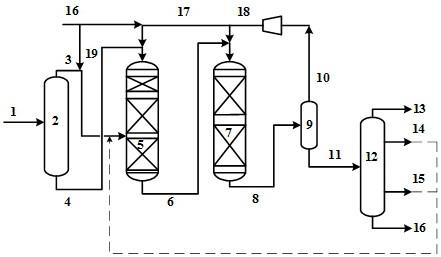
1.本发明属于石油化工领域,涉及一种加氢处理高氮原料的方法与系统,具体地说涉及一种灵活加工高氮劣质原料的加氢裂化方法与系统。
背景技术:
2.随着原油重质化的不断加剧及加氢裂化在炼化一体化中调节器作用的倍受重视,使得加氢裂化原料来源呈现出越来越重质化的趋势,加氢裂化原料油中的含氮化合物大幅度提升,含氮化合物的提升首先会抑制加氢裂化催化剂的活性,导致催化剂失活影响装置运行,其次由于含氮化合物的脱除难度较大,因此对产品质量也带来较大的不利影响。当原料油中的氮含量波动较大或异常增加时,装置的生产操作难度会急剧增加,往往需要降低空速或者提高段反应温度来实现。同时由于精制段反应温度的提升,导致精制段出口温度与裂化段入口温度不匹配,需要大量冷氢,造成巨大的经济损失。
3.cn1940030a公开了一种由高氮含量原料多产柴油的加氢裂化方法,高氮原料油经第一加氢精制反应器处理后,生成油进入热闪蒸罐进行气液分离后进入第二加氢精制反应器,在较缓和的工艺条件下,加工高氮劣质原料可有效地减少加氢精制催化剂的用量。该专利通过增设精制反应器来处理高氮原料,极大的增加了设备投资与催化剂购买成本,存在工艺流程固定灵活性差、精制段催化剂利用不充分及经济效益差等不足。
4.cn103102966a公开了一种处理高氮原料的加氢裂化方法,采用两段工艺流程,经第一段反应区后脱氮率控制为60~95%,第一段反应流出物经气液分离后重质尾油进入第二反应区进一步脱氮,该发明可在相对缓和条件下操作有利于提高加氢装置的运转周期。所述方法实际上也是通过增设精制反应器来处理高氮原料,同时增加了分离系统,存在设备投资与催化剂采购成本高等不足。
5.cn103773481a公开了一种处理劣质原料的联合加氢裂化方法,采用逆流工艺对高氮原料进行预处理,对常规原料采用并流工艺处理。所述方法能处理的高氮原料对于氮含量有所要求,同时工艺复杂,设备投资大经济性差。
技术实现要素:
6.针对现有技术的不足,本发明提供一种处理高氮原料的加氢工艺与加氢系统。所述工艺可在温和的操作条件下灵活处理劣质高氮原料同时延长整个加氢系统的运行周期,解决了现有技术依靠降低进料量、提高反应温度等方式造成催化剂的使用寿命缩短和装置的经济效益差的问题。
7.本发明首先提供一种处理高氮原料的加氢工艺,所述加氢工艺包括如下内容:高氮原料经分离后得到低氮馏分和高氮馏分;其中,高氮馏分经加氢精制反应区顶部进料口进入加氢精制反应区,低氮馏分经加氢精制反应区中下部进料口进入加氢精制反应区,在氢气和催化剂存在下进行加氢反应,反应流出物进入加氢裂化反应区进一步反应并经分离后得到目的产品,根据需要所述目的产品可以包括但不限于石脑油、航煤、柴油以及尾油
等;进一步优选的可以将将航煤和/或柴油循环回加氢精制反应区,更进一步优选通过中下部进料口进入加氢精制反应区与低氮馏分混合。
8.上述处理高氮原料的加氢工艺中,所述的高氮原料为氮含量大于1800μg/g的重质含烃物料,优选氮含量为2000~5000μg/g,硫含量没有特别的限制,所述高氮含量原料的初馏点一般为270~330℃,终馏点一般为460~560℃。进一步具体的所述高氮原料可以为深拔减压蜡油、焦化瓦斯油、脱沥青油、煤焦油、煤液化油中的一种或几种。
9.上述处理高氮原料的加氢工艺中,所述低氮馏分和高氮馏分的分割点温度为300~400℃,优选320~360℃。
10.上述处理高氮原料的加氢工艺中,所述加氢精制反应区和加氢裂化反应区可以设置于1个反应器中,也可以分别设置于独立的一个或多个反应器中。所述加氢精制反应区设置3个以上加氢精制催化剂床层,优选设置3~5个加氢精制催化剂床层,更进一步优选设置3~4个加氢精制催化剂床层。所述加氢裂化反应区设置1个以上的加氢裂化催化剂床层。
11.上述处理高氮原料的加氢工艺中,所述加氢精制反应区中下部进料口位于加氢精制反应区中任意两个加氢精制催化剂床层之间,优选设置于按照液相物料流动方向最下方两层催化剂床层之间,具体的当设置3个加氢精制催化剂床层时,可以设置于第一加氢精制催化剂床层与第二加氢精制催化剂床层之间和/或第二加氢精制催化剂床层与第三加氢精制催化剂床层之间;优选设置于第二加氢精制催化剂床层与第三加氢精制催化剂床层之间;以此类推,可以根据加氢精制催化剂床层设置数量和催化剂装填种类选择进料口的具体设置位置。
12.上述处理高氮原料的加氢工艺中,加氢精制反应区的操作条件为:氢分压为5~18mpa,优选为8~16mpa;氢油体积比为500~5000,优选为700~1500;体积空速为0.5~3h-1
,优选为0.7~2h-1
;反应温度为260~420℃,优选为300~400℃。
13.上述处理高氮原料的加氢工艺中,加氢裂化反应区的操作条件为,氢分压为6~18mpa,优选为7~17mpa;氢油体积比为500~5000,优选为700~1500;体积空速为0.2~5h-1
,优选为0.6~2h-1
;反应温度为270~460℃,优选为300~400℃。
14.上述处理高氮原料的加氢工艺中,所述加氢精制反应区中的加氢精制催化剂通常包括载体和活性金属组分,其中载体为氧化铝、氧化硅等无机耐熔金属氧化物中的一种或几种,优选为氧化铝;所述活性金属组分为vib和/或viii族金属中的一种或几种;如可以为w、mo、ni、co中的一种或几种,优选为ni和mo。一般情况下,以金属氧化物计,第vib族金属组分含量为10wt%~30.0wt%,优选11.5wt%~25.5wt%;第viii族金属组分含量为0.1wt%~8.0wt%,优选2wt%~6wt%。
15.上述处理高氮原料的加氢工艺中,沿液相物料流动方向,所述中下部进料口上方的加氢精制催化剂床层中的加氢精制催化剂的孔容逐渐减小,相邻两层加氢精制催化剂床层中的加氢精制催化剂孔容大小相差0.01~0.40ml/g,优选为0.03~0.22ml/g。所述中下部进料口下方加氢精制催化剂床层中的加氢精制催化剂的孔容不小于中下部进料口上方加氢精制催化剂床层中加氢精制催化剂的孔容,所述加氢精制反应区最上方加氢精制催化剂床层中加氢精制催化剂的孔容一般为0.30~0.50ml/g,优选为0.34~0.40ml/g。
16.上述处理高氮原料的加氢工艺中,沿液相物料流动方向,所述中下部进料口上方的加氢精制催化剂床层中的加氢精制催化剂的活性金属组分含量逐渐减小,以金属氧化物
计,相邻两层加氢精制催化剂床层中的加氢精制催化剂活性金属组分含量相差0.1~3.0wt%,优选相差0.5~2.0wt%;其中,第vib族金属组分含量相差0.1wt%~3.0wt%,优选相差0.5wt%~1.5wt%;第viii族金属组分含量相差0.1wt%~2.0wt%,优选相差0.2wt%~1.0wt%。所述中下部进料口下方加氢精制催化剂床层中的加氢精制催化剂的活性金属组分含量不小于加氢精制反应区最上方加氢精制催化剂床层中加氢精制催化剂的活性金属组分含量,以金属氧化物计,优选比最上方加氢精制催化剂床层中加氢精制催化剂的活性金属组分含量高0.1%~5.0wt%,优选高0.5%~2.0wt%。
17.上述处理高氮原料的加氢工艺中,进一步优选的所述加氢精制催化剂包括助剂氟,且沿液相物料流动方向,加氢精制催化剂中氟的负载量依次增加,相邻两层加氢精制催化剂床层中的加氢精制催化剂氟的负载量依次增加0.2~2.0wt%,优选为0.3~0.5wt%。所述加氢精制催化剂中氟的负载量一般为0.1~7.0wt%,优选为0.1%~3.5wt%。
18.上述处理高氮原料的加氢工艺中,所述加氢裂化反应采用的催化剂包括裂化组分和加氢组分。裂化组分通常包括无定型硅铝和分子筛。加氢组分为vi族、vii族或viii族的非贵金属元素的一种或几种,优选为co、mo、ni、w中的两种或两种以上金属为活性组分。以催化剂的重量为基准,加氢组分按氧化物计算含量10%~40%。可为任何商用加氢裂化催化剂,根据目标产品的不同选用不同类型的加氢裂化催化剂,需求石脑油可选用轻油型加氢裂化催化剂、需求中间馏分油则选用中油型加氢裂化催化剂、需灵活生产石脑油和中间馏分油则选用灵活型加氢裂化催化剂。例如抚顺石油化工研究院(fripp)研制开发的fc-52、fc-70、fc-76、fc-32等商用加氢裂化催化剂,也可根据需要按本领域的常识进行制备。
19.本发明另一方面提供一种处理高氮原料的加氢系统,所述加氢系统包括:分馏塔:其接收高氮原料,分离后得到低氮馏分和高氮馏分;加氢精制反应区:所述加氢精制反应区包括顶部进料口、中下部进料口和底部出料口;高氮馏分通过中下部进料口、低氮馏分通过顶部进料口进入加氢精制反应区,在氢气和加氢精制催化剂存在下进行反应,反应后得到加氢精制反应流出物;加氢裂化反应区:通过加氢精制反应区底部出料口将加氢精制反应流出物引出并进入加氢裂化反应区,在氢气和加氢裂化催化剂存在下进行反应;气液分离单元,其接收来自加氢裂化反应区的反应流出物,并将其分离后得到气相物料和液相物料;分馏单元,其接收来自气液分离单元的液相物料,并将其分离后得到气体、石脑油、航煤、柴油和尾油。
20.上述处理高氮原料的加氢系统中,所述加氢精制反应区和加氢裂化反应区可以设置于1个反应器中,也可以分别设置于独立的一个或多个反应器中。所述加氢精制反应区设置3个以上加氢精制催化剂床层,优选设置3~5个加氢精制催化剂床层,更进一步优选设置3~4个加氢精制催化剂床层。所述加氢裂化反应区设置1个以上的加氢裂化催化剂床层。
21.上述处理高氮原料的加氢系统中,所述航煤和/或柴油可以通过管线循环回加氢精制反应区,更进一步优选通过中下部进料口进入加氢精制反应区与低氮馏分混合。
22.上述处理高氮原料的加氢系统中,所述加氢精制反应区中下部进料口位于加氢精制反应区中任意两个加氢精制催化剂床层之间,优选设置于按照液相物料流动方向最下方两层催化剂床层之间,具体的当设置3个加氢精制催化剂床层时,可以设置于第一加氢精制
催化剂床层与第二加氢精制催化剂床层之间和/或第二加氢精制催化剂床层与第三加氢精制催化剂床层之间;优选设置于第二加氢精制催化剂床层与第三加氢精制催化剂床层之间;以此类推,可以根据加氢精制催化剂床层设置数量和催化剂装填种类选择进料口的具体设置位置。
23.上述处理高氮原料的加氢系统中,所述分馏塔、气液分离单元、分馏单元的设置可以采用本领域现有设置方式。气液分离单元包括热高压分离器、热低压分离器、冷高压分离器和冷低压分离器,所述分馏单元包括一个以上的分馏塔,所述分馏塔可以采用本领域现有能够实现油品分离设备中的任一种如填料塔、板式塔。
24.与现有技术相比,本发明处理高氮原料的加氢工艺与加氢系统具有如下优点:1、本发明提供的处理高氮原料的加氢工艺中,首先将高氮原料进行分离处理,并在加氢精制反应区内进行合理的催化剂级配,加氢精制反应区催化剂自上而下催化剂的孔容先降低再增加,加氢活性呈降低趋势、氢解能力呈增加趋势,将富含稠环含氮化合物(如咔唑等)的高氮馏分首先在上部加氢活性强的催化剂床层进行杂环的加氢饱和反应,可在温和的操作条件下处理劣质高氮原料同时延长整个加氢系统的运行周期。解决了现有技术依靠降低进料量、提高反应温度等方式造成催化剂的使用寿命缩短和装置的经济效益差的问题。
25.2、本发明提供的处理高氮原料的加氢工艺中,高氮馏分流经整个加氢精制反应区所有催化剂床层,由于低氮馏分的切出使得加氢精制反应区上部的加氢精制催化剂床层体积空速明显下降,通过上部加氢活性强的催化剂实现高氮馏分中氮杂质的脱除,同时原料中的杂质也因为低氮馏分从反应器中下部进料口进入加氢精制反应区,实现杂质不集中聚集在最上层催化剂床层,而是在整个反应区均匀分布,使得加氢精制反应区运行周期增加。
26.3、本发明提供的处理高氮原料的加氢工艺中,通过首先将高氮原料进行分离处理,并在加氢精制反应区内进行合理的催化剂级配的方式,使得加氢精制反应区最上方催化剂床层温升以及反应区出口温度明显下降、各床层温升均匀,既降低了冷氢的用量带来经济效益同时也明显降低了操作难度。解决了现有工艺中整个反应区温升分布不均匀(加氢精制反应区温升主要集中在最上方催化剂床层,反应区下部温升明显低于反应区上部),需要在催化剂床层之间注入大量冷氢造成运行成本增加,同时使得加氢精制反应区出口温度较高与裂化反应区入口温度不匹配的问题。
27.4、本发明提供的处理高氮原料的加氢工艺中,通过将中间馏分(柴油、航煤)通过中下部进料口循环回加氢精制反应区,一方面可以最大量生产化工原料(石脑油和尾油),而且可以提高产品质量。与现有中间馏分循环回加氢裂化反应区相比,路线更加合理,经济性大幅提升。
附图说明
28.图1为本发明处理高氮原料的加氢工艺与加氢系统示意图。
具体实施方式
29.下面结合附图和实施例进一步说明本发明方法的作用和效果,但以下实施例不构成对本发明的限制。
30.如图1所示,本发明所述处理高氮原料的加氢工艺包括如下内容:高氮原料1首先进入分馏塔2经切割分离后得到低氮馏分3和高氮馏分4,其中,高氮馏分4与新氢17经加氢精制反应区顶部进料口进入加氢精制反应区5,低氮馏分3和新氢17经加氢精制反应区中下部进料口进入加氢精制反应区5,在氢气和催化剂存在下进行加氢反应,加氢精制反应区的反应流出物加氢精制油6进入加氢裂化反应区7进一步进行开环、断链等反应,加氢裂化反应流出物8进入气液分离单元9经分离后得到气相组分10和液相组分11,其中气相组分10经处理和压缩机18处理后作为循环氢循环使用,可以循环回加氢精制反应区和加氢裂化反应区,液相组分11进一步进入分馏塔12,分馏后得到得到石脑油13、航煤14、柴油15以及尾油16;可以将航煤14和/或柴油15通过加氢精制反应区的中下部进料口循环回加氢精制反应区5与低氮馏分3混合进行处理。
31.实施例1高氮原料性质见表1,采用图1所示的工艺流程,其中柴油和航煤都不循环。分馏塔将高氮原料切为低氮馏分(276℃~360℃)和高氮馏分(360℃~549℃)两部分。加氢精制反应区包括三个催化剂床层,三个床层中的加氢精制催化剂载体都是氧化铝。其中,第一床层装填有加氢精制催化剂a-1,其孔容为0.34ml/g,以金属氧化物计ni、mo负载量分别为3.0wt%、23.0wt%。第二床层装填加氢精制催化剂b-1,其孔容为0.32ml/g,以金属氧化物计ni、mo负载量分别为2.5wt%、22.0wt%;f含量为0.6wt%;第三床层装填加氢精制催化剂c-1,其孔容为0.34ml/g,以金属氧化物计, co、mo负载量分别为3.5wt%、24.0wt%、f含量为2.6wt%。加氢精制催化剂总装填量为100ml,加氢精制催化剂a-1:加氢精制催化剂b-1:加氢精制催化剂c-1的体积装填比为20:30:50。加氢裂化反应区装填由中国石化抚顺石油化工研究院(fripp)开发的fc-76催化剂100ml,控制精制油氮含量不大于10
µg•
g-1
、裂化深度(>360℃)为70%,工艺条件列于表2、实验结果见表3。
32.实施例2高氮原料性质见表1,采用图1所示的工艺流程,其中中间馏分航煤14与柴油15全部通过加氢精制反应区中下部进料口循环回加氢精制反应区,以达到最大量的生产化工原料(石脑油、尾油)的生产目的。分馏塔将高氮原料切为低氮馏分(276℃~320℃)和高氮馏分(320℃~549℃)两部分。加氢精制反应区包括三个催化剂床层,三个床层中的加氢精制催化剂载体都是氧化铝。其中第一床层装填加氢精制催化剂a-2,其孔容为0.40ml/g,以金属氧化物计ni、mo负载量分别为6.0wt%、25.5wt%;f含量为0.5wt%;第二床层装填加氢精制催化剂b-2,其孔容为0.38ml/g,以金属氧化物计ni、mo负载量分别为5.8wt%、24.0wt%;f含量为1.0wt%;第三床层装填加氢精制催化剂c-2,其孔容为0.38ml/g,以金属氧化物计ni、mo负载量分别为6.3wt%、26.1wt%;f含量为1.3wt%。加氢精制催化剂总装填量为100ml,加氢精制催化剂a-2:加氢精制催化剂b-2:加氢精制催化剂c-2的体积装填比为40:40:20,加氢裂化反应区装填由中国石化抚顺石油化工研究院开发的fc-52催化剂100ml,控制精制油氮含量不大于10
µg•
g-1
、裂化深度(>360℃)为70%,工艺条件列于表2、实验结果见表3。
33.实施例3高氮原料性质见表1,采用附图1所示的工艺流程,其中只有柴油循环回加氢精制反应区。分馏塔将高氮原料切为低氮馏分(276℃~340℃)和高氮馏分(340℃~549℃)两部分,加氢精制反应区包括三个催化剂床层,三个床层中的加氢精制催化剂载体都是氧化铝。其
中第一床层装填加氢精制催化剂a-3,其孔容为0.39ml/g,以金属氧化物计ni、mo负载量分别为4.5wt%、24.0wt%,f含量为0.3wt%;;第二床层装填加氢精制催化剂b-3,其孔容为0.38ml/g,以金属氧化物计ni、mo负载量分别为3.8wt%、23.2wt%,f含量为0.6wt%;第三床层装填加氢精制催化剂c-3,其孔容为0.39ml/g,以金属氧化物计ni、mo负载量分别为5.0wt%、24.3wt%,f含量为1.0wt%。加氢精制催化剂总装填量为100ml,加氢精制催化剂a-3:加氢精制催化剂b-3:加氢精制催化剂c-3的体积装填比为30:30:40。加氢裂化反应区装填由中国石化抚顺石油化工研究院开发的fc-32催化剂100ml,控制精制油氮含量不大于10
µg•
g-1
、裂化深度(>360℃)为70%,工艺条件列于表2、实验结果见表3。
34.比较例1高氮原料性质见表1,采用常规单段串联工艺流程,高氮原料不经分馏处理,全部原料依次进入串联设置的加氢精制反应区和加氢裂化反应区,其中加氢精制反应区和加氢裂化反应区催化剂装填与实施例1保持一致。工艺条件列于表2、实验结果见表3。
35.比较例2高氮原料性质见表1,采用常规单段串联工艺流程,高氮原料不经分馏处理,全部原料依次进入串联设置的加氢精制反应区和加氢裂化反应区,其中,加氢精制反应区仅装填由中国石化抚顺石油化工研究院开发的ff-36加氢精制催化剂100ml,其孔容为0.36ml/g,以金属氧化物计ni、mo负载量分别为2.9wt%、23.6wt%,加氢裂化反应区装填由中国石化抚顺石油化工研究院开发的fc-76催化剂100ml。工艺条件列于表2、实验结果见表3。
36.表1 高氮原料性质表2 反应条件
表3 产品分布和产品性质通过对以上的实施例1-3和比较例1-2的数据分析表明,本发明提供的加氢裂化工艺流程,将重质原料分为轻重两部分由精制反应器的不同位置进入精制反应器结合精制催化剂的合理级配,处理高氮含量的加氢裂化原料时可以充分发挥加氢精制催化剂的反应活性,当控制精制油氮含量低于10
µg•
g-1
时,加氢精制反应区温度明显低于现有工艺,同时可以灵
活调整优化产品结构,一定程度的提升重石脑油产率收率以及航煤、柴油、尾油的产品性质,为炼厂带来显著的经济效益。
再多了解一些
本文用于企业家、创业者技术爱好者查询,结果仅供参考。