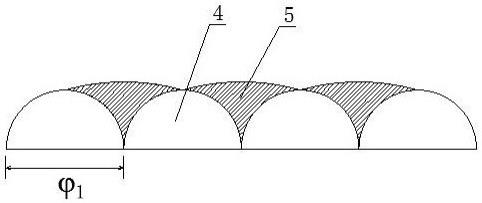
1.本发明属于激光熔覆技术领域,尤其是涉及一种双光头激光熔覆成形工艺。
背景技术:
2.激光熔覆技术是一种新型表面改性技术,是指在基材表面添加金属粉末,在激光束作用下将两者加热并熔化,光束移开后冷却形成与基体材料呈冶金结合的表面涂层,从而显著改善基体表面耐磨、耐蚀、耐热、抗氧化及电气特性等的一种表面强化方法。
3.搭接率是激光熔覆成形技术中一个重要的参数,搭接率的数值决定成形件表面的宏观平整度。目前,激光熔覆的涂层搭接率大多为30%-60%,搭接率过低,熔覆层有效厚度过低,会导致其表面的平整度较差,后续机械加工量增大;提高搭接率虽然可以提高有效厚度和最终成形件表面的平整度,但会导致工作效率低下,且仍然需要后续的机械加工才能使表面光滑平整。
4.此外,现阶段常用的熔覆成形设备,大多采用一个激光熔覆头,针对需要得到有效厚度较高的熔覆层,往往需要进行多层叠加熔覆,即采用单层熔覆后折返再次叠加熔覆,不但生产效率及其低下,且熔覆效果很不理想。
技术实现要素:
5.本发明要解决的问题是提供一种可增加熔覆层有效厚度,减少后续机械加工,减缓冷却时间,提高工作效率的双光头激光熔覆成形工艺。
6.为解决上述技术问题,本发明采用的技术方案是:一种双光头激光熔覆成形工艺,其步骤为:步骤一、将激光头ⅰ和激光头ⅱ的环向相对位置设置为0-180度;步骤二、所述激光头ⅰ在基体上形成螺旋状涂层ⅰ,所述涂层ⅰ的螺纹ⅰ与基体接触位置截面长度为φ1;步骤三、所述激光头ⅱ在两个相邻螺纹ⅰ之间形成螺纹ⅱ,所述螺纹ⅱ组成螺旋状涂层ⅱ;步骤四、所述涂层ⅰ和涂层ⅱ形成最终熔覆层。
7.优选地,所述涂层ⅰ的搭接率为0%时,所述激光头ⅰ的横移螺距为φ2,所述激光头ⅱ的横移螺距为φ3,其中φ2=φ3=φ1,所述激光头ⅰ和激光头ⅱ的横向相对位置为0.5φ1,所述涂层ⅱ的螺纹ⅱ用于填充涂层ⅰ相邻螺纹ⅰ之间的空位,使得最终熔覆层表面平整。
8.优选地,所述激光头ⅰ参数为:激光功率4000-10000w,线速度5-30m/min,光斑直径2-5mm,送粉速度30-60g/min;激光头ⅱ参数为:激光功率2000-4000w,线速度5-30m/min,光斑直径1-3mm,送粉速度10-40g/min。
9.上述工艺通过两束激光空间叠加、能力匹配的方式,可以将搭接率最低降低为0%,生产效率显著提高;激光头ⅱ专用于覆盖涂层ⅰ相邻螺纹ⅰ之间的波谷,可以降低最终涂层的表面粗糙度,提高有效厚度;两束激光同时作用下,后一束激光可以起到缓冷的作用,防
止涂层开裂。
10.优选地,所述涂层ⅰ和涂层ⅱ互相的搭接率为30%-60%时,所述激光头ⅰ和激光头ⅱ的横向相对位置为(1-搭接率)*φ1,该激光头ⅰ和激光头ⅱ的横移螺距为2*(1-搭接率)*φ1,所述涂层ⅱ的螺纹ⅱ与涂层ⅰ的螺纹ⅰ尺寸相同,二者间隔设置得到最终熔覆层。
11.优选地,所述激光头ⅰ和激光头ⅱ的参数为:激光功率4000-10000w,线速度5-30m/min,光斑直径2-5mm,送粉速度30-60g/min。上述工艺在搭接率小于50%的情况下,横向螺距更大,熔覆效率就会更高;同时也可以起到缓冷左右,抑制涂层开裂。
附图说明
12.下面通过参考附图并结合实例具体地描述本发明,本发明的优点和实现方式将会更加明显,其中附图所示内容仅用于对本发明的解释说明,而不构成对本发明的任何意义上的限制,在附图中:图1是本发明双光头的环向位置示意图图2是本发明实施例1的熔覆过程示意图图3是本发明实施例1最终熔覆层的截面图图4是本发明实施例2的熔覆过程示意图图5是本发明实施例2最终熔覆层的截面图图中:1、激光头ⅰ;2、激光头ⅱ;3、基体;4、涂层ⅰ;5、涂层ⅱ。
具体实施方式
13.如图1所示,本发明一种双光头激光熔覆成形工艺,其步骤为:步骤一、将激光头ⅰ1和激光头ⅱ2的环向相对位置设置为0-180度;步骤二、激光头ⅰ1在基体3上形成螺旋状涂层ⅰ4,涂层ⅰ4的螺纹ⅰ与基体3接触位置截面长度为φ1;步骤三、激光头ⅱ2在两个相邻螺纹ⅰ之间形成螺纹ⅱ,螺纹ⅱ组成螺旋状涂层ⅱ5;步骤四、涂层ⅰ4和涂层ⅱ5形成最终熔覆层。
14.实施例1:如图2和图3所示,涂层ⅰ4的搭接率为0%时,激光头ⅰ1的横移螺距(基体3旋转一圈,激光头ⅰ1横向平移的距离)为φ2,激光头ⅱ2的横移螺距为φ3,其中,φ2=φ3=φ1,激光头ⅰ1和激光头2ⅱ的横向相对位置为0.5φ1,涂层ⅱ5的螺纹ⅱ用于填充涂层ⅰ4相邻螺纹ⅰ之间的空位,使得最终熔覆层表面平整。
15.其中,激光头ⅰ1参数为:激光功率6000w,线速度20m/min,光斑直径2mm,送粉速度30g/min;激光头ⅱ2参数为:激光功率2000w,线速度20m/min,光斑直径1mm,送粉速度20g/min。
16.上述工艺通过两束激光空间叠加、能力匹配的方式,可以将搭接率最低降低为0%,生产效率显著提高;激光头ⅱ2专用于覆盖涂层ⅰ4相邻螺纹ⅰ之间的波谷,可以降低最终涂层的表面粗糙度,提高有效厚度;两束激光同时作用下,后一束激光可以起到缓冷的作用,
防止涂层开裂。
17.实施例2:如图4和图5所示,涂层ⅰ4和涂层ⅱ5互相的搭接率为30%-60%时(即激光头ⅰ1形成1,3,5,7
…
涂层,激光头ⅱ2形成2,4,6,7
…
涂层),激光头ⅰ1和激光头ⅱ2的横向相对位置为(1-搭接率)*φ1,该激光头ⅰ1和激光头ⅱ2的横移螺距为2*(1-搭接率)*φ1,涂层ⅱ5的螺纹ⅱ与涂层ⅰ4的螺纹ⅰ尺寸相同,二者间隔设置得到最终熔覆层。
18.其中,激光头ⅰ1和激光头ⅱ2的参数为:激光功率6000w,线速度20m/min,光斑直径2mm,送粉速度30g/min。
19.与实施例1相比,上述工艺在搭接率小于50%的情况下,横向螺距更大,熔覆效率就会更高;同时也可以起到缓冷左右,抑制涂层开裂。
20.以上对本发明的实施例进行了详细说明,但所述内容仅为本发明的较佳实施例,不能被认为用于限定本发明的实施范围。凡依本发明范围所作的均等变化与改进等,均应仍归属于本专利涵盖范围之内。
技术特征:
1.一种双光头激光熔覆成形工艺,其特征在于:其步骤为:步骤一、将激光头ⅰ和激光头ⅱ的环向相对位置设置为0-180度;步骤二、所述激光头ⅰ在基体上形成螺旋状涂层ⅰ,所述涂层ⅰ的螺纹ⅰ与基体接触位置截面长度为φ1;步骤三、所述激光头ⅱ在两个相邻螺纹ⅰ之间形成螺纹ⅱ,所述螺纹ⅱ组成螺旋状涂层ⅱ;步骤四、所述涂层ⅰ和涂层ⅱ形成最终熔覆层。2.根据权利要求1所述的双光头激光熔覆成形工艺,其特征在于:所述涂层ⅰ的搭接率为0%时,所述激光头ⅰ的横移螺距为φ2,所述激光头ⅱ的横移螺距为φ3,其中,φ2=φ3=φ1,所述激光头ⅰ和激光头ⅱ的横向相对位置为0.5φ1,所述涂层ⅱ的螺纹ⅱ用于填充涂层ⅰ相邻螺纹ⅰ之间的空位,使得最终熔覆层表面平整。3.根据权利要求2所述的双光头激光熔覆成形工艺,其特征在于:所述激光头ⅰ参数为:激光功率4000-10000w,线速度5-30m/min,光斑直径2-5mm,送粉速度30-60g/min;激光头ⅱ参数为:激光功率2000-4000w,线速度5-30m/min,光斑直径1-3mm,送粉速度10-40g/min。4.根据权利要求1所述的双光头激光熔覆成形工艺,其特征在于:所述涂层ⅰ和涂层ⅱ互相的搭接率为30%-60%时,所述激光头ⅰ和激光头ⅱ的横向相对位置为(1-搭接率)*φ1,该激光头ⅰ和激光头ⅱ的横移螺距为2*(1-搭接率)*φ1,所述涂层ⅱ的螺纹ⅱ与涂层ⅰ的螺纹ⅰ尺寸相同,二者间隔设置得到最终熔覆层。5.根据权利要求4所述的双光头激光熔覆成形工艺,其特征在于:所述激光头ⅰ和激光头ⅱ的参数为:激光功率4000-10000w,线速度5-30m/min,光斑直径2-5mm,送粉速度30-60g/min。
技术总结
本发明一种双光头激光熔覆成形工艺,属于激光熔覆技术领域,其步骤为:将激光头Ⅰ和激光头Ⅱ的环向相对位置设置为0-180度;激光头Ⅰ在基体上形成螺旋状涂层Ⅰ,涂层Ⅰ的螺纹Ⅰ与基体接触位置截面长度为φ1;激光头Ⅱ在两个相邻螺纹Ⅰ之间形成螺纹Ⅱ,螺纹Ⅱ组成螺旋状涂层Ⅱ;涂层Ⅰ和涂层Ⅱ形成最终熔覆层。涂层Ⅰ的搭接率为0%时,生产效率显著提高;激光头Ⅱ专用于覆盖涂层Ⅰ相邻螺纹Ⅰ之间的波谷,可以降低最终涂层的表面粗糙度,提高有效厚度;且两束激光同时作用下,后一束激光可以起到缓冷的作用,防止涂层开裂。防止涂层开裂。防止涂层开裂。
技术研发人员:陶汪 王威 洪臣 王树良 周远东
受保护的技术使用者:亚琛联合科技(天津)有限公司
技术研发日:2022.01.19
技术公布日:2022/2/23
再多了解一些
本文用于企业家、创业者技术爱好者查询,结果仅供参考。