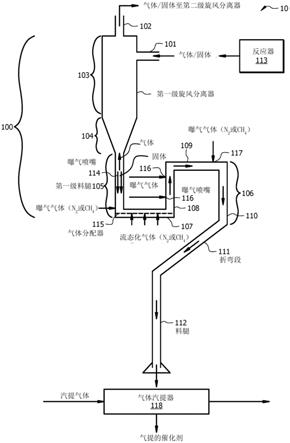
反应器第一级料腿上的回料控制装置以减少向石脑油催化裂化汽提器的烃携带
1.相关申请的交叉引用
2.本技术要求2019年8月5日提交的美国临时专利申请no.62/883,065的优先权的权益,其通过整体引用并入本文。
技术领域
3.本发明一般涉及石脑油催化裂化以生产烯烃。更具体地,本发明涉及在裂化石脑油并形成气体和催化剂颗粒的混合物的条件下使催化剂颗粒与石脑油接触,并通过连接有回料控制装置的旋风分离器将气体与催化剂颗粒分离。
背景技术:
4.石脑油催化裂化是将最终沸点低于350℃的烃混合物(如石脑油)转化为轻质烯烃(即乙烯、丙烯和丁烯)和芳族化合物(即苯、甲苯和二甲苯,或简称btx)的过程。可以改变催化裂化过程中的反应器流体动力学和反应动力学以获得宽范围的产物分布。反应器设计可以包括具有各种配置的循环流化床(cfb)反应器,例如湍流流化床反应器(tfbr)或快速流化床反应器(ffbr)。在cfb中,产物气体和废催化剂进入反应器,混合物在单个或多个二-三级旋风分离器中分离。
5.理论上,超过95wt.%的产物气体通常通过cfb反应器顶部的流出物管线离开cfb反应器,而废催化剂通过料腿到达cfb反应器的底部。然后废催化剂与吸附在催化剂表面的烃蒸气一起进入汽提器。这些蒸气以两种方式携带,第一种是通过填充催化剂孔,第二种是被催化剂夹带。在典型的流化催化裂化(fcc)装置中,蒸汽被用作汽提气体以去除各个催化剂颗粒之间夹带的烃和一小部分吸附的烃。蒸汽需求为每1000kg循环催化剂大约2-5kg蒸汽。然而,蒸汽通过脱铝使催化剂失活。
技术实现要素:
6.已经发现了一种生产烯烃和/或芳族化合物的方法,其中石脑油在反应器中被催化裂化以产生产物气体和废催化剂的混合物,并且与常规方法相比,从反应器流入汽提器的夹带烃的量减少。该方法基于通过安装回料控制装置(loop-seal),将气体产物的流动限制到比废催化剂的流动的限制更大的程度,使得至少一些气体产物与废催化剂分离,从而使从反应器中的旋风分离器到汽提器的烃携带最小化。以这种方式,与常规方法相比,由于进入汽提器的夹带烃量较低,可以最小化从废催化剂中汽提烃的需要,从而最小化汽提气体的需求,并且可以更容易地保持催化剂的活性。
7.本发明的实施方案包括生产烯烃和/或芳族化合物的方法。该方法包括在催化剂流化床中裂化石脑油,以形成包含一种或多种烯烃和/或一种或多种芳族化合物的气体产物。该方法还包括使包含催化剂颗粒和气体产物的混合物从催化剂流化床流至旋风分离器,其中回料控制装置与旋风分离器的第一出口(料腿)流体连通。该方法还包括将气体产
物通过回料控制装置的流动限制到比催化剂颗粒通过回料控制装置的流动的任何限制更大的程度。
8.本发明的实施方案包括生产烯烃和/或芳族化合物的方法,其中该方法包括在催化剂流化床中裂化石脑油以形成包含乙烯、丙烯、丁烯、苯、甲苯和二甲苯中的一种或多种的气体产物。该方法还包括使包含催化剂颗粒和气体产物的混合物从催化剂流化床流至旋风分离器,其中回料控制装置连接到旋风分离器的第一出口(料腿)并与其流体连通。该方法还包括将气体产物通过回料控制装置的流动限制到比催化剂颗粒通过回料控制装置的流动的任何限制更大的程度,使得回料控制装置上游的气体产物与催化剂颗粒的比率比回料控制装置下游的气体产物与催化剂颗粒的比率高至少50%。此外,该方法包括使流出物从回料控制装置流到气体汽提器。
9.以下包括贯穿本技术文件使用的各种术语和短语的定义。
10.术语“约(about)”或“大约(approximately)”被定义为接近,如本领域普通技术人员所理解的。在一个非限制性实施方案中,该术语被定义为在10%内,优选在5%内,更优选在1%内,最优选在0.5%内。
11.术语“wt%”、“vol%”或“mol.%”分别指基于包括所述组分的材料的总重量、总体积或总摩尔数的所述组分的重量百分比、体积百分比或摩尔百分比。在非限制性实例中,在100摩尔材料中的10摩尔组分为10mol.%的组分。
12.术语“基本上”及其变型被定义为包括在10%内,在5%内,在1%内,或在0.5%内的范围。
13.术语“抑制”或“减少”或“防止”或“避免”或这些术语的任何变型,当用在权利要求和/或说明书中时,包括任何可测量的减少量或完全抑制以实现期望的结果。
14.在说明书和/或权利要求书中使用的术语“有效”是指足以实现期望的、预期的或意图的结果。
15.当在权利要求或说明书中与术语“包含”、“包括”、“含有”或“具有”一起使用时,词语“一(a)”或“一(an)”的使用可表示“一个(one)”,但其也具有“一个或多个”、“至少一个”和“一个或多于一个”的含义。
16.术语“包含(comprising)”(和任何形式的包含,如“包含(comprise)”和“包含(comprises)”)、“具有(having)”(和任何形式的具有,如“具有(have)”和“具有(has)”)、“包括(including)”(和任何形式的包括,如“包括(includes)”和“包括(include)”)或“含有(containing)”(和任何形式的含有,例如“含有(contains)”和“含有(contain)”)是包括性的或开放式的,且不排除另外的、未列举的元素或方法步骤。
17.本发明的方法可以“包含”在整个说明书中公开的特定成分、组分、组合物等,“基本上由其组成”或“由其组成”。
18.如在说明书和/或权利要求书中使用的术语,术语“主要”是指大于50wt.%、50mol.%和50vol.%中的任何一种。例如,“主要”可以包括50.1wt.%至100wt.%及其间的所有值和范围、50.1mol.%至100mol.%及其间的所有值和范围、或50.1vol.%至100vol.%及其间的所有值和范围。
19.本发明的其它目的、特征和优点将从以下附图、详细描述和实施例中变得显而易见。然而,应当理解,在指示本发明的具体实施方案的同时,附图、详细描述和实施例仅以说
明的方式给出,而不意味着限制。另外,预期从本详细描述中,在本发明的精神和范围内的改变和修改对于本领域技术人员将变得显而易见。在进一步的实施方案中,来自具体实施方案的特征可以与来自其他实施方案的特征结合。例如,来自一个实施方案的特征可以与来自任何其他实施方案的特征结合。在另外的实施方案中,可以向本文所述的具体实施方案增加附加特征。
附图说明
20.为了更完整地理解,现在结合附图参考以下描述,其中:
21.图1示出了根据本发明的实施方案用于从石脑油催化裂化生产烯烃和/或芳族化合物中的废催化剂中分离气体产物的系统;和
22.图2示出了根据本发明的实施方案生产烯烃和/或芳族化合物的方法。
具体实施方式
23.已经发现了一种生产烯烃和/或芳族化合物的方法,其中石脑油在反应器中被催化裂化以产生产物气体和废催化剂的混合物,并且与常规方法相比,用于将废催化剂与产物气体分离的旋风分离器配备有减少从反应器流入汽提器的夹带烃量的回料控制装置。该方法基于通过在第一级料腿底部安装回料控制装置,使从反应器中的第一级旋风分离器到汽提器的烃携带最小化。回料控制装置在第一垂直段两端产生压降,主要允许固体流过第一水平段,同时迫使被催化剂拖动的向下流动的气体移回料腿的顶部。这可能将料腿下的气体再循环减少至高90%(从高达33%降至低至2%)。这随后减少了汽提所需的气体量。根据本发明的实施方案,回料控制装置的构思包括用于流态化气体(例如氮气或甲烷)的气体分配器(例如喷雾器型),以及在系统的垂直段和第二水平段上的多个曝气喷嘴,以注入少量曝气气体(例如氮气或甲烷)。这个构思使得用于汽提掉剩余夹带烃的汽提气体的需求最小化。然而,仍然需要一些汽提气体(例如氮气、甲烷或烟气)来汽提掉剩余的夹带烃和少量的吸附烃。
24.图1示出了根据本发明的实施方案用于从石脑油催化裂化生产烯烃和/或芳族化合物中的废催化剂中分离气体产物的系统10。图2示出了根据本发明的实施方案用于从石脑油催化裂化生产烯烃和/或芳族化合物中的废催化剂中分离气体产物的方法20。系统10可用于实施方法20。
25.如图1所示,在本发明的实施方案中,系统10包括具有入口101和顶部出口102的旋风分离器100。旋风分离器100的圆柱主体103连接到变窄部分104,变窄部分104又连接到第一级料腿105,使得入口101、顶部出口102、圆柱主体103、变窄部分104和第一级料腿105都适于流体连通。根据本发明的实施方案,如图1所示,旋风分离器100与回料控制装置106流体连通。更具体地,旋风分离器100的第一级料腿105连接到回路106并与其流体连通,使得向下流过旋风分离器100的材料通过第一级料腿105离开旋风分离器100并流入回料控制装置106。第一级料腿105可适于接收曝气气体。
26.在本发明的实施方案中,如图1所示,回料控制装置106包括第一水平段107,该第一水平段107可以具有气体分配器,使得流态化气体可以流入第一水平段107以接触并流化第一水平段107中的材料(例如催化剂颗粒)。根据本发明的实施方案,第一水平段107连接
到第一垂直段108并与其流体连通,第一垂直段108又连接到第二水平段109并与其流体连通。在本发明的实施方案中,第二水平段109连接到第二垂直段110并与其流体连通。根据本发明的实施方案,第二水平段109具有入口117,该入口117位于第二水平段109和第二垂直段110的连接处附近,其中入口117适于允许曝气气体被进料到第二水平段109中。
27.根据本发明的实施方案,回料控制装置106经由第二垂直段109连接到折弯段(dogleg)111并与其流体连通。在本发明的实施方案中,折弯段111包括相对于水平轴线以25至60度范围内的角度倾斜的管。折弯段111可以连接到第二料腿112并与其流体连通。根据本发明的实施方案,第一级料腿105、回料控制装置106(及其各部件)、折弯段111和料腿112由可以具有选自圆形、矩形、三角形、椭圆形等横截面的管组成。圆柱主体103的直径可为1至1.6mm。圆柱主体103的直径与第一级料管105的直径(最大横截面距离)之比可以为2.5至11。
28.图2示出了根据本发明的实施方案生产烯烃和/或芳族化合物的方法。方法20可以从框200开始,框200包括在具有催化剂流化床的反应器113中裂化石脑油以形成包含一种或多种烯烃和/或一种或多种芳族化合物的气体产物。在本发明的实施方案中,石脑油的催化裂化可以包括将最终沸点低于350℃的烃混合物转化为轻质烯烃(即乙烯、丙烯和/或丁烯)和/或芳族化合物(即苯、甲苯和/或二甲苯)。可以改变反应器流体动力学和反应动力学以实现宽范围的产物分布。反应器设计可包括具有各种配置的循环流化床(cfb)反应器,例如带有或不带挡板的一至四个湍流流化床反应器(tfbr)/快速流化床反应器(ffbr),以及一至四个密相提升管。根据本发明的实施方案,因为气体产物在具有流化床的反应器中生产,所以反应器113的流出物包括包含催化剂颗粒和气体产物的混合物。在框201处,包含催化剂颗粒和气体产物的混合物从反应器113(具有催化剂流化床)流至旋风分离器,例如系统10的旋风分离器100。
29.根据本发明的实施方案,旋风分离器100包括入口101,催化剂颗粒和气体产物的混合物通过该入口流入旋风分离器100。旋风分离器100还包括圆柱主体103,其适于引起混合物的循环流动,使得流过顶部出口102的旋风分离器流出物包含比进入的混合物更高的气固比,即混合物的较轻部分。换句话说,一些固体从混合物中分离出来并且这些固体和一些气体产物一起(即混合物的较重部分)向下朝着变窄部分104移动,并进入第一级料腿105。
30.在常规的旋风分离器料腿/配置中,第一级料腿通常在流动流(稀释区)中运行,其中进入旋风分离器的固体将气体向下拖动。这种现象被称为“气体再循环”,并可潜在地使多达1/3的入口气体(即33%)下行。气体再循环随着进入第一级旋风分离器的表观气体速度(sgv)、固体流量和/或催化剂细粒含量的增加而增加。当料腿在所需的密相模式下运行时,只有约2-3%进入旋风分离器的气体随固体一起流下料腿。在本发明的实施方案中,密相模式操作可以通过在料腿末端上方的第一个3-5英尺中存在大于约0.3的高固体体积分数来定义。气体再循环现象的程度可以通过在料腿中形成致密密封(测量的单位长度压降)或通过减少进入第一级旋风分离器的固体流量来降低。
31.因此,根据本发明的实施方案,第一级料腿105适于通过设置在第一级料腿105中的曝气喷嘴114接收曝气气体(例如氮气和甲烷)。通过喷嘴114注入曝气气体具有避免料腿中的颗粒通过曝气去流化的效果。在本发明的实施方案中,第一级料腿105连接至回料控制
装置106并与其流体连通,使得混合物的较重部分向下流过第一级料腿105并进入回料控制装置106,具体地,第一水平段107。在本发明的实施方案中,第一水平段107包括气体分配器115,流态化气体通过气体分配器115流入第一水平段107以接触并流化第一水平段107中的材料。通过气体分配器115注入流态化气体具有避免料腿中的颗粒通过曝气去流化的效果。第一垂直段108连接至第一水平段107并与其流体连通,使得来自第一水平段107的催化剂颗粒向上移动到第一垂直段108。根据本发明的实施方案,第一垂直段108适于通过设置在第一垂直段108中的曝气喷嘴116接收曝气气体(例如氮气和甲烷)。通过喷嘴116注入曝气气体具有避免料腿中的颗粒通过曝气去流化的效果。第二水平段109与第一垂直段108流体连通,使得催化剂颗粒从第一垂直段108移动到第二水平段109中。根据本发明的实施方案,第二水平段109适于通过设置在第一第二水平段109和第二垂直段110的相交处的曝气入口117接收曝气气体(例如氮气和甲烷)。通过喷嘴116注入曝气气体具有避免料腿中的颗粒通过曝气去流化的效果,而曝气气体喷嘴117也有助于打破管线中的潜在真空。在本发明的实施方案中,第二垂直段110与第二水平段109流体连通,使得来自第二水平段109的催化剂颗粒向下移动到第二垂直段110。具有第一水平段107、第一垂直段108、第二水平段109和第二垂直段110的回料控制装置106被配置成通过分离进入第一级旋风分离器的大部分气体,主要将具有吸附的烃的催化剂颗粒沿着料腿向下转移到包围旋风分离器的反应器底部附近。
32.因此,根据本发明的实施方案,在框202处,方法20包括将气体产物通过回料控制装置106的流动限制到比催化剂颗粒通过回料控制装置106的流动的任何限制更大的程度。在本发明的实施方案中,框202的限制使得回料控制装置106上游的气体产物与催化剂颗粒的比率比回料控制装置106下游的气体产物与催化剂颗粒的比率高至少50%。在框203处,根据本发明的实施方案,来自回料控制装置106的流出物流经折弯段111,然后流经料腿112并到达气体汽提器118。在框204处,在本发明的实施方案中,气体汽提器118从催化剂颗粒中汽提剩余的烃。根据本发明的实施方案,因为回料控制装置106设置在第一级料腿105上,所以与常规方法相比,由于进入汽提器的夹带烃的量较低,从废催化剂中汽提烃的需要和汽提气体的需求可以被最小化,并且催化剂的活性可以更容易地保持。
33.在本发明的上下文中,描述了至少以下18个实施方案。实施方案1是生产烯烃和/或芳族化合物的方法。该方法包括在催化剂流化床中裂化石脑油以形成含有一种或多种烯烃和/或一种或多种芳族化合物的气体产物。该方法还包括使含有催化剂颗粒和气体产物的混合物从催化剂流化床流至旋风分离器,其中回料控制装置与旋风分离器的第一料腿流体连通。该方法还包括将气体产物通过回料控制装置的流动限制到比催化剂颗粒通过回料控制装置的任何流动的限制更大的程度。实施方案2是实施方案1所述的方法,其中所述气体产物含有以下中的一种或多种:乙烯、丙烯、丁烯、苯、甲苯和二甲苯。实施方案3是实施方案1或2中任一项所述的方法,其中所述限制使得回料控制装置上游的气体产物与催化剂颗粒的比率比回料控制装置下游的气体产物与催化剂颗粒的比率高至少50%。实施方案4是实施方案3所述的方法,其中回料控制装置上游的气体产物与催化剂颗粒的比率比回料控制装置下游的气体产物与催化剂颗粒的比率高至少90%。实施方案5是实施方案1至4中任一项所述的方法,其进一步包括使流出物从回料控制装置流到气体汽提器。实施方案6是实施方案5所述的方法,其进一步包括从来自所述回料控制装置的流出物中的催化剂颗粒中汽提至少一些烃。实施方案7实施方案1至6中任一项所述的方法,其中流化床包括从由以下
组成的列表中的选择:循环流化床、湍流流化床和快速流化床。实施方案8是实施方案1至7中任一项所述的方法,其中所述旋风分离器是多个串联旋风分离器中的第一个。实施方案9是实施方案1至8中任一项所述的方法,其中所述环形密封连接到折弯段并与其流体连通。实施方案10是实施方案9所述的方法,其中所述折弯段连接到第二料腿并与其流体连通。实施方案11是实施方案1至10中任一项所述的方法,其中所述环形密封包括两个水平段和两个垂直段。实施方案12是实施方案11所述的方法,其中第一水平段包括气体分配器。实施方案13是实施方案12所述的方法,其进一步包括通过气体分配器将流态化气体注入第一水平段。实施方案14是实施方案13所述的方法,其中所述流态化气体含有以下中的一种或多种:氮气和甲烷。实施方案15是实施方案11所述的方法,其中两个垂直段包括曝气气体喷嘴。实施方案16是实施方案15所述的方法,其进一步包括将曝气气体注入两个垂直段中的一个或多个。实施方案17是实施方案16所述的方法,其中所述曝气气体含有以下中的一种或多种:氮气和甲烷。实施方案18是实施方案1至17中任一项所述的方法,其中旋风分离器的第一料腿以密相模式运行。
34.尽管已经详细描述了本技术的实施方案及其优点,但应理解,在不脱离由所附权利要求限定的实施方案的精神和范围的情况下,可以在此进行各种改变、替换和变更。此外,本技术的范围不旨在限于说明书中描述的过程、机器、制造、物质组成、装置、方法和步骤的特定实施方案。如本领域普通技术人员将从上述公开内容中容易理解的,可以利用目前存在的或以后将要开发的与执行本文所述的相应实施方案基本相同的功能或实现基本相同的结果的过程、机器、制造、物质组成、装置、方法或步骤。因此,所附权利要求旨在将这样的过程、机器、制造、物质组成、装置、方法或步骤包括在其范围内。
再多了解一些
本文用于企业家、创业者技术爱好者查询,结果仅供参考。