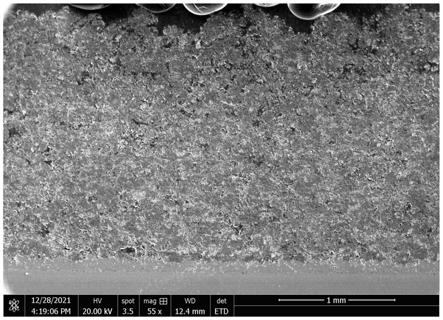
1.本发明涉及表面防护技术领域,具体而言,涉及一种复合封严涂层及其制备方法、机械零件和动力装置。
背景技术:
2.风扇/压气机是涡轮发动机的重要部件,其主要作用是将空气吸入到发动机内部并进行压缩,提高其压力。在发动机运行过程中,由于高速离心力以及热膨胀使得发动机叶片变形伸长,或者叶片偏心转动,导致叶片首先刮削到机匣表面。研究表明,当工作叶片顶端与机匣的相对间隙每增加1%,压气机效率将下降1-3%。径向间隙过大还会导致发动机的气动特性在加速时遭到破坏而引发喘振。因此,必须对气路封严的间隙进行控制。通过在机匣构件内表面涂覆牺牲型可磨耗封严涂层,服役过程中叶片叶尖与封严涂层相互摩擦而在涂层表面形成较浅的凹槽,可实现径向间隙封严控制,从而提高发动机的效率;同时,涂覆的封严涂层还能避免叶片直接与机匣外环内壁刮碰,起到保护叶片的作用。因此,封严涂层性能的好坏将直接影响发动机的功率、推力、效率、安全性和可靠性。
3.al/bn作为一种典型的封严涂层材料,通常采用大气等离子喷涂方法将通过粘结剂团聚的原始粉末涂覆于构件表面,已在发动机风扇和压气机1-4级静子部件获得广泛应用。基于其服役环境,涂层与基体需要具备一定的结合强度和内聚强度,以防止涂层与叶片刮削时发生涂层大块脱落等事故;需要具有一定的强度以抵抗外部颗粒和气体的冲蚀;必须可被刮削,以防止叶片工作时尖端磨损影响封严效果。然而,涂层的可磨耗性和涂层强度是可磨耗封严涂层最重要又相互矛盾的要求,涂层要求具备可磨耗性能,则涂层必须为多孔结构。而当涂层的孔隙过多,涂层的结合强度及抗冲蚀能力必将下降。因此,如何协调和解决好这一对矛盾是封严涂层研究、设计和制造的关键。
4.鉴于此,特提出本发明。
技术实现要素:
5.本发明提供了一种复合封严涂层及其制备方法、机械零件和动力装置,该复合封严涂层旨在降低复合封严涂层中残余应力的累积以及复合封严涂层可磨耗性能和强度兼顾问题,继而降低复合封严涂层在服役过程中整体掉块的风险。
6.本发明是这样实现的:
7.第一方面,本发明实施例提供一种复合封严涂层,其包括依次连接的金属粘结层和铜铝氮化硼可磨耗面层,所述铜铝氮化硼可磨耗面层的孔隙率沿相对远离所述金属粘结层的方向增加。
8.进一步地,在本发明较佳的实施例中,金属粘结层的厚度为0.1-0.3mm;
9.优选地,形成所述金属粘结层的原料选自nialw、nial、nicr和mcraly中的至少一种,其中,m为ni和co中的至少一种。
10.进一步地,在本发明较佳的实施例中,铜铝氮化硼可磨耗面层的厚度为1-3mm;
11.优选地,形成所述铜铝氮化硼可磨耗面层的原料包括微细铝粉、片状六方氮化硼、树枝状电解铜粉和粘合剂;
12.优选地,所述微细铝粉的重量占形成所述铜铝氮化硼可磨耗面层的原料的重量的15-50%,所述树枝状电解铜粉的重量占形成所述铜铝氮化硼可磨耗面层的原料的重量的20-50%,所述片状六方氮化硼的重量占形成所述铜铝氮化硼可磨耗面层的原料的重量的10-30%,其余量为粘合剂;
13.优选地,形成所述铜铝氮化硼可磨耗面层的原料中所述微细铝粉和所述片状六方氮化硼均嵌入所述树枝状电解铜粉内。
14.进一步地,在本发明较佳的实施例中,复合封严涂层的表面洛氏硬度hr15y为35-55,结合强度≥6mpa。
15.第二方面,本发明实施例提供一种上述复合封严涂层的制备方法,包括:在金属粘结层上形成铜铝氮化硼可磨耗面层,且所述铜铝氮化硼可磨耗面层的孔隙率沿相对远离所述金属粘结层的方向增加。
16.进一步地,在本发明较佳的实施例中,利用等离子喷涂,在所述金属粘结层上形成所述铜铝氮化硼可磨耗面层;
17.优选地,形成所述铜铝氮化硼可磨耗面层的条件包括:喷涂功率为20-40kw;载气流量为2-6l/min;送粉速率为20-80g/min;喷距为100-150mm。
18.进一步地,在本发明较佳的实施例中,通过逐渐降低喷涂功率和逐渐增加载气流量中的至少一种,使得所述铜铝氮化硼可磨耗面层的孔隙率沿相对远离所述金属粘结层的方向增加;
19.优选地,所述铜铝氮化硼可磨耗面层的厚度每增加0.1-0.3mm,喷涂功率降低0.5-2kw;载气流量增加0.1-0.5l/min。
20.进一步地,在本发明较佳的实施例中,利用等离子喷涂形成金属粘结层。
21.第三方面,本发明实施例提供一种机械零件,其包括基体和上述复合封严涂层,所述基体与金属粘结层连接;
22.优选地,所述基体包括风扇或压气机的机匣部件。第四方面,本发明实施例提供一种动力装置,其包括上述机械零件;
23.优选地,所述动力装置包括涡轮发动机。
24.本发明的有益效果是:本发明通过设置铜铝氮化硼可磨耗面层的孔隙率沿相对远离所述金属粘结层的方向增加,涂层沉积过程中无新材料的加入,无新的异质界面形成,继而有利于降低大厚度复合封严涂层中的残余应力累积,使得复合封严涂层的可磨耗性能和强度能够兼顾,继而使得复合封严涂层在服役过程中不会大块的掉落,并有助于减少复合封严涂层向对磨转动部件尖端的转移量,满足复合封严涂层对可磨耗性能的需求。
附图说明
25.为了更清楚地说明本发明实施方式的技术方案,下面将对实施方式中所需要使用的附图作简单地介绍,应当理解,以下附图仅示出了本发明的某些实施例,因此不应被看作是对范围的限定,对于本领域普通技术人员来讲,在不付出创造性劳动的前提下,还可以根据这些附图获得其他相关的附图。
26.图1是本发明实施方式提供的实施例1的电镜扫描的结果图。
具体实施方式
27.为使本发明实施例的目的、技术方案和优点更加清楚,下面将对本发明实施例中的技术方案进行清楚、完整地描述。实施例中未注明具体条件者,按照常规条件或制造商建议的条件进行。所用试剂或仪器未注明生产厂商者,均为可以通过市售购买获得的常规产品。
28.下面对本发明实施例提供一种复合封严涂层及其制备方法、机械零件和动力装置具体说明。
29.本发明实施例提供一种复合封严涂层,其包括依次连接的金属粘结层和铜铝氮化硼可磨耗面层,所述铜铝氮化硼可磨耗面层的孔隙率沿相对远离所述金属粘结层的方向增加。
30.为保证铜铝氮化硼可磨耗涂层在被叶片刮削时不损伤到叶片尖端,且能抵抗发动机中高速气流及其中固体粒子的冲刷,所制备的复合封严涂层必须在可磨耗性和强度二者之间达到平衡,以保证在服役过程中,特别是在发生异常刮削时,不会发生大块的掉落或与对磨部件粘连。一般而言,对于同种材料,涂层的微观结构,比如孔隙,与复合封严涂层的其他性能有着密切的关联。具体的,复合封严涂层内孔隙数量及尺寸增加,则复合封严涂层的宏观硬度会相应的下降、复合封严涂层的内聚强度及与基体的结合强度遭到削弱,复合封严涂层的抗冲蚀性能也会急剧的下降,虽然复合封严涂层的可磨耗性能可能会更好,但工作时易出现复合封严涂层撕裂甚至大块脱落现象。相反的,如果复合封严涂层孔隙较少,复合封严涂层的宏观硬度会相应的提高、复合封严涂层的内聚强度及与基体的结合强度得到增强,复合封严涂层的抗冲蚀性能会显著上升,但复合封严涂层的可磨耗性能会有所降低,工作时还可能会发生复合封严涂层转移粘着至对磨转动部件,乃至损伤构件。因此,可通过调控复合封严涂层中的孔隙分布,实现复合封严涂层可磨耗性能和强度二者之间的有效平衡。
31.因此,本发明实施例通过将铜铝氮化硼可磨耗面层的孔隙率沿相对远离所述金属粘结层的方向增加,即使得铜铝氮化硼可磨耗面层致密度沿相对远离所述金属粘结层的方向渐变降低,即靠近金属粘结层一侧的复合封严涂层的孔隙数量相对较少且尺寸更小,可满足对结合强度和内聚强度的需求。而远离金属粘结层一侧的复合封严涂层的孔隙相对较多且尺寸较大,在被对磨转动部件刮削时不会大块的掉落而是以粉尘的形式失效,有助于减少复合封严涂层材料向对磨转动部件的转移量,满足复合封严涂层对可磨耗性能的需求。同时,采用上述结构能够有利于降低大厚度涂层内残余应力的累积,进一步地可降低复合封严涂层服役过程中整体掉块的风险。
32.进一步地,金属粘结层位于基体与铜铝氮化硼可磨耗面层之间,用来缓解铜铝氮化硼可磨耗面层与基体由于物理性能差异导致的热应力。进一步,为了提高铜铝氮化硼可磨耗面层与基体的结合强度,形成所述金属粘结层的原料选自nialw、nial、nicr和mcraly中的至少一种,其中,m为ni和co中的至少一种,金属粘结层的厚度为0.1-0.3mm。
33.进一步地,铜铝氮化硼可磨耗面层附着于金属粘结层的表面,厚度为1-3mm。
34.在发动机工作时,一旦高速旋转的风扇或压气机叶片叶尖部位与机匣表面的封严
涂层相摩擦,会在叶尖端面和封严涂层近表面的局部区域形成异常高温区,具有较高缺口敏感性的钛合金叶片尖端将会与机匣封严涂层中的金属元素发生反应,在叶尖端面生成硬而脆的摩擦产物层并产生微裂纹,进而诱发疲劳裂纹的萌生和扩展,最终导致叶片发生疲劳失效。因此,在选用封严涂层时,要求涂层必须具有较好的可磨耗性能,且涂层与叶片之间还要具有优良的摩擦相容性,以防止叶片工作时尖端磨损。同时,涂层与基体间的结合强度及涂层的内聚强度是涂层最基本的性能,是保证涂层满足力学、物理和化学等使用性能的基本前提,且封严涂层服役过程中需要抵抗发动机中高速气流及其中固体粒子的冲刷,必然要求本身要具有一定的强度来保证涂层与基体以及涂层内部的有效结合,以及抵抗外部颗粒和气体的冲蚀。
35.基于上述性能需求,本发明实施例以铜铝氮化硼复合粉末作为铜铝氮化硼可磨耗面层的原料。其中,金属相的铜和铝均具有优良的延展性和导热性,可作为铜铝氮化硼可磨耗面层的骨架,起到保证复合封严涂层与基体的结合强度及复合封严涂层内聚强度的作用。氮化硼选择中氮和硼组成的六角网状层面并互相重叠形成晶体的六方氮化硼(hbn),具有良好的电绝缘性、导热性、耐化学腐蚀性和润滑性,在铜铝氮化硼可磨耗面层中与其他组分相互协同,提供可磨耗、减摩、抗黏附性能。因此,铜铝氮化硼可磨耗面层中存留的氮化硼含量会直接影响到复合封严涂层的可磨耗性能。由于铜铝氮化硼可磨耗面层中氮化硼组分存在密度低、易氧化、塑性差、粘附性差、在等离子射流中难以加速、容易烧损、在撞击到基体后容易散落等问题,常导致复合封严涂层中氮化硼含量较原始粉末大幅降低的状况。若铜铝以合金的形式混入原始粉末中,而铜铝合金粉常采用雾化方法制备,单个粉末颗粒多呈球形,而混合过程只是物理机械混合,球状的铜铝合金粉末与非金属相仅以粘接剂粘连,易导致团聚粉末内部结合不够紧密和成分存在较大偏差等问题。
36.因此,本发明实施例中形成所述铜铝氮化硼可磨耗面层的原料选择微细铝粉、片状六方氮化硼、树枝状电解铜粉的团聚粉末和粘合剂。其中,微细铝粉的重量占形成所述铜铝氮化硼可磨耗面层的原料的重量的15-50%,所述树枝状电解铜粉的重量占形成所述铜铝氮化硼可磨耗面层的原料的重量的20-50%,所述片状氮化硼的重量占形成所述铜铝氮化硼可磨耗面层的原料的重量的10-30%,其余量为粘合剂。
37.具体地,形成所述铜铝氮化硼可磨耗面层的原料中所述微细铝粉和所述片状六方氮化硼均嵌入所述电解铜粉的树枝状空隙内。更具体地,树枝状电解铜粉可作为团聚复合粉末颗粒的骨架,预混均匀的微细铝粉和片状六方氮化硼组分充分嵌入铜粉的树枝间隙内部,可保证添加的粉末混合时均匀分布而不容易产生偏析。粘结剂通过填充于颗粒之间的缝隙将不同组分的固相粉末粘连到一起成为团聚体,解决混合粉末组分偏聚造成的涂层组织不均匀问题。喷涂时粉末在等离子射流中被快速加热至熔融或半熔融状态,铝和氮化硼被包裹于铜粉的树枝状骨架内部,铜骨架对低熔点的铝和易升华的氮化硼形成保护屏障,降低了喷涂过程中的氮化硼烧损,提高了可磨耗组分及复合粉末整体的沉积率,并避免了金属相或可磨耗相的成分偏聚。因此,复合封严涂层中可磨耗相和孔隙等组织粉末均匀,复合封严涂层硬度波动小,有利于在复合封严涂层可磨耗性能和强度性能二者之间达到平衡。同时,根据服役工况对复合封严涂层硬度和可磨耗性等综合性能的要求,还可以通过对复合粉末中的铜和氮化硼组分进行调控来实现。
38.进一步地,本发明实施例提供的复合封严涂层的表面洛氏硬度hr15y为35-55,结
合强度≥6mpa。
39.第二方面,本发明实施例提供一种复合封严涂层的制备方法,包括:
40.s1、形成金属粘结层;
41.利用等离子喷涂形成金属粘结层,其中,条件包括:喷涂功率为35-50kw;载气流量为2-5l/min;送粉速率为20-40g/min;喷距为100-140mm。
42.需要说明的是,(1)可以采用现有技术形成金属粘结层,本发明实施例提供的等离子喷涂只是效果更高,有利于金属粘结层的形成以及金属粘结层与基体的结合,并不限于等离子喷涂以及上述条件。
43.(2)在基体上形成金属粘结层之前,还包括对基体进行前处理。例如,将基体脱脂除油后,非喷涂部位采用工装夹具或者高温胶带进行遮蔽保护,对喷涂位置进行喷砂处理以去掉基体表面氧化层以增加表面活性并提高复合封严涂层与基体间的结合强度,再将基体置于喷枪前部并在未送粉条件下利用等离子射流对基体进行预热处理,通过提高涂层与基体表面接触的温度的途径来减小因基体与涂层的热膨胀差异产生的应力,进一步增强涂层与基体的结合强度。上述采用的除油、喷砂及预热处理等前处理方法均为本技术领域的现有通用技术,具体的处理参数本发明对其不做限定。
44.s2、形成铜铝氮化硼可磨耗面层;
45.利用等离子喷涂,在所述金属粘结层上形成所述铜铝氮化硼可磨耗面层;其中,形成所述铜铝氮化硼可磨耗面层的条件包括:喷涂功率为20-40kw;载气流量为2-6l/min;送粉速率为20-80g/min;喷距为100-150mm。
46.在此喷涂参数范围内,嵌入树枝状铜粉骨架内部的微细铝粉和片层状氮化硼可吸收足够的热量而充分熔融,部分较大粒径的铜粉仍保留了树枝状结构,进而通过覆盖和裹挟等方式将低熔点的铝和易升华的氮化硼保留在树枝状结构内部,增加了粉末了沉积效率并有效的保留了可磨耗相。
47.通常,为保证其服役效果,可磨耗封严涂层都具有较大的厚度。但喷涂过程中随着涂层厚度的增加,内部残余应力累积会也越来越显著,进而在复合封严涂层内部形成裂纹,导致复合封严涂层在工作过程中被刮削时大块脱落风险急剧增加。因此,针对厚度较大的可磨耗面层,为避免出现涂层掉块和抗冲刷能力不足的现象,减少其变形与形成裂纹倾向,可通过调整喷涂功率和送粉载气流量的方式进行封严涂层结构设计,使复合封严涂层内部发生应力弛豫。
48.一方面,喷涂功率是影响复合封严涂层微观结构和综合性能的关键因素。等离子喷涂以如氮、氩、氢及氦等中的至少一种气体通过压缩电弧时产生电离而形成电中性的等离子体为热源,将送入到等离子射流中的粉末或丝材加热到熔融或半熔融状态,再以一定的速度喷射到经过预处理的基体材料表面,快速在基体表面铺展及冷却凝固,与基体材料以机械咬合的方式相结合并逐层堆垛而形成表面覆盖复合封严涂层。因此,大喷涂功率条件下,送入等离子射流中心的粉末颗粒可以获得更高的温度和更快的速度,粉末颗粒撞击到基体或已沉积复合封严涂层表面后,可获得更充分的结合状态,所形成的复合封严涂层致密度更高,硬度分散性更小,复合封严涂层性能更稳定,结构更均匀。与之相应的,降低喷涂功率时,送入等离子射流中的粉末颗粒的加温加速过程受到抑制,粉末颗粒撞击到基体或已沉积复合封严涂层表面后,结合状况会有所减弱,必然形成更多的孔隙。虽然包括硬度
分布均匀性、结合强度等综合性能会有所降低,但可磨耗性能会有所增强。
49.另一方面,喷涂过程中,粉末在送粉载气作用下,被吹进喷嘴或以一定角度直接送入喷嘴出口处的等离子射流中。在惯性力和气动力的作用下,粉末粒子穿入等离子射流中而被加热和加速。而粉末颗粒在撞击基体或已沉积复合封严涂层前瞬间的温度和速度状态将直接影响到复合封严涂层的微观组织和综合性能,而粉末的加温加速状态与其在等离子射流中的飞行路径及停留时间密切相关,这又取决于粉末进入等离子射流的初始位置和速度。如果载气流量适宜,粉末可被送入等离子射流的中心位置而被充分加温加速,在使用微细铝粉和片状六方氮化硼嵌入树枝状电解铜粉的团聚粉末有效控制了氮化硼烧损并可提高复合封严涂层沉积率的前提下,复合封严涂层以更充分的熔融状态和更大的动能撞击基体或已沉积复合封严涂层,有利于粉末颗粒的充分铺展和结合,并形成较致密的复合封严涂层结构。相应的,载气流量过低会导致粉末材料送不到等离子射流中心,其加温加速效率下降,必然导致复合封严涂层的结合强度或内聚强度的下降和孔隙率上升,还可能导致粉末沉积率的下降和引起喷涂过程中堵塞送粉管,造成材料的浪费,进而影响到复合封严涂层质量和喷涂效率。若载气流量增加,粉末离开送粉嘴进入等离子射流的初始速度较高,从而导致粉末颗粒送出等离子射流中心甚至穿出,尽管等离子射流中心区域的温度很高,但过短的飞行时间不能使粉末颗粒均匀和完全的熔化,也会导致复合封严涂层的结合强度或内聚强度的下降和孔隙率上升。
50.进一步地,本发明实施例通过逐渐降低喷涂功率和逐渐增加载气流量中的至少一种,使得所述铜铝氮化硼可磨耗面层的孔隙率沿相对远离所述金属粘结层的方向增加,继而优化复合封严涂层显微组织中的孔隙的尺寸和分布均匀性,来获得可磨耗性能和强度相兼顾的复合封严涂层。在靠近金属粘结层位置,涂层组织相对较为致密,结合较好,可作为中间过渡层,避免涂层剥落。在远离金属粘结层位置,涂层内孔隙多,硬度相应降低,作为可磨耗面层,可避免或降低对磨叶片损伤。
51.具体的,在制备铜铝氮化硼可磨耗面层过程中,每喷涂一定厚度,通过逐渐降低喷涂功率和逐渐增加送粉载气流量等途径的至少一种,实现复合封严涂层的致密度由靠近金属粘结层侧向表面方向渐变降低。即靠近金属粘结层一侧的涂层孔隙数量相对较少且尺寸更小,可满足对结合强度和内聚强度的需求。而远离金属粘结层一侧的涂层孔隙相对较多且尺寸较大,在被对磨转动部件刮削时不会大块的掉落而以粉尘的形式失效,有助于减少复合封严涂层材料向转动部件接触位置的转移量,满足复合封严涂层对可磨耗性能的需求。
52.具体的,铜铝氮化硼可磨耗面层的厚度每增加0.1-0.3mm,所述喷涂功率降低0.5-2kw;载气流量增加0.1-0.5l/min。
53.本发明实施例提供的上述制备方法有利于提高复合封严涂层中氮化硼及孔隙的分布均匀性或形成渐变结构,降低氮化硼组分的烧损率并提高涂层沉积效率,并在复合封严涂层可磨耗性和强度二者之间达到平衡。复合封严涂层表面洛氏硬度hr15y为35-55,结合强度≥6mpa,复合封严涂层与对磨转动部件(例如叶片)之间的摩擦相容性好。
54.第三方面,本发明实施例提供一种机械零件,其包括基体和上述复合封严涂层,所述基体与金属粘结层连接;
55.优选地,所述基体包括风扇或压气机的机匣部件。
56.且形成基体的材料可以为钛合金、铝合金、合金钢或者高温合金等现有的材料。
57.第四方面,本发明实施例提供一种动力装置,其包括上述机械零件;
58.优选地,所述动力装置包括涡轮发动机。
59.以下结合实施例对本发明的特征和性能作进一步的详细描述。
60.实施例1
61.本实施例提供了一种复合封严涂层的制备方法,其包括以下步骤:
62.(1)基体除油处理后,采用工装夹具或粘贴高温胶带保护非喷涂区域,喷涂区域喷砂粗化,并将试样装夹固定至喷枪前部。
63.(2)未送粉条件下利用大气等离子喷涂射流对基体进行预热后,喷涂nicr粉末形成金属粘结层,所得金属粘结层厚度为0.12mm,其中,喷涂条件包括:喷涂功率为42kw;载气流量为4.5l/min;送粉速率为25g/min;喷距为110mm。
64.(3)将2000克微细铝粉、1000克片状六方氮化硼、1000克树枝状电解铜粉和650ml水玻璃,经过预混、粘连、筛分和烘干形成团聚粉末。
65.采用大气等离子喷涂上述团聚粉末形成铜铝氮化硼可磨耗面层,具体工艺为:送粉量40g/min,喷距110mm,送粉载气流量为3.0l/min,喷涂初始功率为36kw。每喷涂形成的涂层的厚度增加0.2mm,喷涂功率降低1kw,最终铜铝氮化硼可磨耗面层厚度2.2mm。
66.实施例2
67.本实施例提供了一种复合封严涂层的制备方法,其包括以下步骤:
68.(1)基体除油处理后,采用工装夹具或粘贴高温胶带保护非喷涂区域,喷涂区域喷砂粗化,并将试样装夹固定至喷枪前部。
69.(2)未送粉条件下利用大气等离子喷涂射流对基体进行预热后,喷涂nial粉末形成金属粘结层,所得金属粘结层厚度为0.18mm,其中,喷涂条件包括:喷涂功率为43kw;载气流量为2.5l/min;送粉速率为30g/min;喷距为110mm。
70.(3)将2200克微细铝粉、800克片状六方氮化硼、1000克树枝状电解铜粉和700ml水玻璃,经过预混、粘连、筛分和烘干形成团聚粉末。
71.采用大气等离子喷涂上述团聚粉末,具体工艺为:送粉量25g/min,喷距140mm,喷枪功率为30kw,送粉载气初始流量为2.6l/min。每喷涂形成的涂层的厚度增加0.15mm,送粉载气流量增加0.15l/min,所得铜铝氮化硼可磨耗面层厚度1.8mm。
72.实施例3
73.本实施例提供了一种复合封严涂层的制备方法,其包括以下步骤:
74.(1)基体除油处理后,采用工装夹具或粘贴高温胶带保护非喷涂区域,喷涂区域喷砂粗化,并将试样装夹固定至喷枪前部。
75.(2)未送粉条件下利用大气等离子喷涂射流对基体进行预热后,喷涂nialw粉末形成金属粘结层,所得金属粘结层厚度为0.25mm,其中,喷涂条件包括:喷涂功率为48kw;载气流量为4l/min;送粉速率为35g/min;喷距为120mm。
76.(3)1800克微细铝粉、1000克片状六方氮化硼、1200克树枝状电解铜粉和600ml水玻璃,经过预混、粘连、筛分和烘干形成团聚粉末。
77.采用大气等离子喷涂上述团聚粉末,具体工艺为:送粉量45g/min,喷距130mm,喷涂初始功率为35kw,送粉载气初始流量为2.4l/min。每喷涂形成的涂层的厚度增加0.3mm,
喷涂功率降低1.2kw,送粉载气流量增加0.3l/min,最终所得铜铝氮化硼可磨耗面层厚度2.7mm。
78.对比例1:本对比例提供一种复合封严涂层的制备方法,其制备方法与实施例1基本相同,区别在于原始喷涂粉末中没有铜粉。
79.对比例2:本对比例提供一种复合封严涂层的制备方法,其制备方法与实施例1基本相同,区别在于:喷涂团聚粉末时,每喷涂形成的涂层的厚度增加时,并未降低喷涂功率,即喷涂功率从头到尾均为36kw。即本对比例得到的复合封严涂层的铜铝氮化硼可磨耗面层的致密度或者孔隙率并未有变化。
80.表征:
81.对实施例1制备得到的复合封严涂层截面进行电镜扫描,结果参见图1,由图可见,铜铝氮化硼可磨耗面层与金属粘结层结合良好,可磨耗面层内的孔隙数量和大小均沿着相对远离金属粘结层的方向逐渐增加,且不同孔隙率的层间自然过渡,不存在明显的界面,该结构有利于降低涂层内部的应力累积,获得可磨耗性能与强度兼具的可磨耗封严涂层。
82.实验例
83.对实施例1-3和对比例1-2的复合封严涂层进行性能检测,检测结果如下表:
[0084][0085][0086]
根据上表可知,与对比例1相比较,原始粉末中加入电解树枝状铜粉后,可有效降低原材料中的bn含量,保证涂层的可磨耗性能。与对比例2比较,降低喷涂功率或增大送粉载气流量,在保证满足技术要求的结合强度的同时,可有效降低bn的烧损量,表面的相对疏松结构还可降低涂层表面洛氏硬度,改善涂层可磨耗性能。
[0087]
以上所述仅为本发明的优选实施方式而已,并不用于限制本发明,对于本领域的技术人员来说,本发明可以有各种更改和变化。凡在本发明的精神和原则之内,所作的任何修改、等同替换、改进等,均应包含在本发明的保护范围之内。
再多了解一些
本文用于企业家、创业者技术爱好者查询,结果仅供参考。