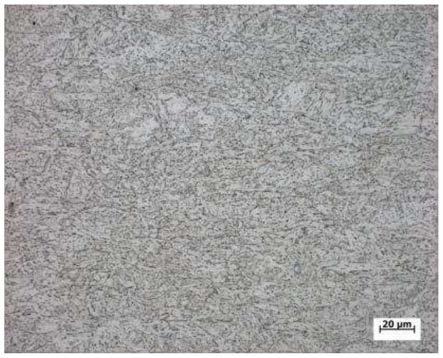
1.本发明涉及钢及其制造方法,具体涉及一种桥梁钢及其制造方法。
背景技术:
2.低屈强比、高强、高韧、高塑、高耐候桥梁钢是桥梁建设的发展趋势。在屈服强度690mpa级的高强度耐候桥梁钢中,合金添加量大,钢基体组织获得贝氏体组织的倾向高,因此控制难点主要集中在钢的塑性、屈强比等指标,特别是厚规格钢板在生产过程中韧塑性和屈强比的控制,此外,厚规格高强度钢板为了保证其淬透性,在线冷却速度较快,内应力较大,性能难以保证。
3.中国专利公开号cn201810426240.6公开了一种屈服强度≥690mpa的低屈强比耐候桥梁用结构钢及生产方法,其组份及wt%为:c 0.04-0.10%,si 0.01-0.20%,mn 0.80-1.70%,p≤0.010%,s≤0.005%,cu 0.20-0.55%,ni 0.40-1.50%,mo 0.20-0.80%,cr:0.35-0.70%,nb 0.030-0.090%,ti 0.008-0.030%,als 0.015-0.060%,n≤0.0080%,ca 0.0010-0.0050%,其余为fe及不可避免的杂质,且c nb:0.11-0.15%,金相组织为贝氏体 铁素体,生产方法:对铸坯加热;粗轧;精轧;分段冷却;回火;自然冷却至室温。该方法在保证桥梁钢结构用高强钢屈服强度≥690mpa,抗拉强度在810-930mpa,-40℃kv2≥150j的前提下,使屈强比在0.74-0.85,但该方法所采用的返红温度较低,返红温度较低时的轧态钢板的板形极难控制,并且其回火温度在180-380℃,属于低温回火,过程中产生的内应力极有可能在焊接加工过程中,发生不可预见的热变形甚至焊缝开裂。
4.中国专利号为cn201910907095.8公开了一种抗震高强度耐候桥梁钢板q690qenhz35及其生产方法,其组分及重量百分比含量为:c 0.05-0.12%,si 0.08-0.25%,mn 0.09-1.45%,p≤0.012%,s≤0.003%,cu 0.25-0.35%,ni 0.80-1.85%,mo 0.25-0.80%,cr:0.50-1.0%,v 0.040-0.080%,ti 0.010-0.020%,b 0.0008-0.00135%,其余为fe及不可避免的杂质;该方法采取预淬火处理 亚温淬火处理 回火处理,相较于现有技术增加了预淬火处理 亚温淬火处理2道离线淬火热处理,导致钢种成本明显增加。
技术实现要素:
5.发明目的:为了解决现有技术存在的技术问题,本发明旨在提供一种低成本和高性能的桥梁钢。本发明的另一目的是提供一种桥梁钢的制造方法。
6.技术方案:本发明提供一种桥梁钢,所述桥梁钢由以下质量百分比的成分组成c0.07-0.09%、si 0.25-0.55%、mn 1.30-1.70%、p≤0.0080%、s≤0.002%、nb 0.040-0.070%、ti 0.010-0.020%、cu 0.20-0.40%、ni 0.80-1.20%、cr 0.40-0.70%、mo 0.35-0.60%、alt 0.02-0.04%,余量的fe及不可避免的杂质,所述桥梁钢厚度超过32mm且小于等于60mm,金相组织为回火贝氏体。
7.进一步的,上述mn 1.55-1.65%。
8.本发明所述的桥梁钢的制造方法包括以下工序:冶炼、连铸、均热、轧制、冷却和离线回火,所述离线回火工序的回火温度为380-450℃,并在此温度下保温90-180min,随后自然冷却至室温。
9.进一步的,上述连铸工序采用的铸坯厚度为220-260mm。
10.进一步的,上述铸坯连铸后进行堆冷24-48h,堆冷时间与铸坯厚度成正相关关系。
11.进一步的,上述均热工序的加热温度为1160-1210℃,温度均匀性小于15℃。
12.进一步的,上述均热工序的加热时间为铸坯厚度
×
0.9min/mm-铸坯厚度
×
1.4min/mm。
13.进一步的,上述轧制工序采取两阶段轧制,再结晶区轧制和未再结晶区轧制,再结晶区轧制温度1030-1070℃,总变形量为49-55%,厚度控制在成品厚度的2.2-3.0倍,未再结晶区轧制温度810-850℃。
14.上述轧制工序终轧温度790-830℃。
15.上述冷却工序采用层流冷却,返红温度控制在50-250℃,随后置于空气中冷却至室温。
16.本发明所述桥梁钢成分配比的确定是通过改变基本元素的含量和添加可以强化并改善钢材料力学性能的合金元素来实现的,遵循多元少量的原则,采用控轧控冷 离线回火的方法,有效保留了钢板轧制时的位错强化作用,再通过离线回火析出金属间化合物来进一步提高钢的屈服强度,获得了厚度规格为32-60mm且屈强比≤0.87的钢板,其交货状态为tmcp(热机械控制轧制和控制冷却) t(回火)。对于以tmcp状态供货的钢板,需要对厚板(板厚大于等于32mm)增加回火消应力处理,以降低钢板内应力。特别是随着桥梁钢使用级别的不断提高,对高性能桥梁钢供货状态的要求应更为严格谨慎,所以提高回火温度降低内应力,是有益于减轻或消除钢板在焊接加工过程中热变形、焊缝开裂等问题。
17.具体而言,本发明成分中钢中c含量不宜过高,同时降低s、气体杂质含量并控制耐蚀元素p含量,确保钢质纯净并具有强韧性。本发明以回火贝氏体的组织类型实现了低屈强比和高低温韧性和高延伸性,各成分及含量的说明如下:
18.c是钢中不可缺少的提高钢材强度及硬度的元素,对钢组织影响显著。c溶入基体形成间隙固溶体,起到固溶强化的作用,显著增加基体的强度。随着碳含量的增加,钢的抗拉强度和屈服极限会提高而延伸率、冲击韧性则下降。当钢材中c含量较高时易加剧产生冷裂纹,因此,本发明采用低碳设计,将c质量百分含量设定为0.07-0.09%。
19.mn是钢中的一种主要元素,锰元素可以提高材料强度,另外mn元素在钢中还是防止热脆性的主要元素,综合考虑,本发明mn百分含量设定为1.30-1.70%。
20.si元素在钢中主要以很强的固溶强化形式提高钢的强度,也是炼钢脱氧的必要元素,可以提高耐大气腐蚀性能,但明显降低钢的塑性和韧性且显著降低钢的表面涂镀性能,因此,综合考虑强度、韧性、塑性等因素,本发明si百分含量设定为0.25~0.55%。
21.p促进锈层非晶态转变,一般而言,cu、p复合具有最优的耐候效果,是比较经济的耐蚀元素,考虑到p导致低温脆性和裂纹敏感性,在重要焊接结构用耐候钢中,一般限制p的含量,本发明p百分含量控制为≤0.0080%。
22.s含量较高时会降低钢的耐蚀性、低温韧性、z向性能,本发明s百分含量控制为≤0.002%。
23.nb是强碳氮化合物形成元素,能提高钢的奥氏体再结晶温度,奥氏体可以在更高的轧制温度下进行轧制。此外nb在控制轧制连续冷却过程中的析出强化作用,通过nb的碳氮化物的应变诱导析出可以钉扎奥氏体晶粒,细化奥氏体晶粒并提高强度及低温韧性。本发明nb百分含量控制在0.040-0.070%。
24.ti能显著提高强度,起到细化晶粒作用,也可提高钢的韧性,适量的ti可以形成第二项质点,提高金属的韧性,本发明ti百分含量为0.010-0.020%。
25.ni能提高淬透性,具有一定的强化作用,能显著地改善钢板的低温韧性,并且能有效阻止cu的热脆引起的网裂,还能提高钢的耐大气腐蚀性能。本发明ni百分含量控制在0.80-1.20%。
26.cu元素在钢中主要起到固溶强化作用,适量的铜可提高强度而不降低韧性,也可提高钢的耐蚀性,本发明cu百分含量为0.20-0.40%。
27.cr适宜的添加可以提高钢的强度,并显著改善钢的耐候性,本发明cr百分含量为0.40-0.70%。
28.mo是较强的固溶强化元素,强烈提高淬透性,并提高回火稳定性,显著降低回火脆性,同时和ni、cr、cu组合添加,能提高钢的抗点蚀能力。本发明mo百分含量为0.35-0.60%。
29.al是钢中的主要脱氧元素,al可以用来阻止晶粒长大,但al含量过高时将导致al的氧化物夹杂增加,降低钢的纯净度,不利于钢的韧性。本发明alt的百分含量为0.02-0.04%。
30.本发明通过提高ni、mo元素的含量,可以显著提高厚板的淬透性,有益于改善厚板心部的强度和韧性。反之,对于高强度、厚规格钢板,若淬透性元素添加量少,则容易在钢板心部形成粒状贝氏体,且由于心部晶粒粗大,虽可以降低屈强比,但易造成钢的低温韧性较低以及强度偏低,从而不满足桥梁制造用690mpa级桥梁钢的要求。
31.进一步的,所述桥梁钢耐大气腐蚀性指数i≥7.0。其中,耐大气腐蚀性指数i=26.01(%cu) 3.88(%ni) 1.20(%cr) 1.49(%si) 17.28(%p)-7.29(%cu)(%ni)-9.10(%ni)(%p)-33.39(%cu)2。
32.有益效果:与现有技术相比,本发明具有以下显著优点:
33.(1)低成本,本发明通过科学的成分设计及相匹配的控轧控冷 离线回火的制造方法,工艺流程简单,成本低;
34.(2)高性能,本发明制得的桥梁钢具有低屈强比、高韧性、高延性和优良的耐腐蚀性能,其屈服强度720mpa以上,抗拉强度850mpa以上,成品钢的屈强比≤0.87,-40℃akv在200j以上且纤维断面率在80%以上,延伸率≥16%,耐大气腐蚀性指数i≥7.0,综合性能好,适应于桥梁结构的应用。
附图说明
35.图1为本发明实施例3的500倍光学金相组织图。
具体实施方式
36.下面,结合具体实施例进一步对本发明进行说明。
37.实施例1
38.所述桥梁钢成分以质量百分比计为:c 0.08%、si 0.25%、mn 1.30%、p 0.0080%、s 0.0012%、nb 0.070%、ti 0.012%、ni 1.05%、cu 0.20%、cr 0.70%、mo 0.35%、alt 0.02%,余量为fe及不可避免杂质。
39.所述桥梁钢的制造工序如下:原料通过冶炼得到钢水,钢水上板坯连铸,铸坯厚度为220mm,连铸坯堆冷24小时,把坯料在1210℃下均热,温度均匀性小于15℃,加热220min后进行除磷,随后进行两阶段轧制,再结晶区轧制温度为1070℃,总变形量为55%,中间坯厚度控制在成品厚度3.0倍,未再结晶区轧制开轧温度为850℃,达到最终产品厚度33mm,终轧温度为830℃。终轧后进行层流冷却,返红温度为250℃,而后空气中冷却至室温,然后对钢板进行离线回火,回火温度在450℃,并在此温度下保温90min,随后自然冷却至室温。
40.实施例2
41.所述桥梁钢成分以质量百分比计为:c 0.07%、si 0.50%、mn 1.70%、p 0.0080%、s 0.0015%、nb 0.060%、ti 0.020%、ni 0.80%、cu 0.25%、cr 0.55%、mo 0.40%、alt 0.04%,余量为fe及不可避免杂质。
42.所述桥梁钢的制造工序如下:原料通过冶炼得到钢水,钢水上板坯连铸,铸坯厚度为260mm,连铸坯堆冷48小时,把坯料在1200℃下均热,温度均匀性小于15℃,加热286min后进行除磷,随后进行两阶段轧制,再结晶区轧制温度为1070℃,总变形量为49%,中间坯厚度控制在成品厚度3.0倍,未再结晶区轧制开轧温度为850℃,达到最终产品厚度44mm,终轧温度为810℃。终轧后进行层流冷却,返红温度为200℃,而后空气中冷却至室温,然后对钢板进行离线回火,回火温度在430℃,并在此温度下保温132min,随后自然冷却至室温。
43.实施例3
44.所述桥梁钢成分以质量百分比计为:c 0.07%、si 0.55%、mn 1.60%、p 0.0070%、s 0.0010%、nb 0.040%、ti 0.015%、ni 0.90%、cu 0.40%、cr 0.40%、mo 0.60%、alt 0.02%,余量为fe及不可避免杂质,金相组织见图1。
45.所述桥梁钢的制造工序如下:原料通过冶炼得到钢水,钢水上板坯连铸,铸坯厚度为260mm,连铸坯堆冷48小时,把坯料在1180℃下均热,温度均匀性小于15℃,加热234min后进行除磷,随后进行两阶段轧制,再结晶区轧制温度为1050℃,总变形量为52%,中间坯厚度控制在成品厚度2.5倍,未再结晶区轧制开轧温度为830℃,达到最终产品厚度50mm,终轧温度为800℃。终轧后进行层流冷却,返红温度为100℃,而后空气中冷却至室温,然后对钢板进行离线回火,回火温度在400℃,并在此温度下保温150min,随后自然冷却至室温。
46.实施例4
47.所述桥梁钢成分以质量百分比计为:c 0.09%、si 0.40%、mn 1.55%、p 0.0070%、s 0.0012%、nb 0.055%、ti 0.010%、ni 1.20%、cu 0.30%、cr 0.50%、mo 0.45%、alt 0.025%,余量为fe及不可避免杂质。
48.所述桥梁钢的制造工序如下:原料通过冶炼得到钢水,钢水上板坯连铸,铸坯厚度为260mm,连铸坯堆冷60小时,把坯料在1160℃下均热,温度均匀性小于15℃,加热234min后进行除磷,随后进行两阶段轧制,再结晶区轧制温度为1160℃,总变形量为49%,中间坯厚度控制在成品厚度2.2倍,未再结晶区轧制开轧温度为810℃,达到最终产品厚度60mm,终轧温度为810℃。终轧后进行层流冷却,返红温度为50℃,而后空气中冷却至室温,然后对钢板进行离线回火,回火温度在380℃,并在此温度下保温180min,随后自然冷却至室温。
49.对比例1
50.与实施例3不同的地方在于:桥梁钢成分中ni含量为0.70%,mo含量为0.30%。
51.对比例2
52.与实施例4不同的地方在于:桥梁钢成分中ni含量为0.75%,mo含量为0.33%。
53.对实施例1-实施例4及对比例1、对比例2得到的试样进行金相组织观察及性能测试,见表1。
54.表1
[0055] 实施例1实施例2实施例3实施例4对比例1对比例2耐大气腐蚀指数7.77.57.38.17.17.3屈服强度/mpa725760735720693648抗拉强度/mpa856871866854825781屈强比0.850.870.850.840.840.83-40℃akv/j26122422326610878纤维断面率/%959590906040延伸率/%16.51617.51818.018.5
再多了解一些
本文用于企业家、创业者技术爱好者查询,结果仅供参考。