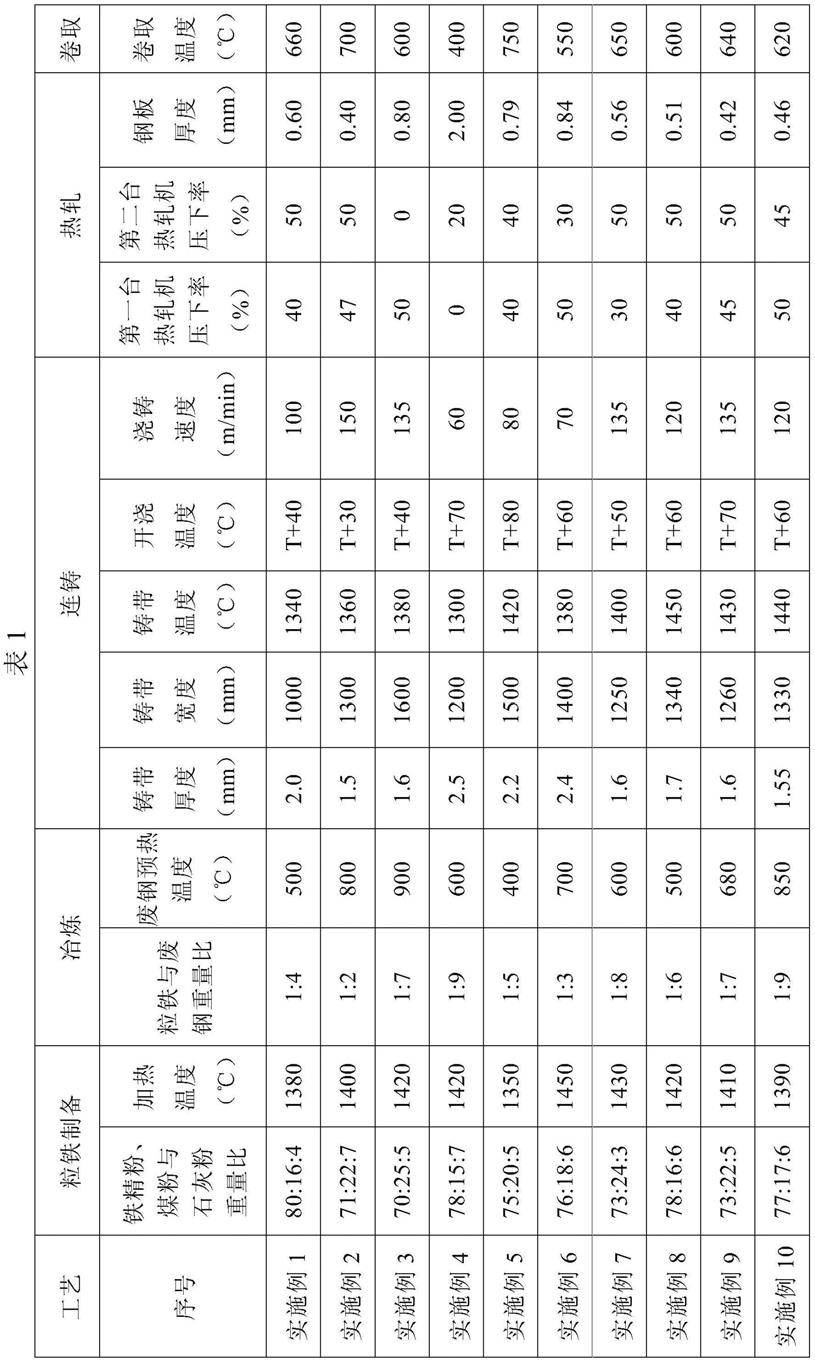
1.本发明属于金属板带的连续生产技术领域,特别涉及一种超薄热轧宽带钢的制造方法。
背景技术:
2.现代钢铁生产企业为节省投资成本与生产成本,积极对现有生产工艺流程进行技术革新,为此,国内外冶金设备供应商和钢铁制造商纷纷提出自己的新技术理念并付诸于实际开发。针对现有热带钢生产工艺流程长、设备多且复杂的问题,逐步发展了源于亨利
·
贝塞麦提出的双辊薄带连铸连轧技术的产业化技术,日本新日铁开发了不锈钢双辊薄带连铸连轧技术dsc,美国纽柯公司与日本ihi、澳大利亚bhp合作开发了碳钢双辊薄带连铸连轧技术castrip,韩国浦项开发了不锈钢双辊薄带连铸连轧技术postrip,欧洲联合开发了不锈钢双辊薄带连铸连轧技术eurostrip,中国宝钢开发了碳钢双辊薄带连铸连轧技术baostrip。
3.为充分发挥薄带连铸连轧工艺技术优势,许多生产厂家将薄带连铸连轧技术与传统工艺紧密结合,以满足薄带连铸连轧工艺的需求。
4.连铸连轧生产钢的过程中,主要是通过电炉或转炉给薄带连铸供应钢水。采用转炉炼钢提供钢水,则需要生产厂家具备有提供铁水的条件,一般情况下,需要有高炉炼铁或者非高炉炼铁设备,属于目前长流程钢铁生产模式。
5.采用电炉炼钢提供钢水,则以废钢为主要原料,传统工艺比如模铸或者厚板连铸,其凝固冷却速度仅有1~10℃/s,废钢中的这些残余元素,会在凝固过程中发生晶界偏析,恶化钢的性能和质量,严重时直接发生开裂、断裂现象,所以在传统工艺中,要对这些有害元素严加控制,在废钢原料的选择上,需要进行一些预筛选,以及在炼钢过程中需要进行一些特殊处理,比如添加一些精料进行稀释等等,这无疑增加了生产作业成本。由于需要控制钢的成分,对采用的废钢原料有一定的质量要求,一般情况下,需要对废钢进行预筛选分类。同时拥有高炉和电炉的钢厂利用自产铁水兑入到电炉中作为电炉原料来提高电炉的生产效率,从而大大缩短电炉的出钢时间,电炉中的铁水勾兑比可达到30~50%。
技术实现要素:
6.本发明的目的在于提供一种超薄热轧宽带钢的制造方法,极大精简工艺流程,所得薄规格钢板厚度能够达到冷轧后钢板的厚度,真正实现“以热代冷”,大大提高产品竞争力,整体工艺更环保、更高效、热利用率高、金属收得率高,该方法不仅直接降低了薄规格带钢的成本,而且能够显著降低一次性投资成本。
7.为达到上述目的,本发明的技术方案是:
8.一种超薄热轧宽带钢的制造方法,其包括如下步骤:
9.1)粒铁制备
10.将铁精粉、煤粉和石灰粉混合均匀,压制成球团或团块并干燥;将球团或团块置于
转底炉中,加热转底炉,使转底炉内的球团或团块进行还原、渗碳、熔融,之后快速水冷至750~850℃,将粒铁和渣分离后分别排出;所述铁精粉、煤粉和石灰粉的重量比为70~80:15~25:3~7,转底炉加热温度为1350~1450℃;
11.2)冶炼
12.将上述制备的粒铁输送至电炉内与经过电炉预热装置预热后的废钢混合,进行熔化和冶炼,获得钢水;粒铁和废钢的重量比为1:2~9,废钢预热温度为400~900℃;
13.3)精炼
14.从电炉流出的钢水依次进行vd真空脱气、lf精炼;
15.4)连铸
16.连铸采用双辊薄带连铸,获得厚度为1.5~2.5mm、宽度为1000~1600mm的铸带;钢水开浇温度为t (30~80)℃,其中t为液相线温度,铸带温度1300~1450℃,结晶辊内部通水冷却,铸机浇铸速度为60~150m/min;
17.5)热连轧
18.铸带经夹送辊送至双机架轧机组进行热连轧,单台机架的压下率≤50%;热连轧后钢板厚度为0.4~2.0mm;
19.6)卷取
20.热轧后的钢板经过雾化冷却,冷却后的钢板经切头或分切处理后送至卷取机进行卷取;卷取温度为400~750℃。
21.进一步,所述卷取后获得的钢卷经喷码、打捆后进行空冷或缓冷。
22.进一步,所述空冷或缓冷后的钢卷进行切边、平整制得黑皮卷;或酸洗、镀锌制得热轧热镀锌卷;或酸洗、平整制得热轧酸洗卷;或切边、平整、射流除鳞,制得薄规格热轧卷。
23.优选的,所述铁精粉为磁铁矿粉、赤铁矿粉、褐铁矿粉或菱铁矿粉中的一种或多种。
24.优选的,所述煤粉为非焦煤粉、普通煤粉、石油焦中的一种或多种。
25.优选的,所述废钢为轻薄料、统废、重废中的一种或多种。
26.优选的,步骤2)中,粒铁和废钢输送至电炉内的输送方式为连续输送或间歇式输送。
27.优选的,步骤5)所述热连轧后钢板厚度为0.4~0.6mm。
28.优选的,步骤6)所述卷取采用卡罗塞尔卷取。
29.在本发明的工艺设计中,采用转底炉 电炉完成钢水冶炼,通过真空脱气(vd)和精炼炉(lf)完成对钢水成分调整和夹杂物控制,之后经过双辊薄带连铸 双机架轧机组完成质量合格、性能优良的超薄热轧带钢卷的生产,实现绿色化、全连续化、智能化、简约化、以热代冷的短流程冶金生产工艺布置。
30.本发明通过转底炉制备粒铁、电炉冶炼钢水、双辊薄带连铸和双机架热轧工艺的有机结合,设计了一种极其精简的集约化冶金生产工艺,该工艺不仅能降低一次性投资成本,并且显著降低了碳排放、能源消耗、金属消耗,同时降低了薄规格带钢产品的加工成本,可以直接得到冷轧厚度规格的产品,真正实现“以热代冷”,大大提高产品的竞争力。
31.转底炉生产粒铁工艺是一种环保的短流程粒铁生产工艺,且该工艺能够连续、经济地生产粒铁,将铁精粉(包括钢铁厂回收的氧化粉尘)、煤粉和石灰粉按一定比例混合,用
造球或压块机得到球团或团块,干燥后作为转底炉生产粒铁的原料,将干燥后的球团或团块放入转底炉,料层不能过厚(1~3层为宜),原料随炉床匀速转动一周(球团或团块依次经过装料区、排烟区、预热区、中温还原区、高温还原区和出料区),在球团或团块与炉床静止状态下加热到1350~1450℃,发生还原、渗碳及熔融反应,渣铁熔化,各自聚集,整个过程约需10min(煤粉与铁氧化物紧密接触,还原速度很快)完成还原熔分;充分还原熔分后的凝聚态渣铁经快速冷却至750~850℃,之后使用排料装置完成粒铁与渣的分别排出。
32.转底炉的传统使用方法是将生产的粒铁冷却到室温后,装袋进行对外销售,或者是输送到炼钢工序作为炼钢原料。本发明利用转底炉生产出的750~850℃的高温粒铁直接通过输送带输送至电炉内,大大利用高温粒铁的余热,对混合在一起的废钢起到预热效果,提高电炉的热效率,减少了能源消耗。
33.本发明所述铁精粉可以是磁铁矿粉、赤铁矿粉、褐铁矿粉或菱铁矿粉中的一种或多种,原料来源广泛,且对原料品位无严格要求;煤粉用非焦煤粉、普通煤、石油焦中的一种或多种;转底炉产生的废烟气经热交换器后除尘排出,实现节能环保要求,一台转底炉粒铁年产量在5~20万吨。
34.转底炉生产的粒铁输送至电炉内与废钢混合后完成钢水冶炼。废钢连续输送或间歇式输送至预热装置中,电炉自带预热装置,预热后与粒铁混合后在电炉内进行冶炼,可以减少热量损耗。提高废钢预热温度,将废钢预热温度至400~900℃,同时利用生产的粒铁温度,大大降低了电炉的电耗,有效提高电炉的热效率。
35.由于薄带连铸的亚快速凝固特征,对废钢质量的要求可以大幅度降低,加入到电炉内的废钢量也可以增大,粒铁与废钢的重量比例范围可以扩大到1:2~9。
36.获得的钢水被运送至精炼工位进行处理,首先在vd真空脱气装置进行脱碳、脱硫、脱氢,其次在lf精炼炉进行成分调整和升温。常规连铸工艺前的钢水精炼一般是先经过lf精炼炉处理,然后再进入到vd炉处理;但是精炼后的钢水需要经过薄带连铸工艺进行铸造,由于其工艺特点,因此要求先经vd、再进入到lf精炼炉处理。
37.精炼后的钢水经过双辊薄带连铸,双辊薄带连铸技术是典型的亚快速凝固过程,凝固冷却速度高达102~104℃/s,废钢无需任何预筛选,可以是轻薄料、统废、重废中一种或多种,废钢中的一些有害残余元素,比如cu、sn、p等,可以最大限度地固溶到钢的基体中而不产生晶界偏析,从而起到固溶强化的作用;对这些有害的残余元素起到“化害为利”,“废物利用”的效果,大大降低原料成本。
38.铸带出来之后的厚度较薄,最薄可以达到1.5mm,铸带温度也较高,一般在1300~1450℃,为降低铸带受高温氧化等因素的影响,通常在结晶辊出带口增设保护罩,且在保护罩内通一定量的惰性气体(如n2或ar),在保护罩内形成微正压以满足气体保护效果。所得的铸带,可以是中、低碳钢、低碳微合金钢、合金钢、不锈钢、电工钢等钢种。
39.薄带连铸获得较薄的铸带结合双机架轧机组热连轧,单台机架压下率可到50%,总压下率可达到100%,热轧后板带厚度可达0.4~0.6mm,实现世界首创。
40.本发明采用双机架四辊热连轧机组,其带有控制板型的弯辊、串辊功能,或弯辊、交叉辊功能,且具有带钢压下、带钢导向、纠偏功能;采用的四辊轧机具有在线换辊功能;单台热轧机的压下率范围为0~50%,轧后成品厚度达到0.4~2.0mm,其中,热轧态产品厚度最薄达到0.4-0.6mm的范围。两台轧机通常情况下同时工作,也可以在特殊情况下如一轧机
工作辊表面粗糙度会急剧增大造成带钢表面质量恶化,则另一轧机交叉投入使用。
41.一台轧机压下率0%表示该轧机辊缝打开不轧,一种情况是在生产较厚(厚度1.2~2.0mm)的带钢时可以采用,即一台轧机空过不轧,另一台轧机投入轧制;另一种情况是其中一台轧机工作辊达到寿命进行在线换辊,另一台轧机持续投入轧制。可见,采用双机架热连轧模式可以实现持续稳定的轧制,在线换辊功能可以克服因工作辊表面磨损而全线停机的问题。
42.换辊过程具体描述如下:在no.1热轧机轧制带钢吨位达到400-800t时,轧机工作辊表面粗糙度会急剧增大造成带钢表面质量恶化,在此事件发生之前,可以和no.2热轧机进行协同,即no.1热轧机缓慢打开,no.2热轧机缓慢压下,待no.1热轧机完全打开后,此时no.2热轧机压下到位,随后no.1热轧机进行在线换辊(工作辊)操作,换完后复位待命,等待no.2热轧机需要换辊时重复上述操作。
43.热连轧后的板带采用卡罗塞尔双卷筒卷取机实现连续生产,每一个钢卷的卷取温度差可以控制在10℃以内。
44.卷取后的10~30吨的钢卷进行喷码、打捆后进行空冷或缓冷。满足工艺要求的材质和力学性能指标钢卷,可以进行切边、平整制得黑皮卷;或酸洗、镀锌制得热轧热镀锌卷;或酸洗、平整制得热轧酸洗卷;或切边、平整、射流除鳞,制得薄规格热轧卷。
45.本发明与已有技术的区别及改进之处:
46.中国专利cn201710763021.2公开了“一种基于直接还原铁的薄带钢短流程生产工艺”,该工艺包括如下工艺步骤:1)直接还原炼铁;2)电炉或转炉炼钢;3)lf精炼;4)rh真空处理;5)薄带铸轧。该发明所述的直接还原炼铁采用竖炉冶炼技术得到,直接还原铁的生产以竖炉工艺为主要海绵铁生产方案,还原温度为1000度左右,还原铁加入到炼钢炉内(电炉、或转炉),原铁加入量为原料总重量的55%~90%。该发明制备粒铁的工艺与本发明转底炉制备粒铁的工艺完全不同,本发明重点强调了从原料到薄带连铸全流程的可控生产超薄热轧带钢,并以低碳钢为主要热轧产品的完整生产流程。
47.美国专利us9725780b2公开了“一种采用感应电炉与棒、线材连铸机、棒线材热轧机连接的工艺路线和产线布置方式”,该发明采用感应电炉熔化废钢的方式得到钢水,还需要对废钢进行预筛选,生产效率比较低。钢水来源不同,后序精炼工艺、轧制工艺与本发明均不同,最终产品也不一样。
48.中国专利cn201210317195.3公开了“一种利用低温在线静态再结晶生产钢带的方法”,该发明采用双机架低温奥氏体在线静态再结晶轧制,开轧温度900-1050℃,总压下量50-70%。本发明与该发明不同,本发明强调了钢水如何获得,即详细阐述了采用转底炉制备粒铁,然后与废钢混合在电炉内冶炼得到钢水,而该发明未涉及;本发明的总压下率可达到100%,产品最薄厚度可达0.4mm,而该发明最大总压下量仅为70%。
49.中国专利cn200910053806.6公开了“具有cu
2-x
s弥散析出相的高强度耐大气腐蚀钢及其制造方法”,该发明采用转炉顶底复合吹炼获得钢水,通过薄带连铸获得铸带,采用双机架轧机对带钢进行轧制获得0.6-2.0mm的带钢,其中第一机架压下率不小于30%,第二机架的压下率在0-30%。本发明与该发明不同,本发明详细阐述了采用转底炉制备粒铁,然后与废钢混合在电炉内冶炼得到钢水,通过薄带连铸得到较薄的铸带,双机架轧机的每台轧机最大压下率都可达到50%,生产的带钢最薄可以达到0.4mm。
50.本发明的有益效果:
51.1、本发明通过转底炉制备粒铁、电炉冶炼钢水、双辊薄带连铸和双机架热轧工艺的有机结合,设计了一种极其精简的集约化冶金生产工艺,该工艺不仅能显著降低一次性投资成本,同时极大精简工艺流程,显著降低了碳排放、能源消耗、金属消耗、电极消耗,直接降低了薄规格带钢产品的加工成本,可以直接得到冷轧厚度规格的产品,真正实现“以热代冷”,大大提高产品的竞争力。
52.2、本发明将电炉冶炼钢水和双辊薄带工艺相结合,粒铁和废钢的重量比可达1:2~9,可以采用大比例的轻薄料废钢,冶炼后的钢水采用双辊薄带连铸技术进行铸造,双辊薄带连铸技术是典型的亚快速凝固过程,凝固冷却速度高达102~104℃/s,废钢中的一些有害残余元素,比如cu、sn、p等,可以最大限度地固溶到钢的基体中而不产生晶界偏析,从而起到固溶强化的作用;对这些有害的残余元素起到“化害为利”,“废物利用”的效果,大大降低原料成本。
53.3、本发明采用双机架热连轧技术,并且单台机架压下率可达到50%,总压下率可达到100%,使产出的金属板带厚度最薄达到0.4-0.6mm的范围,现有技术使用热轧得到的钢板厚度还未见有达到0.4mm的报道;热连轧后钢板厚度为0.4~2.0mm,可以完全替代冷轧制备厚度规格0.4~1.2mm的大部分产品,从而真正实现“以热代冷”。
54.4、本发明将粒铁与废钢直接混合作为冶炼原料,高效利用了转底炉生产出来粒铁的温度,并提高了废钢的预热温度,大大降低了电炉的电耗,有效提高了电炉的热效率,节能环保。
55.5、采用双辊薄带技术直接对液态金属浇注成薄规格(厚度<2.5mm)铸带,取代传统的厚板坯(厚度>150mm)通过粗轧与多道次热轧之后的热轧板,实现非常紧凑的短流程工艺,以满足优异的低碳排放要求与较短的厂房建设要求。
附图说明
56.图1为本发明实施例超薄热轧宽带钢的工艺示意图。
具体实施方式
57.下面通过实施例及附图对本发明作进一步说明,但这并非是对本发明的限制,本领域技术人员根据发明的基本思路可以做出修改或改进,但只要不脱离本发明的基本思想,均在本发明的范围之内。
58.实施例1
59.将铁精粉、煤粉和石灰粉按比例混合均匀,压制成球团或团块并干燥;将其置于转底炉1中,加热转底炉1,使转底炉1内的球团或团块进行还原、渗碳、熔融,快速冷却后将粒铁和渣分离后分别排出;加热温度为1380℃。
60.转底炉1排出的粒铁输送至电炉2,先经过预热装置预热后的废钢进行混合在电炉2中熔化冶炼约40min后出钢,钢水倒入60吨级的钢包,通过台车钢包被运至精炼工位进行处理,钢水首先在vd真空脱气炉3进行脱碳、脱硫、脱氢,其次进入lf精炼炉4进行成分调整和升温。
61.精炼后的钢水运送至双辊薄带连铸单元的大包回转台5上,钢水开浇温度控制在
液相线以上40℃,大包6开浇后,钢水进入中间包7,通过中间包7把钢水送入两个结晶辊8所形成的熔池中,同时对进入熔池的钢水进行分配和布流。钢水在双辊薄带连铸单元的两个结晶辊8上完成凝固,铸造出质量合格的厚度规格2.0mm的铸带9。此时铸带9的温度为1340℃,为降低铸带9受高温氧化等因素影响,通常在结晶辊8出带口增设保护罩,且在保护罩内通一定量的惰性气体(如n2),形成保护罩内具有微正压以满足气体保护效果。
62.受气氛保护的铸带9通过导向装置顺利进入双机架夹送辊10,然后进入双机架四辊热连轧机组11,no.1热轧机的压下率为40%,no.2热轧机的压下率为50%,用于改善带钢的板形,同时改善内部的组织结构和机械性能。
63.轧制后的带钢(厚度0.6mm)经过雾化冷却系统12降温到660℃之后进行卷取,且保证板面的宽度方向、长度方向的卷取温度均匀。冷却处理后的带钢通过飞剪13切头(第一卷)或分切后,进行卡罗塞尔卷取机14成卷,成卷后的25吨钢卷经过喷码、打捆15后由输送机构16送入中间钢卷库进行空冷。满足工艺要求的材质和力学性能指标的热轧带钢,顺次进入酸镀一体单元,生产出热轧热镀锌卷。
64.实施例2
65.将铁精粉、煤粉和石灰粉按比例混合均匀,压制成球团或团块并干燥;将其置于转底炉1中,加热转底炉1,使转底炉1内的球团或团块进行还原、渗碳、熔融,快速冷却后将粒铁和渣分离后分别排出;加热温度为1400℃。
66.转底炉1排出的粒铁输送至电炉2,与经过预热装置预热后的废钢进行混合后在电炉2中熔化冶炼约50min后出钢,钢水倒入80吨级的钢包,通过台车钢包被运至精炼工位进行处理,钢水首先在vd真空脱气炉3进行脱碳、脱硫、脱氢,其次进入lf精炼炉4进行成分调整和升温。
67.精炼后的钢水运送至双辊薄带连铸单元的大包回转台5上,钢水开浇温度控制在液相线以上30℃,大包6开浇后,钢水进入中间包7,通过中间包7把钢水送入两个结晶辊8所形成的熔池中,同时对进入熔池的钢水进行分配和布流。钢水在双辊薄带连铸单元的两个结晶辊8上完成凝固,铸造出质量合格的厚度规格1.5mm的铸带9。此时铸带9的温度为1360℃,为降低铸带9受高温氧化等因素影响,通常在结晶8出带口增设保护罩,且在保护罩内通一定量的惰性气体(如ar),形成保护罩内具有微正压以满足气体保护效果。
68.受气氛保护的铸带9通过导向装置顺利进入双机架夹送辊10,然后进入双机架四辊热连轧机组11,no.1热轧机的压下率为47%,no.2热轧机的压下率为50%,用于改善带钢的板形,同时改善内部的组织结构和机械性能。
69.轧制后的带钢(厚度0.4mm)经过雾化冷却系统12降温到700℃之后进行卷取,且保证板面的宽度方向、长度方向的卷取温度均匀。冷却处理后的带钢通过飞剪13切头(第一卷)或分切后,进行卡罗塞尔卷取机14成卷,成卷后的25吨钢卷经过喷码、打捆15后由输送机构16送入中间钢卷库进行空冷。满足工艺要求的材质和力学性能指标的热轧带钢,按照后部冷轧带钢的质量要求,顺次进入切边、平整、射流除鳞单元,出薄规格热轧卷,可“以热代冷”。
70.实施例3
71.将铁精粉、煤粉和石灰粉按比例混合均匀,压制成球团或团块并干燥;将其置于转底炉1中,加热转底炉1,使转底炉1内的球团或团块进行还原、渗碳、熔融,快速冷却后将粒
铁和渣分离后分别排出;加热温度为1420℃。
72.转底炉1排出的粒铁输送至电炉2,与经过预热装置预热后的废钢进行混合在电炉中熔化冶炼约60min后出钢,钢水倒入100吨级的钢包,通过台车钢包被运至精炼工位进行处理,钢水首先在vd真空脱气炉3进行脱碳、脱硫、脱氢,其次进入lf精炼炉4进行成分调整和升温。
73.精炼后的钢水运送至双辊薄带连铸单元的大包回转台5上,钢水开浇温度控制在液相线以上40℃,大包6开浇后,钢水进入中间包7,通过中间包7把钢水送入两个结晶辊8所形成的熔池中,同时对进入熔池的钢水进行分配和布流。钢水在双辊薄带连铸单元的两个结晶辊8上完成凝固,铸造出质量合格的厚度规格1.6mm的铸带9。此时铸带9的温度为1380℃,为降低铸带9受高温氧化等因素影响,通常在结晶辊8出带口增设保护罩,且在保护罩内通一定量的惰性气体(如ar),形成保护罩内具有微正压以满足气体保护效果。
74.受气氛保护的铸带9通过无引带头的导向装置顺利进入双机架夹送辊10,然后进入双机架四辊热连轧机组11,no.1热轧机的压下率为50%,no.2热轧机的压下率为0%,用于改善带钢的板形,同时改善内部的组织结构和机械性能。在no.1热轧机轧制带钢吨位达到400-800t时,轧机工作辊表面粗糙度会急剧增大造成带钢表面质量恶化,在此之前,可以和no.2热轧机进行协同,即no.1热轧机缓慢打开,no.2热轧机缓慢压下,待no.1热轧机完全打开后,此时no.2热轧机压下到位,压下率达到50%,随后no.1热轧机进行在线换辊(工作辊)操作,换完后复位待命,等待no.2热轧机需要换辊时重复上述操作。
75.轧制后的带钢(厚度0.8mm)经过雾化冷却系统12降温到600℃之后进行卷取,且保证板面的宽度方向、长度方向的卷取温度均匀。冷却处理后的带钢通过飞剪13切头(第一卷)或分切后,进行卡罗塞尔卷取机14成卷,成卷后的25吨钢卷经过喷码、打捆15后由输送机构16送入中间钢卷库进行空冷。满足工艺要求的材质和力学性能指标的热轧带钢,按照后部冷轧带钢的质量要求,顺次进入切边、平整单元,出黑皮卷。
76.本发明实施例具体工艺参数见表1。
77.
再多了解一些
本文用于企业家、创业者技术爱好者查询,结果仅供参考。