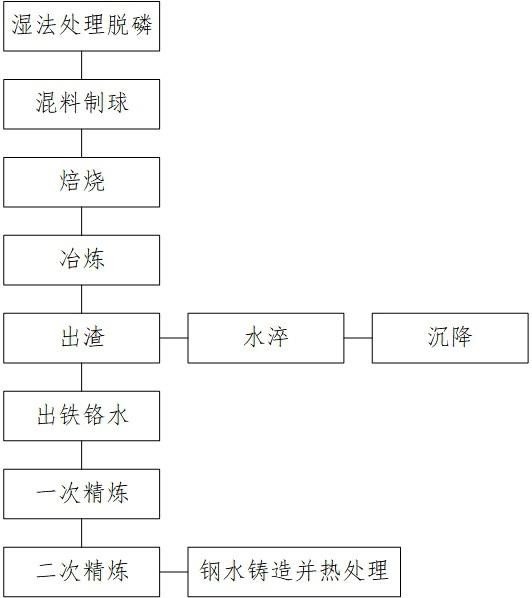
1.本发明涉及固渣处理相关技术领域,尤其涉及一种铁铬固体尾渣中提取含铬合金制造不锈钢产品的方法。
背景技术:
2.铬渣,是指生产加工金属铬和铬盐、冶金、电镀、制革等工业活动中,产生的工业废渣。铬渣中含有的铬酸钙、六价铬等有毒物质具有强氧化性。
3.目前,我国固废处理行业还处于发展初期,固废处理投资占环保行业整体投入比重不足15%,特别是工业固废。而在发达国家,固废处理是环保领域投资和产值最大的子行业。而结合我国固废行业目前发展状况来看,无论是存量需求还是增量需求,市场非常之大。
4.而目前我国大力支持废石尾矿综合利用,在符合安全、生态环保要求的前提下,鼓励和支持综合利用废石、矿渣和尾矿等砂石资源,实现“变废为宝”。鼓励利用固废资源制造再生资源。鼓励利用工业尾矿﹑废渣﹑残渣等固废里含有的贵金属,用新的技术提炼再生资源,应用国民生计,减少资源浪费,保护环境。
技术实现要素:
5.本发明提供一种铁铬固体尾渣中提取含铬合金制造不锈钢产品的方法,以解决上述现有技术的不足,采用直流电弧提供高温直流热源,使用还原剂、化渣助熔材料等(焦炭等)对固态固渣进行快速熔化加热提温,利用温度高(1800-2200℃)的特点,在熔池内形成高温的还原区,使固渣里的有用金属(铬,铁)经过高温熔融,形成二元合金,熔炼后渣料又以液态排渣方式排放出来,再经水淬固化为玻璃状,水淬前渣温1800℃左右,在沉渣池内沉降,这种铬渣可用作水泥等建筑材料生产的原材料。水淬水循环利用,不排水。尾灰经电除尘器除尘,消除二次污染,保护环境,同时通过本发明的制备方法提高了铁铬的收得率且显著地降低了铁铬中的磷与硫含量,并且提高了固渣的处理效率,具有较强的实用性,与单纯提纯铬铁不同的是,含铬铁水不需要浇铸成型,进入钢包做为下一步制造不锈钢产品的材料直接使用。
6.为了实现本发明的目的,拟采用以下技术:一种铁铬固体尾渣中提取含铬合金制造不锈钢产品的方法,包括如下步骤:步骤1,湿法处理脱磷,通过除磷剂和水洗的方式对固渣中的磷进行去除;步骤2,混料制球,通过制球机将步骤1中获得的除磷固渣压制呈球状结构,并对制得的球状物进行烘干;步骤3,焙烧,通过带式烧结炉将步骤2中制得的固渣球进行焙烧;步骤4,冶炼,将步骤3中所得固渣球置于直流电弧炉内,并加入按比例混合配比焦炭、石灰、萤石以及二氧化硅制成的还原剂,进行铁铬的还原和除磷;步骤5,出渣,当步骤4中冶炼时间为140min-160min时,进行出渣操作;
步骤6,出铁铬水,当步骤4中冶炼时间为175min-185min时,进行铁铬水的排出;步骤7,一次精炼,通过氩氧精炼脱碳炉对步骤6所得的铁铬水进行精炼,精炼时需要通入o2与ar或n2的混合气体,同时加入脱硫剂;步骤8,二次精炼,通过钢包精炼炉对铁铬水进行再次精炼,同时根据成品不锈钢产品的成分要求(300系和400系不锈钢),选择性的加入镍板、钼铁、钛铁等合金材料,精炼时通入氩气并对钢水进行搅拌;步骤9,将步骤8所得的钢水进行不锈钢产品的铸造并进行热处理。
7.进一步地,除磷剂七水硫酸亚铁,且除磷后的固渣中五氧化二磷的占比为0.050%。
8.进一步地,步骤2中烘干的温度为100℃,制得固渣球的直径为30mm。
9.进一步地,步骤3中焙烧温度为焙烧温度为850℃-950℃,焙烧时间为120min。
10.进一步地,步骤4中焦炭占固渣的质量分数为10%-12%,石灰占固渣的质量分数为1.5%-3%,萤石占固渣的质量分数为1.5%-3%,二氧化硅占固渣的质量分数为1%-4%。
11.进一步地,步骤4中直流电弧炉内高温还原区的温度为1800-2200℃。
12.进一步地,步骤4中每炉的冶炼时间为175min-185min。
13.进一步地,步骤5中出渣时,出渣温度为1850℃-1950℃。
14.进一步地,步骤6中出铁铬水的温度为1750℃-1850℃。
15.进一步地,脱硫剂为氧化铁。
16.上述技术方案的优点在于:本发明采用直流电弧提供高温直流热源,使用还原剂、化渣助熔材料等(焦炭等)对固态固渣进行快速熔化加热提温,利用温度高(1800-2200℃)的特点,在熔池内形成高温的还原区,使固渣里的有用金属(铬,铁)经过高温熔融,形成二元合金,熔炼后渣料又以液态排渣方式排放出来,再经水淬固化为玻璃状,水淬前渣温1800℃左右,在沉渣池内沉降,这种铬渣可用作水泥等建筑材料生产的原材料。水淬水循环利用,不排水。尾灰经电除尘器除尘,消除二次污染,保护环境,同时通过本发明的制备方法提高了铁铬的收得率且显著地降低了铁铬中的磷与硫含量,并且提高了固渣的处理效率,同时由于采用了专用的制球装置,从而提高了制球的效率,以及制球后球状固渣的密实程度,具有较强的实用性。
附图说明
17.图1示出了其中一种实施例的制备流程图。
18.图2示出了其中一种实施例的立体结构图一。
19.图3示出了其中一种实施例的立体结构图二。
20.图4示出了其中一种实施例的侧视图。
21.图5示出了d-d处剖面图。
22.图6示出了a处放大图。
23.图7示出了b处放大图。
24.图8示出了c处放大图。
具体实施方式
25.为使本发明实施例的目的、技术方案和优点更加清楚,下面将结合本发明实施例
中的附图,对本发明实施例中的技术方案进行清楚、完整地描述,显然,所描述的实施例是本发明一部分实施例,而不是全部的实施例。通常在此处附图中描述和示出的本发明实施例的组件可以以各种不同的配置来布置和设计。
26.因此,以下对在附图中提供的本发明的实施例的详细描述并非旨在限制要求保护的本发明的范围,而是仅仅表示本发明的选定实施例。基于本发明中的实施例,本领域普通技术人员在没有作出创造性劳动前提下所获得的所有其他实施例,都属于本发明保护的范围。
27.应注意到:相似的标号和字母在下面的附图中表示类似项,因此,一旦某一项在一个附图中被定义,则在随后的附图中不需要对其进行进一步定义和解释。
28.在本发明的描述中,需要说明的是,术语“中心”、“上”、“下”、“左”、“右”、“竖直”、“水平”、“内”、“外”等指示的方位或位置关系为基于附图所示的方位或位置关系,或者是该发明产品使用时惯常摆放的方位或位置关系,仅是为了便于描述本发明和简化描述,而不是指示或暗示所指的装置或元件必须具有特定的方位、以特定的方位构造和操作,因此不能理解为对本发明的限制。
29.术语“第一”、“第二”等仅用于区分描述,而不能理解为指示或暗示相对重要性。
30.术语“平行”、“垂直”等并不表示要求部件绝对平行或垂直,而是可以稍微倾斜。如“平行”仅仅是指其方向相对“垂直”而言更加平行,并不是表示该结构一定要完全平行,而是可以稍微倾斜。
31.此外,“大致”、“基本”等用语旨在说明相关内容并不是要求绝对的精确,而是可以有一定的偏差。例如:“大致等于”并不仅仅表示绝对的等于,由于实际生产、操作过程中,难以做到绝对的“相等”,一般都存在一定的偏差。因此,除了绝对相等之外,“大致等于”还包括上述的存在一定偏差的情况。以此为例,其他情况下,除非有特别说明,“大致”、“基本”等用语均为与上述类似的含义。
32.在本发明的描述中,还需要说明的是,除非另有明确的规定和限定,术语“设置”、“安装”、“相连”、“连接”应做广义理解,例如,可以是固定连接,也可以是可拆卸连接,或一体地连接;可以是直接相连,也可以通过中间媒介间接相连,可以是两个元件内部的连通。对于本领域的普通技术人员而言,可以具体情况理解上述术语在本发明中的具体含义。
33.实施例1如图1,一种铁铬固体尾渣中提取含铬合金制造不锈钢产品的方法,包括如下步骤:步骤1,湿法处理脱磷,通过除磷剂和水洗的方式对固渣中的磷进行去除,除磷剂七水硫酸亚铁,且除磷后的固渣中五氧化二磷的占比为0.050%,通过这种除磷可降低所得合金中的磷含量,相应地也避免磷含量的升高对二元合金的塑性、韧性以及可焊性造成影响,提高了合金的强度等,并且采用七水硫酸亚铁作为除磷剂可避免新元素的引入,同时增加铁的含量。
34.步骤2,混料制球,通过制球机将步骤1中获得的除磷固渣压制呈球状结构,并对制得的球状物进行烘干,烘干的温度为100℃,制得固渣球的直径为30mm。将固渣加工成为球状结构在进行冶炼时能够充分的和还原剂接触,同时避免在冶炼时发生爆炉的现象,选择100℃的烘干温度可提高烘干效果,降低了固渣球状物内的水分,同时也起到了定型的作
用,避免在后期操作中,固渣球碎裂。而将固渣球加工成为30mm方便进行后期的操作转移,同时该直径为最大的可接受直径,在实际生产中主要依据制球机的加工尺寸为确定尺寸,若当该直径大于30mm时,在实际生产中不容易成形,同时在烘干等操作中容易碎裂。
35.步骤3,焙烧,通过带式烧结炉将步骤2中制得的固渣球进行焙烧,焙烧温度为850℃-950℃,焙烧时间为120min。通过焙烧可进行固渣球的再次定型,同时蒸发掉固渣球中的大部分水,增加固渣球团的透气性,避免冶炼时固渣板结,并且通过焙烧可除掉矿石中对冶金过程有害的水分及其它易挥发组分(如砷、锑等),而采用850℃-950℃的焙烧温度,主要考虑到水分的蒸发量以及有害组分的蒸发量,降低固渣球毒性,而在实际生产中,当焙烧时间小于120min时,固渣球团内的有害组分蒸发不彻底,同时成形稳定性较差。其中当温度过高时,固渣焙烧后呈现熔融状态,容易板结,球团中间透气性差,而且不利于后续物料输送。若温度过低,固渣内的结晶水不易去除干净。
36.步骤4,冶炼,将步骤3中所得固渣球置于直流电弧炉内,并加入按比例混合配比焦炭、石灰、萤石以及二氧化硅制成的还原剂,进行铁铬的还原。其中,焦炭占固渣的质量分数为10%-12%,石灰占固渣的质量分数为1.5%-3%,萤石占固渣的质量分数为1.5%-3%,二氧化硅占固渣的质量分数为1%-4%。直流电弧炉内高温还原区的温度为1800-2200℃,每炉的冶炼时间为175min-185min。其中,焦炭能够补充热量以及起到还铁以及铬等的作用,石灰(氧化钙)起到稀释固渣和调节炉内气氛的作用,萤石调节炉内物料的流动性和酸碱度,二氧化硅促进渣铁分离。通过焦炭、石灰、萤石等辅料的加入,为固渣的冶炼过程提供了一个良好的还原性环境,所造渣的碱度和流动性合适,使得钢渣固相和液相之间的界面反应朝着有利的方向进行,反应完全后钢渣易分离。
37.步骤5,出渣,当步骤4中冶炼时间为140min-160min时,进行出渣操作,出渣温度为1850℃-1950℃,出渣后对渣物进行水淬,并得到玻璃状物质,而后通过沉降得到无害化的废渣,而该废渣可用于生产制备建筑材料,而其中在1850℃-1950℃进行出渣,主要考虑到溶渣的熔点较高,此温度在渣的熔点以上,保证了渣的流动性,以便从炉内放出和保证渣、铁分离。
38.步骤6,出铁铬水,当步骤4中冶炼时间为175min-185min时,进行铁铬水的排出,出铁铬水的温度为1750℃-1850℃。此温度下铁水有合适的过热度,能够保证顺利出铁水,同时可减少铁水的吸气量。
39.步骤7,一次精炼,通过氩氧精炼脱碳炉对步骤6所得的铁铬水进行精炼,精炼时需要通入o2与ar或n2的混合气体,同时加入脱硫剂;步骤8,二次精炼,通过钢包精炼炉对铁铬水进行再次精炼,同时选择性的加入镍板、钼铁、钛铁等合金材料,精炼时通入氩气并对钢水进行搅拌,由于氩气搅拌加速了渣一钢之间的化学反应,用电弧加热进行温度补偿,可以保证较长时间的精炼时间,从而可使钢中的氧、硫含量降低。
40.步骤9,将步骤8所得的钢水进行不锈钢产品的铸造并进行热处理。
41.实施例2在本实施例中固渣的重量为2660千克,而其中加入的焦炭为300千克、加入的石灰70千克、加入的萤石45千克以及加入的二氧化硅60千克重量的还原剂进行固渣的处理,其中焦炭占固渣重量的质量分数为11.28%、石灰占固渣重量的质量分数为2.63%、萤石占固渣
重量的质量分数为1.69%以及二氧化硅占固渣重量的质量分数为2.26%。且直流电弧炉内的装料量大约为21000千克,经过上述实施例1中的冶炼后产生1000千克的铬铁水,2130千克的熔炼废渣。
42.固渣中含有cr2o3,fe2o3,al2o3,sio2,mgo,cao,alo3,p,s以及其他杂质。上述各个成分的质量百分含量如下表所示:cr2o3fe2o3al2o3sio2mgocaoalo3ps其他10.3749.515.455.8212.792.940.420.380.32.03 固渣通过实施例1中的制备方法获得的fe、cr、si02、cao、mgo、al2o3、p、s以及as的理论质量百分含量如下表所示:fecrsi02caomgoal2o3psas31-326.52.52.09.014-160.03≤0.35≤0.001 而实际测得铁水中的fe、cr、c、si、p以及s的质量百分含量如下表所示:fecrcsips80.014.73.01.80.0340.05关于铁水含s:焦炭带入:300
×
0.5%=1.5kg固渣带入:2660
×
0.3%=7.98kg合计9.48kg按10 kg计算按冶炼脱s率95%计,进入铁水的s=10
×
0.05=0.5kg0.5/1000=0.05%通过上述数据以及产生铁铬水的量来说,铁铬水的产量为37.6%,而铬的回收率为85%,fe的回收率97%。通过上述数据可知该制备方法可显著地提高铁铬水的回收率,同时相应地分别提高了铬和铁的回收率。
43.而新产生固渣实测成份含量(质量百分含量%)如下表所示:feosio2caoal2o3mgomnocr2o3sr2r40.66.848.3849.4929.223.0280.440.111.2250.667从表中可以看出,熔渣中的feo明显减少,同时有害元素也进一步的得到了降低,从而进一步地降低了对环境造成的污染,同时该熔渣可直接进行混凝土以及砖块的加工制备。
44.实施例3如图2-图7所示,该实施例为实施例1中步骤2的提供了一种制球机,该制球机包括挤出组件1,挤出组件1的出料端设有制球组件2,挤出组件1包括上料机构,上料机构上端设有挤出机构,制球组件2包括切断机构,切断机构的出料端设有制球机构;上料机构用于固渣的上料操作,挤出机构用于固渣挤出,并将固渣挤出呈直径大于30mm的柱状结构,切断机构将柱状结构的固渣分切呈若干段,制球机构用于固渣球团的压制成形。
45.该制球机中的上料机构方便进行除磷带有一定水分固渣的上料操作,从而提高了制球时的自动化程度,并且也能避免在制球时对操作人员造成人身危害,并且上料时能够提供一定的推力,从而能够确保固渣的柱状挤出。挤出机构能够自动地将固渣挤压呈柱状结构,从而能便于进行固渣的成球操作,同时通过这种挤压方式确保固渣球团的密实程度,
提高单个固渣球的实际质量,切断机构能够自动地将柱状固渣分切为一定长度,从而方便实施压制成形操作,制球机构作用于柱状固渣,从而完成柱状固渣的分切以及压制呈球形结构。并且这种压制成形方式效率较高,同时成球率较高。
46.在具体的操作中,将固渣放置在上料机构的下端,而后在上料机构的带动下使得固渣向挤出机构内转移,且当挤出机构内储放一定量的固渣时,挤出机构将固渣挤出呈柱状结构,且当固渣挤出至一定长度后,通过切断机构将固渣柱切断,同时在挤出的过程中,柱状固渣将向前移动,并穿于制球机构内,且当柱状固渣在制球机构中达到一定长度后,切断机构将柱状固渣切断,而后通过制球机构进行成球压制,且在压制的过程中,制球机构将柱状固渣先分切为若干段,最后再完成球状压制。
47.挤出机构包括多个凹形支架100,凹形支架100的内部均设有若干个内连横板101,凹形支架100的上端均安装有一对固定环板103,固定环板103内固定有挤出罐104,挤出罐104的一端设有漏斗状罐体105,漏斗状罐体105的一端连通有成形管106,成形管106的内径大于等于30mm,挤出罐104的另一端通过螺杆固定有端盖116,端盖116上安装有多根安装杆117,安装杆117的另一端设有内连支板118,内连支板118的内侧端设有转动座119,转动座119内设有转动丝套120,转动丝套120的外侧端套设有从动齿轮121,从动齿轮121啮合有驱动齿轮122,驱动齿轮122内侧端设有驱动座,驱动座安装于转动座119上,驱动齿轮122上连接有挤压电机123,挤压电机123安装于驱动座上,转动丝套120内设有挤压丝杆124,挤压丝杆124穿于端盖116,挤压丝杆124的内侧端设有挤压盘125,挤压盘125向外延伸地设有四根导向杆127,导向杆127均穿于端盖116。
48.其中,漏斗状罐体105在进行挤出时,能够使得固渣逐渐地向成形管106聚集,并在聚集的过程中使得柱状结构的固渣密实程度提高,从而方便后期的压制成形操作,提高了挤出的质量。
49.其中,在挤出的过程中,通过挤压电机123带动驱动齿轮122进行转动,驱动齿轮122在转动的过程中将带动从动齿轮121进行转动,从动齿轮121在转动的过程中将带动转动丝套120的转动,而转动丝套。120在转动的过程中将带动挤压丝杆124在导向杆127的导向下进行运动,而挤压丝杆124的运动将通过挤压盘125作用于挤出罐104内的固渣向前移动,并先逐步地向漏斗状罐体105聚集,当挤压丝杆124逐步地伸长时挤压力逐步增大,最终将位于漏斗状罐体105处的固渣从成形管106的端部挤出,这种挤出方式由于采用了挤压丝杆124挤出的方式,因此提高了挤出的稳定性,同时也确保了挤出时的推动力,其中为了方便实施,可在挤压电机123的输出轴上连接减速器。
50.上料机构包括连通于挤出罐104的下延筒107,下延筒107的内部上端安装有多个呈间隔设置的内连板108,内连板108的内侧端安装有上料轴承座,上料轴承座上设有转动杆109,转动杆109上设有螺旋输送片110,下延筒107的下端设有下环111,下环111向下延伸地设有多根支撑杆112,支撑杆112的下端安装有进料斗114,进料斗114的下端设有多根支撑腿115,转动杆109的下端穿于进料斗114,转动杆109的下端连接有转动电机113,转动电机113安装于进料斗114的下端,螺旋输送片110的下端位于进料斗114内。
51.其中,进料斗114的设置方便进行固渣上料时的放置,进而方便进行上料操作。
52.其中,由于采用了螺旋输送片110输送的方式,从而提高了输送时的推送力,从而在挤出的过程中避免出现固渣倒流的现象,同时在实施挤出时也方便进行上料操作,从而
提高了可操作性。
53.切断机构包括安装于成形管106上的第一固定环200,第一固定环200向上延伸地设有上延连板201,上延连板201的上端安装有切断轴承座202,切断轴承座202上安装有切断电机204,切断电机204的输出轴偏心地设有转动盘205,转动盘205的外侧套设有工形座206,工形座206的上下两端均套设有横向导板207,横向导板207的两端分别安装有一个侧导套208,侧导套208的外侧分别穿有一个竖向凸板209,竖向凸板209的下端均设有连接平板210,连接平板210的另一端设有第二固定环212,第二固定环212安装于成形管106上,位于下端的横向导板207的下壁安装有切断刀203。
54.该机构取代了传统的油缸切断方式,从而提高了切断的效率,同时相关部件出现故障后容易更换,同时方便控制,一般控制时采用控制切断电机204的转速达到控制切断的速度,同时这种切断方式相对于油缸切断方式耗能较低。
55.该机构在进行柱状固渣的切断时,通过切断电机204带动转动盘205进行偏心的转动,而转动盘205在进行偏心转动时将带动工形座206沿着横向导板207的长度方向进行往复的摆动,且当工形座206在往复摆动的过程中,还能使得侧导套208沿着竖向凸板209的竖向进行往复升降运动,而当侧导套208在进行往复升降运动时,将带动切断刀203进行往复的升降运动,而当切断刀203向下运动时将完成对柱状固渣的切断操作,并通过这种方式确保了切断的效率。
56.制球机构包括两对凹形支撑架213,每个凹形支撑架213的内壁上端均安装有两对呈上下分布的压制轴承座214,每对压制轴承座214之间均设有多根导杆215,位于上端的每个压制轴承座214均安装有压制电机216,压制电机216的输出轴均连接有压制丝杆217,压制丝杆217上下两端的螺纹旋向相反,每根压制丝杆217的上下两端均设有压制座218,位于同一高度处的压制座218之间均安装有连接固定板219,位于同一高度处的每对连接固定板219上均安装有凸台220,凸台220的内壁均成形有成形板221,成形板221的内壁成形有多个半球形槽222,位于下端的相邻两个半球形槽222之间均成形有矩形孔223,位于上端的相邻两个半球形槽222之间均设有分切刀224,位于下端的半球形槽222与位于上端的半球形槽222一一对应,且位于下端的半球形槽222正对于位于上端的半球形槽222,分切刀224与矩形孔223一一对应,且分切刀224穿于与其对应的矩形孔223内,位于下端的成形板221内壁设有一对相互平行的限位侧板,限位侧板位于半球形槽222的两侧,位于上端的成形板221内壁均成形有一对相互平行的限位侧槽,当固渣压制成形时,限位侧板穿于限位侧槽内。
57.其中,限位侧板和限位侧槽的设置对穿于成形板221之间的柱状固渣起着导向限位的作用,从而使得柱状固渣位于半球形槽222处,进而提高了固渣的成形率,限位侧槽的设置在进行压制成形时对限位侧板起着避让的作用,以免对压制成形造成不利的影响。
58.其中,分切刀224和矩形孔223的设置方便将柱状固渣切断,进而方便球状结构的成形,提高了成形的效率。矩形孔223在压制成形时方便分切刀224的切断操作。
59.其中,当在进行成球压制时,同时启动各个压制电机216,并在压制电机216的带动下各个压制丝杆217进行转动,而压制丝杆217的转动将带动每对压制座218相互靠近,而压制座218的相互靠近将带动成形板221相互靠近,最终通过成形板221完成了对固渣的球状压制操作,这种压制成形方式效率较高,同时压制成形时的作用力较大,从而确保压制成形的密实程度,显著地提高了压制成形的质量,同时方便进行控制。
60.以上所述仅为本发明的优选实施例,并不用于限制本发明,显然,本领域的技术人员可以对本发明进行各种改动和变型而不脱离本发明的精神和范围。这样,倘若本发明的这些修改和变型属于本发明权利要求及其等同技术的范围之内,则本发明也意图包含这些改动和变型在内。
再多了解一些
本文用于企业家、创业者技术爱好者查询,结果仅供参考。