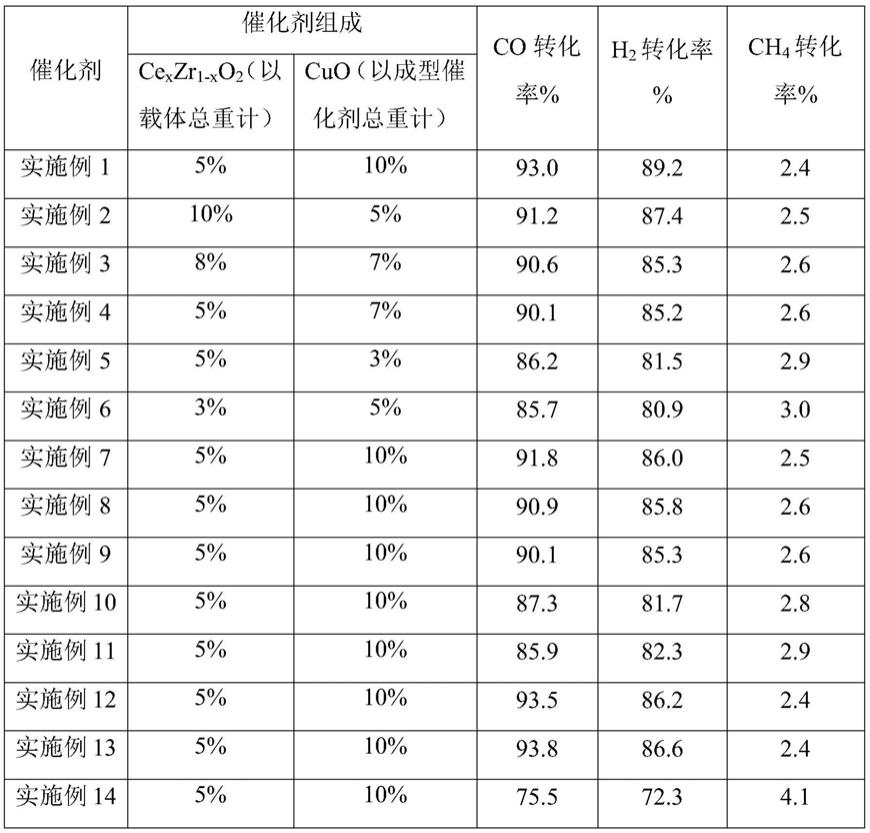
1.本发明涉及一种甲烷氧化偶联制备乙烯废气中回收甲烷的方法。
背景技术:
2.甲烷氧化偶联(ocm)制乙烯技术在石油化工领域中具有潜在的应用价值。原料物料单次通过催化剂床层后,约50wt%甲烷会转化成主产物乙烯、乙烷以及副产物氢气、一氧化碳和二氧化碳等。反应器输出的物料经去除二氧化碳和分离乙烯、乙烷后,主要的副产物是未反应的甲烷、一氧化碳和氢气。为了提高原料甲烷利用效率,专利cn 109456139 a将ocm反应产物进行急冷冷却、压缩升压、脱除杂质、气液分离工序处理,采用膜分离技术将不凝气中的的甲烷分离出来并返回到ocm反应器循环使用。专利cn 108137435 a采用吸附-解吸的方法回收利用未反应的甲烷。选择性催化氧化也可以用来净化ocm尾气,即ocm尾气在一定温度下通过催化剂床层,一氧化碳和氢气被氧化,甲烷不消耗或消耗很少。甲烷净化后,就可以和新鲜甲烷一起进料,提高甲烷利用效率。采用粉末催化剂,可去除尾气中一氧化碳和氢气。
3.具有必要的机械强度是工业多相催化剂必须具备的性能之一,因此催化剂成型是工业催化剂制备工序的重要步骤之一。迄今为止,适用于ocm尾气净化处理催化剂载体的成型方式未见报道。
技术实现要素:
4.鉴于以上现有技术的不足,本发明的目的在于提供一种具有较高机械强度的催化剂,所述催化剂能够较好地除去甲烷氧化偶联制乙烯反应尾气中的一氧化碳和氢气,从而回收甲烷。
5.本发明的第一方面提供了一种从甲烷氧化偶联制备乙烯废气中回收甲烷的方法,其包括在成型催化剂的存在下,将甲烷氧化偶联制备乙烯废气与氧源反应;其中,所述成型催化剂以负载ce
x
zr
1-x
o2的成型氧化铝为载体,x=0-1,以cuo为活性组分。
6.根据本发明的一些实施方式,x=0.1-0.7。
7.根据本发明的一些优选实施方式,x=0.1-0.5。
8.根据本发明的一些实施方式,所述方法包括在成型催化剂的存在下,将甲烷氧化偶联制备乙烯废气与氧源接触后,分离得到甲烷。
9.根据本发明的一些实施方式,所述氧源为氧气和/或空气。
10.根据本发明的一些实施方式,所述成型催化剂中,以载体总重计,ce
x
zr
1-x
o2的质量含量为2-15%,例如3%、4%、5%、6%、7%、8%、9%、10%、11%、12%、13%、14%以及它们之间的任意值。
11.根据本发明的一些实施方式,所述成型催化剂中,以载体总重计,ce
x
zr
1-x
o2的质量含量为5-15%。
12.根据本发明的一些实施方式,所述成型催化剂中,以载体总重计,ce
x
zr
1-x
o2的质量
含量为5-10%。
13.根据本发明的一些实施方式,所述成型催化剂中,以载体总重计,cuo的质量含量为2-15%,例如3%、4%、5%、6%、7%、8%、9%、10%、11%、12%、13%、14%以及它们之间的任意值。
14.根据本发明的优选实施方式,所述成型催化剂中,以催化剂总重计,cuo的质量含量为5-10%。
15.根据本发明的一些实施方式,所述催化剂的制备方法包括在成型氧化铝载体上先负载ce
x
zr
1-x
o2,再负载cuo。
16.根据本发明,所述成型氧化铝负载ce
x
zr
1-x
o2制备方法不限。根据本发明的一些实施方式,所述负载ce
x
zr
1-x
o2可以采用沉淀沉积法和/或浸渍法。
17.根据本发明的一些实施方式,所述负载ce
x
zr
1-x
o2为单次负载或多次负载。
18.根据本发明的一些实施方式,所述负载cuo采用浸渍法。
19.根据本发明的一些实施方式,所述成型催化剂的方法包括以下步骤:
20.s1:将铈盐的水溶液、锆盐的水溶液与成型氧化铝混合进行浸渍,干燥,焙烧,得到负载ce
x
zr
1-x
o2的成型氧化铝载体;
21.s2:将铜盐的水溶液与所述负载ce
x
zr
1-x
o2的成型氧化铝载体混合进行浸渍,干燥,焙烧,得到所述成型催化剂。
22.根据本发明的另一些实施方式,所述成型催化剂的方法包括以下步骤:
23.n1:将铈盐的水溶液、锆盐的水溶液与成型氧化铝混合,加入碱性溶液进行沉淀,经洗涤、干燥、焙烧后,得到负载ce
x
zr
1-x
o2的成型氧化铝载体;
24.n2:将铜盐的水溶液与所述负载ce
x
zr
1-x
o2的成型氧化铝载体混合进行浸渍,干燥,焙烧,得到所述成型催化剂。
25.根据本发明的一些实施方式,所述成型氧化铝为球形氧化铝。
26.根据本发明的一些实施方式,所述铈盐为水溶性铈盐。
27.根据本发明的一些实施方式,所述铈盐选自硝酸铈、硝酸铈铵、硫酸铈和氯化铈中的至少一种,更优选选自硝酸铈。
28.根据本发明的一些实施方式,所述锆盐为水溶性锆盐。
29.根据本发明的一些实施方式,所述锆盐选自氧氯化锆、氯化锆、硫酸锆和硝酸锆中的至少一种,更优选选自硝酸锆。
30.根据本发明的一些实施方式,所述铜盐为水溶性铜盐。
31.根据本发明的一些实施方式,所述铜盐选自硝酸铜、氯化铜和硫酸铜中的至少一种,更优选选自硝酸铜。
32.根据本发明的一些实施方式,所述碱性溶液选自氨水和/或碳酸钠溶液。
33.根据本发明的一些实施方式,步骤s1或n1中,所述干燥的温度为60-120℃。
34.根据本发明的一些实施方式,步骤s1或n1中,所述焙烧的温度为400-800℃。
35.根据本发明的一些实施方式,步骤s1或n1中,时间为2-10h。
36.根据本发明的一些实施方式,步骤s2或n2中,所述干燥的温度为60-120℃。
37.根据本发明的一些实施方式,步骤s2或n2中,所述焙烧的温度为400-800℃。
38.根据本发明的一些实施方式,步骤s2或n2中,时间为2-10h。
39.根据本发明的一些实施方式,所述甲烷氧化偶联制备乙烯废气包括甲烷、一氧化碳和氢气。
40.根据本发明的一些实施方式,甲烷、一氧化碳和氢气的体积比为(12-18):(2-5):1。
41.根据本发明的优选实施方式,甲烷、一氧化碳和氢气的体积比为(15-17):(2-4):1。
42.根据本发明的一些实施方式,所述接触的总反应空速为10-200l
·
h-1
·
g-1
。
43.根据本发明的优选实施方式,所述接触的总反应空速为13-150l
·
h-1
·
g-1
。
44.根据本发明的一些实施方式,所述接触的温度为200-700℃,例如可以是250℃、300℃、350℃、400℃、450℃、500℃、550℃、600℃、650℃以及它们之间的任意值。
45.根据本发明的优选实施方式,所述接触的温度为350-600℃。
46.本发明的第二方面提供了一种根据第一方面所述的方法在甲烷氧化偶联制乙烯反应中的应用。
47.根据本发明的铈锆氧化物ce
x
zr
1-x
o2/球形氧化铝负载cuo用于ocm尾气净化处理。
48.根据本发明,尾气单次通过催化剂床层,即可达到一氧化碳转化率》70%,氢气转化率》70%,甲烷转化率《4.5%效果,在优选的操作条件下,可达到一氧化碳转化率》90%,氢气转化率》85%,甲烷转化率《3%的效果,可将得到的甲烷循环输送至反应釜继续反应。
具体实施方式
49.为使本发明容易理解,下面将结合实施例来详细说明本发明,这些实施例仅起说明性作用,并不局限于本发明的应用范围。
50.本发明中所使用的原料或组分若无特殊说明均可以通过商业途径或常规方法制得。
51.实施例1
52.称取0.54g六水合硝酸铈,4.76g五水合硝酸锆,溶于50ml水中,加入30g球形氧化铝,旋蒸至干,60℃干燥,以5℃/min升温至450℃,保持5h,冷却至室温后得到铈锆氧化物ce
0.1
zr
0.9
o2/球形氧化铝。
53.称取1.01g三水合硝酸铜,溶于30ml水中,加入铈锆氧化物ce
0.1
zr
0.9
o2/球形氧化铝3.01g,旋蒸至干,80℃干燥,以5℃/min升温至600℃,保持5h,得到成型催化剂。
54.在石英玻璃管反应器(内径为8mm)中,装入0.21g上述催化剂,催化剂上下填充石英砂(20-40目)。通入氮气(40ml/min)和氧气(2.8ml/min),以10℃/min的速率升温至600℃并保持30min。切换成副产物反应气(其包含co 13vol%,h
2 1vol%,余量为甲烷,40ml/min)和氧气(2.8ml/min)。反应60min后,通过气相色谱法测定co转化率、ch4转化率和h2转化率,测试结果见表1。
55.实施例2
56.称取0.72g六水合硝酸铈,2.89g五水合硝酸锆,溶于21ml水中,将此溶液边搅拌边滴加入30g球形氧化铝,搅拌均匀后静置5h,80℃干燥,以5℃/min升温至600℃,保持5h,冷却至室温,再重复上述操作两次,得到铈锆氧化物ce
0.2
zr
0.8
o2/球形氧化铝。
57.称取0.48g三水合硝酸铜,溶于30ml水中,加入铈锆氧化物ce
0.2
zr
0.8
o2/球形氧化
铝2.98g,旋蒸至干,60℃干燥,以5℃/min升温至600℃,保持5h,得到成型催化剂。
58.在石英玻璃管反应器(内径为8mm)中,装入0.15g上述催化剂,催化剂上下填充石英砂(20-40目)。通入氮气(100ml/min)和氧气(7ml/min),以10℃/min的速率升温至600℃并保持30min。切换成副产物反应气(其包含co 13vol%,h
2 1vol%,余量为甲烷,100ml/min)和氧气(7ml/min)。反应60min后,通过气相色谱法测定co转化率、ch4转化率和h2转化率,测试结果见表1。
59.实施例3
60.称取0.82g六水合硝酸铈,1.90g五水合硝酸锆,溶于100ml水中,加入30g球形氧化铝,缓慢滴加氨水溶液(1mol/l)至溶液ph为10,继续搅拌30min后过滤,用蒸馏水洗涤滤饼,120℃干燥,以5℃/min升温至800℃,保持5h,冷却至室温再重复上述操作两次,得到铈锆氧化物ce
0.3
zr
0.7
o2/球形氧化铝。
61.称取0.68g三水合硝酸铜,溶于30ml水中,加入铈锆氧化物ce
0.3
zr
0.7
o2/球形氧化铝3.08g,旋蒸至干,120℃干燥,以5℃/min升温至800℃,保持5h,得到成型催化剂。
62.在石英玻璃管反应器(内径为8mm)中,装入0.10g上述催化剂,催化剂上下填充石英砂(20-40目)。通入氮气(180ml/min)和氧气(14ml/min),以10℃/min的速率升温至600℃并保持30min。切换成副产物反应气(其包含co 13vol%,h
2 3vol%,余量为甲烷,180ml/min)和氧气(14ml/min)。反应60min后,通过气相色谱法测定co转化率、ch4转化率和h2转化率,测试结果见表1。
63.实施例4
64.称取0.58g六水合硝酸铈,0.58g五水合硝酸锆,溶于100ml水中,加入30g球形氧化铝,缓慢滴加碳酸钠溶液(1mol/l)至溶液ph为10,继续搅拌30min后过滤,用蒸馏水洗涤滤饼,100℃干燥,以5℃/min升温至600℃,保持5h,冷却至室温再重复上述操作三次,得到铈锆氧化物ce
0.5
zr
0.5
o2/球形氧化铝。
65.称取0.68g三水合硝酸铜,溶于30ml水中,加入铈锆氧化物ce
0.5
zr
0.5
o2/球形氧化铝3.05g,旋蒸至干,80℃干燥,以5℃/min升温至480℃,保持5h,得到成型催化剂。
66.在石英玻璃管反应器(内径为8mm)中,装入0.09g上述催化剂,催化剂上下填充石英砂(20-40目)。通入氮气(180ml/min)和氧气(18ml/min),以10℃/min的速率升温至600℃并保持30min。切换成副产物反应气(其包含co 15vol%,h
2 5vol%,余量为甲烷,180ml/min)和氧气(18ml/min)。反应60min后,通过气相色谱法测定co转化率、ch4转化率和h2转化率,测试结果见表1。
67.实施例5
68.称取0.54g六水合硝酸铈,4.76g五水合硝酸锆,溶于50ml水中,加入30g球形氧化铝,旋蒸至干,80℃干燥,以5℃/min升温至600℃,保持5h,冷却至室温后得到铈锆氧化物ce
0.1
zr
0.9
o2/球形氧化铝。
69.称取0.28g三水合硝酸铜,溶于30ml水中,加入铈锆氧化物ce
0.1
zr
0.9
o2/球形氧化铝3.03g,旋蒸至干,80℃干燥,以5℃/min升温至600℃,保持5h,得到成型催化剂。
70.在石英玻璃管反应器(内径为8mm)中,装入0.21g上述催化剂,催化剂上下填充石英砂(20-40目)。通入氮气(40ml/min)和氧气(4ml/min),以10℃/min的速率升温至600℃并保持30min。切换成副产物反应气(其包含co 15vol%,h
2 5vol%,余量为甲烷,40ml/min)
和氧气(4ml/min)。反应60min后,通过气相色谱法测定co转化率、ch4转化率和h2转化率,测试结果见表1。
71.实施例6
72.称取0.32g六水合硝酸铈,2.80g五水合硝酸锆,溶于50ml水中,加入30g球形氧化铝,旋蒸至干,80℃干燥,以5℃/min升温至600℃,保持5h,冷却至室温后得到铈锆氧化物ce
0.1
zr
0.9
o2/球形氧化铝。
73.称取0.48g三水合硝酸铜,溶于30ml水中,加入铈锆氧化物ce
0.1
zr
0.9
o2/球形氧化铝3.02g,旋蒸至干,80℃干燥,以5℃/min升温至1000℃,保持5h,得到成型催化剂。
74.在石英玻璃管反应器(内径为8mm)中,装入0.21g上述催化剂,催化剂上下填充石英砂(20-40目)。通入氮气(40ml/min)和氧气(4ml/min),以10℃/min的速率升温至600℃并保持30min。切换成副产物反应气(其包含co 15vol%,h
2 5vol%,余量为甲烷,40ml/min)和氧气(4ml/min)。反应60min后,通过气相色谱法测定co转化率、ch4转化率和h2转化率,测试结果见表1。
75.实施例7
76.称取1.49g六水合硝酸铈,3.45g五水合硝酸锆,溶于50ml水中,加入30g球形氧化铝,旋蒸至干,80℃干燥,以5℃/min升温至600℃,保持5h,冷却至室温后得到铈锆氧化物ce
0.3
zr
0.7
o2/球形氧化铝。
77.称取1.01g三水合硝酸铜,溶于30ml水中,加入铈锆氧化物ce
0.3
zr
0.7
o2/球形氧化铝3.01g,旋蒸至干,80℃干燥,以5℃/min升温至600℃,保持5h,得到成型催化剂。
78.在石英玻璃管反应器(内径为8mm)中,装入0.21g上述催化剂,催化剂上下填充石英砂(20-40目)。通入氮气(40ml/min)和氧气(4ml/min),以10℃/min的速率升温至600℃并保持30min。切换成副产物反应气(其包含co 15vol%,h
2 5vol%,余量为甲烷,40ml/min)和氧气(4ml/min)。反应60min后,通过气相色谱法测定co转化率、ch4转化率和h2转化率,测试结果见表1。
79.实施例8
80.称取2.32g六水合硝酸铈,2.30g五水合硝酸锆,溶于50ml水中,加入30g球形氧化铝,旋蒸至干,80℃干燥,以5℃/min升温至600℃,保持5h,冷却至室温后得到铈锆氧化物ce
0.5
zr
0.5
o2/球形氧化铝。
81.称取1.01g三水合硝酸铜,溶于30ml水中,加入铈锆氧化物ce
0.5
zr
0.5
o2/球形氧化铝3.01g,旋蒸至干,80℃干燥,以5℃/min升温至600℃,保持5h,得到成型催化剂。
82.在石英玻璃管反应器(内径为8mm)中,装入0.21g上述催化剂,催化剂上下填充石英砂(20-40目)。通入氮气(40ml/min)和氧气(4ml/min),以10℃/min的速率升温至600℃并保持30min。切换成副产物反应气(其包含co 15vol%,h
2 5vol%,余量为甲烷,40ml/min)和氧气(4ml/min)。反应60min后,通过气相色谱法测定co转化率、ch4转化率和h2转化率,测试结果见表1。
83.实施例9
84.称取3.05g六水合硝酸铈,1.29g五水合硝酸锆,溶于50ml水中,加入30g球形氧化铝,旋蒸至干,80℃干燥,以5℃/min升温至600℃,保持5h,冷却至室温后得到铈锆氧化物ce
0.7
zr
0.3
o2/球形氧化铝。
85.称取1.01g三水合硝酸铜,溶于30ml水中,加入铈锆氧化物ce
0.7
zr
0.3
o2/球形氧化铝3.01g,旋蒸至干,80℃干燥,以5℃/min升温至600℃,保持5h,得到成型催化剂。
86.在石英玻璃管反应器(内径为8mm)中,装入0.21g上述催化剂,催化剂上下填充石英砂(20-40目)。通入氮气(40ml/min)和氧气(4ml/min),以10℃/min的速率升温至600℃并保持30min。切换成副产物反应气(其包含co 15vol%,h
2 5vol%,余量为甲烷,40ml/min)和氧气(4ml/min)。反应60min后,通过气相色谱法测定co转化率、ch4转化率和h2转化率,测试结果见表1。
87.实施例10
88.称取3.98g六水合硝酸铈,溶于50ml水中,加入30g球形氧化铝,旋蒸至干,80℃干燥,以5℃/min升温至600℃,保持5h,冷却至室温后得到铈锆氧化物ceo2/球形氧化铝。
89.称取1.01g三水合硝酸铜,溶于30ml水中,加入铈锆氧化物ceo2/球形氧化铝3.01g,旋蒸至干,80℃干燥,以5℃/min升温至600℃,保持5h,得到成型催化剂。
90.在石英玻璃管反应器(内径为8mm)中,装入0.21g上述催化剂,催化剂上下填充石英砂(20-40目)。通入氮气(40ml/min)和氧气(4ml/min),以10℃/min的速率升温至600℃并保持30min。切换成副产物反应气(其包含co 15vol%,h
2 5vol%,余量为甲烷,40ml/min)和氧气(4ml/min)。反应60min后,通过气相色谱法测定co转化率、ch4转化率和h2转化率,测试结果见表1。
91.实施例11
92.称取5.51g五水合硝酸锆,溶于50ml水中,加入30g球形氧化铝,旋蒸至干,80℃干燥,以5℃/min升温至600℃,保持5h,冷却至室温后得到铈锆氧化物zro2/球形氧化铝。
93.称取1.01g三水合硝酸铜,溶于30ml水中,加入铈锆氧化物zro2/球形氧化铝3.01g,旋蒸至干,80℃干燥,以5℃/min升温至600℃,保持5h,得到成型催化剂。
94.在石英玻璃管反应器(内径为8mm)中,装入0.21g上述催化剂,催化剂上下填充石英砂(20-40目)。通入氮气(40ml/min)和氧气(4ml/min),以10℃/min的速率升温至600℃并保持30min。切换成副产物反应气(其包含co 15vol%,h
2 5vol%,余量为甲烷,40ml/min)和氧气(4ml/min)。反应60min后,通过气相色谱法测定co转化率、ch4转化率和h2转化率,测试结果见表1。
95.实施例12
96.称取0.54g六水合硝酸铈,4.76g五水合硝酸锆,溶于50ml水中,加入30g球形氧化铝,旋蒸至干,80℃干燥,以5℃/min升温至600℃,保持5h,冷却至室温后得到铈锆氧化物ce
0.1
zr
0.9
o2/球形氧化铝。
97.称取1.01g三水合硝酸铜,溶于30ml水中,加入铈锆氧化物ce
0.1
zr
0.9
o2/球形氧化铝3.01g,旋蒸至干,80℃干燥,以5℃/min升温至600℃,保持5h,得到成型催化剂。
98.在石英玻璃管反应器(内径为8mm)中,装入0.21g上述催化剂,催化剂上下填充石英砂(20-40目)。通入氮气(40ml/min)和氧气(4ml/min),以10℃/min的速率升温至400℃并保持30min。切换成副产物反应气(其包含co 15vol%,h
2 5vol%,余量为甲烷,40ml/min)和氧气(4ml/min)。反应60min后,通过气相色谱法测定co转化率、ch4转化率和h2转化率,测试结果见表1。
99.实施例13
100.称取0.54g六水合硝酸铈,4.76g五水合硝酸锆,溶于50ml水中,加入30g球形氧化铝,旋蒸至干,80℃干燥,以5℃/min升温至600℃,保持5h,冷却至室温后得到铈锆氧化物ce
0.1
zr
0.9
o2/球形氧化铝。
101.称取1.01g三水合硝酸铜,溶于30ml水中,加入铈锆氧化物ce
0.1
zr
0.9
o2/球形氧化铝3.01g,旋蒸至干,80℃干燥,以5℃/min升温至600℃,保持5h,得到成型催化剂。
102.在石英玻璃管反应器(内径为8mm)中,装入0.21g上述催化剂,催化剂上下填充石英砂(20-40目)。通入氮气(40ml/min)和氧气(4ml/min),以10℃/min的速率升温至500℃并保持30min。切换成副产物反应气(其包含co 15vol%,h
2 5vol%,余量为甲烷,40ml/min)和氧气(4ml/min)。反应60min后,通过气相色谱法测定co转化率、ch4转化率和h2转化率,测试结果见表1。
103.实施例14
104.称取0.54g六水合硝酸铈,4.76g五水合硝酸锆,溶于50ml水中,加入30g球形氧化铝,旋蒸至干,80℃干燥,以5℃/min升温至600℃,保持5h,冷却至室温后得到铈锆氧化物ce
0.1
zr
0.9
o2/球形氧化铝。
105.称取1.01g三水合硝酸铜,溶于30ml水中,加入铈锆氧化物ce
0.1
zr
0.9
o2/球形氧化铝3.01g,旋蒸至干,80℃干燥,以5℃/min升温至600℃,保持5h,得到成型催化剂。
106.在石英玻璃管反应器(内径为8mm)中,装入0.21g上述催化剂,催化剂上下填充石英砂(20-40目)。通入氮气(40ml/min)和氧气(4ml/min),以10℃/min的速率升温至800℃并保持30min。切换成副产物反应气(其包含co 15vol%,h
2 5vol%,余量为甲烷,40ml/min)和氧气(4ml/min)。反应60min后,通过气相色谱法测定co转化率、ch4转化率和h2转化率,测试结果见表1。
107.表1
[0108][0109]
应当注意的是,以上所述的实施例仅用于解释本发明,并不构成对本发明的任何限制。通过参照典型实施例对本发明进行了描述,但应当理解为其中所用的词语为描述性和解释性词汇,而不是限定性词汇。可以按规定在本发明权利要求的范围内对本发明作出修改,以及在不背离本发明的范围和精神内对本发明进行修订。尽管其中描述的本发明涉及特定的方法、材料和实施例,但是并不意味着本发明限于其中公开的特定例,相反,本发明可扩展至其他所有具有相同功能的方法和应用。
再多了解一些
本文用于企业家、创业者技术爱好者查询,结果仅供参考。