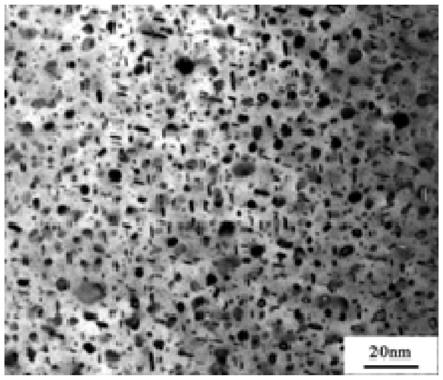
1.本发明涉及航空航天用铝合金挤压材的制备方法材领域。
背景技术:
2.随着我国航空航天事业的迅猛发展,对基础材料提出了更加苛刻的要求。在要求挤压挤压材截面尺寸增大,定尺长度加长的同时,要求挤压挤压材性能具有更高强韧性匹配。需要研制出抗拉强度≥650mpa,屈服强度≥610mpa,压缩屈服强度≥620mpa,延伸率≥8%,断裂韧性≥33kic/mpa
·m1/2
,电导率≥37%iacs的高综合指标的截面积≥50cm2,长度≥12m 的挤压材,并形成稳定化的生产工艺,现有铝合金挤压材的抗拉强度、韧性和耐腐蚀性很难兼顾,若抗拉强度高,则韧性和耐腐蚀性能相对较差,而若韧性和耐腐蚀性能优异,则抗拉强度低。
3.7000系铝合金是典型的沉淀强化合金,是航空工业的主要结构材料之一。7000系铝合金t6峰时效处理后,晶内沉淀相为析出细小的gp区和η
′
相,得到最大强化效果。然而,达到峰值后,合金晶内析出细小的半共格弥散相,晶界分布着较粗大的连续链状质点,这种晶界组织对应力腐蚀和剥落腐蚀十分敏感,在实际应用中很难发挥其综合性能。
技术实现要素:
4.本发明要解决现有方法制备的铝合金挤压材无法同时具有高抗拉强度、高韧性和耐腐蚀性能的技术问题,而提供一种航空航天用超强高韧耐蚀铝合金挤压材的制备方法。
5.一种航空航天用超强高韧耐蚀铝合金挤压材的制备方法,具体按以下步骤进行:
6.一、按照元素质量百分含量为cu:1.8%~2.2%、mg:1.8%~2.6%、zn:8.2%~9.2%、 zr:0.10%~0.13%、cr:0.02%~0.04%、ti:0.01%~0.04%和余量为al的比例称取铝锭、阴极铜、原生镁锭、锌锭、铝锆合金锭、铝铬中间合金锭和铝钛丝作为原料,然后将原料放入熔炼炉中熔炼,得到铝合金熔液;
7.二、将步骤一得到的铝合金熔液采用半连续铸造工艺铸造成铝合金圆铸锭;
8.三、在室温条件下除去步骤二铸造的铝合金圆铸锭的氧化皮;
9.四、将步骤三处理后的铝合金圆铸锭在温度为420℃~440℃的条件下,保温12h,然后升温至470℃的条件下保温60h,出炉后自然冷却至室温,得到退火后的圆铸锭;
10.五、将退火后的圆铸锭放入感应加热炉中,加热到420℃~440℃,然后采用挤压机进行热挤压,得到铝合金挤压材;
11.六、将步骤五获得的铝合金挤压材放入电阻加热炉中进行固溶处理,固溶工艺为:在温度为450~460℃条件下保温2h,再升温至470℃保温2~6h,然后进行淬火处理,出炉水冷至室温;
12.七、将步骤六处理后的铝合金挤压材进行张力矫直,然后进行辊式矫直;
13.八、在室温条件下,将步骤七辊式矫直后的铝合金挤压材放入电阻加热炉中加热至温度为115℃~121℃,保温处理4h~7h,然后升温至154℃~161℃,保温处理6h~9h,得
到过时效处理的挤压材,即为一种航空航天用超强高韧耐蚀铝合金挤压材。
14.本发明的有益效果是:
15.本发明通过合金成分优化、铸造质量控制,张力矫直量控制和双级时效,生产出了同时具有抗拉强度高和耐腐性性能优异的铝合金挤压材,并在挤压材淬火后需进行张力拉伸时,将挤压材的拉伸量控制在0.5%~2.0%,既可有效控制残余应力,又可以提高挤压材最终态产品的断裂韧性。本发明制造的挤压材,根据gb/t 228测试,纵向抗拉强度 659-668n/mm2,规定非比例延伸强度632-642n/mm2,断后伸长率11.1-13.2%,抗压屈服强度639-651mpa;根据gb/t 4161测试挤压材的断裂韧性为34.65~35.96mpa
·m1/2
,根据 gb/t 12966-2008测试电导率37.42~37.75%iacs,根据hb 5455测试剥落腐蚀不低于eb 级。
16.本发明制备的铝合金挤压材应用于航空航天领域。
附图说明
17.图1为实施例二步骤二制备的铝合金圆铸锭的金相照片(低倍);
18.图2为实施例二步骤二制备的铝合金圆铸锭的金相照片(高倍);
19.图3为实施例二步骤四得到的退火后的圆铸锭的sem照片;
20.图4为实施例二步骤四得到的退火后的圆铸锭的tem照片;
21.图5为实施例二步骤五制备的铝合金挤压材壁厚上部的低倍金相组织照片;
22.图6为实施例二步骤五制备的铝合金挤压材壁厚上部的高倍金相组织照片;
23.图7为实施例二步骤五制备的铝合金挤压材壁厚中部的低倍金相组织照片;
24.图8为实施例二步骤五制备的铝合金挤压材壁厚中部的高倍金相组织照片;
25.图9为实施例二步骤五制备的铝合金挤压材壁厚下部的低倍金相组织照片;
26.图10为实施例二步骤五制备的铝合金挤压材壁厚下部的高倍金相组织照片;
27.图11为实施例二步骤六双级固溶处理后铝合金挤压材的ebsd照片;
28.图12为实施例二步骤六双级固溶处理后铝合金挤压材的ebsd组织统计分析图;
29.图13为实施例二步骤六双级固溶处理后铝合金挤压材的金相照片;
30.图14为实施例二步骤六双级固溶处理后铝合金挤压材的sem照片;
31.图15为实施例二步骤六双级固溶处理后的铝合金挤压材的tem照片(高倍);
32.图16为实施例二步骤六双级固溶处理后的铝合金挤压材的tem照片(低倍);
33.图17为现有工艺制备的t6态铝合金挤压材的高倍组织照片;
34.图18为现有工艺制备的t6态铝合金挤压材的低倍组织照片;
35.图19为实施例二制备的航空航天用超强高韧耐蚀铝合金挤压材的高倍组织照片;
36.图20为实施例二制备的航空航天用超强高韧耐蚀铝合金挤压材的低倍组织照片。
具体实施方式
37.本发明技术方案不局限于以下所列举的具体实施方式,还包括各具体实施方式之间的任意组合。
38.具体实施方式一:本实施方式一种航空航天用超强高韧耐蚀铝合金挤压材的制备方法,具体按以下步骤进行:
39.一、按照元素质量百分含量为cu:1.8%~2.2%、mg:1.8%~2.6%、zn:8.2%~
9.2%、 zr:0.10%~0.13%、cr:0.02%~0.04%、ti:0.01%~0.04%和余量为al的比例称取铝锭、阴极铜、原生镁锭、锌锭、铝锆合金锭、铝铬中间合金锭和铝钛丝作为原料,然后将原料放入熔炼炉中熔炼,得到铝合金熔液;
40.二、将步骤一得到的铝合金熔液采用半连续铸造工艺铸造成铝合金圆铸锭;
41.三、在室温条件下除去步骤二铸造的铝合金圆铸锭的氧化皮;
42.四、将步骤三处理后的铝合金圆铸锭在温度为420℃~440℃的条件下,保温12h,然后升温至470℃的条件下保温60h,出炉后自然冷却至室温,得到退火后的圆铸锭;
43.五、将退火后的圆铸锭放入感应加热炉中,加热到420℃~440℃,然后采用挤压机进行热挤压,得到铝合金挤压材;
44.六、将步骤五获得的铝合金挤压材放入电阻加热炉中进行固溶处理,固溶工艺为:在温度为450~460℃条件下保温2h,再升温至470℃保温2~6h,然后进行淬火处理,出炉水冷至室温;
45.七、将步骤六处理后的铝合金挤压材进行张力矫直,然后进行辊式矫直;
46.八、在室温条件下,将步骤七辊式矫直后的铝合金挤压材放入电阻加热炉中加热至温度为115℃~121℃,保温处理4h~7h,然后升温至154℃~161℃,保温处理6h~9h,得到过时效处理的挤压材,即为一种航空航天用超强高韧耐蚀铝合金挤压材。
47.本实施方式通过合金成分优化、铸锭质量控制,多级均匀化处理技术、挤压成型技术、强韧化热处理技术,生产出了超强高韧耐蚀铝合金挤压材,本实施方式制造的挤压材,根据gb/t 228测试,纵向抗拉强度659-668n/mm2,规定非比例延伸强度632-642n/mm2,断后伸长率11.1-13.2%,抗压屈服强度639-651mpa;根据gb/t 4161测试挤压材的断裂韧性为34.65~35.96mpa
·m1/2
,根据gb/t 12966-2008测试电导率37.42~37.75%iacs,根据hb 5455测试剥落腐蚀不低于eb级。
48.具体实施方式二:本实施方式与具体实施方式一不同的是:步骤一中按照元素质量百分含量为cu:2.0%、mg:2.0%、zn:8.4%、zr:0.12%、cr:0.02%、ti:0.02%和余量为al的比例称取铝锭、阴极铜、原生镁锭、锌锭、铝锆合金锭、铝铬中间合金锭和铝钛丝作为原料。其它与具体实施方式一相同。
49.具体实施方式三:本实施方式与具体实施方式一或二不同的是:步骤一中熔炼温度为 720~760℃,熔炼时间为5~9h。其它与具体实施方式一或二相同。
50.具体实施方式四:本实施方式与具体实施方式一至三之一不同的是:步骤二中半连续铸造工艺为控制铸造温度为720℃~760℃、铸造速度为22mm/min~32mm/min、冷却水温度为10℃~20℃、冷却水强度为20m3/h~60m3/h。其它与具体实施方式一至三之一相同。
51.具体实施方式五:本实施方式与具体实施方式一至四之一不同的是:步骤二中半连续铸造工艺为控制铸造温度为740℃、铸造速度为26~30mm/min、冷却水温度为16~17℃、冷却水强度为32~50m3/h。其它与具体实施方式一至四之一相同。
52.具体实施方式六:本实施方式与具体实施方式一至五之一不同的是:步骤五中加热到 430℃进行热挤压。其它与具体实施方式一至五之一相同。
53.具体实施方式七:本实施方式与具体实施方式一至六之一不同的是:步骤六中在温度为450℃条件下保温2h,再升温至470℃保温4h。其它与具体实施方式一至六之一相同。
54.具体实施方式八:本实施方式与具体实施方式一至七之一不同的是:步骤七中控
0.028%、ti:0.02%和余量为al的比例称取铝锭、阴极铜、原生镁锭、锌锭、铝锆合金锭、铝铬中间合金锭和铝钛丝作为原料,然后将原料放入熔炼炉中熔炼,熔炼温度为 750℃,熔炼时间为8h,得到铝合金熔液;
72.二、将步骤一得到的铝合金熔液采用半连续铸造工艺铸造成铝合金圆铸锭;其中半连续铸造工艺为:铸造温度为740℃、铸造速度为30mm/min、冷却水温度为17℃、冷却水强度为50m3/h;
73.三、在室温条件下除去步骤二铸造的铝合金圆铸锭的氧化皮;
74.四、将步骤三处理后的铝合金圆铸锭在温度为440℃的条件下,保温12h,然后升温至470℃的条件下保温60h,出炉后自然冷却至室温,得到退火后的圆铸锭;
75.五、将退火后的圆铸锭放入感应加热炉中,加热到430℃,然后采用挤压机进行热挤压,得到铝合金挤压材;
76.六、将步骤五获得的铝合金挤压材放入电阻加热炉中进行固溶处理,固溶工艺为:在温度为450℃条件下保温2h,再升温至470℃保温4h,然后进行淬火处理,出炉水冷至室温;
77.七、将步骤六处理后的铝合金挤压材进行张力矫直,控制张力矫直的拉伸量为1.6%,然后进行辊式矫直;
78.八、在室温条件下,将步骤七辊式矫直后的铝合金挤压材放入电阻加热炉中加热至温度为118℃,保温处理6.5h,然后升温至157℃,保温处理7h,得到过时效处理的挤压材,即为一种航空航天用超强高韧耐蚀铝合金挤压材。
79.将本实施例制备的航空航天用超强高韧耐蚀铝合金挤压材,按照gb/t228测试性能,该挤压材的纵向抗拉强度662n/mm2,规定非比例延伸强度638n/mm2,断后伸长率12.5%,抗压屈服强度643n/mm2,根据gb/t 4161规定测试挤压材的断裂韧性34.92pa
·m1/2
,根据gb/t 12966测试电导率37.64%iacs,根据hb5455规定测试挤压材的剥落腐蚀性能不低于eb级。
80.本实施例步骤二制备的铝合金圆铸锭的金相照片(低倍)如图1所示,铝合金圆铸锭的金相照片(高倍)如图2所示,由图1和图2可知,铸态样品金相组织晶界处四元相特征明显,高倍组织照片表明晶界处存在明显的片层状结构,凝固过程中形成的alznmgcu 四元相与α(al)相形成连续网状的层片状共晶组织分布的晶界,铸态合金中第二相主要包含alznmgcu四元相,少量al2cu及al2cumg相以及富fe相,整体上晶粒尺寸均匀。
81.7000系合金均匀化处理的目的在于促进粗大的一次凝固析出相回溶,此外需在高温下促进al3zr粒子的弥散析出,该相在后续的变形加工及热处理过程中能够钉扎晶界,抑制再结晶,提高合金性能。al3zr形核率较高的温度区间为420~450℃。因此为了兼顾al3zr 粒子的弥散析出以及一次凝固相的回溶,进行420℃~440℃保温12h的第一级均匀化退火处理后,进行470℃的保温60h的高温处理,出炉后自然冷却至室温。
82.本实施例步骤四得到的退火后的圆铸锭的sem照片如图3所示,退火后的圆铸锭的 tem照片如图4所示,由图3可知,均匀化处理后组织中析出相回溶充分,铸态合金片层状的共晶组织完全消失仅有零星的白色相残留,通过能谱分析表明其为富fe相,富fe 相的数量与分布并不随着均匀化时间的延长而有显著改变,均匀化退火后,合金的晶粒尺寸未发生显著变化。由图4可见,铸锭均匀化过程中析出大量al3zr球形粒子,与基体共格,强烈钉扎
位错及晶界,阻碍位错运动和晶界迁移,具有强烈抑制热加工过程中再结晶的作用,提高挤压材最终状态的综合性能。
83.对铝合金挤压材纵截面进行金相组织观察,本实施例步骤五制备的铝合金挤压材壁厚上部的低倍金相组织照片如图5所示,步骤五制备的铝合金挤压材壁厚上部的高倍金相组织照片如图6所示,步骤五制备的铝合金挤压材壁厚中部的低倍金相组织照片如图7所示,步骤五制备的铝合金挤压材壁厚中部的高倍金相组织照片如图8所示,步骤五制备的铝合金挤压材壁厚下部的低倍金相组织照片如图9所示,步骤五制备的铝合金挤压材壁厚下部的高倍金相组织照片如图10所示,由图中可以看出三个位置的金相组织相似,均有流线形特征,黑色第二相沿挤压方向分布。
84.靠近表面由于变形程度更大,晶粒较小,形态很难辨认;靠近中部金相组织,同样有流线形特征,一些黑色第二相沿挤压方向分布,在高倍下可观察到沿挤压方向存在尺寸为 8~15μm的小晶粒,可能为挤压变形中动态再结晶的结果。
85.本实施例采用双级淬火工艺,第一级固溶温度较低,可以释放较多的形变储能,降低高温固溶处理的再结晶驱动力,使挤压材保留较高比例的变形组织,第二级采用高温处理,保证合金第二相的充分回溶到基体,提高挤压材的强度和断裂韧性,经单级固溶后的再结晶组织占比为33%~45%,经双级固溶后的再结晶组织占比为13%~25%,明显降低。
86.本实施例步骤六双级固溶处理后铝合金挤压材的ebsd照片如图11,步骤六双级固溶处理后铝合金挤压材的ebsd组织统计分析图如图12所示;由图中可以看出再结晶组织铸造占比为18.5%。
87.本实施例步骤六双级固溶处理后铝合金挤压材的金相照片如图13所示,本实施例步骤六双级固溶处理后铝合金挤压材的sem照片如图14所示,由图可知,经双级固溶处理,第二相回溶充分,仅剩余少量富fe第二相。
88.本实施例步骤六双级固溶处理后铝合金挤压材的tem照片(高倍)如图15,本实施例步骤六双级固溶处理后铝合金挤压材的tem照片(低倍)如图16所示,由图可知固溶处理后的铝合金挤压材组织均匀,晶粒内部有al3zr、al3ti弥散相,尺寸约10~15nm。 al3zr、al3ti起到强烈钉扎位错的作用,有效提高合金的强度。
89.现有工艺制备的t6态铝合金挤压材的高倍组织照片如图17,现有工艺制备的t6态铝合金挤压材的低倍组织照片如图18,
90.本实施例制备的航空航天用超强高韧耐蚀铝合金挤压材的高倍组织照片如图19,本实施例制备的航空航天用超强高韧耐蚀铝合金挤压材的低倍组织照片如图20。由于双级时效处理,当晶内析出相为更多、更细小的gp区和小尺寸的η
′
相时,虽能获得更高强度,但是晶界析出相尺寸不大且连续时,则得不到理想的抗腐蚀性能;当双级时效后合金晶界上分布着断续的粗大沉淀相,这种晶界组织能显著提高合金抗腐蚀性能,但要牺牲较大的材料强度。因此为了解决强度和抗应力腐蚀性能之间的矛盾,同时兼顾挤压材的电导率和断裂韧性,本发明采用了传统半连续铸造方式,得到均匀晶粒组织,挤压后,通过减少张力拉伸量,加强辊式矫直的方式,保证挤压材的外形尺寸和残余应力,配合合适的双级时效工艺,保证处理后晶内和晶界析出相的尺寸及分布状态,达到理想的性能匹配效果,以满足更高的服役条件。
再多了解一些
本文用于企业家、创业者技术爱好者查询,结果仅供参考。