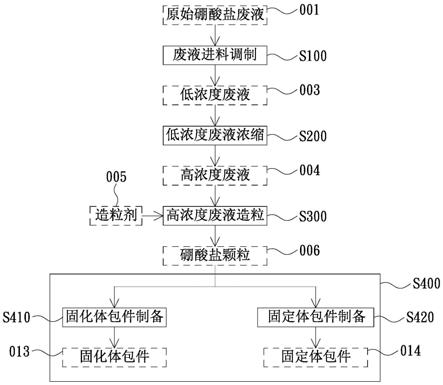
1.本发明涉及一种硼酸盐废液的处理方法,尤其涉及一种放射性硼酸盐废液的处理方法。
背景技术:
2.天然的硼元素含有约80%的硼-11和约20%的硼-10,其中硼-10是良好的中子吸收剂,因 此在压水式的核子反应炉(pressurized water reactor,pwr)中,硼酸被当作反应炉冷却水的中 子吸收剂,用以调节冷却水的中子密度。另外,硼酸也被添加在用过核燃料贮存池的水中, 以调节池水的中子密度。这些硼酸溶液在使用到期而废弃时,即被添加碱液(如氢氧化钠) 中和成为含硼酸钠的放射性废液,以下以硼酸盐废液称呼。放射性硼酸盐废液必须经过固化 处理,使其变成品质符合安全要求的固态废弃物体(solid waste form)后才可进行最终处置(finaldisposal),使其与人类的生活圈隔离,避免其放射性危害人类或环境。此处“最终处置”一词, 是放射性废弃物管理的专用词汇,指在合格的地质建造多重工程障壁(multiple engineeringbarriers)的设施以进行放射性废弃物的永久性隔离掩埋。
3.放射性硼酸盐废液的传统固化处理方法包括水泥固化法、高分子树脂固化法与柏油固化 法等,惟因高分子树脂与柏油等有机固化剂和无机盐类废液的相容性不佳,固化产生的固态 废弃物体会发生盐类析出现象,且高分子树脂与柏油会发生生物劣化现象,因此并不适用于 无机盐类废液的固化。
4.水泥固化法使用水泥和波索兰物料(pozzolanic materials)为固化剂,除了可通过水泥的水 合作用(hydration reaction)固化废液外,也能使无机盐类形成坚硬的固体。然而,使用水泥固 化法进行硼酸盐废液的固化时,当硼浓度较高(例如硼浓度>2wt%),会发生明显的固化阻 滞(solidification retardation)现象,水泥的水合作用(hydration reaction)会因水泥颗粒表面形成坚 硬的硼酸钙薄膜而受到阻碍。因此,传统上硼酸盐废液的水泥固化皆在低硼浓度下进行,或 在添加水泥进行固化之前,先添加熟石灰进行预先处理,以降低固化阻滞现象。另如美国专 利us 4,293,437、us 4,210,619、us 4,800,042、us 4,906,408与us 4,620,947,以及中国专利 cn 102800377a、cn 102254579b等,基本上采用添加碱性沉淀剂,将高水溶性的硼酸钠转 化为低水溶性硼酸盐沉淀后,再添加水泥或柏油进行固化以降低固化阻滞现象。然而,因(1) 所添加的碱性沉淀剂大幅增加了水泥废弃物体的数量,(2)废液固化时仍需使用大量的水泥固 化剂,使得水泥废弃物体体积大幅增加,而放射性废物的管理成本十分昂贵,并且最终处置 场用地难求,因此以传统水泥固化法处理硼酸盐废液不具经济性。
5.为了水泥固化体的减容及提高其硼含量,日本日挥公司(jgc corporation)曾开发所谓进步 型水泥固化法(advanced cement solidification process),在40℃至60℃温度下将石灰加入硼酸 盐废液中,进行约10小时的搅拌,使硼酸盐(一般为钠盐型态)转化为较安定的硼酸钙沉淀, 将沉淀过滤脱水后,再以水泥固化剂进行固化。惟所述法操作冗
长,并会产生含氢氧化钠的 二次废弃物(secondary waste)待处理。
6.此外,美国专利us 5,457,262将硼酸盐废液制备成高聚合度硼酸盐废液后再行水泥固化, 不会产生二次废弃物,可以提高废弃物体的硼荷载量,惟所述法所产出的水泥固化体的抗水 浸性较低,在抗水浸性要求严格的情况下应用上会受到限制。
技术实现要素:
7.本发明提供了一种硼酸盐废液的处理方法,可以不产生二次废弃物,并产出抗水性优良、 硼荷载量高的废弃物体,使其体积大幅减少,大幅降低管理的成本。
8.本发明所提供的硼酸盐废液的处理方法包括以下步骤:原始硼酸盐废液进料的调制使成 适合浓缩的低浓度废液;低浓度废液的浓缩使成高浓度废液;高浓度废液与造粒剂通过固化 作用进行造粒;可硬化浆的制备;废弃物体的制备,包括硼酸盐颗粒固化废弃物体(以下简 称固化体)与硼酸盐颗粒压缩块固定废弃物体(以下简称固定体)的制备。
9.原始的废液进料一般是收集自地面或设备的含硼卸水后,并经初步浓缩处理的含硼数百、 数千甚至数万ppm的低浓度硼酸盐废液,其再经以调节剂调制后,即成为适合进行高度浓缩 的低浓度废液。所述低浓度废液经浓缩制备成含高聚合度硼酸盐的高浓度硼酸盐废液(以下 简称高浓度废液)后,其与造粒剂(即固化剂)通过固化反应进行造粒时,并不发生固化阻滞 (solidification retardation)现象,因此大幅提升了废弃物体中的硼酸盐荷载量,大幅缩减了最终 产出的废弃物体的体积。此外,因使用高浓度硼酸盐废液造粒形成质地坚硬的硼酸盐颗粒, 再以可硬化浆进行固化处理后,即形成高机械强度、高耐水性的废弃物体。此处将硼酸盐颗 粒与可硬化浆混合制备成高机械强度、高耐水性的单块废弃物体(monolithic waste form)的程 序称为固化处理,是比照废离子交换树脂、污泥、残渣等细粒固体废弃物固化处理的习惯称 呼。以下的说明中也将沿用此习惯称呼。
10.上述说明仅是本发明技术方案的概述,为了能够更清楚了解本发明的技术手段,而可依 照说明书的内容予以实施,并且为了让本发明的上述和其他目的、特征和优点能够更明显易 懂,以下特举较佳实施例,并配合附图,详细说明如下。
附图说明
11.图1为本发明一实施例的硼酸盐废液处理方法的流程示意图。
12.图2为本发明方法的一实施例中制备固化体包件的流程示意图。
13.图3为本发明方法的一实施例中制备固定体包件的流程示意图。
具体实施方式
14.本发明提供一种硼酸盐废液的处理方法,如图1所示,包括步骤s100:废液进料调制, 即将原始硼酸盐废液001调制为组成条件符合后续浓缩处理的低浓度硼酸盐废液(以下简称 低浓度废液003);步骤s200:低浓度废液浓缩,以制备成含高聚合度硼酸盐的高浓度硼酸盐 废液(以下简称高浓度废液004);步骤s300:高浓度废液造粒,将高浓度废液制备成硼酸盐 颗粒006;步骤s400:废弃物体包件制备,依步骤s410(如图2)制备可硬化浆并用以进行 硼酸盐颗粒的固化,以制备固化体包件,或依步骤s420(如图3)制备可硬化浆,并将硼酸 盐颗粒压缩成压缩块并盛装于废弃物桶后,再用此可硬化浆进行灌注包覆,以制备固
定体包 件;此处所谓“包件”,是指废弃物体与废弃物盛装桶的总成。分别详述如下:
15.步骤s100废液进料调制:原始硼酸盐废液001,举例来说,可为来自核电厂的不同浓度 的硼酸钠废液。本发明可处理各种不同硼浓度的硼酸钠废液,来自核电厂的硼酸钠废液一般 皆会经过初步的蒸发预处理,进入本发明处理程序的原始硼酸盐废以硼浓度20,000ppm以上 为宜,以40,000ppm以上为较宜,可以减少本发明处理系统蒸发浓缩的负担。
16.步骤s100更包括例如调节来自核电站的原始硼酸钠废液中钠与硼的摩尔比。进一步来 说,可在原始硼酸钠废液中加入调节液并混合均匀以调节。调节液可为例如钠、钾、锂等的 氢氧化物溶液。使用氢氧化钠调节硼酸钠废液时,以使钠/硼的摩尔比为0.25~0.35为宜。步 骤s100还包括调节原始硼酸钠废液的酸碱值,调节剂可选用硼酸、硫酸、磷酸或氢氧化钠、 氢氧化钙、氢氧化钡等。
17.步骤s200低浓度废液浓缩:废液浓缩一般以加热方式进行,使用的装置为搅拌槽式蒸发 器、强制循环式蒸发器或薄膜蒸发器的至少一种,也可视需要同时并用。硼酸钠废液进料经 步骤s100调制后即成为低浓度废液003。本步骤s200是将低浓度废液003加以浓缩,使成 为溶解态含高聚合度聚合硼酸钠的废液004(以下称高浓度废液)。高浓度废液004以硼浓度 至少100,000ppm为宜,110,000ppm以上为较宜,以120,000ppm以上为最宜,但高浓度废 液004具黏稠性,需预防其发生堵塞或产生结晶。硼浓度较高有助于减容以及后续造粒时形 成机械强度较高、性能较佳的颗粒。然而,考量其黏稠性会造成输送困难与发生结晶堵塞的 虞虑,硼浓度以不高于130,000ppm为宜。
18.步骤s200制备完成的高浓度废液004,其钠与硼的摩尔比宜保持在0.25~0.35,而以 0.28~0.32为较宜。高浓度废液004贮放时需保持于适当的温度,以40~80℃为宜,较高温利 于防止产生结晶,惟太高温并不利于造粒产出的颗粒性能。因此贮放时可以保持在较高温度, 临造粒时再稍为降低温度。
19.步骤s300高浓度废液造粒:可使用选自例如水泥基物料(cementitious materials)、波索兰 物料(pozzolanic materials)、二价或二价以上碱土金属的氧化物或氢氧化物粉末、过渡金属的 氧化物或氢氧化物粉末、类金属的氧化物或氢氧化物粉末,或其组合的物料配制造粒剂005。 造粒剂005也可包含过渡金属或类金属的硅酸盐、磷酸盐、碳酸盐或复合盐类粉末,或其组 合。除以所述成分自行调制的造粒剂外,亦可径行选用合适的市贩污泥固化剂等。高浓度硼 酸钠废液与造粒剂是通过固化反应形成硼酸盐颗粒,反应中,液态的高聚合度聚合硼酸钠与 造粒剂产生固化反应而变成高强度的固态硼酸盐颗粒,颗粒的硼酸盐组成与机械强度主要由 造粒剂的成份所决定。
20.造粒装置可采用习知设备,亦可另行设计。因本发明实施例的高浓度废液004具黏稠性, 且步骤中的颗粒半成品具有高黏性,因此造粒装置的设计或材料的选用宜避免或减少前述物 料或半成品的沾黏。例如,采用滚筒式造粒装置或搅拌槽式造粒装置。滚筒式造粒装置的内 部构造简单,有助减少物料或半成品的沾黏。搅拌槽式造粒装置以滚筒式搅拌槽或具有行星 式公自转与自转搅拌叶者较佳,有助形成密实度高且机械强度佳的颗粒。
21.步骤s300的造粒步骤可包括初始造粒步骤s310以及连续造粒步骤s320。步骤s310为 在尚无颗粒情况下的造粒,需在造粒装置中预置造粒剂005,其数量需足以覆盖搅拌叶,预 置的造粒剂输入完成后即启动搅拌叶使造粒剂005翻滚流动,接着再分次缓慢加入预定量的 高浓度废液004。高浓度废液004与翻滚流动的造粒剂005粉末接触后会发生固化反
应,形 成硼酸盐颗粒006。预定量的高浓度废液输入完后,再持续搅拌3~5分钟,初始造粒即完成。 一般而言,步骤s310只需进行一次。步骤s320为在造粒装置中已有颗粒的情况下的造粒: 可将初始造粒得到的或先前制备好的硼酸盐颗粒006放置在造粒装置中,然后启动搅拌叶后, 以交叉的方式分别添加造粒剂与高浓度废液;添加两者的先后次序可以自由选择;两者添加 量的比例宜固定,以确保颗粒性质的均匀性。步骤s320可重复执行直至足够数量的颗粒制备 完成为止,如产出的颗粒达到造粒装置的容量限度时,可暂停造粒并取出部分颗粒成品后再 继续进行。
22.步骤s300所用的造粒剂005的总重量以小于高浓度废液004的总重量为佳,而步骤s310、 步骤s320或整个s300中造粒剂005用量与高浓度废液004用量间的比例可依造粒剂005的 硬化反应当量、造粒操作性、颗粒性能需求等而决定。此外,步骤s310为避免产生沾黏现象, 一般以使用较高比例的造粒剂005为宜。在步骤s320中,造粒剂005与高浓度废液004重量 的比大致为0.2~0.6。步骤s310、s320中搅拌的速度可依所用的造粒装置(如造粒装置类型)、 物料及半成品性质,以及欲得的颗粒大小而决定。举例言之,快速的搅拌可用于形成较小的 颗粒。较佳而言,本发明实施例的硼酸盐颗粒006具有2~5mm的直径。造粒装置可更包括 例如使用筛网以调节出料颗粒的大小。
23.步骤s400:废弃物体包件制备,其可包括步骤s410固化体包件制备,以及步骤s420固 定体包件制备。如图1~2所示,步骤s410包括可硬化浆制备,以及颗粒固化浆体制备及装桶。 可硬化浆009a可选自例如水泥浆、高性能混凝土浆、活性粉末混凝土(reactive powder concrete) 浆、石膏浆,以及由波索兰材料(pozzolanic material)粉末调制之高流动性浆体等之一,並以具 高流動性者為佳,其是以可硬化浆原料007a以及水与添加剂所调制的添加剂溶液008a进行 制备。颗粒固化浆体010的制备包括混合硼酸盐颗粒006(用于步骤s410的硼酸盐颗粒又以006a表示)及可硬化浆009a,使硼酸盐颗粒006a充分包埋于可硬化浆009a当中而成可硬化 的颗粒固化浆体010。所述颗粒固化浆体010注入容器例如废弃物桶012a(放射性废弃物盛 装桶)中,待浆体硬化后即形成颗粒固化体。步骤s410可再包括执行固化体的养护,以获得 成熟稳定的品质(于后详述)。颗粒固化体连同废弃物桶012a封盖后即成为固化体包件013。
24.如图3所示,步骤s420包括颗粒装桶、颗粒压缩块制备、颗粒压缩块装桶、可硬化浆制 备以及颗粒压缩块装桶后灌注可硬化浆固定。颗粒的装桶可使用普通容器012c。颗粒装桶后 可将普通容器012c连同硼酸盐颗粒006b进行压缩,而形成颗粒压缩块011。颗粒压缩块011 的装桶则使用废弃物桶012b。可硬化浆009b的制备与s410中可硬化浆009a的制备步骤相 同,不再重述。颗粒压缩块011的固定包括将可硬化浆009b注入装有数个颗粒压缩块011的 废弃物桶012b中,使可硬化浆009b充满空隙并包覆颗粒压缩块011形成压缩块固定体。步 骤s420亦可包括执行固定体的养护。压缩块固定体连同废弃物桶012b封盖后即成为固定体 包件014。
25.以下进一步通过实施例一~六例示本发明的硼酸盐废液的处理方法。
26.实施例一:
27.步骤s100~s200:取980克去离子水置入一个装设电动搅拌叶的6升玻璃烧杯中,并启 动电动加以搅拌。再取99%氢氧化钠833克与99%硼酸4,340克,分4次以先氢氧化钠、后 硼酸的方式缓慢将氢氧化钠、硼酸加进烧杯水中。待硼酸完全溶解后,以去离子水调整
型中,以震荡方式去除气泡并抹平表面后,再置于温度25℃、相对湿度95%的恒温恒湿箱中 进行28天养护。经计算,实施例一的可硬化浆重量为硼酸盐颗粒的1.04倍,所制得的废弃 物体的硼含量为3.86wt%,相当于22.07wt%的硼酸含量。固化浆体比重经测为1.87,因此 其硼荷载率为72.16kg/m3,相当于412.69kg/m3的硼酸荷载率。
35.固化浆体经养护28天后脱模,并将直径5公分的圆柱形固化体经切成高5公分后,依照 中国台湾低放射性废料体品质规范进行抗压强度、耐候性(抗冻融性)、抗水浸性等测试,此 外,也另进行9公尺坠落的抗冲击性测试,结果如表2所示。
36.表2:实施例一的固化体样品性能测试结果
37.测试项目抗压强度抗冲击性冻融测试抗水浸性测试结果10.3mpa合格10.85mpa11.2mpa
38.实施例二:
39.步骤s100~s200:依据实施例一的程序与方式制备模拟高浓度废液,其硼浓度及钠/硼摩 尔比如表3所示。
40.步骤s300:取市贩的污泥固化剂sta-110(环鼎国际公司产品)及试药级氢氧化钙粉末 以1:1的重量混合,再依实施例一的程序制备造粒剂粉末(造粒剂-b)。
41.步骤s300(s310~s320):依据实施例一的程序与方式,依表3的物料条件进行造粒,所 得的硼酸盐颗粒的硼含量为8.28wt%,相当于47.36wt%的硼酸含量。
42.表3:实施例二的物料条件
[0043][0044]
步骤s400:采用与实施例一相同的可硬化浆。依据实施例一的程序,采用可硬化浆/硼酸 盐颗粒为0.65的重量比进行颗粒固化浆体制备。所制得的固化浆体的硼含量为5.01wt%,相 当于28.64wt%的硼酸含量。经测所述固化浆体比重为1.87,因此其硼荷载率为93.65kg/m3, 相当于535.62kg/m3的硼酸荷载率。
[0045]
依实施例一的程序进行固化体样品制备及性能测试,结果如表4所示。
[0046]
表4:实施例二的固化体样品性能测试结果
[0047]
测试项目抗压强度抗冲击性冻融测试抗水浸性测试结果13.14mpa合格10.98mpa13.8mpa
[0048]
实施例三:
[0049]
步骤s100~s200:依据实施例一的程序与方式制备高浓度废液,所述高浓度废液的硼浓 度及钠/硼摩尔比如表5所示。
[0050]
步骤s300(s310~s320):依据实施例一的程序并依表5的物料条件使用造粒剂-b进行 造粒。所得的硼酸钠颗粒的硼含量为8.61wt%,相当于49.26wt%的硼酸含量。
[0051]
表5:实施例三的物料条件
[0052][0053]
步骤s400:采用与实施例一相同的可硬化浆。依据实施例一的程序,采用可硬化浆/硼酸 钠颗粒的重量比为0.82进行颗粒固化浆体的制备。再依实施例一的程序进行养护。所制得的 废弃物体的硼含量为4.73wt%,相当于27.07wt%的硼酸含量。经测所述固化浆体比重为1.86, 因此其硼荷载率为88.03kg/m3,相当于503.5kg/m3的硼酸荷载率。
[0054]
依实施例一的程序进行固化体样品制备及性能测试,结果如表6所示。
[0055]
表6:实施例三的固化体样品性能测试结果
[0056]
测试项目抗压强度抗冲击性冻融测试抗水浸性测试结果12.84mpa合格11.5mpa13.92mpa
[0057]
实施例四:
[0058]
步骤s100~s200:依据实施例一的程序与方式制备高浓度废液,所述高浓度废液的硼浓 度及钠/硼摩尔比如表7所示。
[0059]
步骤s300:以市贩的污泥固化剂sta-110(环鼎国际公司产品)40份与单水氢氧化钡 30份,依实施例一的程序制备造粒剂粉末(造粒剂-c)。
[0060]
步骤s300(s310~s320):依据实施例一的程序与方式,采表7的物料条件进行步骤 s310~s320。在步骤s320中,每次先加入高浓度废液200克、再添加造粒剂83克,如此回 圈交叉添加高浓度废液与造粒剂各50次后,因产生的颗粒已接近造粒装置容量限制,因此暂 停操作,取出一半重量的硼酸钠颗粒后再继续以同样的方式进行造粒,于再回圈交叉添加高 浓度废液与造粒剂各50次后停止,完成硼酸钠颗粒的造粒。步骤s320共计添加高浓度废液 与造粒剂各100次,总共添加高浓度废液20,000克、造粒剂8,300克。接着收集所有的硼酸 钠颗粒并混合,等待后续步骤。
[0061]
如表7所示,实施例四使用的造粒剂/高浓度废液的重量比平均为0.454,硼酸钠颗粒的 直径主要分布在2~5mm之间。经计算,颗粒的硼含量为8.26wt%,相当于47.25wt%的硼酸 含量。
[0062]
表7:实施例四的物料条件
[0063]
[0064]
步骤s400:使用市贩的核废处理专用固化剂ecocrete-rs(环鼎国际公司产品)40份、 石英粉35份及水25份,依实施例一的程序制备可硬化浆。接着,再依实施例一的程序,采 用可硬化浆/硼酸钠颗粒的重量比为1.12配制颗粒固化浆体。所制得的固化浆体的硼含量为 3.89wt%,相当于22.25wt%的硼酸含量。经测固化浆体的比重为1.87,因此其硼荷载率为 72.74kg/m3,相当于416.04kg/m3的硼酸荷载率。
[0065]
依实施例一的程序制作固化体样品,并在养护28天后进行性能测试,结果如表8所示。
[0066]
表8:实施例四的固化体的性能测试结果
[0067]
测试项目抗压强度抗冲击性冻融测试抗水浸性测试结果12.04mpa合格16.5mpa13.6mpa
[0068]
实施例五:
[0069]
步骤s100~s200:依据实施例一的程序与方式制备高浓度废液,所述高浓度废液的硼浓 度及钠/硼摩尔比如表9所示。
[0070]
步骤s300:以市贩的污泥固化剂sta-110(环鼎国际公司产品)52份、波特兰二型水泥 36份与试药级氢氧化镁12份、依实施例一的程序制备造粒剂粉末(造粒剂-d)。
[0071]
步骤s300(s310~s320):依据实施例四的程序,依表9的物料条件进行,其中造粒剂/ 高浓度硼酸钠废液的重量比平均为0.363。所得的硼酸钠颗粒的硼含量为8.81wt%,相当于 50.39wt%的硼酸含量。颗粒直径主要分布在2~5mm之间。
[0072]
表9:实施例五的物料条件
[0073][0074]
步骤s400:采用与实施例四相同的可硬化浆。依据实施例四的程序,采用可硬化浆/硼酸 钠颗粒为1的重量比进行颗粒固化浆体制备。所制得的固化浆体硼含量为4.41wt%,相当于 25.2wt%的硼酸含量。固化浆体比重经测为1.88,因此其硼荷载率为82.79kg/m3,相当于473.5 kg/m3的硼酸荷载率。
[0075]
依实施例一的程序进行固化体样品的制备、养护与性能测试,结果如表10所示。
[0076]
表10:实施例五的固化体样品性能测试结果
[0077]
测试项目抗压强度抗冲击性冻融测试抗水浸性测试结果11.38mpa合格12.55 mpa11.21mpa
[0078]
实施例六:
[0079]
步骤s100~s200:依据实施例一的程序与方式制备高浓度废液,所述高浓度废液的硼浓 度及钠/硼摩尔比如表11所示。本实施例为了测定固化体的抗浸出性,因此于高浓度废液中 添加200ppm的六水硝酸钴以及100ppm的硝酸铯并以其为实验组,对照组则不添
加六水硝酸 钴及硝酸铯。
[0080]
步骤s300(s310~s320):使用造粒剂-a。依据实施例一的程序,依表11的物料条件进 行步骤s300;实验组及对照组分别进行。所得的硼酸钠颗粒的硼含量为3.57wt%,相当于20.39 wt%的硼酸含量。
[0081]
表11:实施例六的物料条件
[0082][0083]
步骤s400:使用市贩的核废处理专用固化剂ecocrete-rs(环鼎国际公司产品)70份 及水30份,依实施例一的程序制备可硬化浆。接着,再依实施例一的程序,采用可硬化浆/ 硼酸钠颗粒重量比为1.10配制颗粒固化浆体;实验组及对照组分别进行。所制得的固化体浆 体的硼含量为3.57wt%,相当于20.39wt%的硼酸含量。固化浆体比重经测为1.86,因此其 硼荷载率为66.32kg/m3,相当于379.31kg/m3的硼酸荷载率。
[0084]
实验组及对照组分别依实施例一的程序进行固化体样品的制备、养护及性能测试,且使 用感应耦合等离子原子发射光谱仪(icp-oes)作抗浸出性测试时,浸出液中的钴与铯元素的定 量。实验组的性能测试结果如表12所示,且皆符合性能标准要求。对照组的浸出液中则未测 得钴与铯的存在。
[0085]
表12:实施例六固化体样品性能测试结果
[0086][0087]
实施例一~六都将硼酸钠颗粒依步骤s410形成颗粒固化体,惟如前所述,硼酸钠颗粒亦 可依步骤s420形成压缩块固定体;惟固定体的性能规范与固化体不同,一般要求须具备一定 厚度的安定性外包封层,本发明的实施例已充分证实所制备的各种可硬化浆,可形成性能优 良的硬化体,以其灌注包覆固定压缩块,足以产出性能优良的固定体。
[0088]
综上所述,本发明的处理方法可制备性能优良、高硼荷载率的废弃物体,达成废弃物的 减容。再者,相比于习知方法,本发明的造粒方法简单易行,不产生二次废液,可大幅降低 放射性废弃物的管理成本。
[0089]
以上所述,仅是本发明的较佳实施例而已,并非对本发明作任何形式上的限制,虽然本 发明已以较佳实施例公开如上,然而并非用以限定本发明,任何熟悉本专业的技术人员,在不脱 离本发明技术方案范围内,当可利用上述揭示的方法及技术内容作出些许的更动或修饰为等 同变化的等效实施例,但凡是未脱离本发明技术方案的内容,依据本发明的技术实质对以上 实施例所作的任何简单修改、等同变化与修饰,均仍属于本发明技术方案的范围内。
再多了解一些
本文用于企业家、创业者技术爱好者查询,结果仅供参考。