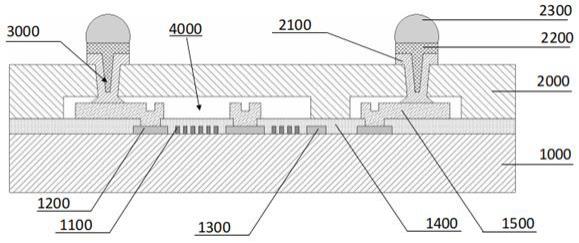
1.本发明提出了温度补偿型声表面滤波器晶圆级封装结构和制造方法,属于滤波器制造技术领域。
背景技术:
2.温度补偿型声表面波滤波器即tc-saw),其天然地在晶圆表面置有一层1~1.5um的sio2层作为温补层,且该sio2层是在整片晶圆范围内被精确平坦化和精确厚度控制的否则滤波器的频率就偏了,而sio2层是天然的sio2-si键合材料fusion bonding,如能直接利用该层sio2实现sio2-si的键合并在idt上方形成空腔结构,则将是比使用双层有机膜做出的晶圆级封装结构更为优异的结构,其键合强度高,粘附性好,对外界环境的隔绝好,可靠性高,因为不再使用昂贵的有机膜材料而成本较低,且由于si的刚性可在其上可靠地做rdl在布线金属层,能使得滤波器芯片设计的版图更为灵活,有助于缩小芯片面积,降低成本。然而,直接使用温补层sio2做sio2-si键合的一个困难是,滤波器的busbar金属层或者叫对外电气连接金属衬垫pad金属层,即前述的140层,为减小滤波器阻抗,其厚度一般需要设置在2~3um,其高度高出sio2表面1um~2um,即sio2层的高度并不是在晶圆表面最高处,不能直接接触si而键合。当然可以在siwafer的一侧相对于busbar金属层的上方开出凹槽,凹槽深度略高于busbarmetal高出sio2的高度使得键合时si接触sio2表面而busbarmetal仍没有碰触si,这样做的一个坏处是,会在si和padmetal之间留下间隙,造成以下问题:第一:需要在si上做出tsv结构以连通滤波器pad金属层,之后通过在tsv内形成金属层而形成对外的电气连接,制造过程繁琐。
3.第二:tsv通过深硅刻蚀工艺形成,刻蚀工艺需要产生有机聚合物附着在tsv孔侧壁以保证刻蚀形貌和表面光滑度,刻蚀后必须用化学清洗工艺清洗掉聚合物。因为tsv孔底和pad metal之间由空隙,在化学品清洗工艺时化学品会通过空隙进入滤波器内,且后续无法清洗出来,导致滤波器芯片失效。
4.第三:也可以先在si上刻蚀半通孔tsv并清洗干净聚合物,之后再键合到滤波器晶圆,再使用si研磨工艺back side grinding减薄si以暴露tsv通孔,如此聚合物清洗问题被克服,但减薄过程中的水混合工艺产生的si粉浆会通过空隙进入滤波器内而导致滤波器失效。
技术实现要素:
5.本发明提供了温度补偿型声表面滤波器晶圆级封装结构和制造方法,用以解决现有技术中直接将温补层sio2做sio2-si键合存在制造过程繁琐,易导致滤波器芯片失效的问题:温度补偿型声表面滤波器晶圆级封装结构的制造方法,所述温度补偿型声表面滤波器晶圆级封装结构的制造方法的过程包括:步骤1、获取tc-saw滤波器晶圆1000,在所述tc-saw滤波器晶圆上制作滤波器idt
叉指结构1100,idt电气连接金属条1200和idt反射栅边侧金属条1300;步骤2、在所述tc-saw滤波器晶圆1000、滤波器idt叉指结构1100,idt电气连接金属条1200和idt反射栅边侧金属条1300的上表面淀积覆盖一层温补层sio21400;步骤3、通过刻蚀方式移除所述idt电气连接金属条1200上表面的温补层sio21400用以形成接触窗,并对所述接触窗进行busbar金属层设置;同时,对所述温补层sio21400表面进行部分移除处理。其它区域的sio2包括芯片切割道表面全部保留,以尽可能多地保留可做键合地sio2表面。
6.步骤4、获取硅盖晶圆2000,并在所述硅盖晶圆2000上沉积sio2层2010作为硅盖晶圆2000的硅表面保护层;以免硅盖制造结构的制造方法中损伤si表面而造成后续si-sio2fusionbonding键合质量问题。
7.步骤5、在带有硅表面保护层的硅盖晶圆2000上进行刻蚀形成凹槽4000,所述凹槽4000的位置与所述滤波器idt叉指结构1100和busbar金属层的位置垂直对齐;步骤6、在所述凹槽4000内通过刻蚀方式形成硅通孔tsv3000,所述硅通孔tsv3000的位置与所述busbar金属层延展于的位置垂直对应;步骤7、使用氢氟酸溶液剥离所述sio2层2010;步骤8、将所述硅盖晶圆2000对位键合到所述tc-saw滤波器晶圆1000上;形成idt1100上方的空隙腔,且达到1500离硅衬底间距《1um的效果。
8.步骤9、在所述硅盖晶圆2000上形成对外连接电气结构。
9.进一步地,步骤1所述叉指结构的厚度小于0.8μm。
10.进一步地,所述滤波器idt叉指结构1100,idt电气连接金属条1200和idt反射栅边侧金属条1300的材料和厚度均相同。
11.进一步地,所述对所述接触窗进行busbar金属层设置;同时,对所述温补层sio21400表面进行部分移除处理,包括:步骤301、在所述接触窗上通过lift-off结构的制造方法方式淀积形成busbar金属层1500,并且将所述busbar金属层1500的一部分层体延展至所述温补层sio21400的上表面;步骤302、对所述tc-saw滤波器晶圆1000进行测试获取所述tc-saw滤波器晶圆1000的频率参数;步骤303、利用离子束trim调频方式对所述温补层sio21400进行表面部分移除。其中,所述表面部分移除量与所述述tc-saw滤波器晶圆1000的频率分布图相对应。
12.具体的,将温补层sio2的很小的一部分实施高精度控制的移除,使得滤波器频率刚好到需要的工作频率,所使用的结构的制造方法是离子束刻蚀,刻蚀速率很慢,可以根据晶圆上滤波器的频率分部图来调整晶圆各个区域的刻蚀量,达到各个滤波器的频率都修正到需要值的目的,其在移除表面sio2时,整个晶圆表面的所有材料都被表面移除掉微小的部分,这个过程将移除sio2表面因为之前的一些结构的制造方法被污染的部分,从而保证后续sio2-si键合的正常进行。
13.进一步地,所述busbar金属层1500厚度范围为2-3μm。
14.进一步地,步骤4所述硅盖晶圆2000采用高阻硅(阻值一般需求在》3000ohm.cm)制成。
15.进一步地,步骤5所述凹槽4000深度要大于所述busbar金属层的厚度,其中,所述凹槽4000深度超过所述busbar金属层的厚度的深度差值不超过1μm。
16.进一步地,步骤6所述硅通孔tsv3000采用上开口小于下开口的梯形结构;所述梯形结构的小底边两侧的锐角范围为85
°‑
87
°
。
17.进一步地,步骤9中所述的在所述硅盖晶圆2000上形成对外连接电气结构,包括:步骤901、使用研磨工艺减薄硅盖晶圆2000,减薄后的所述硅盖晶圆2000的厚度标准为高于所述硅通孔tsv3000底部10~20um的厚度;这里不能直接研磨暴露tsv3000,不然研磨减薄过程中的水混合工艺产生的si粉浆会通过空隙进入滤波器内而导致滤波器失效;步骤902、使用深硅刻蚀设备对所述硅盖晶圆2000进行si刻蚀以暴露硅通孔tsv3000;其中,刻蚀时使用纯si刻蚀工艺参数设定而不做聚合物淀积工艺步骤此时因为不是刻蚀形成通孔tsv,无需考虑刻蚀形貌保护),如此暴露通孔而无聚合物问题,无需后续做湿法化学品清洗工艺,避免化学清洗液和水通过空隙进入滤波器内部而导致器件失效。刻蚀过程中,可以适当过刻蚀,从而利用tsv孔表面刻蚀速度块而孔底部刻蚀速度慢的工艺特性,将tsv的倾角加大,从而有利于后续电气连接金属的填充,可优化tsv半通孔的深度和开口大小以结合此处的过刻蚀量,在达到需要剩余的硅厚度的情况下,实现最终适合的开口大小和倾角。
18.步骤903、在所述硅盖晶圆2000和硅通孔tsv3000上淀积电气连接金属层2100,其中,电气连接金属层2100可以是ti/cu叠层,其在硅通孔tsv3000的底部的厚度需要》1.5um以保证其厚度超过1um的空隙,从而保证电气连接的可靠性。
19.步骤904、将所述硅通孔tsv3000内部全部填充金属2200(如填充cu金属),且所述金属2200的高度高出电气连接金属层2100表面;步骤905、将所述硅通孔tsv3000顶部外围的电气连接金属层2100通过刻蚀方式去除掉;步骤906、在所述金属2200上形成焊锡球2300。
20.温度补偿型声表面滤波器晶圆级封装结构,温度补偿型声表面滤波器晶圆级封装结构为利用上述温度补偿型声表面滤波器晶圆级封装结构的制造方法形成的晶圆级封装结构。
21.本发明有益效果:本发明提出的温度补偿型声表面滤波器晶圆级封装结构和制造方法能够直接在封装过程中将si与sio2进行键合连接,有效提高si与sio2直接键合的键合质量,并且,键合过程中通过先深硅时刻方式形成tsv通孔再进行键合的方式,能够有效避免因先键合再刻蚀产生tsv通孔而产生的有机聚合物附着物,进而无需采用聚合物沉积工艺流程和湿法化学品清洗工艺,使tsv通孔与busbar金属层之间的空隙不会附着聚合物或者渗入湿法化学品,进而,有效提高si与sio2键合质量和键合效率,同时,能够有效避免对键合结构对滤波器芯片性能的不良影响。
附图说明
22.图1为本发明所述温度补偿型声表面滤波器晶圆级封装结构的制造过程结构示意图一;
图2为本发明所述温度补偿型声表面滤波器晶圆级封装结构的制造过程结构示意图二;图3为本发明所述温度补偿型声表面滤波器晶圆级封装结构的制造过程结构示意图三;图4为本发明所述温度补偿型声表面滤波器晶圆级封装结构的制造过程结构示意图四;图5为本发明所述温度补偿型声表面滤波器晶圆级封装结构的制造过程结构示意图五;图6为本发明所述温度补偿型声表面滤波器晶圆级封装结构的制造过程结构示意图六;图7为本发明所述温度补偿型声表面滤波器晶圆级封装结构的制造过程结构示意图七;图8为本发明所述温度补偿型声表面滤波器晶圆级封装结构的制造过程结构示意图八;图9为本发明所述温度补偿型声表面滤波器晶圆级封装结构的制造过程结构示意图九;图10为本发明所述温度补偿型声表面滤波器晶圆级封装结构的制造过程结构示意图十;图11为本发明所述温度补偿型声表面滤波器晶圆级封装结构的制造过程结构示意图十一;图12为本发明所述温度补偿型声表面滤波器晶圆级封装结构的制造过程结构示意图十二;图13为本发明所述温度补偿型声表面滤波器晶圆级封装结构的制造过程结构示意图十三;图14为本发明所述温度补偿型声表面滤波器晶圆级封装结构的制造过程结构示意图十四;图15为本发明所述温度补偿型声表面滤波器晶圆级封装结构的制造过程结构示意图十五;图16为本发明所述温度补偿型声表面滤波器晶圆级封装结构示意图。
具体实施方式
23.以下结合附图对本发明的优选实施例进行说明,应当理解,此处所描述的优选实施例仅用于说明和解释本发明,并不用于限定本发明。
24.本发明实施例提出了一种温度补偿型声表面滤波器晶圆级封装结构的制造方法,在si晶圆上做凹槽形成idt上方和pad metal上方的空隙腔结构(凹槽深度可精确控制在比pad metal的厚度深《1.0um,尽量减少空隙高度,以有利于后续形成对外电气连接的金属接触),之后在凹槽内形成半深度的通孔tsv(根据业界深硅刻蚀的工艺能力,可将tsv刻蚀成略微的梯形形状,以利于后续铺垫金属层)。将si直接键合到滤波器晶圆上,减薄si到即将暴露通孔tsv(留约10~20umsi不暴露tsv),之后使用深硅刻蚀设备做si刻蚀以暴露tsv通
孔,刻蚀时使用纯si刻蚀工艺参数设定而不做聚合物淀积工艺步骤(此时因为不是刻蚀形成通孔tsv,无需考虑刻蚀形貌保护),如此暴露通孔而无聚合物问题,无需后续做湿法化学品清洗工艺。之后,再淀积足够厚的金属层到tsv内,厚度高过缝隙,形成有效电气连接。如图1至图15所示,所述温度补偿型声表面滤波器晶圆级封装结构的制造方法的过程包括:步骤1、获取tc-saw滤波器晶圆1000,在所述tc-saw滤波器晶圆上制作滤波器idt叉指结构1100,idt电气连接金属条1200和idt反射栅边侧金属条1300;其中,所述叉指结构的厚度小于0.8μm。所述滤波器idt叉指结构1100,idt电气连接金属条1200和idt反射栅边侧金属条1300的材料和厚度均相同。
25.步骤2、在所述tc-saw滤波器晶圆1000、滤波器idt叉指结构1100,idt电气连接金属条1200和idt反射栅边侧金属条1300的上表面淀积覆盖一层温补层sio21400;步骤3、通过刻蚀方式移除所述idt电气连接金属条1200上表面的温补层sio21400用以形成接触窗,并对所述接触窗进行busbar金属层设置;同时,对所述温补层sio21400表面进行部分移除处理。其它区域的sio2包括芯片切割道表面全部保留,以尽可能多地保留可做键合地sio2表面。
26.步骤4、获取硅盖晶圆2000,并在所述硅盖晶圆2000上沉积sio2层2010作为硅盖晶圆2000的硅表面保护层;以免硅盖制造结构的制造方法中损伤si表面而造成后续si-sio2fusionbonding键合质量问题。
27.步骤5、在带有硅表面保护层的硅盖晶圆2000上进行刻蚀形成凹槽4000,所述凹槽4000的位置与所述滤波器idt叉指结构1100和busbar金属层的位置垂直对齐;步骤6、在所述凹槽4000内通过刻蚀方式形成硅通孔tsv3000,所述硅通孔tsv3000的位置与所述busbar金属层延展于的位置垂直对应;步骤7、使用氢氟酸溶液剥离所述sio2层2010;步骤8、将所述硅盖晶圆2000对位键合到所述tc-saw滤波器晶圆1000上;形成idt1100上方的空隙腔,且达到1500离硅衬底间距《1um的效果。
28.步骤9、在所述硅盖晶圆2000上形成对外连接电气结构。
29.其中,所述对所述接触窗进行busbar金属层设置;同时,对所述温补层sio21400表面进行部分移除处理,包括:步骤301、在所述接触窗上通过lift-off结构的制造方法方式淀积形成busbar金属层1500,并且将所述busbar金属层1500的一部分层体延展至所述温补层sio21400的上表面;其中,所述busbar金属层1500厚度范围为2-3μm。
30.步骤302、对所述tc-saw滤波器晶圆1000进行测试获取所述tc-saw滤波器晶圆1000的频率参数;步骤303、利用离子束trim调频方式对所述温补层sio21400进行表面部分移除。其中,所述表面部分移除量与所述述tc-saw滤波器晶圆1000的频率分布图相对应。
31.具体的,将温补层sio2的很小的一部分实施高精度控制的移除,使得滤波器频率刚好到需要的工作频率,所使用的结构的制造方法是离子束刻蚀,刻蚀速率很慢,可以根据晶圆上滤波器的频率分部图来调整晶圆各个区域的刻蚀量,达到各个滤波器的频率都修正到需要值的目的,其在移除表面sio2时,整个晶圆表面的所有材料都被表面移除掉微小的部分,这个过程将移除sio2表面因为之前的一些结构的制造方法被污染的部分,从而保证
后续sio2-si键合的正常进行。
32.其中,步骤4所述硅盖晶圆2000采用高阻硅(阻值一般需求在》3000ohm.cm)制成。
33.步骤5所述凹槽4000深度要大于所述busbar金属层的厚度,其中,所述凹槽4000深度超过所述busbar金属层的厚度的深度差值不超过1μm。
34.步骤6所述硅通孔tsv3000采用上开口小于下开口的梯形结构;所述梯形结构的小底边两侧的锐角范围为85
°‑
87
°
。
35.步骤9中所述的在所述硅盖晶圆2000上形成对外连接电气结构,包括:步骤901、使用研磨工艺减薄硅盖晶圆2000,减薄后的所述硅盖晶圆2000的厚度标准为高于所述硅通孔tsv3000底部10~20um的厚度;这里不能直接研磨暴露tsv3000,不然研磨减薄过程中的水混合工艺产生的si粉浆会通过空隙进入滤波器内而导致滤波器失效;步骤902、使用深硅刻蚀设备对所述硅盖晶圆2000进行si刻蚀以暴露硅通孔tsv3000;其中,刻蚀时使用纯si刻蚀工艺参数设定而不做聚合物淀积工艺步骤此时因为不是刻蚀形成通孔tsv,无需考虑刻蚀形貌保护),如此暴露通孔而无聚合物问题,无需后续做湿法化学品清洗工艺,避免化学清洗液和水通过空隙进入滤波器内部而导致器件失效。刻蚀过程中,可以适当过刻蚀,从而利用tsv孔表面刻蚀速度块而孔底部刻蚀速度慢的工艺特性,将tsv的倾角加大,从而有利于后续电气连接金属的填充,可优化tsv半通孔的深度和开口大小以结合此处的过刻蚀量,在达到需要剩余的硅厚度的情况下,实现最终适合的开口大小和倾角。
36.步骤903、在所述硅盖晶圆2000和硅通孔tsv3000上淀积电气连接金属层2100,其中,电气连接金属层2100可以是ti/cu叠层,其在硅通孔tsv3000的底部的厚度需要》1.5um以保证其厚度超过1um的空隙,从而保证电气连接的可靠性。
37.步骤904、将所述硅通孔tsv3000内部全部填充金属2200(如填充cu金属),且所述金属2200的高度高出电气连接金属层2100表面;步骤905、将所述硅通孔tsv3000顶部外围的电气连接金属层2100通过刻蚀方式去除掉;步骤906、在所述金属2200上形成焊锡球2300。
38.上述技术方案的效果为:本实施例提出的温度补偿型声表面滤波器晶圆级封装结构的制造方法能够直接在封装过程中将si与sio2进行键合连接,有效提高si与sio2直接键合的键合质量,并且,键合过程中通过先深硅时刻方式形成tsv通孔再进行键合的方式,能够有效避免因先键合在刻蚀产生的有机聚合物附着物,进而无需采用聚合物沉积工艺流程和湿法化学品清洗工艺,使tsv通孔与busbar金属层之间的空隙不会附着聚合物或者渗入湿法化学品,进而,有效提高si与sio2键合质量和键合效率,同时,能够有效避免对键合结构对滤波器芯片性能的不良影响。
39.本发明的一个实施例,所述busbar金属层1500的一部分层体延展至所述温补层sio21400的上表面,其中,所述busbar金属层1500的延展部分的最大延长长度满足如下条件:3.7d≤l≤4.8d其中,l表示busbar金属层的延展部分的最大延长长度;d表示busbar金属层的厚度。
40.上述技术方案的效果为:通过上述方式获取的busbar金属层延长长度能够保证busbar金属层的延展部分抱有足够的性能功能的情况下,最大程度缩小busbar金属层延长尺寸,通过最大限度缩小延长尺寸的方式能够有效缩小封装结构的尺寸的同时,最大限度提高键合接触面积,进而有效提高键合质量。
41.本发明实施例提出了一种温度补偿型声表面滤波器晶圆级封装结构,如图16所示,温度补偿型声表面滤波器晶圆级封装结构为利用上述温度补偿型声表面滤波器晶圆级封装结构的制造方法形成的晶圆级封装结构。
42.具体的,所述封装结构包括tc-saw滤波器晶圆1000和硅盖晶圆2000;所述tc-saw滤波器晶圆1000和硅盖晶圆2000键合连接;所述tc-saw滤波器晶圆1000上设置有滤波器idt叉指结构1100,idt电气连接金属条1200和idt反射栅边侧金属条1300;在tc-saw滤波器晶圆1000、所述滤波器idt叉指结构1100,idt电气连接金属条1200和idt反射栅边侧金属条1300的上表面设置有温补层sio21400;并且,在所述idt电气连接金属条1200上设置有没附着温补层sio21400的接触窗;在所述接触窗上设置有busbar金属层1500,并且,所述busbar金属层1500外沿覆盖至所述温补层sio21400的部分上表面位置;所述busbar金属层1500与所述idt电气连接金属条1200相连接;位于所述接触窗上方的busbar金属层1500上表面设置有凹槽结构;所述硅盖晶圆2000上设置有凹槽4000;所述凹槽4000与所述滤波器idt叉指结构1100和idt电气连接金属条1200位置对应;在所述凹槽4000内部设置有硅通孔tsv3000;在所述硅通孔tsv3000内壁上设置电气连接金属层2100;在所述电气连接金属层2100形成的凹槽型结构内填充金属2200,并在所述金属2200上设置有焊锡球2300。当所述tc-saw滤波器晶圆1000和硅盖晶圆2000键合连接,所述凹槽4000即可形成所述滤波器晶圆内部的空腔。
43.上述技术方案的效果为:本实施例提出的温度补偿型声表面滤波器晶圆级封装结构能够直接在封装过程中将si与sio2进行键合连接,有效提高si与sio2直接键合的键合质量,并且,键合过程中通过先深硅时刻方式形成tsv通孔再进行键合的方式,能够有效避免因先键合在刻蚀产生的有机聚合物附着物,进而无需采用聚合物沉积工艺流程和湿法化学品清洗工艺,使tsv通孔与busbar金属层之间的空隙不会附着聚合物或者渗入湿法化学品,进而,有效提高si与sio2键合质量和键合效率,同时,能够有效避免对键合结构对滤波器芯片性能的不良影响。
44.显然,本领域的技术人员可以对本发明进行各种改动和变型而不脱离本发明的精神和范围。这样,倘若本发明的这些修改和变型属于本发明权利要求及其等同技术的范围之内,则本发明也意图包含这些改动和变型在内。
再多了解一些
本文用于企业家、创业者技术爱好者查询,结果仅供参考。