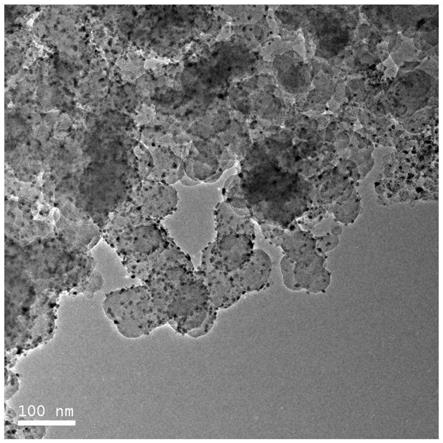
1.本发明涉及催化剂技术领域,尤其涉及一种氮化物负载钯催化剂及其制备方法和应用。
背景技术:
2.环己甲酸是合成药物的重要有机中间体。目前,主要是通过苯甲酸选择性加氢合成环己甲酸。然而,与其它官能团加氢相比(c=o、c=c和c=n),芳香环加氢需要更苛刻的条件,因为需要克服苯环的高共振能量。研究发现,在含碳贵金属催化剂上,熔化的苯甲酸在不需要任何溶剂的情况下可以氢化生成环己甲酸。不幸的是,这些反应都需要在高压高温下进行。因此,急需在温和的反应条件下制备一种高效、环保的苯甲酸选择性加氢催化剂。
3.近年来,研究人员发现pd可用于选择性加氢反应。通过改变pd催化剂载体材料可以控制催化剂的活性。例如有人用mgo(claus,p.;berndt,h.;mohr,c.;radnik,j.;shin,e.-j.;keane,m.a.,j.catal.2000,192,88-97.),al2o3(cervantes,g.g.;aires,f.c.s.;bertolini,j.,j.catal.2003,214,26-32),活性炭(cabiac,a.;delahay,g.;durand,r.;trens,p.;coq,b.;pl
é
e,d.,carbon2007,45,3-10),tio2(panpranot,j.;kontapakdee,k.;praserthdam,p.,j.phys.chem.b,2006,110,8019-8024.)等载体。而碳材料是常见的pd催化剂载体,然而,正如anderson(anderson,j.a.;athawale,a.;imrie,f.e.;mckenna,f.m.;mccue,a.;molyneux,d.;power,k.;shand,m.;wells,r.p.k.,j.catal.2010,270,9-15)所报道的,活性炭碳负载pd催化剂对芳香环加氢的活性也较差,在85℃、1bar的氢气下,pd/ac(活性炭)在24小时内仅将34%的苯甲酸转化为环己甲酸。此外,沉积在碳上的钯在催化过程中很容易被过滤,因为金属和碳表面的相互作用很弱。因此,碳的化学或催化性质并不总是能满足催化作用急剧增加的需求。
技术实现要素:
4.本发明的目的在于提供一种氮化物负载钯催化剂及其制备方法和应用,本发明的氮化物负载钯催化剂拥有很好的活性和较高的环己甲酸选择性,并且由于钯与氮化物的强相互作用导致稳定性提高,从而增加催化剂的使用寿命。
5.为了实现上述发明目的,本发明提供以下技术方案:
6.本发明提供了一种氮化物负载钯催化剂,包括氮化物和负载在所述氮化物上的钯纳米颗粒;所述氮化物为氮化钴、氮化硅、氮化硼或氮化锆。
7.优选的,所述钯纳米颗粒占所述氮化物质量的3~6%。
8.本发明提供了上述方案所述氮化物负载钯催化剂的制备方法,包括以下步骤:
9.将氮化物和钯前驱体溶液混合后进行蒸干,得到固态混合物;
10.将所述固态混合物依次进行煅烧和还原,得到氮化物负载钯催化剂。
11.优选的,所述钯前驱体溶液中的钯前驱体为氯化钯、六氯钯酸钾、醋酸钯、氯钯酸
钠、硝酸钯、乙酰丙酮钯和四氯钯酸铵中的一种或多种。
12.优选的,所述蒸干的温度为80~160℃,时间为6~14h。
13.优选的,所述煅烧在保护气体中进行;所述煅烧的温度为500~800℃,时间为2~7h。
14.优选的,所述还原在氢气和/或氨气中进行;所述还原的温度为200~600℃,时间为2~5h。
15.优选的,所述钯前驱体溶液的浓度为10mg/ml。
16.本发明提供了上述方案所述氮化物负载钯催化剂或上述方案所述制备方法制备得到的氮化物负载钯催化剂在催化苯甲酸加氢制环己甲酸中的应用。
17.优选的,所述应用的条件包括:以水为溶剂,反应温度为50~200℃,氢气压力为0.05~4mpa;苯甲酸与氮化物负载钯催化剂的质量比为(1~4):1。
18.本发明提供了一种氮化物负载钯催化剂,包括氮化物和负载在所述氮化物上的钯纳米颗粒;所述氮化物为氮化钴、氮化硅、氮化硼或氮化锆。
19.本发明以氮化物为载体,氮可以与金属钯之间形成强相互作用的化学键,提高了钯催化剂的稳定性,从而增加了催化剂的使用寿命;此外,金属钯纳米颗粒和氮化物载体之间的强相互作用还有利于钯纳米颗粒的均匀分散,进而有利于提高催化剂的活性;本发明的氮化物负载钯催化剂,氮化物载体与钯纳米颗粒相互协调,拥有很好的活性和较高的环己甲酸选择性。
20.将本发明的氮化物负载钯催化剂用于催化苯甲酸加氢制环己甲酸,可以在较低温度和压力下反应,且使用水为溶剂更加环保。
附图说明
21.图1为实施例1制备的氮化硅负载pd催化剂的tem图;
22.图2为实施例1制备的氮化硅负载pd催化剂的循环稳定性测试结果图;
23.图3为对比例1制备的活性炭负载pd催化剂的循环稳定性测试结果图。
具体实施方式
24.本发明提供了一种氮化物负载钯催化剂,包括氮化物和负载在所述氮化物上的钯纳米颗粒;所述氮化物为氮化钴、氮化硅、氮化硼或氮化锆。
25.在本发明中,所述钯纳米颗粒的粒径优选为3~10nm,更优选为4~6nm。在本发明中,所述氮化物优选为氮化硅。在本发明中,所述钯纳米颗粒的质量优选占所述氮化物质量的3~6%,更优选为4.5~5.5%,更优选为5%。
26.在本发明中,所述钯纳米颗粒均匀分布在氮化物的表面和/或孔道中。
27.本发明以氮化物为载体,可以与金属钯之间形成强相互作用的化学键,提高了钯催化剂的稳定性,从而增加了催化剂的使用寿命;此外,金属钯纳米颗粒和氮化物载体之间的强相互作用还有利于钯纳米颗粒的均匀分散,进而有利于提高催化剂的活性;本发明的氮化物负载钯催化剂,氮化物载体与钯纳米颗粒相互协调,拥有很好的活性和较高的环己甲酸选择性。
28.本发明提供了上述方案所述氮化物负载钯催化剂的制备方法,包括以下步骤:
29.将氮化物和钯前驱体溶液混合后进行蒸干,得到固态混合物;
30.将所述固态混合物依次进行煅烧和还原,得到氮化物负载钯催化剂。
31.在本发明中,未经特殊说明,所用原料均为本领域熟知的市售商品。
32.本发明将氮化物和钯前驱体溶液混合后进行蒸干,得到固态混合物。
33.在本发明中,所述氮化物的粒径优选为纳米级别,本发明对所示氮化物的来源没有特殊要求,采用本领域熟知的市售商品即可。在本发明中,所述钯前驱体溶液中的钯前驱体优选为氯化钯、六氯钯酸钾、醋酸钯、氯钯酸钠、硝酸钯、乙酰丙酮钯和四氯钯酸铵中的一种或多种,更优选为氯化钯。本发明对所述钯前驱体溶液中的溶剂没有特殊要求,根据钯前驱体的种类选择本领域熟知的可将其溶解且不会与氮化物反应并能够蒸发掉的溶剂即可。在本发明中,当所述钯前驱体为氯化钯时,所述溶剂为盐酸和水,所述盐酸的浓度优选为2m。在本发明中,所述钯前驱体溶液的浓度优选为10mg/ml。在本发明中,所述氮化物和钯前驱体溶液的用量根据氮化物负载钯催化剂中氮化物和钯纳米颗粒的含量确定。
34.本发明优选将氮化物和钯前驱体溶液混合后搅拌2~8h,再进行蒸干。本发明对所述搅拌的速率没有特殊要求,采用本领域熟知的搅拌速率即可。本发明利用搅拌使钯前驱体溶液分散均匀。
35.在本发明中,所述蒸干的温度优选为80~160℃,更优选为90~110℃;所述蒸干的时间优选为6~14h,更优选为8~10h。在本发明中,所述蒸干优选在搅拌条件下进行,以加快蒸干速度。本发明在所述蒸干过程中,钯离子吸附在氮化物上。
36.得到固态混合物后,本发明将所述固态混合物依次进行煅烧和还原,得到氮化物负载钯催化剂。
37.在本发明中,所述煅烧优选在保护气体中进行;所述保护气体优选为氮气或惰性气体。在本发明中,所述煅烧的温度优选为500~800℃,更优选为550~650℃;所述煅烧的时间优选为2~7h,更优选为3~5h。本发明利用煅烧,使钯离子与氮化物载体很好地结合在一起。
38.在本发明中,所述还原优选在氢气和/或氨气中进行;当还原气体采用氢气和氨气时,本发明对所述氢气和氨气的配比没有特殊要求,任意配比均可。在本发明中,所述还原的温度优选为200~600℃,更优选为350~450℃;所述还原的时间优选为2~5h,更优选为3~4h。本发明在所述还原过程中,钯离子被还原为金属钯,以纳米颗粒形式分布于氮化物载体上,与氮化物载体牢固结合。
39.本发明提供了上述方案所述氮化物负载钯催化剂或上述方案所述制备方法制备得到的氮化物负载钯催化剂在催化苯甲酸加氢制环己甲酸中的应用。
40.在本发明中,所述应用的条件优选包括:以水为溶剂,反应温度为50~200℃,氢气压力为0.05~4mpa;苯甲酸与氮化物负载钯催化剂的质量比为(1~4):1。进一步的,所述反应温度更优选为70~150℃,最优选为90℃;氢气压力更优选为0.1~2mpa,最优选为0.1mpa;苯甲酸与氮化物负载钯催化剂的质量比更优选为(2~3):1,最优选为2:1。在本发明中,所述苯甲酸与水的用量比优选为(10~13)mg:1ml,更优选为10mg:1ml。
41.下面结合实施例对本发明提供的氮化物负载钯催化剂及其制备方法和应用进行详细的说明,但是不能把它们理解为对本发明保护范围的限定。
42.实施例1
43.1)称取1g的pdcl2溶解于浓盐酸中,转移至100ml容量瓶中,加入去离子水到相应刻度,制得质量浓度为10mg/ml的氯钯酸溶液;
44.2)将1g的氮化硅与85.5ml步骤1)中的氯钯酸溶液(氯钯酸溶液中pd占氮化硅质量的5%)混合在一起进行搅拌4h,随后在温度100℃下搅拌9h进行蒸干,得到固态混合物;
45.3)将步骤2)得到的固态混合物在氮气下进行600℃高温煅烧4h,随后在氢气气体下进行400℃还原3h,即得到氮化硅负载pd催化剂。
46.图1是实施例1制备的氮化硅负载pd催化剂的tem图,由图1可知,金属钯颗粒分散均匀,颗粒大小约为5nm左右。
47.实施例2
48.1)称取1g的pdcl2溶解于浓盐酸中,转移至100ml容量瓶中,加入去离子水到相应刻度,制得质量浓度为10mg/ml的氯钯酸溶液;
49.2)将1g的氮化钴与85.5ml步骤1)中的氯钯酸溶液(氯钯酸溶液中pd占氮化钴质量的5%)混合在一起进行搅拌4h,随后在温度100℃下搅拌9h进行蒸干,得到固态混合物;
50.3)将步骤2)得到的固态混合物在氮气下进行600℃高温煅烧4h,随后在氢气气体下进行400℃还原3h,即得到氮化钴负载pd催化剂。
51.实施例3
52.1)称取1g的pdcl2溶解于浓盐酸中,转移至100ml容量瓶中,加入去离子水到相应刻度,制得质量浓度为10mg/ml的氯钯酸溶液;
53.2)将1g的氮化硼与85.5ml步骤1)中的氯钯酸溶液(氯钯酸溶液中pd占氮化硼质量的5%)混合在一起进行搅拌4h,随后在温度100℃下搅拌9h进行蒸干,得到固态混合物;
54.3)将步骤2)得到的固态混合物在氮气下进行600℃高温煅烧4h,随后在氢气气体下进行400℃还原3h,即得到氮化硼负载pd催化剂。
55.实施例4
56.1)称取1g的pdcl2溶解于浓盐酸中,转移至100ml容量瓶中,加入去离子水到相应刻度,制得质量浓度为10mg/ml的氯钯酸溶液;
57.2)将1g的氮化锆与85.5ml步骤1)中的氯钯酸溶液(氯钯酸溶液中pd占氮化锆质量的5%)混合在一起进行搅拌4h,随后在温度100℃下搅拌9h进行蒸干,得到固态混合物;
58.3)将步骤2)得到的固态混合物在氮气下进行600℃高温煅烧4h,随后在氢气气体下进行400℃还原3h,即得到氮化锆负载pd催化剂。
59.实施例5
60.1)称取1g的硝酸钯溶解于去离子水中,转移至100ml容量瓶中,加入去离子水到相应刻度,制得质量浓度为10mg/ml的硝酸钯溶液;
61.2)将1g的氮化硅与108.5ml步骤1)中的硝酸钯溶液(硝酸钯溶液中pd占氮化硅质量的5%)混合在一起进行搅拌4h,随后在温度100℃下搅拌9h进行蒸干,得到固态混合物;
62.3)将步骤2)得到的固态混合物在氮气下进行600℃高温煅烧4h,随后在氢气气体下进行400℃还原3h,即得到氮化硅负载pd催化剂。
63.实施例6
64.1)称取1g的六氯钯酸钾溶解于去离子水中,转移至100ml容量瓶中,加入去离子水到相应刻度,制得质量浓度为10mg/ml的六氯钯酸钾溶液;
65.2)将1g的氮化硅与187.3ml步骤1)中的六氯钯酸钾溶液(六氯钯酸钾溶液中pd占氮化硅质量的5%)混合在一起进行搅拌4h,随后在温度100℃下搅拌9h进行蒸干,得到固态混合物;
66.3)将步骤2)得到的固态混合物在氮气下进行600℃高温煅烧4h,随后在氢气气体下进行400℃还原3h,即得到氮化硅负载pd催化剂。
67.实施例7
68.与实施例1的不同之处在于步骤3)的氢气还原改为氨气还原。
69.对比例1
70.与实施例1的不同之处仅在于将氮化硅换成了活性炭,具体的步骤如下:
71.1)称取1g的pdcl2溶解于浓盐酸中,转移至100ml容量瓶中,加入去离子水到相应刻度,制得质量浓度为10mg/ml的氯钯酸溶液。
72.2)将1g的活性炭与85.5ml步骤1)中的氯钯酸溶液混合在一起进行搅拌4h,随后在温度100℃下搅拌9h进行蒸干,得到固态混合物;
73.3)将步骤2)得到的固态混合物在氮气下进行600℃高温煅烧4h,随后在氢气气体下进行400℃还原3h,即得到活性炭负载pd催化剂。
74.性能测试
75.将实施例1~7和对比例1制备的催化剂10mg装填在高压反应釜中,以2ml水为溶剂,在温度为90℃、0.1mpa氢气的反应压力、苯甲酸与氮化硅负载pd催化剂的质量比为2:1条件下,苯甲酸加氢得到环己甲酸,苯甲酸的转化率和环己甲酸的选择性见表1。
76.表1实施例1~7及对比例1制备的催化剂对苯甲酸的转化率和环己甲酸选择性数据
77.编号苯甲酸转化率环己甲酸选择性实施例198.5%99.2%实施例290.1%92.6%实施例380.9%91.6%实施例489.3%94.5%实施例597.2%98.8%实施例695.8%97.3%实施例798.3%98.9%对比例150.7%37.5%
78.由表1的结果可知,本发明以氮化物为载体,相较以活性炭为载体制备的催化剂具有更高的苯甲酸转化率,说明本发明的催化剂具有更好的催化活性,且对环己甲酸的选择性更高。尤其是以氮化硅为载体制备的催化剂的催化活性和选择性更好。
79.将实施例1制备的催化剂进行循环稳定性测试,结果见图2。由图2可以发现,经过六次的循环实验,催化剂的转化率基本上不变,维持在99.0%左右,说明其具有良好的稳定性。
80.将对比例1制备的催化剂进行循环稳定性测试,结果见图3。由图3可以发现,经过六次的循环实验,催化剂的转化率下降严重(降低至20.5%),稳定性较差。
81.以上所述仅是本发明的优选实施方式,应当指出,对于本技术领域的普通技术人
员来说,在不脱离本发明原理的前提下,还可以做出若干改进和润饰,这些改进和润饰也应视为本发明的保护范围。
再多了解一些
本文用于企业家、创业者技术爱好者查询,结果仅供参考。