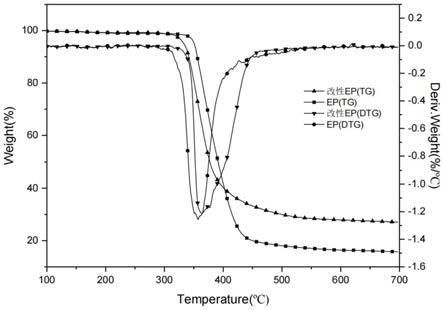
1.本发明属于树脂基复合材料领域,特别的涉及一种高热稳定性的膨胀型复配阻燃剂改性环氧树脂材料及其制备方法。
背景技术:
2.树脂基复合材料具有高比强度和比刚度、可设计性强、抗疲劳断裂性能好、耐腐蚀、结构稳定性好、可大尺寸成型等特点,在航空航天、汽车、电子电器和海洋工业等领域有着广泛应用。先进树脂基复合材料多为碳纤维增强的热固性树脂复合材料,主要有环氧树脂(ep)、双马来酰亚胺树脂、聚酰亚胺树酯等热固性树脂。其中,环氧树脂因具有工艺性能优良、黏结性强和收缩率低,以及价格低等优点,统治着高性能复合材料的市场。
3.环氧树脂作为传统的一种热固性树脂,具有一系列优异性能,但其氧指数(loi)只有19.5%左右,极易燃烧,且燃烧时发热量较大,燃烧速度快。近年来,为了提高复合材料阻燃性能,减少火灾危害,阻燃环氧树脂复合材料成为各领域迫切需求研发的材料。
4.传统的溴化环氧树脂具有良好的阻燃性能。然而,溴化环氧树脂在燃烧过程中会分解产生大量有害气体。随着全球对绿色环保阻燃剂的强烈呼吁,许多国家和地区开始禁止使用含卤阻燃剂的聚合物材料。因此,开发新型无卤阻燃环氧树脂体系成为发展趋势。
5.目前,膨胀型阻燃剂因阻燃性能优良和价格相对低廉,逐渐成为市场上卤素阻燃剂的替代品,也是未来阻燃剂的重要研究开发领域。膨胀型阻燃剂主要依靠通过酸源、炭源和气源作用,在材料表面形成多孔泡沫炭层进行阻燃,主要包括磷系和氮系阻燃剂等。然而,上述阻燃剂单独添加时,为满足阻燃要求常常需要将用量增大到35%以上,其势必会对环氧树脂的热稳定性、力学性能和电绝缘性等其它性能产生影响。因此,研究学者采用了多元素(p-n、p-n-c等)协同,或无机-有机协效阻燃改性等策略。
6.在阻燃改性方法上,一般采用添加型或反应型阻燃剂进行改性,然而反应型阻燃剂化学合成过程相对复杂、成本高,且存在应用范围受限等问题。添加型阻燃剂因制备工艺简单,配方可灵活调控,成本低等优势,依然是当今环氧树脂工业中阻燃改性的主要途径,也是阻燃剂开发的重点方向,如专利cn 103525004b中采用铁化合物作为阻燃协效剂,与复配膨胀型阻燃剂形成一种复合阻燃剂,添加至环氧树脂中来实现协效阻燃。专利cn 105111688b采用三氯氧磷、二乙胺和缩水甘油制备了一种p-n膨胀型阻燃剂。文献(陈学习等,高分子材料科学与工程,2021,37(04):49-55 62)报道了采用固体超强酸(so
42-‑mx
oy)与蒙脱土改性聚磷酸铵进行复配,协同阻燃环氧树脂。文献(孙悦等,化学与粘合,2021,43(3):197-199)报道了采用g-c3n4/cnts/app复配体系,添加至环氧树脂中,通过形成三维立体导热通道进行阻燃改性。上述膨胀型阻燃剂均有效提高了环氧树脂的阻燃性能。然而,膨胀型阻燃剂为有效起到阻燃作用,在阻燃过程中会催化环氧树脂基体降解成炭,同时也因自身热分解温度低于基体的热分解温度,不可避免的造成阻燃改性后基体的热分解温度下降,从而对其热稳定性产生不同程度的影响,而上述文献报道只是片面的从残炭率上来考
察热稳定性,初始分解温度是评估材料热稳定性的一个主要参数。因此,在考察阻燃剂对环氧树脂基体热稳定性的影响时,应首先对其初始分解温度进行考量。然而,报道的大部分膨胀型阻燃剂,常在添加后与基体的相容性差,造成分散困难,致使阻燃改性环氧树脂材料的初始分解温度大幅度下降,使得热稳定性呈现急剧降低现象,从而满足不了中、高档塑料的加工要求,且阻燃效率低。可见,获得兼具高热稳定性和高阻燃效率的阻燃改性环氧树脂材料仍是一个巨大挑战。
7.综上所述,采用制备工艺简洁、能耗低的阻燃技术,开发热稳定性高、阻燃性能优异、且绿色环保的新型阻燃剂成为阻燃环氧树脂复合材料发展的迫切需求。
技术实现要素:
8.基于以上研究现状,本发明的目的在于提供一种高热稳定性的膨胀型复配阻燃剂改性环氧树脂材料及其制备方法,该方法从提高阻燃剂与基体间的界面相容性、复配组分的热降解温度和阻燃性能三方面出发,拟开发热稳定性高、阻燃性能优异、且绿色环保的新型阻燃剂,通过低成本合成一种热稳定性高的p-n系阻燃剂,同时加入少量si系和n系阻燃剂,从而形成一种新型p-n-si系膨胀型复配阻燃剂,依据p-n-si的协效阻燃原理,来提高环氧树脂的阻燃性能。本发明制备方法简单、原料成本和能耗低,且制得的复合材料兼具优异的热稳定性和阻燃效率。
9.本发明的技术方案如下:
10.一种高热稳定性的膨胀型复配阻燃剂改性环氧树脂材料;由聚焦磷酸哌嗪、埃洛石纳米管和三聚氰胺氰尿酸盐按照质量比例(5~8):(1~2):(4~1)共混配制形成p-n-si系膨胀型复配阻燃剂,加入至环氧树脂中进行阻燃改性,并通过加入固化剂实施固化,其中各组分的质量百分比为:环氧树脂:55~83.6%,膨胀型复配阻燃剂:4.4~20%,固化剂:12%~25%。
11.所述的聚焦磷酸哌嗪制备方法由磷酸和哌嗪在85~95℃下反应2~3h,首先经脱水缩合得到中间体二磷酸哌嗪,再在真空条件下,绝压为20~60mmhg,温度为260~280℃,将二磷酸哌嗪进行高温脱水2~3h,最终经分子内脱水缩合制备得到聚焦磷酸哌嗪。
12.所述聚焦磷酸哌嗪的热失重1%的温度要高于300℃,热失重5%的温度要高于336℃。
13.本发明提供的一种高热稳定性的膨胀型复配阻燃剂改性环氧树脂材料的制备方法,包括如下操作步骤:
14.(1)在伴有机械搅拌装置的反应器中,预热环氧树脂至60~90℃;
15.(2)将聚焦磷酸哌嗪、埃洛石纳米管和三聚氰胺氰尿酸盐按照质量比例(5~8):(1~2):(4~1)共混,得到膨胀型复配阻燃剂,然后将其加入到反应器中与步骤(1)得到的环氧树脂进行混合;
16.(3)将步骤(2)得到的共混液搅拌,并进行超声分散后加入固化剂,其中各组分的质量百分比为:环氧树脂:55~83.6%,膨胀型复配阻燃剂:4.4~20%,固化剂:12%~25%;在60~90℃的条件下继续搅拌,真空处理后趁热倒入预热好的模具中,放入烘箱于100~110℃下预固化0.5~1.5h,再升温至150~180℃固化1~2h,得到高热稳定性的膨胀型复配阻燃剂改性环氧树脂材料。
17.所述的固化剂为间苯二胺、4,4'-二氨基-二苯甲烷或聚酰胺固化剂。
18.具体说明如下:
19.本发明提供的一种高热稳定性的膨胀型复配阻燃剂改性环氧树脂材料是由聚焦磷酸哌嗪(p-n系)、埃洛石纳米管(si系)和三聚氰胺氰尿酸盐(n系)按照质量比例(5~8):(1~2):(4~1)共混配制形成p-n-si系膨胀型复配阻燃剂,加入至环氧树脂中进行阻燃改性,并通过加入固化剂实施固化,其中各组分的质量百分比为:环氧树脂:55~83.6%,膨胀型复配阻燃剂:4.4~20%,固化剂:12%~25%。
20.上述复配阻燃剂中的聚焦磷酸哌嗪是一种白色粉粒体,可以由公开报道的磷酸和哌嗪,在氮气或其他惰性气氛下制备获得,但合成的聚焦磷酸哌嗪热分解温度太低(报道的失重5%的初始分解温度为300℃),会明显的降低阻燃改性基体的热稳定性。也可以采用其他方法公开的方法制备,要求是制备的聚焦磷酸哌嗪的热失重1%的温度要高于300℃,热失重5%的温度要高于336℃。
21.为保证阻燃改性环氧树脂具有优异的热稳定性,本发明也可以采用如下方法,通过在真空条件下进行高强度脱水,从而获得热稳定性高的聚焦磷酸哌嗪,具体是由价格低廉的磷酸和哌嗪反应生成,由磷酸和哌嗪在85~95℃下反应2~3h,首先经脱水缩合得到中间体二磷酸哌嗪,再在真空条件下,绝压为20~60mmhg,温度为260~280℃,将二磷酸哌嗪进行高温脱水2~3h,最终经分子内脱水缩合制备得到聚焦磷酸哌嗪,其化学结构式(1)如下:
[0022][0023]
为提高复配阻燃剂改性环氧树脂的热稳定性,从而起到有效的阻燃效果,制备的聚焦磷酸哌嗪的热失重1%的温度要高于300℃,热失重5%的温度要高于336℃。
[0024]
本发明中的埃洛石为天然矿物中提取的硅酸盐化合物,价格低廉易得,热稳定性优异,且其表面的si-o和al-oh键可以与三聚氰胺氰尿酸盐的-nh和-nh2键通过氢键结合,从而形成界面相容性好的稳定阻燃材料。埃洛石纳米管(2)和三聚氰胺氰尿酸盐(3)的化学结构式如下:
[0025]
上述复配阻燃剂中的聚焦磷酸哌嗪中含有-oh、
–
p=o和-nh2基团,埃洛石纳米管和三聚氰胺氰尿酸盐中含有si-o、al-oh、-nh和-nh2基团,环氧树脂基体中含有-o-和-oh等基团。因此,阻燃剂之间、以及阻燃剂与环氧树脂之间均能形成氢键网络,从而使得制备的阻燃材料具有良好的界面相容性和稳定性。
[0026]
本发明提供的一种高热稳定性的膨胀型复配阻燃剂改性环氧树脂材料的制备方
法,按如下操作步骤:
[0027]
(1)在伴有机械搅拌装置的反应器中,预热环氧树脂至60~90℃;
[0028]
(2)将聚焦磷酸哌嗪、埃洛石纳米管和三聚氰胺氰尿酸盐按照质量比例(5~8):(1~2):(4~1)共混,得到膨胀型复配阻燃剂,然后将其加入到反应器中与步骤(1)得到的环氧树脂进行混合;
[0029]
(3)将步骤(2)得到的共混液充分搅拌,并进行超声分散后加入固化剂,其中各组分的质量百分比为:环氧树脂:55~83.6%,膨胀型复配阻燃剂:4.4~20%,固化剂:12%~25%;在60~90℃的条件下继续搅拌,真空处理后趁热倒入预热好的模具中,放入烘箱于100~110℃下预固化0.5~1.5h,再升温至150~180℃固化1~2h,最终得到一种p-n-si系膨胀型复配阻燃剂改性环氧树脂复合材料。
[0030]
本发明中所使用的固化剂可以为间苯二胺、4,4'-二氨基-二苯甲烷,聚酰胺等固化剂,优选间苯二胺。
[0031]
本发明的优点:
[0032]
(1)本发明开发的高热稳定性的膨胀型复配阻燃剂,其粒径均在5~20μm,同时因体系中氢键网络的形成,阻燃剂与基体间具有良好的相容性,分散性较优,所得改性环氧树脂产品表面光滑,且通过热重分析结果(图2)证实阻燃改性环氧树脂的热稳定性优异,从而避免了传统添加型阻燃剂热稳定性差的问题。
[0033]
(2)本发明开发的高热稳定性的膨胀型复配阻燃剂改性环氧树脂材料,原料价格低廉,制备工艺简单,且阻燃效果优良,在优化配方条件下,通过阻燃性能测试证实改性环氧树脂阻燃可达ul94 v-0级的垂直燃烧等级,极限氧指数可达34.3%。
[0034]
(3)本发明开发的膨胀型复配阻燃剂,无需添加格外的协效剂,其复配组分间显示出良好的协效作用,如聚焦磷酸哌嗪受热分解产生偏磷酸或焦磷酸等物质,其催化环氧树脂形成致密的膨胀型炭层,如图3燃烧后的残炭照片所示;从而抑制了热量和氧气的传递;埃洛石纳米管的管体对传热具有阻隔作用和成炭作用;三聚氰胺氰尿酸盐在分解过程中可以生成no2、nh3和o3等不燃气体,稀释了氧气浓度,在气相进行了阻燃。可见,三者从凝聚相和气相共同提高了环氧树脂的阻燃效率,且为无卤型阻燃剂,满足绿色环保阻燃剂要求。
附图说明
[0035]
图1为实施例1聚焦磷酸哌嗪的热重分析曲线图。
[0036]
图2为实施例5和对比例中环氧树脂改性前后的热重分析曲线图,ep为纯环氧树脂样条,改性ep为加入复配阻燃剂后的环氧树脂样条。
[0037]
图3为实施例5、实施例7和对比例样条经锥形量热测试燃烧后的残炭照片。
具体实施方式
[0038]
下面对本发明的具体实施方式作进一步说明。在此需要说明的是,对于这些实施方式的说明用于帮助理解本发明,但并不构成对本发明的限定。此外,下面所描述的本发明各个实施方式中所涉及到的技术特征只要彼此之间未构成冲突就可以互相结合。
[0039]
实施例1聚焦磷酸哌嗪的制备
[0040]
在氮气保护下,首先向五口烧瓶中加入磷酸(浓度85%)86g;在烧杯中加入无水哌
嗪32g及20g蒸馏水,在45℃下溶解后,通过恒压滴液漏斗滴加至五口瓶中,然后将反应液升温至95℃,反应2h后停止反应,冷却至室温后,反应液经过滤、淋洗、干燥后,得到97g中间体二磷酸哌嗪。将二磷酸哌嗪放至旋转蒸发器中进行真空脱水。首先,进行氮气置换,然后抽真空,绝压为20mmhg。控制升温速率,逐渐升温至脱水温度为280℃,脱水时间为3h,最终得到91.6g聚焦磷酸哌嗪。对其进行热重分析,如图1所示,失重1%的温度为302℃,失重5%的温度为338℃,800℃的残炭率高于25%。
[0041]
实施例2聚焦磷酸哌嗪的制备
[0042]
在氮气保护下,首先向五口烧瓶中加入磷酸(浓度85%)86g;在烧杯中加入无水哌嗪32g及20g蒸馏水,在45℃下溶解后,通过恒压滴液漏斗滴加至五口瓶中,然后将反应液升温至85℃,反应3h后停止反应,冷却至室温后,反应液经过滤、淋洗、干燥后,得到96.8g中间体二磷酸哌嗪。将二磷酸哌嗪放至旋转蒸发器中进行真空脱水。首先,进行氮气置换,然后抽真空,绝压为60mmhg。控制升温速率,逐渐升温至脱水温度为260℃,脱水时间为2h,最终得到92.1g聚焦磷酸哌嗪。
[0043]
实施例3聚焦磷酸哌嗪的制备
[0044]
在氮气保护下,首先向五口烧瓶中加入磷酸(浓度85%)86g;在烧杯中加入无水哌嗪32g及20g蒸馏水,在45℃下溶解后,通过恒压滴液漏斗滴加至五口瓶中,然后将反应液升温至90℃,反应2.5h后停止反应,冷却至室温后,反应液经过滤、淋洗、干燥后,得到96.6g中间体二磷酸哌嗪。将二磷酸哌嗪放至旋转蒸发器中进行真空脱水。首先,进行氮气置换,然后抽真空,绝压为40mmhg。控制升温速率,逐渐升温至脱水温度为270℃,脱水时间为2.5h,最终得到91.8g聚焦磷酸哌嗪。
[0045]
实施例4改性环氧树脂样条的制备
[0046]
称取150g环氧树脂加入到烧瓶中,于60℃水浴条件下预热,称取38.18g聚焦磷酸哌嗪、10.90g埃洛石纳米管、5.45g三聚氰胺氰尿酸盐,加入到环氧树脂中,在60℃水浴加热条件下充分搅拌30min,再超声分散1h,使得阻燃剂分散均匀,再加入68.18g固化剂间苯二胺,继续搅拌3min,保持温度,进行抽真空处理,除去混合物中多余的气泡,趁热倒入到预热处理并涂好jd-909a脱模剂的标准尺寸聚四氟乙烯模具中,放入烘箱于100℃下预固化1h,再升温至150℃固化1h,冷却脱模。
[0047]
实施例5改性环氧树脂样条的制备
[0048]
称取150g环氧树脂加入到烧瓶中,于80℃水浴条件下预热,称取35g聚焦磷酸哌嗪、5g埃洛石纳米管、10g三聚氰胺氰尿酸盐,加入到环氧树脂中,在75℃水浴加热条件下充分搅拌30min,再超声分散1h,使得阻燃剂分散均匀,再加入65g固化剂间苯二胺,继续搅拌3min,保持温度,进行抽真空处理,除去混合物中多余的气泡,趁热倒入到预热处理并涂好jd-909a脱模剂的标准尺寸聚四氟乙烯模具中,放入烘箱于110℃下预固化1.5h,再升温至150℃固化2h,冷却脱模。如图2所示,对其进行热重分析,其失重5%的初始分解温度为334℃,700℃残炭率为27%。
[0049]
实施例6改性环氧树脂样条的制备
[0050]
称取150g环氧树脂加入到烧瓶中,于70℃水浴条件下预热,称取18.75g聚焦磷酸哌嗪、3.75g埃洛石纳米管、15g三聚氰胺氰尿酸盐,加入到环氧树脂中,在75℃水浴加热条件下充分搅拌30min,再超声分散1h,使得阻燃剂分散均匀,再加入46.88g固化剂4,4'-二氨
基-二苯甲烷,继续搅拌3min,保持温度,进行抽真空处理,除去混合物中多余的气泡,趁热倒入到预热处理并涂好jd-909a脱模剂的标准尺寸聚四氟乙烯模具中,放入烘箱于105℃下预固化0.5h,再升温至180℃固化1.5h,冷却脱模。
[0051]
实施例7改性环氧树脂样条的制备
[0052]
称取150g环氧树脂加入到烧瓶中,于65℃水浴条件下预热,称取15.88g聚焦磷酸哌嗪、5.29g埃洛石纳米管、5.29g三聚氰胺氰尿酸盐,加入到环氧树脂中,在75℃水浴加热条件下充分搅拌30min,再超声分散1h,使得阻燃剂分散均匀,再加入44.12g固化剂聚酰胺,继续搅拌3min,保持温度,进行抽真空处理,除去混合物中多余的气泡,趁热倒入到预热处理并涂好jd-909a脱模剂的标准尺寸聚四氟乙烯模具中,放入烘箱于105℃下预固化1h,再升温至150℃固化2h,冷却脱模。
[0053]
实施例8改性环氧树脂样条的制备
[0054]
称取150g环氧树脂加入到烧瓶中,于90℃水浴条件下预热,称取13.33g聚焦磷酸哌嗪、1.67g埃洛石纳米管、1.67g三聚氰胺氰尿酸盐,加入到环氧树脂中,在90℃水浴加热条件下充分搅拌30min,再超声分散1h,使得阻燃剂分散均匀,再加入29.41g固化剂间苯二胺,继续搅拌3min,保持温度,进行抽真空处理,除去混合物中多余的气泡,趁热倒入到预热处理并涂好jd-909a脱模剂的标准尺寸聚四氟乙烯模具中,放入烘箱于105℃下预固化1h,再升温至150℃固化2h,冷却脱模。
[0055]
实施例9改性环氧树脂样条的制备
[0056]
称取150g环氧树脂加入到烧瓶中,于75℃水浴条件下预热,称取4.74g聚焦磷酸哌嗪、0.79g埃洛石纳米管、2.37g三聚氰胺氰尿酸盐,加入到环氧树脂中,在75℃水浴加热条件下充分搅拌30min,再超声分散1h,使得阻燃剂分散均匀,再加入21.53g固化剂间苯二胺,继续搅拌3min,保持温度,进行抽真空处理,除去混合物中多余的气泡,趁热倒入到预热处理并涂好jd-909a脱模剂的标准尺寸聚四氟乙烯模具中,放入烘箱于105℃下预固化1h,再升温至150℃固化2h,冷却脱模。
[0057]
对比例 纯环氧树脂样条的制备
[0058]
为了便于考察阻燃改性前后环氧树脂样条的性能对比,将购买的液体环氧树脂样品,按实施例4~9的操作步骤制备成固体样条,作为对比例,称取150g环氧树脂加入到烧瓶中,在80℃水浴加热条件18g固化剂间苯二胺,搅拌3min,保持温度,进行抽真空处理,除去混合物中多余的气泡,趁热倒入到预热处理并涂好jd-909a脱模剂的标准尺寸聚四氟乙烯模具中,放入烘箱于105℃下预固化1h,再升温至150℃固化2h,冷却脱模。如图2所示,对其进行热重分析,其失重5%的温度为342℃,700℃残炭率为15.7%。
[0059]
将上述实施例4~实施例9和对比例所制备的样条进行极限氧指数和垂直燃烧测试,其中极限氧指数测试样条的尺寸为100
×
10
×
2mm3,垂直燃烧ul-94测试样条的尺寸为125
×
13
×
3.2mm3,得到的实验结果如表1所示。对实施例5、实施例7和对比例进行了锥形量热测试,测试样条尺寸为100mm
×
10mm
×
2mm,得到的实验结果如表1和图3所示。
[0060]
表1样条的极限氧指数和垂直燃烧测试结果
[0061][0062]
从图2中可以看出,加入18.8%的高添加量阻燃剂时,实施例5样条的失重5%的分解温度由342℃降低为334℃。可见,添加阻燃剂后使其分解温度仅降低了2.3%,而残炭率由15.7%提高到了27%,说明本发明中添加阻燃剂后对环氧树脂热稳定性的降低影响较小,阻燃改性后的环氧树脂仍然具有较高的热稳定性。
[0063]
从表1中可以看出,在垂直燃烧和极限氧指数测试中,对比例样条有明显的滴落现象,且没有通过垂直燃烧等级测试,极限氧指数仅为19.5%,而加入阻燃剂的实施例4~实施例9样条的熔滴滴落现象得到了明显的抑制。其中,实施例4和例5在垂直燃烧测试中达到了ul-94v-0等级,且极限氧指数均高于34%。此外,在锥形量热测试中,对比例样条几乎燃烧殆尽,没有形成炭层,而实施例5和例7均形成了膨胀性炭层,从而提高了阻燃效率。同时,加入阻燃剂的实施例5和例7样条的平均热释放速率比对比样条也有明显的降低。上述结果表明本发明开发的膨胀型复配阻燃剂改性环氧树脂材料相比于改性前环氧树脂,在阻燃性能方面有了明显的提高。
[0064]
表2本发明与报道的已有膨胀型阻燃剂对比
[0065][0066]
注:初始分解温度降幅δt=(改性前样条初始分解温度-改性后样条初始分解温度)*100%/改性前样条初始分解温度(初始分解温度均为热重分析5%失重时温度)。
[0067]
将本发明开发的膨胀型复配阻燃剂与报道的已有膨胀型阻燃剂改性环氧树脂,在
优化配比下的极限氧指数和热稳定性进行了比较,如表2所示,本发明开发的复配阻燃剂改性环氧树脂的极限氧指数均高于文献报道的阻燃剂,且阻燃改性后与改性前样条的初始分解温度降幅均小于文献报道的阻燃剂,上述结果表明本发明开发的是兼具高稳定性和高阻燃效率的改性环氧树脂环保材料,可以满足环氧树脂复合材料发展的要求。
[0068]
本发明公开了一种高热稳定性的膨胀型复配阻燃剂改性环氧树脂材料及其制备方法,该方法通过低成本合成一种热稳定性高的p-n系阻燃剂,同时加入少量si系和n系阻燃剂,从而形成一种新型p-n-si系膨胀型复配阻燃剂,依据p-n-si的协效阻燃原理,来提高环氧树脂的阻燃性能。具体是由聚焦磷酸哌嗪、埃洛石纳米管和三聚氰胺氰尿酸盐按照质量比例(5~8):(1~2):(4~1)共混配制形成p-n-si系膨胀型复配阻燃剂,加入至环氧树脂中进行阻燃改性。本发明制备的阻燃材料具有良好的界面相容性和热稳定性,且阻燃效率优异,在优化配方条件下,改性环氧树脂阻燃可达ul94 v-0等级,极限氧指数可达34.3%。
[0069]
本发明公开和提出的技术方案,本领域技术人员可通过借鉴本文内容,适当改变条件路线等环节实现,尽管本发明的方法和制备技术已通过较佳实施例子进行了描述,相关技术人员明显能在不脱离本发明内容、精神和范围内对本文所述的方法和技术路线进行改动或重新组合,来实现最终的制备技术。特别需要指出的是,所有相类似的替换和改动对本领域技术人员来说是显而易见的,他们都被视为包括在本发明精神、范围和内容中。本发明未尽事宜属于公知技术。
再多了解一些
本文用于企业家、创业者技术爱好者查询,结果仅供参考。