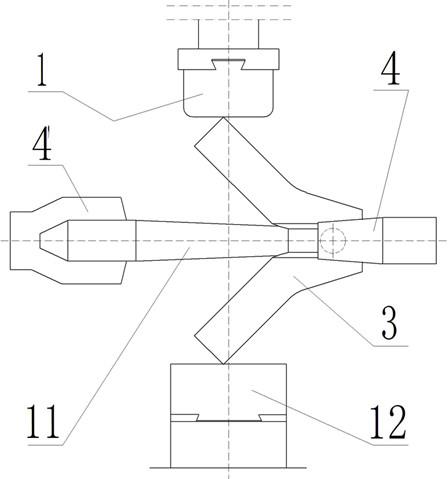
1.本发明涉及曲拐锻件,具体涉及一种曲拐成型锻造工艺,属于锻造技术领域。
背景技术:
2.曲拐是曲轴上的重要零件,因曲轴承担机械旋转运动和往复运动的变换,大型曲轴的曲拐受力大而复杂,因此要有足够的刚度、强度和承受冲击载荷的能力,为了满足上述性能要求,通常选用锻制曲拐,而锻制曲拐的过程中最重要的工序就是满足锻造比和减少锻造火次。目前锻造的方法存在以下弊端:一是由于锻造操作过程复杂,需要多火次才能成型,二是由于锻造火次多,不能满足锻造比,造成锻件内部组织晶粒粗大质量不过关,三是锻造成本高,因此有必要对传统的锻造工艺优化改进。
技术实现要素:
3.本发明提出一种曲拐成型锻造工艺,设置工艺锻件形状和参数,一火次完成制型、折弯、压合、精锻,实现减少火次和增加锻造比的目的。
4.设计方案如下:一种曲拐成型锻造工艺,包括:锻造机、机械手、替砧模、反扣折弯模、芯模、上砧、下砧、工作台和锻件, 所述替砧模包括凹形替砧模和弧形替砧模,所述芯模为多个,不同芯模两端厚薄差不同,所述下砧包括小平砧、凸模、梯形模、凹形模和大平砧,所述机械手包括机械手1和机械手2;所述上砧固定连接在锻造机上,所述凸模与大平砧构成固定较链,通过翻转更换;所述小平砧、凸模、梯形模、凹形模和大平砧设置在所述工作台上,随工作台移动,所述锻件为中部带有凸台的双翅体,其特征在于:包括以下步骤一、锻制曲颈工步1、将半成品锻件加热至锻造温度;工步2、将加热后的锻件置于大平砧上,压薄拔长双翅至设定尺寸;工步3、机械手1夹持锻件,将锻件中部置于凸模上方,180度来回翻转锻制,左右移动锻制,多次变换位置锻制,初步锻制出曲颈的两侧面;工步4、将工步2锻件凸台向上置于梯形模上,机械手2夹持凹形替砧模套置在锻件上,凸台相对的双翅体底面初步锻制出曲颈的下面;工步5、将工步2和3所述曲颈的两侧面和下面置于凸模上,来回翻转、左右移动交替锻制所述曲颈的两侧面、下面和连接部位,锻至接近曲颈形状;工步6、将工步4锻件的曲颈置于凹模上,来回翻转改变锻压角度,上砧下压凸台头部,凸台头部被锻压成多边形曲颈的上面,曲颈的两侧面和下面被凹模锻压成半圆柱体;工步7、将工步6锻制的曲颈交替置于凸模、凹模上,上砧分别采用小平砧和弧形替砧模上,多角度锻制曲颈,锻造成圆柱形曲颈坯件;二、折弯工步8、将曲颈置于凹模上,机械手2夹持反扣折弯模反扣在双翅体两翅上面,上砧
下压,两翅被折弯成
ꢀ“
人”字形;三、压合工步9、将“人”字形锻件置于大平砧上,机械手2将两端厚薄差最大的芯模插入锻件的开口中,上砧下压,两翅靠近,翻转锻件再锻制,两翅贴近芯模;工步10、依序更换两端厚薄差逐步减小的芯模,重复工步8动作,两翅进一步贴合芯模,翻转锻件再精锻双翅体外侧,锻成两曲柄;四、拔头工步11、将芯模与锻件在压合状态下同步翻转,置于大平砧上,锻制凸台头部,拔成四棱台曲拐头部;五、精整工步12、将工步11锻件置于大平砧或小平砧上,精整曲拐锻件至设定尺寸。
5.进一步地,所述凸模为梯形模或弧形模。
6.优选地,所述凹形替砧模的凹形面与锻件凸形面啮合。
7.本发明采用多种不同的特型砧模,左右移动、来回翻转变换角度锻压,反复更换不同砧模锻压,使曲颈逐步成型。在锻件与上砧之间设置反扣折弯模,不仅实现快速更换砧模,还利用折弯模弧形挤压面,使锻件双翅体折弯过程中与模具之间形成滚动挤压,以较小的挤压力和较短的挤压行程将曲拐锻件连续弯曲,以压力较小的锻造机完成较大曲拐锻件折弯工艺,实现一火次完成锻造成型。本发明具有锻件成型度好,加工余量小、锻造时间短、材料损耗小、生产成本低的特点。
附图说明
8.附图1为工步2锻制示意图,附图2为工步3初始锻制状态主视图,附图3为附图2左视图,附图4为附图2工件翻转180
°
状态左视图,附图5为工步4初始锻制状态示意图,附图6为工步4终了锻制状态示意图,附图7为工步5一方位锻制状态示意图,附图8为工步5另一方位锻制状态示意图,附图9为工步6锻制状态示意图,附图10、11为工步7上砧与凸模锻制状态示意图,附图12为工步7凹形替砧模与凹模锻制状态示意图,附图13为工步8初始锻制状态示意图,附图14为工步8终了锻制状态示意图,附图15为工步9初始锻制状态示意图,附图16为工步9终了锻制状态示意图,附图17为工步10锻制状态示意图,附图18为工步11锻制曲拐头部状态示意图,附图19为附图18锻件旋转90
°
锻制曲拐头部状态示意图,
附图20、21为工步12带有芯模状态下精锻曲柄示意图,附图22、23为工步12去掉芯模精锻曲柄示意图。
9.附图中,1为上砧、2为大平砧、3为锻件、4为机械手1、4
′
为机械手2、5为凸模、6为梯形模、7为凹形替砧模、8为凹模、9为弧形替砧模、10为反扣折弯模、11为两厚薄差大的芯模、11
′
为厚薄差逐步减小的芯模、12为小平砧。
具体实施方式
10.下面结合附图对本发明作进一步说明,如附图1所示,将加热后的锻件3置于大平砧上2,上砧1下压,双翅被压薄拔长至设定尺寸。
11.如附图2、3、4所示,机械手4夹持锻件3,将锻件3中部置于凸模5上方,180度翻转锻件3锻制,左右移动锻件3锻制,多次变换锻件3位置锻制,初步锻制出曲颈的两侧面。
12.如附图5、6所示,锻件3凸台向上置于梯形模6上,机械手4
′
夹持凹形替砧模7套置在锻件3上,上砧1下压,凸台相对的双翅体底面初步锻制出曲颈的下面。
13.如附图7、8所示,曲颈的两侧面和下面置于凸模5上,来回翻转、左右移动交替锻制曲颈的两侧面、下面和连接部位,锻至接近曲颈形状。
14.如附图9所示,将附图2、3、4、5、6、7、8锻制出的曲颈置于凹模8上,来回翻转锻件3,改变锻压角度,上砧1下压凸台头部,凸台头部被锻压成多边形曲颈的上面,曲颈的两侧面和下面被锻压成半圆柱体。
15.如附图10、11所示,使用凸模5与上砧1多角度锻制曲颈。
16.如附图12所示,使用弧形替砧模9与凹模8,对曲颈周向锻制,将曲颈锻成圆柱形,完成曲颈圆柱形坯件锻造。
17.如附图13、14所示,将曲颈下面置于凹模8上,机械手4
′
夹持反扣折弯模10反扣在双翅体两翅上面,上砧1下压,锻件3被折弯成
ꢀ“
人”字形;如附图15、16所示,将“人”字形锻件3置于大平砧2上,机械手4
′
将两端厚薄差最大的芯模11插入锻件3的开口中,锻压锻件3,锻件3两边靠近,上下翻转锻件3再锻制,锻件3两边贴近芯模11。
18.如附图17所示,依序更换两端厚薄差逐步减小的芯模11
′
,锻压锻件3,锻件3上的双翅体的两翅贴合芯模11
′
,翻转锻件3再锻制,精锻双翅体外侧,锻成平行的两曲柄。
19.如附图18所示,将芯模11
′
与锻件3在压合状态下同步翻转,对曲颈上端锻制;将附图18状态下的锻件3翻转90
°
,至附图19所示,对曲颈上端继续锻制,曲颈上端被拔成棱台状曲拐头部。
20.如附图20所示,锻件3置于小平砧12上,精整曲柄,如附图21所示,翻转带有芯模4
′
的锻件90
°
,精整曲柄侧面。
21.如附图22所示,锻件3置于小平砧12上,精整曲柄,如附图23所示,翻转锻件90
°
,精整曲柄侧面,完成曲拐锻制。
再多了解一些
本文用于企业家、创业者技术爱好者查询,结果仅供参考。