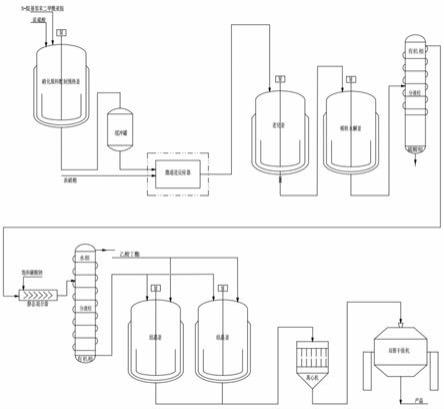
一种n-烷基-硝基邻苯二甲酰亚胺的连续化工业生产方法
技术领域
1.本发明涉及化工技术领域,具体涉及一种n-烷基-硝基邻苯二甲酰亚胺的连续化工业生产方法。
背景技术:
2.n-烷基-硝基邻苯二甲酰亚胺是一种重要的化工中间体,其在化工、医疗、染料等行业具有非常重要的地位。其结构如式ⅰ所示:
ꢀꢀꢀꢀꢀ
式ⅰ其中,r可以为甲基、乙基、正丙基、异丙基、丁基、异丁基、戊基等烷基基团。
3.目前,制备n-烷基-硝基邻苯二甲酰亚胺的方法一般是以n-烷基邻苯二甲酰亚胺为反应原料,在硝化试剂及催化剂、脱水剂的存在下进行反应。中国专利申请cn104086476a公开了一种4-硝基-n-甲基邻苯二甲酰亚胺的制备方法,先将发烟硝酸冷却到5℃~10℃,然后滴加计量比的浓硫酸,在10℃~15℃配成混酸;在0℃将n-甲基邻苯二甲酰亚胺与浓硫酸搅拌溶解,再滴加混酸,反应3~4h,用有机萃取剂萃取反应中的硝化物,分层后分离上层有机相和下层硫酸溶液;回收上层有机相,得4-硝基-n-甲基邻苯二甲酰亚胺,离心过滤,干燥得成品。该制备方法采用滴加硝化剂的方式进行间歇反应,同传统的釜式硝化工艺相似,难以进行均匀的传质传热,且反应热量难以及时移除,易造成反应“飞温”,从而引发安全事故,不再适宜现在化工环境下的工业化生产。
4.近年来,微通道反应器在硝化反应中的应用越来越广,与常规的釜式反应器相比,微通道反应器具有持液量小、安全、对物料加热和移热反应快速、物料混合均匀等优点。中国专利申请cn109305933a公开了一种制备n-烷基-4-硝基邻苯二甲酰亚胺的方法,其采用不同结构的微通道反应器进行n-烷基邻苯二甲酰亚胺的硝化反应,反应结束后进行冷却、水洗、过滤收集、干燥等后处理操作,制备得到n-甲基-4-硝基邻苯二甲酰亚胺。然而,该制备方法仅在硝化反应过程实现了连续化,在后续对产物的提取过程仍然为传统间歇式后处理的方式,最终得到的产物纯度低,不能满足后续反应对纯度的要求,需再进一步提纯才能用于下步反应;且其后处理采用水洗方式,会产生大量的酸性废液,回收时耗费更多的能源,会带来生产成本的提高;另外,间歇式生产过程难以稳定控制最终产品质量,是目前传统工业化生产中所面临的问题。
技术实现要素:
5.为了克服上述现有技术存在的不足,本发明目的在于,提供一种n-烷基-硝基邻苯二甲酰亚胺的连续化工业生产方法,反应收率高、产品纯度高,且产品质量稳定、可控。
6.本发明是通过以下技术方案实现的:
一种n-烷基-硝基邻苯二甲酰亚胺的连续化工业生产方法,包括以下步骤:(1)原料预处理;(2)连续硝化;(3)老化;(4)稀释分层;(5)中和分层;(6)结晶、分离、干燥;所述的原料预处理、连续硝化、老化、稀释分层、中和分层、结晶、分离、干燥的整个生产操作过程是动态连续进行的;所述步骤(1)原料预处理为按一定比例将n-烷基邻苯二甲酰亚胺加入硫酸中,混合溶解后,得到n-烷基邻苯二甲酰亚胺硫酸溶液;其中,n-烷基邻苯二甲酰亚胺与硫酸的摩尔比为1:1~1:10;预处理温度为0℃~100℃;所述步骤(2)连续硝化为将预处理后的n-烷基邻苯二甲酰亚胺硫酸溶液和硝酸按一定比例连续泵入微通道反应器中混合进行硝化反应;其中,n-烷基邻苯二甲酰亚胺和硝酸的摩尔比为1:1~1:10;反应温度为30℃~95℃;n-烷基邻苯二甲酰亚胺硫酸溶液和硝酸在微通道反应器中的混合停留时间为5s~500s;所述步骤(3)老化为经微通道反应器流出的硝化完成的物料连续泵入老化反应器中进行老化,控制老化温度为30℃~200℃,老化完成的物料不间断流出老化反应器,在老化反应器中的停留时间控制在10min~600min;所述步骤(4)稀释分层为经老化反应器流出的物料连续泵入稀释水解反应器中,同时按比例连续泵入纯水,与物料混合将硫酸浓度稀释至10%~85%进行水解,水解完成的物料不间断进入第一分液器中分层,形成上层有机相和下层酸液,上层有机相不间断地从第一分液器流出;其中,控制稀释水解反应器和第一分液器内的温度为20℃~100℃;所述步骤(5)中和分层为经第一分液器流出的上层有机相连续泵入中和反应器中,同时按比例连续泵入碱性料液,与有机相混合将体系的ph调至6~8,中和完成的物料连续进入第二分液器中分层,形成上层废水层和下层有机相,下层有机相不间断地从第二分液器流出;其中,控制中和反应器和第二分液器内的温度为20℃~100℃;所述步骤(6)结晶、分离、干燥为在结晶釜中加入结晶溶剂,经第二分液器流出的下层有机相连续泵入结晶釜中,降温结晶后,进行固液分离,将得到的固体进行干燥,制得n-烷基-硝基邻苯二甲酰亚胺。
7.本发明所采用的原料n-烷基邻苯二甲酰亚胺的烷基可选自1~10个碳原子烷基基团中的任意一种;具体的,所述n-烷基邻苯二甲酰亚胺可选自n-甲基邻苯二甲酰亚胺、n-乙基邻苯二甲酰亚胺、n-正丙基邻苯二甲酰亚胺、n-异丙基邻苯二甲酰亚胺、n-正丁基邻苯二甲酰亚胺、n-异丁基邻苯二甲酰亚胺、n-正戊基邻苯二甲酰亚胺或n-异戊基邻苯二甲酰亚胺中的任意一种。
8.本发明步骤(1)原料预处理中所述的硫酸为质量浓度大于90%的浓硫酸,步骤(2)连续硝化中所述的硝酸的质量浓度大于90%的浓硝酸。
9.所述步骤(2)连续硝化中n-烷基邻苯二甲酰亚胺和硝酸的摩尔比优选为1:1.05~1:2。
10.本发明采用微通道反应器进行n-烷基邻苯二甲酰亚胺的连续硝化反应,根据微通道反应器规格,通过控制原料泵入的速度,来控制n-烷基邻苯二甲酰亚胺硫酸溶液和硝酸在微通道反应器中的混合停留时间,混合停留时间过短硝化反应的转化率低,混合停留时间过长会使生产效率的降低。优选的,所述n-烷基邻苯二甲酰亚胺硫酸溶液和硝酸在微通道反应器中的混合停留时间为10s~100s。
11.微通道反应器能够精准的控制反应的温度在本发明要求范围内,温度太高会使反应副产物增加,且温度大于浓硝酸的沸点,使微通道反应器的压力增加,从而使设备的投资增大。
12.本发明在硝化反应后进行老化步骤,进一步使硝化反应充分,提高反应转化率。经微通道反应器完成硝化反应的物料直接连续泵入老化反应釜中进行老化,老化完成的物料会以溢流的方式不断流出老化反应釜,可以根据老化反应釜规格,通过控制物料泵入速度,来控制物料在老化反应器中的停留老化时间,以保证在动态连续生产过程中能够有效提高反应转化率。在要求的老化温度范围内,硝化反应能够达到较高的转化率,若温度过高,会使反应副产物增加,最终的目标产物转化率降低;优选的,控制老化温度为40℃~120℃。
13.本发明经研究发现,增加设置步骤(4)稀释分层,采用一定比例的纯水,将老化反应完成的物料中硫酸浓度稀释至≤85%,能够使目标产物从反应体系中水解析出,从而达到提纯目的;纯水比例越高越有利于目标产物的水解析出,但过多的水会产生大量废酸,增加酸液浓缩的能耗,提高成本;优选的,所述纯水与老化反应完成的物料比例为将硫酸浓度稀释至30%~60%,能够使目标产物析出更完全,又不会产生过多废酸。
14.通过将纯水与老化完成的物料按一定比例连续泵入稀释水解反应器中进行水解,水解完成的物料不断进入第一分液器后分层,上层为目标产物有机相,下层为废酸,根据分液器规格,控制进料速度,上层有机相会以溢流的方式不断流出分液器,使分液器中的分层维持在一个动态平衡,保证生产过程能够动态连续进行。收集下层废酸经浓缩后可再次使用。
15.步骤(5)中和分层中,通过使用碱性料液中和以更完全的除去目标产物中残留的酸液。所述的碱性料液选自ph大于7的碳酸钠溶液、碳酸氢钠溶液、碳酸钾溶液、碳酸氢钾溶液、氢氧化钠溶液、氢氧化钙溶液、甲胺溶液、乙胺溶液、乙二胺溶液或丙胺溶液中的任意一种。本发明提供一种优选操作方式,可以在中和反应器出口端设置ph计,将其与碱性料液的进料速度形成连锁控制,从而能够实现控制碱性料液的比例使得最终物料体系的ph在6~8。
16.通过将碱性料液与目标产物有机相按一定比例连续泵入中和反应器中进行中和反应,中和完成的物料不断进入第二分液器后分层,上层为废水层,下层为目标产物有机相,根据分液器规格,控制进料速度和下层有机相的出料速度,使分液器中的分层维持在一个动态平衡,保证生产过程能够动态连续进行。回收上层废水层。
17.本发明所述的老化反应器、稀释水解反应器和中和反应器为具有混合和保温功能的反应装置;所述具有混合和保温功能的反应装置具体可以选择带搅拌的釜式反应器、带搅拌的管式反应器、静态混合器等;可以根据实际生产需要,选择不同规格、不同类型的反应器来实现本发明。
18.本发明所述的第一分液器和第二分液器为具有分液功能的装置,具体的,可选择的有分液柱或分液塔等;可以根据实际生产需要,选择不同规格、不同类型的分液器来实现本发明。
19.所述步骤(6)中的结晶溶剂选自乙酸甲酯、乙酸乙酯、乙酸丁酯、甲醇、乙醇、异丙醇、丙酮、丁酮中的任意一种或几种。
20.根据实际生产需要,可以设置多个结晶釜,以实现从结晶到后续固液分离、干燥步骤连续进行。
21.结晶后的固液分离步骤,可以根据实际生产需要,选择离心机、板框过滤器或抽滤槽等具有固液分离功能的装置设备进行固液分离操作。
22.干燥步骤,可以根据实际生产需要,选择转鼓干燥器、双锥干燥器、流化床、沸腾干燥器、螺旋干燥器或者具有等同效果的其它设备进行干燥操作。
23.本发明与现有技术相比,具有如下有益效果:本发明n-烷基-硝基邻苯二甲酰亚胺的连续化工业生产方法,采用微通道反应器进行连续硝化反应,且后处理过程中不需使用有机萃取剂进行提取,操作简单,安全环保,制得产品收率高、纯度高(产品纯度≥99.5%);通过使原料反应及其后处理操作的整个生产过程实现动态连续进行,生产效率高,大幅度减少了人工劳动成本,最终产品质量稳定、可控,能够实现大规模的工业化生产。
附图说明
24.图1为本发明实施例的一种n-烷基-硝基邻苯二甲酰亚胺的连续化工业生产方法的流程示意图。
具体实施方式
25.下面结合具体实施例对本发明进行详细说明。以下实施例将有助于本领域的技术人员进一步理解本发明,但不以任何形式限制本发明。应当指出的是,对本领域的普通技术人员来说,在不脱离本发明构思的前提下,还可以做出若干变形和改进,这些都属于本发明的保护范围。
26.本发明实施例和对比例所用的试剂均来源于市购,但不限于这些材料。
27.产品纯度的测试方法:本发明采用气相色谱法测试产品浓度。
28.测试条件:色谱柱:hp-5,30m
×
0.32mm
×
0.25μm;溶剂:二氯甲烷;浓度:2mg/ml;进样口温度:280℃;分流比 30:1;柱箱温度:初始温度100℃,停留时间1min,以升温速度15℃/min升温到260℃,停留1min;检测器温度:280℃;空气:400ml/min;h2:40ml/min;尾气:30ml/min;柱流速:1.4ml/min。
29.实施例1(1)原料预处理:将320kg n-甲基邻苯二甲酰亚胺和300kg浓硫酸(质量分数为98%)投入到配制釜中,混合溶解后,升温至40℃进行预处理,得到n-甲基邻苯二甲酰亚胺硫酸溶液;其中,n-甲基邻苯二甲酰亚胺与硫酸的摩尔比为1:1.5;(2)连续硝化:将预处理后的n-甲基邻苯二甲酰亚胺硫酸溶液以5kg/min的流速、浓硝酸(质量分数为95%)以5.3kg/min的流速,连续泵入微通道反应器中混合进行硝化反应;其中,n-烷基邻苯二甲酰亚胺和硝酸的摩尔比为1:5,反应温度为90℃, n-甲基邻苯二
甲酰亚胺硫酸溶液和浓硝酸在微通道反应器中的混合停留时间为60s;(3)老化:经微通道反应器流出的硝化完成的物料以10.3kg/min流速连续泵入老化反应器中进行老化,控制老化温度为90℃,老化完成的物料不间断流出老化反应器;物料在老化反应器中的停留时间为120min;(4)稀释分层:经老化反应器流出的物料以10.3kg/min流速连续泵入稀释水解反应器中,同时以5.6kg/min流速连续泵入纯水,与物料混合将硫酸浓度稀释至60%进行水解,保持釜内温度90℃,水解完成后,物料不间断进入第一分液柱中,保持分液柱内温度90℃,分层为上层有机相和下层酸液,上层有机相不间断地从第一分液柱溢流出来,同时收集下层酸液经浓缩后可再次使用;(5)中和分层:经第一分液柱流出的上层有机相以3.5kg/min流速连续泵入静态混合器中,同时按一定比例连续泵入10%碳酸钠溶液,保持静态混合器内温度90℃,静态混合器出口端设置ph计,与碳酸钠溶液的泵入速度形成连锁控制,控制碳酸钠溶液的流速使静态混合器出口端流出的物料ph为7.5,中和完成的物料连续进入第二分液柱中,保持分液柱内温度90℃,分层为上层废水层和下层有机相,下层有机相不间断地从第二分液柱流出,同时回收上层废水层;(6)结晶、分离、干燥:在结晶釜中加入1200kg乙酸甲酯,经第二分液柱流出的下层有机相连续泵入结晶釜中进行降温结晶,冷却至室温后,用离心机进行离心使固液分离,使用双锥干燥器对得到的固体湿料进行干燥,制得n-甲基-硝基邻苯二甲酰亚胺;收率为95.9%,纯度为99.6%。
30.实施例2(1)原料预处理:将320kg n-异丁基邻苯二甲酰亚胺和640kg浓硫酸(质量分数为98%)投入到配制釜中,混合溶解后,得到n-异丁基邻苯二甲酰亚胺硫酸溶液;其中,n-异丁基邻苯二甲酰亚胺与硫酸的摩尔比为1:4;(2)连续硝化:将预处理后的n-异丁基邻苯二甲酰亚胺硫酸溶液以5.1kg/min的流速、浓硝酸(质量分数为95%)以1.1kg/min的流速,连续泵入微通道反应器中混合进行硝化反应;其中,n-异丁基邻苯二甲酰亚胺和硝酸的摩尔比为1:2,反应温度为70℃, n-异丁基邻苯二甲酰亚胺硫酸溶液和浓硝酸在微通道反应器中的混合停留时间为400s;(3)老化:经微通道反应器流出的硝化完成的物料以6.2kg/min流速连续泵入老化反应器中进行老化,控制老化温度为70℃,老化完成的物料不间断流出老化反应器;物料在老化反应器中的停留时间为240min;(4)稀释分层:经老化反应器流出的物料以6.2kg/min流速连续泵入稀释水解反应器中,同时以2.27kg/min流速连续泵入纯水,与物料混合将硫酸浓度稀释至60%进行水解,保持釜内温度70℃,水解完成后,物料不间断进入第一分液柱中,保持分液柱内温度70℃,分层为上层有机相和下层酸液,上层有机相不间断地从第一分液柱溢流出来,同时收集下层酸液经浓缩后可再次使用;(5)中和分层:经第一分液柱流出的上层有机相以2.08kg/min流速连续泵入静态混合器中,同时按一定比例连续泵入10%氢氧化钠溶液,保持静态混合器内温度90℃,静态混合器出口端设置ph计,与氢氧化钠溶液的泵入速度形成连锁控制,控制氢氧化钠溶液的流速使静态混合器出口端流出的物料ph为7.5,中和完成的物料连续进入第二分液柱中,保
持分液柱内温度70℃,分层为上层废水层和下层有机相,下层有机相不间断地从第二分液柱流出,同时回收上层废水层;(6)结晶、分离、干燥:在结晶釜中加入1200kg乙酸乙酯,经第二分液柱流出的下层有机相连续泵入结晶釜中进行降温结晶,冷却至室温后,用离心机进行离心使固液分离,使用双锥干燥器对得到的固体湿料进行干燥,制得n-异丁基-硝基邻苯二甲酰亚胺;收率为95.0%,纯度为99.8%。
31.实施例3(1)原料预处理:将320kg n-异丙基邻苯二甲酰亚胺和550kg浓硫酸(质量分数为98%)投入到配制釜中,混合溶解后,升温至60℃进行预处理,得到n-异丙基邻苯二甲酰亚胺硫酸溶液;其中,n-异丙基邻苯二甲酰亚胺与硫酸的摩尔比为1:3.3;(2)连续硝化:将预处理后的n-异丙基邻苯二甲酰亚胺硫酸溶液以5.1kg/min的流速、浓硝酸(质量分数为95%)以0.72kg/min的流速,连续泵入微通道反应器中混合进行硝化反应;其中,n-异丙基邻苯二甲酰亚胺和硝酸的摩尔比为1:1.1,反应温度为80℃, n-异丙基邻苯二甲酰亚胺硫酸溶液和浓硝酸在微通道反应器中的混合停留时间为10s;(3)老化:经微通道反应器流出的硝化完成的物料以5.82kg/min流速连续泵入老化反应器中进行老化,控制老化温度为80℃,老化完成的物料不间断流出老化反应器;物料在老化反应器中的停留时间为240min;(4)稀释分层:经老化反应器流出的物料以5.82kg/min流速连续泵入稀释水解反应器中,同时以3.2kg/min流速连续泵入纯水,与物料混合将硫酸浓度稀释至50%进行水解,保持釜内温度80℃,水解完成后,物料不间断进入第一分液柱中,保持分液柱内温度80℃,分层为上层有机相和下层酸液,上层有机相不间断地从第一分液柱溢流出来,同时收集下层酸液经浓缩后可再次使用;(5)中和分层:经第一分液柱流出的上层有机相以1.95kg/min流速连续泵入静态混合器中,同时按一定比例连续泵入5%氢氧化钾溶液,保持静态混合器内温度80℃,静态混合器出口端设置ph计,与氢氧化钾溶液的泵入速度形成连锁控制,控制氢氧化钾溶液的流速使静态混合器出口端流出的物料ph为7.5,中和完成的物料连续进入第二分液柱中,保持分液柱内温度80℃,分层为上层废水层和下层有机相,下层有机相不间断地从第二分液柱流出,同时回收上层废水层;(6)结晶、分离、干燥:在结晶釜中加入1200kg乙醇,经第二分液柱流出的下层有机相连续泵入结晶釜中进行降温结晶,冷却至室温后,用离心机进行离心使固液分离,使用双锥干燥器对得到的固体湿料进行干燥,制得n-异丙基-硝基邻苯二甲酰亚胺;收率为97.0%,纯度为99.6%。
32.实施例4实施例4与实施例3的区别仅在于步骤(4)稀释分层中,加入纯水的比例为使物料中硫酸浓度稀释至70%,具体步骤如下:(1)原料预处理:将320kg n-异丙基邻苯二甲酰亚胺和550kg浓硫酸(质量分数为98%)投入到配制釜中,混合溶解后,升温至60℃进行预处理,得到n-异丙基邻苯二甲酰亚胺硫酸溶液;其中,n-异丙基邻苯二甲酰亚胺与硫酸的摩尔比为1:3.3;(2)连续硝化:将预处理后的n-异丙基邻苯二甲酰亚胺硫酸溶液以5.1kg/min的流
速、浓硝酸(质量分数为95%)以0.72kg/min的流速,连续泵入微通道反应器中混合进行硝化反应;其中,n-异丙基邻苯二甲酰亚胺和硝酸的摩尔比为1:1.1,反应温度为80℃, n-异丙基邻苯二甲酰亚胺硫酸溶液和浓硝酸在微通道反应器中的混合停留时间为10s;(3)老化:经微通道反应器流出的硝化完成的物料以5.82kg/min流速连续泵入老化反应器中进行老化,控制老化温度为80℃,老化完成的物料不间断流出老化反应器;物料在老化反应器中的停留时间为240min;(4)稀释分层:经老化反应器流出的物料以5.82kg/min流速连续泵入稀释水解反应器中,同时以1.38kg/min流速连续泵入纯水,与物料混合将硫酸浓度稀释至70%进行水解,保持釜内温度80℃,水解完成后,物料不间断进入第一分液柱中,保持分液柱内温度80℃,分层为上层有机相和下层酸液,上层有机相不间断地从第一分液柱溢流出来,同时收集下层酸液经浓缩后可再次使用;(5)中和分层:经第一分液柱流出的上层有机相以1.95kg/min流速连续泵入静态混合器中,同时按一定比例连续泵入5%氢氧化钾溶液,保持静态混合器内温度80℃,静态混合器出口端设置ph计,与氢氧化钾溶液的泵入速度形成连锁控制,控制氢氧化钾溶液的流速使静态混合器出口端流出的物料ph为7.5,中和完成的物料连续进入第二分液柱中,保持分液柱内温度80℃,分层为上层废水层和下层有机相,下层有机相不间断地从第二分液柱流出,同时回收上层废水层;(6)结晶、分离、干燥:在结晶釜中加入1200kg乙醇,经第二分液柱流出的下层有机相连续泵入结晶釜中进行降温结晶,冷却至室温后,用离心机进行离心使固液分离,使用双锥干燥器对得到的固体湿料进行干燥,制得n-异丙基-硝基邻苯二甲酰亚胺;收率为90.0%,纯度为99.6%。
33.实施例5(1)原料预处理:将320kg n-乙基邻苯二甲酰亚胺和1886kg硫酸(质量分数为95%)投入到配制釜中,混合溶解后,升温至40℃进行预处理,得到n-乙基邻苯二甲酰亚胺硫酸溶液;其中,n-乙基邻苯二甲酰亚胺与硫酸的摩尔比为1:10;(2)连续硝化:将预处理后的n-乙基邻苯二甲酰亚胺硫酸溶液以5.1kg/min的流速、浓硝酸(质量分数为95%)以0.56kg/min的流速,连续泵入微通道反应器中混合进行硝化反应;其中,n-乙基邻苯二甲酰亚胺和硝酸的摩尔比为1:2,反应温度为80℃, n-乙基邻苯二甲酰亚胺硫酸溶液和浓硝酸在微通道反应器中的混合停留时间为300s;(3)老化:经微通道反应器流出的硝化完成的物料以5.66kg/min流速连续泵入老化反应器中进行老化,控制老化温度为80℃,老化完成的物料不间断流出老化反应器;物料在老化反应器中的停留时间为240min;(4)稀释分层:经老化反应器流出的物料以5.66kg/min流速连续泵入稀释水解反应器中,同时以10.17kg/min流速连续泵入纯水,与物料混合将硫酸浓度稀释至30%进行水解,保持釜内温度80℃,水解完成后,物料不间断进入第一分液柱中,保持分液柱内温度80℃,分层为上层有机相和下层酸液,上层有机相不间断地从第一分液柱溢流出来,同时收集下层酸液经浓缩后可再次使用;(5)中和分层:经第一分液柱流出的上层有机相以0.8kg/min流速连续泵入静态混合器中,同时按一定比例连续泵入5%氢氧化钾溶液,保持静态混合器内温度80℃,静态混合
器出口端设置ph计,与氢氧化钾溶液的泵入速度形成连锁控制,控制氢氧化钾溶液的流速使静态混合器出口端流出的物料ph为7.5,中和完成的物料连续进入第二分液柱中,保持分液柱内温度80℃,分层为上层废水层和下层有机相,下层有机相不间断地从第二分液柱流出,同时回收上层废水层;(6)结晶、分离、干燥:在结晶釜中加入1200kg乙醇,经第二分液柱流出的下层有机相连续泵入结晶釜中进行降温结晶,冷却至室温后,用离心机进行离心使固液分离,使用双锥干燥器对得到的固体湿料进行干燥,制得n-乙基-硝基邻苯二甲酰亚胺;收率为96.0%,纯度为99.7%。
34.实施例6(1)原料预处理:将320kg n-异戊基邻苯二甲酰亚胺和608kg硫酸(质量分数为95%)投入到配制釜中,混合溶解后,升温至40℃进行预处理,得到n-异戊基邻苯二甲酰亚胺硫酸溶液;其中,n-异戊基邻苯二甲酰亚胺与硫酸的摩尔比为1:4;(2)连续硝化:将预处理后的n-异戊基邻苯二甲酰亚胺硫酸溶液以5.1kg/min的流速、浓硝酸(质量分数为95%)以2.69kg/min的流速,连续泵入微通道反应器中混合进行硝化反应;其中,n-异戊基邻苯二甲酰亚胺和硝酸的摩尔比为1:5,反应温度为75℃, n-异戊基邻苯二甲酰亚胺硫酸溶液和浓硝酸在微通道反应器中的混合停留时间为300s;(3)老化:经微通道反应器流出的硝化完成的物料以7.79kg/min流速连续泵入老化反应器中进行老化,控制老化温度为75℃,老化完成的物料不间断流出老化反应器;物料在老化反应器中的停留时间为240min;(4)稀释分层:经老化反应器流出的物料以7.79kg/min流速连续泵入稀释水解反应器中,同时以7.79kg/min流速连续泵入纯水,与物料混合将硫酸浓度稀释至30%进行水解,保持釜内温度60℃,水解完成后,物料不间断进入第一分液柱中,保持分液柱内温度60℃,分层为上层有机相和下层酸液,上层有机相不间断地从第一分液柱溢流出来,同时收集下层酸液经浓缩后可再次使用;(5)中和分层:经第一分液柱流出的上层有机相以1.8kg/min流速连续泵入静态混合器中,同时按一定比例连续泵入5%氢氧化钾溶液,保持静态混合器内温度60℃,静态混合器出口端设置ph计,与氢氧化钾溶液的泵入速度形成连锁控制,控制氢氧化钾溶液的流速使静态混合器出口端流出的物料ph为7.5,中和完成的物料连续进入第二分液柱中,保持分液柱内温度60℃,分层为上层废水层和下层有机相,下层有机相不间断地从第二分液柱流出,同时回收上层废水层;(6)结晶、分离、干燥:在结晶釜中加入1200kg乙醇,经第二分液柱流出的下层有机相连续泵入结晶釜中进行降温结晶,冷却至室温后,用离心机进行离心使固液分离,使用双锥干燥器对得到的固体湿料进行干燥,制得n-异戊基-硝基邻苯二甲酰亚胺;收率为96.8%,纯度为99.6%。
35.由上述实施例可以看出,本发明n-烷基-硝基邻苯二甲酰亚胺的连续化工业生产方法,能够实现从原料反应及其后处理操作的整个生产过程是动态连续进行,在连续硝化反应后,通过动态连续的进行老化、稀释分层、中和分层、结晶、分离和干燥的后处理步骤,能够有效提高产品的收率和纯度,制得产品的纯度达到99.5%及以上,可直接在下一步反应中使用;同时能够保证产品质量稳定、可控。
再多了解一些
本文用于企业家、创业者技术爱好者查询,结果仅供参考。