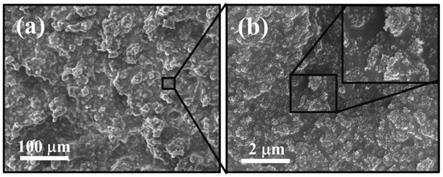
1.本发明涉及一种耐久性多功能仿生超疏水涂层及其制备方法,属于涂层材料设计与制造技术领域。
背景技术:
2.自然界许多生物表面都具备优异的界面润湿特性,其静态水滴接触角大于150
°
,滚动角小于10
°
,这种对水滴表现出非浸润状态的表面被称为超疏水表面,典型代表有:荷叶、水稻叶、水黾腿、蝴蝶翅膀和沙漠甲虫等。科研人员深入研究发现:此类生物表面均具有微-纳多级复合结构,微-纳多级结构能够储存大量空气,从而形成空气层,大幅降低水滴与固体表面之间的接触面积;综合生物表面独特的成分,使得水滴在其表面保持球型无法铺展,并极易在较小的倾斜角度下滚落。因此,研究人员指出:低表面能的化学成分和适宜的微-纳多级复合结构是实现超疏水特性的两个关键性因素。受此启发,仿生超疏水涂层的设计制备引起了科技工作者的广泛关注。仿生超疏水涂层优异的界面润湿特性,使其在自清洁、抗结冰、抗腐蚀、集水、减阻等诸多领域具有广阔的应用前景。
3.超疏水涂层的物理-化学稳定性主要取决于涂层成膜物质的耐磨性、涂层与金属基底的附着力以及涂层抗化学侵蚀稳定性。然而,超疏水涂层在实际应用过程中通常会遭受机械外力作用,导致超疏水涂层表面微-纳多级结构极易发生破碎或脱落;此外,超疏水涂层材料在真实气候中通常会面临强酸强碱、雨水冲刷及海水腐蚀等严苛化学环境的挑战,致使超疏水涂层发生损伤失效,这是超疏水涂层工业应用的重要障碍之一。
4.随着纳米加工制造技术的深入发展,仿生超疏水涂层的制备技术层出不穷,例如自组装、模板法、相分离法、激光加工、静电纺丝和溶胶-凝胶法等。上述技术手段存在制备工艺复杂、材料设备昂贵、难以大规模工业生产等实际问题;同时低表面能氟硅烷的引入,会给环境带来严峻的挑战。
5.目前,现有关于超疏水涂层的制备技术手段主要包括:
6.cn 107880770 b公开了一种环保多功能超疏水涂层的制备方法。其制备方法主要包括制备纳米二氧化钛粉末、异氰酸十八酯改性纳米二氧化钛粉末、硅树脂与改性纳米二氧化钛粉末混合制备疏水涂料,并利用喷涂或刷涂的方法制备超疏水涂层。由于该方法填料成分的单一性,使得超疏水涂层仅能承受100g砝码压力下砂纸摩擦100cm的距离。
7.cn 110172292 b公开一种机械耐久的超疏水纳米涂层及其制备方法。其制备方法包括树脂浆料的制备、涂覆树脂浆料ⅱ的基板制备和浸渍树脂浆料ⅰ的纳米纤维膜制备、将经过浸渍的纳米纤维膜叠置在涂覆有树脂浆料ⅱ的基板上,加热固化后获得机械耐久的超疏水纳米涂层。由于纳米纤维膜尺寸和叠置方法的影响,导致该方法不适宜在工业生产中大面积的制备耐久性超疏水涂层。
8.cn 111621049 a公开了一种强耐久性超疏水涂层及其制备方法。其利用多巴胺混合溶液涂覆在pvc基材表面自聚合形成聚多巴胺作为粘结层;再将烷基硫醇或月桂酸或硬脂酸改性的纳米二氧化硅、纳米氧化铝和纳米二氧化钛涂覆在含有聚多巴胺粘结层的pvc
基材表面;最后进行清洗、干燥得到强耐久性超疏水涂层。由于低表面能改性剂的原因,该耐久性超疏水涂层表面润湿性未表现出对非机械损伤的可修复性。
9.cn 113122040 a公开了一种具有机械稳定性的多功能超疏水涂层的制备方法。该方法首先利用水热合成、离心干燥制得具有特殊形貌的氧化锌,其次利用十三氟辛基三乙氧基硅烷将上述方法所得的氧化锌粒子进行疏水改性,最后与按一定比例混合的正己烷、聚二甲基硅氧烷、无水乙醇溶液混合,喷涂制备超疏水复合涂层。由于该方法所制备的氧化锌形貌为非片层状,如应用到腐蚀防护方向,可能不利于抵抗侵蚀介质的渗透、不具有长效腐蚀防护效果。
10.因此,亟需开发一种简便、环保、并且能够大面积生产的仿生超疏水涂层制备技术;同时,超疏水涂层应兼具机械耐久性、化学稳定性、可修复性、耐腐蚀性等优异的多功能特性。耐久性仿生多功能超疏水涂层的研发是提高工程材料表面性能和应用领域的关键,能够为工程材料实现其结构功能一体化提供技术支撑。
技术实现要素:
11.为克服现有技术存在的缺陷,本发明的目的之一在于提供一种耐久性多功能仿生超疏水涂层。
12.本发明的目的之二在于提供一种耐久性多功能仿生超疏水涂层的制备方法。
13.为实现本发明的目的,提供以下技术方案。
14.一种耐久性多功能仿生超疏水涂层,以所述涂层组成成分的总体质量为100%计,其中,各原料组分及其质量分数如下:
[0015][0016]
优选改性氧化石墨烯(go)和改性云母(mp)的质量分数不为0.0%。
[0017]
所述改性sio2纳米颗粒为将sio2纳米颗粒分散于甲苯中,再加入三氯十八烷基硅烷(ots),加热、搅拌得到悬浊液;最后将悬浊液干燥,得到改性sio2纳米颗粒。所述sio2纳米颗粒和甲苯的质量比为1:35~1:20,优选1:28;sio2纳米颗粒与ots质量比为4:1~2:1,优选1:3。
[0018]
优选的,所述加热温度为30℃~90℃。
[0019]
优选的,所述干燥的温度为50℃~100℃,所述干燥的时间为4h~8h。
[0020]
所述改性go为将go分散于无水乙醇中,再加入三氯十八烷基硅烷(ots),加热、搅拌得到悬浊液;最后将悬浊液干燥,得到改性go。所述go和无水乙醇的质量比为1:180~1:150,优选1:160;go与ots质量比为1:3~1:1,优选1:2。
[0021]
优选的,所述加热温度为30℃~90℃。
[0022]
优选的,所述干燥的温度为50℃~100℃,所述干燥的时间为4h~8h。
[0023]
所述改性mp为将mp粉分散于甲苯中,再加入三氯十八烷基硅烷(ots),加热、搅拌得到悬浊液;最后将悬浊干燥,得到改性mp。所述mp和甲苯的质量比为1:20~1:40,优选1:30;mp与ots质量比为4:1~2:1,优选3:1。
[0024]
优选的,所述加热温度为30℃~90℃。
[0025]
优选的,所述干燥的温度为50℃~100℃,所述干燥的时间为4h~8h。
[0026]
由上述改性sio2纳米颗粒、改性go和改性mp组成填料,所述填料与msr质量比为1:3.3~1:2.4,所述固化剂与msr的质量比为1:4.7~1:5.8;所述msr与有机溶剂的质量比为1:1.7~1:2。
[0027]
优选的,所述固化剂为n75。
[0028]
优选的,所述有机溶剂为甲苯或乙酸乙酯。
[0029]
一种本发明所述的耐久性多功能仿生超疏水涂层的制备方法,所述方法步骤如下:
[0030]
(1)将环氧改性有机硅树脂完全溶解于有机溶剂中,分别加入改性sio2纳米颗粒,改性go和改性mp,超声分散均匀,加入固化剂,搅拌均匀,得到悬浊液。
[0031]
优选的,所述搅拌时间为1h~3h。
[0032]
(2)将步骤(1)制备的悬浊液喷涂在基体材料上得到一种耐久性多功能仿生超疏水涂层。
[0033]
具体为:将步骤(1)制备的悬浊液倾倒入喷枪中,采用压缩空气喷涂法喷涂在基体上,干燥,固化,在基体材料上得到耐久性多功能仿生超疏水涂层。
[0034]
喷涂参数为:喷枪的喷嘴直径为1.5mm;喷涂压力为0.6mpa~0.8mpa压缩空气;喷涂过程中控制喷枪喷嘴与基材的距离为20cm~30cm;喷涂时间为20s~30s。
[0035]
固化时间为2h~4h;固化温度为100℃~140℃。
[0036]
所述基体材料为镁合金薄片、铜泡沫或玻璃片,优选镁合金薄片;
[0037]
优选的,所述基体材料表面可以进行预处理,所述预处理为超声清洗和/或砂纸打磨,所述超声清洗时间均为10min;所述砂纸为1000#和2000#sic砂纸中的至少一种。
[0038]
有益效果
[0039]
1.本发明提供了一种耐久性多功能仿生超疏水涂层,所述涂层添加了质量分数为8.6%~9.3%的表面接枝了低表面能官能团的改性sio2纳米颗粒,化学改性可以有效减少sio2纳米颗粒团聚现象,进一步降低涂层的表面能,保证涂层的致密性及超疏水特性。所述涂层表现出优异的超疏水低黏附特性,水滴接触角为163.8
°
,滑动角为3.5
°
,微液滴黏附力仅为12.6
±
0.5μn。
[0040]
2.本发明提供了一种耐久性多功能仿生超疏水涂层,所述涂层通过引入go和mp延缓侵蚀介质在涂层内部的渗透扩散,展现出良好的长效腐蚀防护稳定性,揭示了复合涂层较长时间抵抗腐蚀介质微观侵蚀机制。针对工程实际应用需求,拓展了界面润湿性在工程领域的应用,提出仿生复合结构、组织形态多因素耦合腐蚀防护新机制。
[0041]
3.本发明提供了一种耐久性多功能仿生超疏水涂层,所述涂层通过调节表面改性填料(sio2、go和mp)与树脂(msr)之间的比例得到多功能特性:超疏水涂层能够抵抗-196℃和200℃之间多次高低温交替循环变化;并且展现出优异的抗砂纸摩擦性能,当满足疏水性
的表面微-纳多级结构摩擦受损后,砂纸打磨后重新暴露的粗糙结构依然能够满足超疏水低黏附特性;同时超疏水涂层对强酸、强碱、盐溶液及紫外光照射等条件均具有较长的抵抗能力。
[0042]
4.本发明提供了一种耐久性多功能仿生超疏水涂层,所述涂层添加低表面能改性二氧化硅纳米颗粒后,由于加热时低表面能疏水碳氢链向上迁移,并在涂层表面堆积,因此使涂层表现出优异的抗o2等离子体侵蚀的可修复能力,并且即使在机械损伤后,在空气和油中同样展现出优异的自清洁性能。
[0043]
5.本发明提供了一种耐久性多功能仿生超疏水涂层,所述涂层用ots替代了传统工艺中低表面能氟硅烷,涂层成分绿色环保。
[0044]
6.本发明提供了一种耐久性多功能仿生超疏水涂层的制备方法,所述方法工艺操作简便、实验参数可控且设备、原料价格成本低廉,适用于多种基体材料,适合大规模生产和工业应用。
附图说明
[0045]
图1为实施例1制备得到的耐久性多功能仿生超疏水涂层接触角(ca)测试图和滚动角(sa)测试图。
[0046]
图2为实施例2制备得到的耐久性多功能仿生超疏水涂层表面微观形貌。
[0047]
图3为实施例3制备得到的耐久性多功能仿生超疏水涂层抵抗高低温转变测试循环次数及润湿性变化。
[0048]
图4为实施例3制备得到的耐久性多功能仿生超疏水涂层抵抗高低温转变测试循环测试后表面微观形貌。
[0049]
图5为实施例3制备得到的耐久性多功能仿生超疏水涂层在100g载荷条件下在1000#砂纸上经过24次砂纸摩擦循环测试后表面润湿性和表面微观形貌。
[0050]
图6为实施例1~4制备得到的耐久性多功能仿生超疏水涂层在紫外光照射7天、3.5wt.%nacl溶液浸泡7天、ph=1的强酸和ph=14的强碱分别浸泡14h条件下表面润湿性变化。
[0051]
图7为实施例4制备得到的耐久性多功能仿生超疏水涂层的o2等离子体刻蚀和加热自修复循环次数。
[0052]
图8为实施例4制备得到的耐久性多功能仿生超疏水涂层表面经过小刀刻划和多次强力胶带剥离后在油中的自清洁行为。
[0053]
图9为实施例3制备得到的耐久性多功能仿生超疏水涂层、镁合金基体和实施例5制备的msr@sio2超疏水涂层在3.5wt.%nacl溶液中浸泡21天后的动电位极化曲线。
具体实施方式
[0054]
下面结合附图和具体实施例来详述本发明,但不作为对本发明专利的限定。对以下实施例中制备得到的耐久性多功能仿生超疏水涂层进行检测如下:
[0055]
(1)表面湿润性和表面黏附力定量测量:接触角测量仪,型号:dsa 255,germany;高灵敏度微机电平衡系统,型号:dcat11。
[0056]
(2)微观形貌表征:场发射扫描电子显微镜,型号:jsm-6700f,jeol,japan。
[0057]
(3)抗高低温转变性能进行测试:将所述涂层在液氮浸泡10min,随后在加热板200℃下加热10min,记录涂层表面润湿性并观察测试后涂层表面形貌。
[0058]
(4)耐摩擦性能测试:将涂有仿生超疏水涂层的镁板与1000#砂纸接触,并在100g重量的外载下沿水平往复摩擦,摩擦距离1m定义为一个循环,每一个磨损循环后记录cas和sas,并观察涂层最终摩擦后的微观形貌。
[0059]
(5)耐酸碱、盐溶液、抗紫外光照射性能进行测试:将涂覆超疏水涂层的4个样品密封好,其中2个样品分别浸泡在ph=1的强酸溶液、ph=14的强碱溶液,每隔2个小时测量涂层表面的接触角和滚动角;还有2个样品暴露在3.5wt.%nacl溶液和紫外线光照射下,每隔1天测量涂层表面的接触角和滚动角。
[0060]
(6)非机械损伤可修复性能测试:o2等离子刻蚀机:型号:diener electronic,germany。
[0061]
(7)自清洁性能测试:将仿生超疏水涂层经过小刀水平、垂直刻划和50次强力胶带剥离试验后,在十二烷中的自清洁性能测试。
[0062]
(8)动电位极化曲线进行测试:电化学工作站:型号:gamry reference 600。将仿生超疏水涂层样品及基体在3.5wt%nacl溶液中浸泡21天,对其动电位极化曲线进行测试。
[0063]
实施例1
[0064]
一种耐久性多功能仿生超疏水涂层,以所述涂层组成成分的总体质量为100%计,其中,各原料组分及其质量分数如下:
[0065][0066]
所述改性sio2纳米颗粒为将3.6g sio2纳米颗粒分散于100g甲苯中,再加入1.2g ots,60℃加热、搅拌得到悬浊液;最后将悬浊液转入鼓风炉中80℃干燥6h,得到改性sio2纳米颗粒。其中,所述sio2纳米颗粒和甲苯的质量比为1:28,sio2纳米颗粒与ots质量比为3:1。
[0067]
所述改性go为将0.5g go分散于80g无水乙醇中,再加入1.0g ots,60℃加热、搅拌得到悬浊液;最后将悬浊液转入鼓风炉中干燥80℃干燥6h,得到改性go。其中,所述go和无水乙醇的质量比为1:160,go与ots质量比为1:2。
[0068]
所述改性mp为将3g mp粉分散于90g甲苯溶剂中,再加入1.0g ots,60℃加热、搅拌得到悬浊液;最后将悬浊液转入鼓风炉中干燥80℃干燥6h,得到改性mp。其中,所述mp和甲苯的质量比为1:30,mp与ots质量比为3:1。
[0069]
由上述改性sio2纳米颗粒、改性氧化石墨烯(go)、改性云母(mp)组成的填料与msr质量比为1:3.3,所述固化剂n75与msr的质量比为1:5;所述msr与甲苯的质量比为1:2。
[0070]
一种本实施例所述耐久性多功能仿生超疏水涂层的制备方法,所述方法步骤如下:
[0071]
(1)将5g环氧改性有机硅树脂完全溶解于10g有机溶剂中,分别加入1.5g改性sio2纳米颗粒,0g改性go和0g改性mp,超声分散均匀,加入1.0g n75,再次超声分散均匀,搅拌2h,得到msr@sio2悬浊液。
[0072]
(2)再将msr@sio2悬浊液喷涂在玻璃片上得到一种耐久性多功能仿生超疏水涂层。
[0073]
具体为:将步骤(1)制备的msr@sio2悬浊液倾倒入喷枪中,采用压缩空气喷涂法喷涂在玻璃片上,干燥,固化,在基体上得到耐久性多功能仿生超疏水涂层。
[0074]
喷涂参数为:喷枪的喷嘴直径为1.5mm;喷涂压力为0.6mpa压缩空气;喷涂过程中控制喷枪喷嘴与基材的距离为20cm;喷涂时间为20s。
[0075]
固化时间为4h;固化温度为100℃。
[0076]
实施例2
[0077]
一种耐久性多功能仿生超疏水涂层,以所述涂层组成成分的总体质量为100%计,其中,各原料组分及其质量分数如下:
[0078][0079]
所述改性sio2纳米颗粒为将3.6g sio2纳米颗粒分散于100g甲苯中,再加入1.2g ots,60℃加热、搅拌得到悬浊液;最后将悬浊液转入鼓风炉中80℃干燥6h,得到改性sio2纳米颗粒。其中,所述sio2纳米颗粒和甲苯的质量比为1:28,sio2纳米颗粒与ots质量比为3:1。
[0080]
所述改性go为将0.5g go分散于80g无水乙醇中,再加入1.0g ots,60℃加热、搅拌得到悬浊液;最后将悬浊液转入鼓风炉中干燥80℃干燥6h,得到改性go。其中,所述go和无水乙醇的质量比为1:160,go与ots质量比为1:2。
[0081]
所述改性mp为将3g mp粉分散于90g甲苯溶剂中,再加入1.0g ots,60℃加热、搅拌得到悬浊液;最后将悬浊液转入鼓风炉中干燥80℃干燥6h,得到改性mp。其中,所述mp和甲苯的质量比为1:30,mp与ots质量比为3:1。
[0082]
由上述改性sio2纳米颗粒、改性氧化石墨烯(go)、改性云母(mp)组成的填料与msr质量比为1:2.8,所述固化剂n75与msr的质量比为1:5.8;所述msr与甲苯的质量比为1:1.7。
[0083]
一种本实施例所述耐久性多功能仿生超疏水涂层的制备方法,所述方法步骤如下:
[0084]
(1)将7g环氧改性有机硅树脂(msr)完全溶解于12g有机溶剂中,分别加入2g改性sio2纳米颗粒,0.03g改性go和0.5g改性mp,超声分散均匀,加入1.2g n75,再次超声分散均匀,搅拌2h,得到msr@sio2 go mp悬浊液。
[0085]
(2)再将msr@sio2 go mp悬浊液喷涂在铜泡沫上得到一种耐久性多功能仿生超疏水涂层。
[0086]
具体为:将步骤(1)制备的msr@sio2 go mp悬浊液倾倒入喷枪中,采用压缩空气喷涂法喷涂在铜泡沫上,干燥,固化,在基体上得到耐久性多功能仿生超疏水涂层。
[0087]
喷涂参数为:喷枪的喷嘴直径为1.5mm;喷涂压力为0.7mpa压缩空气;喷涂过程中控制喷枪喷嘴与基材的距离为20cm;喷涂时间为20s。
[0088]
固化时间为2h;固化温度为120℃。
[0089]
实施例3
[0090]
一种耐久性多功能仿生超疏水涂层,以所述涂层组成成分的总体质量为100%计,其中,各原料组分及其质量分数如下:
[0091][0092]
所述改性sio2纳米颗粒为将3.6g sio2纳米颗粒分散于100g甲苯中,再加入1.2g ots,60℃加热、搅拌得到悬浊液;最后将悬浊液转入鼓风炉中80℃干燥6h,得到改性sio2纳米颗粒。其中,所述sio2纳米颗粒和甲苯的质量比为1:28,sio2纳米颗粒与ots质量比为3:1。
[0093]
所述改性go为将0.5g go分散于80g无水乙醇中,再加入1.0g ots,60℃加热、搅拌得到悬浊液;最后将悬浊液转入鼓风炉中干燥80℃干燥6h,得到改性go。其中,所述go和无水乙醇的质量比为1:160,go与ots质量比为1:2。
[0094]
所述改性mp为将3g mp粉分散于90g甲苯溶剂中,再加入1.0g ots,60℃加热、搅拌得到悬浊液;最后将悬浊液转入鼓风炉中干燥80℃干燥6h,得到改性mp。其中,所述mp和甲苯的质量比为1:30,mp与ots质量比为3:1。
[0095]
由上述改性sio2纳米颗粒、改性氧化石墨烯(go)、改性云母(mp)组成的填料与msr质量比为1:2.5,所述固化剂n75与msr的质量比为1:4.7;所述msr与乙酸乙酯的质量比为1:1.7。
[0096]
一种本实施例所述耐久性多功能仿生超疏水涂层的制备方法,所述方法步骤如下:
[0097]
(1)将7g环氧改性有机硅树脂(msr)完全溶解于12g有机溶剂中,分别加入2g改性sio2纳米颗粒,0.03g改性go和0.8g改性mp,超声分散均匀,加入1.5g n75,再次超声分散均匀,搅拌2h,得到msr@sio2 go mp悬浊液。
[0098]
(2)再将msr@sio2 go mp悬浊液喷涂在az31镁合金薄板上得到一种耐久性多功能仿生超疏水涂层。
[0099]
具体为:将步骤(1)制备的msr@sio2 go mp悬浊液倾倒入喷枪中,采用压缩空气喷涂法喷涂在az31镁合金薄板上,干燥,固化,在基体上得到耐久性多功能仿生超疏水涂层。
[0100]
喷涂参数为:喷枪的喷嘴直径为1.5mm;喷涂压力为0.8mpa压缩空气;喷涂过程中控制喷枪喷嘴与基材的距离为30cm;喷涂时间为30s。
[0101]
固化时间为3h;固化温度为120℃。
[0102]
实施例4
[0103]
一种耐久性多功能仿生超疏水涂层,以所述涂层组成成分的总体质量为100%计,其中,各原料组分及其质量分数如下:
[0104][0105]
所述改性sio2纳米颗粒为将3.6g sio2纳米颗粒分散于100g甲苯中,再加入1.2g ots,60℃加热、搅拌得到悬浊液;最后将悬浊液转入鼓风炉中80℃干燥6h,得到改性sio2纳米颗粒。其中,所述sio2纳米颗粒和甲苯的质量比为1:28,sio2纳米颗粒与ots质量比为3:1。
[0106]
所述改性go为将0.5g go分散于80g无水乙醇中,再加入1.0g ots,60℃加热、搅拌得到悬浊液;最后将悬浊液转入鼓风炉中干燥80℃干燥6h,得到改性go。其中,所述go和无水乙醇的质量比为1:160,go与ots质量比为1:2。
[0107]
所述改性mp为将3g mp粉分散于90g甲苯溶剂中,再加入1.0g ots,60℃加热、搅拌得到悬浊液;最后将悬浊液转入鼓风炉中干燥80℃干燥6h,得到改性mp。其中,所述mp和甲苯的质量比为1:30,mp与ots质量比为3:1。
[0108]
由上述改性sio2纳米颗粒、改性氧化石墨烯(go)、改性云母(mp)组成的填料与msr质量比为1:2.4,所述固化剂n75与msr的质量比为1:5.3;所述msr与乙酸乙酯的质量比为1:1.75。
[0109]
一种本实施例所述耐久性多功能仿生超疏水涂层的制备方法,所述方法步骤如下:
[0110]
(1)将8g环氧改性有机硅树脂(msr)完全溶解于14g有机溶剂中,分别加入2.5g改性纳米sio2纳米颗粒,0.03g改性go和0.8g改性mp,超声分散均匀,加入1.5g n75,再次超声分散均匀,搅拌2h,得到msr@sio2 go mp悬浊液。
[0111]
(2)再将msr@sio2 go mp悬浊液喷涂在az31镁合金薄板上得到一种耐久性多功能仿生超疏水涂层。
[0112]
具体为:将步骤(1)制备的msr@sio2 go mp悬浊液倾倒入喷枪中,采用压缩空气喷涂法喷涂在az31镁合金薄板上,干燥,固化,在基体上得到耐久性多功能仿生超疏水涂层。
[0113]
喷涂参数为:喷枪的喷嘴直径为1.5mm;喷涂压力为0.8mpa压缩空气;喷涂过程中控制喷枪喷嘴与基材的距离为30cm;喷涂时间为30s。
[0114]
固化时间为2h;固化温度为140℃。
[0115]
为了对比研究改性氧化石墨烯和改性云母对涂层的长效腐蚀性能的影响,改变填料成分,制备了实施例5。实施例5只添加了与实施例3质量相同的改性sio2纳米颗粒,未添加改性氧化石墨烯和改性云母,其余步骤均与实施例3保持一致,最终制备得到超疏水涂层
样品(msr@sio2)。
[0116]
实施例5
[0117]
一种耐久性多功能仿生超疏水涂层,以所述涂层组成成分的总体质量为100%计,其中,各原料组分及其质量分数如下:
[0118][0119]
所述改性sio2纳米颗粒的制备过程与实施例3保持一致;所述固化剂n75与msr的质量比为1:4.7;所述msr与乙酸乙酯的质量比为1:1.7。
[0120]
一种本实施例所述耐久性多功能仿生超疏水涂层的制备方法,所述方法步骤如下:
[0121]
(1)将7g环氧改性有机硅树脂(msr)完全溶解于12g有机溶剂中,分别加入2g改性sio2纳米颗粒,超声分散均匀,加入1.5g n75,再次超声分散均匀,搅拌2h,得到msr@sio2悬浊液。
[0122]
(2)再将msr@sio2悬浊液喷涂在az31镁合金薄板上得到一种耐久性多功能仿生超疏水涂层。
[0123]
具体步骤和喷涂参数与实施例3保持一致。
[0124]
实施例1~5的测试及结果如下:
[0125]
(1)表面湿润性和表面黏附力定量测量:
[0126]
对实施例1制备得到的耐久性多功能仿生超疏水涂层表面润湿性进行测试,结果如图1所示,水滴接触角(ca)为163.8
°
,滑动角(sa)为3.5
°
,微液滴黏附力约为12.6
±
0.5μn。
[0127]
实施例2仿生超疏水涂层表面ca为162.5
°
,sa为3.9
°
,微液滴黏附力约为13.4
±
0.6μn。
[0128]
实施例3仿生超疏水涂层表面ca为162.9
°
,sa为3.3
°
,微液滴黏附力约为12.4
±
0.4μn。
[0129]
实施例4仿生超疏水涂层表面ca为163.2
°
,sa为4.0
°
,微液滴黏附力约为13.7
±
0.6μn。
[0130]
说明实施例1~4制备的涂层表现出优异的超疏水低黏附特性。
[0131]
(2)微观形貌表征:
[0132]
实施例2制备得到的耐久性多功能仿生超疏水涂层表面形貌表征结果如图2所示,所制备的仿生超疏水涂层表面形成了均匀致密的多尺度微-纳层级复合结构,其中图(a)的标尺100μm,图(b)的标尺为2μm。
[0133]
实施例1、3、4涂层样品表面微观形貌测试结果与实施例2相似。
[0134]
(3)抗高低温转变性能进行测试:
[0135]
对实施例3制备得到的耐久性多功能仿生超疏水涂层进行耐高低温测试,结果如图3所示,本实施例所述涂层能够抵抗-196℃和200℃之间多次循环交替变化,12次循环测试后涂层表面水滴接触角依然接近160
°
,且滚动角小于6
°
;并且12次循环交替测试后涂层表面微观形貌未发生明显变化,未产生裂缝,如图4所示。
[0136]
实施例1、2、4制备的仿生超疏水涂层3个样品经过相同的耐高低温测试循环后水滴接触角同样在160
°
左右,并且滚动角小于6
°
。
[0137]
(4)耐摩擦性能测试:
[0138]
实施例3制备得到的耐久性多功能仿生超疏水涂层在100g载荷条件下,1000#砂纸上经过24次砂纸摩擦循环测试后表面润湿性如图5a所示,表面微观形貌如图5b所示:可以看出,仿生超疏水涂层具有优异的耐机械摩擦性能,当总摩擦距离达24m后,涂层仍然满足超疏水低粘附特性,即接触角163.3
°
,滚动角4.2
°
。
[0139]
实施例1、2、4制备的仿生超疏水涂层3个样品经过总摩擦距离24m后,水滴接触角分别为162.8
°
、163.1
°
、162.4
°
;水滴滚动角分别为4.5
°
、3.9
°
、4.0
°
。
[0140]
(5)耐酸碱、盐溶液、抗紫外光照射性能测试:实施例1~4制备的耐久性多功能仿生超疏水涂层抗紫外、耐酸碱和盐溶液测试结果如图6所示,(a)抗耐紫外线测试结果;(b)耐3.5%nacl盐溶液测试结果;(c)ph=1时耐强酸性能测试结果;(d)ph=14时耐强碱性能测试结果;4种条件下测试后涂层的水滴接触角均大于160
°
,且滚动角小于8
°
。结果表明:制备的仿生超疏水涂层对强酸、强碱、盐溶液及紫外光照射均具有较长的抵抗能力。
[0141]
(6)非机械损伤可修复性能测试:实施例4制备的耐久性多功能仿生超疏水涂层表现出优异的抗o2等离子体侵蚀的可修复能力;o2等离子体侵蚀后超疏水涂层转变为超亲水状态,接触角为0
°
;在180℃温度下,加热10min,又恢复涂层超疏水特性,接触角高于160
°
,循环次数可达16次,如图7所示。
[0142]
实施例1~3制备的仿生超疏水涂层样品的非机械损伤可修复性能同样均可达到16次,恢复疏水性后表面接触角能够达到160左右
°
。
[0143]
(7)自清洁性能测试:实施例4制备的耐久性多功能仿生超疏水涂层经小刀水平、垂直刻划和50次强力胶带剥离试验后,在十二烷油环境,图(a)为静置6s;图(b)为静置12s;图(c)为静置21s;图(d)为静置66s;涂层表面的污染物颗粒能够在水滴自然滚落情况下被清除,表明制备的超疏水涂层即使在机械损伤后,在油中同样展现出优异的自清洁性能,如图8所示。
[0144]
实施例1~3制备的耐久性多功能仿生超疏水涂层在十二烷油环境中同样表现出良好的自清洁性能。
[0145]
(8)动电位极化曲线进行测试:
[0146]
实施例3制备得到的耐久性多功能仿生超疏水涂层及镁基体的动电位极化曲线如图9所示。可以看出:制备的仿生超疏水涂层(msr@sio2 go mp)与镁合金基体(mg alloy substrate)相比,腐蚀电流密度(i
coor
)降低了5个数量级,腐蚀电势(e
corr
)向正向移动了0.38v;当仿生超疏水涂层样品浸泡21天后(immersion for 21days),防腐性能仍然高于实施例5制备的超疏水涂层(msr@sio2)。表明制备的超疏水涂层具有优异的防腐性能,在恶劣的腐蚀环境中具有长期的腐蚀防护稳定性,且三种填料组分组成仿生超疏水涂层性能更好。
再多了解一些
本文用于企业家、创业者技术爱好者查询,结果仅供参考。