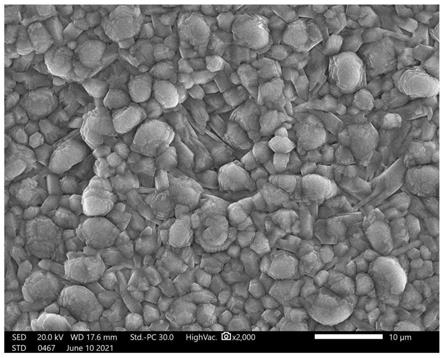
1.本发明属于金属材料表面处理领域,具体涉及一种提高冷轧汽车板表面可涂装性能的方法。
背景技术:
2.汽车钢板在涂装前要进行磷化处理,其目的是在钢板表面形成均匀致密的磷化膜,从而提高提高表面耐腐蚀性能和增强底漆的附着力。因此,磷化钢板的可涂装性能也是衡量其能否广泛应用于汽车的重要指标。汽车钢板表面磷化反应过程决定其磷化成膜质量,发生均匀的磷化反应不仅要求涂装前基板需化学成份、组织结构分布均匀,表面无明显的元素富集,表面洁净度高,无任何污染及缺陷,无锈蚀,基板表面还需有较高的表面能和一定的粗糙度值,促进磷化形核反应,降低形核势垒,而且还需严格控制表调、磷化液组分,成膜条件。
3.2016年3月23日cn105420607a公开了一种提高冷轧汽车板可涂装性能表面质量的控制方法,通过控制了冷轧汽车板的元素分布情况、氧化状态及表面粗糙度等提高冷轧汽车板可涂装性能。2020年9月11日cn111647733a公开了一种提高低碳铝镇静钢汽车板磷化性能的方法、汽车板,通过控制铸坯成分、热轧、冷轧、退火和平整工艺,提升了钢板表面质量,进而对提高低碳铝镇静钢汽车板磷化性能。
4.以上方法都忽视了涂装前基板残留物、防锈油的清洗难易程度,基板表面活性大小,磷化液成分及成膜条件对磷化成膜质量的影响。因此,研究一种新的提高冷轧汽车板表面可涂装性能的方法,很有必要。
技术实现要素:
5.本发明所要解决的技术问题是现有方法提高冷轧汽车板可涂装性能较差的问题。
6.本发明解决其技术问题所采用的技术方案是:提高冷轧汽车板表面可涂装性能的方法,所述方法的工艺流程为冶炼铸造
→
热轧卷取
→
酸洗冷轧
→
连续退火
→
平整涂油
→
除油酸洗
→
表面调整
→
磷化处理。
7.上述冶炼铸造工序中,按照化学成分冶炼浇注成铸坯,所述化学成分按质量百分比为c≤0.25%,si≤0.30%,0.05%≤mn≤3%,p≤0.01%,s≤0.01%,al≤0.02%,n≤0.01%,as sn≤0.02%,余量为fe及不可避免的杂质。
8.上述热轧卷取工序中,将铸坯加热至1150-1300℃保温2-4h后轧制,终轧温度≥850℃;轧制后卷取,卷取温度为400-600℃,得到热轧卷。
9.上述酸洗冷轧工序中,酸洗速度为80-120m/min,冷轧压下率为40-60%,乳化液皂化值为100-200mgkoh/g,乳化液温度为50-70℃,得到冷硬带钢。
10.进一步的是,上述乳化液皂化值为150-180mgkoh/g,乳化液温度为55-60℃,乳化液中杂油含量≤3%;所述乳化液中缓蚀剂为乌洛托品、硫脲、硫脲-硫酸铝在酸洗液中至少一种,质量分数为0.5-1.5%。
11.更进一步的是,上述冷轧后冷硬带钢表面残留物(残油 残铁)总量≤200mg/m2,表面反射率≥80%。
12.上述连续退火工序中,以10-20℃/s的速率升温至800-930℃保温30-200s,以50-100℃/s的速率冷却至350-450℃,然后空冷到室温,得到退火钢板;退火炉气氛为n
2-h2的混合气体,其中h2含量为0.5-20%,退火气氛露点温度为-40-10℃。
13.进一步的是,上述退火钢板的平均晶粒尺寸为8-10μm,氧化膜层厚度≤3μm。
14.上述平整涂油工序中,控制平整后带钢表面粗糙度ra值为0.7-1.3μm,rpc值为80-130;所述涂油采用喷涂的方式,喷涂温度为30-50℃,带钢表面涂油量为600-1000mg/m2。
15.进一步的是,上述涂油采用防锈油,所述防锈油粘度(40℃)为15-20mm2/s。
16.上述除油酸洗工序中,除油采用碱液除油,除油温度为50-80℃;酸洗时间为5-15min,酸洗温度为30-50℃,酸洗后基板的表面能为1.5-1.8j/m2。
17.进一步的是,上述碱液主要组成成分按浓度为碱1-5%,乳化剂0.1-0.5%,磷酸三钠0.1-0.3%;所述碱为naoh,na2co3,na2sio3,磷酸盐中至少一种;所述乳化剂为烷基磺酸盐,烷基碳数目为12-14。
18.进一步的是,上述酸洗采用的酸洗液为液盐酸-硫酸混合酸或磷酸-柠檬酸混合酸,其中混合酸浓度为2-5%,缓蚀剂为0.5-1%硫脲。
19.上述表面调整工序中,采用的表面调整剂为胶体钛,浓度为0.08-0.12%,表面调整温度为室温,时间为30-90s。
20.上述磷化处理工序中,磷化处理时间为2-3min,温度为30-40℃。
21.进一步的是,上述磷化处理采用的磷化槽液总酸度为18-22pt.,游离酸度为1-3pt.,其主要成分为znh2po4,zn(no3)2,h3po4,nano2,naf,mn(no3)2;其中znh2po4浓度为1-3%,mn(no3)2浓度为0.1-0.3%。
22.进一步的是,上述磷化处理后膜层厚度为1-2μm。
23.本发明的有益效果是:本发明采用的冷轧汽车板制备方法,除了通过控制铸坯成分、热轧、冷轧、退火和平整等工序来提升钢板表面质量外,还对现有技术中常常忽略的除油脱脂酸洗、表面调整、磷化处理等工序进行了限定。影响汽车板磷化成膜的因素有很多,仅仅通过控制晶粒度、表面元素分布及表面粗糙度等特性无法制备出高质量的磷化膜,因此本技术对轧制过程中乳化液进行了限定,以保证基板表面具有较高的清洁度,较少的残留物,避免基板表面有害元素富集,进而对提高汽车板磷化性能;为了保证脱脂清洗效果,本发明对带钢表面涂油量及防锈油品质进行了限定,进一步提升了汽车板磷化成膜质量。
24.采用本发明的合金成分以及工艺控制方法,制备得到的冷轧汽车板表面无明显的元素富集现象,表面发生均匀的磷化反应过程;同时,本发明设计的酸洗除油除脂工艺可以提高冷轧汽车板表面清洁度及表面能;本发明提供了一种全流程控制汽车板磷化成膜质量的方法,形成的磷化膜层结构致密,结晶均匀,呈颗粒状,平均晶粒尺寸为2-3μm,孔隙率较小,具有较高的可涂装性能。
附图说明
25.图1为本发明实施例1制得的冷轧汽车板表面磷化膜形貌图;
26.图2为本发明实施例2制得的冷轧汽车板表面磷化膜形貌图。
具体实施方式
27.本发明的技术方案,具体可以按照以下方式实施。
28.提高冷轧汽车板表面可涂装性能的方法,所述方法的工艺流程为冶炼铸造
→
热轧卷取
→
酸洗冷轧
→
连续退火
→
平整涂油
→
除油酸洗
→
表面调整
→
磷化处理。
29.上述冶炼铸造工序中,按照化学成分冶炼浇注成铸坯,所述化学成分按质量百分比为c≤0.25%,si≤0.30%,0.05%≤mn≤3%,p≤0.01%,s≤0.01%,al≤0.02%,n≤0.01%,as sn≤0.02%,余量为fe及不可避免的杂质。
30.为了避免过烧导致晶粒组织粗大,为了降低精轧时坯料变形抗力,同时为了便于后续酸洗冷轧工序的进行,因此优选的是,上述热轧卷取工序中,将铸坯加热至1150-1300℃保温2-4h后轧制,终轧温度≥850℃;轧制后卷取,卷取温度为400-600℃,得到热轧卷。
31.为了将钢板表面的氧化皮完全去除避免形成表面缺陷,同时为了提高钢板的延展性和组织均匀性,因此优选的是,上述酸洗冷轧工序中,酸洗速度为80-120m/min,冷轧压下率为40-60%,乳化液皂化值为100-200mgkoh/g,乳化液温度为50-70℃,得到冷硬带钢。
32.为了提高酸洗的效果,保证基板表面具有较高的清洁度,较少的残留物,因此更优选的是,上述乳化液皂化值为150-180mgkoh/g,乳化液温度为55-60℃,乳化液中杂油含量≤3%;所述乳化液中缓蚀剂为乌洛托品、硫脲、硫脲-硫酸铝在酸洗液中至少一种,质量分数为0.5-1.5%。更优选的是,上述冷轧后冷硬带钢表面残留物(残油 残铁)总量≤200mg/m2,表面反射率≥80%。
33.基于退火工序对带钢基体组织、性能的影响,对钢板表层内氧化层厚度的影响以及成型性能的影响,因此优选的是,上述连续退火工序中,以10-20℃/s的速率升温至800-930℃保温30-200s,以50-100℃/s的速率冷却至350-450℃,然后空冷到室温,得到退火钢板。
34.为了还原带钢表面的氧化铁,因此优选的是,上述退火炉气氛为n
2-h2的混合气体,其中h2含量为0.5-20%,退火气氛露点温度为-40-10℃。
35.上述退火钢板的平均晶粒尺寸为8-10μm,氧化膜层厚度≤3μm。
36.涂装前处理工艺(除油酸洗-表调-磷化)及基板表面能大小为影响汽车板磷化成膜质量的主要因素,涂装前处理工艺不当将直接影响汽车板的磷化效果,进而影响其可涂装性能,因此必须对除油-酸洗-表调-磷化工艺进行限定。
37.上述平整涂油工序中,控制平整后带钢表面粗糙度ra值为0.7-1.3μm,rpc值为80-130;所述涂油采用喷涂的方式,喷涂温度为30-50℃,带钢表面涂油量为600-1000mg/m2。
38.通常带钢表面还需进行的防腐处理,防锈油的品质及油量大小直接影响到脱脂清洗效果,进而影响汽车板磷化成膜质量,为了达到更好的涂油防锈的效果,因此优选的是,上述涂油采用防锈油,所述防锈油粘度(40℃)为15-20mm2/s。更优选的是,上述除油酸洗工序中,除油采用碱液除油,除油温度为50-80℃;酸洗时间为5-15min,酸洗温度为30-50℃,酸洗后基板的表面能为1.5-1.8j/m2。
39.为了达到更好的除油除脂的效果,因此优选的是,上述碱液主要组成成分按浓度为碱1-5%,乳化剂0.1-0.5%,磷酸三钠0.1-0.3%;所述碱为naoh,na2co3,na2sio3,磷酸盐中至少一种;所述乳化剂为烷基磺酸盐,烷基碳数目为12-14。更优选的是,上述酸洗采用的酸洗液为液盐酸-硫酸混合酸或磷酸-柠檬酸混合酸,其中混合酸浓度为2-5%,缓蚀剂为
0.5-1%硫脲。
40.上述表面调整工序中,采用的表面调整剂为胶体钛,浓度为0.08-0.12%,表面调整温度为室温,时间为30-90s。
41.上述磷化处理工序中,磷化处理时间为2-3min,温度为30-40℃。
42.优选的是,上述磷化处理采用的磷化槽液总酸度为18-22pt.,游离酸度为1-3pt.,其主要成分为znh2po4,zn(no3)2,h3po4,nano2,naf,mn(no3)2;其中znh2po4浓度为1-3%,mn(no3)2浓度为0.1-0.3%。
43.上述磷化处理后膜层厚度为1-2μm。
44.下面通过实际的例子对本发明的技术方案和效果做进一步的说明。
45.实施例
46.本发明提供两组采用本发明方法制备冷轧汽车板的实施例,实施例1、2铸坯的主要化学成分如表1所示。
47.表1实施例铸坯化学成分/%
[0048] csimnpsalnassn实施例10.0240.0030.1350.0090.0070.0180.0050.0060.004实施例20.0240.0030.1350.0090.0070.0180.0050.0060.004
[0049]
实施例1、2的具体实验步骤如下:
[0050]
1、按照表1中化学成分冶炼浇注成铸坯,将实施例1、2的铸坯加热至1300℃保温2h后轧制卷取,终轧温度为880℃,卷取温度为600℃,得到热轧卷;
[0051]
2、对热轧卷进行酸洗冷轧,具体工艺参数如表2所示,得到冷硬带钢;
[0052]
实施例1冷硬带钢表面残留物(残油 残铁)总量为50mg/m2,表面反射率为85%;
[0053]
实施例2冷硬带钢表面残留物(残油 残铁)总量为100mg/m2,表面反射率为90%;
[0054]
表2酸洗冷轧工艺
[0055][0056]
3、将冷硬带钢进行连续退火处理,具体工艺参数如表3所示,得到退火钢板;
[0057]
实施例1的退火钢板平均晶粒尺寸为10μm,氧化膜层厚度为3μm;
[0058]
实施例2的退火钢板平均晶粒尺寸为8μm,氧化膜层厚度为2μm;
[0059]
表3退火工序
[0060][0061]
4、将带钢进行平整涂油处理,具体工艺参数如表4所示;
[0062]
表4平整涂油工序
[0063][0064]
5、采用碱液对实施例1、2涂油后的钢板进行除油脱脂处理,在50℃下除油时间3min,采用的碱液中乳化剂为0.5%十二烷基磺酸盐,碱为2%naoh、1%na2sio3;将实施例1、2除油后的钢板在30℃的条件下进行酸洗除锈处理,采用的酸洗液为1.5%盐酸-0.5%硫酸混合酸,1%硫脲缓蚀剂;
[0065]
实施例1的钢板酸洗5min,得到基板的表面能为1.7j/m2;
[0066]
实施例2的钢板酸洗10min,得到基板的表面能为1.7j/m2;
[0067]
6、对酸洗后的实施例1、2所得基板进行表面调整,采用的表面调整剂为胶体钛,表调剂浓度0.1%,室温条件下表调30s;
[0068]
7、将表面调整后的实施例1、2所得钢板在2%znh2po4,0.2%mn(no3)2的磷化槽液中进行磷化处理,其中磷化液游离酸度为3pt.,总酸度为22pt.,磷化时间3min,磷化温度40℃,得到覆有表面磷化膜的冷轧汽车板。
[0069]
对实施例1、2得到的冷轧汽车板表面磷化膜进行检测:
[0070]
图1为本发明实施例1制得的冷轧汽车板表面磷化膜形貌图,图2为本发明实施例2制得的冷轧汽车板表面磷化膜形貌图,由图可知,实施例1制得的磷化膜层平均晶粒尺寸为2μm,实施例2制得的磷化膜层平均晶粒尺寸为3μm;采用本发明的方法制备得到磷化膜层结构致密,结晶均匀,呈颗粒状,孔隙率较小,具有较高的可涂装性能。
再多了解一些
本文用于企业家、创业者技术爱好者查询,结果仅供参考。