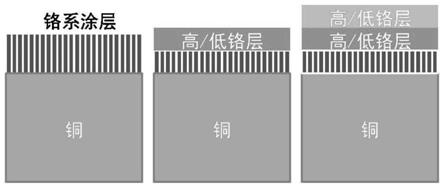
1.本发明涉及防护涂层技术领域,特别涉及一种铜导体用低互扩散、抗高温氧化涂层及其制备方法。
背景技术:
2.铜及铜合金电阻率低、导热性好、加工性能优异,广泛应用在电力传输、电机、线圈、微电子连接及轨道交通等领域。然而,高温空气中(》200℃)铜极易被氧化,且生成的氧化膜不具有保护性,氧化速率较高,特别是在400℃以上,铜导线将被迅速氧化,失去导电性,限制了其在高温导电领域的应用。当前先进动力装备对高温电力传输、电磁线圈的需求呈不断增加的趋势,如何提升铜导体抗氧化性能,确保其稳定的高温导电性能,是满足先进动力装备发展要求迫切需要解决的难题。
3.为改善400℃以上铜的抗氧化能力及维持其高导电性,可通过施加防护涂层获得,通常抗氧化涂层与铜在高温下发生严重元素互扩散,从而导致其电导率下降明显。铜导体抗高温氧化涂层的难点在于,如何在具有优异抗高温氧化的前提下涂层组元不向铜基体发生扩散。
4.施加al层或添加al元素制备铜铝合金可显著改善铜的抗氧化性,但由于cu与al固溶度大且存在多种中间化合物相,在高温服役中由于互扩散或中间化合物相的生成会增大铜的电阻率,甚至影响到其机械性能。对铜导体进行渗铝处理可大幅提升其抗氧化性能,但al元素内扩散严重,会大幅降低铜导体特别是微细铜导线的导电性[参见文献:马壮,董书琳,董世知,李智超,纯铜热喷涂陶瓷/渗铝复合涂层的制备及耐磨性研究,材料导报,2011,25:70-76.]。汤优钢等采用铜线表面镀锌的方案[参见文献:汤优钢,林家弘,一种具有超强抗氧化能力的镀锡软铜绞线,专利申请号:cn107146651a],由于锌的低熔点及与铜易于扩散特性,其抗氧化能力及长期使用条件将不超过200℃,无法满足400℃以上高温使用要求。同样抗氧化性较好的ni或si元素也存在与cu固溶度较大的问题。因而,如何在增强铜抗氧化性的同时避免元素扩散可能引起的电阻率增大是铜在高温电力系统应用中需解决的问题。
[0005]
基于cu与cr几乎不相溶的特性,以cr为主要成分的涂层高温下其与cu间不发生元素互扩散行为,同时cr具有优异的抗氧化能力,可满足铜导体高温防护的要求。常延丽等采用冷喷涂cu-cr复合粉末加高温退火的方法获得了cr颗粒弥散分布的cu-cr复合涂层[参见文献:常延丽,王金龙,梁苗苗,付翀,王亚平,张宏伟,刘德华,一种铜铬复合涂层的制备方法,专利申请号:cn112195462a],然而涂层表面大部分铜组分裸露与空气中,导致该涂层高温下无法形成保护性氧化膜,进而高温防护性能不足。
技术实现要素:
[0006]
本发明的目的是为了解决先进动力装备中铜导体抗氧化不足且易与涂层互扩散导致性能恶化的难题,特提供了一种铜导体用低互扩散、抗高温氧化涂层及其制备方法。
[0007]
本发明提供了一种铜导体用低互扩散、抗高温氧化涂层,其特征在于:所述的铜导体用低互扩散、抗高温氧化涂层化学成分为纯铬或铬原子百分比不低于95%的铬合金,其组织结构为单一择优取向的单层或多层细晶组织。
[0008]
铬合金中能加入的增韧合金组元包括但不限于金属组元如ag、fe、ti、zr或其组合,以及非金属组元si、n、o、c或其组合,所述组元总原子百分比不超过5%。
[0009]
涂层晶粒度不大于500nm,优化的晶粒度为5~100nm。
[0010]
优化的择优取向为200晶面。
[0011]
铜导体用低互扩散、抗高温氧化涂层厚度为0.05~15μm,优选为0.1~10μm。
[0012]
一种铜导体用低互扩散、抗高温氧化涂层的制备方法,其特征在于:在真空中进行,通过密度不低于4.6
×
10
20
m-2
s-1
、荷能在90~900ev范围的铬离子流轰击方法在零件表面沉积涂层。
[0013]
制备过程需要采用铬离子源,所述离子源符合如下要求:离子产生方法包括但不限于真空电弧蒸发源,优选为真空电弧蒸发源,弧电流为70~300a,优选为80~240a。
[0014]
沉积过程中需要在零件表面施加负脉冲偏压,所述脉冲符合如下要求:偏压峰值为-30~-300v,优选为-100~-250v;脉冲偏压占空比15~60%,优选为20~30%;脉冲偏压频率5~40khz,优选为20~40khz。
[0015]
制备过程中在ar或he或其组合气氛,通气前真空度小于0.005pa,通气后真空度0.005~2pa,优选为0.005~0.5pa。
[0016]
制备过程中零件温度范围为50~480℃,优选为80~380℃。
[0017]
基于cu与cr几乎不相溶的特性,以cr为主要成分的涂层高温下其与cu间不发生元素互扩散行为,同时cr具有优异的抗氧化能力,可满足铜导体高温防护的要求。常延丽等采用冷喷涂cu-cr复合粉末加高温退火的方法获得了cr颗粒弥散分布的cu-cr复合涂层[参见文献:常延丽,王金龙,梁苗苗,付翀,王亚平,张宏伟,刘德华,一种铜铬复合涂层的制备方法,专利申请号:cn112195462a],然而涂层表面大部分铜组分裸露与空气中,导致该涂层高温下无法形成保护性氧化膜,进而高温防护性能不足。
[0018]
本发明采用高cr含量体系作为防护涂层,高温下既能实现表面氧化铬的形成,达到抗氧化目的,又能维持与铜的界面稳定性,同时达到不降低铜导体导电能力的目的。铬基涂层可采用湿法电镀制备,也可采用干法真空镀膜制备。为避免电镀铬工艺污染及电镀涂层结合力不足等问题,推荐采用真空镀膜方法制备该涂层。真空镀膜方法包括但不限于磁控溅射、多弧离子镀、电子束蒸发,优选为多弧离子镀,该方法具有沉积效率高、膜基结合力强等独特优势,广泛用于多种类高性能涂层的制备,是制备本发明涂层的优选技术。
[0019]
本发明的优点:
[0020]
本发明所述的铜导体用低互扩散、抗高温氧化涂层及其制备方法,不仅能够显著解决铜导体高温应用时面临的严重氧化问题,而且能够解决其他类高温防护涂层应用于铜导体时涂层/基体互扩散导致的导电性能下降的难题。涂层表面光滑,组织致密,该铬基涂层应用于400℃以上服役的铜导体,综合服役效果远优于其他如镍基防护涂层、渗铝、热喷涂涂层等常见防护涂层体系。
[0021]
制备方法工艺较简单,工艺稳定性和可控性高,多种铬基涂层均可高效制备,工艺过程绿色无污染,不存在如电镀工艺废水废气排放问题;同时适合各种铜导体制品,如块状
零部件、铜导线等的涂层制备。
附图说明
[0022]
下面结合附图及实施方式对本发明作进一步详细的说明:
[0023]
图1为铬系涂层的表面(a)及截面(b)扫描电镜照片;
[0024]
图2为纯铜基体与铬系涂层在600℃空气中氧化后的宏观形貌图片;
[0025]
图3为纯铜基体(a)与铬系涂层(b)(c)在600℃空气中氧化后的截面扫描电镜照片;
[0026]
图4为铬系涂层在600℃空气中氧化1000小时后的面扫成分分布图;
[0027]
图5为铬系涂层在600℃空气中氧化1000小时后的明场像透射照片(a)及其红线位置处的线扫成分分布图(b)。
[0028]
图6为单层、双层及多层铬系涂层结构示意图。
具体实施方式
[0029]
实施例1
[0030]
本实施例对多弧离子镀制备铜导体用低互扩散、抗高温氧化涂层及其制备方法进行说明。首先将纯铬靶安装于阴极水冷靶套,将铜片基体挂于靶前,关闭真空室门,进行抽气;腔室背底真空度达到10-3
pa级或更低时,打开压强阀向真空室内通入ar气使真空度维持在2~3pa时,偏压设定在-700v~-1000v范围内对基体表面进行辉光清洗10分钟左右,随后关闭压强阀使真空度维持在10-3
pa;采用接触法由引弧针直接引燃阴极电弧。本例采用电弧电流200a,脉冲偏压-100v,占空比20%,时间20min。由此得到的沉积态cr层的表面及截面扫描照片如图1所示。涂层表面平滑均匀,零星分散着小熔滴。涂层截面致密,与基体结合良好,界面及涂层内部无明显孔隙存在。涂层厚度约为3.5微米。
[0031]
对涂层与未保护的铜基体的高温氧化性能进行了对比。图2展示了纯铜基体和涂层氧化后的宏观形貌。可以看出,纯铜基体在600℃仅氧化1小时后就出现了严重的剥落与分层,甚至暴露出铜基体,可见其高温下不具备防护能力。相比之下,铬层保护的铜基体在氧化500和1000小时后氧化膜完整地生长在样品表面,很好地保护了铜基体。图3展示了基体和涂层氧化后的扫描截面照片。可以看出铜氧化1小时后生成了厚约16微米的双层氧化膜,且残留的氧化膜和基体由于热膨胀系数差异在界面处发生了脱附。而铬层氧化1000小时后生成的氧化膜厚度接近1微米左右,远低于基体氧化膜的厚度,且氧化膜与涂层、涂层与基体保持良好的结合。可见,铜的抗高温氧化性能在铬层保护下得到了明显改善。
[0032]
对涂层1000小时氧化后的截面成分分布进行了表征。从图4可以看出涂层与铜基体界面处的cu和cr的成分分布保持着清晰明确的界面,没有发生明显的铜向铬层或者铬向基体的扩散。图5给出的透射明场像和对应线扫成分分布图表明涂层与基体界面处扩散深度低于100纳米。这一结果表明高温下不会发生可能由扩散引起的铜基体的电阻率增大,保证了铜在高温应用中电阻率稳定。
[0033]
实施例2
[0034]
本实施例对多弧离子镀制备铜导体用低互扩散、抗高温氧化涂层及其制备方法进行说明。首先将纯铬靶安装于阴极水冷靶套,将铜件挂于靶前,关闭真空室门,进行抽气;腔
室背底真空度达到10-3
pa级或更低时,打开压强阀向真空室内通入ar气使真空度维持在2~5pa时,偏压设定在-700v~-1000v范围内对基体表面进行辉光离子刻蚀10分钟左右,随后关闭ar气,通入氮气使真空度维持在0.1~0.5pa;采用接触法由引弧针直接引燃阴极电弧。本例采用电弧电流150a,脉冲偏压-80v,占空比40%,时间30min。由此得到cr-n涂层。
[0035]
此外,涂层沉积期间,以氧气、或甲烷、乙炔气体单独或混合通入或替代氮气,可得到含o、c、n的涂层。
[0036]
实施例3
[0037]
本实施例对多弧离子镀制备铜导体用低互扩散、抗高温氧化多组元涂层及其制备方法进行说明。首先将铬合金靶安装于阴极水冷靶套,铬合金靶含有al、ni、ag、si、fe、ti、zr的一种或其组合,其总含量为原子比0-50%。将铜件挂于靶前,关闭真空室门,进行抽气;腔室背底真空度达到10-3
pa级或更低时,打开压强阀向真空室内通入ar气使真空度维持在2~5pa时,偏压设定在-500v~-700v范围内对基体表面进行辉光离子刻蚀2分钟左右,随后关闭ar气采用接触法由引弧针直接引燃阴极电弧。本例采用电弧电流200a,脉冲偏压-60v,占空比30%,时间10min。由此得到铬合金涂层。此外,还可通入氧气、或甲烷、乙炔、氮气使真空度维持在0.02~0.5pa,得到含o、c、n的铬合金涂层。
[0038]
实施例4
[0039]
本实施例对多弧离子镀制备铜导体用低互扩散、抗高温氧化涂层多种结构制备方法进行说明。首先将高铬和低铬合金靶安装于两个或多个阴极水冷靶套,高铬合金靶含铬原子百分比90-100%,低铬合金靶含铬原子百分比50-80%。铬合金靶含有al、ni、ag、si、fe、ti、zr的一种或其组合,其总含量为原子比0-50%。将铜件挂于靶前,关闭真空室门,进行抽气;腔室背底真空度达到10-3
pa级或更低时,打开压强阀向真空室内通入ar气使真空度维持在2~5pa时,偏压设定在-500v~-700v范围内对基体表面进行辉光离子刻蚀2分钟左右,随后关闭ar气采用接触法由引弧针直接引燃高铬靶阴极电弧。本例采用电弧电流200a,脉冲偏压-60v,占空比30%,时间5min。由此得到高铬涂层底层。然后,关闭该高铬靶电源,开启低铬靶电源,进行低铬涂层沉积,由此得到双层结构的铬基涂层。依次方法,可获得多层结构的铬基合金涂层,涂层结构示意图如图6所示。
[0040]
本发明未尽事宜为公知技术。
[0041]
上述实施例只为说明本发明的技术构思及特点,其目的在于让熟悉此项技术的人士能够了解本发明的内容并据以实施,并不能以此限制本发明的保护范围。凡根据本发明精神实质所作的等效变化或修饰,都应涵盖在本发明的保护范围之内。
再多了解一些
本文用于企业家、创业者技术爱好者查询,结果仅供参考。