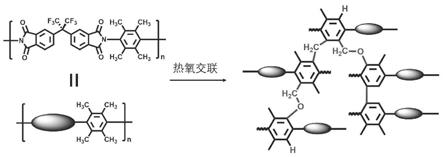
1.本发明属于聚合物分离膜的技术领域,尤其涉及一种热交联聚合物分离膜的制备方法及应用。
背景技术:
2.沼气是有机物发酵而产生的一种环保能源,与煤炭、石油以及页岩气等能源相比,其绿色经济可行性更为优越,而且可以实现碳“零排放”。研究复杂成分沼气的分离纯化对我国具有重要意义。此外,沼气中总是同时存在二氧化碳(co2)和甲烷(ch4) 两种成分,co2不但降低了天然气的热值,而且还容易腐蚀运输管路。因此,研究沼气中co2和ch4的分离纯化对获得高热值的能源也非常重要。与传统热驱动的分离工艺相比,聚合物气体分离膜技术具有高效、节能、及操作简便等优点。聚酰亚胺膜(pi)具有热和化学稳定性好、内在渗透选择性系数好的特点,在co2和ch4分离中的应用已经得到广泛研究。然而,高压 co2进料条件下往往会引起聚合物膜塑化。塑化是指气体分子在聚合物膜内吸附“溶”,在一定的温度和压力下,这些气体分子会破坏大分子链的堆砌,使聚合物膜发“溶胀”,导致膜的分离选择性系数大大降低,极大地削减了分离膜的使用寿命。
3.由于交联可以抑制聚合物膜中的过度溶胀和链段运动和迁移,所以交联被认为是提高聚酰亚胺膜抗塑化能力的有效策略。通常,交联方法可以分为化学交联和物理交联。化学交联是通过小分子二醇或二胺等化学试剂与聚酰亚胺发生化学反应来实现,多数具有改性的抗塑化性能的聚酰亚胺膜是由脂肪族二胺(c
2-c6)或丙二醇交联形成的。这些形成交联键的化学反应一般是可逆的,在高温、腐蚀性和酸性等极端条件下容易被破坏。作为一种可靠的替代方式,热交联可以通过不可逆反应生成稳定的共价交联键来提高聚酰亚胺膜的抗塑化能力。已经有研究者提出了脱羧诱导的交联机理以提高均质膜的抗塑化性能,并将其应用到含羧酸的聚酰亚胺膜在389℃下的交联以及羧基化自具微孔聚合物膜在375℃下的交联。虽然具有无缺陷的薄选择层的非对称膜也可以进行脱羧交联,但是这种高于聚酰亚胺玻璃化转变温度的热处理温度容易导致纳米多孔过渡层的坍塌,从而导致2-4倍的产率损失。脱羧交联的高温反应条件使得开发具有高选择性系数的、稳定的商业分离膜具有挑战性。
技术实现要素:
4.为解决上述技术问题,本发明提供了一种热交联聚合物分离膜的制备方法及应用。
5.一种热交联聚合物分离膜的制备方法,包括以下步骤:
6.s1、在第一极性有机溶剂中,将含苄甲基的二胺单体与二酐单体在催化剂的作用下(160~230℃)反应,得到聚酰亚胺;
7.s2、将s1中所述聚酰亚胺溶于第二极性有机溶剂中,形成3wt%~40 wt%的成膜溶液,将所述成膜溶液进行成膜处理,得到中间体膜;所述中间体膜为平板均质膜或中空纤
维膜;
8.s3、向s2中所述中间体膜通入氩气和氧气的混合吹扫气,进行热氧化交联反应,得到所述热交联聚合物分离膜。
9.在本发明的一个实施例中,s1中,所述含苄甲基的二胺单体选自结构式为nh
2-r
’‑
nh2的单体,其中r’选自以下结构基团:
[0010][0011]
在本发明的一个实施例中,s1中,所述二酐单体选自结构式为的单体,其中r选自以下结构基团:
[0012][0013]
在本发明的一个实施例中,s1中,所述第一极性有机溶剂为n,n-二甲基甲酰胺或/和n-甲基吡咯烷酮。
[0014]
在本发明的一个实施例中,s2中,所述第二极性有机溶剂为n,n-二甲基甲酰胺、n-甲基吡咯烷酮、氯仿和四氢呋喃中的一种或多种。
[0015]
在本发明的一个实施例中,s2中,所述中间体膜为平板均质膜时,所述中间体膜为平板均质膜时,所述成膜处理包括以下步骤:将所述成膜溶液均匀涂覆基体表面,溶剂挥发获得均质膜,将所得均质膜干燥即得所述平板均质膜时。
[0016]
在本发明的一个实施例中,s2中,所述中间体膜为平板均质膜时,所述中间体膜为平板均质膜时,所述成膜处理的具体步骤(采用溶液浇铸法制备均质平板膜):利用ptfe过滤器去除成膜溶液中的不溶杂质。随后,将滤液静置去除气泡,倒入的玻璃皿中,盖上玻璃片,玻璃皿置于水平的台面上,室温下溶剂自然挥发以获得均质膜,最后将揭下来的膜置于真空干燥箱中干燥,去除膜内痕量溶剂得到所述平板均质膜。此方法制备的平板均质膜的膜厚度为60-120μm。
[0017]
在本发明的一个实施例中,s2中,所述中间体膜为中空纤维膜时,所述成膜处理包括以下步骤:将所述成膜溶液通过筛网过滤,于15-50℃下进行脱气,将脱气后的成膜溶液进行纺丝,形成所述中空纤维膜。
[0018]
在本发明的一个实施例中,所述溶液纺丝处理步骤为将芯液流体通过同心孔喷丝头的中心孔挤出,而脱气后的滤液通过所述同心孔喷丝头的环状间隙挤出。
[0019]
在本发明的一个实施例中,s3中,所述氩气或氮气和氧气中的氧含量为10ppm-800000ppm,
[0020]
在本发明的一个实施例中,s3中,所述热氧化交联反应的温度为250-450 ℃,时间为0.1-100h。
[0021]
本发明提供了所述的制备方法制备得到的热交联聚合物分离膜。
[0022]
本发明提供了所述的热交联聚合物分离膜在分离混合气体中的应用;所述混合气
体为co2和ch4的混合或者h2和ch4的混合。
[0023]
在本发明的一个实施例中,当混合气体中含有甲烷和二氧化碳时,二氧化碳渗透系数为100barrer,二氧化碳塑化点为50大气压以上,混合气体二氧化碳甲烷分离选择性系数达到70以上;当混合气体为氢气和甲烷时,氢气渗透系数为200-600barrer,氢气和甲烷选择性系数达到100以上。
[0024]
本发明还提供所述的热交联聚合物分离膜在制备耐塑化性气体分离膜、有机液体中的小分子分离膜或耐溶胀纳滤膜中的应用。
[0025]
本发明的上述技术方案相比现有技术具有以下优点:
[0026]
现有技术中报道的聚合物热氧交联都倾向于在高温(375-385℃)下发生以获得高交联度,这个过程涉及到骨架结构的不可控氧化降解。与此不同的是,本发明建立了氧诱导苯环上甲基取代基脱氢的策略,以在温和的条件下在苄基聚酰亚胺体系中构建交联网络。
[0027]
本发明通过设计含苄基的聚酰亚胺结构,大大降低了热处理的温度和时间,节约能耗,并且很好地保存了聚合物原始的主链刚性结构以及高的机械强度。
[0028]
本发明含苄基的聚酰亚胺合成过程简单,无需特殊的结构设计,可以大大降低合成成本。
[0029]
本发明通过调整热氧处理时间,该类膜的分离选择性系数大幅度提高,超过2008年的分离性能上限。
[0030]
本发明由于采用热氧交联的方式,所制备的该类膜材料具有超交联的结构,限制了链段运动,分离膜具有很好的耐时间老化和抗气体塑化的特性。
[0031]
本发明提供的该类混合基质膜制备工艺简单可控,重复性好,可以以平板膜和中空纤维膜的形式放大,适于规模化工业生产。
附图说明
[0032]
为了使本发明的内容更容易被清楚的理解,下面根据本发明的具体实施例并结合附图,对本发明作进一步详细的说明,其中
[0033]
图1是本发明的实施例1中的含苄基聚酰亚胺dupi的化学式;
[0034]
图2是本发明的实施例6中含苄基聚酰亚胺膜在不同气氛下处理后的溶解状态;
[0035]
图3是本发明的实施例6中含苄基聚酰亚胺热氧交联膜的核磁及xps 表征;
[0036]
图4是本发明实施例1-6中含苄基聚酰亚胺热氧交联膜的机械强度曲线;
[0037]
图5是本发明实施例1-6中含苄基聚酰亚胺热氧交联膜与其他交联膜对 co2/ch4分离性能比较;
[0038]
图6是本发明实施例1-6中含苄基聚酰亚胺热氧交联膜的二氧化碳塑化压力表征及混合气体选择性系数表征;
[0039]
图7是本发明的实施例6中含苄基聚酰亚胺热氧交联膜的co2和ch4混气综合分离性能比较;
[0040]
图8是本发明热交联苄基聚酰亚胺的交联结构。
具体实施方式
[0041]
下面结合附图和具体实施例对本发明作进一步说明,以使本领域的技术人员可以
更好地理解本发明并能予以实施,但所举实施例不作为对本发明的限定。
[0042]
实施例1
[0043]
合成dupi:向装有磁力搅拌子的三颈烧瓶中加入30mmol的苄基二胺单体,氮气保护下,加入适量超干n-甲基吡咯烷酮溶剂,搅拌至所有固体粉末被溶解,再加入30mmol 4,4'-(六氟异亚丙基)二邻苯二甲酸酐,补加超干n-甲基吡咯烷酮溶剂得到质量浓度为20wt%的均一混合溶液,搅拌预聚12h。此过程中,二酐与二胺发生缩合反应开环生成聚酰胺酸。随后,在体系中加入5-10 ml无水甲苯,并为三颈烧瓶侧颈加装分水器、球形冷凝管,逐步升高温度至200℃,恒温反应5h,聚酰胺酸转化为聚酰亚胺过程中生成的水通过与甲苯共沸蒸馏出去,反应正向进行。待反应结束后,将粘稠的反应产物溶液缓缓倒入500ml无水甲醇中析出沉淀。经过滤、无水乙醇洗涤沉淀后,在150℃真空烘箱干燥24h除去痕量残留溶剂,即可得到苄基聚酰亚胺dupi(图1)。
[0044]
均质膜的制备:取苄基聚酰亚胺材料溶于n,n-二甲基甲酰胺中,搅拌过夜,放置24h脱气泡后得到5wt%的成膜溶液。取配制好聚合物的成膜溶液,通过流延干燥的方式形成薄膜,将所述薄膜于120℃真空干燥24h以上,得到聚合物共混膜。
[0045]
热氧交联苄基聚酰亚胺膜:将未处理的均质膜放入管式炉中,用石英板固定,将管式炉设置为密闭环境,通入21.0vol%氧含量的氩气/氧气混合吹扫气,预吹扫30min后,从室温以5-20℃/min分别升温至250℃,在目标温度下恒温24h,进行不同程度的热氧化交联反应,整个过程中混合气体的流速保持 200ml/min。其中该类膜氢气渗透系数可达到500barrer,氢气甲烷分离选择性系数系数达到60,二氧化碳渗透系数为300barrer,二氧化碳甲烷选择性系数为40。
[0046]
实施例2
[0047]
苄基聚酰亚胺合成方式及膜制备方法与实例1相同,不同的是热氧处理的温度为300℃,5h。其中该类膜氢气渗透系数可达到330barrer,氢气甲烷分离选择性系数达到85,二氧化碳渗透系数为200barrer,二氧化碳甲烷选择性系数系数为50。
[0048]
实施例3
[0049]
苄基聚酰亚胺合成方式及膜制备方法与实例1相同,不同的是热氧处理的温度为300℃,10h。其中该类膜氢气渗透系数可达到330barrer,氢气甲烷分离选择性系数达到85,二氧化碳渗透系数为200barrer,二氧化碳甲烷选择性系数系数为50。
[0050]
实施例4
[0051]
苄基聚酰亚胺合成方式及膜制备方法与实例1相同,不同的是热氧处理的温度为300℃,24h。其中该类膜氢气渗透系数可达到170barrer,氢气甲烷分离选择性系数达到200,二氧化碳渗透系数为100barrer,二氧化碳甲烷选择性系数为78,二氧化碳高压塑化点为50bar以上,对二氧化碳甲烷混合气体的选择性系数系数达到70以上。
[0052]
实施例5
[0053]
苄基聚酰亚胺合成方式及膜制备方法与实例1相同,不同的是热氧处理的温度为330℃,5h。其中该类膜氢气渗透系数为90barrer,氢气甲烷分离选择性系数达到400以上,二氧化碳渗透系数为30barrer,二氧化碳甲烷选择性系数为100以上。
[0054]
实施例6
[0055]
苄基聚酰亚胺合成方式及膜制备方法与实例1相同,不同的是热氧处理的温度为
350℃,1h。其中该类膜氢气渗透系数可达到390barrer,氢气甲烷分离选择性系数达到130,二氧化碳渗透系数为230barrer,二氧化碳甲烷选择性系数为55。
[0056]
实施例7
[0057]
苄基聚酰亚胺合成方式及膜制备方法与实例1相同,不同的是热氧处理的温度为370℃,10min。其中该类膜氢气渗透系数可达到300barrer,氢气甲烷分离选择性系数达到70,二氧化碳渗透系数为180barrer,二氧化碳甲烷选择性系数为45。
[0058]
实施例8
[0059]
苄基聚酰亚胺合成方式及膜制备方法与实例1相同,不同的是热氧处理的温度为410℃,10min。其中该类膜氢气渗透系数可达到500barrer,氢气甲烷分离选择性系数达到79,二氧化碳渗透系数为290barrer,二氧化碳甲烷选择性系数为46。
[0060]
实施例9
[0061]
苄基聚酰亚胺合成方式实例1相同,不同的是膜材料的制备,中空纤维膜的制备:取苄基聚酰亚胺材料(30wt%)溶于n,n-二甲基甲酰胺(50%)、四氢呋喃(10wt%)及乙醇(10wt%)的混合溶液中将成膜溶液通过筛网过滤,将滤液转移至膜液罐中,将所述滤液在50℃的温度下进行脱气;将脱气后的滤液通过具有中心孔的同心孔喷丝头进行纺丝处理,其中芯液流体通过喷丝头的中心孔挤出,脱气后的滤液通过环状间隙挤出,形成表面致密中空纤维膜。
[0062]
膜的热处理方式:将未处理的均质膜放入管式炉中,用316l不锈钢管固定,将管式炉设置为密闭环境,通入21.0vol%氧含量的氩气/氧气混合吹扫气,预吹扫30min后,从室温以20℃/min分别升温至300℃,在目标温度下恒温10 h,进行不同程度的热氧化交联反应。整个过程中混合气体的流速保持200 ml/min。
[0063]
其中该类膜氢气渗透量达到120gpu,氢气甲烷分离选择性系数达到50,二氧化碳渗透系数为70gpu,二氧化碳甲烷选择性系数为30。
[0064]
显然,上述实施例仅仅是为清楚地说明所作的举例,并非对实施方式的限定。对于所属领域的普通技术人员来说,在上述说明的基础上还可以做出其它不同形式变化或变动。这里无需也无法对所有的实施方式予以穷举。而由此所引申出的显而易见的变化或变动仍处于本发明创造的保护范围之中。
再多了解一些
本文用于企业家、创业者技术爱好者查询,结果仅供参考。