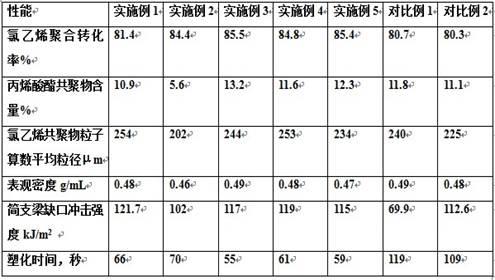
1.加工性能优良的氯乙烯接枝共聚物的制备方法,属于氯乙烯接枝共聚技术领域。
背景技术:
2.聚氯乙烯树脂具有成本较低、耐化学品性能优良的优点,但也存在机械性能低、加工性能和热稳定性差等主要问题。对于聚氯乙烯树脂机械性能的改进和提升,主要采用物理和化学两种方法。物理方法主要包括共混等手段,如将专用抗冲改性剂与pvc树脂粉料共混,然后深度的塑化加工等操作,有效提高抗冲击性能。物理方法受原料、加工条件和配方等因素影响较大,抗冲改性剂在pvc树脂中易产生分散不均、机械性能取向差异较大等问题,无法充分保证加工制品质量稳定性。相比之下,在pvc树脂制造过程中将具有抗冲功能的橡胶类核心组分与氯乙烯单体共聚,可有效解决制品机械性能各向差异和稳定性问题。橡胶类核心组分形成的胶乳粒径大小对树脂改性能力具有重要影响。
3.申请人在研究中发现,现有的氯乙烯接枝共聚物存在以下问题:现有的氯乙烯接枝共聚物加工性能并不理想,主要表现为塑化时间过长,这会导致氯乙烯接枝共聚物在组合物体系中的分散性不佳,还会导致组合物所制得的制品外观不理想,具体表现为制品表面不够光滑、形状不够规整,并且该问题在高抗冲性氯乙烯接枝共聚物中表现尤为明显。
4.如何在保证氯乙烯接枝共聚物抗冲性的基础上,还能获得较好的加工性能,是目前迫切需要解决的问题。
技术实现要素:
5.本发明要解决的技术问题是:克服现有技术的不足,提供一种加工性能优良的氯乙烯接枝共聚物的制备方法,该方法所得氯乙烯接枝共聚物具有较短的塑化时间、加工性能优异。
6.本发明解决其技术问题所采用方法的技术方案是:该加工性能优良的氯乙烯接枝共聚物的制备方法,包括以下步骤:1)丙烯酸酯胶乳一次聚合:将脱盐水、阴离子乳化剂、第一分散剂、第一引发剂、丙烯酸酯单体和交联剂混匀;在惰性气氛下聚合,得丙烯酸酯胶乳;2)丙烯酸酯胶乳二次聚合:向步骤1)所得丙烯酸酯胶乳中,搅拌加入无机强酸强碱盐的水溶液,静置10~20分钟;加入第一引发剂,升温至55~70℃,再加入丙烯酸酯类混合单体进行聚合,然后补加第一引发剂,聚合反应得固含量25~35%质量百分比、数均粒径0.1~0.4μm的丙烯酸酯大粒径胶乳;步骤2)所述丙烯酸酯类混合单体为甲基丙烯酸甲酯、丙烯酸丁酯和乙二醇二甲基丙烯酸酯按重量比12~25:3~5:0.01~0.02的混合物;3)氯乙烯接枝共聚:加入脱盐水、纤维素醚、ph调节剂、第二引发剂,在惰性气氛保护下、抽真空,加氯乙烯
单体和步骤2)所得丙烯酸酯大粒径胶乳,混匀后,悬浮接枝聚合,得氯乙烯接枝共聚物。
7.步骤1)的具体操作为:按重量份将脱盐水160~220份、阴离子乳化剂0.5~5份、第一分散剂0.08~0.1份、第一引发剂0.10~1份、丙烯酸酯单体100份和交联剂0.75~2份混匀;在惰性气氛、55~70℃下聚合反应,得固含量30~40%质量百分比、数均粒径0.050~0.100μm的丙烯酸酯胶乳。
8.步骤2)的具体操作为:在20~50℃下,向步骤1)所得丙烯酸酯胶乳中,搅拌加入5~10 %质量百分比的无机强酸强碱盐的水溶液50~90份,静置10~20分钟;按重量份加入第一引发剂0.001~0.02份,升温至55~70℃,再加入丙烯酸酯类混合单体10~50份进行聚合,补加第一引发剂0.005~0.01份,得固含量25~35%质量百分比、数均粒径0.1~0.4μm的丙烯酸酯大粒径胶乳。
9.步骤3)的具体操作为:按重量份加入脱盐水150~200份、纤维素醚0.1~0.2份、ph调节剂0.05~0.1份、第二引发剂0.01~0.2份,在惰性气氛保护下、抽取真空后,加氯乙烯单体100份、步骤2)所得丙烯酸酯大粒径胶乳18~45份,混匀后,45~65℃条件下悬浮接枝聚合,经终止、脱气、脱水、干燥、筛分,得氯乙烯接枝共聚物。
10.步骤1)所述丙烯酸酯单体为丙烯酸乙酯和丙烯酸丁酯按重量比1~2:8~9的混合物;步骤1)所述的交联剂为甲基丙烯酸烯丙酯。
11.步骤2)所述加入丙烯酸酯类混合单体的具体操作为:将丙烯酸酯类混合单体混合均匀,按重量均分为3~4等分,间隔15~30分钟加入1等分。
12.步骤2)所述无机强酸强碱盐为氯化钠、氯化钾、硫酸钠。
13.步骤1)和2)所述第一引发剂为过硫酸钾、过硫酸钠或过硫酸铵。
14.步骤3)所述第二引发剂为过氧化新癸酸叔丁酯、过氧化叔戊酸叔戊酯、过氧化新癸酸异丙苯酯、过氧化二碳酸二(2-乙基己基)酯中的一种或两种。
15.步骤3)所述纤维素醚为羟丙基甲基纤维素。
16.对本发明的说明如下:步骤1)所述阴离子乳化剂为月桂酸钾、油酸钾或硬脂酸钾。
17.步骤1)所述第一分散剂为氯化钾或焦磷酸钠。
18.步骤3)所述ph调节剂为碳酸氢铵。
19.步骤2)所述无机强酸强碱盐水溶液中无机强酸强碱盐用量,占步骤2)所述丙烯酸酯胶乳干重的质量百分比为0.1~5.0%步骤3)终止所用终止剂为0.01~0.02份,终止剂为丙酮缩氨基硫脲。
20.优选的,步骤1)所得固含量33~38.5%质量百分比、数均粒径0.063~0.078μm的丙烯酸酯胶乳。进一步优选的,步骤1)所得丙烯酸酯胶乳固含量为33~35%质量百分比,如步骤1)所得丙烯酸酯胶乳浓度高于该范围,需加脱盐水稀释,再在步骤2)中使用。
21.优选的,步骤2)所得固含量27.4~32.4%质量百分比、数均粒径0.194~0.287μm的丙烯酸酯大粒径胶乳。
22.与现有技术相比,本发明的所具有的有益效果是:1、本发明所得氯乙烯接枝共聚物具有较短的塑化时间、加工性能优异。
23.第一,本发明在步骤2)中,首先搅拌加入无机强酸强碱盐的水溶液,静置10~20分钟,然后再加入第一引发剂升温聚合。
24.第二,本发明在步骤2)中所用丙烯酸酯类混合单体为甲基丙烯酸甲酯、丙烯酸丁酯和乙二醇二甲基丙烯酸酯按重量比12~25:3~5:0.01~0.02的混合物。
25.第三,本发明在步骤2)中将丙烯酸酯类混合单体混合均匀,按重量均分为3~4等分,间隔15~30分钟加入1等分,从而提高了步骤2)聚合反应的稳定性。
26.以上设计能够使步骤2)所得丙烯酸酯大粒径胶乳聚结紧密、核壳结构较为均匀,最终步骤3)氯乙烯聚合转化率较高。本发明所得氯乙烯共聚物塑化时间短,具有较好的加工性能,易于加工。
27.、在保证加工性能的同时,本本发明所得氯乙烯接枝共聚物还具有较好的抗冲击性能。
28.第一,本发明采用三步设计,在步骤1)丙烯酸酯胶乳一次聚合获得丙烯酸酯胶乳后,采用步骤2)丙烯酸酯胶乳二次聚合进行扩径,然后再进行步骤3)氯乙烯接枝共聚得氯乙烯接枝共聚物,该工艺路线明显提高了氯乙烯共聚物粒子算数平均粒径和氯乙烯共聚物的抗冲击性能。
29.第二,在步骤3)氯乙烯接枝共聚中添加了纤维素醚,明显提高了氯乙烯共聚物的抗冲击性能。
具体实施方式
30.下面结合具体实施例对本发明做进一步说明,其中实施例3为最佳实施例。
31.实施例11)一次聚合得丙烯酸酯胶乳:向配有氮气入口、搅拌器、回流冷凝管和升降温装置的四口烧瓶中加入脱盐水160份、月桂酸钾2份、氯化钾0.08份、以及由85份丙烯酸丁酯、15份丙烯酸乙酯和2份甲基丙烯酸烯丙酯组成的单体混合物,瓶内空气用氮气吹扫干净,开启搅拌并升温至65℃,入过硫酸钾0.25份聚合反应;当转化率达到97%以上后,结束聚合反应,得到固含量38.2%、算数平均粒径0.063μm的丙烯酸酯胶乳;加脱盐水将所得丙烯酸酯胶乳固含量稀释至33%;2)丙烯酸酯胶乳二次聚合:将步骤1)所得丙烯酸酯胶乳降温至35℃,在搅拌状态下滴加浓度5.0%质量百分比的氯化钠水溶液50份,稳定10分钟后,加入过硫酸钾0.01份,升温至65℃,将由15份甲基丙烯酸甲酯、5份丙烯酸乙酯和0.02份乙二醇二甲基丙烯酸酯组成的混合单体均分为3等分,间隔20分钟加入1等分到聚合体系中,最后再补加0.005份过硫酸钾,继续反应至单体转化率大于98.0%,得到固含量32.2% 胶乳平均粒径0.194μm的丙烯酸酯大粒径胶乳;3)氯乙烯接枝共聚向洁净的不锈钢压力聚合釜中加入脱盐水130份、羟丙基甲基纤维素e50(道化学公司产品)0.12份、碳酸氢铵0.06份以及第二引发剂过氧化二碳酸-双(2-乙基己酯)0.13份,封闭聚合釜后,用氮气置换釜内空气,再抽取真空至-0.080mpa以下,加入氯乙烯单体100份,在常温下搅拌混合15分钟,加入步骤2)所得丙烯酸酯大粒径胶乳31份(含干基聚合物10份),升温至57℃进行反应,直至压力降达到0.15mpa时加入终止剂丙酮缩氨基硫脲0.01份;排净未反应单体、得树脂浆料,将树脂浆料经过脱水得到湿料,再于60℃下干燥,经过筛,即得氯乙烯接枝共聚物;
实施例聚合完成后,釜壁和搅拌桨叶表面均干净,证明聚合体系稳定性良好。
32.实施例21)丙烯酸酯胶乳一次聚合向配有氮气入口、搅拌器、回流冷凝管和升降温装置的四口烧瓶中加入脱盐水220份、油酸钾1.5份、焦磷酸钠0.10份以及由90份丙烯酸丁酯、10份丙烯酸乙酯和2份甲基丙烯酸烯丙酯组成的单体混合物,瓶内空气用氮气吹扫干净,开启搅拌并升温至55℃,再加入过硫酸钠0.75份引发聚合反应,待转化率达到98%以上后,得到固含量33.3%、算数平均粒径0.075μm的丙烯酸酯胶乳;2)丙烯酸酯胶乳二次聚合将步骤1)所得丙烯酸酯胶乳降温至40℃,在搅拌状态下滴加浓度5.0%质量百分比的氯化钾水溶液90份,稳定10分钟后,加入过硫酸钠引发剂0.01份,升温至55℃,将由12份甲基丙烯酸甲酯、3份丙烯酸丁酯和0.01份乙二醇二甲基丙烯酸酯组成的混合单体均分为3等分,间隔30分钟加入1等分到聚合体系中,最后再补加0.005份过硫酸钠,继续反应至单体转化率大于95%,得到固含量27.4% 胶乳平均粒径0.239μm的丙烯酸酯大粒径胶乳;3)氯乙烯接枝共聚向洁净的不锈钢压力聚合釜中加入脱盐水200份、羟丙基甲基纤维素e50(道化学公司产品)0.10份、碳酸氢铵0.1份以及第二引发剂过氧化二碳酸-双(2-乙基己酯)0.09份,封闭聚合釜后,用氮气置换釜内空气,再抽取真空至-0.080mpa以下,加入氯乙烯单体100份,在常温下搅拌混合15分钟,加入步骤2)所得丙烯酸酯大粒径胶乳18.2份,升温至63.5℃进行反应,直至压力降达到0.35mpa时加入终止剂丙酮缩氨基硫脲0.01份;排净未反应单体,pvc树脂浆料经过脱水得到湿料,再于60℃下干燥,经过筛,即得氯乙烯接枝共聚物;聚合完成后,釜壁和搅拌桨叶表面均光滑干净,聚合体系稳定性良好。
33.实施例31)丙烯酸酯胶乳一次聚合:向配有氮气入口、搅拌器、回流冷凝管和升降温装置的四口烧瓶中加入脱盐水180份、硬脂酸钾1份、焦磷酸钠0.08份以及由80份丙烯酸丁酯、20份丙烯酸乙酯和0.75份甲基丙烯酸烯丙酯组成的单体混合物,瓶内空气用氮气吹扫干净,开启搅拌并升温至70℃,再加入过硫酸铵0.30份引发聚合反应;待转化率达到99%以上后,得到固含量35.0%、算数平均粒径0.078μm的丙烯酸酯胶乳;2)丙烯酸酯胶乳二次聚合:将步骤1)所得丙烯酸酯胶乳降温至40℃,在搅拌状态下滴加浓度5.0%质量百分比的氯化钾水溶液80份, 稳定10分钟后加入过硫酸铵0.02份,升温至70℃,将由25份甲基丙烯酸甲酯、5份丙烯酸丁酯和0.01份乙二醇二甲基丙烯酸酯组成的混合单体均分为4等分,间隔15分钟加入1等分到聚合体系中,再补加0.01份过硫酸铵,继续反应至单体转化率大于97%,得到固含量32.4% 、平均粒径0.287μm的丙烯酸酯大粒径胶乳;3)氯乙烯接枝共聚:向洁净的不锈钢压力聚合釜中加入脱盐水100份、羟丙基甲基纤维素e50(道化学公司产品)0.18份、碳酸氢铵0.05份以及第二引发剂过氧化二碳酸-双(2-乙基己酯)0.12份,封闭聚合釜后,用氮气置换釜内空气,再抽取真空至-0.080mpa以下,加入氯乙烯单体100份,
在常温下搅拌混合15分钟,加入步骤2)所得丙烯酸酯大粒径胶乳40.1份,升温至52℃进行反应,直至压力降达到0.27mpa时加入终止剂丙酮缩氨基硫脲0.01份;排净未反应单体、得树脂浆料,将树脂浆料经过脱水得到湿料,再于60℃下干燥,经过筛,即得氯乙烯接枝共聚物;聚合完成后,釜壁和搅拌桨叶表面均光滑干净,聚合体系稳定性良好。
34.实施例41)丙烯酸酯胶乳一次聚合:向配有氮气入口、搅拌器、回流冷凝管和升降温装置的四口烧瓶中加入脱盐水175份、硬脂酸钾1份、焦磷酸钠0.08份以及由85份丙烯酸丁酯、15份丙烯酸乙酯和1份甲基丙烯酸烯丙酯组成的单体混合物,瓶内空气用氮气吹扫干净,开启搅拌并升温至68℃,再加入过硫酸铵0.30份引发聚合反应;待转化率达到99%以上后,得到固含量34.2%、算数平均粒径0.091μm的丙烯酸酯胶乳;2)丙烯酸酯胶乳二次聚合:将步骤1)所得丙烯酸酯胶乳降温至50℃,在搅拌状态下滴加浓度10%质量百分比的硫酸钠水溶液85份, 稳定10分钟后加入过硫酸铵0.015份,升温至70℃,将由20份甲基丙烯酸甲酯、4份丙烯酸丁酯和0.02份乙二醇二甲基丙烯酸酯组成的混合单体均分为4等分,间隔15分钟加入1等分到聚合体系中,再补加0.01份过硫酸铵,继续反应至单体转化率大于98%,得到固含量33.7% 、平均粒径0.292μm的丙烯酸酯大粒径胶乳;3)氯乙烯接枝共聚:同实施例3;聚合完成后,釜壁和搅拌桨叶表面均光滑干净,聚合体系稳定性良好。
35.实施例 51)丙烯酸酯胶乳一次聚合:向配有氮气入口、搅拌器、回流冷凝管和升降温装置的四口烧瓶中加入脱盐水170份、硬脂酸钾1份、焦磷酸钠0.08份以及由80份丙烯酸丁酯、20份丙烯酸乙酯和0.75份甲基丙烯酸烯丙酯组成的单体混合物,瓶内空气用氮气吹扫干净,开启搅拌并升温至60℃,再加入过硫酸铵1份引发聚合反应;待转化率达到99%以上后,得到固含量35%、算数平均粒径0.078μm的丙烯酸酯胶乳;2)丙烯酸酯胶乳二次聚合:将步骤1)所得丙烯酸酯胶乳降温至20℃,在搅拌状态下滴加浓度7%质量百分比的氯化钠水溶液65份, 稳定20分钟,后加入过硫酸铵0.02份,升温至55℃,将由15份甲基丙烯酸甲酯、5份丙烯酸丁酯和0.01份乙二醇二甲基丙烯酸酯组成的混合单体均分为4等分,间隔20分钟加入1等分到聚合体系中,再补加0.005份过硫酸铵,继续反应至单体转化率大于97%,得到固含量34.8% 、平均粒径0.262μm的丙烯酸酯大粒径胶乳;3)氯乙烯接枝共聚:同实施例3;聚合完成后,釜壁和搅拌桨叶表面均光滑干净,聚合体系稳定性良好。
36.对比例1本对比例制备方法同实施例3,区别在于:本对比例仅采用步骤1)和3),未操作步骤2)。
37.对比例2本对比例制备方法同实施例3,区别在于:步骤2)所用丙烯酸酯类混合单体不同,丙烯
酸酯类混合单体中未加甲基丙烯酸甲酯。
38.步骤2)中:由30份丙烯酸丁酯和0.01份乙二醇二甲基丙烯酸酯组成丙烯酸酯类混合单体。
39.性能测试对实施例和对比例所得氯乙烯接枝共聚物进行性能测试,测试标准如下,测试结果录入表1。
40.1、共聚物胶乳粒径和接枝共聚物树脂粒度测定采用malvern公司产mastersizer 2000 激光粒度仪测定;2、氯乙烯聚合转化率:重量法;3、表观密度:按照gb/t 20022-2005测试;4、简支梁缺口冲击强度:按gb/t 1043.1-2008规定的条件在23℃进行测试;4.1)样条配方,按如下重量份计:氯乙烯接枝共聚树脂100份,有机锡8831
ꢀꢀ
1.5份,润滑剂zb-60
ꢀꢀ
0.5份,润滑剂zb-74
ꢀꢀ
0.4份;4.2)样条制样方法:按上述配方称量并混合物料,经高速混合机中捏合、sk-160b双辊混炼机混炼(175
±
5℃,5分钟)制得混炼片材,再于热压机上压制4mm厚片材(180
±
2℃,3分钟),按标准要求制成简支梁冲击样条;5、氯乙烯接枝共聚树脂加工性能测定:按4.1)~4.2)中配混料制备样条,在德国haake公司的转矩流变仪上进行塑化性能测试,测试条件为温度160℃,转子转速40r/min,加料量68g。
41.表1 性能测试结果。
42.通过表1可以看出:对比例1未操作步骤2),所得氯乙烯接枝共聚物的抗冲击性低,塑化时间长。并且,拌轴及桨叶端处有少许结块,结块干燥质量为接枝聚合物质量的0.110%。可见未经步骤2)扩径的丙烯酸酯胶乳接枝共聚物抗冲击强度较低,塑化时间较长。
43.对比例2步骤2)所用丙烯酸酯类混合单体与本发明不同,最终所得氯乙烯接枝共聚物塑化时间长,加工性能不理想。
44.实施例1~5不但具有较好的抗冲击强度,并且塑化时间短,加工性能优异。其中实
施例3抗冲击性能较好,并且塑化时间最短,为最优实施例。
45.以上所述,仅是本发明的较佳实施例而已,并非是对本发明作其它形式的限制,任何熟悉本专业的技术人员可能利用上述揭示的技术内容加以变更或改型为等同变化的等效实施例。但是凡是未脱离本发明技术方案内容,依据本发明的技术实质对以上实施例所作的任何简单修改、等同变化与改型,仍属于本发明技术方案的保护范围。
再多了解一些
本文用于企业家、创业者技术爱好者查询,结果仅供参考。