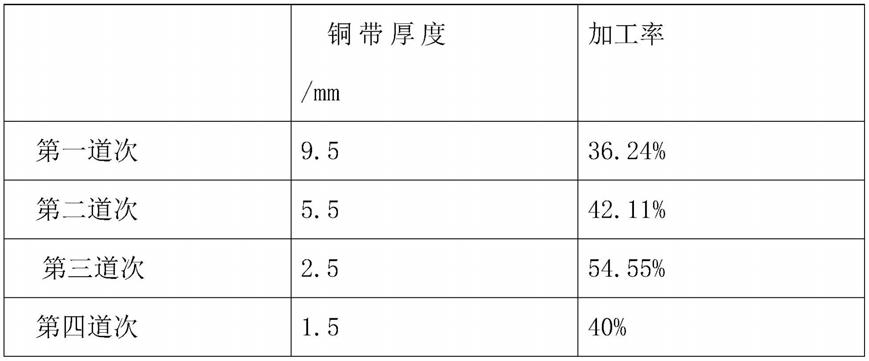
1.本发明涉及铜带生产技术领域,具体涉及一种用于热交换器翅片超硬铜箔及其生产工艺。
背景技术:
2.铜及铜合金板材作为材料发展过程中市场占比较大的金属材料,因其各项性能优良,尤其是导电导热性能突出,广泛应用于各工业领域,我国生产的铜及铜合金板带材的产品用途不同,其性能也有差异,目前对铜箔进行生产流程优化,量产可供使用的高质量铜箔能够显著减少市场进口占比,增加我国高档铜箔的竞争力,满足工业使用需求。
3.目前现有超硬铜箔的生产工艺为熔铸
→
铣面
→
粗轧
→
纵剪
→
退火
→
清洗
→
中轧
→
退火
→
清洗
→
精轧
→
清洗
→
分切
→
检验
→
包装入库。以上生产工艺存在工艺流程长、成材率低、性能差、生产能耗大等缺点,很难满足相关行业的使用要求。
技术实现要素:
4.本发明的目的在于提供一种用于热交换器翅片超硬铜箔及其生产工艺,通过对整体工艺流程的优化以及轧制工序加工道次的优化,从而缩短加工流程,减少加工时间,提高生产效率;通过对退火的温度、升温时间和保温时间的优化,优化晶粒的大小,提升产品的综合性能。
5.本发明具体技术方案如下:
6.一种用于热交换器翅片超硬铜箔的生产工艺,包括以下步骤:
7.1)熔铸;
8.2)铣面;
9.3)粗轧;
10.4)第一次退火;
11.5)清洗;
12.6)中轧;
13.7)第二次退火;
14.8)清洗;
15.9)精轧;
16.10)清洗;
17.11)钝化;
18.12)第三次退火;
19.13)成品轧制;
20.14)成品清洗;
21.15)分切;
22.16)成品包装。
23.步骤1)中所述熔铸,采用水平连铸的方式将熔融铜水进行拉铸,获得原始的紫铜带坯;步骤1)由熔炼车间进行水平连铸通过拉、停、反推、停、反推、停的周期循环连续引拉,牵引形成的铜带坯的规格为16-17mm
×
650-850mm(厚度
×
宽度)。
24.步骤2)中所述铣面具体为:将带坯进行上下左右四面进行铣削;步骤2)中将步骤1)制备的铜带坯的上下两面各铣削1mm,左右各铣削1mm。将上下铣面和左右铣面控制在1mm,铣掉边裂部分后在打卷的过程中进行垫纸,防止铣削过程中铜带层与层之间发生剐蹭和磨损。
25.步骤3)中所述粗轧具体为:使用四辊可逆轧制机组对铜带坯进行粗轧,轧制规程为5道次,前3个道次的加工率为35%-55%,后2个道次的加工率在30%-40%;步骤3)中需要将每层之间的垫纸去除。按照每一个道次的加工率设置进行加工。在加工过程中使用轧制介质乳化液进行冷却和润滑;
26.步骤4)第一次退火具体为:将粗轧后的铜带经过轧制之后,在钟罩式光亮退火炉进行退火,退火温度为460-500℃,升温时间四小时,保温8-12小时,风冷至100℃切换进行水冷至60℃出炉,总冷却时间8小时;
27.步骤5)中所述清洗依次包括酸清洗、抛光、清洗、钝化处理和烘干,用以去除铜带表面的轧制介质等,并在铜带表面进行防氧化处理,保证铜带的表面质量良好。
28.步骤6)所述中轧具体为:将剪边处理后的铜带经过四辊可逆轧制机组进行中轧,轧制规程为3道次,前2个道次加工率40-45%,最后一个道次加工率15%-25%;中轧过程,按照该工艺提供的加工率进行加工,在加工过程中使用轧制介质乳化液进行冷却和润滑;
29.步骤7)中所述第二次退火具体为:将中轧后的铜带放入钟罩式光亮退火炉中,在保护性气体氛围下进行退火,保温温度440-480℃,升温时间3小时,保温时间8小时,风冷至100℃切换水冷至70℃出炉;退火过程,在保护性气氛下进行;所述保护性气氛是纯度99.999%氮气;
30.步骤8)中所述清洗,具体为:将退火后的铜箔进行酸洗、钝化处理;进行表面处理,处理之后的铜箔表面质量更加优良;
31.步骤9)中所述精轧具体为:将经过清洗的铜箔经过六辊可逆轧制机组进行精轧使铜带符合成品所需尺寸,轧制规程为2个道次,第一个道次加工率为:25-30%,下一个道次加工率35-40%;精轧过程,轧制介质为轧制油,有效进行冷却和润滑,保护铜箔的表面在轧制过程中降低磨损,保证铜箔板型状态良好;
32.步骤10)所述清洗具体为:将精轧后的铜带进行清洗,清洗线上进行的脱脂和钝化处理。进行风干,保证铜箔表面清洗后的钝化作用进行的更加彻底。
33.步骤12)第三次退火具体为:在钟罩式光亮退火炉中的保护性气体氛围下进行退火,从室温开始升温到340-370℃温度后,升温时间5小时,保温6-8小时,再进行冷却,风冷至80℃切换水冷至45℃出炉;在钟罩式光亮退火炉中进行悬空退火。
34.步骤13)成品轧制,共3个道次;第一个道次加工率为:50-55%,第二道次加工率35-40%;第三道次加工率25-30%;
35.步骤15)分切;按照使用要求对于宽度进行设置之后分切。
36.本发明提供的一种热交换器翅片超硬铜箔,采用上述生产工艺生产得到。
37.热交换器翅片超硬铜箔生产过程中,铜箔的厚度和板形控制与相关性能要求较为
特殊,对于工艺流程要求十分严格。同时,由于紫铜自身加工特性,作为一种加工率较大的金属材料,冷压延能够改变金属内部的组织形貌,改变晶粒的大小;压延铜箔的性能上,紫铜的退火工艺参数与加工率相关,本发明通过优化生产过程,缩短工期,调整材料的性能,使其能够满足市场需求。采用本发明技术方案后,本发明相对于热交换器翅片超硬铜箔生产工艺主要有以下优点:在轧制过程中,总加工率不改变的条件下,控制道次加工率,减少轧制道次,提高了生产效率,降低能耗,缩短生产流程、节省成本;进行四面铣,相比传统工艺省去一道纵剪流程,缩短生产流程,节省成本;在退火过程中进行特定的温度设计,可在满足市场要求的状态下,控制成品的硬度和延伸率,对热交换器翅片的冲压过程中的部分参数的调整能够做出相应的调整;采用悬空退火,使得铜箔在退火过程中,铜箔各层之间的气氛相同,铜箔的各个部分的成分均匀,性能一致;并且有效控制成品铜箔不发生塔卷;缩短加工流程,在进行成品退火之后可直接进行包装,减少生产流程,节省生产成本。
具体实施方式
38.实施例1
39.一种用于热交换器翅片超硬铜箔的生产工艺,包括以下工艺流程:
40.1)熔铸:水平连铸使连续引拉步骤,进行引拉、停、反推、停、反推、停的循环动作连续引拉,本实施例中选取规格为16.9mm
×
650mm(厚度
×
宽度)的铜带坯。
41.2)铣面:将上述步骤1)生产的铜带坯上、下、左、右四面各铣削1mm,铣削速度控制在特定的范围内,进行四面铣,去除表面和侧边的缺陷,避免缺陷层影响下一个工序,并进行垫纸,铜带表面不发生划伤;
42.3)粗轧:采用四辊可逆轧制机组对步骤2)处理后的铜带坯(厚度14.9mm)进行粗轧,轧制规程为5道次,具体加工率如表1所示。
43.4)第一次退火:将步骤3)处理后的铜带经过轧制之后,在钟罩式光亮退火炉进行退火,退火温度为480-500℃,升温时间4小时,保温8小时,风冷至100℃切换进行水冷至60℃出炉;总冷却时间8小时;
44.5)清洗:清洗步骤4)处理后的铜带,进行包括酸清洗、抛光、清洗、钝化处理和烘干,用以去除铜带表面的轧制介质等,并在铜带表面进行防氧化处理,保证铜带的表面质量良好;
45.6)中轧:将步骤5)处理后的产品送入四辊可逆轧制机组进行中轧,轧制规程为3道次,具体参数如表2。
46.7)第二次退火:将中轧后的铜带放入钟罩式光亮退火炉中,在保护性气体氛围下进行退火,从室温开始进行升温,升温时间3小时,升温至温度440-460℃,保温时间8小时,风冷至100℃切换水冷至70℃出炉;退火过程,在保护性气氛下进行;所述保护性气氛是纯度99.999%氮气;
47.8)清洗:将退火后的铜箔进行酸洗、钝化处理;进行表面处理,处理之后的铜箔表面质量更加优良;
48.9)精轧:精轧将经过中间清洗的铜带经过六辊可逆轧制机组进行精轧,轧制规程为2个道次,具体工艺参数如表3所示。
49.10)清洗:将精轧后的铜箔进行清洗,在清洗线上进行的脱脂和钝化处理。
50.11)钝化处理;
51.12)第三次退火:在钟罩式光亮退火炉中的保护性气体氛围下进行退火,从室温开始升温到340-350℃温度后,升温时间5小时,保温6小时,再进行冷却,风冷至80℃切换水冷至45℃出炉;在钟罩式光亮退火炉中进行悬空退火。
52.13)成品轧制:具体加工率如表4所示。
53.14)成品清洗;
54.15)分切:按照使用要求对于宽度进行设置之后分切;
55.16)成品包装。
56.表1实施例1粗轧参数
[0057][0058][0059]
表2实施例1中轧参数
[0060] 加工率铜带厚度/mm第一道次40%0.60第二道次41.67%0.35第三道次22.86%0.27
[0061]
表3实施例1精轧工艺参数
[0062] 加工率铜带厚度/mm第一道次30%0.189第二道次36.5%0.12
[0063]
表4实施例1成品轧制工艺参数
[0064] 加工率铜带厚度/mm第一道次52.5%0.057第二道次38.6%0.035第三道次25.7%0.026
[0065]
实施例1的产品达到85.9hv;延伸率满足使用要求,抗拉强度325mpa。
[0066]
对比例1
[0067]
一种用于热交换器翅片超硬铜箔的生产工艺,包括以下工艺流程:
[0068]
1)熔铸:水平连铸使连续引拉步骤,进行引拉、停、反推、停、反推、停的循环动作连续引拉,本实施例中选取规格为16.5mm
×
650mm(厚度
×
宽度)的铜带坯。
[0069]
2)铣面:将上述步骤1)生产的铜带坯上、下、左、右四面各铣削1mm,铣削速度控制在特定的范围内,进行四面铣,去除表面和侧边的缺陷,避免缺陷层影响下一个工序,并进行垫纸,铜带表面不发生划伤;
[0070]
3)粗轧:采用四辊可逆轧制机组对步骤2)处理后的铜带坯(厚度14.5mm)进行粗轧,轧制规程为5道次,具体加工率如表5所示。
[0071]
4)第一次退火:将步骤3)处理后的铜带经过轧制之后,在钟罩式光亮退火炉进行退火,退火温度为460℃,升温时间4小时,保温6小时,风冷至100℃切换进行水冷至60℃出炉;总冷却时间8小时;
[0072]
5)清洗:清洗步骤4)处理后的铜带,进行包括酸清洗、抛光、清洗、钝化处理和烘干,用以去除铜带表面的轧制介质等,并在铜带表面进行防氧化处理,保证铜带的表面质量良好;
[0073]
6)中轧:将步骤5)处理后的产品送入四辊可逆轧制机组进行中轧,轧制规程为3道次,具体参数如表6。
[0074]
7)第二次退火:将中轧后的铜带放入钟罩式光亮退火炉中,在保护性气体氛围下进行退火,从室温开始进行升温,升温时间3小时,升温至温度420℃,保温时间8小时,风冷至100℃切换水冷至70℃出炉;退火过程,在纯度99.999%氮气下进行;
[0075]
8)清洗:将退火后的铜箔进行酸洗、钝化处理;进行表面处理,处理之后的铜箔表面质量更加优良;
[0076]
9)精轧:精轧将经过中间清洗的铜带经过六辊可逆轧制机组进行精轧,轧制规程为2个道次,具体工艺参数如表7所示。
[0077]
10)清洗:将精轧后的铜箔进行清洗,在清洗线上进行的脱脂和钝化处理。
[0078]
11)钝化处理;
[0079]
12)第三次退火:在钟罩式光亮退火炉中的保护性气体氛围下进行退火,从室温开始升温到350℃温度后,升温时间5小时,保温8小时,再进行冷却,风冷至80℃切换水冷至45℃出炉;在钟罩式光亮退火炉中进行悬空退火。
[0080]
13)成品清洗;
[0081]
14)分切:按照使用要求对于宽度进行设置之后分切;
[0082]
15)成品包装。
[0083]
表5对比例1粗轧参数
[0084][0085]
表6对比例1中轧参数
[0086] 加工率铜带厚度/mm第一道次40%0.60第二道次41.67%0.35第三道次25.7%0.26
[0087]
表7对比例1精轧工艺参数
[0088] 加工率铜带厚度/mm第一道次53%0.12第二道次25%0.09
[0089]
对比例1产品带型不平整,无法进行下一个道次的轧制,并且厚度硬度为不满足使用要求,厚度不能满足市场要求;
[0090]
本发明通过优化生产工艺,相对于传统的用于热交换器翅片超硬铜箔生产工艺减少了一道纵剪与一道清洗工序,减少加工时间,控制生产成本,提高生产速度,降低能耗。本发明优化轧制工艺,在总加工率不变的情况下,控制道次加工率,优化轧制流程;本发明基于紫铜带的大加工率,进行退火工艺的优化,改变退火温度、升温时间以及保温时间,在成品退火的过程中,根据成品的市场需求能够有效的控制成品的性能,细化晶粒,控制性能,降低生产成本的条件下,生产出用于热交换器翅片超硬铜箔,匹配冲压过程中对于铜箔的要求,满足市场的需求。
再多了解一些
本文用于企业家、创业者技术爱好者查询,结果仅供参考。