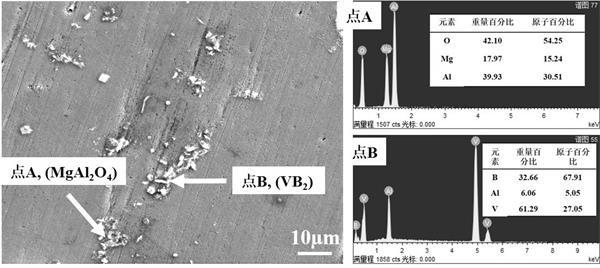
1.本发明属于镁及镁合金的改性领域,涉及一种镁合金的晶粒细化方法。
背景技术:
2.镁合金产品的最大的应用领域是压铸行业,主要集中在汽车、航空和3c领域。当前,铸造镁合金牌号众多,其中多领域大规模应用的合金系列当属mg-al系合金,由于其工艺稳定、成本低、烧损较小等优点,在汽车、电子、航空航天和国防军事等领域具有极大的应用价值和广阔的应用前景。因此,采用经济、高效的手段来提高镁合金的力学性能和铸造性能是满足工业需求、拓宽镁合金应用范围的必要举措之一,也是我国未来镁合金研究领域的迫切要求。
3.研究发现晶粒细化可以大幅度提升镁合金的强度,同时还能有效地提高镁合金的塑性,对改善合金的组织、提高其塑性成形能力以及力学性能具有十分重要的意义。另一方面,晶粒细化可以使凝固合金中存在更高体积分数的枝晶搭接点,有利于液态合金的补缩,提升合金的流动性。可见,晶粒细化是提高镁合金综合性能极为理想的手段,因此对镁合金晶粒细化的研究受到广泛的关注。晶粒细化剂的研发对提高mg-al系合金性能、促进镁合金制品的应用意义重大。
4.目前含铝镁合金的晶粒细化主要集中在过热法、elfinal法、施加外场、碳孕育处理和合金化等技术的研究。其中过热法、elfinal法和施加外场的方法存在能耗大、污染环境以及成本高等问题,一直没能成功地应用于商业化生产。目前工业生产常用晶粒细化方法是的碳孕育处理和添加合金化元素。其中碳孕育处理是向镁合金中添加碳粉、含碳气体和含碳化合物,一般含碳的原料易得但是效果并不显著,并且碳质处理时存在c与镁熔体润湿性不佳的现象,并且碳孕育处理的细化效果并不稳定,保温一定时长后细化效果出现明显的衰退现象。对于向镁合金添加合金化元素,也具有一定的局限性,因为合金元素一方面通过溶质限制作用来限制镁合金晶粒的长大;另一方面是合金化元素会与镁合金中特定的元素形成中间化合物,在熔体中起到异质形核的作用,常用的合金化元素有ca、sr和稀土元素等。但是合金化元素一方面增加了镁合金的密度和成本,另一方面合金化元素的选择要根据特定的镁合金体系,不同的合金体系需要不同的合金化元素来进行组织细化。但是目前商业用且普适性较强的镁合金晶粒细化剂仍没有出现。因此我们急需找寻一种高效、无污染、适用性强的镁合金晶粒细化剂。
5.公开号为cn 108866344a的专利涉及了通过镁合金添加mgal2o4粉末作为细化剂的细化方法,虽说具有一定的细化能力,但是专利提及的直接向熔体中添加粉末的方法会导致形核颗粒相的团聚和与熔体之间的不润湿,导致细化效率的降低,另外直接粉末的添加也不适用于大规模的镁合金生产。公开号为cn 113512675a的专利涉及了一种ti-zr-re-mg晶粒细化剂,该细化剂中颗粒相细小、分布均匀并且杂质含量低。但是其制备过程是将纯ti与纯zr为原料通过真空感应熔炼、电磁搅拌和气雾化,随后进行高能球磨,最后进行粉体压实。制备过程繁琐,且能耗较高。公开号为cn 101886196a和cn 112921225a的专利涉及了碳
孕育处理来细化镁合金,主要利用向镁合金中引入al4c3颗粒相作为镁晶粒的异质形核位点,促进高效形核。但是该方法受限于镁合金的种类,且细化效果不稳定。因此开发出制备简单、添加方式便捷、稳定性高和适用性强的镁合金晶粒细化剂是目前亟需解决的重要问题。
技术实现要素:
6.针对现有技术中的不足,本发明的目的在于提供一种适用于不同铝含量镁合金的晶粒细化剂及其制备方法,既能显著细化镁合金的晶粒尺寸,又具有广泛的适用性和良好的抗细化衰退性,可以对不同铝含量的镁合金都具有明显的细化效果,为镁及镁合金晶粒细化提供新的选择。
7.本发明的目的是通过以下技术方案实现的:一种适用于不同铝含量镁合金的晶粒细化剂,所述细化剂中含有铝、钒、硼、镁和氧;所述细化剂中同时包含vb2颗粒相和mgal2o4颗粒相,颗粒相vb2的粒径为0.5-2微米,所述中间合金中异质形核颗粒相mgal2o4的粒径为0.2-1微米;所述细化剂采用以下方法制备:其中,采用钒粉作为钒源时,具体步骤为:(1)制备晶粒细化剂的原料选取:采用纯铝作为基体;钒粉作为v源;硼酸作为b源和o源;纯镁作为mg源;所述纯铝:钒粉:硼酸:纯镁的质量比为60~90:1.5~7.5:7.5~20.5:1~12。
8.(2)将纯铝在750℃-900℃下进行熔炼,得到铝熔体;(3)将v粉、h3bo3粉进行烘干脱水处理,并在行星球磨机上混合均匀,并进行预热200℃后加入到铝熔体中,用金属罩压至熔体以下,并进行搅拌;随后进行保温处理,保温过程中间隔对熔体进行搅拌处理;保温结束后清理熔体表面浮渣得到成分均匀的al-v-b-o合金熔体,随后将熔体温度降至680℃-750℃;将纯镁加入到熔体中,保温后对熔体进行机械搅拌;搅拌结束后将熔体保温60-90分钟,最后将合金熔体浇铸到钢模具中,凝固后脱模得到合金细化剂;其中,采用铝-钒中间合金作为钒源时,具体步骤为:(1)制备晶粒细化剂的原料选取:采用纯铝作为基体;铝-钒中间合金作为钒源;硼酸作为b源和o源;纯镁作为mg源;所述纯铝:铝-钒中间合金:硼酸:纯镁的质量比为3~20:60~90:6~15:1~5。
9.(2)将al和al-5v中间合金在750℃-900℃下进行熔炼,得到al-v合金熔体;(3)将h3bo3粉进行烘干脱水,并进行预热200℃后加入到al-v合金熔体,并进行搅拌;随后进行保温处理,保温过程中间隔对熔体进行搅拌处理;保温结束后清理熔体表面浮渣得到成分均匀的al-v-b-o合金熔体,随后将熔体温度降至680℃-750℃;将纯镁加入到熔体中,保温后对熔体进行机械搅拌;搅拌结束后将熔体保温60-90分钟,最后将合金熔体浇铸到钢模具中,凝固后脱模得到合金细化剂。
10.所述细化剂应用于不同铝含量的镁合金中,镁合金中铝含量为1wt. %-9wt. %。
11.所述细化剂应用于不同铝含量的镁合金中,具体为将细化剂添加到不同铝含量的710℃-730℃镁合金熔体中,搅拌后,保温结束浇铸到钢模具中,得到细化后的镁合金。
12.所述细化剂中同时包含vb2颗粒相和mgal2o4颗粒相,颗粒相vb2的粒径为0.5-2微米,颗粒相mgal2o4的粒径为0.2-1微米;总颗粒相含量约为5.4%,其中vb2颗粒相为3.9%,mgal2o4颗粒相的含量为1.5%。
13.制备的细化剂中弥散分布着不同粒径的vb2颗粒相和mgal2o4颗粒相,可以在镁合金凝固过程中作为α-mg的异质形核位点,从而高效细化镁合金。
14.为了提高中间合金细化剂中各个元素的获得率和反应程度,在所述步骤(2)将al和a-5v中间合金在750℃-900℃下进行熔炼,得到al-v合金熔体。将h3bo3粉进行烘干脱水,并进行预热200℃后加入到al-v合金熔体,并进行手动搅拌50秒。随后进行120分钟的保温处理,保温过程中每间隔20分钟对熔体进行搅拌处理30秒。保温结束后清理熔体表面浮渣得到成分均匀的al-v-b-o合金熔体,随后将熔体温度降至680℃-750℃,将纯镁加入到熔体中,保温10分钟后对熔体进行快速机械搅拌5分钟。搅拌结束后将熔体保温60分钟,最后将合金熔体浇铸到钢模具中,凝固后脱模得到中间合金细化剂。
15.一种适用于不同铝含量镁合金的晶粒细化剂的应用,将细化剂添加到不同铝含量的710℃-730℃镁合金熔体中(mg-1wt. %al、mg-2wt. %al、mg-3wt. %al、mg-6wt. %al、mg-9wt. %al、商用az31和商用az91合金),待细化剂熔化后进行搅拌处理使得细化剂可以均匀分布于镁合金熔体中,搅拌一定时长后,保温结束浇铸到钢模具中,得到细化后的镁合金,研究细化剂对不同铝含量镁合金晶粒细化普适性。
16.为了研究晶粒细化剂的抗细化衰退性,将细化剂添加到az91镁合金中,待细化剂后熔化后进行搅拌处理使得细化剂可以均匀分布于镁合金熔体中,随后将添加细化剂后的镁熔体在710℃-730℃下在进行不同时长的保温处理(不施加任何的熔体搅拌处理),保温结束后浇铸到钢模具中,得到细化后不同保温时间的镁合金。
17.本发明与现有技术相比较,具有如下显而易见的实质性特点和优点:1.本发明细化剂的晶粒细化效果显著,细化剂中弥散分布着不同粒径的vb2颗粒相和mgal2o4颗粒相,且颗粒相的尺寸具有较大的分布区间。细化剂对不同铝含量的镁合金具有显著的细化效果,具有一定的普适性。对典型商用的az31和az91合金也具有明显的细化效果,az31的平均晶粒尺寸从220
µ
m细化到105
µ
m,az91的平均晶粒尺寸从182
µ
m细化到74
µ
m,晶粒细化效率均超过了50%,考虑到镁合金晶粒尺寸处于200
µ
m以下时,晶粒细化难度增加,晶粒尺寸很难发生大幅度的变化。可以看出本发明的细化剂具有非常优异的效果。
18.2.本发明细化剂的细化方法操作简单,添加量方便控制,且原料易得,并且制备时不产生烟雾,有利于工人操作。
19.3.本发明细化剂中的存在不止一种细化颗粒相,并且存在的两种颗粒相vb2和mgal2o4的粒径分布区间很广,尺寸在几百纳米到几个微米之间,促进异质形核的过程更长,在细化镁合金过程中可以促进更多的高效形核。保温时间为10分钟、20分钟、30分钟时,az31合金的晶粒尺寸分别为105
µ
m、112
µ
m、121
µ
m,虽然改变保温时长对细化剂的细化效果有所影响,但是细化剂的细化效率与未经细化的晶粒尺寸220
µ
m相比,仍处于高效状态,证明细化剂具有优良的抗细化衰退性能。这是因为异质形核过程不是瞬时的,而是从逐步在不同的形核颗粒相上形核生长。根据自由生长模型,异质形核首先发生在大尺寸的颗粒相上,初始形核所需的过冷度由溶质偏析所产生的成分过冷提供,随着形核过程的推进,为熔体提供异质形核位点的颗粒相的尺寸也会逐渐减小,最终晶粒之间发生碰撞,形成细小晶
粒。本发明中具有较广粒径分布区间的两种颗粒相的细化剂相比于具有单一颗粒相的细化剂具有更高效的形核效率,且具有优良的抗细化衰退性能。
20.附图说明
21.图1为本发明实施例1中al-v-b-mg细化剂的sem图像。
22.图2为本发明实施例2中al-v-b-mg细化剂的sem图像。
23.图3为本发明实施例3中mg-3wt. %al经不同含量的al-v-b-mg细化剂细化前后的宏观图。
24.图4为本发明实施例4中mg-1wt. %al经1wt. %的al-v-b-mg细化剂细化前后的宏观图。
25.图5为本发明实施例5中mg-2wt. % al经1wt. %的al-v-b-mg细化剂细化前后的宏观图。
26.图6为本发明实施例6中mg-6wt. % al经1wt. %的al-v-b-mg细化剂细化前后的宏观图。
27.图7为本发明实施例7中mg-9wt. % al经1wt. %的al-v-b-mg细化剂细化前后的宏观图。
28.图8为实施例3至例7中细化前后的晶粒尺寸变化折线图。
29.图9为本发明实施例8中商用az31合金经1wt. %的al-v-b-mg细化剂前后的微观组织图。
30.图10为本发明实施例9中商用az91合金经1wt. %的al-v-b-mg细化剂前后的微观组织图。
具体实施方式
31.下面结合实例对本发明作进一步的详细说明,但本发明的实施方式不限于此:实施例1:一种适用于不同铝含量镁合金的晶粒细化剂的制备一种适用于不同铝含量镁合金的晶粒细化剂的制备方法,具体包括以下步骤:(1)制备500克的细化剂。采用纯al作为基体;v粉作为v源;硼酸(h3bo3)作为b源和o源;纯mg作为mg源。为了补偿实验过程中的元素烧损,额外称取5 wt.%的v源、b源、o源的原料来补充设计成分。按照合金化学组分质量百分比,称取450克纯铝,21克v粉,57克h3bo3粉和15克纯镁。
32.(2)将步骤(1)中al在750℃-850℃下进行熔炼,得到al熔体。
33.(3)将步骤(1)中v粉和h3bo3粉进行烘干脱水处理,并在行星球磨机上混合均匀,并进行预热200℃后加入到步骤(2)中所述的al熔体中,用金属罩压至熔体以下,并进行手动搅拌持续30秒。随后进行120分钟的保温处理,保温过程中每间隔20分钟对熔体进行搅拌处理30秒。保温结束后清理熔体表面浮渣得到成分均匀的al-v-b-o合金熔体,随后将熔体温度降至680℃-750℃,将纯镁加入到熔体中,保温10分钟后对熔体进行机械搅拌5分钟,机械搅拌转速调节为600rpm。搅拌结束后将al-v-b-mg熔体保温60分钟,最后将合金熔体浇铸到钢模具中,凝固后脱模得到al-4v-2b-3mg细化剂。
34.为了确定制备的al-v-b-mg中间合金细化剂的相组成和颗粒相尺寸分布,对本实施例中的中间合金细化剂进行扫描电镜的表征,如图1所示。颗粒相分布于铝基体上,vb2颗粒相尺寸大约为1微米,mgal2o4颗粒相尺寸大约0.5微米。
35.实施例2:一种适用于不同铝含量镁合金的晶粒细化剂的制备。
36.一种适用于不同铝含量镁合金的晶粒细化剂的制备方法,具体包括以下步骤:(1)制备500克的细化剂。采用纯al和al-v合金作为基体;硼酸(h3bo3)作为b源和o源;纯mg作为mg源。为了补偿实验过程中的元素烧损,额外称取5wt. %b源、o源的原料来补充设计成分。按照合金化学组分质量百分比,称取400克al-5v合金,50克纯al,57克h3bo3粉和15克纯镁。
37.(2)将步骤(1)中纯al和al-v合金在750℃-850℃下进行熔炼,得到al-v熔体。
38.(3)按照实施例1中的步骤将h3bo3粉加入到al-v熔体中,并按照实施例1中的保温和搅拌工艺进行制备细化剂,最后将合金熔体浇铸到钢模具中,凝固后脱模得到细化剂al-4v-2b-3mg细化剂。对本实施例中的中间合金细化剂进行扫描电镜的表征,如图2所示。相对于实施例1中的细化剂,本实施例中的分布于铝基体上的颗粒相的数量更多,分布更均匀,vb2颗粒相尺寸大约为1微米,mgal2o4颗粒相尺寸大约0.5微米。
39.实施例3:将不同含量的晶粒细化剂应用到含铝镁合金中。
40.对细化剂的细化效果进行评估,具体方法包括以下步骤:(1)将300克的纯镁,去除表面油污和表层氧化皮,置于不锈钢坩埚中,并在730℃井式电阻炉中进行熔炼,得到镁熔体。随后称取纯铝使合金成分稳定在mg-3.0wt. %al(因为后续添加的细化剂中含有al,将细化剂中的al也计算在内,称取纯铝时要改变铝含量来稳定成分),加入到镁熔体中保温10分钟,随后清理熔体表面氧化渣,得到mg-3.0wt. %al熔体。
41.(2)分别称取0.2wt. %、0.5wt. %、1.0wt. %、1.5wt. %的实施例2中制备的细化剂,并加入到730℃的镁熔体中,保温10分钟使细化熔化分布到镁熔体中。随后进行2分钟的机械搅拌使得细化剂均匀地分布与镁熔体中。搅拌结束后静止一段时间,将熔体温度降至710℃左右,再去除熔体表面氧化渣,最后浇铸到预热200℃大的钢模具中。镁合金熔炼过程均使用rj-2覆盖剂保护。
42.(3)作为对比,按照本实施例中的熔炼工艺,制备出未经细化剂细化处理的mg-3.0wt. %al样品。
43.(4)为了使得晶界更加明显,便于对比晶粒尺寸大小,对细化前后的镁合金进行固溶处理:400℃下保温10h,随后将样品置于水中进行淬火。
44.(5)制备细化前后的样品:将固溶后的镁合金用砂纸打磨,随后抛光,最后在苦味酸-乙酸溶液中进行腐蚀,得到细化前后mg-3.0wt. %al镁合金的宏观组织图,如图3所示。
45.图3中a是未添加细化剂的mg-3.0wt. %al镁合金的宏观组织图,b-e是分别添加0.2wt. %、0.5wt. %、1.0wt. %、1.5wt. %的实施例2中细化剂后的mg-3.0wt. %al镁合金的宏观组织图。对比添加细化剂前后的mg-3wt.%al合金的宏观图可以看出,细化剂可以显著细化纯镁mg-3wt.%al合金,并且随着细化剂的添加量从0.2wt. %增加到1.0wt. %,细化效果越明显(图4中 a-d,但是当添加量超过1.0wt. %(图3中 e)后,虽然也具有一定的细化效果,但是细化效率有所下降。因此考虑到细化效率和成本,认为1wt. %是最佳的细化剂添加
量。
46.实施例4:将晶粒细化剂应用到铝含量为1wt. %的镁合金(mg-1wt. %al)中。
47.根据实施例3的结果可知,认为1 wt. %是最佳的细化剂添加量。在本实施例中,选择1.0wt. %的细化剂添加量来对mg-1wt. %al进行细化。具体方法包括以下步骤:(1)称取纯铝和300克的纯镁(因为后续添加的细化剂中含有al,将细化剂中的al也计算在内,称取纯铝时要改变铝含量来稳定成分),去除表面油污和表层氧化皮。为了补偿熔炼过程中镁的燃烧造成的损失,额外称取1wt. %的纯镁。首先将纯镁置于不锈钢坩埚中,在730℃井式电阻炉中进行熔炼,得到镁熔体,随后清理熔体表面氧化渣。
48.(2)将纯铝,置于730℃镁熔体中,保温10分钟后进行机械搅拌,得到mg-1wt. %al熔体。随后称取实施例2中制备的细化剂,并加入到730℃的mg-1wt. %al熔体中,保温10分钟,待细化剂熔化后分布到镁熔体中。随后进行2分钟的机械搅拌使得细化剂均匀地分布与镁熔体中。搅拌结束后静止,将熔体温度降至710℃左右,再去除熔体表面氧化渣,最后浇铸到预热200℃大的钢模具中。镁合金熔炼过程均使用rj-2覆盖剂保护。
49.(3)作为对比,按照本实施例中的熔炼工艺,制备出未经细化剂细化处理的mg-1wt. %al镁合金样品。
50.(4)细化前后的晶粒尺寸的观察如实施例3步骤(4)和(5),得出细化前后mg-1wt. %al镁合金的宏观组织图,如图4所示。图4中右侧添加细化剂后的图中可以看出,添加细化剂后显著细化mg-1wt. %al镁合金。
51.实施例5:将晶粒细化剂应用到铝含量为2wt. %的镁合金(mg-2wt. %al)中本实施例中配比的原材料、熔炼工艺与实施例4中相同,细化剂添加量为1.0wt. %,具体方法包括以下步骤:(1)称取纯铝和300克的纯镁和(因为后续添加的细化剂中含有al,将细化剂中的al也计算在内,称取纯铝时要改变铝含量来稳定成分),去除表面油污和表层氧化皮。为了补偿熔炼过程中镁的燃烧造成的损失,额外称取1wt. %的纯镁。首先将纯镁置于不锈钢坩埚中,在730℃井式电阻炉中进行熔炼,得到镁熔体,随后清理熔体表面氧化渣。
52.(2)将纯铝,置于730℃镁熔体中,保温10分钟后进行机械搅拌,得到mg-2wt. %al熔体。随后称取实施例2中制备的细化剂,并加入到730℃的mg-2wt. %al熔体中,保温10分钟。随后进行2分钟的机械搅拌使得细化剂均匀地分布与镁熔体中。搅拌结束后静止,将熔体温度降至710℃左右,再去除熔体表面氧化渣,最后浇铸到预热200℃大的钢模具中。镁合金熔炼过程均使用rj-2覆盖剂保护。
53.(3)作为对比,按照本实施例中的熔炼工艺,制备出未经细化剂细化处理的mg-2wt. %al镁合金样品。
54.(4)细化前后的晶粒尺寸的观察如实施例3步骤(4)和(5)。得出细化前后mg-2wt. %al镁合金的晶粒尺寸,如图5所示。图5中右侧添加细化剂后的图中可以看出,添加细化剂后mg-2wt. %al镁合金的晶粒尺寸也发生了明显的减小。
55.实施例6:将晶粒细化剂应用到铝含量为6wt. %的镁合金(mg-6wt. %al)中本实施例中配比的原材料、熔炼工艺与实施例4中相同,细化剂添加量为1.0wt. %,具体方法包括以下步骤:(1)称取纯铝和300克的纯镁,其余步骤与实施例3步骤(1)相同。
56.(2)将纯铝,置于730℃镁熔体中,保温10分钟后进行机械搅拌,得到mg-6wt. %al熔体。随后称取实施例2中制备的细化剂,并加入到730℃的mg-6wt. %al熔体中,保温10分钟。其余步骤与实施例3步骤(2)相同。
57.(3)作为对比,按照本实施例中的熔炼工艺,制备出未经细化剂细化处理的mg-6wt. %al镁合金样品。
58.(4)细化前后的晶粒尺寸的观察如实施例3步骤(4)和(5)。得出细化前后mg-6wt. %al镁合金的晶粒尺寸,如图6所示。图6中右侧添加细化剂后的图中可以看出,当合金中铝含量增加到6 wt. %时,添加细化剂仍可以起到明显的细化效果。
59.实施例7:将晶粒细化剂应用到铝含量为9wt. %的镁合金(mg-9wt. %al)中本实施例中配比的原材料、熔炼工艺与实施例4中相同,细化剂添加量为1.0wt. %,具体方法包括以下步骤:(1)称取300克的纯镁和一定含量的纯铝,其余步骤与实施例3步骤(1)相同。
60.(2)将纯铝置于730℃镁熔体中,保温10分钟后进行机械搅拌,得到mg-9wt. %al熔体。随后称取实施例2中制备的细化剂,并加入到730℃的mg-9wt. %al熔体中,保温10分钟。其余步骤与实施例3步骤(2)相同。
61.(3)作为对比,按照本实施例中的熔炼工艺,制备出未经细化剂细化处理的mg-9wt. %al镁合金样品。
62.(4)细化前后的晶粒尺寸的观察如实施例3步骤(4)和(5)。得出细化前后mg-9wt. %al镁合金的晶粒尺寸,如图7所示。可以看出,当铝含量的进一步增加到9wt. %时,细化剂的添加仍具有较明显的细化效果。
63.综合上图实施例中结果可以看出细化剂对不同铝含量的镁合金都具有细化效果,具有一定的普适性。
64.实施例8:将晶粒细化剂应用到商用az31镁合金中本实施例中用到的商用az31中含有1 wt. %zn和0.3wt. %mn元素,其中添加zn元素用纯zn作为原料,添加mn元素用mg-5mn中间合金作为原料。其它熔炼工艺与实施例3中相同,细化剂添加量为1.0wt. %,具体方法包括以下步骤:(1)称取300克的纯镁和纯铝、纯锌和mg-5mn中间合金,其余步骤与实施例3步骤(1)相同。
65.(2)将纯铝、纯锌和mg-5mn中间合金置于730℃镁熔体中,保温10分钟后进行机械搅拌,得到az31熔体。称取实施例2中的细化剂,其余步骤与实施例3步骤(2)相同。
66.(3)作为对比,按照本实施例中的熔炼工艺,制备出未经细化剂细化处理的az31镁合金样品。
67.(4)细化前后的晶粒尺寸的观察如实施例3步骤(4)和(5),得出细化前后az31镁合金的微观组织,如图8所示。可以看出,当将细化剂应用到商用az31镁合金中,可以将平均晶粒尺寸从220
µ
m细化至105
µ
m,细化剂仍具有有效的细化能力。
68.实施例9:将晶粒细化剂应用到商用az91镁合金中本实施例中用到的商用az91中含有zn 1 wt. %zn和0.3wt. %mn元素,其中添加zn元素用纯zn作为原料,添加mn元素用mg-5mn中间合金作为原料。其它熔炼工艺与实施例3中相同,细化剂添加量为1.0wt. %,具体方法包括以下步骤:
(1)称取300克的纯镁和纯铝、纯锌和mg-5mn中间合金,其余步骤与实施例3步骤(1)相同。
69.(2)将纯铝、纯锌和mg-5mn中间合金置于730℃镁熔体中,保温10分钟后进行机械搅拌,得到az91熔体。称取实施例2中的细化剂,其余步骤与实施例3步骤(2)相同。
70.(3)作为对比,按照本实施例中的熔炼工艺,制备出未经细化剂细化处理的az91镁合金样品。
71.(4)细化前后的晶粒尺寸的观察如实施例3步骤(4)和(5),得出细化前后az91镁合金的微观组织,如图9所示。可以看出,当将细化剂应用到商用az91镁合金中,可以将平均晶粒尺寸从182
µ
m细化至74
µ
m,细化剂仍具有高效的细化能力。
72.实施例10将晶粒细化剂应用到商用az31镁合金中,通过改变保温时间来研究细化剂的抗衰退性能。
73.本实施例中配比的原材料、熔炼工艺与实施例8中相同,细化剂添加量为1.0wt. %,具体方法包括以下步骤:(1)称取300克的纯镁和纯铝、纯锌和mg-5mn中间合金,其余步骤与实施例3步骤(1)相同。
74.(2)将纯铝、纯锌和mg-5mn中间合金,置于730℃镁熔体中,保温10分钟后进行机械搅拌,得到az31熔体。称取实施例2中的细化剂,其余步骤与实施例3步骤(2)相同。
75.(3)为了研究细化剂抗衰退性能,加入细化剂,待熔化后进行机械搅拌使细化剂均匀分布于az31镁合金熔体中。随后进行10分钟、20分钟和30分钟的保温,保温期间不施加任何的搅拌措施,待保温结束清除熔体表面残渣,最后浇铸到预热200℃的钢模具中,得到az31合金经1wt. %的细化剂细化后不同保温时间后的样品。
76.(4)细化前后的晶粒尺寸的观察如实施例3步骤(4)和(5)。得到az31合金经1wt. %的细化剂细化后不同保温时间后的晶粒尺寸。如图10所示。图10中(a)为未经细化的颗粒尺寸图,其粒径尺寸为220
µ
m;(b)为保温时间为10分钟时,az31合金的晶粒尺寸为105
µ
m,延长保温时间至20分钟时,(c)为晶粒尺寸为112
µ
m,进一步延长保温时间至30分钟,(d)为az31合金的晶粒尺寸为121
µ
m。虽然改变保温时长对细化剂的细化效果有所影响,但是细化剂的细化效率仍处于高效状态,证明细化剂具有优良的抗细化衰退性能。
77.综上所有实施例中结果可知,制备的含有不同粒径分布的vb2和mgal2o4颗粒相的细化剂对不同铝含量的镁合金均有明显的细化效果,且具有有效的抗细化衰退性能。其制备方法简便,添加方式简单,适合于大规模的工业应用。
78.上面对本发明实施例结合附图进行了说明,但本发明不限于上述实施例,其他的任何未违背本发明的精神实质与原理下所做的修改、修饰、替代、组合、简化,均应为等效的置换方式,都包含在本发明的保护范围之内。
再多了解一些
本文用于企业家、创业者技术爱好者查询,结果仅供参考。