g/m2~100g/m2。
11.渗透层的材质为碳纤维、玻璃纤维或芳纶纤维。
12.短切纤维毡中纤维长度为5mm~8mm,渗透层的面密度为8g/m2~12g/m2。
13.本发明所采用的第二技术方案是,一种高渗透性插层增韧材料的制备方法,包括将固态的增韧层树脂熔融至流体,通过高速热气流喷丝,在下方纤维渗透层的上表面喷附网状增韧层,最后在未冷却的增韧层表面铺设粘合一层纤维渗透层。
14.具体步骤如下:
15.步骤1,准备一层纤维渗透层,纤维渗透层为短切纤维毡;
16.步骤2,将固态的增韧层树脂放入熔融设备中,高温熔化至流体;
17.步骤3,将熔化后的增韧层树脂通过高速热气流喷头喷丝,在步骤1准备的纤维渗透层上表面喷附网状增韧层;
18.步骤4,在未冷却的网状增韧层上表面铺设粘合一层纤维渗透层,待冷却降温后,即制备出一种高渗透性插层增韧材料。
19.纤维渗透层由碳纤维、玻璃纤维或芳纶纤维制成。
20.增韧层树脂为聚氨酯、聚酰胺、聚醚砜、聚砜或聚醚酰亚胺。
21.步骤3中,在步骤1准备的纤维渗透层上表面喷附网状增韧层,网状增韧层的面密度为40g/m2~100g/m2。
22.本发明的有益效果是:
23.(1)通过在网状增韧层上下表面铺设短切纤维毡状渗透层,以提高复合材料液体成型树脂的透过性,进而平衡树脂在渗透层和增韧层中的流动速度,减小了复合材料层间包裹气体的概率;
24.(2)增韧层树脂扩散后与渗透层纤维融为一体,形成可靠的增韧梯度结构,有效抵抗了层间集中的应力,提高了复合材料抗冲击性能;
25.(3)渗透层采用短切纤维毡,短切纤维可嵌入纤维织物和增韧层的空隙中,在厚度上起到对两者桥联的作用,从而改变了常规增韧方式下层间剪切破坏机理,增大了能量消耗,提高了层间抗损伤能力;
26.(4)增韧层和渗透层均为非织造结构,透气性高,在树脂填充过程中能起到良好的导气作用,使层间组织更致密,同时具有良好的伏模性,可适应任何形状产品的插层铺设;
27.(5)采用增韧层喷附和渗透层粘合一次成型的方式,形成增韧和透气的优势互补,降低了增韧材料的涂覆难度,生产过程不间断,材料长度不限,质量稳定,均匀性高,重复性好,生产过程完全自动化,生产效率高。
附图说明
28.图1是本发明一种高渗透性插层增韧材料的结构示意图;
29.图2是实施例1中采用本发明高渗透性插层增韧材料制备的复合材料制品的结构示意图。
30.图中,1.高渗透性插层增韧材料,2.增韧层,3.渗透层,4.纤维织物。
具体实施方式
31.下面结合附图和具体实施方式对本发明进行详细说明。
32.实施例1
33.制备一种由聚氨酯和芳纶纤维复合而成的高渗透性插层增韧材料,具体包括以下步骤:
34.步骤1,准备一层纤维渗透层,纤维渗透层的面密度为10g/m2,纤维渗透层为短切纤维毡,由芳纶纤维制成,短切纤维毡中纤维长度为6mm;
35.步骤2,将聚氨酯粒料放入熔融设备中,在220℃下高温熔化至流体;
36.步骤3,将熔化后的聚氨酯通过高速热气流喷头喷丝,在步骤1准备的纤维渗透层上表面喷附面密度为40g/m2的均匀网状增韧层,通过卷辊输送至铺贴辊位置;熔融状态的粘性丝状增韧材料仅对短切纤维渗透层表面的浮纤进行粘合,不会浸渗至渗透层内部,从而使短切纤维渗透层继续保持良好的树脂透过性;
37.步骤4,在未冷却的网状增韧层上表面铺设粘合一层短切芳纶纤维渗透层,经过产线上冷却降温后,即制备出一种由聚氨酯和芳纶纤维复合而成的高渗透性插层增韧材料1,增韧层2位于芯部,渗透层3位于增韧层的两侧,呈夹芯结构(参见图1)。
38.采用该高渗透性插层增韧材料1作为原料制备复合材料制品时,先对其进行裁切,然后与芳纶纤维制成的纤维织物4间隔铺设在模具中,采用vip工艺注射tde85环氧树脂,并按照树脂固化制度完成固化,拆模后即获得复合材料制品(参见图2)。制备的复合材料制品具有良好的抗冲击分层能力和抗疲劳特性,保证了热固性层合板复合材料的强韧性和内部质量的稳定性,同时能够有效降低制备增韧材料的工艺控制难度,实现自动化连续生产的目标,同时从根本上解决液体成型工艺方式下树脂高渗透性和复合材料高韧性的矛盾。
39.实施例2
40.制备一种由聚酰胺和玻璃纤维复合而成的高渗透性插层增韧材料,具体包括以下步骤:
41.步骤1,准备一层纤维渗透层,纤维渗透层的面密度为8g/m2,纤维渗透层为短切纤维毡,由玻璃纤维制成,短切纤维毡中玻璃纤维长度为5mm;
42.步骤2,将聚酰胺粒料放入熔融设备中,在250℃下高温熔化至流体;
43.步骤3,将熔化后的聚酰胺通过高速热气流喷头喷丝,在步骤1准备的纤维渗透层上表面喷附面密度为60g/m2的网状增韧层,通过卷辊输送至铺贴辊位置;
44.步骤4,在未冷却的网状增韧层上表面铺设粘合一层短切玻璃纤维渗透层,经过产线上冷却降温后,即制备出一种由聚酰胺和玻璃纤维复合而成的高渗透性插层增韧材料,增韧层位于芯部,渗透层位于增韧层的两侧,呈夹芯结构。
45.采用该高渗透性插层增韧材料作为原料制备复合材料制品时,先对其进行裁切,
然后与玻璃纤维织物间隔铺设在模具中,采用vartm工艺注射901乙烯基酯树脂,并按照树脂固化制度完成固化,拆模后即获得复合材料制品。
46.实施例3
47.制备一种由聚醚砜和碳纤维复合而成的高渗透性插层增韧材料,具体包括以下步骤:
48.步骤1,准备一层纤维渗透层,纤维渗透层的面密度为10g/m2,纤维渗透层为短切纤维毡,由碳纤维制成,短切纤维毡中碳纤维长度为6mm;
49.步骤2,将聚醚砜粒料放入熔融设备中,在400℃下高温熔化至流体;
50.步骤3,将熔化后的聚醚砜通过高速热气流喷头喷丝,在步骤1准备的纤维渗透层上表面喷附面密度为80g/m2的网状增韧层,通过卷辊输送至铺贴辊位置;
51.步骤4,在未冷却的网状增韧层上表面铺设粘合一层短切碳纤维渗透层,经过产线上冷却降温后,即制备出一种由聚醚砜和碳纤维复合而成的高渗透性插层增韧材料,增韧层位于芯部,渗透层位于增韧层的两侧,呈夹芯结构。
52.采用该高渗透性插层增韧材料作为原料制备复合材料制品时,先对其进行裁切,然后与碳纤维织物间隔铺设在模具中,采用rtm工艺注射ag-70环氧树脂,并按照树脂固化制度完成固化,拆模后即获得复合材料制品。
53.实施例4
54.制备一种由聚砜和碳纤维复合而成的高渗透性插层增韧材料,具体包括以下步骤:
55.步骤1,准备一层纤维渗透层,纤维渗透层的面密度为12g/m2,纤维渗透层为短切纤维毡,由碳纤维制成,短切纤维毡中碳纤维长度为8mm;
56.步骤2,将聚砜粒料放入熔融设备中,在350℃下高温熔化至流体;
57.步骤3,将熔化后的聚砜通过高速热气流喷头喷丝,在步骤1准备的纤维渗透层上表面喷附面密度为60g/m2的网状增韧层,通过卷辊输送至铺贴辊位置;
58.步骤4,在未冷却的网状增韧层上表面铺设粘合一层短切碳纤维渗透层,经过产线上冷却降温后,即制备出一种由聚砜和碳纤维复合而成的高渗透性插层增韧材料,增韧层位于芯部,渗透层位于增韧层的两侧,呈夹芯结构。
59.采用该高渗透性插层增韧材料作为原料制备复合材料制品时,先对其进行裁切,然后与碳纤维织物间隔铺设在模具中,采用rtm工艺注射e54环氧树脂,并按照树脂固化制度完成固化,拆模后即获得复合材料制品。
60.实施例5
61.制备一种由醚酰亚胺和碳纤维复合而成的高渗透性插层增韧材料,具体包括以下步骤:
62.步骤1,准备一层纤维渗透层,纤维渗透层的面密度为10g/m2,纤维渗透层为短切纤维毡,由碳纤维制成,短切纤维毡中碳纤维长度为7mm;
63.步骤2,将醚酰亚胺粒料放入熔融设备中,在410℃下高温熔化至流体;
64.步骤3,将熔化后的醚酰亚胺通过高速热气流喷头喷丝,在步骤1准备的纤维渗透层上表面喷附面密度为100g/m2的网状增韧层,通过卷辊输送至铺贴辊位置;
65.步骤4,在未冷却的网状增韧层上表面铺设粘合一层短切碳纤维渗透层,经过产线
上冷却降温后,即制备出一种由醚酰亚胺和碳纤维复合而成的高渗透性插层增韧材料,增韧层位于芯部,渗透层位于增韧层的两侧,呈夹芯结构。
66.采用该高渗透性插层增韧材料作为原料制备复合材料制品时,先对其进行裁切,然后与碳纤维织物间隔铺设在模具中,采用rtm工艺注射6421双马来酰亚胺树脂,并按照树脂固化制度完成固化,拆模后即获得复合材料制品。
再多了解一些
本文用于企业家、创业者技术爱好者查询,结果仅供参考。