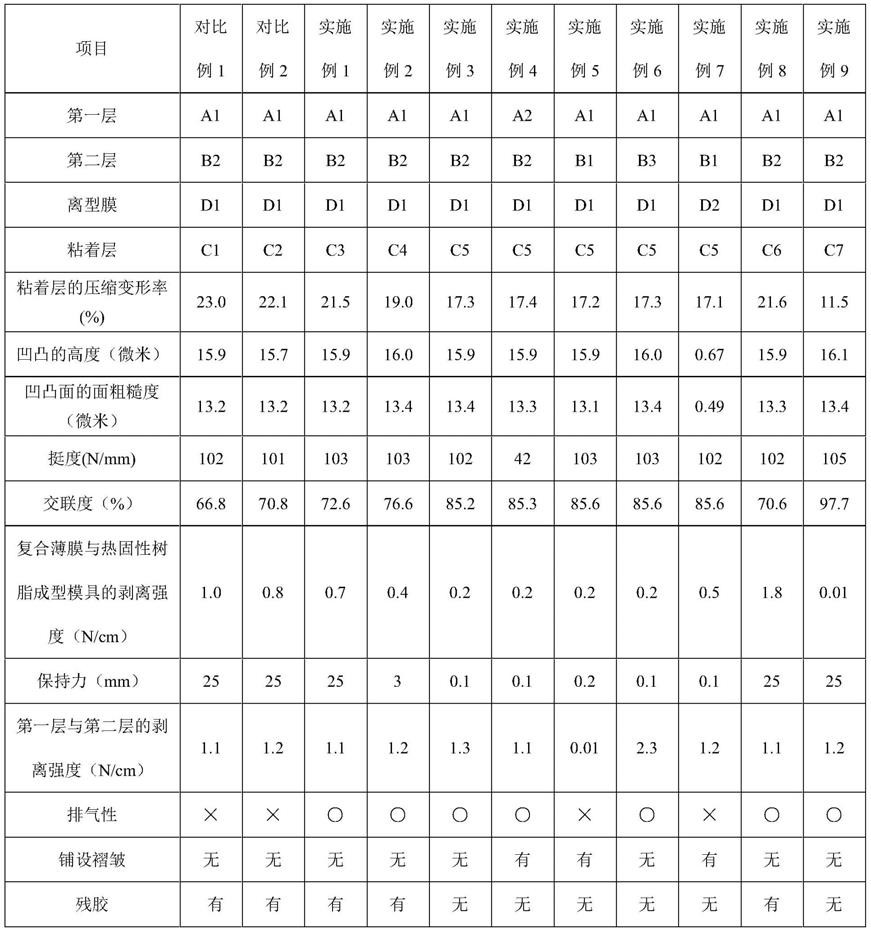
1.本发明属于高分子材料领域,具体涉及一种复合薄膜及其应用。
背景技术:
2.热固性树脂是指在一定温度、压力或紫外照射等条件下,发生交联反应,逐渐硬化成型,再受热也不软化、不溶解的一种树脂。热固性树脂与人类的生产、生活息息相关,可按照设计与使用需求,被加工成多种形状。比如环氧树脂,可以用于汽车内饰、支架、车门内外侧的外壳等各种形状板材上。
3.作为高分子材料的一种,热固性树脂的优点是耐热性高,受压不易变形。但其机械性能较差,一般难以满足超高机械强度的要求,这时需采用与无机材料复合的方法,既保证了材料轻量化、易成型的特点,又保证了材料的机械性能。最常见的是与玻璃纤维、碳纤维复合,这样可以增加材料的抗冲击性能。
4.无论是热固性树脂还是其复合材料,都可以采用常见的真空灌注成型工艺:将热固性树脂及固化剂等原料真空灌注到设定的模具内并加热,使之固化成型后脱去模具。为了保证成型品的尺寸精度,在具体的实施过程中,对树脂本身的性能和模具的表面状态、加工条件都有一定的要求。
5.风力发电机叶片作为大型成型体的一种,其结构一般较为复杂,对机械性能要求较高,而且随着技术的革新,叶片的大型化已经成为必然的趋势,这就对叶片的形状以及尺寸精度提出了更高的要求。叶片的成型工艺基本上采用上述的真空灌注成型,其技术难点集中在以下几个方面:1.如何高效脱模并保证模具在反复使用后,仍保持尺寸上的精度;2.如何高效处理叶片表面,同时避免涂装过程中粉尘和溶剂的产生。
6.作为现有技术,pct专利申请公开文本wo/2019/128802(申请号:pct/cn2018/122071)提供一种热固性树脂成型用(尤其是风力发电机叶片成型用)的薄膜材料,具有易操作、易移除、不损害模具内表面的尺寸精度、且在热固性树脂成型工艺后,薄膜材料功能层可向热固性树脂表面转移,赋予其功能性的特点,从而能够改善使用液体脱模剂带来的有机溶剂挥发、后续成型体表面打磨产生的粉尘及打磨难度高、模具多次使用后难以维持设计精度等问题。但现有技术仍然存在以下问题:(1)在模具上铺设时排气性差,有时薄膜和模具间的空气难以排出,形成气泡,影响成型品外观;(2)在模具铺设时易出现褶皱问题,影响成型品外观;(3)真空成型后在模具表面易出现残胶问题。
7.现有技术中,对于上述问题点(1)和(2),通常用腻子修复真空成型品表面的凹陷,再进行腻子的打磨,打磨过程仍然会产生粉尘,并增加了腻子修补以及腻子打磨的工序,对改善生产现场粉尘环境、缩短工期及节约用工成本不利。
8.现有技术中,对于上述问题点(3),通常用乙醇或乙酸乙酯等有机溶剂去除模具表面的残胶,增加了作业工序和用工成本,同时也会增加生产现场的voc的排放,不利于操作人员的健康,并且多次使用溶剂对模具进行擦拭会对模具造成损伤。
技术实现要素:
9.为了解决上述问题,本发明提供一种复合薄膜,该复合薄膜具有在热固性树脂成型工艺后,复合薄膜的功能层可向热固性树脂表面转移的功能性,同时具有易铺设、无褶皱、排气性好,易返工,且热固性树脂真空成型后模具表面无残胶、不损伤模具内表面的尺寸精度的特点。从而能够改善使用液体脱模剂带来的有机溶剂挥发、后续成型体表面打磨产生粉尘、模具多次使用后难以维持设计精度等问题,且相对于现有技术,该复合薄膜能够基本消除铺设过程中复合薄膜和模具间形成的气泡和褶皱提高铺设的质量和效率。同时真空成型后无残胶,避免因清理残胶而造成的现场voc排放及模具损伤等问题。
10.具体而言,本发明提供一种复合薄膜,至少含有相邻的第一层和第二层,所述的第一层的一侧设置有所述的第二层,另一侧设置有粘着层,在25℃时粘着层的压缩变形率小于等于22.0%。
11.所述的第一层是复合薄膜的基材,其主要功能是提供所述的复合薄膜以足够的力学强度、可操作性及可施工性。
12.所述的第一层含有聚酯树脂、聚氨酯树脂、聚碳酸酯树脂、聚烯烃树脂、丙烯酸树脂、聚酰亚胺树脂、聚酰胺树脂、芳纶树脂或氟树脂中的一种或多种。
13.所述的聚酯树脂是指主链上有酯键的杂链聚合物。可以举出聚对苯二甲酸乙二醇酯、聚对苯二甲酸丁二醇酯、聚对苯二甲酸环己二甲醇酯、聚偏苯三酸乙二醇酯、聚苯均三酸丁二醇酯、对羟基苯甲酸乙酯、聚间苯二甲酸新戊二醇酯、聚乳酸、聚对苯二甲酸己二酸丁二醇酯、聚丁二酸丁二醇酯、聚丁二酸己二酸丁二醇酯、聚己内酯或聚丁内酯等化学结构或上述化学结构与其它化学结构形成的共聚物。
14.所述聚氨酯树脂是指主链上具有氨酯键的高分子化合物。通常聚氨酯树脂可以通过多元醇和异氰酸酯的反应来制作。多元醇可以举出乙二醇、一缩二乙二醇、1,2-丙二醇、一缩二丙二醇、1,4-丁二醇、新戊二醇、1,6-己二醇、2-甲基-1,3-丙二醇、3-甲基-1,5-戊二醇、二羟基聚氧化丙醚、三羟基聚氧化丙醚、四羟丙基乙二胺或二羟基聚四氢呋喃氧化丙醚等含有多个羟基化学结构。作为异氰酸酯,可以举出甲苯二异氰酸酯、苯二亚甲基二异氰酸酯、亚甲基二苯基二异氰酸酯、亚苯基二异氰酸酯、萘二异氰酸酯、联甲苯胺二异氰酸酯等芳香族二异氰酸酯、α,α,α’,α
’-
四甲基苯二亚甲基二异氰酸酯等具有芳香环的脂肪族二异氰酸酯、亚甲基二异氰酸酯、亚丙基二异氰酸酯、赖氨酸二异氰酸酯、三甲基六亚甲基二异氰酸酯、六亚甲基二异氰酸酯等脂肪族二异氰酸酯、环己烷二异氰酸酯、甲基环己烷二异氰酸酯、异佛尔酮二异氰酸酯、二环己基甲烷二异氰酸酯或异亚丙基二环己基二异氰酸酯等脂环族二异氰酸酯等。这些物质可以单独使用,也可以多种并用。
15.所述聚碳酸酯树脂是指主链上含有碳酸酯键的高聚物树脂。聚碳酸酯树脂可以通过碳酸二酯进行酯交换,或者光气法合成。其中碳酸二酯可以举出碳酸二苯酯、碳酸二卞酯所代表的取代碳酸二苯酯、碳酸二甲酯或碳酸二叔丁酯等。这些碳酸二酯可以单独使用,也可以多种并用。具体的,聚碳酸酯树脂可以列举出双酚a型聚碳酸酯、氯代聚碳酸酯或烯丙基二甘醇碳酸酯等化学结构或上述化学结构同其它化学结构形成的共聚物等。
16.所述聚烯烃树脂是指由一种或多种烯烃聚合或共聚制得的树脂以及多种烯烃聚合物或共聚物共混制得的树脂,其中烯烃可以举出,乙烯、丙烯、丁烯、戊烯或降冰片烯等。具体的,聚烯烃树脂可以列举出高密度聚乙烯、低密度聚乙烯、等规聚丙烯,间规聚丙烯、聚
降冰片烯、聚1-丁烯、聚4-甲基-1-戊烯或乙烯-醋酸乙烯酯共聚物等化学结构或上述化学结构同其它化学结构形成的共聚物或共混物等。
17.所述丙烯酸树脂是以丙烯酸酯、甲基丙烯酸酯及苯乙烯等乙烯基类为主要单体合成的共聚物。所述的单体可以举出甲基丙烯酸甲酯、甲基丙烯酸乙酯、苯乙烯、丙烯腈、丙烯酸乙酯、丙烯酸正丁酯、丙烯酸月桂酯、丙烯酸-2-乙基己酯、甲基丙烯酸月桂酯、甲基丙烯酸正辛酯、丙烯酸-2-羟基乙酯、丙烯酸-2-羟基丙酯、甲基丙烯酸-2-羟基乙酯、甲基丙烯酸-2-羟基丙酯、甲基丙烯酸缩水甘油酯、丙烯酰胺、n-羟甲基丙烯酰胺、n-丁氧甲基(甲基)丙烯酰胺、二丙酮丙烯酰胺、甲基丙烯酸乙酰乙酸乙酯、二乙烯基苯、乙烯基三甲氧基硅烷、乙烯基三乙氧基硅烷、乙烯基三异丙氧基硅烷、γ-甲基丙烯酰氧基丙基三甲氧基硅烷、苯乙烯磺酸或乙烯基磺酸钠等化学结构或上述化学结构同其它化学结构形成的共聚物等。
18.所述聚酰亚胺树脂是主链上含有酰亚胺键的聚合物,可以举出缩聚型芳香族聚酰亚胺或加聚型聚酰亚胺。具体可以举出均苯型聚酰亚胺、双马来聚酰亚胺、pmr聚酰亚胺或乙炔端基聚酰亚胺等化学结构或上述化学结构同其它化学结构形成的共聚物等。
19.所述聚酰胺树脂,又称尼龙,可以举出尼龙6、尼龙66、尼龙11、尼龙12、尼龙610、尼龙612、尼龙46或尼龙1010等。
20.所述芳纶树脂,即芳香族聚酰胺,包括对位芳酰胺、间位芳酰胺或其共聚物。
21.所述氟树脂是指分子结构中含有氟原子的聚合物,可以举出,全氟化烷基乙烯基醚共聚物、聚全氟化异丙烯、乙烯-四氟乙烯共聚物、氟化乙烯丙烯共聚物、聚偏氟乙烯、聚四氟乙烯、聚三氟氯乙烯等化学结构或上述化学结构同其它化学结构形成的共聚物等。
22.考虑成本和原料的易得性,优选所述的第一层含有聚酯树脂、聚烯烃树脂、或聚酰胺树脂中的一种或多种。
23.所述的第一层可以通过公知的方法进行制备,比如通过压延法、流延法、吹塑法或拉伸等工艺。压延法是指将热塑性塑料通过一系列加热的压辊,使其连续成型为薄膜或片材的成型方法。流延法是指将树脂在挤出机熔融塑化,通过狭缝机头模口挤出,使熔料紧贴在冷却辊上,再经过拉伸、切边、卷取等工序形成薄膜的工艺。吹塑法是指树脂借助流体压力,在闭合模具中进行吹胀,使树脂成为中空制品的工艺。拉伸法是指在低于薄膜材料熔点、高于薄膜材料玻璃化转变温度的温度条件下,对膜纵向或横向拉伸,或纵横双向拉伸,然后在张紧状态下进行适当冷却的成膜工艺。
24.所述的第二层是功能性层,在热固性树脂成型工艺过程中或过程后,所述的第二层可以全部或部分地从所述复合薄膜上脱离,转移到热固性树脂成型品上,从而起到有益效果。所述的有益效果可以举例出,如提供耐热性、耐光性、耐紫外、耐燃性、耐腐蚀性、耐溶剂性、耐水性、耐老化性、耐燃油性、耐液压油、耐磨性、耐冲击性或装饰性等效果。第二层还可以起到粘结热固性树脂和额外相邻层的目的。此时根据需要,转移后的第二层的外侧还可以增加额外相邻层。
25.考虑到第二层需要有一定的功能性,优选所述的第二层含有聚氨酯树脂、环氧树脂、不饱和聚酯树脂、丙烯酸树脂或氟树脂中的一种或多种。
26.具体而言,作为所述的第二层可以举出以下这些。作为聚氨酯树脂类,可以列举出以下聚合物或涂料的固化物:佐敦涂料(张家港)有限公司产的jotatop bc100系列、jotatop bc100p系列、hardtop xp系列、jotatop bc200系列、jotatop bc800系列;上海麦
加涂料有限公司产的wu210a/b系列、wu233a/b系列;庞贝捷涂料(上海)有限公司产的lt2552/lw7260系列;鸿泽天诚科贸有限公司产的881-fydm-a/b系列。作为环氧树脂类,可以列举出以下聚合物或涂料的固化物:庞贝捷涂料(上海)有限公司产的lp149系列;阿克苏诺贝尔产的670hs-a/b系列;巴斯夫涂料(德国)有限公司产的wind hs topcoat-a/b系列;双狮涂料有限公司产的em400-a/b系列。作为不饱和聚酯树脂类,可以列举出以下聚合物或涂料的固化物:三化化工涂料有限公司产的191系列;青衣化工物资有限公司产的ts-817系列。作为丙烯酸树脂类,可以列举出以下聚合物或涂料的固化物:仁爱科技开发有限公司产的fnuh-606系列;吉田化工有限公司产的e0512系列。作为氟树脂类,可以列举出以下聚合物或涂料的固化物:大金氟化工(中国)有限公司产的gk570系列;山东应强新材料科技有限公司产的yq-f-011
-ⅰ
系列;仁爱科技开发有限公司产的hc-0210f-a/b系列。
27.所述的粘着层通过粘接所述的复合薄膜和热固性树脂成型模具,在模具上固定复合薄膜,并且能够在使用结束后,从成型模具上剥离,没有或很少有残胶。所述的粘着层含有聚乙酸乙烯酯、不饱和聚酯树脂、聚乙烯醇、聚酰胺树脂、聚氨酯树脂、聚丙烯酸树脂、聚酯树脂或有机硅树脂中的一种或多种。
28.所述的粘着层具体可以举例,水性胶粘剂:如聚乙烯醇类;溶剂型胶粘剂:如聚丙烯酸类、聚氨酯类;乳液型胶粘剂:如聚乙酸乙烯酯乳液;热固化型胶粘剂:如有机硅树脂类、不饱和聚酯树脂类;紫外线固化型胶粘剂:如聚丙烯酸酯类;厌氧固化型:如聚丙烯酸酯类;湿固化胶粘剂:如聚氨酯类;自由基聚合型:如聚丙烯酸酯类;热熔型胶粘剂:如聚丙烯酸酯类、聚酰胺树脂类、聚酯树脂类;压敏型胶粘剂:如聚丙烯酸酯类。
29.优选所述的粘着层为聚丙烯酸树脂的固化物,进一步优选所述聚丙烯酸树脂由丙烯酸-2-乙基己酯、丙烯酸丁酯、丙烯酸异丁酯、丙烯酸甲酯、甲基丙烯酸异丁酯、丙烯酸乙酯、乙酸乙烯酯、丙烯酸2-甲氧基乙酯、丙烯酸或甲基丙烯酸中的一种或多种单体聚合而成。进一步优选不包括含带羟基的丙烯酸类单体。具体而言,作为所述的聚丙烯酸树脂的固化物,可以举出以下这些:上海东洋油墨制造有限公司产bps 5330系列、bps 6298系列、bps5227-1系列、bps p-162n系列。
30.为了实现复合薄膜铺设时良好的排气性、耐残胶性及可返工性,所述的粘着层在25℃时的压缩变形率小于等于22.0%。如果在25℃下粘着层的压缩变形率大于22.0%,则会因为粘着层太软而压缩形变量过大而使粘着层表面的排气道堵塞而无法较好的排除气泡,且会因为胶层太软而出现残胶问题。进一步优选所述的粘着层的压缩变形率小于等于19.0%。
31.进一步的,为了使第二层能牢固的贴敷在第一层表面,第一层与第二层间需有一定的结合力,且考虑到热固性树脂成型中或后,所述第一层能够快速、简易的从第二层上剥离,第二层能够转移到热固性树脂成型品上,优选所述第一层和所述第二层之间的剥离强度在0.05~2n/cm之间。如果剥离强度大于2n/cm,则可能会出现第二层不能转移至热固性树脂表面,或第一层难以快速、简易的从第二层上剥离,一部分残留在第二层上的现象;如果剥离强度小于0.05n/cm,则可能第二层不能够稳定贴敷在第一层表面,复合薄膜在模具上铺设的过程中,第一层与第二层可能会发生剥离,难以顺畅的进行铺设。
32.为了复合薄膜在热固性树脂成型模具上铺设时具有良好的排气性,优选所述复合薄膜至少单个外表面有凹凸。所述的外表面是指复合薄膜最外侧与空气接触的表面。为了
制备外表面具有凹凸结构的粘着层的目的,在此优选使用压纹离型膜的制备方法,所述的压纹离型膜一般是指表面具有规则凹凸形状且凹凸高度均一的离型膜,将所述的压纹离型膜与复合薄膜的粘着层进行贴合,压纹离型膜凹凸面的形状会转印到粘着层表面,形成表面有凹凸结构的粘着层的复合薄膜,但复合薄膜表面的凹凸的制备并不限定此方法,具体可列举其他的制备方法例如:间隔涂布、点状涂布等。
33.为了复合薄膜在热固性树脂成型模具上铺设时具有良好的排气性,优选所述的粘着层的外表面有凹凸。
34.所述的凹凸是指复合薄膜表面高度大于1微米的凹陷或凸起。
35.考虑到较好的实现排气性,所述的粘着层外表面的凹凸高度在1~200微米。进一步优选所述的粘着层的具有凹凸的外表面的凹凸高度大于15微米。如果表面的凹凸高度小于15微米,则无法顺利实现排气的功能;如果表面的凹凸高度大于200微米,尽管也可以实现排气功能,但从实际生产的成本考虑,没有实际效益。
36.考虑到较好的实现排气性,优选所述的粘着层的具有凹凸的外表面的面粗糙度大于等于0.5微米。如果凹凸面的面粗糙度小于0.5微米,则会出现排气性不良。进一步优选所述的粘着层的具有凹凸的外表面的面粗糙度大于等于10微米。
37.考虑改善复合薄膜的排气性及铺设中的褶皱问题,优选所述复合薄膜的挺度在50~300n/mm。如果复合薄膜的挺度小于50n/mm,则铺设时易产生褶皱和排气性不良;如果复合薄膜的挺度大于300n/mm,尽管无褶皱和排气性问题,但因为挺度太大,复合薄膜对模具的随形性差,在模具弯角处复合薄膜弯曲而产生的应力易导致复合薄膜的粘着层与模具间脱胶,造成成型品的缺陷。
38.考虑到较好的实现排气性,优选所述粘着层的交联度在70~95%。如果粘着层的交联度小于70%,则会因为粘着层太软,铺设时粘着层表面受压后凹凸高度下降过大而造成铺设排气性不良;粘着层的交联度大于95%,则会因为粘着层交联度过高而造成粘着性下降,影响复合薄膜在模具上的固定。进一步优选所述的粘着层的交联度在80~95%。
39.所述交联度是指粘着层中不溶于乙酸乙酯的部分的质量在粘着层总质量中的占比。
40.粘着层的交联度的调整可通过对硬化剂的比例或粘着剂的分子量以及粘着剂中可参与交联反应的功能基团的量进行调整来实现。
41.考虑到较好的实现耐残胶性,优选在23℃时,所述复合薄膜粘着层对热固性树脂成型模具的剥离强度在0.02~4n/cm之间。如果剥离强度小于0.02n/cm,则复合薄膜会因为剥离强度太低而无法在模具表面固定;如果剥离强度大于4n/cm,则会因为剥离强度太高,在使用结束后剥除时出现残胶问题。
42.考虑到较好的实现耐残胶性,优选所述的复合薄膜在80℃,1kg挂重条件下70000秒后的保持力小于等于2.0mm。如果该条件下保持力大于2.0mm,则复合薄膜在真空成型温度下可能会因为粘着层的内聚强度低而出现内聚破坏,造成残胶问题。
43.本发明还提供上述的复合薄膜在汽车、火车、飞机等交通工具、电子元器件、成型加饰板等热固性树脂真空成型领域,尤其是风力发电机叶片成型上的应用。
44.在风力发电机叶片的真空成型工艺中使用时,第二层可以转移到叶片(主要由环氧树脂或聚氨酯树脂组成)的表面,起到底漆或底漆和面漆的作用,从而省去了现有工艺中
底漆涂覆前打磨叶片表面的工序和底漆(以及面漆)涂覆的工序,使得工艺流程简化,缩短工艺时间、节省人工、降低voc排放。
45.本发明的复合薄膜在风力发电机叶片的真空成型工艺中,能够改善该复合薄膜在模具铺设时的气泡和褶皱问题,可提升成型叶片表面的品质,提高铺设效率。另外,真空成型后易于从叶片模具上脱离,没有或很少有残胶,无需对模具进行清理,减少对模具的损伤,延长模具使用期限。
具体实施方式
46.通过以下实施例对本发明做更详细的描述,但所述实施例不构成对本发明的限制。
47.实施例与对比例中使用的测试方法如下,对于所有测试,如果没有明确说明测试温度,则在23℃时测试。
48.1.复合薄膜的粘着层的压缩变形率:
49.所述的复合薄膜的粘着层的压缩变形率是指通过热机械分析仪(tma)测得的粘着层的压缩变形率。具体测试的样品结构为所述复合薄膜剥除第二层后的结构,测试样品的尺寸为:8mm
×
8mm。测试前使用标准样品对tma进行校正、标准样品为东丽株式会社产双向拉伸聚丙烯薄膜30-2500h,厚度为30μm,粗糙度都为0.1μm。在25℃下对上述标准样品,沿厚度方向上施压一个从100mn起始并且以100mn/min的加压速率持续增加到1000mn的压力,记录压力到达1000mn时的压缩变形量。当上述标准样品压力到达1000mn时的压缩变形量≤0.3μm,校正完成。在25℃下使用校正后的tma对上述测试样品(复合薄膜剥除第二层),沿厚度方向上施压一个从100mn起始并且以100mn/min的加压速率持续增加到1000mn的压力,记录压力到达1000mn时的压缩变形量。所述的压缩变形率=压力到达1000mn时的压缩变形量/粘着层的厚度
×
100%。每个样品测3次,取3次结果的算术平均值记为复合薄膜的粘着层的压缩变形率的值。
50.所述粘着层的厚度为在25℃下测得的样品(复合薄膜剥除第二层)的厚度与第一层的厚度的差值。
51.所述的第一层的厚度为在25℃下测得的表面的粘着剂去除的样品(复合薄膜剥除第二层)的厚度,具体的样品表面粘着剂去除过程如下:将样品的粘着层用乙酸乙酯充分溶胀后用无尘布将粘着层擦除,再将粘着层擦除后的样品置于80℃烘箱中干燥10min。
52.2.复合薄膜层间的剥离强度:
53.复合薄膜层间的剥离强度指复合薄膜的第一层和第二层之间的剥离强度,单位n/cm:用tesa7475测试胶带对第二层进行补强,样品尺寸为150mm
×
10mm,使用拉伸机进行180
°
剥离、剥离速度为200mm/min。测试样品数量为3个,取3个测试结果的算术平均值作为剥离强度的结果。
54.3.复合薄膜表面的凹凸高度:
55.使用扫描电子显微镜或3d显微镜进行测量。测试复合薄膜表面5个不同点的凹凸的高度,取这5个不同点的高度的算术平均值作为复合薄膜表面的凹凸的高度值。
56.4.复合薄膜凹凸面的面粗糙度:
57.使用非接触表面形状测定仪(vertscan)进行测量。测试复合薄膜凹凸面5个不同
位置的面粗糙度,取这5个不同位置的面粗糙度的算术平均值作为面粗糙度的值。
58.5.复合薄膜的挺度:
59.先使用测厚仪测试复合薄膜样条(尺寸:150mm(长)
×
10mm(宽))的厚度,再用万能拉伸机测试该样条的弹性模量,拉升速率200mm/min,挺度=弹性模量
×
厚度,取5根样条挺度的算术平均值,记作复合薄膜的挺度。
60.6.复合薄膜的粘着层的交联度:
61.裁剪尺寸为5cm
×
12cm的300目的钢丝网称重记为w1,裁剪尺寸为3cm
×
10cm的复合薄膜样品,将复合薄膜的粘着层贴附于裁切好的钢丝网的中央并折叠钢丝网将复合薄膜完全包裹于钢丝网中称重记为w2,包裹有复合薄膜样品的钢丝网完全浸没于乙酸乙酯中,在50℃条件下放置16h,之后将包裹样品的钢丝网取出用乙酸乙酯清洗干净再在100℃下干燥5分钟后称重记为w3,将复合薄膜从钢丝网中取出,将表面残留的粘着剂用乙酸乙酯溶胀后擦除,然后在100℃下干燥5分钟称重记为w4。
62.交联度=(w3-w1-w4)/(w2-w1-w4)
×
100%
63.取3个不同位置样品的交联度的算术平均值作为复合薄膜的粘着层的交联度。
64.7.复合薄膜与热固性树脂成型模具的剥离强度:
65.复合薄膜与热固性树脂成型模具的剥离强度指复合薄膜的粘着层和热固性树脂成型模具之间的剥离强度,单位n/cm。将尺寸为150mm
×
10mm的样条,贴合到厚度为5mm,表面粗糙度(sa)≤0.7μm的环氧树脂板上,使用2kg的滚轮,在200mm/min的速度下在贴合有样条的环氧树脂板上来回滚压样条1次,静置20min后,使用拉伸机进行180
°
剥离强度测试,剥离速度为200mm/min,测试样品数量为3个,取3个测试结果的算术平均值作为剥离强度结果。
66.8.复合薄膜的保持力:
67.在23℃-65%rh的环境下,将尺寸为90mm
×
25mm的复合薄膜样品的一端25mm
×
25mm面积的区域与市售镜面钢板贴合后放入80℃中,在复合薄膜的另一端挂1.0kg重的砝码开始计时,如果70000秒内砝码不掉落,则将70000秒时复合薄膜在镜面钢板上滑移的距离作为保持力的数值,单位为mm,如果70000秒内砝码掉落,将复合薄膜与镜面钢板贴合区域的长度25mm作为保持力的数值,测试样品数量为5个,取5次测试结果的算术平均值作为保持力的结果,保持力的单位为mm。
68.9.复合薄膜的排气性:
69.将宽幅为1m的复合薄膜样品沿膜卷的放卷方向在橡胶刮片的压合下沿环氧树脂模具长度或宽度方向进行铺设,统计贴合区域的气泡的投影面积≥10mm2的气泡。测试不同的5个区域,取得到的5个值的算术平均值作为测试的结果,单位为个/m2。进行以下判定:
70.〇:排气性优,每平方米贴合区域中,气泡的投影面积≥10mm2且≤300mm2的气泡的个数小于3且无面积≥300mm2的气泡,则判定复合薄膜的排气性优;
71.×
:排气性差,不符合排气性优的条件则判定复合薄膜的排气性差;
72.实施例和对比例中使用的原料如下:
73.《第一层》
74.a1:东丽株式会社产双向拉伸聚丙烯薄膜30-2500h。厚度为30μm。两表面的表面张力都为31mn/m,粗糙度都为0.1μm。
75.a2:东丽株式会社产聚烯烃薄膜7h55g。厚度30μm,单面为自粘性表面,自粘性表面的表面张力为20mn/m,粗糙度为0.1μm;非自粘面表面张力为25mn/m,粗糙度为0.2μm。
76.《第二层》
77.b1:佐敦涂料(张家港)有限公司产bc100a/b,其中bc100a为主剂,固含量为76%,主要成份为聚氨酯类化合物聚酯多元醇类化合物;bc100b为固化剂,固含量为90%,主要成份为六亚甲基二异氰酸酯三聚体。按照bc100a:bc100b=6:1的质量比混合后,待用。该涂层的固化条件为23℃、144小时。
78.b2:添加了附着力促进剂的佐敦涂料(张家港)有限公司产bc100a/b,,其中bc100a为主剂,固含量为76%,主要成份为聚氨酯类化合物聚酯多元醇类化合物;bc100b为固化剂,固含量为90%,主要成份为六亚甲基二异氰酸酯三聚体;附着力促进剂,固含量为35%,化学组成:氯化聚丙烯,溶剂为乙酸乙酯,按照bc100a:bc100b:附着力促进剂=6:1:0.18的质量比混合后,待用。该涂层的固化条件为23℃、144小时。
79.b3:添加了附着力促进剂的佐敦涂料(张家港)有限公司产bc100a/b,,其中bc100a为主剂,固含量为76%,主要成份为聚氨酯类化合物聚酯多元醇类化合物;bc100b为固化剂,固含量为90%,主要成份为六亚甲基二异氰酸酯三聚体;附着力促进剂,固含量为35%,化学组成:氯化聚丙烯,溶剂为乙酸乙酯,按照bc100a:bc100b:附着力促进剂=6:1:0.51的质量比混合后,待用。该涂层的固化条件为23℃、144小时。
80.《粘着层》
81.c1:上海东洋油墨制造有限公司产bps5330/bxx5134,为聚丙烯酸酯型胶粘剂,bps5330为主剂,固含量主要成份为40%;bxx5134为固化剂,固含量为5%。质量配比为100:1.0,干燥条件为100℃,2分钟,固化条件为40℃,72小时。
82.c2:上海东洋油墨制造有限公司产bps5330/bxx5134,为丙烯酸酯型胶粘剂,bps5330为主剂,固含量主要成份为40%;bxx5134为固化剂,固含量为5%。质量配比为100:1.5,干燥条件为100℃,2分钟,固化条件为40℃,72小时。
83.c3:上海东洋油墨制造有限公司产bps5330/bxx5134,为丙烯酸酯型胶粘剂,bps5330为主剂,固含量主要成份为40%;bxx5134为固化剂,固含量为5%。质量配比为100:2.0,干燥条件为100℃,2分钟,固化条件为40℃,72小时。
84.c4:上海东洋油墨制造有限公司产bps5330/bxx5134,为丙烯酸酯型胶粘剂,bps5330为主剂,固含量主要成份为40%;bxx5134为固化剂,固含量为5%。质量配比为100:2.5,干燥条件为100℃,2分钟,固化条件为40℃,72小时。
85.c5:上海东洋油墨制造有限公司产bps5330/bxx5134,为丙烯酸酯型胶粘剂,bps5330为主剂,固含量主要成份为40%;bxx5134为固化剂,固含量为5%。质量配比为100:3.5,干燥条件为100℃,2分钟,固化条件为40℃,72小时。
86.c6:上海东洋油墨制造有限公司产bps p-162n/bxx4805,为丙烯酸酯型胶粘剂,bps p-162n为主剂,固含量主要成份为33%;bxx4805为固化剂,固含量为5%。质量配比为100:1.0,干燥条件为100℃,2分钟,固化条件为40℃,72小时。
87.c7:上海东洋油墨制造有限公司产bps-5227-1/bxx-5134,为丙烯酸酯型胶粘剂,其中bps-5227-1为主剂,固含量为41.5%;bxx-5134为固化剂,固含量为5%。bps-5227-1与
bxx-5134质量配比为100:15。粘度在25℃下为2000cps,干燥条件为100℃,2分钟,固化条件为40℃,72小时。
88.《离型膜》
89.d1:深圳德固赛诺技术有限公司产聚对苯二甲酸乙二醇酯压纹离型膜,厚度85μm。单面为离型表面,通过硅离型处理,通过扫描电镜的edx元素分析到离型表面有硅元素的存在,离型表面的表面张力为20mn/m;非离型面的表面张力为30mn/m。单面压纹处理,压纹形状为正方形尺寸约为:0.45mm
×
0.45mm,凹凸高度:20μm。
90.d2:上海孚众实业有限公司产聚对苯二甲酸乙二醇酯离型膜fz-mslxm。厚度75μm,纵向拉伸强度为149mpa,断裂伸长率为155%。单面为离型表面,通过硅离型处理,通过扫描电镜的edx元素分析到离型表面有硅元素的存在,离型表面的表面张力为20mn/m;非离型面的表面张力为32mn/m。单面凹凸处理,凹凸高度:0.69um。凹凸面粗糙度为0.47μm。
91.对比例1-2和实施例1-9
92.按表1所示的组成,使用湿膜制备器在a1或a2的任一面上涂敷粘着剂c2、c3、c4、c5、c6或c7后,与d1或d2进行复合,在所使用的粘着层的固化条件下固化,得到表面凹凸的粘着剂层。
93.继而,按表1所示的组成,使用湿膜制备器在第一层的另一面上涂敷第二层的原液b1、b2或b3后,在所使用的第二层的固化条件下固化,得到厚度为150μm的第二层。对得到的样品进行各种性能测定,结果列于表1。
94.表1
[0095][0096]
对比例1和2粘着层的压缩变形率较大,出现排气性、残胶问题。
[0097]
实施例1通过提高粘着层固化剂的量,使粘着层的压缩变形率降低,无排气性问题,但仍有残胶问题。
[0098]
实施例2在实施例1基础上继续提高粘着层固化剂的量,粘着层的压缩变形率继续降低但仍有少量残胶问题。
[0099]
实施例3在实施例2基础上继续提高粘着层固化剂的量,未出现残胶问题。
[0100]
实施例4相比实施例3,基材换成了更柔软的a2,挺度降低,出现了铺设褶皱问题。
[0101]
实施例5相比实施例3,去除了第二层配方中的附着力促进剂,第一层与第二层的剥离强度过低,第一层与第二层铺设时分层,出现铺设褶皱问题。
[0102]
实施例6相比实施例3,增加了第二层配方中的附着力促进剂的量,第一层与第二层的剥离强度过高,虽然未出现排气泡、铺设褶皱和残胶问题,但成型后出现第一层难以快速、简易的从第二层上剥离,一部分残留在第二层上的问题。
[0103]
实施例7相比实施例3,压纹离型膜换成表面凹凸高度较小的d2,造成粘着层表面凹凸高度变小,出现排气泡和铺设褶皱问题。
[0104]
实施例8相比实施例3,粘着层换成主剂分子量更低的c6,保持力变差,出现残胶问题。
[0105]
实施例9相比实施例3,粘着层的交联程度过大,粘着层与热固性树脂成型模具的剥离强度以及粘着层的保持力变差,复合薄膜无法在模具表面固定。
[0106]
综合以上实施例,实施例3为优选配方。
[0107]
由各实施例可见,本发明的复合薄膜,其设计的挺度和粘着层的压缩变形率、交联度及表面的凹凸结构可以在模具铺设过程中起到消除褶皱、排除气泡、及改善残胶性的效果。
再多了解一些
本文用于企业家、创业者技术爱好者查询,结果仅供参考。