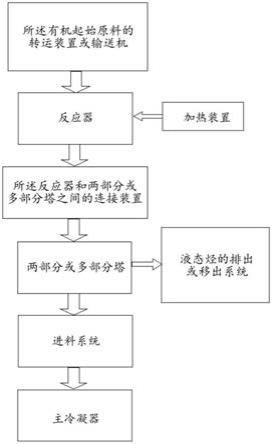
1.本发明涉及一种具有较高分子量的基本上有机起始原料的解聚(oiling)的方法,其中,通过高温作用获得优选为液态或半固态形式的烃和具有高碳含量的残余材料。
背景技术:
2.鉴于工业生产的商品数量不断增加,商品使用后的再利用或再循环越来越成为人们关注的焦点。例如,这些商品中许多是由有机产品制成的,比如塑料和/或塑料复合材料,因此该类产品的再利用或再循环尤为重要。另一方面,对于可用作例如化学合成的燃料和/或起始原料的产品的需求正在增加。
3.当将有机产品解聚时,上述需求均应被纳入考虑。解聚的原理基于这样一个事实,即对于具有高分子量的有机起始原料,例如生物残余材料以及工业可回收和残余材料,通过高达900℃高温的影响并在尽可能排除氧气的情况下,会引发一个或多个键断裂,从而形成具有较低分子量的较小分子。
4.解聚的一个实例为催化无压解聚(也被称为热催化低温转化),其本质上是人造或天然聚合物及长链碳氢化合物的解聚合方法。在无超压且温度低于400℃下添加催化剂的情况下,并优选在排除空气的情况下,其被转化为短链、脂肪族或芳香族的烃,其中对于高能塑料和油的效率或产率通常要高于生物质。如所述及地,所有含烃的高能物质都可以用作起始原料。实例为作为生物产品的植物残渣、木材、稻草和动物粪便,以及废油、固体残渣、橡胶、污水污泥,尤其是上述提到的作为工业产品的塑料。无机产品如金属、石头和其他污染物应事先去除。在高温下生成的气体可以通过冷凝分离成不同的馏分。
5.热解或热分解可视为解聚的另一个实例,其中使用与上述相同的起始原料。热解基于所述起始原料在高达900℃的温度下的热化学分解,其中不供应额外的氧气。所获得产物可以是气体、液体和固体,其中尤其是液体和蜡/石蜡可以通过蒸馏分离成不同的馏分,即发生不同温度下的分馏冷凝。
6.ep 3 260 181 a1记载了一种塑料材料(特别是废料)进料的热裂解方法。所述方法包括以下步骤:熔化进料,将熔化的进料输送至热解室,在热解室中置换氧气后,在基本惰性气氛中加热熔化的进料以将其转化为热解气体。该方法还包括以下进一步的步骤:将来自热解室的热解气体引入在其上端包含部分冷凝器的板式回流塔,使板式回流塔中冷凝的热解气体返回热解室,并蒸馏从回流塔的部分冷凝器排出的热解气体以获得一种或多种适合用作燃料的产物。然而,含碳的人造煤也作为副产物在热解室中形成。热解完成后,必须等待所述人造煤冷却后才能将其从热解室中移出,以便使热解室再次运转以用于后续批次。
7.因此,所记载的方法在某些方面似乎仍需改进,例如通过连续运转实现的高适应性应用、可变的材料投加量、确保热解室中排除氧气的完全惰性气氛,以及在热解气体分馏液化之前从其中分离粉尘和悬浮颗粒。
8.us 2018/273848 a1记载了一种在500℃至750℃温度的真空下进行的热解方法。
为此,将起始原料例如聚乙烯和聚丙烯在热解步骤之前进行造粒。
9.us 6,011,187记载了一种方法,在该方法中,使起始原料在不同温度下分两个阶段气化,其中热传递通过起始原料与砂的直接接触发生。在第一阶段,将起始原料与砂和/或添加剂混合并加热至250℃至350℃,以基本上去除卤素,例如氯。在第二阶段,将含砂的混合物加热至350℃至500℃以生成热解气体。第二阶段后,可以将留在砂中的焦炭在砂中燃烧。
10.us 2007/062104 a1记载了一种经特别改进的真空热解方法。热解反应器以类似于活塞发动机的方式工作,即其交替产生真空和压力,其中气化在600℃的真空下发生,热解气体和焦炭在随后的压缩冲程中被排出。
11.在这种方法中,经常会出现诸如热解反应器的活塞和气缸磨损的问题。
12.因此,仍然需要灵活可用的解聚方法,例如可以连续运行和/或在排除氧气的情况下运行的方法。
13.因此,本发明所针对的问题在于提供一种解聚方法并克服上述现有技术的缺点。
14.特别是,应提供一种可以连续运行的方式长期使用的解聚方法。
15.此外,应提供一种方法,其中不需要对起始原料进行高程度的处理,例如对起始原料造粒。特别是,还应可以使用研磨的起始原料和/或可能柔软、海绵状的起始原料。
16.除了在热解室(反应器)中排除氧气外,还应确保在将起始原料送入热解室时,以及在从热解室排出含碳残余材料期间,尤其是在连续运行期间排除氧气。
17.此外,还应提供基本上能量自给自足地运行的方法。
18.此外,应确保通过从生成热解气体中分离不需要的副产物(如粉尘和灰)而对热解气体进行清洁/冷凝的简化。
技术实现要素:
19.根据权利要求,本技术解决了这些问题中的至少一个。
20.因此,本发明的主题为一种连续生产烃的方法,包括以下步骤:(a)提供有机起始原料,(b)将所述有机起始原料转移到反应器中,(c)加热所述起始原料,产生热解气体,(d)将所述热解气体进料到两部分(two-part)或多部分(multi-part)塔,获得分离的液态和/或半固态的烃馏分,(e)获得在步骤(d)中所得的分离的烃,其中,步骤(b)和(c)在不存在氧气且在惰性气体下进行,并且其中,在步骤(c)中,将所述起始原料加热至400℃至600℃。
21.在上述ep 3 260 181 a1和实验室操作中,解聚通常以分批操作进行。为此,将一批起始原料转移到反应器中,并在所述反应器中加热以生成热解气体,随后通过蒸馏将其分离为相应的馏分。然后可以再次向反应器装料,也可以再次进行其他的步骤。
22.与此相反,本方法是一个连续的过程。换言之,其确保了反应器中起始原料的连续装料以及反应器连续运行,还有将生成的热解气体进料到两部分或多部分塔以及连续获得烃。此外,含碳残余材料(也被称为人造煤或焦炭)也可以在排除氧气的情况下从反应器中
连续移出,而无需中断甚至完全停止该过程。
23.在一个优选实施方案中,步骤(e)中获得的烃包含具有1至75个碳原子、优选2至60个碳原子、更优选3至40个碳原子、尤其是6至30个碳原子的脂肪族烃和芳香族烃。这些烃可以包括例如本领域技术人员已知的烷烃、环烷烃、环石蜡和芳香族化合物。优选地,所述烃在23℃和101.325kpa(常压)下以固体或液体形式存在,优选以液体形式存在。优选地,所生成的产物的沸点在柴油、汽油和蜡/石蜡的范围内。
24.在步骤(a)中,提供有机起始原料。在本发明的上下文中,有机起始原料为基于碳和氢的物质,并且还可以含有例如氧、氮、硫和卤素的元素。如上所述,有机起始原料可以是天然物质或天然来源的物质,也可以是合成(人造)生产的物质。有机起始原料也可以被称为替代燃料或二次燃料,因为它们也可以用于通过燃烧产生热能。
25.作为有机起始原料的天然物质的实例为植物或动物染料、糖、脂肪、蛋白质和维生素。还包括上述的植物残渣、木材、稻草、动物粪便、天然橡胶以及原油和煤炭等物质。
26.作为有机起始原料的合成物质的实例为如上所述的废油、固体残渣、橡胶和塑料,这些物质是从例如生活和商业废弃物的废弃物处理、生产废弃物和报废汽车的回收获得的。
27.合成材料,尤其是塑料或塑料混合物,优选地用作本方法中的有机起始原料。
28.塑料(德语:“kunststoffe”)为基本上由大分子组成的材料。塑料通常被通俗地称为塑料(德语:“plastik”)。在一个优选的实施方案中,所述塑料为聚合物。所述聚合物由一个或多个结构单元组成,即所谓的结构重复单元。本领域技术人员已知的塑料或聚合物可用于本方法。
29.聚合物的实例为聚酯,例如聚对苯二甲酸丁二醇酯、聚对苯二甲酸乙二醇酯、聚萘二甲酸乙二醇酯和聚碳酸酯;聚醚,例如聚亚烷基二醇醚、聚乙二醇、聚甲醛、聚甲醛二甲醚、聚丙二醇、聚四氢呋喃和聚乙烯醚;聚酰胺,例如pa612(来自己二胺和十二烷二酸)、pa11(来自11-氨基十一烷酸)、pa12(来自十二内酰胺或ω-氨基十二酸)和pa6/12(来自己内酰胺和月桂内酰胺);经取代和未经取代的聚亚烷基,例如聚乙烯、聚丙烯、聚乙酸乙烯酯、聚乙烯醇、聚氯乙烯和聚(烷基)甲基(丙烯酸酯),以及聚氨酯及其共聚物。
30.优选地,使用聚丙烯(pp)、聚乙烯(pe)、聚对苯二甲酸乙二醇酯(pet)、聚酰胺(pa)、丙烯酸-丁二烯-苯乙烯共聚物(abs)、聚对苯二甲酸丁二醇酯(pbt)及其混合物作为有机起始原料。
31.更优选使用聚亚烷基作为塑料。聚亚烷基的实例为聚乙烯、聚丙烯及其共聚物。
32.所述有机起始原料优选含有含量小于1.0wt.%的氯化物,和/或含量小于1.2mg/kg起始原料的汞,和/或含量小于2.0mg/kg起始原料的铊,和/或含量小于15.0wt.%、优选小于10wt.%、更优选小于5wt.%的水。在一个优选的实施方案中,上述水含量可通过例如在减压(优选50至600毫巴)下和/或在升高的温度(优选40℃至70℃)下干燥有机起始原料来实现。
33.此外,所述有机起始原料优选以小于60mm、更优选小于30mm、尤其是小于25mm的粒度存在,这特别是确保无问题地转移到反应器中(步骤(b))。或者,如果起始原料以膜的形式存在,则膜的表面优选小于0.25m2,更优选小于0.2m2,尤其是小于0.1m2。上述粒度或膜的表面可通过本领域技术人员已知的粉碎过程实现,例如切割、撕裂、研磨和筛分。
34.所述有机起始原料优选具有15mj/kg至40mj/kg、优选18mj/kg至35mj/kg、尤其是25mj/kg至30mj/kg的能量密度(热值)。
35.对步骤(a)中的起始原料的处理不必超过最普通的材料制备程度。特别优选的是,不必对起始原料进行造粒。
36.在一个优选的实施方案中,可将催化剂添加到有机起始原料中。所述催化剂可在有机起始原料转移或直接进料到反应器之前添加,或在反应器中添加;优选地,所述催化剂可在有机起始原料转移或直接进料到反应器之前添加到有机起始原料中。
37.催化剂是一种通过降低活化能而不消耗自身来提高化学反应的反应速率的物质。
38.本方法中,可使用相应的市售催化剂,例如铝硅酸盐基沸石。
39.在一个优选的实施方案中,将赤泥、粉煤灰、铝土矿、莫来石、沸石(优选来自zsm系列,尤其zsm-5系列)、fcc催化剂(“流化催化裂解”催化剂)、赤铁矿、氧化铁(ii)、铁或其混合物用作催化剂。
40.在一个更优选的实施方案中,将粉煤灰尤其是活化的粉煤灰用作催化剂。活化的粉煤灰为已经过本领域技术人员已知的预处理的粉煤灰。例如,将粉煤灰筛分,与naoh混合,煅烧(熔化),研磨,与水混合,硬化,过滤,洗涤,以及干燥。
41.在可选的更优选的实施方案中,将赤泥用作催化剂。赤泥是一种可例如在采用拜耳法处理铝土矿以获得氧化铝时生成的残渣。将精细研磨的铝土矿与氢氧化钠混合,氢氧化铝可在其中溶解。不溶性化合物残留在残渣中,即赤泥。赤泥基本上可含有30wt.%至40wt.%的fe2o3、20wt.%至30wt.%的al2o3、10wt.%至17wt.%的tio2、5wt.%至12wt.%的sio2、3wt.%至6.5wt.%的cao和1wt.%至3wt.%的na2o。
42.在另一个优选的实施方案中,还可以将用于去除在有机起始原料于反应器中热解过程中生成的有机和无机卤素化合物(例如氟、氯、溴和碘化合物和/或硫化合物)的输入材料添加到有机起始原料中。换句话说,所述输入材料可被视为热解过程中生成的卤素和/或硫化合物的吸附剂。它们可以与热解产生的其他残余材料(例如含碳的人造煤(焦炭))相同的方式从反应器中连续排出。
43.用于去除有机和无机卤素化合物和/或硫化合物的输入材料的实例为氢氧化钙(ca(oh)2)、氧化钙(cao)、碳酸钙(caco3)、氢氧化钠(naoh)、纯碱(na2co3)、氢氧化钾(koh)、碳酸钾(k2co3)、赤铁矿(fe2o3)、赤泥或其混合物。
44.在一个优选的实施方案中,将赤泥或赤铁矿,更优选赤泥添加到有机起始原料中,因为赤泥作为催化剂和作为去除有机和无机卤素化合物和/或硫化合物的输入材料均是有效的。
45.在一个优选的实施方案中,所述有机起始原料和催化剂可在反应器中以10:1至1:2的重量比使用。
46.在可选的优选实施方案中,未向有机起始原料中添加催化剂。这意味着根据本发明的方法也可以在没有催化剂的情况下进行。
47.在步骤(b)中,将所述有机起始原料转移到反应器中,其中该步骤在不存在氧气的情况下进行。
48.可以本领域技术人员已知的任何方式将有机起始原料转移到反应器中。为此,例如可以使用所有已知的转运装置或输送机;有机起始原料的转移可优选地通过一条或多条
传送带进行。此外,在转移起始原料期间,可以使用金属分离器分离金属。通过使用金属分离器分离可能残留在有机起始原料中的金属部分,可以保护系统部件,例如转运装置,并且可以实现过程的无故障或几乎无故障运行。结果是,可以实现进行本发明方法的装置的稳定性的增加。此外,上述金属部分的分离防止或者至少有利地减少步骤(c)中可能的副产物的形成,其中在排除氧气的情况下加热起始原料。
49.在本方法中,将有机起始原料转移到反应器中是在无氧气下和在惰性气体下进行的。在本发明的上下文中,这意味着有机起始原料已基本上不含氧气,所述氧气例如可存在于周围大气(通常为空气)中,存在于各个起始原料碎片之间的间隙中。这可以通过本领域技术人员已知用于产生负压的任何抽空系统来实现,后续可通过引入惰性气体特别是氮气来消耗负压。
50.在一个优选的实施方案中,在步骤(b)中,所述有机起始原料不含氧气。例如,在本方法中,可通过双锁系统使有机起始原料在传送带上不含氧气。换言之,在本方法中,利用经由两个锁室(每个锁室均具有双挡板系统)的真空泵抽空有机起始原料周围的气体,特别是空气,由此使有机起始原料不含氧气。然后,可以向有机起始原料施加优选至多为大气压力的惰性气体(优选氮气)。此过程可以重复若干次以尽可能多地置换氧气。然后,可优选通过冷却螺旋输送机将有机起始原料引入反应器。因此,优选以无压的方式将有机起始原料引入反应器中。
51.在本方法的上下文中,在开始转移有机起始原料或将其首次引入反应器之前,使反应器本身也不含氧气并达到所需的温度。为此,对反应器进行加热,并使惰性气体(优选氮气)流过反应器。在用输入材料填充反应器之前,用惰性气体吹扫以确保尽可能完全排除氧气,并确保反应器尽可能完全充满惰性气体。
52.在步骤(c)中,加热有机起始原料以产生热解气体。在一个优选的实施方案中,步骤(c)通过对反应器进行加热来进行。为此,直接或间接地对反应器进行加热,优选间接加热。在一个优选的实施方案中,反应器优选在步骤(c)中经由双重壁间接加热。可以使用本领域技术人员已知的任何加热装置经由双重壁对反应器进行加热。优选使用一个或多个热气发生器将反应器的一个或多个加热区加热至加热区特定的恒定温度,在该温度下随后发生起始原料的热解。这些温度在400℃到600℃之间,优选在450℃到580℃之间,特别是在500℃到560℃之间;特别优选地,该温度约为550℃。
53.在一个优选的实施方案中,可以将来自塔顶部的水不溶性气体和不可凝性气体和/或引导通过燃烧后室的热解气体进给到加热装置,以便在达到上述温度后对反应器进行加热,从而使得本发明的方法可以能量自给地进行。优选地,在被进给到加热装置之前,可以例如通过气体洗涤器对所述水不溶性气体和不可凝性气体进行清洁。
54.所述热气发生器可以是本领域技术人员已知用于产生高温的所有装置。对反应器的热空气供应优选由气体燃烧器和各个燃烧室组成。在所述燃烧室中,气体燃烧器火焰的热量可以传递到空气,从而可以将各个加热区内的反应器双重壁之间的间隙加热到所需温度。
55.此外,优选将较大的有机起始原料碎片在反应器中混合(优选通过搅拌器)并将含碳残余材料输送至排出口。此外,优选将有机起始原料强烈混合(优选通过搅拌器),任选地进行压缩并使其可更快地进行热输入。此外,将有机起始原料的碎片部分或全部(优选全
部)转化为气相。另外优选地,还将所述有机起始原料优选通过搅拌器分布在反应器的尽可能大的内表面上,以便在双重壁的反应器侧发生尽可能多的热传递。在反应器的后部,使搅拌器倾斜较小。
56.在上述温度范围内,有机起始原料在反应器中的平均停留时间在15分钟和120分钟之间,优选在20分钟和100分钟之间,特别是在30分钟和90分钟之间,尤其是大约45分钟。在该过程中,有机起始原料中的键在排除氧气的情况下发生热分解,其中生成热解气体。在排除氧气情况下的热分解也可被称为裂解过程。
57.残余材料,优选固体残余材料,可在本方法中作为副产物形成。可在本方法中形成的固体残余材料的实例为上述含碳人造煤和同样可能存在于有机起始原料中的矿物组分。可将残余材料从反应器中排出,其中在本方法中以这样的方式进行,即当排出残余材料时,防止氧气输入反应器中。为此在本方法中,可以例如通过缓冲溜槽确保残余材料的累积(灰层)。随后,可将残余材料优选在冷却的情况下(例如通过冷却螺旋输送机)从反应器中排出。将残余材料通过冷却螺旋输送机冷却至优选室温。所述冷却可优选地防止残余材料中所含的碳的氧化。
58.在一个优选的实施方案中,将步骤(c)中获得的热解气体在反应器上端移出并进行步骤(d)。这样做是为了避免或至少大大减少可能的不期望的其他副反应。在一个优选的实施方案中,生成的热解气体包含气态烃。此外,生成的热解气体优选不包含液态或固态形式的烃。
59.在步骤(d)中,将热解气体经由连接装置从反应器进料至两部分或多部分塔,以获得分离的烃馏分。为此,可以将热解气体从反应器室连续进料到(优选通过绝热管道)两部分或多部分塔以进行分馏。
60.在本方法中,所述两部分或多部分塔优选配置为两部分塔。在一个优选的实施方案中,塔的第一部分设置在反应器或绝热管道与塔的第二部分之间,并且可以被视为两部分或多部分塔的下部。塔的第二部分设置在两部分或多部分塔的第一部分之上。因此,它也被称为塔的上部。塔的第一部分(下部)和第二部分(上部)优选以流体密封的方式(即以气体密封和液体密封的方式)彼此连接。在本方法中,该流体密封连接可优选地配置为绝热管道或法兰连接,尤其是绝热管道。
61.在本方法中,当将热解气体进料到两部分或多部分塔中时,将气体冷却,并根据沸程使其组分分馏液化。可以例如使用控制阀来确保对分馏液化组分的各馏分的移出。换言之,通过将热解气体进料到两部分或多部分塔中,使其进行(分馏)冷凝,其中不同的馏分彼此分离地获得。
62.在一个优选的实施方案中,所述两部分或多部分塔,优选两部分塔的第一部分(下部)为急冷塔。如上所述,在本方法中,将热解气体从反应器连续地进料到两部分或多部分塔,并由此进料到急冷塔。所述急冷塔可为普通蒸馏塔或分馏塔。分馏塔是一种蒸馏塔,其中塔身装有组件(也称为塔板)以加强气相和液相之间的热量和物质交换。在本方法中,分馏塔包含有多个塔板,优选10至30个塔板,特别是约15个塔板。此外,急冷塔优选在轻微负压下运行,尤其是在0.75巴至0.85巴的顶部压力下,优选为约0.8巴。在所述急冷塔内,优选将热解气体的温度降低到280℃至320℃,尤其是约300℃。第二上部塔底部的液体产物特别地可用于冷却热解气体。此外,优选将急冷塔配备有一个或多个温度测量点,用于检查本方
法的合适实施。
63.在一个优选的实施方案中,所述两部分或多部分塔,优选两部分塔的第二部分为分馏塔。两部分或多部分塔的第二部分(上部)中的分馏塔优选具有多个塔板,优选10至40个塔板,更优选20至35个塔板,尤其是约30个塔板。经过急冷塔时被冷却的气体通过第一和第二塔的气体密封连接件流入第二塔,即分馏塔。与第一塔(急冷塔)类似,分馏塔优选在轻微的负压下运行,尤其是在0.75巴至0.85巴的顶部压力下,优选为约0.8巴。
64.在两部分塔的第一部分(下部)和第二部分(上部)中,均可在组件(例如塔板)处建立相应馏分的液相和气相之间的平衡。换言之,通过这样的方式,可以在优选的两部分塔中的不同塔板处优选分馏地获得分离的液态烃,其中该获得和分离是通过相应馏分的不同沸程而实现的。
65.在本方法的优选实施方案中,热解气体在两部分或多部分塔的第一部分中的流速低于其在后续的两部分或多部分塔的第二部分中的流速。特别优选地,热解气体在优选的两部分塔的第一部分中的流速低于其在后续的优选的两部分塔的第二部分中的流速。由于在塔的第一部分中的流速较低,因此可以实现对热解气体的清洁作用。例如,没有粉尘颗粒或灰被夹带到优选两部分塔的第二部分(上部)中。
66.在本方法的一个实施方案中,步骤(d)中,水,例如在热解过程中形成的水或已存在于有机起始原料中的水,通过相分离而从烃中分离。在该水相中,污染物,例如酸性化合物、挥发性重金属(比如汞)和卤素(比如氯)可积聚,从而导致这些物质在后续馏分中的比例降低(“污染物去除”)。为此,可以使用本领域技术人员已知的相分离器。分离出的水可优选进给到水处理单元,在那里将污染物分离。
67.在步骤(e)中,获得在步骤(d)中所得的分离的并且优选为液态的烃。这意味着将分离的优选液态的烃通过排出系统从优选的两部分塔中排出,并且如有必要,进一步处理或清洁。从优选的两部分塔排出后获得的烃优选在23℃(室温)和101.325kpa(常压)下呈液态形式。或者优选地,所述烃在从优选的两部分塔,特别是从优选的两部分塔的第一部分排出后可以固化,使其可以半固体物质或固体形式存在。半固态物质为介于固态和液态之间的物质,例如蜡(比如石蜡)。这些物质优选以温暖、液体的状态储存。
68.为此,可将优选的两部分塔的第一部分(急冷塔)配备一个或多个控制阀作为排出系统,通过该系统将沸程大于300℃且小于500℃的馏分排出/移出。在一个优选的实施方案中,将沸程为从热解气体入口温度(合成气)到约320℃的馏分移出。该馏分可含有多达75个碳原子的烃。实例为重油/石蜡。由于急冷塔底部的高温,当装填产物储罐时优选将底部产物冷却。
69.此外,优选的两部分塔的第二部分(分馏塔)可包括一个或多个温度传感器,其可监测分馏塔内的底部、各个塔板和顶部的温度。与急冷塔类似,分馏塔也可以配备有一个或多个控制阀,通过这些控制阀可以将所需范围内的各个馏分移出。在一个优选的实施方案中,将沸程为220℃至320℃的馏分移出。该馏分可含有7至22个碳原子的烃。实例为柴油燃料。优选地,还可将沸程为150℃至200℃的馏分移出。该馏分可含有5至9个碳原子的烃。实例为汽油燃料。
70.此外,优选将通过优选的两部分塔后仍为气态的热解产物部分(气体顶部产物)经由进料系统进料到主冷凝器,该主冷凝器在冷却的同时将热解气体另外的馏分冷凝/液化。
这些液化/冷凝的馏分也可以优选通过控制阀移出。优选将沸程为50℃至150℃的馏分移出。该馏分也被称为顶部馏分,可包含具有1至10个碳原子、优选2至9个碳原子、尤其是5至7个碳原子的脂肪族烃或芳香族烃。实例包括烷烃,例如戊烷、己烷、庚烷、辛烷;和烯烃,例如戊烯、己烯、庚烯、辛烯。另外的实例为环烷烃,例如环戊烷、环己烷、环庚烷;和环烯烃,例如环己烯和环庚烯;以及芳香族化合物,例如苯、甲苯、邻二甲苯、间二甲苯和对二甲苯。
71.任选地,可以将另外的次级冷凝器包括其进料系统连接到主冷凝器的下游,其基本上基于相同的运行模式,本质上去除冷凝热。
72.反应器中生成的热解气体还可含有气态组分,这些气态组分不仅可通过优选的两部分塔,还可通过主冷凝器和任选的其他次级冷凝器,而不会在其中冷凝/液化。结果是,这些气体不能以液态形式从塔、主冷凝器和/或其他任选的次级冷凝器中排出/移出,并且仍以气体状态离开主冷凝器或其他任选的次级冷凝器。热解气体的这些组分被称为尾气,并且优选含有烃,优选具有1至5个碳原子的烃。尾气组分的实例为甲烷、乙烷、乙烯、丙烷、丙烯、正丁烷、异丁烷、异丁烯、1-丁烯、2-丁烯、2,2-二甲基丙烷、环丙烷和环丙烯。
73.在一个优选的实施方案中,可将经由主冷凝器和一个或多个任选次级冷凝器逸出的尾气通过管道系统进给到上述气体燃烧器,用于对反应器进行加热。在一个优选实施方案中,所述尾气在离开最后的冷凝器后进行清洁步骤以去除污染物。为此,可使用本领域技术人员已知的气体净化装置,例如气体洗涤器。通过经由管道系统将尾气进给到气体燃烧器以对反应器进行加热,本方法在启动过程后在能量上变得自给自足。根据另外的实施方案,可以通过设定相应的冷却温度来运行冷凝器,使得尾气的馏分在组成上发生变化,由此可以对这些尾气的热值进行设定。通过这种尾气,根据本发明的方法可以如上所述地以能量自给的方式运行,和/或可以例如利用燃气发动机获得电能(电)和热量。
具体实施方式
74.本发明的另一主题为一种用于实施根据本发明所述方法的装置。
75.根据本发明的装置包括:(1)所述有机起始原料的转运装置或输送机;(2)反应器;(3)加热装置;(4)所述反应器和两部分或多部分塔之间的连接装置;(5)两部分或多部分塔;(6)液态烃的排出或移出系统;(7)进料系统;(8)主冷凝器。
76.图1示出了根据本发明的装置的框图。
77.转运装置或输送机(1)将起始原料转移到反应器中。在一个优选的实施方案中,所述转运装置可以为传送带,其优选地包括金属分离器。
78.此外,转运装置(1)包括这样的系统,通过该系统确保在不存在氧气的情况下可以将有机起始原料转移到反应器中。该系统可以是例如用于产生负压的抽空系统,后续可通过引入惰性气体特别是氮气来消散负压。在一个优选的实施方案中,所述系统为双锁系统,
其具有两个锁室,每个锁室均具有双挡板系统。
79.此外,所述转运装置可以优选地具有冷却装置,以便能够在冷却转运装置上将有机起始原料引入反应器中,这可以优选地防止起始原料熔化。
80.图2示出了根据本发明的转运装置到反应器的一个实施方案。
81.在反应器(2)中,加热起始原料以生成热解气体。优选通过双重壁间接地对所述反应器进行加热。此外,所述反应器优选地包括搅拌器,利用该搅拌器可将有机起始原料粉碎、混合和/或分布在反应器的尽可能大的内表面上。为了加强混合以获得更快的热量输入和压缩所使用的材料,优选将搅拌器配置为使得搅拌器的前部具有不同的倾斜度,优选地具有比后部更大的倾斜度。
82.可使用本领域技术人员已知的任何加热装置(3)对反应器进行加热。所述加热装置优选为热气发生器,尤其是一个或多个气体燃烧器与各自的燃烧室。
83.将反应器中产生的热解气体通过连接装置(4)进给到两部分或多部分塔(5)。换句话说,这意味着反应器通过连接装置连接到所述两部分或多部分塔,并且热解气体通过/经由所述连接装置从反应器进给到两部分或多部分塔。在一个优选的实施方案中,所述连接装置为管道,优选绝热管道。
84.两部分或多部分塔(5)优选为两部分塔,其中该两部分塔优选以流体密封的方式连接。流体密封连接件优选为绝热管道或法兰连接件,尤其是管道。
85.优选的两部分塔的第一部分(下部)优选为急冷塔,其可以是普通蒸馏塔或分馏塔,优选分馏塔。所述急冷塔(其优选配置为分馏塔)可含多个塔板,优选10至30个塔板。所述急冷塔优选配备有一个或多个温度测量点。
86.优选的两部分塔的第二部分(上部)优选为分馏塔。优选的两部分塔的第二部分(上部)中的分馏塔优选具有多个塔板,优选10至40个塔板,更优选20至35个塔板,尤其是约30个塔板。
87.在一个优选的实施方案中,优选的两部分塔的第一部分(下部)的直径大于优选的两部分塔的后续第二部分(上部)的直径。这种配置使得热解气体在优选的两部分塔的第一部分中的流速可以比在优选的两部分塔的后续第二部分中更低。
88.图3示出了具有冷却回路的根据本发明的两部分或多部分塔的一个实施方案。
89.优选的两部分塔的下部塔优选含有排出或移出系统(6),通过该系统可将液态烃的馏分排出/移出。这同样适用于优选的两部分塔的上部塔。优选的两部分塔的下部和上部的排出系统(6)均可优选地配置为控制阀。
90.根据本发明的装置还包括进料系统(7),所述进料系统设置在优选的两部分塔的第二部分(上部)的塔头和主冷凝器之间。优选的两部分塔中的热解气体的非液化/非冷凝组分通过所述进料系统被进给到主冷凝器。进料系统(7)可以为管道或套接口,优选套接口。
91.主冷凝器(8)为冷凝器,其中在冷却的同时可液化热解气体另外的馏分。其优选配备有控制阀,用于移出液化的馏分。
92.任选地,可将另外的次级冷凝器包括其进料系统连接到主冷凝器(8)的下游,它们基本上基于相同的运行模式。在一个优选的实施方案中,根据本发明的装置包括两个次级冷凝器,其中用于冷凝的第二次级冷凝器在比布置于主冷凝器和第二次级冷凝器之间的第
一次级冷凝器更低的温度下进行冷却。
93.根据本发明的装置还可以优选地包括管道系统,通过所述管道系统,可将加热装置的未冷凝尾气从主冷凝器或任选的次级冷凝器优选地进给到上述气体燃烧器以用于对反应器进行加热,或进给到燃气发动机以用于产生电能(电)和热量。
94.在根据本发明的装置的一个优选实施方案中,可在所述管道系统中设置气体清洁装置。气体清洁装置为本领域技术人员已知。一个实例为气体洗涤器。借助于这种气体清洁装置,可以在进料到上述气体燃烧器或燃气发动机之前,将尾气中的污染物除去。
再多了解一些
本文用于企业家、创业者技术爱好者查询,结果仅供参考。