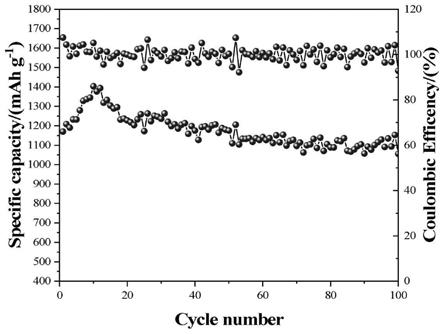
1.本发明属于新型储能材料技术研究领域,具体涉及自支撑正极的载硫木材基碳骨架的制作方法及其应用。
背景技术:
2.能源作为人类社会赖以生存和发展的物质基础,在国民经济中具有重要的战略地位。尽管太阳能、风能、水能、地热能、核能和潮汐能等新能源产业已经得到了大力开发,但由于这些可再生资源通常具有间歇性、不可预测性、季节性的特点,严重地制约了可再生资源的高效储存与利用效率。因而,建立清洁、高效、先进的可再生能源储存系统成为有效利用可再生能源的关键所在。经过近十年发展,锂离子电池能量密度已经趋于理论极限,实际组装电池能量密度小于260wh/kg已经无法满足当代社会电动汽车、智能电网等新兴产业对于电化学储能系统的更高需求,开发新型高效的电池储能系统是当务之急。
3.锂硫电池具有超高理论比容量(1675mah/g)和理论能量密度(2600wh/l),且单质硫储量丰富、环境友好,在成本和能量密度方面具有天然的优势。然而,由于活性物质的绝缘性和体积应变、中间产物的“穿梭效应”以及金属锂的安全隐患,导致锂硫电池发展缓慢。多年来,国内外学者采用活性物质(s8或li2s)与导电材料复合的策略改善锂硫电池正极内部电子传导能力,常用的导电材料包括碳材料、聚合物材料和金属化合物等。其中碳材料具有密度低、导电和导热性能优异、物理化学性质稳定、便于进行结构调控等优势,获得了广泛认可。
4.目前,商业化的电极材料制备过程都需要添加导电剂、粘结剂等,将活性物质涂布在金属集流体上。这种工艺会降低电极材料能量密度,限制电极中离子、电子的扩散迁移,从而降低储能性能。而利用整块导电多孔材料作为基体可无需添加剂和集流体制备自支撑电极,不仅能提高电池能量密度和理论容量,更能在大电流密度下表现出高倍率性能,更好的循环性能以及机械稳定性。
5.作为绿色碳源,生物质材料通常具有多级孔结构和丰富的有机大分子(糖类、蛋白质等),而且生物质材料一般含有多种非碳元素,因此碳化过程中还可同步实现杂原子掺杂,从而提高其应用性能。将生物质碳材料前驱体应用于制备环保可持续的新型储能器件是目前的研究热点,在众多的前驱体材料中,木质材料廉价易得、来源广泛,易于加工,可方便地制备成自支撑电极,且内部具有层状多孔结构(如垂直通道和众多的微/纳米孔隙),可以快速传递电子和电荷,同时等特点得到了众多研究人员的青睐。然而木材基碳材料用于锂硫电池时,由于垂直通道的尺寸过大,活性物质硫虽能大量存储但极易流失,对活性物质硫的束缚能力较低,导致储能性能孱弱,仍需深入研究改进其微观结构。
6.将木质基碳材料应用于高载硫自支撑正极尤其利于定制大规格锂硫软包电池。值得关注的是,木材基碳骨架作为束硫基体在软包电池有广泛的应用前景,但由于因此对木材孔道进行修饰以提高束硫能力必然是将木材应用于锂硫软包电池自支撑正极材料的关键步骤。
技术实现要素:
7.(一)解决的技术问题
8.针对现有技术的不足,本发明的目的是提供一种自支撑正极的载硫木材基碳骨架的制作方法,通过对木材中木质素进行去除,增加孔道结构,并溶解木材中的部分纤维素后,在在木材孔道中析出纤维素网络,从而起到改造木材孔道空间的作用,进而通过旋转滴涂的方法在木材基碳骨架内高密度负载八硫化锂,并实现活性物质的均匀分布。且通过改进后的木材孔道结构,增加电池容量的基础上改善动力学性能。本发明还将载硫木材基碳骨架作为自支撑正极应用于软包锂硫电池,可实现高的活性物质载量以及优良的电化学性能,易于定制大规格软包电池。
9.(二)技术方案
10.为实现上述目的,本发明提供如下技术方案:一种自支撑正极的载硫木材基碳骨架的制作方法,包含如下制作步骤:
11.步骤1:切割木材成条状,保持高度方向为木材生长方向,垂直于高度方向将木材切割成2mm厚的薄片,将木材薄片浸泡在去离子水中,70℃保温至木材薄片沉底;
12.步骤2:将沉底的木材薄片取出,在不同浓度亚氯酸钠的醋酸和乙酸钠缓冲溶液中,按浓度由高到低的顺序依次浸泡,之后将木材薄片用去离子水洗涤至中性;
13.步骤3:再将木材薄片依次在乙醇和n-n二甲基乙酰胺溶液中浸泡3~8min,重复4次,之后浸入含8wt.%licl的n-n二甲基乙酰胺溶液中静置24h;
14.步骤4:最后,取出木材薄片迅速浸入丙酮溶液中,停留2~4秒后取出,重复3-6次,后立即用液氮迅速冷冻,冷冻干燥24h;
15.步骤5:将冷冻干燥后的木材薄片压在两片石墨板之间,在氮气气氛炉中以3℃/min速度升温至250℃,保温3h,实现预碳化,继续在氮气气氛炉中以5℃/min速度升温至1000℃,保温3h,得到具有低挠度的孔道阵列结构的木材基碳骨架材料。
16.步骤6:将具有低挠度的孔道阵列结构的木材基碳骨架材料送入干室或手套箱,固定在旋涂仪上,设置转速为50~300rad/min,分次滴加一定体积一定浓度li2s8的dol/dme混合溶液,获得载硫木材基自支撑正极片。
17.优选的,步骤1中所述木材包括但不限于美洲椴木、白杨木和巴尔沙木,所述保温时间不固定,以木材薄片沉底为判断标准。
18.优选的,步骤2中所述的醋酸和乙酸钠缓冲溶液中亚氯酸钠的浓度梯度为5wt.%、3wt.%、1wt.%,浸泡温度为25~90℃及每次浸泡时间为3~9小时。
19.优选的,步骤4中所述的取出木材薄片迅速浸入丙酮溶液中,停留2-4秒取出,并重复该操作3-6次,后立即用液氮迅速冷冻,冷冻干燥24h。
20.优选的,步骤5中所述在预碳化后依次用1000、2000目砂纸将木材碳片打磨至300~600μm;并辅助超声清洗去除碳屑。
21.优选的,步骤6中采用旋转木材基碳骨架,滴加li2s8的dol/dme混合溶液的方法实现载硫,通过调节li2s8溶液体积为20~100μl、浓度为0.05~0.2g/ml实现对自支撑正极片载硫量的控制。
22.优选的,在载硫木材基自支撑正极片和锂箔负极片上端焊接相应极耳,再将自支撑正极、pp隔膜、负极进行层状堆叠,每层间滴加锂硫专用电解液,正负极耳集束分别焊实
后用铝塑壳密封,即获得锂硫软包电池。
23.优选的,层状堆叠保证两片负极在最外侧,内侧插入正极,根据电池设计容量规格内侧堆叠1~8层正极,两正极间需增加额外负极,每两极间需加入pp隔膜;三者尺寸应服从隔膜》负极》正极。
24.优选的,每层间滴加锂硫专用电解液为含有1m litfsi和2.5m lino3的dol/的混合溶液,添加体积为5~20μl/mg(s)。
25.(三)有益效果
26.本发明提供了可用作软包锂硫电池自支撑正极的木材基导电碳骨架的制备方法。具备以下有益效果:
27.1.本发明选取的生物质前驱体为木材,原料来源广泛、廉价环保。宏观结构上木材具有力学性能优异、便于加工组装等优点,微观上木材具有纤维和管胞组成的定向有序天然孔道结构以及孔壁上供气体交换的微孔结构,此种独特天然的木材孔道结构既有利于负载高密度硫活性物质,又为电解液的传输及离子扩散提供了高效通道,能够改善锂硫电池的电化学性能;
28.2.本发明制备的木材基碳骨架将木材切片浸泡于梯度亚氯酸钠溶液中并逐级递减溶质质量分数,在去除木质素、溶解纤维素的同时减少持续的酸性环境对木材产生副反应;加热过程中利用石墨板对木材切片保形,防止其卷曲,采用预碳化的处理方式有利于提升木材韧度,便于其打磨减薄以及后续处理;最终制备而成的木材基碳骨架具有更加合理的孔道分布状态,伴随孔壁和细胞壁上木质素的刻蚀以及纤维素的溶解及再析出,大量孔道得到填充和修饰,进一步提升了木材活化造孔的效果;基于孔道内部纤维素的三维交联结构,不仅能够提供完整的电子迁移网络和离子快速传输通道,而且可以捕获活性物质硫,限制多硫化物的溶解,抑制穿梭效应,从而增加放电比容量,提升循环寿命等电化学性能。
29.3.本发明制备的载硫木材基碳骨架自支撑正极材料同常用涂布型正极材料相比,制备工艺简单便捷,不需要导电剂、粘结剂和金属集流体,大幅增加了活性物质占比,载硫方式也有重要创新,配制高浓度电解液以旋涂的方式滴加在木材基碳骨架上,实现高载硫量的同时使得电解液在木材基碳骨架上浸润更为完全,活性物质分布更为均匀;
30.4.本发明制备的载硫木材基碳骨架自支撑正极材料组装软包电池方面也做出创新。电池组装过程以载硫木材基碳骨架自支撑正极材料尺寸为基准裁切锂箔和pp分别作为负极材料和隔膜,可根据设计规格,对极片尺寸、载硫量、堆叠层数进行合理调控,可制备出廉价高性能的定制大规格软包锂硫电池。
附图说明
31.图1本发明的为实施例1中制得自生纤维素填充的木材基碳骨架的扫描电镜图;
32.图2本发明的实施例1中装配电池的循环性能;
33.图3本发明的实施例2中装配电池的循环性能;
34.图4本发明的实施例3中装配电池的循环性能;
35.图5本发明的实施例4中装配电池的循环性能。
具体实施方式
36.下面将结合本发明实施例中的附图,对本发明实施例中的技术方案进行清楚、完整地描述,显然,所描述的实施例仅仅是本发明一部分实施例,而不是全部的实施例。基于本发明中的实施例,本领域普通技术人员在没有做出创造性劳动前提下所获得的所有其他实施例,都属于本发明保护的范围。
37.实施例1:
38.1.按照长宽尺寸为20*10mm切割木材为条状,保持高度方向为木材生长方向,垂直于高度方向将木材切割成2mm厚的薄片,将木材薄片浸泡在去离子水中,70℃保温至木材薄片沉底。
39.2.将沉底木材薄片取出,在不同浓度亚氯酸钠的醋酸和乙酸钠缓冲溶液中,按浓度由高到低的顺序(5wt.%,3wt.%,1wt.%)依次浸泡6h,浸泡温度为60℃,之后去离子水洗涤至中性。
40.3.再将木材薄片依次在乙醇和n-n二甲基乙酰胺溶液中浸泡5min,重复4次,之后浸入含8wt.%licl的dmac溶液中静置24h。
41.4.最后,取出木材薄片迅速浸入丙酮溶液中,停留3秒后取出,重复5次,后立即用液氮迅速冷冻,冷冻干燥24h。
42.5.将冷冻干燥后的木材薄片压在两片石墨板之间,在氮气气氛炉中以3℃/min速度升温至250℃,保温3h,实现预碳化,依次用1000、2000目砂纸将木材碳片打磨至450μm左右,每打磨几次需用超声清洗去除碳屑;继续在氮气气氛炉中以5℃/min速度升温至1000℃,保温3h,得到具有低挠度的孔道阵列结构的木材基碳骨架材料。
43.6.将具有低挠度的孔道阵列结构的木材基碳骨架材料送入干室或手套箱,固定在旋涂仪上,设置转速为200rad/min,分两次滴加40μl,0.1g/ml的li2s8溶液,获得载硫木材基自支撑正极片。
44.7.在载硫木材基自支撑正极片和锂箔负极片上端焊接相应极耳,再将自支撑正极、pp隔膜、负极进行层状堆叠,经过铝塑壳封装后获得锂硫软包电池。
45.实施例1制得的木材基碳骨架自生纤维素自支撑正极材料有很好的机械性能,其扫描电镜如图1所示,可见木材在垂直的孔道内部形成了三维交联纤维素结构。同时,图2为木材基碳骨架自生纤维素自支撑正极材料组装的锂硫电池电化学性能,可以看到,其初始放电比容量可以达到1276.3mahg-1
,在100次循环过程中每一圈的容量衰减仅在0.086%。利用bet比表面积测试得到木材基碳骨架自生纤维素自支撑正极材料的比表面积为380.65m2g-1
。
46.实施例2:
47.1.按照长宽尺寸为40*20mm切割木材为条状,保持高度方向为木材生长方向,垂直于高度方向将木材切割成2mm厚的薄片,将木材薄片浸泡在去离子水中,70℃保温至木材薄片沉底。
48.2.将沉底木材薄片取出,在含3wt.%亚氯酸钠的醋酸和乙酸钠缓冲溶液中,浸泡18h,浸泡温度为60℃,之后去离子水洗涤至中性。
49.3.再将木材薄片依次在乙醇和n-n二甲基乙酰胺溶液中浸泡8min,重复4次,之后浸入含8wt.%licl的dmac溶液中静置24h。
50.4.最后,取出木材薄片迅速浸入丙酮溶液中,停留4秒后取出,重复6次,后立即用液氮迅速冷冻,冷冻干燥24h。
51.5.将冷冻干燥后的木材薄片压在两片石墨板之间,在氮气气氛炉中以3℃/min速度升温至250℃,保温3h,实现预碳化,依次用1000、2000目砂纸将木材碳片打磨至450μm左右,每打磨几次需用超声清洗去除碳屑;继续在氮气气氛炉中以5℃/min速度升温至1000℃,保温3h,得到具有低挠度的孔道阵列结构的木材基碳骨架材料。
52.6.将具有低挠度的孔道阵列结构的木材基碳骨架材料送入干室或手套箱,固定在旋涂仪上,设置转速为200rad/min,分两次滴加40μl,0.1g/ml的li2s8溶液,获得载硫木材基自支撑正极片。
53.7.在载硫木材基自支撑正极片和锂箔负极片上端焊接相应极耳,再将自支撑正极、pp隔膜、负极进行层状堆叠,经过铝塑壳封装后获得锂硫软包电池。
54.实施例2制得的木材基碳骨架自生纤维素自支撑正极材料也具有很好的机械性能,电化学性能测试结果表明具有较好的电化学性能,如图3所示,其初始放电比容量可以达到1148.7mah g-1
,在100次循环过程中每一圈的容量衰减仅在0.34%。利用bet比表面积测试得到木材基碳骨架自生纤维素自支撑正极材料的比表面积为347.28m2g-1
。
55.实施例3:
56.1.按照长宽尺寸为20*20mm切割木材为方形,保持高度方向为木材生长方向,垂直于高度方向将木材切割成2mm厚的薄片,将木材薄片浸泡在去离子水中,70℃保温至木材薄片沉底。
57.2.将沉底木材薄片取出,在含1wt.%亚氯酸钠的醋酸和乙酸钠缓冲溶液中,浸泡18h,浸泡温度为60℃,之后去离子水洗涤至中性。
58.3.再将木材薄片依次在乙醇和n-n二甲基乙酰胺溶液中浸泡3min,重复4次,之后浸入含8wt.%licl的dmac溶液中静置24h。
59.4.最后,取出木材薄片迅速浸入丙酮溶液中,停留2秒后取出,重复3次,后立即用液氮迅速冷冻,冷冻干燥24h。
60.5.将冷冻干燥后的木材薄片压在两片石墨板之间,在氮气气氛炉中以3℃/min速度升温至250℃,保温3h,实现预碳化,依次用1000、2000目砂纸将木材碳片打磨至600μm左右,每打磨几次需用超声清洗去除碳屑;继续在氮气气氛炉中以5℃/min速度升温至1000℃,保温3h,得到具有低挠度的孔道阵列结构的木材基碳骨架材料。
61.6.将具有低挠度的孔道阵列结构的木材基碳骨架材料送入干室或手套箱,固定在旋涂仪上,设置转速为300rad/min,滴加20μl,0.2g/ml的li2s8溶液,获得载硫木材基自支撑正极片。
62.7.在载硫木材基自支撑正极片和锂箔负极片上端焊接相应极耳,再将自支撑正极、pp隔膜、负极进行层状堆叠,经过铝塑壳封装后获得锂硫软包电池。
63.实施例3制得的木材基碳骨架自生纤维素自支撑正极材料机械性能较差,电化学性能一般,如图4所示,其初始放电比容量可以达到647.35mahg-1
,在100次循环过程中每一圈的容量衰减仅在0.096%。利用bet比表面积测试得到木材基碳骨架自生纤维素自支撑正极材料的比表面积为420.78m2g-1
。
64.实施例4:
65.1.按照长宽尺寸为20*10mm切割木材为条状,保持高度方向为木材生长方向,垂直于高度方向将木材切割成2mm厚的薄片,将木材薄片浸泡在去离子水中,70℃保温至木材薄片沉底。
66.2.将沉底木材薄片取出,在含5wt.%亚氯酸钠的醋酸和乙酸钠缓冲溶液中,浸泡18h,浸泡温度为60℃,之后去离子水洗涤至中性。
67.3.再将木材薄片依次在乙醇和n-n二甲基乙酰胺溶液中浸泡5min,重复4次,之后浸入含8wt.%licl的dmac溶液中静置24h。
68.4.最后,取出木材薄片迅速浸入丙酮溶液中,停留3秒后取出,重复5次,后立即用液氮迅速冷冻,冷冻干燥24h。
69.5.将冷冻干燥后的木材薄片压在两片石墨板之间,在氮气气氛炉中以3℃/min速度升温至250℃,保温3h,实现预碳化,依次用1000、2000目砂纸将木材碳片打磨至450μm左右,每打磨几次需用超声清洗去除碳屑;继续在氮气气氛炉中以5℃/min速度升温至1000℃,保温3h,得到具有低挠度的孔道阵列结构的木材基碳骨架材料。
70.6.将具有低挠度的孔道阵列结构的木材基碳骨架材料送入干室或手套箱,固定在旋涂仪上,设置转速为300rad/min,分两次滴加40μl,0.1g/ml的li2s8溶液,获得载硫木材基自支撑正极片。
71.7.在载硫木材基自支撑正极片和锂箔负极片上端焊接相应极耳,再将自支撑正极、pp隔膜、负极进行层状堆叠,经过铝塑壳封装后获得锂硫软包电池。
72.实施例4制得的木材基碳骨架自生纤维素自支撑正极材料也具有很好的机械性能,电化学性能测试结果表明,也具有较好的电化学性能,如图5所示,其初始放电比容量可以达到961.2mah g-1
,在100次循环过程中每一圈的容量衰减仅在0.28%。利用bet比表面积测试得到木材基碳骨架自生纤维素自支撑正极材料的比表面积为416.53m2g-1
。
73.本发明在微观结构上具有低挠度通道,所用原料成本低廉且易于定制大规格、高载硫量及高能量密度的锂硫软包电池。便于加工组装等优点,微观上木材具有纤维和管胞组成的定向有序天然孔道结构以及孔壁上供气体交换的微孔结构,此种独特天然的木材孔道结构十分契合锂硫电池对正极材料的需求。
74.需要说明的是,在本文中,诸如第一和第二等之类的关系术语仅仅用来将一个实体或者操作与另一个实体或操作区分开来,而不一定要求或者暗示这些实体或操作之间存在任何这种实际的关系或者顺序。而且,术语“包括”、“包含”或者其任何其他变体意在涵盖非排他性的包含,从而使得包括一系列要素的过程、方法、物品或者设备不仅包括那些要素,而且还包括没有明确列出的其他要素,或者是还包括为这种过程、方法、物品或者设备所固有的要素。在没有更多限制的情况下,由语句“包括一个
……”
限定的要素,并不排除在包括所述要素的过程、方法、物品或者设备中还存在另外的相同要素。
75.尽管已经示出和描述了本发明的实施例,对于本领域的普通技术人员而言,可以理解在不脱离本发明的原理和精神的情况下可以对这些实施例进行多种变化、修改、替换和变型,本发明的范围由所附权利要求及其等同物限定。
再多了解一些
本文用于企业家、创业者技术爱好者查询,结果仅供参考。