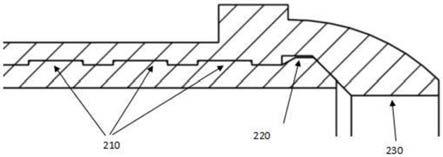
1.本实用新型属于管路件技术领域,更具体地说,涉及一种滚压式球面密封管路件。
背景技术:
2.氢能具有来源多样性、清洁环保、可再生、转化效率高等优点,被誉为21世纪最具发展前景的二次能源。氢能源汽车在加注、储存、输送和使用时,都离不开具有耐腐蚀、耐高压特性的金属管路连接件。
3.氢燃料电池汽车车载供氢系统设计中,经常因为氢气压力高、分子小易泄漏、金属材料的氢脆和汽车运行时苛刻的外部环境(比如外部环境的温度变化,崎岖路段颠簸造成的振动)而担忧。
4.如果车载供氢系统的管路接头发生泄漏,可能会引起严重的安全事故,如何正确选择安全的连接形式是一直困扰着设计者的问题。
5.一般来说,燃料电池汽车车载供氢系统的连接需要采用全金属密封结构,避免使用非金属密封圈面。非金属密封圈面的耐温范围比较局限,加氢机给燃料电池汽车加氢的时候,氢瓶和管路的温度会上升,而随着燃料电池动力系统持续的消耗氢气,氢气金属导管温度会降低,所以选择密封圈的材质时需要考虑耐高低性能。如果车载供氢系统附近发生火烧事故,非金属密封材料会失效,造成氢气大量泄漏,会加剧事故程度。
6.非金属密封圈还存在老化问题,车载供氢系统应用中氢气的压力、温度变化、外部环境的臭氧、紫外线等很多因素会加剧其老化。而这样的老化程度和速度是难以定量和预判的,不及时的更换会造成很大的安全隐患,定期的更换又会显著增加维修保养的时间和金钱成本,为氢燃料电池汽车的民用大范围推广造成障碍。氢气压力的快速降低还有使非金属密封圈产生裂纹的风险,从而造成密封失效,产生严重事故。
7.高压氢气管路成型过程不可热加工,管路件与金属导管的连接不可采用焊接工艺,焊接对材料的抗氢脆性能会产生负面影响。316奥氏体不锈钢的面心立方体晶体结构抗氢脆性能是非常好的,焊接过程的二次热加工离焊针近的位置熔融钢水温度高,离焊针远的位置熔融钢水温度低,造成焊缝的化学成分不均匀,铬镍含量比较高的区域会生产铁素体,焊接过程产生的铁素体对氢脆敏感。焊接过程中的二次热加工还会造成未熔融的热影响区晶体结构(晶粒)的大小发生变化,加剧氢脆。
8.如果供氢管路系统对清洁度要求高也不可采用焊接工艺,经长期实践验证,焊接管路长期使用后易发生焊料掉落,如果进入系统内,会污染氢液。
技术实现要素:
9.1、要解决的问题
10.针对现有技术中存在的问题,本实用新型提供一种滚压式球面密封管路件,采用纯金属密封面结构与内滚压连接方式,机械加工的密封面较传统金属导管末端进行冷墩产生的密封面,提高了密封性和复装性能,解决了冷墩(或其他方式对金属金属导管直接进行
的机械成型)后形成的球面密封面的尺寸一致性和材质疏密稳定性难以控制的问题;而金属金属导管与金属管路件的内滚压连接方式相较传统焊接方式,性能稳定、工艺易控制、加工效率高、质量一致性好、产生缺陷少、易检测等优点,避免了焊接后金属导管材料的抗氢脆性能的下降。
11.2、技术方案
12.为解决上述问题,本实用新型采用如下的技术方案。
13.一种滚压式球面密封管路件,包括金属导管和套接在所述金属导管上的金属管套,所述金属管套与金属导管相套接的一端内侧壁设置有若干环槽,经滚压连接工艺所述环槽内被所述金属导管的金属导管材料充分填充。
14.其优选的技术方案为:
15.如上所述的一种滚压式球面密封管路件,所述环槽内金属导管的金属导管材料填充料率为85~100%。
16.如上所述的一种滚压式球面密封管路件,所述环槽在所述金属管套内侧壁上等间距分布。
17.如上所述的一种滚压式球面密封管路件,所述环槽设置有3个,3个所述环槽的宽度和深度均相同。
18.如上所述的一种滚压式球面密封管路件,所述金属管套与金属导管相套接的一端内侧壁还设置有堆料槽,所述堆料槽的径向方向深度大于所述环槽的径向方向深度。
19.如上所述的一种滚压式球面密封管路件,所述金属导管的外壁与所述环槽之间形成有6个垂直密封面和3个水平密封面。
20.3、有益效果
21.相比于现有技术,本实用新型的有益效果为:
22.(1)本实用新型中,金属管套与金属导管之间的密封面较传统金属导管末端进行冷墩产生的密封面,提高了密封性和复装性能,解决了冷墩(或其他方式对金属金属导管直接进行的机械成型)后形成的球面密封面的尺寸一致性和材质疏密稳定性难以控制的问题;
23.(2)本实用新型属中,金属导管与金属管路件的内滚压连接工艺相较焊接工艺,性能稳定、工艺易控制、加工效率高、质量一致性好、产生缺陷少、易检测等优点,避免了焊接后金属导管材料的抗氢脆性能的下降;
24.(3)本实用新型在环槽的基础上额外设置一个堆料槽,堆料槽不参与连接,它被设计的径向方向深度更大,进而可以在填充滚压过程中向金属管套球型密封面端轴向延伸的多余材料,将金属导管的轴向伸长控制在堆料槽的长度范围内,避免金属导管材料伸长超过过孔,形成材料压延缺陷,如圆凸台、飞边等。
附图说明
25.图1为本实用新型其中一个实施例中的一种滚压式球面密封管路件的整体结构示意图;
26.图2为本实用新型其中一个实施例中的一种滚压式球面密封管路件的部分结构示意图;
27.图中:100、金属导管;200、金属管套;210、环槽;220、堆料槽;230、过孔。
具体实施方式
28.下面结合具体实施例和附图对本实用新型进一步进行描述。
29.实施例1
30.氢燃料电池汽车车载供氢系统设计中,经常因为氢气压力高、分子小易泄漏、金属材料的氢脆和汽车运行时苛刻的外部环境(比如外部环境的温度变化,崎岖路段颠簸造成的振动)而担忧。如果车载供氢系统的管路接头发生泄漏,可能会引起严重的安全事故,因此如何正确选择安全的连接形式是一直困扰着设计者的问题。燃料电池汽车车载供氢系统的连接需要采用全金属密封结构,避免使用非金属密封圈面。这是因为其一:非金属密封圈面的耐温范围比较局限;其二,非金属密封圈还存在老化问题。
31.由于高压氢气管路成型过程不可热加工,管路件与金属导管的连接不可采用焊接工艺,焊接对材料的抗氢脆性能会产生负面影响。如果供氢管路系统对清洁度要求高也不可采用焊接工艺,经长期实践验证,焊接管路长期使用后易发生焊料掉落,如果进入系统内,会污染氢液。
32.综上,本设计提出采用纯金属密封面结构与内滚压连接工艺的氢燃料电池汽车车载供氢系统滚压式球面密封管路件设计方案,其优点有:
33.机械加工的密封面较传统金属导管末端进行冷墩产生的密封面,提高了密封性和复装性能,解决了冷墩(或其他方式对金属金属导管直接进行的机械成型)后形成的球面密封面的尺寸一致性和材质疏密稳定性难以控制的问题。
34.金属金属导管与金属管路件的内滚压连接工艺相较焊接工艺,性能稳定、工艺易控制、加工效率高、质量一致性好、产生缺陷少、易检测等优点,避免了焊接后金属导管材料的抗氢脆性能的下降。
35.实施例2
36.基于实施例1中的纯金属密封面结构与内滚压连接工艺的氢燃料电池汽车车载供氢系统滚压式球面密封管路件设计思路,本实施例提供一种滚压式球面密封管路件,请参阅图1~2,包括金属导管100和套接在所述金属导管100上的金属管套200。
37.所述金属管套200与金属导管100相套接的一端内侧壁设置有若干环槽210,经滚压连接工艺所述环槽210内被所述金属导管100的金属导管100材料充分填充,所述环槽210内金属导管100的金属导管100材料填充料率为85~100%。
38.对金属导管100而言,本实施例采用内滚压工艺对金属导管100内壁经旋转滚压,壁厚减薄为常规金属导管100壁壁厚的1/4~1/3),方便金属导管100壁厚材料填充到环槽210中。
39.对环槽210而言,所述环槽210在所述金属管套200内侧壁上等间距分布。所述环槽210设置有3个,3个所述环槽210的宽度和深度均相同。
40.进一步的,所述金属导管100的外壁与所述环槽210之间形成有6个垂直密封面和3个水平密封面,保证了连接可靠性。
41.实施例3
42.与实施例2基本相同。由于经滚压连接工艺所述环槽210内被所述金属导管100的
金属导管100材料充分填充,这就必然会导致新的问题。当述金属导管100的金属导管100材料在所述环槽210内充分填充后还有多余残量时,势必会导致金属导管100材料伸长超过金属管套200的过孔230。基于上述理由,本实施例在实施例2的基础上,在所述金属管套200与金属导管100相套接的一端内侧壁还设置有堆料槽220,所述堆料槽220的径向方向深度大于所述环槽210的径向方向深度。
43.本实施例中,堆料槽220不参与连接,它被设计的径向方向深度更大,进而可以在填充滚压过程中向金属管套200球型密封面端轴向延伸的多余材料,将金属导管100的轴向伸长控制在堆料槽220的长度范围内,避免金属导管100材料伸长超过过孔230,形成材料压延缺陷,如圆凸台、飞边等。
44.本实用新型所述实例仅仅是对本实用新型的优选实施方式进行描述,并非对本实用新型构思和范围进行限定,在不脱离本实用新型设计思想的前提下,本领域工程技术人员对本实用新型的技术方案作出的各种变形和改进,均应落入本实用新型的保护范围。
再多了解一些
本文用于企业家、创业者技术爱好者查询,结果仅供参考。