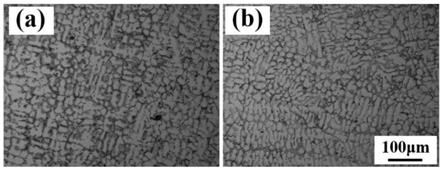
1.本发明涉及铝合金材料技术领域,特别是指一种高性能低碳铝合金与制备方法。
背景技术:
2.铝合金具有密度低、比强度高、耐腐蚀性能好及可回收利用等优点,广泛应用于汽车、航天等领域,但铝电解过程的高能耗和碳排放制约着行业的进一步发展。针对我国“碳达峰、碳中和”国家重大战略及“低碳铝”核心技术难题,再生铸造铝合金技术降低碳排放95%以上,具有良好的应用价值和发展前景。
3.铝硅系合金由于铸造性能好、缩孔倾向小、产品易于成型而成为最主要的铸造铝合金。但是fe元素的富集、粗大晶粒、微观孔洞及板片状共晶硅的存在阻碍性能提升。
4.cn102071341a公开了一种发动机缸盖用铸造铝硅合金及热处理工艺,合金化学成分按重量百分比为:si:5.0~7.0%;cu:3.0~4.0%;mg:0.2~0.4%;mn:0.1~0.3%;zr:0.10~0.20%;ti:0.15~0.25%;b:0.01~0.05%;sr:0.02~0.09%;re:0.1~0.3%;fe《0.3%;al:余量。稀土re采用混合稀土。其热处理工艺采用不同的500
±
5℃的一级固溶温度,520
±
5℃的二级固溶温度,最终抗拉强度为325~355mpa,强化效果不够明显。
5.cn113355567a公开了一种铝硅系铸造铝合金及其制备方法,包括如下成分及其重量含量:si:7.2~7.4%,mg:0.4~0.8%,b:0.003~0.007%,sr:0.005~0.01%,ti:0.05~0.15%,re:1~2%,cu≤0.1%,余量为al。其在铝硅合金中加入1~2%的re元素,可获得较高的韧性,但该技术添加了较多含量的稀土元素,富稀土相的析出制约性能提升,且不利于成本控制。
6.总之,铝硅系合金的力学性能仍然需要进一步提升。
技术实现要素:
7.本发明要解决的技术问题是提供一种高性能低碳铝合金与制备方法,其力学性能大大提升,能够满足汽车结构件制造与应用过程中的高要求,尤其是新能源汽车。
8.为解决上述技术问题,本发明提供如下技术方案:
9.第一方面提供一种高性能低碳铝合金,包括如下化学组成:以质量百分比计,si:6~8%,cu:3~5%,mg:0.2~0.6%,fe≤0.8%,mn:0.3~0.6%,ti:0.02~0.04%,la:0.05~0.15%,余量为al和不可避免的杂质。
10.优选地,以质量百分比计,si:7~8%,cu:3~4%,mg:0.2~0.4%,fe≤0.4%,mn:0.3~0.4%,ti:0.02~0.03%,la:0.06~0.14%,余量为al和不可避免的杂质。
11.其中,mn/fe含量之比为0.7~1。
12.其中,所述高性能低碳铝合金所形成铸件的性能满足:屈服强度达到400mpa以上,抗拉强度达到430mpa以上,硬度达到155hv以上,延伸率达到4%以上。
13.第二方面提供一种第一方面所述的高性能低碳铝合金的制备方法,包括:
14.s1:按所需化学组成配比原料,原料为纯铝和其他原料的中间合金;
15.s2:将原料进行预热;
16.s3:将预热后的原料进行熔炼、精炼,待所有原料熔化后进行浇注、冷却,得到铝合金铸件;
17.s4:将所述铝合金铸件进行固溶热处理,采用双级固溶工艺:一级固溶处理温度为400~450℃,一级固溶处理时间为4~10h,二级固溶温度为500~510℃,二级固溶处理时间为8~20h;
18.s5:将所述固溶热处理后的铝合金铸件进行水淬、人工时效,得到所述高性能低碳铝合金。
19.优选地,s4中,所述固溶热处理中控制升温速度为2-8℃/min。
20.优选地,s3中,所述熔炼的条件包括:熔炼温度在710-740℃,保温时间为10-20min。
21.优选地,s3中,所述精炼的条件包括:精炼时间为10~20min,然后扒去熔体表面浮渣,之后静置15~20min。
22.优选地,s2中,所述预热的条件包括:预热温度为180~200℃,预热时间为20~30min。
23.优选地,s5中,所述水淬使得降温至20~30℃;所述水淬后在170~180℃的热处理炉中进行人工时效处理6~18h。
24.优选地,该制备方法还包括:s3中,在待所有原料熔化后先保温10~15min,再进行所述浇注。
25.本发明的发明人经过大量研究发现,在常规铝硅系合金的基础上,从材料配方及制备方法的角度出发,通过调整微合金成分和工艺参数,能够细化组织及第二相,减小富铁相和微孔的危害,兼顾细晶强化、析出强化、第二相强化效果,开发一种高性能低碳铝合金,能够满足新能源汽车结构件对于性能更高的需求。该高性能低碳铝合金的制备方法既符合节能减排、绿色发展的理念,又充分考虑了成本,同时能够提升高性能低碳铝合金材料的综合力学性能。
26.具体地,本发明的上述技术方案的有益效果如下:
27.上述方案中,调整铝硅合金中si、mn、la等元素含量,能够减小铸造铝合金中粗大晶粒、富铁相、孔洞、粗大共晶硅的不利影响;其中,具体体现在:
28.1、通过调整mn元素的加入量,复合添加晶粒细化剂al-ti-b(b为不可避免的元素之一)和稀土la,显著减少了铸件中的孔洞数量与β-fe含量,促进共晶硅由板片状向珊瑚状转化,细化晶粒,兼顾铸件强度与塑性的同时提升;
29.2、适宜少量的la元素,能显著吸附合金铸件中的h,从而减少孔洞;la对粗大共晶硅具有一定程度的变质作用,促使共晶硅由板片状向珊瑚状转变,削弱其对基体的割裂作用。由于稀土元素是表面活性元素,铸造过程中会富集在固液界面,产生成分过冷,阻碍晶粒长大,增强细晶强化效果。但过量的稀土元素容易形成硬脆相,降低铸件塑性。本发明中la的添加量在充分发挥稀土有益作用的同时又不会产生原料的浪费和性能损害。
30.本发明提供的高性能低碳铝合金铸件的屈服强度达到400mpa以上,抗拉强度达到430mpa以上,硬度达到155hv以上,延伸率达到4%以上。本发明符合国家“碳达峰、碳中和”的重大战略,制造过程无污染,碳排放不到电解铝生产高性能铝合金结构件的5%,彻底解
决再生铝合金无法应用于高端产品的瓶颈难题,提高了铸锭内部组织致密性、消除微孔聚集和粗大第二相引起应力集中等工程技术难题。
31.在本发明的优选方案中,具有适宜mn/fe含量之比,其中mn元素可在一定程度上取代富铁相中的fe原子,减小富铁相的危害;适量的mn元素可促使铁化物由针状向骨架状转变,进一步提升所得材料的力学性能。而过量的mn元素会导致富fe相的体积分数增加,从而恶化其力学性能。
32.关于本发明的制备方法,其利用热处理工艺能够进一步提升材料的力学性能,尤其是采用双级固溶处理工艺,其中,4~10小时的400~450℃保温促使低熔点非平衡共晶相提前发生溶解,而在二级固溶处理中,500~510℃单级固溶不会溶解的粗大第二相在相同的温度下开始融入基体而不会发生过烧,增大合金过饱和度,提升时效强化效果。
附图说明
33.图1为本发明实施例1、实施例2中合金腐蚀后的微观组织形貌,用于观测和量化合金二次枝晶臂间距,其中:(a)为实施例1对应的光镜照片,(b)为实施例2对应的光镜照片。
34.图2为本发明实施例1、实施例2中合金的共晶硅变质后的微观组织形貌,其中:(a)为实施例1对应的光镜照片,(b)为实施例2对应的光镜照片。
35.图3为本发明实施例1、实施例2中合金的微观组织形貌,用于观察铁化物形态转变,其中:(a)为实施例1对应的sem电镜图像,(b)为实施例2对应的sem电镜图像。
具体实施方式
36.为使本发明要解决的技术问题、技术方案和优点更加清楚,下面将结合附图及具体实施例进行详细描述。
37.第一方面提供一种高性能低碳铝合金,包括如下化学组成:以质量百分比计,si:6~8%,cu:3~5%,mg:0.2~0.6%,fe≤0.8%,mn:0.3~0.6%,ti:0.02~0.04%,la:0.05~0.15%,余量为al和不可避免的杂质。
38.在本发明的高性能低碳铝合金中,al、si、cu、mg作为基本组元,mn、ti、la为添加组元,特别的针对铸造铝合金中fe元素的富集问题添加适量的mn,并选择适量的稀土元素la与细化剂al-ti-b(b为不可避免的杂质之一)复合添加,基于他们的协同调控作用来优化合金组织结构,从而提升高性能低碳铝合金的综合力学性能。
39.上述各组元的作用包括:
40.al、si、cu、mg为合金的基本组元,si的加入可降低和避免热裂,提升合金的铸造性能;cu元素有一定的固溶强化效果,此外时效析出的al2cu有显著的时效强化作用;mg元素提升铸件的抗拉强度。其中,si可以选自6%,6.5%,7%,7.5%,8%中的任意值以及相邻点值之间的任意值,cu可以选自3%,3.5%,4%,4.5%,5%中的任意值以及相邻点值之间的任意值,mg可以选自0.2%,0.3%,0.4%,0.5%,0.6%,0.7%,0.8%中的任意值以及相邻点值之间的任意值。
41.mn、ti、la作为添加组元,对组织和性能调控有积极作用,mn是高效的fe中和元素,促使β-fe向α-fe转化,减小β-fe对基体的割裂作用,减小应力集中;la对铸件组织有多方面的优化功能,la对h元素有很强的吸附作用,可显著减少气孔数量;la元素富集在固液界面
前端,阻碍晶粒长大,与ti复合添加,增强细晶强化效果,同时兼顾强度和塑性的提升;la元素对粗大片状共晶硅有一定的变质作用,加入少量的la就能促使共晶硅由板片状向珊瑚状、颗粒状转变;此外,与mn类似,la元素也能促使富铁相向危害更小的类型转化从而减小危害。其中,mn可以选自0.3%,0.35%,0.4%,0.45%,0.5%,0.55%,0.6%中的任意值以及相邻点值之间的任意值,ti可以选自0.02%,0.03%,0.035%,0.04%中的任意值以及相邻点值之间的任意值,la可以选自0.05%,0.07%,0.1%,0.13%,0.15%中的任意值以及相邻点值之间的任意值。
42.优选情况下,以质量百分比计,si:7~8%,cu:3~4%,mg:0.2~0.4%,fe≤0.4%,mn:0.3~0.4%,ti:0.02~0.03%,la:0.06~0.14%,余量为al和不可避免的杂质。
43.优选地,mn/fe含量之比为0.7~1。该优选方案下,mn元素可在一定程度上取代富铁相中的fe原子,减小富铁相的危害;适量的mn元素可促使铁化物由针状向骨架状转变,进一步提升所得合金材料的力学性能。而过量的mn元素会导致富fe相的体积分数增加,从而恶化其力学性能。
44.其中,所述高性能低碳铝合金所形成铸件的性能满足:屈服强度达到400mpa以上,抗拉强度达到430mpa以上,硬度达到155hv以上,延伸率达到4%以上。
45.第二方面提供一种第一方面所述的高性能低碳铝合金的制备方法,包括:
46.s1:按所需化学组成配比原料,原料为纯铝和其他原料的中间合金;
47.s2:将原料进行预热;
48.s3:将预热后的原料进行熔炼、精炼,待所有原料熔化后进行浇注、冷却,得到铝合金铸件;
49.s4:将所述铝合金铸件进行固溶热处理,采用双级固溶工艺:一级固溶处理温度为400~450℃,一级固溶处理时间为4~10h,二级固溶温度为500~510℃,二级固溶处理时间为8~20h;
50.s5:将所述固溶热处理后的铝合金铸件进行水淬、人工时效,得到所述高性能低碳铝合金。
51.在s1中,可以理解的是,其他原料的中间合金包括:铝硅、铝铁、铝锰、铝铜、铝镧、铝镁和铝钛硼等中间合金。
52.本发明中,一般地,除了按照所得材料的组成进行配料,还应考虑各个制备步骤中的损耗或积累,例如考虑mg元素20%的烧损及fe元素在中间合金中的积累。其为本领域所公知,在此不再赘述。
53.本发明中,本领域技术人员可以根据需要对原料进行预处理,包括但不限于将所有原料进行表面打磨抛光、超声震荡等预处理,以去除氧化物和杂质。
54.优选地,s2中,所述预热的条件包括:预热温度为180~200℃,预热时间为20~30min。
55.本领域技术人员可以根据需要选用上述各个步骤所需采用的设备,包括但不限于模具、坩埚及夹具等。优选将所需设备进行所述预热,经充分干燥后进行使用。优选地,将所采用的坩埚提前经过130-160℃加热20-30min,用氮化硼涂料在坩埚内表面进行涂覆处理,然后在所述熔炼前进行所述预热。
56.优选地,s3中,所述熔炼的条件包括:熔炼温度在710-740℃,优选720-740℃。该优
选方案下,熔炼温度适宜,更能促进晶粒适宜增长,避免偏析,从而更利于所得合金的力学性能的提升。而当熔炼温度过高,合金短时间内烧损严重,且会促使晶粒粗大,当熔炼温度过低时,金属液偏析较为严重。
57.优选地,s3中,所述熔炼的条件包括:保温时间为10-20min。
58.可以理解的是,在进行所述熔炼之后,随即进行所述精炼,故精炼的温度与熔炼温度相同。
59.优选地,s3中,所述精炼的条件包括:精炼时间为10~20min,然后扒去熔体表面浮渣,之后静置15~20min。
60.本领域技术人员可以在所述熔炼和所述精炼中分别加入保护剂或添加剂,来对合金熔体进行保护,或促进熔炼和精炼。优选地,在所述精炼中加入覆盖剂和精炼剂,所述覆盖剂和精炼剂的用量各自独立地为原料总量的0.5~1wt%。
61.本领域技术人员可以根据需要确定各原料的加入时间。一般地,在所述熔炼中先加入纯铝、铝硅、铝铁、铝锰、铝铜中间合金,然后在所述精炼之后再扒去表面浮渣的熔体中依次加入铝镧、铝镁和铝钛硼中间合金,搅拌(优选搅拌3~5min),然后进行所述浇注。
62.优选地,该制备方法还包括:s3中,在待所有原料熔化后先保温10~15min,再进行所述浇注。
63.本领域技术人员可以根据需要确定所述浇注的温度,例如在730℃左右。
64.优选地,s4中,所述固溶热处理中控制升温速度为2-8℃/min。
65.优选地,s5中,所述水淬使得降温至20~30℃;所述水淬后在120~180℃、优选170~180℃的热处理炉中进行人工时效处理6~18h。
66.s5中,所述冷却优选为空冷。
67.本发明的高性能低碳铝合金能够满足新能源汽车部件的高要求。
68.下面通过实施例对本发明进行详细的阐述。
69.实施例1
70.一种高性能低碳铝合金,其化学成分按质量百分比计为:si 7.23%、cu 3.38%、mg 0.26%、fe 0.39%、mn 0.38%、ti 0.02%,la 0.07%,其余为al和不可避免的杂质。
71.上述合金的制备方法,按如下步骤:
72.s1、原料选择:按上述高性能低碳铝合金成分进行配比,原料为纯铝和其他原料的中间合金;
73.s2、预处理:所有原料进行表面打磨抛光及超声震荡预处理,去除氧化物和杂质的影响;熔炼前,将原料、模具、坩埚、夹具及覆盖剂在200℃下预热20分钟,经充分干燥后进行使用;
74.s3、熔炼:将步骤s2预热后的原料中纯铝、铝硅、铝铁、铝锰、铝铜中间合金,依次加入炉内,炉内温度升至730℃,保温15min,得到熔体;
75.s4、铝液处理:将步骤s3的熔体充分搅拌后,加入用量为原料总质量0.8wt%的覆盖剂(具体由nacl 43.5wt%和kcl 56.5wt%组成,易潮解需提前预热)和用量为原料总量0.8wt%的精炼剂(具体为六氯乙烷,不必预热),精炼10min后扒去浮渣,之后静置15min;
76.s5、中间合金加入:向步骤s4中扒去浮渣的熔体中依次加入铝镧、铝镁和铝钛硼中间合金,搅拌3min;
77.s6、浇注:直至步骤s5中加入的中间合金都完全熔化后,再保温10min,730℃下进行浇注,待冷却后取出高性能低碳铝合金铸件;
78.s7、固溶热处理:对s6取出的铸件转移至预热的热处理炉中进行固溶热处理:炉内升温速度为5℃/min,采用双级固溶工艺,一级固溶处理温度为450℃,处理时间为4小时,二级固溶温度为500℃,固溶时间为8小时;
79.s8、时效处理:固溶处理后进行水淬,水淬降温至25℃,后转移至180℃的热处理炉中进行人工时效处理7小时,时效后进行空冷,冷却至室温。
80.对所得铝合金取样进行腐蚀处理,具体采用凯勒试剂(95wt%h2o、2.5wt%hno3、1.5wt%hcl和1.0wt%hf)蚀刻样品,持续时间8s。腐蚀处理后的光镜照片、共晶硅变质后的光镜照片分别如图1、图2中的图(a)。经上述s7、s8处理后样品的sem电镜图像如图3中的图(a)。每个样品二次枝晶臂间距取30个样本数据,统计出平均值,共晶硅平均当量直径与圆度量化统计各采用8张图片。结果显示,实施例1中的二次枝晶臂间距平均值为13.89μm,共晶硅平均当量直径为3.59μm,平均圆度为0.46。
81.对所得铝合金进行力学性能测试,其中,拉伸性能测试在suns utm6104电子万能拉伸机室温下进行,应变速率为1mm/min,实验结果取3个试样的平均值;显微硬度测试使用数字显微硬度计(tmvs-1),载荷设置为200gf,保持时间为10s,每个样品重复测试10次,取平均值。结果测得:屈服强度达到406.65mpa,抗拉强度达到432.17mpa,延伸率为4.4%,硬度达到160.47hv。
82.实施例2
83.一种高性能低碳铝合金,其化学成分按质量百分比计,si:7.29%、cu:3.49%、mg:0.28%、fe:0.38%、mn:0.37%、ti:0.02%,la:0.11%,其余为铝和不可避免的杂质。合金的制备方法按实施例1的工艺步骤进行。
84.按照实施例1的方法对所得铝合金取样、处理、测试,腐蚀处理后的光镜照片、共晶硅变质后的光镜照片、热处理后的sem电镜图像分别如图1、图2、图3中的图(b)。结果显示,实施例2中的二次枝晶臂间距平均值为13.42μm,共晶硅平均当量直径为3.63μm,平均圆度为0.47。
85.按照实施例1的方法对所得铝合金进行力学性能测试,结果测得:屈服强度达到403.13mpa,抗拉强度达到438.49mpa,延伸率为4.8%,硬度达到162.35hv。
86.实施例3
87.一种高性能低碳铝合金,其化学成分按质量百分比计为:si 7.29%、cu 3.48%、mg 0.27%、fe 0.37%、mn 0.69%、ti 0.02%,la 0.05%,其余为al和不可避免的杂质。
88.按照实施例1的方法对本实施例所得合金进行相应测试。
89.结果显示,二次枝晶臂间距平均值为13.97μm,共晶硅平均当量直径为3.63μm,平均圆度为0.47。
90.力学性能测试结果:屈服强度达到403.25mpa,抗拉强度达到425.57mpa,延伸率为3.5%,硬度达到155.82hv。
91.实施例4
92.一种高性能低碳铝合金,其化学成分按质量百分比计为:si 7.38%、cu 3.52%、mg 0.26%、fe 0.39%、mn 0.38%、ti 0.02%,la 0.18%,其余为al和不可避免的杂质。
93.按照实施例1的方法对本实施例所得合金进行相应测试。
94.结果显示,二次枝晶臂间距平均值为13.40μm,共晶硅平均当量直径为3.64μm,平均圆度为0.47。
95.力学性能测试结果:屈服强度达到402.58mpa,抗拉强度达到428.66mpa,延伸率为3.9%,硬度达到162.77hv。
96.实施例5
97.按照实施例1进行,不同的是,熔炼温度在690℃。
98.按照实施例1的方法对本实施例所得合金进行相应测试。
99.结果显示,二次枝晶臂间距平均值为13.42μm,共晶硅平均当量直径为3.71μm,平均圆度为0.48。
100.力学性能测试结果:屈服强度达到406.05mpa,抗拉强度达到435.94mpa,延伸率为3.6%,硬度达到161.83hv。
101.对比例1
102.按照实施例1进行,不同的是,固溶热处理中,一级固溶处理温度为500℃,二级固溶温度为520℃。此时固溶温度过高,样品出现过烧现象,因此二级固溶温度不超过510℃。
103.以上所述是本发明的优选实施方式,应当指出,对于本技术领域的普通技术人员来说,在不脱离本发明所述原理的前提下,还可以做出若干改进和润饰,这些改进和润饰也应视为本发明的保护范围。
再多了解一些
本文用于企业家、创业者技术爱好者查询,结果仅供参考。